Eine neue Welt für die Herstellung von Energieteilen
Bedenken hinsichtlich des Klimawandels und des globalen Kohlendioxidgehalts haben grüne Energie in den letzten Jahren näher an den Fahrersitz gebracht. Laut dem Global Energy Review der Internationalen Energieagentur (IEA) erwarten die meisten Experten, dass erneuerbare Energien im Jahr 2021 fast 30 Prozent des gesamten Stroms erzeugen werden, wobei die Wind- und Solarenergie um 17 Prozent bzw. 18 Prozent steigen wird.
Trotz dieses beeindruckenden Wachstums dominieren weiterhin fossile Brennstoffe den Markt, wobei die IEA prognostiziert, dass allein die Kohlenachfrage 60 Prozent mehr ausmachen wird als alle erneuerbaren Energien zusammen. Dadurch energiebedingtes CO2 -Emissionen sind bereit, ihren zweitgrößten jährlichen Anstieg aller Zeiten zu erreichen und alle pandemiebedingten Verringerungen der Treibhausgaskonzentrationen zunichte zu machen.
Es ist sicher eine dynamische Branche, aber eines ist sicher:Der globale Energieverbrauch – in welcher Form auch immer – wird auch weiterhin neue Möglichkeiten für Maschinenwerkstätten und andere diskrete Hersteller schaffen. Pumpen- und Turbinengehäuse, Getriebe, Wurzelabschnitte für Windmühlen, Bohrlochköpfe und Bohrkomponenten – dies sind nur einige der Teile, die täglich von Energie-OEMs und ihren Tier-Zulieferern hergestellt werden, viele davon ziemlich groß, schwer und aus anspruchsvollen Materialien wie Inconel und Duplex-Stahl.
Werde groß oder gehe nach Hause
Große Teile erfordern große Maschinen, große Spannmittel und große Schneidwerkzeuge – die alle eine große Investition erfordern. Klaus Miller, Vice President of Sales bei Absolute Machine Tools Inc., Lorain, Ohio, hilft gerne bei der ersten davon. Er merkte an, dass die Energie- und Luft- und Raumfahrtmärkte in den letzten zwei Jahren langsam waren, obwohl beide sich jetzt zu erholen scheinen, da das Schlimmste der Pandemie hoffentlich hinter uns liegt.
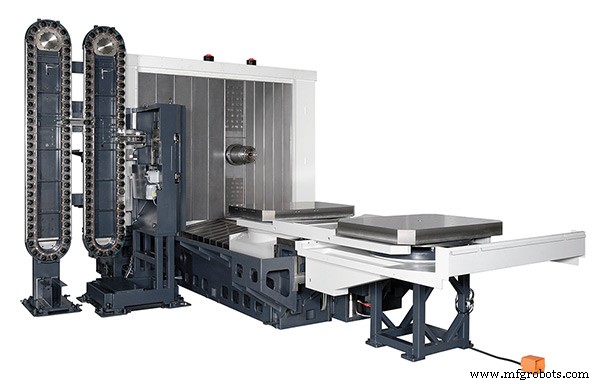
„Wir sind ein Importeur von You Ji und anderen Marken von CNC-Maschinen“, sagte Miller. „You Ji rüstet einige seiner größeren Anlagen mit hydrostatischen Tischlagern aus, was sie bei Herstellern von Energieteilen sehr beliebt macht. Das liegt daran, dass diese Werkzeugmaschinen die extrem hohen Belastungen bewältigen können, die in diesem und anderen Bearbeitungsbereichen auftreten, und aufgrund dieser Eigenschaft eine hervorragende Langzeitgenauigkeit bieten.“
In einem kürzlich erschienenen Beispiel installierte Absolute eine vertikale Revolverdrehmaschine (VTL) von You Ji mit einem 4-m-Tisch. Das Unternehmen, das es kaufte, bearbeitet große Energiewerkstücke, die laut Miller nach dem Anstieg der Investitionen in saubere Energie im Zeitraum 2006 stark ankamen, aber etwa ein Jahrzehnt später nachließen, als die Fertigung nach China, Rumänien und anderen Billiganbietern ins Ausland verlagert wurde . Diese neue Installation könnte eine Umkehrung dessen anzeigen, was seit langem ein Trend ist.
Absolute hat Anfang dieses Jahres auch ein Bohrwerk mit großer Kapazität für einen lokalen Kunden installiert. Obwohl die Betriebsleitung die spezifische Anwendung nicht offenlegte, teilte sie Miller mit, dass sie für Energiearbeiten bestimmt sei und eine Tragfähigkeit von 35.000 lbf (155,7 kN) haben müsse. „Sie hatten bereits eine Brückenmühle in Johnford, brauchten aber etwas Größeres“, sagte er. „Auch hier erwies es sich zwischen den hydrostatischen Lagern und der schieren Masse der Maschine – 58.967 kg (130.000 lb) – als die richtige Lösung.“
Je schwerer desto besser
Die Maschinenmasse ist eindeutig wichtig, wenn schwere Schnitte durchgeführt werden und Genauigkeit bei Teilen angestrebt wird, die größer als ein Pick-up sind. Miller und andere schlugen vor, dass heute nur noch wenige Werkzeugmaschinenhersteller „sie so machen wie früher“ und dass viele Maschinenwerkstätten sich daher dafür entschieden haben, ihre Lucas, Giddings &Lewis und andere alte Eisen mit CNC-Steuerungen nachzurüsten. Und obwohl dies eine hervorragende Möglichkeit ist, die Lebensdauer einer sicherlich erheblichen Investition zu verlängern, kommt eine Zeit, in der selbst die beste Ausrüstung im Vergleich zu ihrem modernen Äquivalent zu kurz kommt, egal wie oft sie aktualisiert wurde.
Eine weitere Möglichkeit für Werkstätten, diese Investitionen zu maximieren, besteht darin, ihre Kapazitäten für die Bearbeitung großer Teile zu nutzen, um über den Energiemarkt hinaus zu expandieren. Beispielsweise ist die Verteidigungsindustrie ein bedeutender Nutzer von übergroßen Teilen, ebenso wie die Bergbau-, Landwirtschafts- und Bauindustrie. Die Bewältigung solcher Arbeiten bedeutet jedoch, dass Werkstätten in flexible Werkzeugmaschinen investieren müssen, die sich leicht an eine Vielzahl von Teilen anpassen lassen und über Funktionen verfügen, die Ausfallzeiten minimieren.
Bernard Otto, Leiter des technischen Supports und Produktmanager für Produkte von Kiwa Japan und OKK Japan bei Methods Machine Tools Inc., Sudbury, Mass., hat mehrere Empfehlungen, wie dies erreicht werden kann. Er stellte fest, dass zahlreiche Kunden von Methods die Fracking-Industrie unterstützen und Pumpen, Gehäuse und ähnlich große Komponenten herstellen. Wettbewerbsfähig zu sein bedeutet hier nicht nur, große Materialmengen effizient von Stahlguss- und Schmiedeteilen zu entfernen, sondern auch die Spindel ständig am Laufen zu halten.
„Eine hohe Spindelauslastung erfordert, dass die Person, die die Maschine bedient, Teile mit einem Gewicht von 7.711 kg (17.000 lb) schnell, genau und vor allem sicher in die Maschine ein- und auslagern kann“, sagte er. „Das geht in den meisten Fällen am besten mit einem Palettenwechsler.“
In die Tiefe gehen
Otto wies auch darauf hin, dass ein breites Spektrum an Spindeldrehzahlen eine ähnliche Flexibilität bietet. Er sagte, dass viele der Bearbeitungszentren in diesem Bereich mit 50-Kegel-Getriebespindelstöcken mit nur zwei Bereichen, Hochgeschwindigkeit und Niedriggeschwindigkeit, und einer maximalen Drehzahl von 3.600 U / min ausgestattet sind. Dies schränkt die Fähigkeit ihrer Besitzer ein, kleine Bohrer und Fräser zu verwenden oder Aluminiumlegierungen zu bearbeiten.
„OKK ist einer der wenigen Hersteller, der drei Getriebebereiche und bis zu 6.000 U/min anbietet, sodass seine Kunden beispielsweise mit großen Planfräsern sehr aggressiv zerspanen und bei Bedarf auch kleinere Schneidwerkzeuge verwenden können“, sagte Otto. „Das macht sie viel vielseitiger für Werkstätten, die eine Vielzahl von Werkstücken produzieren müssen.“
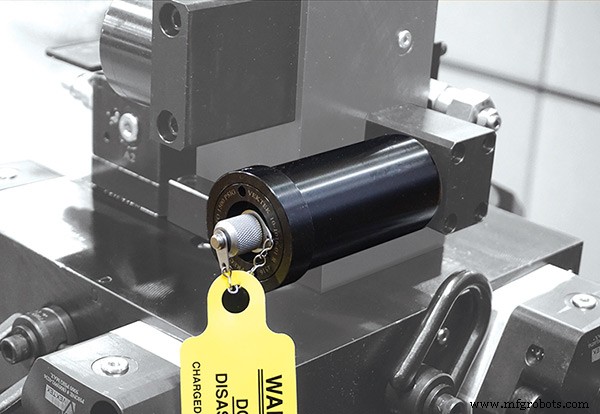
Weitere Merkmale, auf die Sie achten sollten, sind ein hoher Z-Achsen-Schub für schwere Bohrarbeiten, integrierte Rohrleitungen für automatisierte hydraulische Werkstückspannung und bei Bohrwerken die Möglichkeit, die Pinole (die W-Achse) an Ort und Stelle zu arretieren, wodurch die Steifigkeit beim tiefen Schruppen erheblich erhöht wird Taschen. Aus diesen und anderen Gründen stimmt Otto mit Miller von Absolute darin überein, dass es der klare Weg nach vorne für Werkstätten ist, mit der aktuellen Werkzeugmaschinentechnologie Schritt zu halten, die so wettbewerbsfähig wie möglich bleiben möchten.
Aber die vielleicht wichtigste Empfehlung für Energieversorger und andere mit schwankendem Bedarf ist, ihre Maschinen eingeschaltet und voll funktionsfähig zu halten. Dies gilt insbesondere für den Öl- und Gassektor, der sehr zyklisch sein kann, und für Unternehmen mit längst abbezahlten Maschinenparks, die zwischen den Jobs eher brach liegen.
Otto:„In diesen Situationen nimmt unsere Serviceabteilung oft Anrufe von Kunden entgegen, die versuchen, eine Maschine zu starten, die Monate und manchmal Jahre nicht benutzt wurde, nur um festzustellen, dass eine Achse eingefroren oder ein elektronisches Bauteil defekt ist . Aus diesem Grund raten wir den Geschäften, ihre Maschinen regelmäßig zu warten, und, noch besser, sie auf einen vorbeugenden Wartungsplan mit einem autorisierten Händler zu setzen. So vermeiden Sie unangenehme Überraschungen, unabhängig von der Maschinenmarke, ihrer Größe oder der Art der Arbeit.“
Konsequent greifen
Braden Damman unterstützte die Notwendigkeit einer hydraulischen Werkstückaufnahme, obwohl er schnell darauf hinwies, dass die zuvor erwähnte integrierte Verrohrung keine Voraussetzung ist. Ein Anwendungstechniker beim Lieferanten von Werkstückhalterungskomponenten Vektek LLC, Emporia, Kan., Damman, stellte fest, dass mehrere zusätzliche Konfigurationsoptionen verfügbar sind, darunter solche, bei denen die Werkstückhalterung selbst für die Hydraulik angeschlossen und von einem externen „Akkumulator“ angetrieben wird, einem Gerät, das den Druck aufrechterhält am System während der Bearbeitung.
Unabhängig vom Ansatz ist die hydraulische Spanntechnik der klare Sieger in Bezug auf Beständigkeit und Zuverlässigkeit, wenn nicht sogar im Preis. „Bei den meisten Anwendungen ist die Hydraulik die teuerste Lösung, obwohl die anfänglichen Kosten schnell durch Produktivitätssteigerungen ausgeglichen werden“, sagte Damman. „Es eliminiert die Variationen, die bei manuellen Spannmethoden auftreten, und ist ein Muss für automatisierte Prozesse.“
Ironischerweise ist ein Großteil der großen Energieteil-Arbeitshaltung, bei der Damman gerufen wird, um zu helfen, für sekundäre Operationen bestimmt. „Wir sehen eine ganze Reihe von Gasturbinenkomponenten, die feine Details mit sehr engen Toleranzen aufweisen“, sagte er. „Bei diesen Anwendungen möchte der Kunde das Teil oft auf einer CNC-Schleifmaschine für die Endbearbeitung montieren und muss es außerdem automatisieren. Hydraulische Werkstückspannung ist aufgrund ihrer hohen Wiederholgenauigkeit fast immer die bevorzugte Methode.“
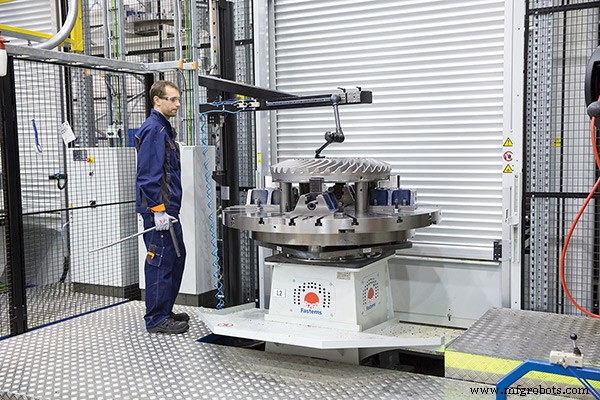
Larry Robbins, Präsident des Spannmittelspezialisten SMW Autoblok Corp., Wheeling, Illinois, ist ein großer Fan von wiederholbarem Spannen, stellte jedoch fest, dass es aufgrund ihrer Variabilität häufig notwendig ist, große Teile neu zu positionieren. „Egal, ob es sich um ein Schmiede- oder Gussstück handelt, jedes Mal, wenn Sie einen Durchmesser von über einem Meter oder so haben, brauchen Sie fast immer eine Möglichkeit, seine Position innerhalb des Spannfutters anzupassen“, sagte er. „Seit etwa 25 Jahren bieten wir eine unabhängige Backeneinstellung mit unseren manuellen und hydraulischen Spannfuttern an, haben diese Fähigkeit jedoch in den letzten Jahren auf unsere Produktlinie mit elektrisch betätigten Spannprodukten ausgeweitet.“
Energetische Arbeitshaltung
Robbins erklärte, dass die MM e-motion-Spannfutter des Unternehmens über ein patentiertes lineares Positionierungssystem (LPS) verfügen, das es dem Bediener – automatisch oder anderweitig – ermöglicht, die Position des Teils in der Maschine über einen Messtaster zu messen, die Positionsinformationen an die Steuerung zu senden und zu verwenden das Spannfutter zentriert das Teil entsprechend. Jede Backe wird von einem eigenen „E-Motor“ angetrieben und gesteuert, der wiederum von einem induktiven Koppler angetrieben wird, wodurch das System in stationären oder rotierenden Anwendungen eingesetzt werden kann. Teile aller Formen und Größen bis zu 1.250 mm werden aufgenommen, ebenso wie die Änderung der Greifkraft, sogar während das Teil bearbeitet wird.
Wie mehrere andere hier bereits festgestellt haben, haben Robbins und SMW Autoblok in den letzten zwei Jahren Rückgänge im Energie- und Luft- und Raumfahrtsektor erlebt, obwohl beide in letzter Zeit einen Aufwärtstrend verzeichneten. Interessanterweise sieht er eine Nachfrage aus der Öl- und Gasindustrie nach Spannfuttern, die immer größere Rohre greifen können, eine Anforderung, die sowohl aus Sicht der Werkstückspannung als auch aus Sicht der Werkzeugmaschine herausfordernd ist.
„In der Vergangenheit haben wir die Grundbacken neu gestaltet, um die Kapazität in bestehenden Spannfuttern zu erhöhen, aber jetzt sehen wir uns angesichts der Nachfrage nach Durchgangsbohrungen von 24 Zoll (610 mm) mit völlig neuen Produktdesigns konfrontiert“, sagte er. „ Solch große Durchmesser stellen auch eine hohe Belastung für die Spindellager einer Drehmaschine dar. Das können wir durch den Einsatz von Lünetten etwas abmildern, aber auch hier stoßen wir an die Grenzen der bestehenden Spanntechnik Schaffung eines völlig neuen Marktplatzes.“
Automatisierung vereinbaren
Ähnliche Nachfragen nach neuen Technologien sieht der Automatisierungssystemanbieter Fastems LLC USA, West Chester, Ohio. Loy McEldowney, Regional Sales Manager, sagte, dass der Energiesektor traditionell langsam bei der Einführung der automatisierten Teilehandhabung sei, obwohl sich diese Denkweise dank des anhaltenden Mangels an qualifizierten Arbeitskräften zu ändern begonnen habe. „Wie viele Branchen verlieren sie Know-how und haben keine andere Wahl, als zu automatisieren, wo immer sie können.“
Dies erfordert mehrere Dinge. Eines der zuvor beschriebenen palettenwechselnden Bearbeitungszentren ist ein guter Ausgangspunkt, dicht gefolgt von einer Form der automatisierten Werkstückaufnahme. Neben der bereits angesprochenen hydraulischen und elektronischen Befestigung sind auch luft- oder mechanisch betätigte Nullpunkt-Ortungssysteme erhältlich. McEldowney sagte, dass die Halteknöpfe für solche Systeme oft direkt an großen Werkstücken montiert werden, wobei die passende Aufnahme an der Palette befestigt ist.
Am wichtigsten ist vielleicht die Entwicklung stabiler, vorhersagbarer Prozesse. Diese Aufgabe kann bei jedem bearbeiteten Teil eine Herausforderung darstellen, insbesondere jedoch bei Arbeiten mit geringem Volumen und hoher Produktvielfalt, die in der Energieerzeugung üblich sind. Trotzdem tun immer mehr Lieferanten von Öl- und Gaskomponenten genau das.
„Um die Investition in die Automatisierung und die anschließende Prozessentwicklung zu rechtfertigen, sind weniger hohe Volumina als vielmehr ziemlich wiederholbare Aufträge erforderlich“, sagte McEldowney. „Für Unternehmen, die langfristige Vereinbarungen mit ihren Kunden haben und sehen können, was in den nächsten 18 bis 24 Monaten kommt, ist es viel weniger beängstigend, Geld für spezielle Vorrichtungen, Paletten, auf die sie gestellt werden, und eine automatisierte oder sogar halbautomatische automatisiertes Lagersystem. Kommt ein Auftrag, müssen sie nur noch die Palette beladen, das Programm aufrufen und das Teil abfahren. Und diejenigen mit unserem MMS-System (Manufacturing Management Software) und integriertem Zellcontroller können dies ohne weiteres tun. In jedem Fall macht es die Fertigung auch kleinerer Stückzahlen sehr effizient.“
Automatisierungssteuerung System
- Neues Karriereprofil für Industrie 4.0
- Neue Gebiete in der Fertigung voraus
- B&R stellt neues Simulationstool für die Entwicklung digitaler Zwillinge vor
- Coil-Drehmaschine für Kleinteile
- Acht Spindeln für komplexe Teile
- Vertikale Pick-up-Drehmaschine für große Teile
- Ein definitiver Leitfaden für die Lights-Out-Fertigung
- Grüne Fertigung:Umweltfreundliche Ideen für Fabriken
- McKinsey:digitale Fertigung, Vorbereitung auf eine neue Normalität
- Carbon und Ford arbeiten zusammen, um neue Teile digital herzustellen