Wie wir den 3D-Druck zur Validierung der Ventildesigns und des Schemas für unser mechanisches Notfallbeatmungsgerät verwendet haben
Als die COVID-19-Pandemie Anfang 2020 in Nordamerika zu einem ernsthaften Problem wurde, gab es viele Unbekannte. Wie wurde COVID-19 verbreitet? Was waren die Symptome? Könnte COVID-19 verbreitet werden, wenn keine Symptome vorhanden waren? Gab es bleibende Nachwirkungen oder Nebenerkrankungen? Wie weit und wie schnell würde die Ausbreitung erfolgen? Würde das Tragen von Masken helfen, die Ausbreitung einzudämmen? Wann wäre ein Impfstoff fertig?
Unter all diesen Unbekannten war jedoch eine Tatsache sicher – wenn Die Ausbreitung der Pandemie und die Zunahme schwerer Fälle exponentiell, Beatmungsgeräte wären von entscheidender Bedeutung, um Patienten richtig zu behandeln. Eine weitere Gewissheit:Viele Länder, einschließlich der Heimatbasis von Protocase in Kanada, verfügten für ein solches Szenario nicht über eine ausreichende Versorgung mit Beatmungsgeräten.
In den frühen Stadien der COVID-19-Pandemie hielt die Bundesregierung Protocase aufgrund unseres Kundenstamms von Organisationen, die in den Bereichen Innovation, Medizin, Luft- und Raumfahrt und Verteidigung tätig sind, für unverzichtbar. Aber Team Protocase war nicht nur offen und bereit, kundenspezifische Teile und Gehäuse unserer Kunden herzustellen, damit sie weiterhin innovativ sein und neue Technologien entwickeln konnten, sondern wollte auch seinen Teil dazu beitragen, bei der Bewältigung der COVID-19-Pandemie zu helfen. Das Projekt? Bauen Sie ein funktionelles, tragbares Beatmungsgerät das schnell hergestellt und montiert werden konnte.
Die Herausforderung
Nachdem wir uns mit einer Gruppe medizinischer Fachleute, darunter Notärzte, Atemtherapeuten und andere, in Verbindung gesetzt hatten, um die Kriterien für ein funktionsfähiges Beatmungsgerät zu besprechen, entwarf unser Forschungs- und Entwicklungsteam das pneumatische System. Ein entscheidender Teil des Designs eines Beatmungsgeräts sind die Ventile, die zusammen mit den Abzweigrohren einen Kreislauf für die Ein- und Ausatmung bilden. Das Team musste drei gängige Arten von Ventilen beschaffen :ein Rückschlagventil, ein einstellbares Druckrückschlagventil und ein Solenoid.
Ein Problem – die kauffertigen Ventile waren außerordentlich stark nachgefragt.
„Jeder sprang irgendwie auf die Versionen dieser Teile, die für Beatmungsgeräte und all die verschiedenen Lösungen für die Pandemie geeignet wären. Es gab einige Unterbrechungen in der Lieferkette“, sagt Justin Lewis, Maschinenbauingenieur im F&E-Team von Protocase. „Nachdem wir ein wenig damit zu kämpfen hatten, die benötigten Ventile zu bestellen, entschieden wir uns, unsere eigenen herzustellen. Die am Ende resultierenden Ventile sind im Wesentlichen die Version der Teile, die wir mit dem, was wir im Haus hatten, schnell herstellen konnten, ohne sich mit Vorlaufzeiten auseinandersetzen zu müssen.“
Die Entwürfe für die Ventile kamen schnell zusammen, da das Gesamtdesign (und zwingende Kriterien für die Funktion eines Ventils) bereits gut festgelegt und etabliert waren.
„Im Grunde erhielten wir eine Liste mit Kriterien, die von den Ärzten und Atemtherapeuten, die wir konsultierten, erfüllt werden mussten“, sagt Jordan Rose, R&D Mechanical Engineer bei Protocase. „Anhand des pneumatischen Designs des gesamten Systems kann man gewissermaßen ableiten, bei welchen Drücken diese Dinger wirken müssen. Das ist die andere Hälfte der Informationen, die wir brauchen, um fortzufahren. Wir haben uns angesehen, wie ein Rückschlagventil funktioniert und bei welchen Drücken und Durchflussraten diese Dinge funktionieren müssen, wobei wir die Mathematik verwendet haben, die wir in der Ingenieurschule gelernt hätten.“
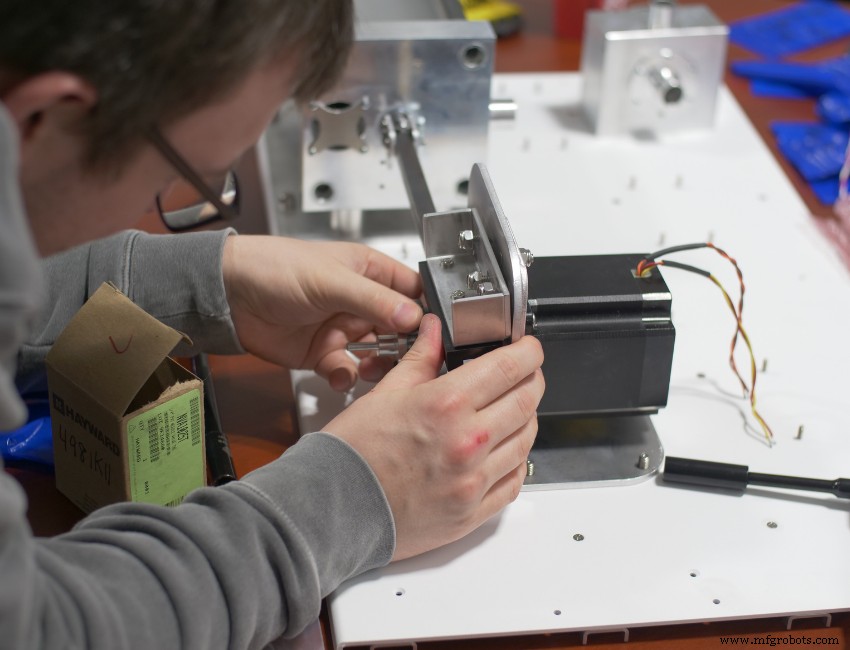
„Es ist industrielles Lego. Es geht darum, das Ganze zu sehen, alles aufgebaut aus diesen Grundbausteinen“, erklärt Lewis. „Dies sind die Grundbausteine – wir müssen sie nur bauen und in der richtigen Reihenfolge zusammenfügen, damit sie alle das Ziel erreichen.“
Nachdem die Ventildesigns gut etabliert waren und die Druck- und Durchflussanforderungen festgelegt waren, machte sich das Team an die Arbeit, die ersten Prototypen zu bauen. Für diese Aufgabe war der 3D-Druck der logische erste Schritt, da er die Abmessungen validieren und die Berechnungen für Druck und Durchflussraten verifizieren würde.
„Da der Bearbeitungsprozess wesentlich länger dauert, ist es wichtig, die Teile zuerst in 3D zu drucken, um die Spezifikationen zu bestätigen“, sagt Rose.
„Der 3D-Druck hat den gesamten Schaltplan validiert“, fügt Lewis hinzu. „So konnten wir alles zusammenbauen und sagen:‚Okay, das funktioniert‘, bevor wir all die Zeit und das Geld in den Bau der korrekt bearbeiteten Teile investierten.“
Das Team führte einige Iterationen des 3D-Drucks des Rückschlagventils und des einstellbaren Rückschlagventils durch und versuchte, das Design so weit wie möglich zu rationalisieren und sicherzustellen, dass es ordnungsgemäß funktioniert. Zum Beispiel hatte das Ventil in einer frühen Konstruktion des einstellbaren Rückschlagventils einen Kreis und einen Vorsprung auf einer Seite.
„Der Grund, warum ich das getan habe, war, um zu sehen, welche Art von Unterstützung für diesen Zirkelchef erforderlich ist. Denn sonst müssen Sie es möglicherweise darunter stützen“, sagt Rose. „Ich wollte versuchen, eventuell vorhandene Oberflächenprobleme zu vermeiden, damit der Schlauch im pneumatischen System richtig passt. Schließlich gingen wir zu einer geraden Rohrform über, die gut funktionierte.“
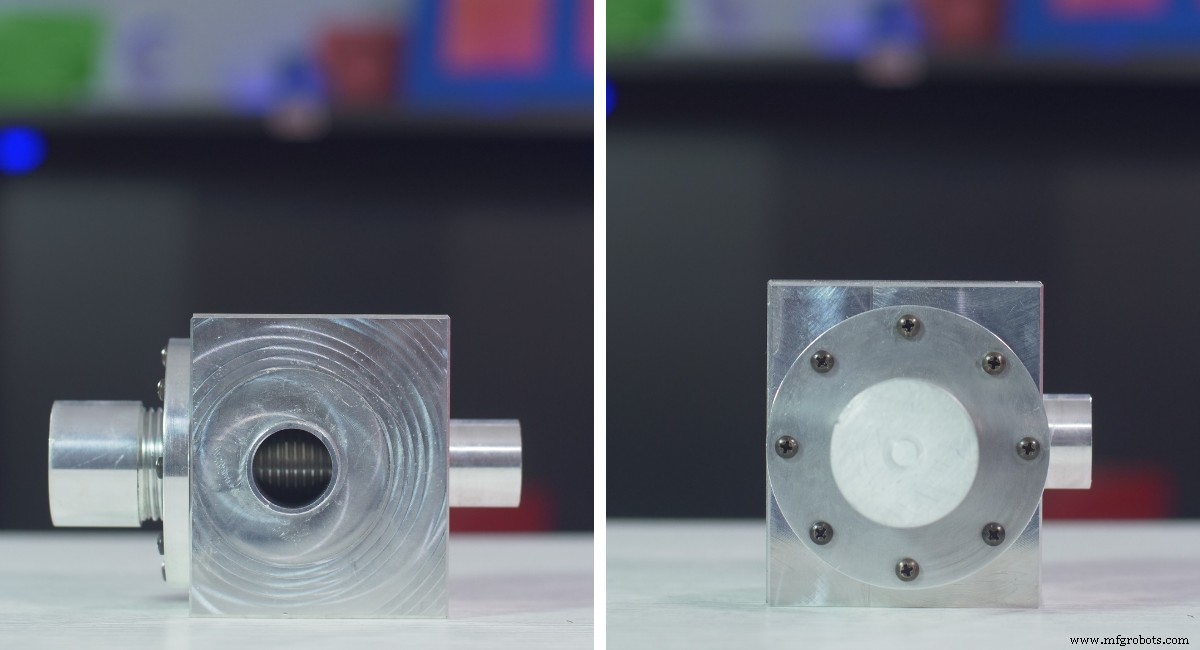
„Die Gesamttheorie war von Anfang an gut, es ging mehr darum, es richtig abzudichten und sicherzustellen, dass wir die richtigen Federn haben“, sagt Lewis.
Das einzige Ventil, das nicht als erster Prototyp in 3D gedruckt wurde, war das pneumatische Solenoid – aus gutem Grund.
„Von außen sieht es einfach aus, weil es nur ein großer Metallblock ist, aber im Inneren gibt es viele verschiedene Kammern“, erklärt Rose. „Es ist nicht etwas, das für den 3D-Druck machbar wäre.“
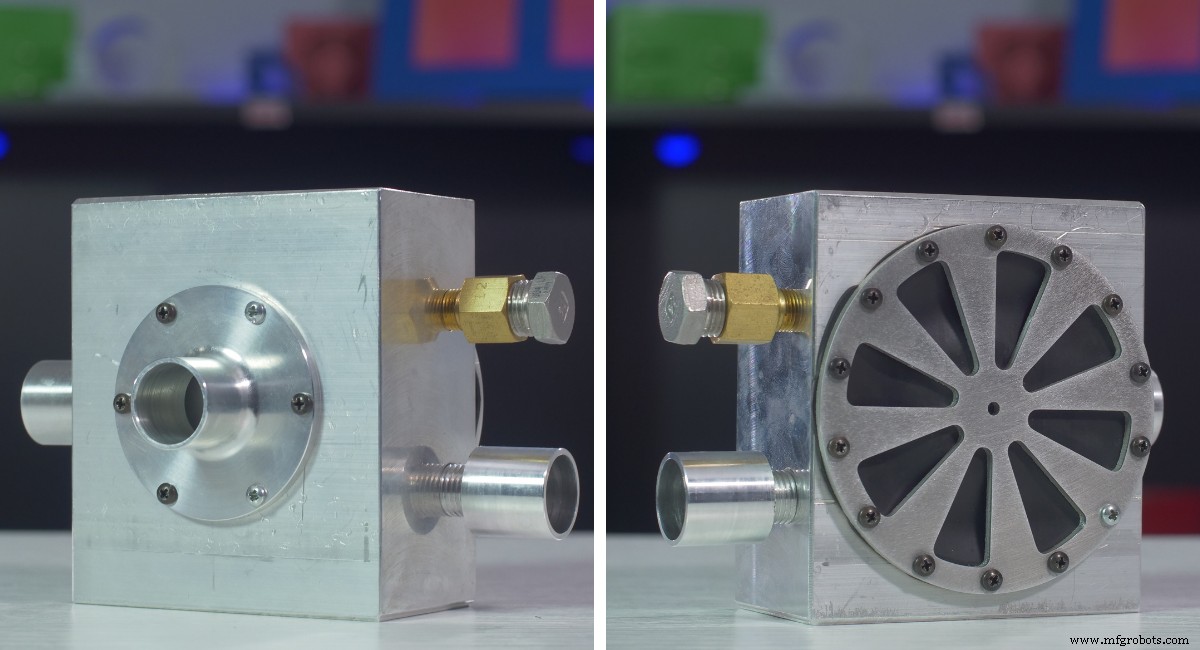
„Mit dem 3D-Druck kann es schwieriger sein, eine Wellendichtung auf dieser Art von Material herzustellen“, sagt Lewis. „Durch das Fräsen des Solenoids konnten wir ihm ein schönes Finish verleihen und eine passende Welle hineinstecken, damit alles richtig abgedichtet ist.“
Das pneumatische Solenoid umfasst alle Aspekte der kundenspezifischen Fertigung von Protocase, mit CNC-Drehteilen, gefrästen Teilen, Blechteilen, einem 3D-gedruckten Teil sowie Dichtungsmaterial. Anstatt das Gummidichtungsmaterial in eine typische Dichtung zu schneiden, schnitt das Team den Gummi mit einem CNC-Fräser in einen Kreis, um eine Rückschlagventilblase herzustellen.
Rückblick – und Ausblick
Am Ende war es enorm vorteilhaft, zuerst mit dem 3D-Druck zu beginnen, um sicherzustellen, dass die industriellen Lego-Teile zusammenpassen und wie im Schaltplan ausgelegt funktionieren, ohne wertvolle, entscheidende Zeit für die CNC-Bearbeitung aller Teile in Anspruch zu nehmen.
„Es ist einfach schön zu wissen, dass man auf dem richtigen Weg ist. Sie haben den Schaltplan, Sie setzen alles zusammen und sagen dann:‚Oh, warten Sie, das ist alles falsch angelegt.‘ Es gab Zeiten, in denen wir Anpassungen am Layout des gesamten Systems vorgenommen haben“, sagt Lewis. „Sie wollen nicht viel Geld und Zeit für bearbeitete Blöcke ausgeben, um das zu tun. Diese 3D-gedruckten Teile waren etwas undicht, aber wir wussten, dass das Gesamtsystem funktioniert, sodass wir getrost in die nächste Phase investieren konnten.“
Selbst die endgültige Version der CNC-gefrästen Ventile ist vielleicht nicht die stromlinienförmigste und vielleicht klobig im Vergleich zu den kauffertigen Gegenstücken auf dem Markt, aber dafür gibt es einen Grund, sagt Rose.
„Wir haben sie so konzipiert, dass sie unseren Möglichkeiten entsprechen, denn wenn wir jemals 2.000 davon bearbeiten müssten, könnten wir sie schnell herstellen“, erklärt er. „Wir haben aktiv versucht, nichts Ausgefallenes zu entwerfen oder die Grenzen unserer Bearbeitung zu überschreiten.“

Wie bei jedem Prototyp oder jeder Entwicklung eines Produkts kann es hilfreich sein, darüber nachzudenken, was gut gelaufen ist und was verbessert werden könnte. Alles in allem waren sich sowohl Rose als auch Lewis einig, dass das Projekt dank der flinken Fertigung, die ihnen zur Verfügung steht, um Layouts zu testen und Spezifikationen ohne Zeitverzögerungen zu bestätigen, auf solider Basis blieb.
Rückblickend sehen sie jedoch die Vorteile eines elektrischen Systems für das Beatmungsgerät. Ein System mit einem elektrischen System kann mit der Software eingeschaltet werden, wenn Sie es brauchen, und ausgeschaltet werden, wenn Sie es brauchen. Ein pneumatisches System hingegen hat ein Vakuumsystem, das schwierig sein kann.
„Diese pneumatische Magnetspule ist wie das Spielen eines Musikinstruments“, erläutert Lewis. „Es ist großartig, wenn Sie es auf dem Weg nach draußen einstellen lassen können, aber wenn sich etwas ändert, möchten Sie nicht jemanden im Krankenhaus haben, der wirklich weiß, wie man die Maschine bedient. Idealerweise möchten Sie jemanden, der den Knopf leicht einstellen kann. In Bezug auf etwas, das wir intern schnell erledigen konnten, ist das von uns entworfene und gebaute System großartig, aber was wir seit März gelernt haben, ist, dass sich die Versorgungsleitungen wieder etwas normalisiert haben und wir vielleicht mit einem elektrischen System hätten weitermachen können .“
„Das war damals das einzige, was wir nicht bekommen konnten – ein Elektromagnet“, fügt Rose hinzu. „Alle waren in Panik. Jetzt sind sie viel einfacher zu beschaffen.
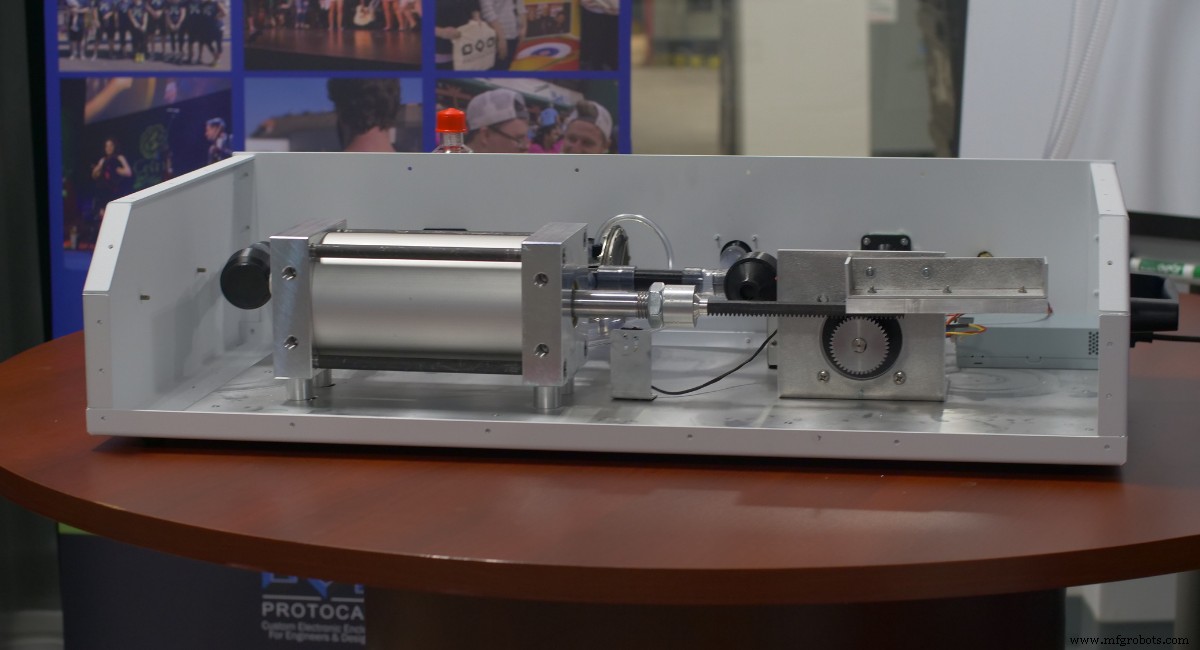
Wenn man das Gesamtbild betrachtet, hat das Beatmungsprojekt, einschließlich des Designs und der Herstellung der drei Ventile, dazu beigetragen, die Arbeit des F&E-Teams von Protocase zu formen.
„Als dieses Projekt aufkam, schien es ein globaler Notfall zu sein. Wir ließen alles andere fallen und ein Haufen von uns kam zusammen“, sagt Rose. „Was uns bei diesem Projekt klar wurde, war, dass wir unsere anderen Projekte stoppen konnten, um uns nur auf ein oder zwei Dinge zu konzentrieren und die Dinge wirklich einzugrenzen.“
Anstatt sich zu dünn zu verteilen oder sich von der Arbeit der anderen zu isolieren, konzentriert sich die Forschungs- und Entwicklungsgruppe jetzt darauf, als Team zu funktionieren.
„Wir haben konkrete Ziele, an denen wir alle gemeinsam arbeiten und unsere Ressourcen bündeln können“, erklärt Lewis. „Es hat einfach die Art und Weise verändert, wie jeder an Projekten arbeitet, wir behandeln jetzt fast jedes Projekt als eine Art Notfall. Dieses Projekt war der Auslöser für viele Verbesserungen in unserer Forschungs- und Entwicklungsabteilung.“
Industrietechnik
- Wie man die Kühlkette auf den COVID-19-Impfstoffbedarf vorbereitet
- Wie Kunstlogistik den Kunstmarkt zum Guten verändert
- Wie man sich auf die nächste Unterbrechung der Lieferkette vorbereitet
- So stellen Sie die Notfallvorsorge im Lager sicher
- Was sind die Vorteile des 3D-Drucks für Metallverarbeiter?
- Vier neue Chancen für die Aluminiumindustrie
- Was ist AutoCAD? Wie es funktioniert und wofür es verwendet wird
- Einige der für die Bearbeitung mechanischer Teile erforderlichen Messwerkzeuge
- Einsatz des 3D-Drucks in der Formenbauindustrie
- Was sind RFID-Tags? Erfahren Sie, wie RFID-Tags funktionieren, wofür sie verwendet werden und einige der Nachteile der RFID-Technologie