Schweizer Trockenbearbeitung in der Medizin
MMD Medical hat einen separaten Reinraum mit einem dedizierten HLK-System gebaut, um die trockenen Bearbeitungsvorgänge in der Schweiz frei von anderen potenziellen Verunreinigungen rund um die Produktionsstätte zu halten.
In der schnelllebigen, stark regulierten Welt der Medizinprodukte der Klasse II und III stehen Unternehmen oft vor der Herausforderung, eine kühlmittelfreie Bearbeitungsumgebung zu benötigen, die das Potenzial für Kontamination in hochkritischen Geräten ausschließt. Ein in Minnesota ansässiger Hersteller tätigt weiterhin zusätzliche Investitionen, um sicherzustellen, dass seine Kunden wichtige Geschäfts- und Fertigungsziele erreichen können, indem er einzelne Räume in der Anlage einrichtet, die auf spezifische Kundenbedürfnisse ausgerichtet sind. Dieser Ansatz hat dem Unternehmen geholfen, die Marktnachfrage nach kritischen, komplexen medizinischen Geräten mit einer erheblichen Kostensenkung bei gleichzeitiger Beschleunigung der Markteinführung erfolgreich zu erfüllen.
MMD Medical (Brooklyn Park, Minnesota) wurde 1973 gegründet und konzentrierte sich ursprünglich hauptsächlich auf den Formenbau. Im Laufe der Jahre hat das Unternehmen seine Fähigkeiten um Spritzguss, Präzisionsbearbeitung und Montage erweitert. Anfang 2018 konsolidierte MMD Medical diese Betriebe in einer einzigen 100.000 Quadratfuß großen Einrichtung, die unter anderem einen fast 2.000 Quadratfuß großen weißen Raum zeigt, in dem Schweizer Bearbeitungsbetriebe untergebracht sind, die frei von Schneidflüssigkeiten sind.
Die Herausforderungen bei der Bearbeitung einer Kanüle
Ein potenzieller Kunde wandte sich mit einem jährlichen Produktionsbedarf von 600.000 Kanülen mit engen Toleranzen an MMD Medical, um einer Vielzahl von chirurgischen Eingriffen gerecht zu werden. Die Kanüle ist ein wesentlicher Bestandteil eines Geräts, das bei der Reparatur von Hernien und anderen Bauchoperationen verwendet wird. Es leitet Luft in einen anatomischen Ballon, der genau die Menge an Raum im Körper schafft, um den Arzt bei der Durchführung des medizinischen Eingriffs zu unterstützen.
Eines der kniffligen Merkmale der Kanüle ist ein Lumen, das über die Länge des Kunststoffschlauchs verläuft. Während dieses Lumen nicht maschinell bearbeitet wird (es ist Teil eines Extrusionsprozesses), stellen sein kleiner Durchmesser und seine geringe Länge in bestimmten Bearbeitungsumgebungen, insbesondere in solchen, in denen Schneidflüssigkeiten verwendet werden, Herausforderungen hinsichtlich des Kontaminationsrisikos dar – es ist schwierig und kostspielig, Flüssigkeiten aus dem Teil zu entfernen. P>
Der bisherige Lieferant schnitt die extrudierten Rohre ab, bevor er einen vertikalen Fräsprozess durchführte, bei dem nur eine Seite des Rohrs bearbeitet wurde. Dann wurde das Rohr manuell gewendet, um die andere Seite zu bearbeiten. Der bisherige Produktionsprozess erwies sich als ineffizient und konnte die Anforderungen des Kunden nicht erfüllen.
Ein kreativer Ansatz für die medizinische Bearbeitung
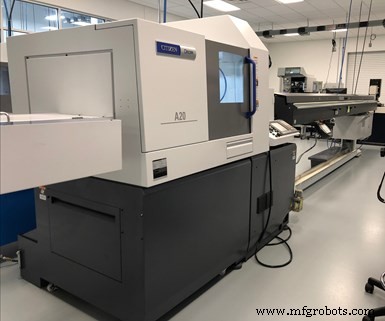
MMD Medical verwendet derzeit Maschinen vom Schweizer Typ für die Trockenbearbeitung der medizinischen Kunststoffkomponenten.
Bei der Untersuchung des Teils wusste das Team von MMD Medical, dass es den vielfältigen Hintergrund seiner Mitarbeiter nutzen konnte, um den Prozess – und die erforderliche Technologie – zu verstehen, um die angestrebten Kosteneinsparungen und Produktionsziele des Kunden zu erreichen. Das Team sah die Chance, den Wert des Unternehmens zu beweisen und damit die Beziehung zum Kunden weiter zu vertiefen. MMD Medical war in der Lage, über Productivity Inc. schnell einen Marubeni Citizen-Cincom A20 CNC-Drehautomaten vom Schweizer Typ zu erwerben, um ihn der Entwicklung und Erprobung des Konzepts für das Projekt zu widmen. MMD Medical spezifizierte, dass alle extrudierten Rohre in Längen von 12 Fuß geliefert würden, und stattete den A20 mit einem automatischen Citizen C-320 Stangenlader im Magazinstil aus.
„Früher wurden die Teile einzeln eingespannt, und alle Merkmale mussten interpoliert werden“, sagt Tim Schmit, Betriebsleiter der Präzisionsbearbeitung. „Es war ein großer Gewinn für uns, sie automatisiert auf einer Schweizer Drehbank mit einer 12-Fuß-Stange laufen zu lassen, sodass wir sie nicht schneiden mussten. Sie produzieren einfach weiter mit hoher Geschwindigkeit ohne die manuelle Arbeit der Fixierung.“
„Einen Trockenlauf eines Stangenladers ist in der Branche nicht üblich“, sagt Vice President Darren Bjork. „Unser Team musste einige Versuche durchführen, um die Auswirkungen des Trockenlaufens zu verstehen, um einen effizienten und erfolgreichen Prozess entwickeln zu können.“ Da die Teile aus Kunststoff bestehen und kein Kühlmittel verwendet wird, war die richtige Werkzeuggeometrie entscheidend, um die Wärme im Span abzuführen. Der Raum, in dem die Teile hergestellt werden, verfügt außerdem über ein eigenes HLK-System, um ihn weiter von Bereichen zu trennen, in denen Öle verwendet werden. Die Bearbeitung ohne Schneidflüssigkeiten und die Verwendung einer kontrollierten Produktionsumgebung mit strengen Qualitätskontrollprozessen ermöglichen es dem Unternehmen zwar, das Kontaminationsrisiko auf dem Gerät zu eliminieren, es löst jedoch nicht alle Herausforderungen.
Als Kunststoffteile sind sie sehr anfällig für Beschädigungen, aber wie es in der medizinischen Bearbeitung üblich ist, ist die Oberflächenbeschaffenheit entscheidend. Das Vermeiden von Kratzern ist schwierig, da sich das Material mit hoher Drehzahl dreht, während es durch einen automatischen Stangenlader und durch den Spindelstock einer Langdrehmaschine läuft.
Wenn sich die Teile durch die Buchse bewegten, bekamen sie anfänglich Längskratzer entlang der Länge und es bildeten sich Peitschenlinien, wo die Stangen im Stangenlader reiben würden. Um das Problem zu lösen, fügte das Unternehmen an mehreren Stellen Abstandshalter hinzu, und für alle Komponenten der Maschine, die aus Metall bestanden und mit dem Teil in Kontakt kamen, stellte es Ersatzkomponenten aus anderen Materialien her, die das Teil nicht markieren würden. Das Unternehmen fügte eine kundenspezifische Auskleidung für die automatische Einstellbuchse und eine kundenspezifische Distanzbuchse in der Gegenspindel hinzu.
Herr Schmit sagt, dass die wichtigsten kundenspezifischen Komponenten, die das Unternehmen gebaut hat, neue Kanalsätze für den Stangenlader waren. „Stangenlader sind hochgradig geschmiert und voller Öl“, sagt er. Dieses Öl hält die Stange kühl und verhindert Abrieb. „Wir haben drei Iterationen benötigt, aber wir konnten Kanalsätze intern entwerfen und bauen, die es uns ermöglichen, das Material bei normaler Drehzahl vollständig trocken zu verarbeiten, ohne die Teile überhaupt zu beschädigen.“
Eine weitere Anpassung erfolgte in Zusammenarbeit mit dem Maschinenhersteller. Um die Maschine sauberer zu halten, minimieren sie das Schmieröl, um nur das Nötigste zu verwenden, anstatt zu viel zu schmieren, und MMD Medical führt ein Protokoll zum regelmäßigen Abwischen der Maschine.
Die ersten produktionsreifen Kanülen wurden innerhalb von zwei Monaten geliefert, was vier Monate früher als geplant war. Die Programmkosten wurden um 150.000 US-Dollar pro Jahr gesenkt, und die Vorlaufzeiten wurden um 67 Prozent verkürzt. Die Bereitschaft des Unternehmens, in die richtige Ausrüstung zu investieren und die beste Lösung zu entwickeln und auszuführen, zahlte sich bei der Bereitstellung für den Kunden aus. Und MMD Medical hat das Programm nach der Markteinführung weiter gestärkt, indem es eine effizientere Methode zum Aufbringen eines nahezu mikroskopisch kleinen Polyurethanfilms auf jeden Schlauch nach der Bearbeitung entwickelt hat, wodurch noch mehr Schritte im Produktionsprozess eingespart und die Kosten weiter gesenkt werden.
Anwenden dieser Lektionen auf die Bearbeitung neuer Teile
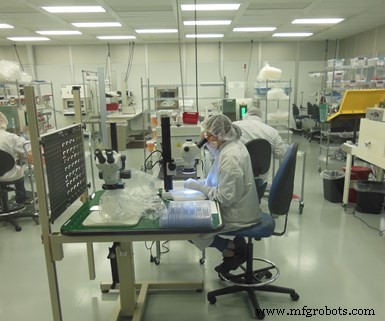
Das Unternehmen verfügt über zusätzliche Reinräume der ISO-Klasse 7 für andere Bearbeitungs- und Montagevorgänge.
Aufgrund des Erfolgs mit der Kanüle konnte MMD Medical schnell weitere Arbeiten mit demselben Kunden sichern. Der nächste Teil ist eine Komponente für ein Ligaturgerät, ein langes, schmales Rohr, das während einer Operation in einen Körper eingeführt werden soll, um Körperteile mit einem Lasso – einem Polypropylenfaden – zu greifen und abzubinden, das durch die Mitte gezogen wird des Geräts. Die Ligaturschlaufe wird häufig für Appendektomien sowie für veterinärmedizinische Anwendungen verwendet.
Viele der im ersten Teil implementierten Strategien wurden auch auf diese Komponente übertragen. Es ist ein ziemlich einfaches Teil, aber es erfordert auch eine sorgfältige Handhabung sowohl innerhalb als auch außerhalb der Maschine. Das Material für dieses Teil wird auch in 12-Fuß-Rohrlängen geliefert, die wie vorgekochte Spaghetti aussehen. Während die Stäbe etwas steif sind, hängen sie bei dieser Länge erheblich durch, so dass auch beim Regalen darauf geachtet werden muss, dass sich das Material nicht verzieht. Die Teile werden auch auf einer Citizen-Swiss-Maschine verarbeitet.
Am hinteren Ende jedes Teils befindet sich eine Rille, die so konzipiert ist, dass der letzte Abschnitt oder die Lasche während des Gebrauchs leicht abgebrochen werden kann (sobald das Lasso an Ort und Stelle ist). Ein Ende des Fadens wird an dieser Lasche befestigt, sodass er durch den Schlauch gezogen werden kann, um den Faden festzuziehen. Die Tiefe der Rille ist entscheidend, um ein leichtes, aber nicht vorzeitiges Abbrechen zu ermöglichen.
Eine der Herausforderungen des Teils war das ursprüngliche Design der Rille, die schwierig herzustellen war und ein ordnungsgemäßes und konsistentes Abbrechen ermöglichte. MMD Medical empfahl eine Änderung der Form von einer quadratischen Kerbe zu einer V-Kerbe, die einen sehr deutlichen Bruchpunkt bietet. Das Unternehmen führt immer noch regelmäßige Bruchkrafttests der Rille durch, aber sie trifft durchweg innerhalb der angegebenen Parameter.
Erfolgreiche Arbeit in der medizinischen Fertigung
Das Geschäftsmodell des Unternehmens konzentriert sich auf ausgewählte Gelegenheiten bei wichtigen Herstellern medizinischer Geräte, sodass das Team maximalen Nutzen erzielen kann. „Wir folgen dem 80/20-Prinzip, damit wir uns darauf konzentrieren können, unseren Schlüsselkunden bei der Lösung ihrer größten geschäftlichen Herausforderungen zu helfen“, sagt Herr Björk. „Unser Ziel ist es, langfristige Beziehungen zu großen Medizingeräteherstellern aufzubauen.“
Ein Merkmal, das das Unternehmen für potenzielle Kunden attraktiv macht, ist seine Fähigkeit, die beste Lösung für die Probleme der Kunden zu finden und diese schnell umzusetzen, auch wenn es darum geht, die neueste Technologie einzusetzen. Während sich Gespräche über zukünftige Arbeiten entwickeln, kommuniziert Herr Schmit bereits mit Maschinenhändlern darüber, welche Ausrüstung erforderlich sein könnte. Mit der richtigen Begründung drückt das Management schnell auf neue Maschinen, und in den meisten Fällen konnten diese Händler sofort liefern.
„Jeder sucht nach Kosteneinsparungen“, sagt Herr Bjork. „Der Vorteil, den wir bringen, ist, dass wir ein Team kreativer Problemlöser haben, die kreative Lösungen finden können – und die finanzielle Stärke, um die Lösungen durch Investitionen in die neueste Technologie und Ausrüstung zu unterstützen.“
Seit der Konsolidierung der Geschäftstätigkeiten des Unternehmens unter einem Dach konnten die Teams besser zusammenarbeiten und ihre unterschiedlichen Perspektiven und ihr Fachwissen nutzen, um kreative Lösungen für die größten Probleme der Kunden zu liefern.
Für weitere Informationen von MMD Medical rufen Sie 763-428-8310 an oder besuchen Sie mmdmedical.com.
Industrielle Ausrüstung
- Warum ist die CNC-Bearbeitung in der Medizinbranche gefragt?
- Jenseits der Schweizer Präzision
- 8 wichtige Taktiken für die medizinische Präzisionsbearbeitung
- Was ist Schweizer Bearbeitung und woher kommt sie?
- Wie die Präzisionsbearbeitung medizinische Geräte beeinflusst?
- Prototyp entwickeln
- Swiss Machining von medizinischen Elektroden aus MP35N®
- Schweizer Bearbeitung von kundenspezifischen Buchsen für medizinische Geräte
- Schweizer Bearbeitung von Knochenschrauben und Ankern
- Durchbiegung und Präzision in der CNC-Swiss-Bearbeitung