Überdenken von Steuersystemen für Multi-Well-Pads
Daten- und Steuerungsanforderungen erfordern eine modulare, skalierbare Steuerungsarchitektur.
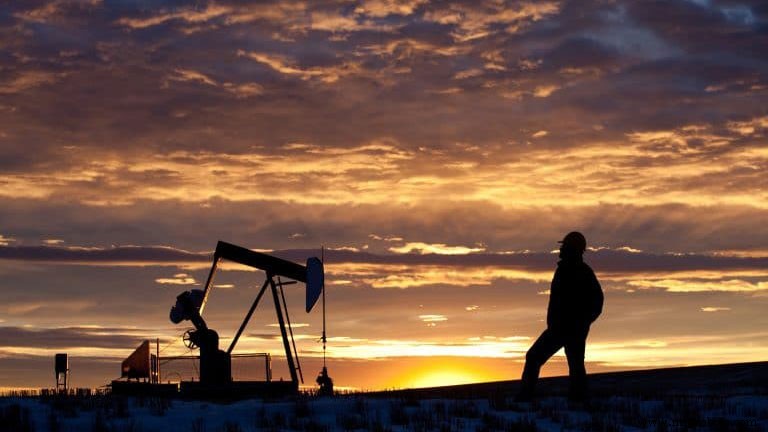
Bohrfortschritte haben die Entwicklung von Öl- und Gasbetrieben von einfachen Feldern mit einzelnen Bohrlöchern zu komplexeren Bohrlöchern mit mehreren Bohrlöchern vorangetrieben.
Heutzutage verwenden viele Produzenten Fracking- und Lateralbohrtechniken, um 10 oder mehr Bohrlöcher auf einem Pad zu platzieren. Einige Betreiber erweitern ihren Betrieb sogar auf bis zu 52 Bohrlöcher auf einem einzigen Pad.
Diese Fortschritte haben nicht nur die Produktionsausbeute aus Bohrlöchern erhöht, sondern auch völlig neue Produktionsmöglichkeiten in unkonventionellen Gebieten geschaffen. Sie haben es auch Öl- und Gasproduzenten ermöglicht, ihren betrieblichen Fußabdruck zu reduzieren.
Bei allen Vorteilen von Pads mit mehreren Vertiefungen hat jedoch ihre erhebliche Zunahme an Größe und Anwendungsbereich eine neue Herausforderung geschaffen. Die höhere Dichte mehrerer Wells auf einem einzigen Pad erhöht die vor Ort erforderliche Ausrüstung und führt zu viel größeren Daten- und Kontrollanforderungen.
Die traditionellen, jahrzehntelang verwendeten Steuerungsarchitekturen stoßen an ihre Grenzen und sind möglicherweise nicht mehr zukunftsfähig. Stattdessen werden fortschrittlichere Steuerungssysteme benötigt, um die skalierbaren Architekturen zu handhaben, die für moderne Bohrlochplatten erforderlich sind.
Infolgedessen müssen sowohl Betreiber als auch die sie unterstützenden Gerätehersteller nun ihren Steuerungssystemansatz für diese Multi-Well-Pads ändern – wenn nicht sogar radikal ändern.
Entwicklung der RTU-Technologie
Vorgelagerte Öl- und Gasproduzenten verlassen sich seit Jahrzehnten auf die Remote Terminal Unit (RTU)-Technologie für die Bohrlochsteuerung. Anfänglich beschränkten die Kosten für die Implementierung von RTUs und die Herausforderungen bei deren Programmierung die Geräte auf einfache Datenerfassung und -steuerung.
Im Laufe der Zeit haben RTUs jedoch mehr Funktionen integriert, darunter E/A, Kommunikation und IEC-61131-Programmierung. Diese Funktionen ermöglichten es Öl- und Gasbetreibern, mehr Datenpunkte zu überwachen, Historie und Alarme zu protokollieren und komplexere Berechnungen in die RTUs einzufügen. Gerätehersteller und Ingenieurbüros begannen auch mit der Entwicklung von Spezialanwendungen für Bohrlochkopf-Kunststoffhubsteuerungen mit proprietären Mikroprozessorsteuerungen.
Schließlich hatte praktisch jeder Hersteller von künstlichen Aufzügen seine eigene RTU entwickelt, um seine jeweiligen Lösungen zu steuern und zu optimieren. Ingenieurbüros entwickelten auch ihre eigenen Methoden mit leicht unterschiedlichen RTU-Anwendungen, während Instrumentenhersteller neue Instrumente einführten, um nahezu jeden erforderlichen Prozesspunkt zu messen.
In letzter Zeit jedoch haben die gestiegenen Anforderungen im Zusammenhang mit dem Betrieb von Multi-Well-Pads begonnen, die Möglichkeiten der RTU-Technologie zu übersteigen.
Geräte an ihre Grenzen gebracht
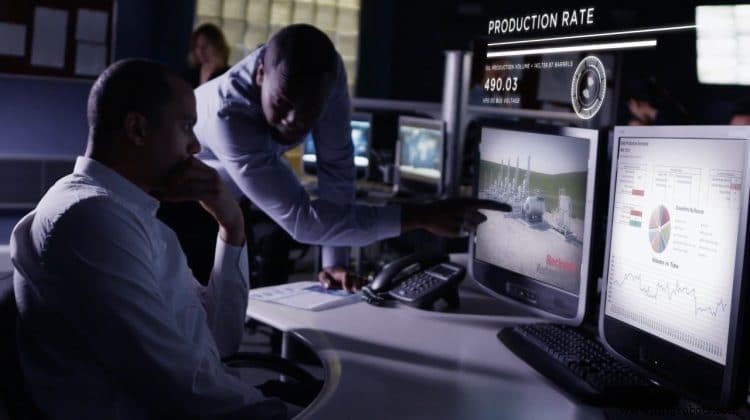
Jedes Well in einem Multi-Well-Pad erfordert einen künstlichen Lift, eine Durchflussmessung, eine Gerätesteuerung und eine Füllstandsmessung. Dadurch entsteht mehr E/A- und Steuerungsbedarf, als eine einzelne RTU bewältigen kann. Infolgedessen sind Öl- und Gasproduzenten gezwungen, zusätzliche RTUs zu kaufen und die Anwendungs- und Standortsteuerung auf mehrere Einheiten zu verteilen.
Öl- und Gasproduzenten haben erfolgreich mehrere RTU-Controller auf einer Bohrinsel implementiert, aber sie stoßen bei diesen Architekturen auf einige häufige Probleme. Einige dieser Probleme sind:
- Änderungsverwaltung mehrerer Konfigurationen oder Programme an jedem Bohrloch.
- Kommunikationsmanagement der vielen RTUs vor Ort (z. B. Peer-to-Peer-Kommunikation).
- SCADA-Kommunikation mit der Hardware mehrerer Anbieter.
- Unzuverlässige Ausführung von benutzerdefinierten Programmen in den RTUs.
Die ultimative Nachfrage nach RTU-Geräten kommt, wenn eine viel größere Multi-Well-Pad-Steuerung benötigt wird. Dies kann eine Operation mit 10 oder sogar mehreren Dutzend Wells auf einem einzigen Well-Pad umfassen. Die höhere Dichte an Vertiefungen auf einem Pad erhöht auch die erforderliche Ausrüstung vor Ort. Zum Beispiel haben viele dieser Wellpads ihren eigenen Separator.
Es wird auch wirtschaftlicher, Pipeline-Kompressionseinheiten, Dampfrückgewinnungseinheiten (VRUs) und VRU-Türme zu installieren, da aus dem Pad eine hohe Rate an Erdgas produziert wird. Mietgeräte für den automatischen eichpflichtigen Verkehr (LACT), Wassertransfer- und Chemikalieninjektionsmaschinen sind ebenfalls häufig auf diesen Bohrlochpads zu sehen.
Darüber hinaus investieren viele Öl- und Gasproduzenten in elektrische Gebäude, die als E-Häuser bekannt sind. Diese Gebäude beherbergen die Hauptstromverteilung, Motor Control Center (MCC), Netzwerk-Switches und unterbrechungsfreie Stromversorgungen (USV) und sind oft umgebungskontrolliert.
All diese Steigerungen – bei Geräten, Feldinstrumenten und Anwendungen – verstärken nur die allgemeinen Probleme mit RTU-Architekturen.
Sie schaffen auch neue Service- und Support-Herausforderungen. Die Verwendung mehrerer RTUs hat zu mehreren Anwendungskonfigurationen und Programmen zu ihrer Wartung geführt. Außerdem sind Öl- und Gasbetreiber gezwungen, mit mehreren Anbietern zusammenzuarbeiten.
Darüber hinaus erfordert der Besitz mehrerer Geräte von mehreren Anbietern auch, dass die Mitarbeiter über mehr Schulung und Erfahrung verfügen, um sie zu unterstützen. Während einige Hersteller mit ausreichend geschultem Personal ausgestattet sind, um die Wartung der Bohrlochsteuerungssysteme zu übernehmen, sind viele dies nicht. Diese Hersteller müssen sich auf die Unterstützung des Herstellers oder des Vertragsingenieurs verlassen, um ihre Kontrollsysteme zu warten.
Wechsel zu modularen, skalierbaren Steuerungssystemen
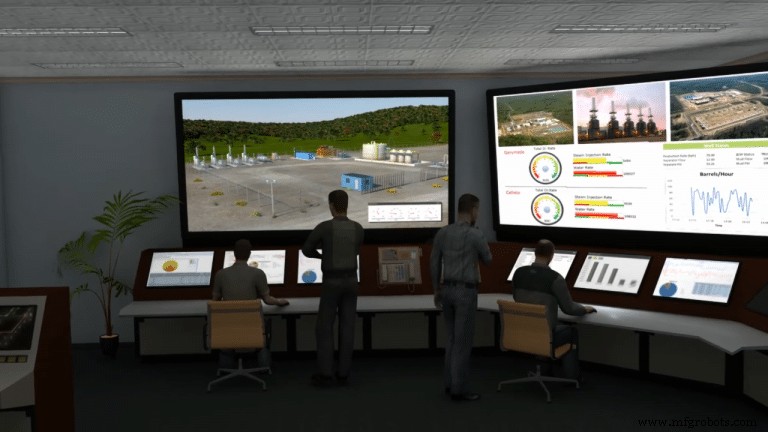
RTUs erfüllen seit Jahrzehnten ihre Rolle bei der Bewältigung einfacher Steuerungsanforderungen, einfacher Interaktion zwischen Feldgeräten und einfacher Kommunikation. In den komplexeren Betriebsumgebungen von heute reichen sie jedoch nicht mehr aus.
Viele Öl- und Gasproduzenten, die häufig RTU-Probleme hatten, haben eine praktikable Alternativlösung in Form einer modularen und skalierbaren speicherprogrammierbaren Steuerung (SPS) gefunden. Die SPS-Technologie wird seit Jahren in industriellen Prozesssteuerungsumgebungen verfeinert, die genauso robust sind wie die vorgelagerte Öl- und Gasförderung.
SPS bieten im Vergleich zu RTUs eine Reihe von Vorteilen:
- Modularität: Einige RTUs unterstützen modulare Hardware. Aber die Modulanforderungen mit Anwendungs- und Steuerungsanforderungen in einer RTU in Einklang zu bringen, ist viel schwieriger als in einer SPS. Darüber hinaus sind Module von Drittanbietern für RTUs in der Regel nicht verfügbar, da RTUs im Gegensatz zu SPS keine offenen Architekturen sind.
Für SPS ist eine Vielzahl von Modulen verfügbar, die die Überwachung und Steuerung einer Vielzahl von Funktionen ermöglichen Feldinstrumente. Durch die modulare Konfiguration wird auch die Kommunikationsunterstützung für viele verschiedene Netzwerktypen unterstützt. - Skalierbarkeit: Dies ist wichtig, wenn man bedenkt, wie ein Pad mit mehreren Vertiefungen zusammengesetzt wird. An einem Standort mit mehreren Bohrlöchern wird oft ein einziger Brunnen installiert, und erst Monate oder sogar Jahre später werden zusätzliche Brunnen und Ausrüstung in Betrieb genommen.
In diesen Fällen möchten Gerätehersteller dies tun in der Lage sein, Ausrüstungsgestelle außerhalb des Standorts zu bauen und sie dann einfach an der Bohrlochplattform anzuschließen und zu konfigurieren. Sie möchten den Bedarf an Gräben, Kabelziehen, Kabelanschlüssen, Panel- und Instrumenteninstallationen vor Ort reduzieren, um Kosten zu senken. Hier ist Skalierbarkeit sowohl in der Programmierung als auch in der Hardware gefragt und genau das bietet die SPS-Technologie. - Einfache Programmierung: In der Vergangenheit wurden SPSen als leere Leinwand für Automatisierung und Steuerung angesehen. Nur Ingenieurbüros oder erfahrene Programmierer wussten, wie man bei Null anfängt und die in einer SPS erforderliche Steuerung entwickelt.
Moderne SPS verfügen jedoch über Bibliotheken mit vorentwickeltem und dokumentiertem Code, der in kürzester Zeit schnell hinzugefügt werden kann Drag-and-Drop-Mode. Einige SPS-Anbieter verfügen auch über vorentwickelte vorgelagerte Öl- und Gasbibliotheken, die vor Ort konfiguriert werden können. Öl- und Gasproduzenten müssen nur die erforderlichen Daten vom HMI aktivieren und konfigurieren, um eine SPS zu starten oder Skid-Hardware zu einem bestehenden System hinzuzufügen.
Dadurch kann jemand wie ein Brunnen überflüssig werden Techniker mit Fachkenntnissen, um die Programmierumgebung zu kennen und beim Hinzufügen von Hardware neuen Code zu schreiben.
Darüber hinaus können Programm- und Konfigurationsänderungen online in einer SPS vorgenommen werden, ohne den Prozess herunterzufahren. RTUs können solche Änderungen traditionell nicht akzeptieren, ohne offline genommen und heruntergeladen zu werden. Dies ist ein entscheidendes Unterscheidungsmerkmal in einer modernen Multi-Well-Pad-Umgebung, da das Abschalten des Steuersystems zu Produktionsausfällen führt. - Remote I/O-Funktionalität: RTUs haben traditionell keine native Remote-I/O-Funktionalität, aber SPSen schon. Dies kann die Kosten für die Installation reduzieren. Wenn Gerätegestelle zu einem Standort hinzugefügt werden, können sie auch mit vormontierten und verdrahteten E/A und Instrumenten geliefert werden. Die Inbetriebnahme dieser Skids ist so einfach wie das Einstecken eines Ethernet-Kabels in einen Switch und das Konfigurieren der E/A in der Steuerung.
Verbesserung des Lebenszyklusmanagements
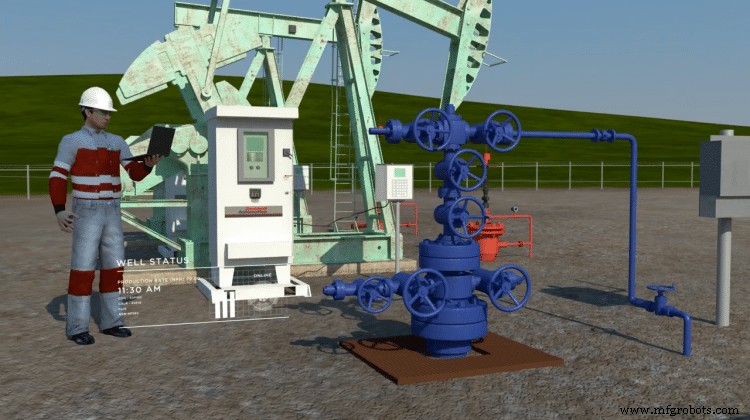
Das Lifecycle-Management von Brunnenpads kann für Betriebsteams große Kopfschmerzen bereiten. Brunnen können viele verschiedene Strömungszustände durchlaufen, darunter natürlich fließende, elektronische Tauchpumpen (ESP) oder Exzenterschneckenpumpen (PCP) und Saugstangenpumpen. Und die Flussart und der Lebenszyklus können sehr unterschiedlich sein.
Oft werden mehrere RTUs verwendet, nur um die verschiedenen Lebenszyklen des Bohrlochs zu steuern. Das Ändern der RTU bedeutet, dass die Kommunikationstreiber zum SCADA-System geändert werden müssen, da die physische RTU am Bohrloch Hardware eines neuen Anbieters ist. Und die Konfiguration der RTU zur Steuerung der Anwendung und die Einrichtung dieser Hardware im System ist oft ein mühsamer Prozess.
Eine SPS-basierte Bohrlochplatte kann in diesem Bereich eine erhebliche Erleichterung bieten und Effizienz- und Optimierungsvorteile bieten, die Betreiber vielleicht nie für möglich gehalten hätten.
Durch die Verwendung der modularen und skalierbaren E/A-Hardwarearchitekturen, die eine SPS bietet, können Bediener E/A-Module direkt dort installieren, wo sich die Instrumentierung befindet, und diese Daten an die SPS senden. Und unabhängig davon, welchen E/A-Designansatz ein Öl- oder Gasproduzent verwendet, bleibt die Hardware im Steuerungssystem konstant, die Kommunikation mit dem SCADA-System verwendet dieselben Treiber, und das System bleibt online und kontrolliert alle Anwendungen Aktualisierungen vorgenommen werden. Dabei muss nur noch ein SPS-Programm gepflegt werden.
Es gibt auch die Frage der Anwendungsunterstützung durch den Anbieter. Wie bereits erwähnt, erstellen viele Anbieter ihre eigenen Anwendungen für eine Vielzahl von Upstream-Produktionsanforderungen, und jeder Anbieter verwendet typischerweise einen anderen RTU-Typ. Infolgedessen können Anbieter normalerweise nur wenige spezifische Anwendungen unterstützen, nicht alle.
Die Unterstützung von SPS-Anbietern für Multi-Well-Pad-Designs wächst täglich. Dazu gehört die Unterstützung für Gerätesteuerung, künstliche Auftriebs- und Durchflussmessungsanwendungen. Die Anlagenautomatisierung lässt sich durch reichhaltige Programmierumgebungen und eine Vielzahl von E/A- und Kommunikationsmodulen einfach handhaben. Die Durchflussmessung wird auch mit AGA- und API-konformer Durchflussmessung, Kalibrierungsunterstützung und eichpflichtiger Übermittlung von Berichten an SCADA-Systeme unterstützt. Anwendungen für künstliche Aufzüge werden, obwohl sie in PLCs nicht so weit verbreitet sind, ebenfalls schnell entwickelt, um alle Arten von künstlichen Aufzügen zu unterstützen.
Schließlich haben viele Öl- und Gasproduzenten ihre Frustration darüber zum Ausdruck gebracht, dass RTU-Anwendungen „Black Box“ sind. Das bedeutet, dass das System mit bestimmten Eingängen ausgestattet ist, die nur bestimmte Ausgänge steuern sollen.
Ein Black-Box-Ansatz verhindert Flexibilität, da er Öl- und Gasproduzenten nicht erlaubt, die Funktionsweise des Systems zu ändern. Infolgedessen müssen sie entweder den Anbieter wechseln, um ihre Anforderungen zu erfüllen, oder einfach mit der Technologie leben, die sie haben, da sie wissen, dass sie nicht so effizient funktioniert, wie sie es benötigen.
Ein SPS-basiertes System hingegen kann vor Ort mit gängigen Industriewerkzeugen (IEC-61131) modifiziert werden, was eine viel größere Flexibilität bietet.
Die neue Normalität annehmen
Die SPS wurde lange als eine Lösung angesehen, die eher für Produktionsanlagen als für die Bohrlochsteuerung geeignet ist. Aber die modernen Brunnenpads von heute sind im Wesentlichen kleine Fabriken. Sie haben ökologisch kontrollierte Gebäude, Versorgungs- oder Generatorstrom und viel größere Daten- und Kontrollanforderungen.
Damit passen sie ideal zu einer SPS. Ein Multi-Well-Pad-Steuerungssystem, das die modularen und skalierbaren Fähigkeiten einer SPS nutzt, kann Kosten und Installationszeiten reduzieren, die Produktionsverfügbarkeit verbessern und das Lebenszyklusmanagement vereinfachen.
Zack Munk ist Onshore Upstream Oil &Gas Business Development Manager für Rockwell Automation.
Automatisierungssteuerung System
- Aufbau flexibler Fertigungssysteme für Industrie 4.0
- ASM Assembly Systems verwendet den Sawyer-Roboter von Rethink Robotics für Qualitätskontrollen
- Überlegungen zu AFD-Bedienfeldern
- Vorteile eingebetteter Technologien für modulares Design
- Einfache Lösungen für alte Automatisierungssysteme
- Unternehmen setzen Fristen für intelligente Systeme
- Top 10 Arbeitsabläufe für Hersteller
- Lokale vs. globale Systeme zur Produktionssteuerung
- Vorteile der Verwendung von VIA in Pads
- Marposs kündigt modulares Steuerungssystem BLÚ LT für Werkzeugmaschinen an