Wie 5 große Automobilhersteller den 3D-Druck verwenden
3ERP hat viele der verschiedenen Möglichkeiten abgedeckt, wie Automobilhersteller von den Vorteilen profitieren, die der 3D-Druck in den Vordergrund stellt. Da die Technologie in der Automobilindustrie immer mehr Fuß fasst, nehmen viele Unternehmen dies zur Kenntnis, aber viele nutzen sie in unterschiedlichen Funktionen und für verschiedene Zwecke. Diese Anforderungen können alles umfassen, von Werkzeugen über Ersatzteile/Supply-Chain-Management bis hin zu Endverbrauchsteilen und sogar kompletten Autos.
Es ist interessant zu sehen, wie weit die Technologie gekommen ist, wie sie von den großen Namen der Branche eingesetzt wird und wo sie sie für ihre zukünftigen Produktionsketten sehen. Dieser Artikel soll einen Einblick in die vielen Möglichkeiten geben, wie einige der größten Automobilhersteller der Welt den 3D-Druck in ihrem Arbeitsablauf einsetzen.
BMW
Da der 3D-Druck meist für kleinere Produktionsserien verwendet wird, gibt es viel Raum für Anpassungen und zusätzliche Komplexität, indem die einzigartigen Elemente verwendet werden, die der 3D-Druck ermöglicht. BMW ist solchen Design- und Fertigungsformen nicht fremd und setzt 3D-Druck in der Vorentwicklung, Fahrzeugvalidierung und -erprobung oder in Konzept- und Showcars ein. Sie setzen die Technologie für größere Mengen ein, aber kleinere Produktionsläufe ermöglichen es ihnen, Produkte genau auf die Bedürfnisse ihrer Kunden zu personalisieren.
Das Unternehmen hat die additive Fertigung erfolgreich eingesetzt und festgestellt, dass es möglicherweise „großes zukünftiges Potenzial für die Serienproduktion und neue Kundenangebote sieht “ (laut Experten von BMW in Deutschland). Sie nutzen die Technologie, um sowohl Kunststoff- als auch Metallkomponenten zu verbessern. Sie haben vor allem mit HP zusammengearbeitet, um Produkte auf ihren großen Fertigungssystemen herzustellen.
Wie viele andere Unternehmen auf dieser Liste hat BMW es als Mittel zur Herstellung von Teilen verwendet, die andere Technologien nicht herstellen können. Ein gutes Beispiel dafür ist die obere Abdeckung des i8 Roadster. Die Herstellung der Halterung für dieses Bauteil wäre mit einem herkömmlichen Gussverfahren nicht möglich gewesen. Abgesehen von der Erweiterung der Designmöglichkeiten ist das 3D-gedruckte Autoteil haltbarer und wiegt auch weniger als frühere Iterationen.
In ähnlicher Weise stellte BMW den Formel-E-Renner iFE.20 mit einem 3D-gedruckten Kühlschaft aus Flachsfasern vor. Das Teil wurde Ende 2019 gezeigt. Flachs hat im Vergleich zu den üblichen Carbonmaterialien eine höhere Dämpfung und eine höhere Schlagfestigkeit, was auf den Stadtkursen mit ihren Bodenwellen und Leitplanken, auf denen die Formel E stattfindet, von Vorteil sein kann. Damit war es der erste BMW Rennwagen, der von einem Arbeitsteam mit Teilen aus nachwachsenden Textilfasern eingesetzt wurde, was ihn auch umweltfreundlich macht.
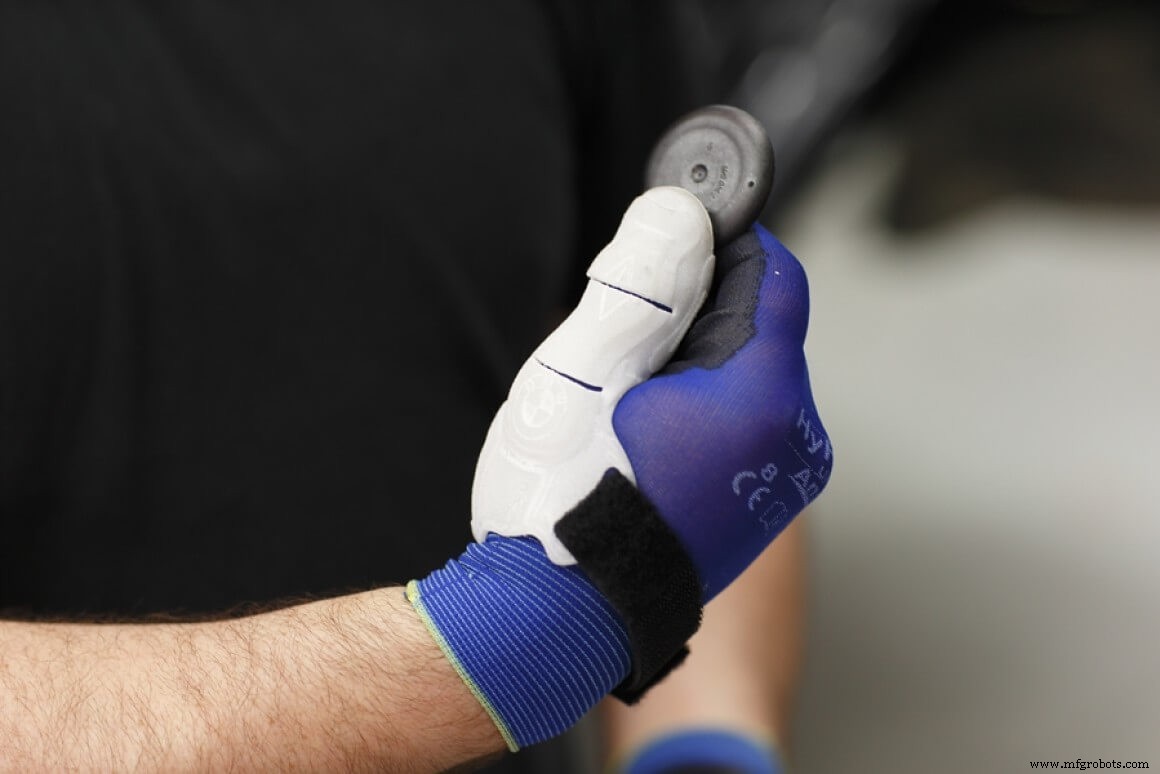
BMW Handschuhe mit geschütztem Daumen
Das Unternehmen verwendet den 3D-Druck auch für Werkzeuge und Sicherheit. Ein gutes Beispiel dafür sind die speziellen Handschuhe, die sie verwenden, um die Stopfen für Abflusslöcher fertigzustellen. Diese Stopper müssen manuell mit den Fingern des Monteurs eingestellt werden, was eine große Belastung für die Daumen bedeutet. Glücklicherweise fanden sie die 3D-gedruckte Lösung, die auf die Arbeitshandschuhe passte.
Auch abseits der Arbeit an den eigenen Automobilen haben die Ingenieure des Unternehmens bei externen Projekten mitgeholfen. Ein Beispiel ist die Entwicklung der maßgeschneiderten 3D-gedruckten Sitze für das britische Paralympics-Basketballteam. Unter Verwendung von 3D-Körperscans und der neuesten additiven Fertigung konstruierten die Ingenieure von BMW eine ganze Flotte von Rollstühlen, die es den Spielern ermöglicht, ein fortgeschritteneres Maß an sportlichen Fähigkeiten zu zeigen.
Ford
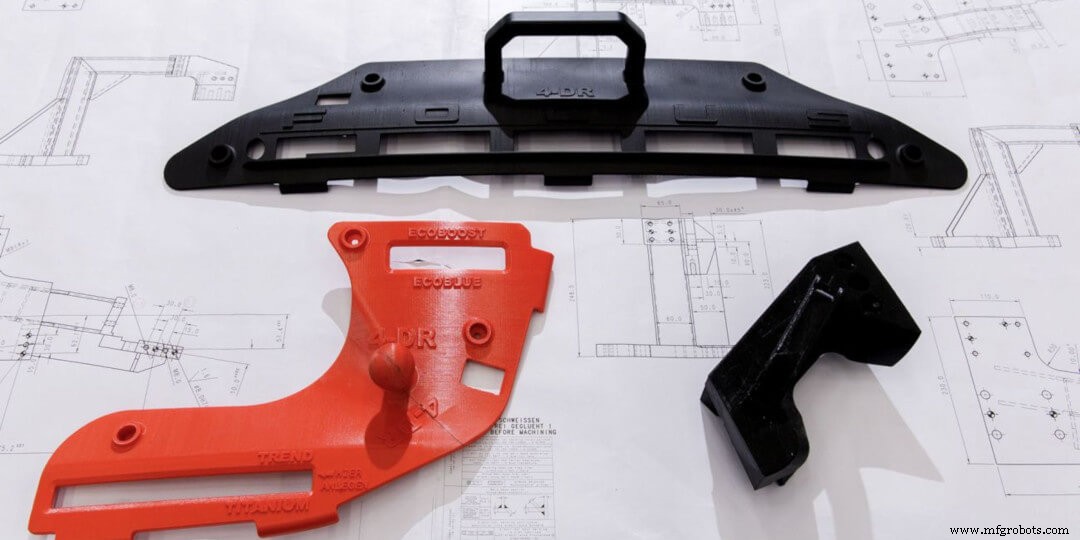
Ford’s Jigs &Fixtures
Was das Engagement für den 3D-Druck betrifft, so stürzt sich Ford kopfüber in die Umarmung der Technologie. Das Unternehmen richtete ein Zentrum für additive Fertigung ein und integrierte dessen Betrieb umfassend in seine Arbeitsabläufe. In Bezug auf die Erstellung von Kunststoff- und Metalldrucken besteht eine langjährige Partnerschaft mit verschiedenen Unternehmen wie Ultimaker, Stratasys und GE Additive, die Maschinen für alle Arten von AM-Anwendungen in der gesamten Produktionskette anbieten.
Sie verwenden den 3D-Druck auch, um Kosten und Zeit für die Werkzeugbestückung zu sparen, da das Unternehmen feststellte, dass es schneller war, seine eigenen Teile in der Anlage herzustellen, als auf Lieferanten und ähnliche Dinge warten zu müssen. Dieselben Prinzipien wenden sie auch auf Vorrichtungen und Vorrichtungen an, die sie in Einrichtungen auf der ganzen Welt entwickeln.
Sie haben ihre 3D-Druckbetriebe im Laufe der letzten Jahrzehnte erweitert und stellen sowohl Metall- als auch Kunststoffkomponenten her. Wie das Unternehmen feststellt:„In den letzten Jahrzehnten hat Ford weit über 500.000 Teile gedruckt und Milliarden von Dollar und Millionen von Arbeitsstunden eingespart. Wo die Herstellung eines Prototyps mit herkömmlichen Methoden 4-5 Monate gedauert und 500.000 US-Dollar gekostet hätte, kann ein 3D-gedrucktes Teil in wenigen Tagen oder Stunden zu einem Preis von einigen tausend US-Dollar hergestellt werden “.
In ähnlicher Weise haben die verschiedenen Tochterunternehmen von Ford ihre AM-Fähigkeiten gezeigt, insbesondere die Designteams hinter dem Shelby GT500. In diesem Jahr druckten sie innerhalb weniger Tage die vielversprechendsten Designs für den neuen GT500 in 3D, was die Verbesserungs- und Testphasen enorm beschleunigte. Dieses Tempo ermöglicht es ihnen, den Shelby GT500 Stück für Stück schnell zu optimieren und neue physische Designs mit halsbrecherischer Geschwindigkeit einzuführen. Sie entwickelten auch ein neues Spoiler-Flügel-Hybriddesign, das das Team „The Swing“ nennt. Dieses neue Design ist ein herausragender Faktor für die beeindruckenden aerodynamischen Fähigkeiten des GT500.
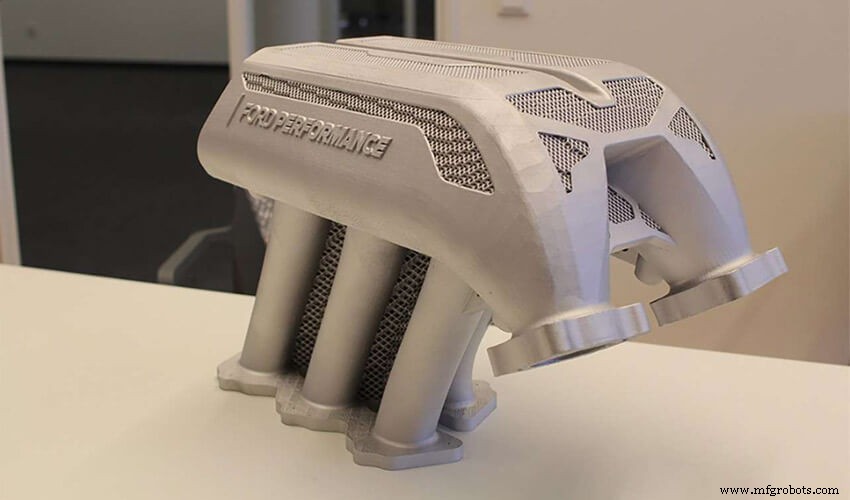
EcoBoost-Motor
Das Unternehmen hat bereits im Februar einen weiteren großen Meilenstein im 3D-Druck gesetzt. Ihre Ford Performance-Abteilung, die sich mit Hochleistungskomponenten befasst, hat in 3D gedruckt, was ihrer Meinung nach das größte Metallautomobilteil für ein funktionierendes Fahrzeug in der Automobilgeschichte ist. Das Metallteil wurde in den Hoonitruck eingebaut, einen Ford F-150 von 1977 mit einem 3,5-Liter-V6-EcoBoost-Twin-Turbo-Motor. Das Teil selbst ist ein Aluminium-Krümmereinlass, der mit dem Concept Laser X LINE 2000R von GE Additive gedruckt wurde.
Volvo
Volvo ist zwar nicht der prominenteste Nutzer des automobilen 3D-Drucks, hat aber in den letzten Jahren große Fortschritte an dieser Front gemacht. Ähnlich wie viele andere Unternehmen auf dieser Liste hat Volvo den 3D-Druck für das Werkzeug- und Lieferkettenmanagement eingesetzt. Der Einsatz des 3D-Drucks war besonders nützlich, um die Maschinen des Unternehmens mit neuen Drucken für nicht mehr produzierte Teile aufzufüllen. Volvo verwendet hauptsächlich 3D-gedruckte Kunststoffteile und plant in naher Zukunft die Implementierung von Metallteilen.
Ab 2018 nutzte das Unternehmen die additive Fertigung hauptsächlich für den Prototypen- und Werkzeugbau. „Da wir nur geringe Mengen an Teilen für das Prototyping produzieren müssen, ist es eine gute Möglichkeit zu sehen, was funktioniert“, sagt Fredrick Andersson, Entwicklungsingenieur für Radlader-Antriebsstranginstallation bei Volvo CE [Baumaschinen]. „Wir haben viel Wissen und können mit dem 3D-Druck schnell und einfach Änderungen vornehmen. Aus diesem Grund verkürzt sich die Markteinführungszeit für ein neues Produkt, was für unser Unternehmen von großem Vorteil ist .“
Die erhöhte Geschwindigkeit des Prototyping war für das Unternehmen enorm hilfreich, wie verschiedene neue Technologien, die sie testeten, beweisen. Volvo-Ingenieure haben beispielsweise neue Wasserpumpengehäuse für die A25G- und A30G-Fahrzeuge des Unternehmens entwickelt. Sie führten Simulationen durch, um das Design der internen Strömungskanäle im Gehäuse zu optimieren, mussten jedoch einen Prototyp bauen, um Funktionstests durchzuführen, um das neue Design zu validieren. Die Werkzeugkosten für dieses Projekt hätten etwa 9.090 US-Dollar betragen, die Teilekosten etwa 909 US-Dollar. Die Vorlaufzeit für die Herstellung des Prototyps hätte mindestens 20 Wochen betragen. Andererseits kostete der 3D-Druck des Prototyps 770 $ und dauerte nur zwei Wochen.
Im Jahr 2019 legte das Unternehmen jedoch in Bezug auf seine AM-Prozesse nach, insbesondere mit seiner Volvo Trucks-Niederlassung. Ihr Werk in New River Valley (NRV) in Dublin, Virginia, machte in diesem Jahr einige Schlagzeilen in der Fertigungswelt. Sie verwenden hauptsächlich SLS, haben sich aber auch mit anderen AM-Methoden beschäftigt. Diese spezielle Einrichtung produziert über 500 Fertigungswerkzeuge und Vorrichtungen, die in der Werkstatt verwendet werden und mit 3D-Druck hergestellt werden. Die Anlage ist auch ein wichtiger Knotenpunkt für die nordamerikanische Automobiltechnik.
Neben Nutzfahrzeugen entwickelt das Unternehmen auch Baumaschinen. Sicherlich hat der 3D-Druck auch diesen Aspekt der Geschäftstätigkeit des Unternehmens geprägt. Volvo setzte den 3D-Druck bei der Umrüstung seiner knickgelenkten Muldenkipper ein und senkte so die Kosten für die Prototypenerstellung um ein Zehntel. Dadurch konnte auch der Zeitaufwand von 20 auf nur noch 2 Wochen reduziert werden.
GM
General Motors und seine verschiedenen anderen Zweige sind wichtige Anwender (und Entwickler) der 3D-Drucktechnologie. Ab 2018 sparte GM jährlich 300.000 US-Dollar an Werkzeugen ein und macht ausreichende Fortschritte bei der Entwicklung neuer Technologien unter Verwendung alternativer Kraftstoffquellen. Der führende Autohersteller hat letztes Jahr angekündigt, bis zum Jahr 2023 weltweit 20 neue Elektro- und Brennstoffzellenmodelle auf den Markt zu bringen.
Obwohl sich ihre 3D-Druckoperationen hauptsächlich auf das Prototyping konzentrierten, expandieren sie. Das Unternehmen plant außerdem, seine Druckbetriebe zu erweitern, um „Zehntausende von Teilen in großem Umfang zu produzieren, wenn sich die Technologie verbessert “, so Kevin Quinn, Direktor für additives Design und Fertigung bei GM. Dieser Plan wird sich wahrscheinlich in den nächsten 5 Jahren entfalten.
Das Warren Tech Center des Unternehmens produziert jedes Jahr rund 30.000 Prototypenteile. Die Teile bestehen aus mindestens neun Materialarten, wobei Kombinationen aus Kunststoffen und Metall und Pulver verwendet werden. Sie werden hauptsächlich für das Prototyping verwendet, aber das Unternehmen sucht auch nach Teilen für den Endverbrauch. Sie besitzen auch gemeinsam mit Boeing HRL-Labors, die die Produktion einer 3D-gedruckten Aluminiumlegierung eingestellt haben.
Dan Grieshaber, Director of Global Manufacturing Integration bei GM, sagte, die Mehrheit der Fabriken von GM habe jetzt 3D-Drucker. Das Unternehmen plant, es zumindest in seinen nordamerikanischen Fabriken noch weiter zu erhöhen. Der Schritt wird GM wahrscheinlich jährlich Millionen von Dollar an Produktionskosten sparen. GM investiert seit langem in den 3D-Druck und seine verschiedenen Teilzweigtechnologien. Sie wenden es für den schnellen Bau von Werkzeugen und Zubehör für Arbeiter in ihren Werken an. Erst in diesem Jahr gab das Unternehmen an, dass die Implementierung einer 3D-Druckmaschine im Wert von 35.000 US-Dollar dem Unternehmen über zwei Jahre 300.000 US-Dollar eingespart hat. Während die Werkzeugherstellung die Hauptrolle des Druckers spielt, ist es möglich, dass das Unternehmen die Rolle der additiven Fertigung in seinem täglichen Betrieb ausbaut.
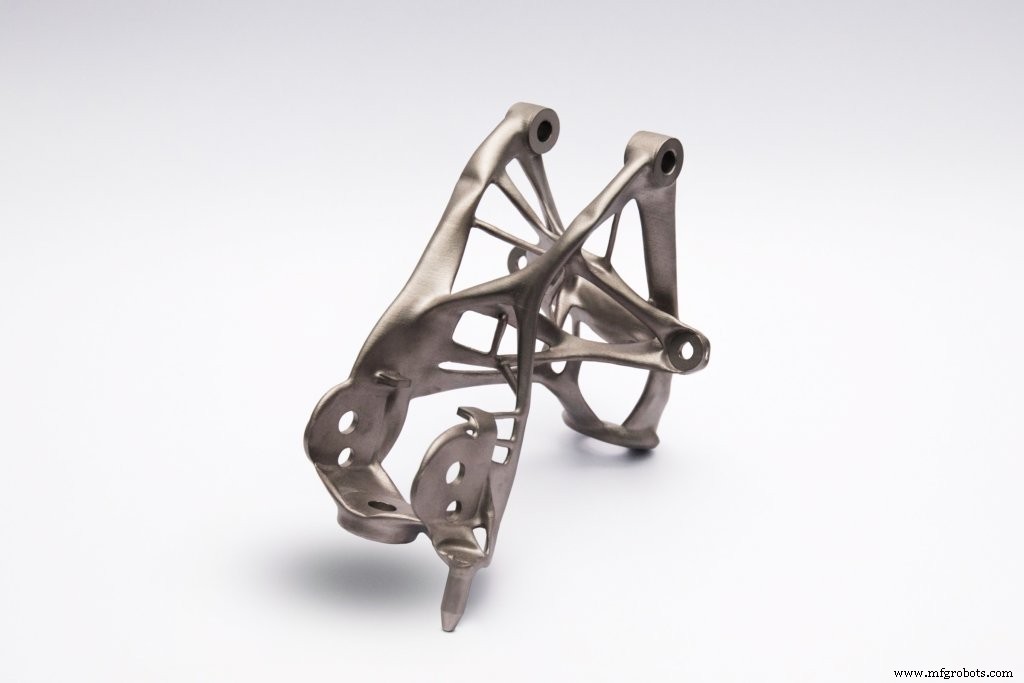
Halterung von GM in Zusammenarbeit mit Autodesk entwickelt
Ihre Partnerschaft mit Autodesk war von Vorteil bei der Herstellung leichter 3D-gedruckter Teile, die dem Autohersteller helfen könnten, seine Ziele zu erreichen, Fahrzeuge mit alternativen Kraftstoffen in seine Produktpalette aufzunehmen. Ebenfalls im Rahmen dieser Zusammenarbeit zeigten beide Unternehmen 2019 eine 3D-gedruckte Sitzhalterung aus Edelstahl, die mit der Autodesk-Technologie entwickelt wurde.
Anfang 2019 befasste sich GM mit einer neuartigen neuen Designanwendung für den 3D-Druck. In Zusammenarbeit mit Michellin wollten sie einen neuen Reifentyp mit überlegener Haltbarkeit herstellen. Der Uptis-Reifen ist noch in Arbeit, aber die Unternehmen sind in die Testphase übergegangen. Sie behaupten, die Reifen seien zu 100 Prozent nachhaltig, widerstandsfähig und könnten noch länger halten. Sie sind auch eine viel umweltfreundlichere Alternative mit weniger Abfall während der Produktion. Kürzlich haben Ingenieure eine Flotte von Chevrolet Bolt EVs verwendet, um die neuen Reifen in Michigan zu testen, und haben die Möglichkeit ins Spiel gebracht, sie der Öffentlichkeit im Jahr 2024 zur Verfügung zu stellen.
Porsche
Porsche hat den 3D-Druck für eine Reihe unterschiedlicher Zwecke eingesetzt, von wichtigen Komponenten bis hin zur Neuerfindung der Lieferkette für seine älteren Modelle. Porsche verwendet derzeit den 3D-Druck, um sehr spezifische Ersatzteile herzustellen, aber nicht so umfangreich. Dies liegt an den strengen Qualitätsstandards, die sie durchführen müssen, um sicherzustellen, dass die Sicherheit auf dem neuesten Stand ist. Das Unternehmen arbeitet auch mit einer geringeren Gesamtzahl an produzierten Einheiten, da es sich eher um klassische und Luxusautomarken handelt.
Für die Entwicklung von vergriffenen Bauteilen wie dem Ausrückhebel für die Kupplung des Porsche 959 setzt das Unternehmen auf das Laserschmelzen. Sie verwenden pulverisierten Werkzeugstahl und holen das Teil weitaus effizienter heraus, als dies mit alternativen Methoden möglich wäre.
Der Einsatz des 3D-Drucks hat es dem Unternehmen auch ermöglicht, in Richtung On-Demand-Druck zu wechseln, was weitaus niedrigere Kosten für Materialien, Transport und Lagerung ermöglicht. Dies ist auch vorteilhaft, da diese Teile nicht stärker nachgefragt werden und oft teuer in der ständigen Produktion sind. Porsche hat vor allem mit Markfordged zusammengearbeitet, um diese klassischen Teile wiederzubeleben.
Hauptsächlich verwenden sie SLM und SLS für die verschiedenen Teile, die sie herstellen müssen. Porsche hat erklärt, dass die 3D-gedruckten Teile den älteren in vielen Fällen überlegen sind. Während sie derzeit eine begrenzte Anzahl von Teilen drucken, haben sie das Portfolio seit 2018 erweitert und zukünftige Komponenten getestet.
CNC-Maschine
- Wie verwenden wir Molybdän?
- Wie nachhaltig ist der industrielle 3D-Druck?
- So verwenden Sie eine Funktion in VHDL
- So verwenden Sie eine Prozedur in VHDL
- So verwenden Sie eine Acryl-Schneidemaschine zum Schneiden von Acryl
- Werkzeugsensor des Holz-CNC-Fräsers, wie benutzt man ihn?
- Einsatz des 3D-Drucks in der Formenbauindustrie
- Wie Hersteller Analytics für ein besseres Kundenerlebnis nutzen können
- Wie funktioniert der Offsetdruck?
- So verwenden Sie einen Cutter Grinder