Warum die Anzahl der Flöten wichtig ist
Eine der wichtigsten Überlegungen bei der Auswahl eines Schaftfräsers ist die Bestimmung, welche Schneidenzahl für die jeweilige Aufgabe am besten geeignet ist. Sowohl das Material als auch die Anwendung spielen eine wichtige Rolle in diesem kritischen Teil des Werkzeugauswahlprozesses. Das Verständnis der Auswirkungen der Schneidenanzahl auf andere Werkzeugeigenschaften und wie sich ein Werkzeug in verschiedenen Situationen verhält, ist eine wesentliche Überlegung bei der Werkzeugauswahl.
Machining Advisor Pro (MAP) berücksichtigt die Schneidenzahl, wenn es Ihnen hilft, Laufparameter einzustellen.
Klicken Sie hier, um loszulegen.
Grundlagen der Werkzeuggeometrie
Im Allgemeinen haben Werkzeuge mit mehr Spannuten einen größeren Kern und kleinere Spannuten als Werkzeuge mit weniger Spannuten. Mehr Spannuten mit einem größeren Kern können je nach Anwendung sowohl Vorteile als auch Einschränkungen bieten. Einfach ausgedrückt ist ein größerer Kern direkt proportional zur Werkzeugstärke; Je größer der Kern, desto stärker ist ein Werkzeug. Ein größerer Kern wiederum verringert auch die Spannutentiefe eines Werkzeugs, wodurch der Platz für Späne eingeschränkt wird. Dies kann bei Anwendungen, die eine starke Materialabtragung erfordern, zu Problemen mit der Spanpackung führen. Diese Überlegungen führen uns jedoch nur zum Teil bei der Entscheidung, welches Tool wann zu verwenden ist.
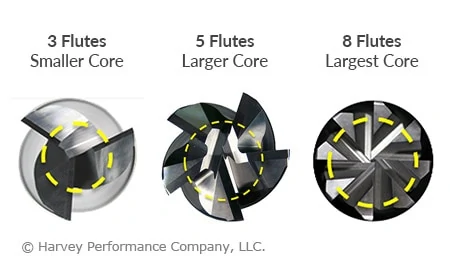
Materialüberlegungen
Traditionell gab es Schaftfräser entweder mit 2 oder 4 Schneiden. Die allgemein anerkannte Faustregel lautete, 2 Schneiden für die Bearbeitung von Aluminium und Nichteisenwerkstoffen und 4 Schneiden für die Bearbeitung von Stahl und härteren Legierungen zu verwenden. Da Aluminium- und Nichteisenlegierungen typischerweise viel weicher als Stähle sind, ist die Festigkeit eines Werkzeugs weniger von Bedeutung, ein Werkzeug kann schneller zugeführt werden und größere Materialabtragsraten (MRR) werden durch die großen Nutentäler von 2-Nuten-Werkzeugen ermöglicht. Eisenhaltige Materialien sind typischerweise viel härter und erfordern die Stärke eines größeren Kerns. Die Vorschubraten sind langsamer, was zu kleineren Spänen führt und die kleineren Rillentäler eines größeren Kernwerkzeugs ermöglicht. Dadurch können auch mehr Spannuten auf das Werkzeug passen, was wiederum die Produktivität erhöht.
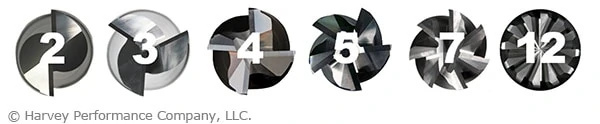
In letzter Zeit sind mit fortschrittlicheren Maschinen und Werkzeugwegen Werkzeuge mit höherer Nutenzahl zur Norm in der Fertigung geworden. Nichteisen-Werkzeuge konzentrieren sich weitgehend auf 3-Nuten-Werkzeuge, was eine höhere Produktivität ermöglicht und gleichzeitig eine ordnungsgemäße Spanabfuhr ermöglicht. Eisenwerkzeuge sind einen Schritt weiter gegangen und haben sich nicht nur zu 5 und 6 Schneiden, sondern in einigen Fällen zu 7 Schneiden und mehr entwickelt. Mit einem breiteren Härtebereich, manchmal ganz oben auf der Rockwell-Härteskala, haben viel mehr Spannuten eine längere Werkzeuglebensdauer, weniger Werkzeugverschleiß, stärkere Werkzeuge und weniger Durchbiegung ermöglicht. All dies führt zu spezialisierteren Werkzeugen für spezifischere Materialien. Das Endergebnis ist ein höherer MRR und eine gesteigerte Produktivität.
Laufparameter
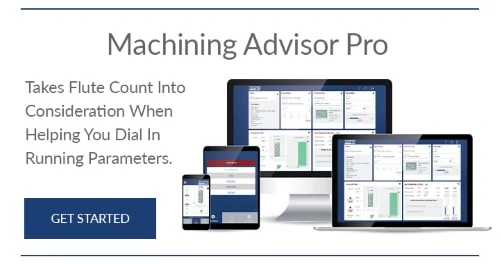
So wie Materialüberlegungen einen Einfluss auf das von Ihnen gewählte Werkzeug haben, können auch die Bearbeitungsart und die Anforderungen an die Schnitttiefe einen großen Einfluss auf die ideale Anzahl von Schneiden für Ihre Anwendung haben. Bei Schruppanwendungen können niedrigere Spannutenzahlen wünschenswert sein, um große Spanmengen mit größeren Spannuten schneller abzutransportieren. Allerdings muss ein Gleichgewicht gefunden werden, da moderne Werkzeugwege wie High Efficiency Milling (HEM) mit einem sehr kleinen Schritt und einer höheren Anzahl von Spannuten eine extreme MRR erreichen können. Im traditionelleren Sinne eignen sich höhere Schneidenzahlen hervorragend für Schlichtoperationen, bei denen sehr wenig Material entfernt wird, und eine bessere Oberflächengüte kann mit mehr Schneiden erreicht werden, ohne dass man sich so viele Gedanken über die Spanabfuhr machen muss.
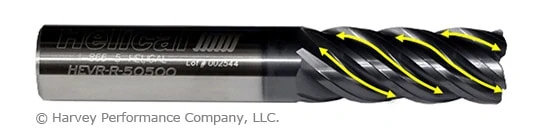
Die Nutenzahl spielt auch bei der Geschwindigkeits- und Vorschubberechnung eine große Rolle. Eine gängige Faustregel lautet „mehr Flöten, mehr Vorschub“, aber dies kann ein sehr schädlicher Irrtum sein. Obwohl dies in einigen Fällen zutrifft, ist dies kein unbegrenzt skalierbares Prinzip. Wie bereits erwähnt, begrenzt die Erhöhung der Anzahl von Rillen auf einem Werkzeug die Größe, die die Rillentäler haben können. Beim Hinzufügen eines 5 ten Schneiden zu einem 4-Schneiden-Werkzeug ergibt theoretisch 25 % mehr Materialabtrag pro Umdrehung bei entsprechend erhöhter Vorschubgeschwindigkeit, ein viel schnelleres Vorschieben des Werkzeugs kann das Werkzeug überlasten. Die Steigerung des Materialabtrags um 25 % liegt eher bei 10–15 %, da das Werkzeug in allen anderen Spezifikationen genau gleich ist. Bei Werkzeugen mit höherer Nutenzahl müssen die Drehzahlen und Vorschübe in einigen Fällen möglicherweise so stark zurückgefahren werden, dass eine niedrigere Nutenzahl sogar noch effizienter sein kann. Die richtige Balance zu finden, ist der Schlüssel in modernen Fräspraktiken.
CNC-Maschine
- Die digitale Fabrik:Was sie ist und warum sie wichtig ist
- Warum der Standort wichtig ist.
- So implementieren Sie die Multi-Faktor-Authentifizierung – und warum sie wichtig ist
- Nachfolgeplanung:Warum es wichtig ist und wann sie beginnen sollte
- Warum ist Made in USA wichtig?
- 4 Gründe, warum Gerätetests und -inspektionen wichtig sind
- Warum Druck beim Wasserstrahlschneiden wichtig ist
- Kauf eines Mobilkrans:Warum Gelände wichtig ist
- Warum ist Ausrüstung ein Vermögenswert und nicht nur ein Werkzeug?
- Warum die Kompatibilität von Atemschutzmasken und Zylindern für Pressluftatmer wichtig ist