Legacy-Maschinen können für den modernen Betrieb gedatamint werden
Noch vor zwei Jahren, als Brad Klippstein von Okuma America einige Betriebsdaten aus einer alten Werkzeugmaschine herausquetschen wollte, musste er Dutzende von Kabeln an den Schaltschrank anschließen und eine SPS hinzufügen. Sobald er fertig war, flossen die Daten von der Werkzeugmaschine zur SPS und dann weiter zu einem Hub oder Server, wo sie gespeichert werden.
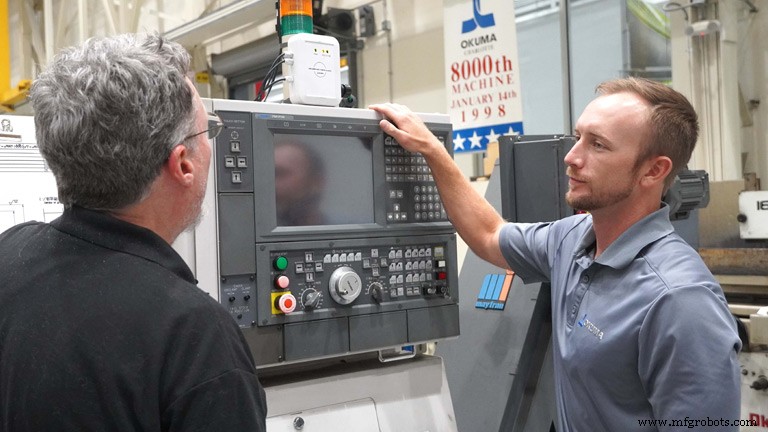
„Wir haben Dinge wie Ethernet und Wi-Fi und all diese Technologien, die wir heute nutzen können“, sagte Klippstein, Supervisor für Produktspezialisten. „Aber Geräte von vor über 30 Jahren hatten diese Fähigkeit nicht, also musste man ein Gerät physisch mit dem Schaltschrank verdrahten, um all diese Daten zu extrahieren. Jetzt müssen wir nicht einmal mehr eine feste Verbindung [mit neuen Maschinen] haben. Sie können Dinge drahtlos erledigen. Das ist der Übergang in den letzten 30-40 Jahren.“
Ein Teil von Klippsteins Job ist es, Kunden dabei zu helfen, diskrete Schritte in die vernetzte, digitalisierte und datengesteuerte Welt der Industrie 4.0 zu unternehmen – für neue und ältere Werkzeugmaschinen.
Zu diesen Vorteilen können gehören:
- Werkzeugmaschinenüberwachung in Echtzeit, im Werk oder von einem entfernten Standort aus
- Höhere Produktivität und Qualität
- Voreingenommene Berichterstattung
- Erwerbsbegründung
- Vorausschauende Wartung
- Top-Talente gewinnen und halten, die von der Aussicht begeistert sind, neue Dinge zu lernen und an der Spitze moderner Prozesse zu stehen.
Unabhängig davon, ob sie über Kabel oder die Luft übertragen werden, können die von Werksgeräten gesammelten Daten einem Ladenbesitzer dabei helfen, klügere Geschäftsentscheidungen zu treffen.
Durch die Analyse der vorliegenden Daten haben die Mitarbeiter einen besseren Einblick in die Betriebsabläufe, was ihnen helfen kann, Probleme zu lösen, Prozesse zu verbessern und die Produktivität zu steigern.
Mit einem kürzlichen Fortschritt braucht dieser Ladenbesitzer vielleicht nicht einmal mehr jemanden wie Klippstein für seine alten Werkzeugmaschinen.
Im Jahr 2019 brachte Okuma NET BOX Suite-C Quick als kostengünstigere Alternative zu einer technischen Lösung zum Sammeln von Daten von älteren Maschinen heraus. Die NET BOX CQ, kurz gesagt, wird direkt mit einer Signalsäule und dann mit einem Hub oder Gerät verbunden, das zum Empfangen von Signalen verwendet wird.
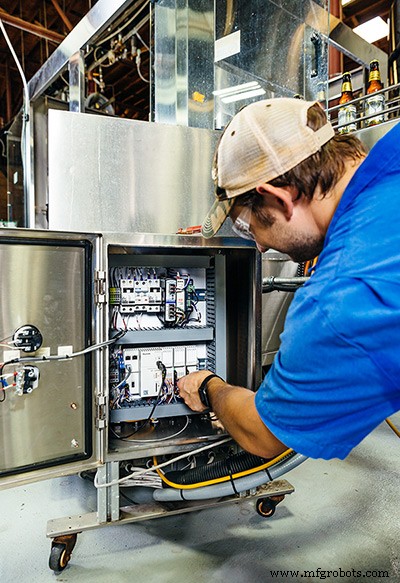
NET BOX CQ verwendet drei optische Sensoren – je einen für die grünen, gelben und roten Lichter am Turm – und wandelt die gesammelten Informationen in ein Format um, das von einem Computersystem gelesen werden kann. Um die von seiner Software erfassten Daten zu standardisieren, verwendet Okuma MT Connect, ein häufig verwendetes Open-Source-Kommunikationsprotokoll.
„Es ist einfach zu installieren, und Sie brauchen keinen Okuma-Techniker, um es zu tun“, sagte Klippstein über NET BOX CQ.
Zunächst einmal ist die Möglichkeit, zu sehen, ob eine Maschine läuft, eine großartige Metrik, die es zu verfolgen gilt, da ein Ladenbesitzer normalerweise jedes Gerät auf maximale Produktion bringen möchte. Er möchte, dass seine Gesamtanlageneffektivität (OEE) im Bereich von 65 bis 85 Prozent liegt, da eine Maschine nur dann Geld verdient, wenn sie läuft.
„Durch das Abrufen dieser Informationen – grün, gelb, rot – kann ich diese im Laufe der Zeit verfolgen und tendieren und zumindest sehen, wann und wie lange Unterbrechungen aufgetreten sind“, sagte Klippstein. „Und dann würde ich den nächsten Schritt machen und sagen:‚Warum ist das passiert und warum passiert es weiterhin jeden Tag um 2:30?‘ Also, jetzt kann ich die Dinge trenden. Das bringt mich zumindest einen Schritt in die richtige Richtung.“
Christopher Rezny, zentraler Regionalleiter des Fabrikautomatisierungsanbieters Fastems, sagte, dass MT Connect und die Software von Okuma zwar sehr gute Mittel zur Datenerfassung sind, die begrenzte Menge an Daten, die von einer älteren Maschine verfügbar sind, jedoch nicht der einzige Nachteil im Vergleich zu modernen Maschinen ist. P>
„Schnittstellen von älteren, veralteten Maschinen zurück zu anderer verwendeter interner Software, beispielsweise einem ERP-System, sind ebenfalls entweder sehr begrenzt oder nicht vorhanden“, sagte er. „Es kann auch Probleme im Zusammenhang mit den Feedback-Mechanismen dieser älteren Maschinen in Bezug auf Sicherheitsprotokolle für den Benutzer geben.“
Werksmitarbeiter müssen bereit sein für Veränderungen
Trotz der von Rezny beschriebenen Einschränkungen gibt es viele Daten und Maschinen, mit denen Unternehmen wie Okuma und Excellerant Manufacturing arbeiten können.
„Die Mehrheit der Geschäfte hat Altgeräte“, sagte John Carpenter, Präsident von Excellerant Manufacturing. „Die meisten Leute kommen zu uns aufgrund unserer Erfahrung mit Altgeräten – weil wir diese Schränke in- und auswendig kennen –, weil wir im Laufe der Jahre buchstäblich Zehntausende von CNC-Maschinen miteinander verbunden und so etwas wie Betriebsgeheimnisse angesammelt haben beste Weg, um diese Altgeräte zu verbinden.“
Das erste Ziel, wenn man zu einem neuen Kunden gerufen wird, ist zu verstehen, was er oder sie will. Versucht diese Person nur, Daten aus der Fabrikhalle hochzuladen, damit jeder weiß, was vor sich geht?
„Es geht nur darum, welches Problem Sie zu lösen versuchen“, sagte Carpenter. „Und dann geben wir Ihnen die Grundlagen für den Anfang. Die meisten Fabriken haben die dort vorhandenen Daten nicht vollständig gewürdigt. Sie krabbeln gerade. Ich werde in Geschäfte gehen und sie bemitleiden, weil sie noch nicht einmal die Kriechphase erreicht haben.“
Carpenter erinnerte sich an einen Kunden, bei dem das Management grundlegende Transparenz wünschte – Daten aus dem, was in der Werkstatt vor sich ging. Und Fabrikarbeiter wehrten sich dagegen, die Daten zu sammeln, aus Angst, Big Brother könnte sie beobachten.
Carpenter überließ das Problem der Ladenleitung. Aber er erkannte, dass die Arbeiter keine Wahl hatten. Er wusste, dass Betriebsleiter nach Daten suchten, um die Produktion zu messen und Prozesse zu verbessern, und nicht als Big-Brother-Taktik. Leider hatte das Management seine Mitarbeiter nicht auf den Umzug vorbereitet.
„Es öffnet so vielen Augen auf so vielen Ebenen, aber Ihre Mitarbeiter müssen auf den Wandel vorbereitet sein“, sagte er.
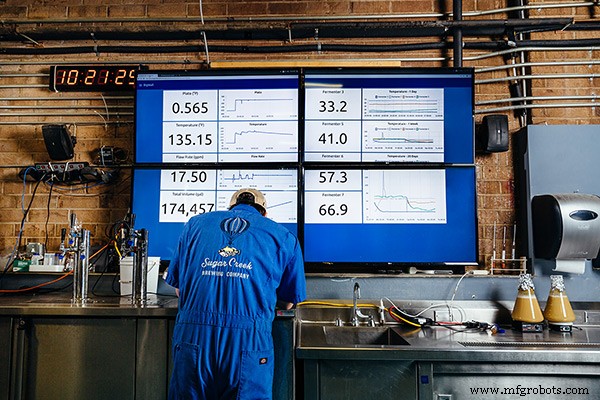
Sobald die Grundlagen verfolgt sind – schneiden wir? Wenn wir schneiden, ist es bei 100 Prozent? Und wenn nicht, befinden wir uns in einem reduzierten Produktionsmodus? – und die Daten werden in die Echtzeit-, Maschinendaten- und Kommunikationsplattform von Excellerant eingespeist, es ist möglich, unzählige Sensoren und Wandler hinzuzufügen, um mehr Daten zu erhalten.
Sensoren können integriert werden, um Temperatur, Vibration, Druck, Durchfluss, Konzentration und mehr zu messen.
„Man muss entscheiden, was wichtig ist“, sagte Carpenter. „Wir können alle Arten von Daten von einem Punkt in einem Fertigungsbereich sammeln. Es gibt eine riesige Menge an Daten, wenn Sie in die Vibrationsanalyse und Werkzeugbrüche einsteigen. Die Liste geht weiter und weiter.“
Es gibt immer eine Möglichkeit, mehr Daten zu sammeln, aber manchmal werden die Kosten unerschwinglich, sagte er. Der Ladenbesitzer muss festlegen, wie viel er für einen Sensor ausgeben möchte, um seine Daten auf die nächste Ebene zu bringen.
„Wenn Sie dies um eine Art OEE-Projekt wickeln, ist dies normalerweise ein schneller ROI“, sagte Carpenter.
Kennen Sie die zu stellenden Fragen
„Das ist natürlich ein branchenweites Problem, aber die Fragen, die wir bekommen, lassen sich normalerweise in zwei Kategorien einteilen“, sagt Cory Weber, Senior Industrial IoT Architect bei Bosch Rexroth. „Es ist:Wie steigere ich die Qualität meiner Produktion mit IoT oder mit IIoT? Oder:Wie steigere ich meine Effizienz?
„Die andere Frage, die dabei aufgeworfen wird, lautet:Wie senke ich meine Produktionskosten?“
Neben der Hilfe bei der Beantwortung dieser produktionsbezogenen Fragen, schätzt Weber, wünschen sich 90 % der Kunden eine Echtzeit-Visualisierung und Werkzeugmaschinenüberwachung vor Ort und aus der Ferne.
„Das ist der erste Schritt, oder?“ er sagte. „Was macht meine [automatisierte Linie oder Werkzeugmaschine]?“
Die Lösung von Bosch Rexroth zum Herausholen von Daten aus Altmaschinen ist ein IoT-Gateway namens PR-21, ein kleiner Einplatinencomputer, der für industrielle Umgebungen gehärtet ist. Es verfügt auch über eine IIoT-Plattform, ctrlX CORE, um Daten abzurufen und zu verarbeiten und sie auf einem lokalen Server oder in der Cloud zu speichern.
Eine der häufigeren Anwendungen, die Weber für die Verwendung gesammelter Daten gesehen hat, ist die vorbeugende Wartung.
Intelligente, datengesteuerte Optimierungen in einem Wartungsplan sind eine Möglichkeit, Werkzeugmaschinen am Laufen zu halten und gleichzeitig die Produktionskosten durch weniger Ausschuss zu senken.
„Ich weiß, dass wir sogar in unseren eigenen Einrichtungen Dinge wie die Umstellung auf Betriebsstunden im Gegensatz zu planmäßigen [Kalender]-Wartungsarbeiten durchgeführt haben“, sagte Weber.
Bosch Rexroth hat zum Beispiel einen hydraulischen Testbereich, auf dem Arbeiter früher alle zwei Wochen die Flüssigkeit wechselten. Nachdem sie die Maschine kontinuierlich überwacht hatten, konnten sie den Zeitplan für den Flüssigkeitswechsel auf einen basierend auf der Nutzungszeit im Vergleich zur Kalenderzeit ändern.
"Wenn Sie über 50-60 Gallonen Hydraulikflüssigkeit oder mehr sprechen, kann das teuer werden", sagte er.
Andere Arten von Flüssigkeiten haben festgelegte Parameter, die für ihre optimale Verwendung erfüllt werden müssen, sei es basierend auf Konzentration, Hitzeeinwirkung oder anderen Faktoren.
„Wenn Sie regelmäßig testen können, können Sie Ihre Wartung auf Bedarf umstellen und Sie können viel Geld sparen und Ihre Qualität schützen“, sagte Weber. „Es ist ein attraktives Verkaufsargument und relativ niedrig hängende Früchte.“
Weber eignete sich in seiner Jugend Domänenkenntnisse für die Fertigung an:Sein Vater besitzt einen kleinen Fertigungsbetrieb. Seine Ausbildung liegt jedoch in der Informationstechnologie. Sowohl Kenntnisse im Fertigungsbereich als auch Datenintelligenz sind erforderlich, um von der Implementierung von Industrie 4.0 zu profitieren, sagte er.
„Sie brauchen jemanden, der den eigentlichen Prozess versteht“, sagte er. „Und jemand, der den Prozess versteht, kann sich die Daten ansehen und sagen:‚Das sieht nicht so aus, wie es aussehen soll‘.“
Sobald die Daten vorliegen, sind die Möglichkeiten endlos, je nachdem, wie viel der Benutzer sie verarbeiten möchte.
Wenn ein Ladenbesitzer das Glück hat, jemanden mit echtem Data-Science-Hintergrund zu haben, kann er sich sogar an künstliche Intelligenz wagen.
„Es geht darum, genügend Daten zu sammeln, um sie wertvoll zu machen, und dann, und ich kann das nicht genug betonen, zu wissen, welche Fragen man den Daten stellen möchte“, sagte er.
Die datenbezogenen Ratschläge von Weber gelten natürlich sowohl für neue als auch für ältere Maschinen. Data Mining für Smart Operations gilt für beide.
Automatisierungssteuerung System
- Digitale Zwillinge können der intelligente Vorsprung für das IoT im Fertigungssektor sein – Teil 2
- So sammeln Sie Daten aus Legacy-Systemen, um den Betrieb zu verbessern
- Roboterschweißen:Können Sie den ROI für Kleinserienproduktionen ermitteln?
- ABB pilotiert Automatisierungslösung für Rechenzentren
- Arch Systems arbeitet mit Flex für die Transformation von Fertigungsdaten zusammen
- Smart Home-Upgrades für modernes Wohnen
- Altgeräte und IIoT:Können Sie einem alten Hund neue Tricks beibringen?
- Wie Hersteller Analytics für ein besseres Kundenerlebnis nutzen können
- Industrielle Automatisierung macht Platz für Informationsautomatisierung
- Drei Möglichkeiten, wie KI Fertigungsabläufe verbessert