Virtuelle Zwillinge optimieren den Betrieb bei CenterLine
In der Militärwissenschaft ist ein „Kraftmultiplikator“ ein operatives System, das Strategien einsetzt, um die Effektivität bestehender Waffen zu erhöhen. Wir können die Idee als Metapher für die Verbesserung der Effizienz von Konstruktions- und Fertigungsinformationssystemen verwenden, vom ersten Konzept bis zum laufenden Kundendienst.
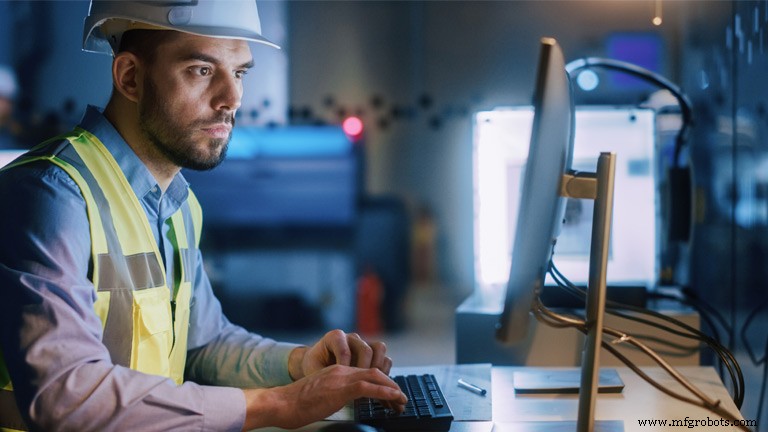
Die „Waffen“ der industriellen Automatisierung werden durch eine Vielzahl von Akronymen repräsentiert:CAD, CAE, PDM, PLM, SCM, MES, CMS und mehr. Nahezu jedes Fertigungsunternehmen verfügt über ein gewisses Maß an Prozessautomatisierung, doch viele Gespräche über Fertigungsprozesse enden mit dem Satz:„Dann kopieren wir die Daten aus der Stückliste“. Hier hören Effizienzsteigerungen auf. Um unsere anfängliche Metapher fortzusetzen:Produktionsunternehmen besitzen die Waffen, aber es gibt keine vorrangige Strategie, um sie zu einem industriellen Machtmultiplikator zu machen.
Wir haben Zugriff auf zahlreiche Datenerstellungs-, Erfassungs- und Verwaltungslösungen im gesamten Fertigungsbereich, die verschiedene Aspekte darüber informieren, was ein Produkt sollte werden und wie ein Herstellungsprozess sollte arbeiten, System für System. Der nächste Schritt besteht darin, über „sollte“ hinaus zu „macht“ zu gehen. Die Umwandlung von Informationen in Echtzeitinformationen ist der Kraftmultiplikator – die geplanten Leistungsdaten, die diese Lösungen bereitstellen, können zu Informationen über die Leistung in Echtzeit und in der realen Welt werden.
Strategische Informationsrahmen
Virtueller Thread und virtueller Zwilling (auch bekannt als digitaler Zwilling/Thread) sind zwei verwandte Konzepte, die im Vordergrund dieses Strebens nach Echtzeit-Intelligenz stehen. Zur Erinnerung:Ein virtueller Thread ist die Möglichkeit für Benutzer, bestimmte Leistungen zu verbessern, indem die richtigen Informationen zur richtigen Zeit an die richtigen Personen übermittelt werden. Ein virtueller Zwilling hingegen ist eine ständig aktualisierte visuelle Darstellung eines Produkts, Systems oder Prozesses, die auf Daten aus der realen Welt basiert.
Diese neuen Informationsrahmen treiben ein neues Prozessmodell voran, in dem Daten sowohl als Teil eines virtuellen Threads als auch eines virtuellen Zwillings betrachtet werden. Im modellbasierten Engineering beispielsweise stellen Faden und Zwilling einen strategischen Rahmen dar, um im Unternehmen maximalen Wert zu schaffen. Beide beinhalten As-Designed-Anforderungen; Validierungs- und Kalibrierungsaufzeichnungen; und Bestands-, Betriebs- und Wartungsdaten.
Virtueller Faden und virtueller Zwilling sind Konzepte, keine spezifischen Produkte oder Dienstleistungen:Sie können nicht zu Ihrem lokalen Integrator laufen und einen virtuellen Faden bestellen. Stattdessen bieten sie Lösungen, die Benutzern helfen, vollständig digitale Systeme zu erstellen, in denen jeder Einzelne in der Organisation alle benötigten Informationen in einem leicht zugänglichen und leicht zu teilenden System hat.
Konnektivität ist das übergeordnete Ziel. Viele datenbezogene Probleme sind auf Verbindungen und Zugriff zurückzuführen, was bedeutet, dass Unternehmen die Ineffizienzen beseitigen müssen, die Fertigungsabläufe plagen.
Wie viele dieser Herausforderungen gibt es in Ihrem Unternehmen?
- Engineering-Änderungen erreichen die Werkstatt nicht rechtzeitig
- Mangelnde Lieferantentransparenz
- Kein Standard oder Kontrolle bei der Erstellung von Arbeitsanweisungen
- Asynchrone Verwaltung und Steuerung von Inhalten
- Marketing erstellt Inhalte mit veralteten Designinformationen
- Produktivitätsverlust durch ungenaue, unklare Informationen
- Mangelnder Datenzugriff für die richtigen Personen.
Während viele dieser Probleme nach Technologie- oder Methodikproblemen klingen, wirken sie sich immer auf die Personen im nachgelagerten Betrieb aus, indem sie ihre Fähigkeit zur Optimierung von Arbeitsabläufen beeinträchtigen. Um den Betrieb effizienter zu gestalten, müssen Sie die verwendeten Systeme verbessern und nicht versuchen, die Menschen, die sie verwenden, zu „reparieren“. Vollständig digitale Systeme erfüllen die Anforderungen der Teammitglieder, indem sie diese Konnektivitäts- und Datenzugriffsprobleme eliminieren.
Der virtuelle Faden
Der virtuelle Thread – die Kommunikationsseite des neuen industriellen Frameworks – ermöglicht einen verbundenen Datenfluss für alle Asset-Informationen und zugehörigen Metadaten. Die Idee des virtuellen Fadens entstand vor mehr als 10 Jahren in der Luft- und Raumfahrtforschung, als Forscher des U.S. Air Force Research Laboratory auf der Wright-Patterson Air Force Base damit die modellgetriebene Montage in der Fabrikhalle beschrieben. Mehrere Threads erstrecken sich vom Modell (der gemeinsamen Datenquelle) bis hin zu Design-, Beschaffungs-, Test-, Produktions-, Außendienst- und Wartungsteams, was bedeutet, dass keine Person im Thread Daten anfordern oder auf Datenanforderungen mit einer Kopie antworten muss / E-Mail einfügen. Die Informationen sind immer „on“ und immer zugänglich, wodurch eine wirklich einzigartige Ressource und ein Kommunikationsweg für alle Parteien unabhängig von Silo oder Workstream geschaffen wird.
Der virtuelle Zwilling bei CenterLine
Ein ständig aktiver Echtzeitzugriff auf Daten aus virtuellen Threads macht einen virtuellen Zwilling möglich. Die Threads übertragen eine umfassende Ansicht des Produkts und kombinieren Stücklistendetails mit CAD/CAE-Daten für eine visuelle, virtuelle Echtzeitdarstellung. Es bedarf eines bidirektionalen Flusses in virtuellen Threads, um einen echten virtuellen Zwilling zu ermöglichen, was eine Rückkopplungsschleife erfordert, in der Kalibrierung, Validierung, As-Built- und As-Used-Daten den Zwilling aktualisieren. Zusammen bilden der virtuelle Faden und der virtuelle Zwilling die Vereinigung von Design und Daten.
Das kanadische Industrieautomatisierungsprozess- und Technologieunternehmen CenterLine Limited (Windsor, Ontario), ein Hersteller von kundenspezifischen automatisierten Schweiß- und Montagelinien, stand beispielsweise vor Herausforderungen mit teuren Fabrikeinrichtungen, insbesondere wenn das Unternehmen Konstruktionsfehler beheben oder Betriebsunfälle beheben musste zwischen Maschinen und Menschen in bereits installierten physischen Systemen.
CenterLine war bestrebt, das Design seiner Roboter-Arbeitszellen zu optimieren und diese Herausforderungen durch digitale Simulation zu meistern, bevor die physische Ausrüstung in den Fabrikhallen eingesetzt wird. Um dieses Ziel zu erreichen, implementierten sie die DELMIA-Lösung auf der 3DEXPERIENCE-Plattform von Dassault Systèmes, um Produkte, Prozesse und Fabrikabläufe für optimierte Roboterbewegungen, Anlagenlayout, Materialfluss und Ergonomie virtuell zu simulieren.
Seit der Implementierung von DELMIA für jede Roboter-Arbeitszelle hat CenterLine werkzeugbezogene Probleme und Nacharbeiten um bis zu 90 Prozent und die Programmierzeit am Boden um bis zu 75 Prozent reduziert. Die Zeitersparnis durch die Simulation von Roboter-Lichtbogenschweiß-Werkzeugwegen hat die Produktivität um 15 Prozent verbessert und die Time-to-Market für Simulation und Konstruktion um 15 bis 20 Prozent verkürzt. Als Single Source of Truth für verschiedene CAD-Daten ermöglicht die einheitliche Plattform den Führungskräften bei CenterLine, sich auf den täglichen Betrieb zu konzentrieren, anstatt Daten und Produkte zu verwalten
Wenn alle Datenkanäle in einem Virtual Thread/Virtual Twin-Framework verbunden sind, sind die Teammitglieder in einer Strategie vereint, die eine bessere Nutzung vorhandener Daten ermöglicht. In der Tat erhalten Hersteller letztendlich einen neuen Kraftmultiplikator für den Fertigungswert.
Automatisierungssteuerung System
- Digitale Zwillinge:Warum virtuelle Nachbildungen von Assets echten Geschäftswert schaffen
- So sammeln Sie Daten aus Legacy-Systemen, um den Betrieb zu verbessern
- Bedeutung von IoT-Daten in der Landwirtschaft bei John Deere
- Präzision digitaler Zwillingsdatenmodelle ist der Schlüssel zum Erfolg
- Wie digitale Zwillinge die Logistikleistung steigern können
- Ridecell führt die „erste Plattform“ ein, um Fahrzeugdaten in automatisierte Abläufe umzuwandeln
- Was ist Standzeit? Werkzeugoptimierung mit Maschinendaten
- Drei Möglichkeiten, wie KI Fertigungsabläufe verbessert
- Warum Ihr Lager- und Fabrikbetrieb IIoT braucht
- Digitale Zwillinge:Was meinen Sie damit?