Was ist Prozessplanung | Prozessplanungsschritte, Typen, Vorteile
In diesem Artikel erfahren Sie mehr über Was ist Prozessplanung ? Was sind die Anforderungen? Was sind die Prozessplanungsschritte für diesen Prozess? , Typen , Vorteile , Nachteile und die Sequenz der Aktivitäten enthalten. Beginnen wir mit der Definition .
Was ist Prozessplanung?
Prozessplanung ist das Verfahren, das verwendet wird, um eine detaillierte Liste der Herstellungsvorgänge zu erstellen, die für die Herstellung eines Teils oder Produkts erforderlich sind. Es ist die Verbindung zwischen Produktdesign und Produktherstellung.
Die Prozessplanung legt eine effiziente Abfolge von Arbeitsgängen fest, wählt geeignete Ausrüstung und Werkzeuge aus und spezifiziert ihre Arbeitsgänge so, dass das Produkt alle in der Spezifikation festgelegten Anforderungen erfüllt. Gleichzeitig wird der Prozess bei minimalen Kosten und maximaler Produktivität durchgeführt.
Grundsätzlich gibt es zwei Möglichkeiten, Prozesspläne zu erstellen. Sie sind :
1. Manuelle Prozessplanung und 2. Computergestützte Prozessplanung
ANFORDERUNGEN AN DIE PROZESSPLANUNG
Ein halbwegs guter Ablaufplan muss folgende Anforderungen erfüllen:
1. Eine kurze Beschreibung des zu fertigenden Auftrags, die dessen Dienstleistungsfunktion klar und umfassend definiert.
2. Spezifikationen und Normen, die die Servicefunktion festlegen.
3. Arbeitszeichnungen des Auftrags mit vollständiger Spezifikation.
4. Zeichnung des Rohlings.
5. Daten über die Menge der in einem Zeitraum zu fertigenden Teile. Ersatzteile für jede Einheit erforderlich.
6. Gesamtmenge der in einem Zeitraum zu fertigenden Teile.
7. Ausrüstungsdaten, die Spezifikationen und Kapazitätsdaten von Werkzeugmaschinen und anderen verfügbaren Ausrüstungen enthalten, die Daten bezüglich der Anordnung und Beladung der Ausrüstung in der Werkstatt.
8. Bedingungen, unter denen Produktionstechnik und Fertigung organisiert und durchgeführt werden sollen, d. h. ob eine neue oder bestehende Anlage, vorhandene Ausrüstung in der Anlage, Möglichkeit der Beschaffung neuer Ausrüstung usw.
9. Standort der Anlage.
10. Verfügbarkeit von Arbeitskräften, um die Anlage zu besetzen.
11. Datum des Arbeitsbeginns und Lieferdatum.
Nachdem Sie die grundlegenden Anforderungen verstanden haben, geht es als Nächstes um verschiedene Schritte in der Prozessplanung .
Prozess Planungsschritte
Der Zweck der Prozessplanung besteht darin, den besten Prozess zu bestimmen und zu beschreiben, der zur Herstellung eines Teils erforderlich ist. Um diese Ziele zu erreichen, können die folgenden Prozessplanungsschritte befolgt werden:
1. Kennenlernen der Servicefunktion des Teils.
2. Untersuchung und kritische Analyse der Herstellungsspezifikationen und verschiedener Standards, z. B. Genauigkeit, Leistung, Effizienz usw., die die Servicefunktion definieren.
3. Sich mit der Jahresproduktion des Produkts vertraut machen.
4. Die Arbeitszeichnungen zu studieren und kritisch zu analysieren, um zu sehen, ob es in jeder Hinsicht machbar ist, das Teil herzustellen, und alle Fehler in den Zeichnungen aufzudecken und zu korrigieren.
5. Festlegen, welche Teile hergestellt und welche Teile mit vollständiger Identifizierung und erforderlicher Menge gekauft werden müssen.
6. Erstellen einer Liste von Rohstoffen in der richtigen Qualität und Menge, die von außen gekauft werden sollen, unter Angabe ihrer Form, Größe und besonderen Eigenschaften.
7. Auswahl des wirtschaftlichsten Verfahrens zur Gewinnung der Rohlinge und Ermittlung der zu fertigenden Stückzahlen zur Kalkulation.
8. Bestimmung des wirtschaftlichsten Verfahrens zur Herstellung der Teile unter Berücksichtigung der aktuellen Produktionsverpflichtungen, des Liefertermins, der zu produzierenden Menge und des Qualitätsstandards.
9. Bestimmung der besten Arbeitsfolge für jedes Teil in einem bestimmten Prozess.
10. Auswahl der Werkzeugmaschinen, die die Operationen mit der erforderlichen Genauigkeit ausführen.
11. Um andere Zubehörteile und Ausrüstungen wie Vorrichtungen, Vorrichtungen, Matrizen, Lehren usw. auszuwählen, die möglicherweise erforderlich sind, um eine höhere Produktionsrate zu erzielen.
12. Anlagen und Arbeitsplätze auslegen, Maschinenbelastungen berechnen und notwendige Korrekturen im Prozess vornehmen.
13. Den Prozess zu überarbeiten, um alle Fehler und Mängel zu korrigieren, die entdeckt wurden, als der Prozess in der tatsächlichen Produktion realisiert wurde.
14. Zur Bestimmung der Inspektionsstufen, des Inspektionsverfahrens und der Grenzlehren, die für die verschiedenen Herstellungsstufen erforderlich sind, um eine genaue und schnellere Inspektion zu ermöglichen.
15. Bestimmung der Rüstzeit und Standardzeit für jeden Vorgang und Festlegung der Zahlungsrate.
16. Um die Art der Arbeit für die erfolgreiche Ausführung der Arbeit zu bestimmen.
17. Um die geschätzten Kosten des Produkts zu bestimmen, um zu sehen, ob es auf dem Verkaufsmarkt vervollständigt wird oder nicht.
Es ist erwähnenswert, dass die Prozessplanung ein dynamischer Prozess zur Vereinfachung der Verarbeitung unter Berücksichtigung des technologischen Wandels ist und die Planer aufgefordert sind, den Produktionsablauf in der Fertigung zu analysieren.
Einige der vorgenannten Schritte der Prozessplanung, die einer weiteren Erläuterung bedürfen, werden im Folgenden näher ausgeführt.
Herstellungsspezifikationen : Das Hauptdokument, in dem Fertigungsspezifikationen aufgeführt sind, ist die Detailzeichnung. Die Zeichnung legt fest:
1. Maß- und Bearbeitungsgenauigkeit mit zulässiger Abweichung von der richtigen geometrischen Form.
2. Genauigkeit in der Zuordnung verschiedener Oberflächen mit zulässiger Abweichung.
3. Orte, die einer Wärmebehandlung unterzogen werden, und Art der erforderlichen Wärmebehandlung. 4. Oberflächenqualität.
5. Bearbeitungsverfahren, das erforderlich ist, um die angegebene Oberflächengüte zu erhalten, falls erforderlich.
6. Stellen der Schutzbeschichtung mit Art und Dicke dieser Beschichtung. 7. Aufnahmeort für Maßmessungen am Fertigteil. 8. Spezielle Inspektionsverfahren, wie Röntgenaufnahmen, hydraulische Tests, falls erforderlich.
Schließlich sollten die Spezifikationen mit dem Bearbeitungsprozess und der Inspektion so weit wie möglich abgestimmt werden. Falls erforderlich, können geringfügige Änderungen oder Änderungen vorgenommen werden, um die Planung erfolgreich zu machen.
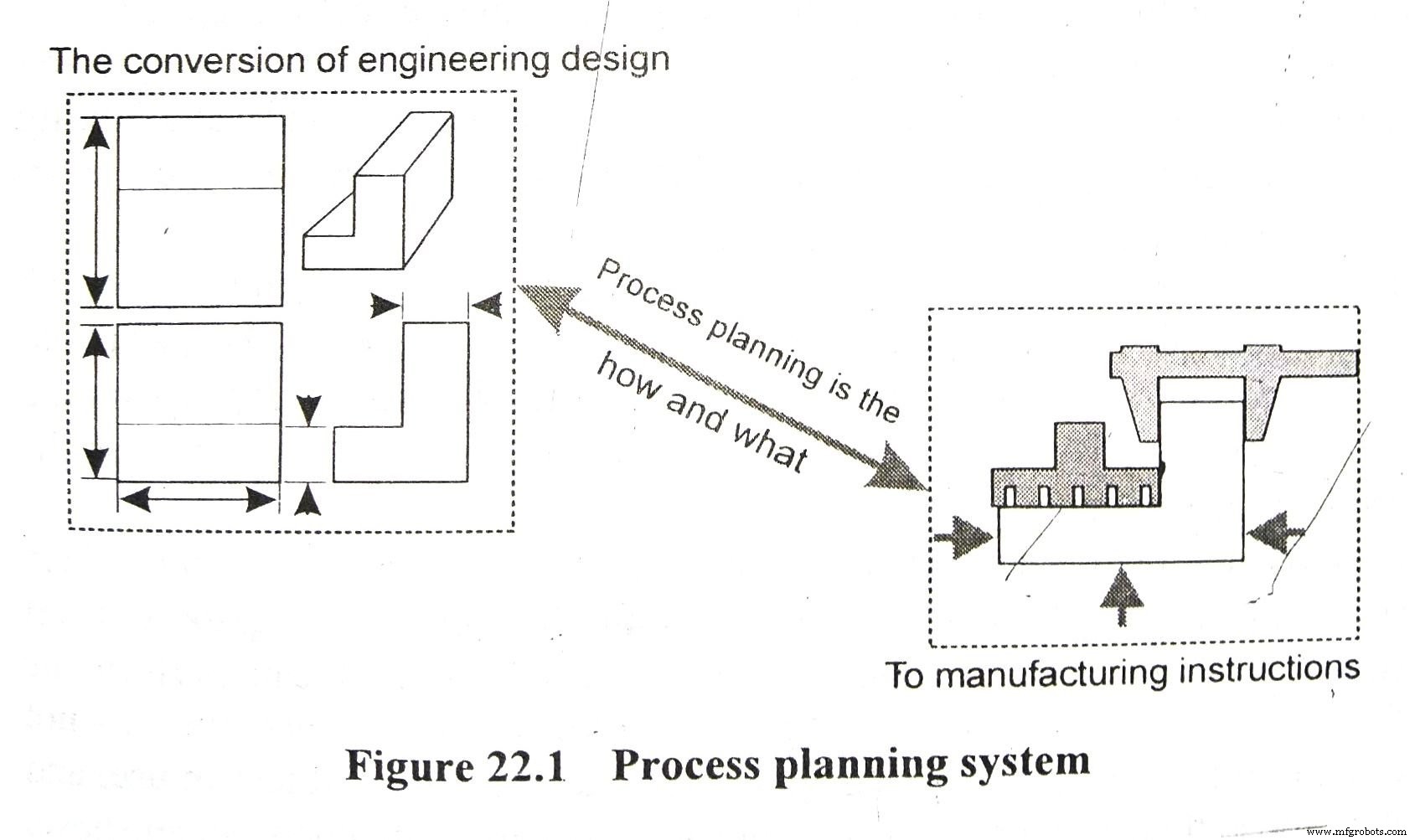
Bestimmung des Rohlings : Die Prozessplanung beginnt eigentlich schon bei der Rohlingsauswahl. Die Rohlingsgröße und die Spezifikationen des fertigen Teils hängen zusammen und bestimmen den allgemeinen Ablauf der Bearbeitungs- und Endbearbeitungsvorgänge.
Die herstellungsbedingte Genauigkeit des Rohlings und die Vorgaben des fertigen Maschinenteils bestimmen den groben Ablauf des Bearbeitungsprozesses und seine Unterteilung in Schrupp-, Vorschlicht- und Schlichtoperationen.
Auswahl an Werkzeugmaschinen : Der nächste Schritt der Prozessplanung ist die Auswahl der Werkzeugmaschinen, die maßgeblich von der Wahl der Methode oder des Prozesses zur Bearbeitung eines Teils bestimmt wird. Mit anderen Worten, Prinzipien, die Bearbeitungsprozesse regeln, sollten die Grundlage für die Auswahl von Werkzeugmaschinen sein. Obwohl es schwierig ist, eine definitive Regel für die Auswahl der Werkzeugmaschine für jede Art von Bearbeitung zu formulieren, müssen die folgenden Faktoren bei der Auswahl einer Werkzeugmaschine für einen bestimmten Vorgang berücksichtigt werden:
1. Größe, Form und Material des Werkstücks.
2. Genauigkeit und Oberflächenbeschaffenheit erforderlich.
3. Erforderliche Leistung und Produktionskapazität der Werkzeugmaschine.
4. Leistung der Werkzeugmaschine, um zu wissen, ob sie zur Durchführung der Operation ausreicht oder nicht.
5. Durchführung der Operation, um zu wissen, ob sie wirtschaftlich ist oder nicht. 6. Einfache und bequeme Bedienung der Werkzeugmaschine.
Verfügbarkeitsdiagramme : Die Verfügbarkeitstabelle ist eine Liste von Werkzeugmaschinen, geordnet nach ihren Klassen (d. h. klassifizierte Liste), z. B. Motordrehmaschinen, Revolverdrehmaschinen, Automaten und dergleichen, mit Angabe ihrer Identifikations- und Modellnummer, ihres Standorts, ihres allgemeinen Zustands, ihrer verfügbaren Werkzeuge und ihrer Schnittgeschwindigkeiten und Vorschübe usw. Bei neuen Werkzeugmaschinen werden jedoch Schnittgeschwindigkeiten und Vorschübe dem beiliegenden Katalog entnommen. Dieses Verfügbarkeitsdiagramm ist eine Notwendigkeit bei der Auswahl von Werkzeugmaschinen für ein neues Produkt in einer bestehenden Anlage.
Maschinenbelastungsdiagramme zeigt an, welche Maschine im Leerlauf bleibt und welche geladen ist. Dementsprechend wählt der Prozessplaner die bestimmte Werkzeugmaschine aus, die zur Durchführung des Bearbeitungsvorgangs verwendet werden kann. Der Prozessplaner kümmert sich nicht so sehr um das Maschinenlastdiagramm wie der Produktionsplaner.
Leistungsdiagramme : Das Fähigkeitsdiagramm kann als ein Diagramm definiert werden, das die Fähigkeit einer Werkzeugmaschine zeigt, die Arbeit zu erledigen. Das Fähigkeitsdiagramm zeigt, wie viel seiner Nennkapazität eine Werkzeugmaschine ihre Funktion zufriedenstellend ausführen kann. Eine Werkzeugmaschine bleibt, wie jede andere Maschine auch, durch Verschleiß im Gebrauch nicht mehr im gekauften Zustand und verliert auf Dauer an Genauigkeit. Das Fähigkeitsdiagramm, das den aktuellen Zustand der Maschine zeigt, dient dem Prozessplaner als Leitfaden für die Auswahl der richtigen Maschinen.
PLANUNG DES BETRIEBSABLAUFS
Die Bestimmung der optimalen Arbeitsfolge ist einer der wichtigsten Schritte im Planungsprozess und bei der Realisierung eines produktionsgerechten Produkts. Sowohl die Produktkosten als auch die Produktqualität hängen eng mit dem Arbeitsablauf zusammen. Eine unterschiedliche Abfolge der durchgeführten Operationen führt zu unterschiedlichen Betriebszeiten, unterschiedlichen Transportzeiten zum Arbeitszentrum, unterschiedlichen Werkzeugen im Hinblick auf unterschiedliche Positionierungs- und Spannflächen.
Wird für ein Produkt eine neue Anlage errichtet, hat der Prozessplaner viel mehr Freiheiten bei der Bestimmung des für den Zweck am besten geeigneten Arbeitsablaufs. Bei einer bestehenden Anlage ist die Arbeitsfolge für ein neues Produkt anhand der vorhandenen Ausrüstung und des Beladungszustandes der Ausrüstung festzulegen. Im letzteren Fall müssen dem Prozessplaner folgende Informationen zur Verfügung gestellt werden:
- Liste der verfügbaren Maschinen.
- Liste verfügbarer Allzweckwerkzeuge.
- Fähigkeit der Ausrüstung.
- Maschinenbelastungsdiagramme.
- Standarddaten.
In jedem Fall gibt es jedoch einige Grundprinzipien, die bei der Planung des optimalen Arbeitsablaufs beachtet werden müssen . Diese sind:
1. Zunächst sollten die Bezugsflächen sorgfältig ausgewählt werden. Die Auswahl des Datums beeinflusst alle nachfolgenden Bearbeitungsvorgänge und Kontrollen. Nur bei der Erstbearbeitung sollte als erste Rüstbezugsfläche eine Fläche gewählt werden, die unbearbeitet bleiben soll. In den nachfolgenden Arbeitsgängen dürfen nur bearbeitete Flächen als Einrichtbezug dienen.
2. Oberflächen, deren Bearbeitung die Steifigkeit des Werkstücks nicht nennenswert verringert, sollten früher in der Folge bearbeitet werden.
3. Interne Operationen werden vor externen Operationen durchgeführt. Dies ist keine Regel, die immer eingehalten werden muss. Der Haupt-Grund zur Durchführung interner Vorgänge früh ist, dass innere Oberflächen bei der Materialhandhabung und nachfolgenden Prozessen weniger wahrscheinlich beschädigt werden, sodass ihre Oberflächen häufig ein besseres Mittel zum Halten des Werkstücks bieten und somit dazu beitragen, die Konzentrizität zwischen Innen- und Außendurchmesser sicherzustellen.
4. Der Vorgang in der Sequenz sollte mit dem Entfernen der größten Metallschicht beginnen . Durch das Entfernen dicker Schichten durch schwere Schnitte werden innere Defekte in den Rohmaterialien (normalerweise Guss- oder Schmiedeteile) viel leichter sichtbar als bei leichten Schnitten. Außerdem wird das Werkstück von inneren Spannungen befreit, wodurch die Gefahr des Verziehens in nachfolgenden Arbeitsgängen beseitigt wird.
Die großen Schnitt- und Klemmkräfte, die mit einem starken Schnitt verbunden sein können, beeinträchtigen die Genauigkeit der fertigen Oberflächen eines anderen Teils desselben Werkstücks und erfordern Maschinen, die für Schruppoperationen vorgesehen sind. Darüber hinaus sind schwere Schnitte mit groben oder groben Oberflächen normalerweise schneller mit weniger teuren Handwerkern als feine Oberflächen.
5. Arbeitsgänge, bei denen aufgrund oben genannter Fehleraufdeckung mit erhöhtem Ausschuss zu rechnen ist, sollten möglichst nahe am Beginn des Maschinenablaufs durchgeführt werden. Es ist immer von Vorteil zu erfahren, dass das fehlerhafte Material so schnell wie möglich mit geringsten Investitionen in Nebenprozesse bearbeitet wird.
6. Endbearbeitungen sollten am Ende der Arbeitsfolge durchgeführt werden, um die Gefahr zu verringern, dass fertige Oberflächen beschädigt werden, ihre Abmessungen und Koordination in Bezug auf andere Oberflächen des Teils geändert werden.
7. Schrupp- und Schlichtoperationen sollte auf separaten Maschinen durchgeführt werden, damit die Genauigkeit der für die Endbearbeitung vorgesehenen Maschinen nicht durch schwere Lasten bei Schrupparbeiten gestört wird.
8. Inspektionsphasen sollte (a) eingeführt werden nach dem Schruppen, (b) vor Operationen, die in anderen Geschäften und Abteilungen durchgeführt werden sollen, (c) vor mühsamen und wichtigen Operationen (z. B. vor der Vorbereitung von Bezugsflächen) und danach und (d) nach der Laserbearbeitung.
9. Die Reihenfolge der Bearbeitungsoperationen sollte mit Wärmebehandlungsoperationen abgestimmt werden die bei der Herstellung von Maschinenteilen von entscheidender Bedeutung sind. Die Verformung des Arbeitsplatzes nach der Wärmebehandlung erfordert eine Erhöhung der Bearbeitungszugaben für nachfolgende Operationen für die notwendige Korrektur der geometrischen Form des Teils durch Bearbeitung.
10. Die Materialhandhabung ist eine Notwendigkeit für jede produktive Tätigkeit, da sie sich auf die Bewegung von Rohstoffen, Teilen in Bearbeitung, Fertigwaren, Verpackungsmaterialien und die Entsorgung von Abfällen bezieht. Somit Arbeitsablauf und Materialhandling sind eng miteinander verbunden. Dies ist ein lukrativer Bereich für mögliche Kostensenkungen und macht einen großen Teil der Herstellungskosten aus. Daher geht der moderne Trend dahin, das Handhabungssystem wo immer möglich zu mechanisieren.
11. Das Warten von Materialien in den Lagern sowie in der Verarbeitung sollte möglichst vermieden werden, da es mit unterschiedlichen Kostenparametern verbunden ist. Sie befinden sich daher so weit wie möglich in der Nähe der Verwendungsstelle für minimale Kosten .
Die Operationsfolge ist nicht starr. Sie variiert von Produkt zu Produkt und sogar im selben Produkt. Es gibt immer Spielraum für Verbesserungen und es sollte kontinuierlich überprüft werden, um bessere Methoden zu entwickeln, die Produktivität zu steigern und die Kosten zu senken.
Prozess Planungsblatt
Das Prozessplanungsblatt ist ein detaillierter Datensatz, in dem alle Informationen zu verschiedenen Arbeitsgängen, die zur Herstellung eines Teils erforderlich sind, in tabellarischer Form aufgelistet sind. Dies wird auch als Analyseblatt bezeichnet , Anleitung , Arbeitsblatt oder Prozessentwurfsblatt . Ein Beispiel für ein Prozessblatt finden Sie in Tabelle 22.1.
Die Beschreibung der im Prozessblatt angegebenen Vorgänge und ihrer Elemente sollte äußerst präzise, aber umfassende Informationen darüber geben, was zu tun ist und warum. Aus den Daten sollte klar hervorgehen, wie und womit die Arbeit erledigt werden soll und möglichst mit welchem Zeitaufwand.
Die Form solcher Blätter kann für unterschiedliche Produktionsbedingungen variieren. Der Charakter eines Prozessblatts hängt hauptsächlich vom Produktionsumfang und dem Bedeutungsgrad des herzustellenden Produkts ab. Darüber hinaus werden unterschiedliche Arten von Blechen in Fertigungskonzepten verwendet, die bereits in Betrieb sind, und in Organisationen, die neue Anlagen entwerfen.
In den meisten Fällen sind jedoch folgende Informationen in Prozessblättern aufgeführt:
1. Informationen zum Werkstück mit Name, Zeichnung und ggf. Servicefunktion.
2. Angaben zum Rohling wie Material, Rohteilgröße bei Verwendung als Rohling, Zeichen etc.
3. Beschreibungen und Nummern der Operationen und ihrer Elemente.
4. Angaben zu den Fertigungsmitteln wie Maschinenzubehör, Werkzeuge, Hilfseinrichtungen etc.
5. Daten zu Vorrichtungen, Vorrichtungen und Werkzeugen wie Beschreibung, Größen oder Artikelnummern.
6. Elemente der Standardzeit wie Rüstzeit, Bearbeitungszeit und Bearbeitungszeit usw.
7. Arbeitsbewertung des Arbeiters für jeden Vorgang.
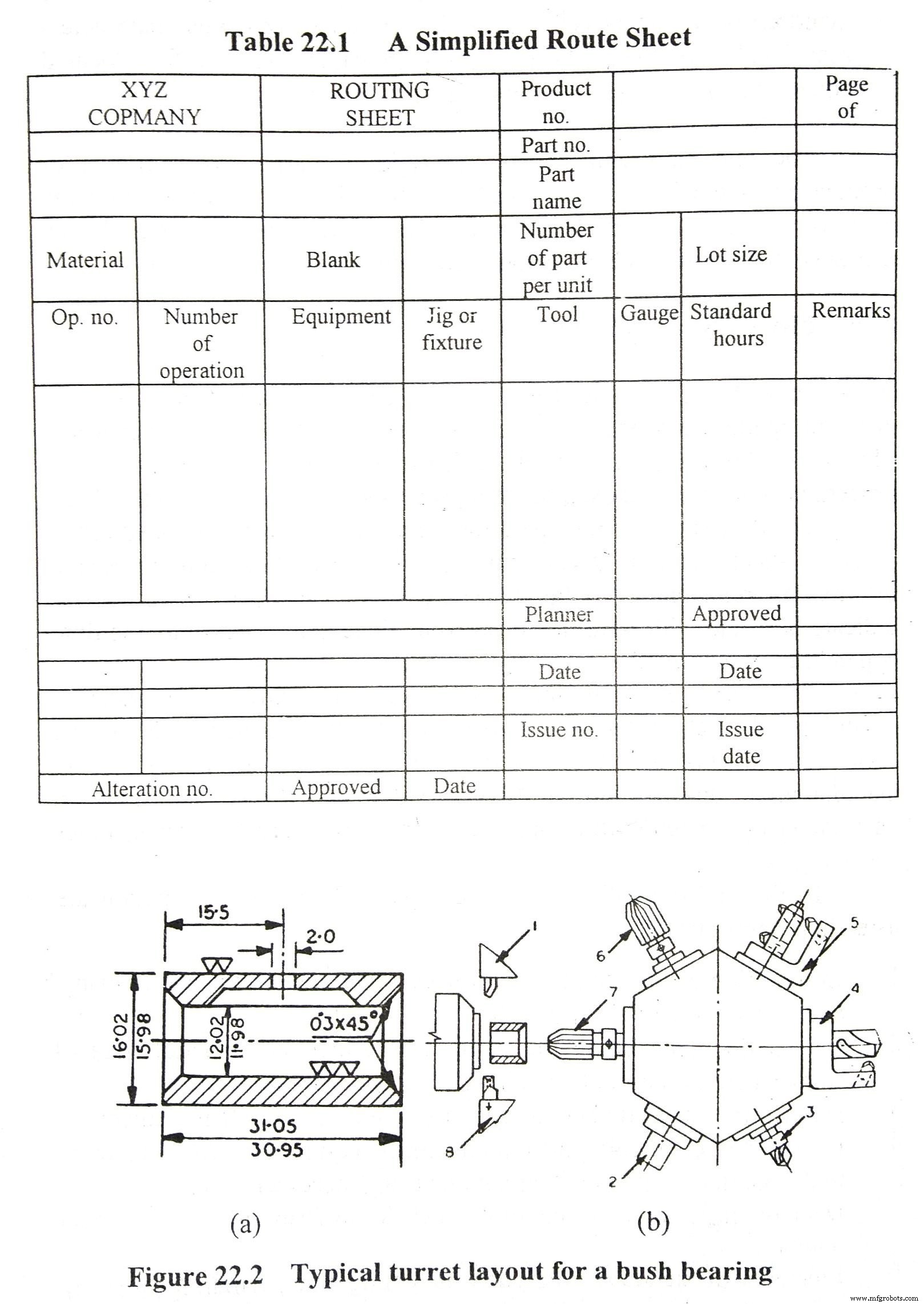
Bei der Planung von Fertigungsprozessen für spanabhebende Bearbeitungen werden häufig Arbeitsgangskizzen für verschiedene Arbeitsgänge gezeichnet, wie in Abb. 1 dargestellt. 22.2. Die zu bearbeitenden Oberflächen geben die gewünschte Toleranz an.
Ein Beispiel für einen Betriebsablauf
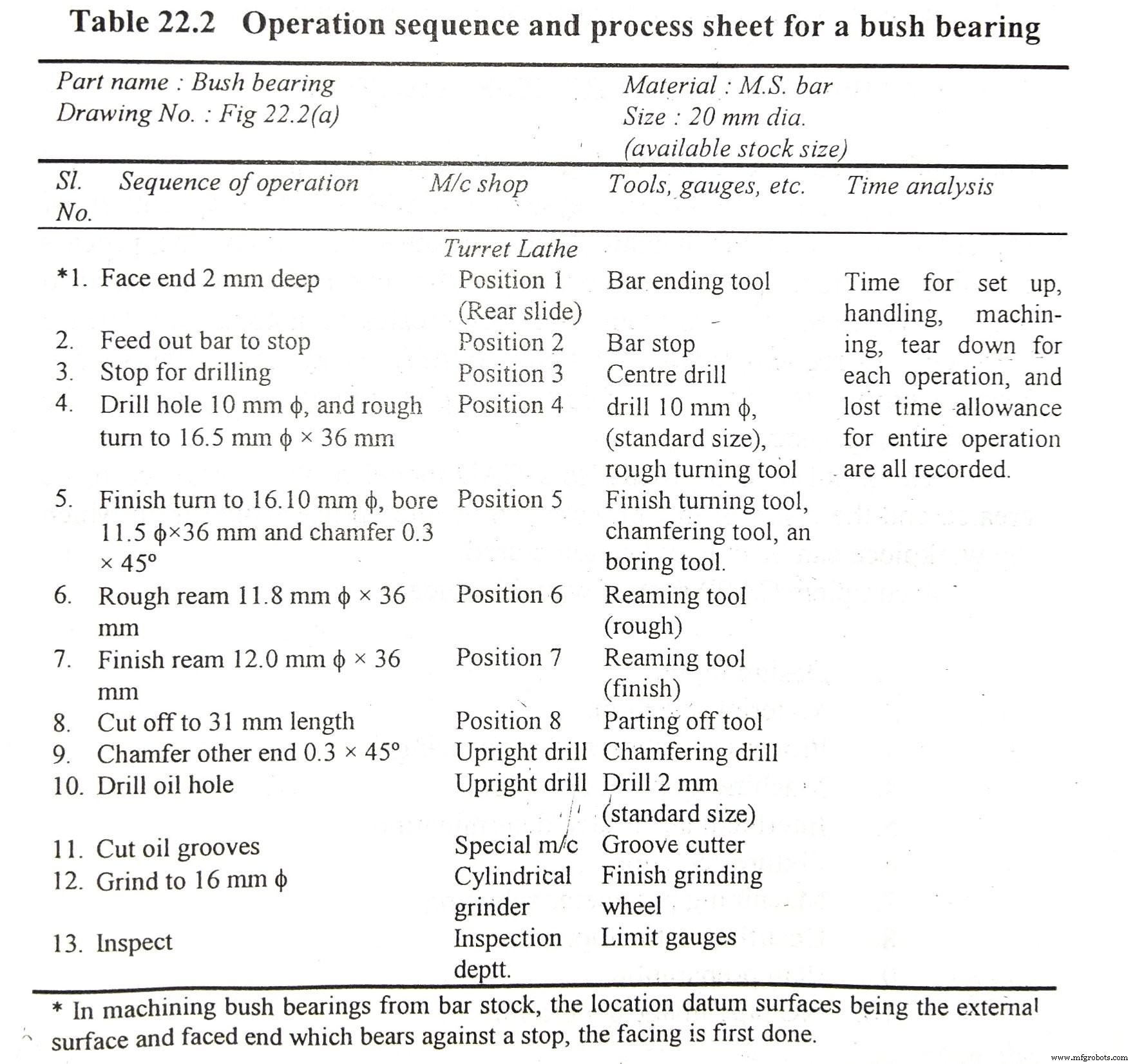
Nachteile der manuellen Prozessplanung
Die manuelle Prozessplanung (MPP) hat viele Nachteile. Sie sind:
- MPPs sind weitgehend subjektiv.
- Die Qualität des Prozessplans steht in direktem Zusammenhang mit den Fähigkeiten und Erfahrungen des Planers.
- Die Einarbeitung von Prozessänderungen ist extrem schwierig.
- Technologische Änderungen oder Änderungen der Losgrößen erfordern die Änderung des Prozessplans. MPPs reagieren langsam.
- Es ist schwierig zu überprüfen, ob der Prozessplan konsistent und optimiert ist. Wenn es nicht optimiert ist, wird es einen übermäßigen Werkzeug- und Materialbedarf spezifizieren.
- Es ist mühsam, in der großen Menge an Dokumentation des Unternehmens die Prozesspläne ähnlicher Teile manuell zu durchsuchen.
Computergestützte Prozessplanung
Computergestützte Prozessplanung (CAPP) ist zum wichtigsten Bindeglied zu integrierten CAD/CAM-Systemen geworden. CAPP ist die Anwendung von Computern zur Unterstützung des menschlichen Prozessplaners bei der Ausführung der Prozessplanungsfunktion. CAPP reduziert nicht auch den Zeit- und Arbeitsaufwand für die Erstellung konsistenter Prozesspläne, sondern schafft lediglich eine automatisierte Schnittstelle zwischen Computer Aided Design (CAD) und Computer Aided Manufacturing (CAM), um eine vollständige Integration in das Fertigungssystem zu erreichen.
Die Eingabe dieses Prozesses ist ein CAD-Modell des zu erstellenden Werkstücks und das Ergebnis dieses Prozesses ist ein detaillierter Prozessplan, aus dem das Werkstück erstellt/hergestellt werden kann.
Ein vollständiges CAPP-System würde Folgendes umfassen:
1. Design-Eingabe.
2. Materialauswahl.
3. Prozessauswahl und Sequenzierung.
4. Maschinen- und Werkzeugauswahl.
5. Bestimmung der Zwischenoberfläche.
6. Geräteauswahl,
7. Auswahl der Bearbeitungsparameter.
8. Kosten-/Zeitschätzung.
9. Vorbereitung planen.
10. Generierung von NC-Bandbildern.
Zwei grundlegende Ansätze zur automatisierten Prozessplanung sind:
1. Variante und 2. Generativ
1 .Variantenmethode
Variantenmethode: Die Variantenprozessplanung untersucht die Ähnlichkeiten zwischen Komponenten (Teilen) und durchsucht eine Datenbank, um den Standardprozessplan für die Teilefamilie abzurufen, zu der die Komponente gehört. Der Plan wird dann abgerufen und modifiziert, um einen geeigneten Plan für das neue Teil zu erstellen.
Beim Variantenansatz wird der Prozessplan in zwei Arbeitsschritten erstellt. Sie sind :
1. Vorbereitungsphase und 2. Produktionsphase.
Vorbereitung Stufe
In der Vorbereitungsphase die vorhandenen Bauteile werden kodiert, klassifiziert und in Teilefamilien gruppiert. Die Klassifizierung und Codierung bietet eine relativ einfache Möglichkeit, Ähnlichkeiten zwischen Teilen zu identifizieren. Teilefamilien können danach gebildet werden, indem ähnliche Teile geclustert werden.
Es werden verschiedene Kodifizierungsschemata eingeführt. MICLASS, DCLASS, OPITZ, CODE sind einige der Klassifizierungsschemata. Nachdem Teilefamilien gebildet wurden, wird jeder Familie ein Standardplan zugewiesen. Ein Standardplan besteht aus einer Reihe von Bearbeitungsprozessen, die den gemeinsamen Satz von Prozessen zur Herstellung der Teile darstellen.
Produktion Stufe
In der Produktionsphase Das eingehende Bauteil wird anhand seiner geometrischen Merkmale oder der Verarbeitungsanforderungen codiert. Dasselbe Kodierungsschema, das in der Vorbereitungsphase verwendet wurde, wird auch hier verwendet. Der resultierende Code dient dann als Grundlage für die Zuordnung des Teils zu einer Teilefamilie.
Wenn das Kodiersystem effizient genutzt wird, sollte das Teil ähnlich zu den anderen Teilen sein, die zu seiner Familie gehören. Ein Prozessplan für das neue Teil kann erhalten werden, indem der aus der Datenbank abgerufene Standardplan (der Teilefamilie, zu der das neue Teil gehört) modifiziert wird.
2 .Generative Methode
Generative Methode: Generative Computer Aided Process Planning (GCAPP) synthetisiert Fertigungsinformationen, um einen Prozessplan für eine neue Komponente (Teil) zu erstellen. Entscheidungslogiken und Optimierungsmethoden sind im System selbst codiert, was zu minimaler oder keiner menschlichen Interaktion bei der Prozessplanung führt.
Ein generatives System erstellt aus der Konstruktionszeichnung oder einer CAD-Datei einen vollständigen Prozessplan.
Die drei Bereiche eines GCAPP-Systems sind:
1. Komponentendefinition in Bezug auf CAD-Datei. Es enthält Teilemerkmale und Teilespezifikationen.
2. Identifikation, Erfassung und Darstellung des Wissens des Prozessplaners. Dies berücksichtigt die Begründung der vom Prozessplaner getroffenen Entscheidungen über Prozessauswahl, Sequenzierung etc.
3. Kompatibilität der Planerlogik
In GCAPP werden Designspezifikationen in das System eingegeben. Die Entscheidungslogik erkennt Rohmaterial und Bearbeitungsmerkmale des Teils. Es bestimmt ferner optimale Arbeitsabläufe zusammen mit den optimalen Vorrichtungstypen und -standorten.
Nachteile der generativen computergestützten Prozessplanung
Die folgenden Nachteile werden in den GCAPP-Systemen beobachtet.
1. Eingeschränkte Nutzung bis heute. Die erforderlichen Informationen (z. B. Toleranzen) sind in der Regel nicht im CAD-Modell vorhanden.
2. Dem System muss viel Wissen hinzugefügt werden, damit es in der Lage ist, all die verschiedenen Arten von zugeführten Teilen zu handhaben.
3. Aufgrund der hohen Komplexität der Algorithmen und des enormen Rechenaufwands spezialisieren sich einige Systeme darauf, Pläne für bestimmte Geometrietypen zu entwickeln. Einige Systeme gehen so weit, die Herstellbarkeit eines Teils zu prüfen und gegebenenfalls Änderungen im Design vorzuschlagen.
Bisher haben Sie die Schritte der Prozessplanung, Definition, Arten, Abfolge von Aktivitäten, Vor- und Nachteile verschiedener Arten der Prozessplanung kennengelernt. Bitte teilen Sie diesen Artikel mit Ihren Freunden und geben Sie Ihr Feedback in den Kommentaren unten ab.
Industrietechnik
- Was sind Testtechniken:Typen, Vor- und Nachteile
- Was ist eine virtuelle Maschine – Typen und Vorteile
- Was ist Embedded System Design:Schritte im Designprozess
- Was ist Räumen? - Verfahren, Arbeiten und Arten
- Was ist Schmieden? - Definition, Prozess und Arten
- Was ist Aufkohlen? - Definition, Typen und Verfahren
- Was ist Metallguss? - Definition, Typen und Prozess
- Was sind die Hauptschritte im Bearbeitungsprozess?
- Was sind die 4 Arten von Herstellungsprozessen?
- Welche Schritte umfasst der Leiterplattenmontageprozess?