Geschwindigkeit, Prozesskontrolle kombiniert in einer aktualisierten Mehrspindelplattform
Diese Maschine kombiniert die schnellen Produktionsmöglichkeiten einer Nockenschraubmaschine mit mehreren Spindeln, deren Programmierung und Präzision durch Computer Numerical Control (CNC) ermöglicht wird. Bildnachweis:Davenport Machine
Die Marke Davenport ist niemandem in unserer Präzisionsbearbeitungsbranche fremd. Es wäre unmöglich, die Gesamtzahl der Teile zu schätzen, die Geräte wie der Mehrspindler Modell B im Laufe der Jahre produziert haben.
Und eine gute Anzahl dieser kurvenbetätigten Schraubmaschinen sind noch heute im Einsatz. Dessen ungeachtet bietet Davenport Machine (Teil der Brinkman International Group Inc.) jetzt die nächste Weiterentwicklung dieser Fünf-Spindel-Maschinen an – den Hybrid – der entwickelt wurde, um eine strengere Prozesskontrolle und Präzision zu realisieren und gleichzeitig einfacher zu bedienen und mehr zu sein flexibel einzurichten und auf neue Jobs umzustellen.
Andy Laniak, CEO von Davenport Machine, sagt, dass das Ziel mit dem Hybrid darin bestand, die Produktionsgeschwindigkeit beizubehalten, für die die traditionelle Mehrspindelplattform des Unternehmens bekannt ist, und gleichzeitig eine wiederholbare CNC-Positionierungsgenauigkeit mit einer intuitiven Computerschnittstelle zu bieten, die den heutigen Maschinenbedienern, Programmierern und Setups zur Verfügung steht Personal würde sich wie zu Hause fühlen. Er fügt hinzu, dass der Hybrid auch für die Bearbeitung anspruchsvollerer Materialien wie Hochtemperaturlegierungen entwickelt wurde, die zur Herstellung von Teilen wie Befestigungselementen für die Luft- und Raumfahrt verwendet werden könnten.
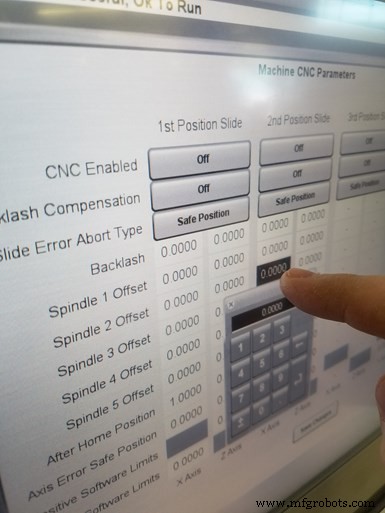
Auf der CNC mit Touchscreen läuft eine proprietäre Steuerungssoftware. Werkzeug-zu-Spindel-Versatz kann durchgeführt werden, um jede Spindel für Teiledurchmesser und -länge für globale Versatzfähigkeit anzupassen. Das Steuerungssystem bietet auch Funktionen wie Teilezählung, Bestandserschöpfungserkennung und Spindellastüberwachung.
Einige von Ihnen kennen diese Maschine vielleicht aufgrund ihrer Vorstellung auf der Precision Machining Technology Show (PMTS) im Jahr 2017. (Besuchen Sie pmts.com, um mehr über die diesjährige Messe vom 10. bis 12. August in Cleveland zu erfahren.) Allerdings gibt es eine Vielzahl von Seitdem wurden Designverbesserungen und Ergänzungen vorgenommen. Hier ist eine kurze Aufschlüsselung dessen, was das Unternehmen sagt, dass die neueste Version der Hybridmaschine, die an seinem Hauptsitz in Rochester, New York, hergestellt wird, derzeit enthalten ist.
- Starre Basis. Eine optimierte Gussgeometrie sorgt für hohe Steifigkeit, während die Maschinenbasis über integrierte strukturelle Stützen für verbesserte Vibrationsdämpfungseigenschaften verfügt. Darüber hinaus wird der Drehkopf/Spindelträger, der auf dem HP-Design des Unternehmens basiert, am Maschinenbett montiert, das von vorgespannten 9-Zoll-Schrägkontaktlagern getragen wird, um eine konsistente Spindelpositionierung und eine schnellere Indexiergeschwindigkeit zu gewährleisten. Jede Spindel verwendet Schrägkugellager für eine verbesserte Größenkontrolle und Rundheit der Teile.
- CNC-gesteuerte Folien. Die CNC-gesteuerten Schlitten der ersten und zweiten Position laufen auf vorgespannten Linearschienen, wobei die Bewegung durch servogetriebene Kugelumlaufspindeln erfolgt (es werden keine Nocken oder Gestänge verwendet). In ähnlicher Weise verfügen die dritte und fünfte Position über CNC-gesteuerte Schwenkarme anstelle von Nocken oder Spannschlössern. Die vierte Position mit einem zweiachsigen (X-Z) Schlitten kann Einpunkt-Drehen und Gewindeschneiden, 2D-Profilieren und schräges Hinterschneiden ausführen. Es kann auch Bohrstangenhalter für komplexe Innenkonturen und Hinterschneidungen sowie Mehrfachwerkzeuge aufnehmen, um sowohl Innen- als auch Außenbearbeitungen auf demselben Schlitten auszuführen.
- CNC mit proprietärer Software. Die CNC des Hybrid mit 15-Zoll-Touchscreen führt eine von Davenport Machine entwickelte (und modifizierte und aktualisierte) Steuersoftware aus. Jede Schlittenachse kann unabhängig programmiert werden. Werkzeug-zu-Spindel-Versatz kann durchgeführt werden, um jede Spindel auf Teiledurchmesser und -länge einzustellen. Einmal eingestellt, bietet dies eine globale Ausgleichsfunktion für jedes Werkzeug an jeder Spindel, um beispielsweise den Werkzeugverschleiß auszugleichen. Das Steuerungssystem bietet auch Funktionen wie Stückzählung, Bestandserschöpfungserkennung und Spindellastüberwachung.
Schnellwechsel-Schwalbenschwanz-Werkzeugsystem erleichtert schnelle Einrichtung für neue Jobs und nimmt Hartmetalleinsätze nach Industriestandard auf, was bedeutet, dass keine speziellen Formwerkzeuge erforderlich sind.
- Schwalbenschwanz-Werkzeughaltesystem. Um den Wechsel zu beschleunigen, verfügt der Hybrid über ein Schnellwechsel-Schwalbenschwanz-Werkzeugsystem, das in Schäl-, Umform- oder Standard-5/8-Zoll-Stick-Werkzeugkonfigurationen erhältlich ist, um präzise Konus-, Höhen- und Längenpositionseinstellungen zu ermöglichen. Alle Werkzeughalter verfügen über Hochdruck-Kühlmittelzufuhröffnungen (1.000 psi) durch das Werkzeug, um Kühlmittel zur Schneidkante eines Werkzeugs zu leiten, während Kupfer oder einstellbare Düsen im Arbeitsbereich überflüssig werden. (Die Kapazität des Kühlmittelsumpfs beträgt 200 Gallonen, und Hochdruck-Kühlmittel ist eine Standardfunktion der Maschine.) Werkzeugmodule akzeptieren herkömmliche Hartmetalleinsätze von verschiedenen Werkzeuganbietern, was bedeutet, dass keine Spezialwerkzeuge erforderlich sind.
- Optionen zum Entfernen von Teilen. Hybridmaschinen sind mit drei verschiedenen Teileentnahmeoptionen erhältlich. Einer ist ein herkömmlicher federbelasteter Auswerfer, der Teile zu einer Rutsche innerhalb der Maschine schiebt. Alternativ können Teile für eine schonendere Handhabung aus der Rückseite der Aufnehmerspindel gleiten. Oder ein System mit einer pneumatischen Teilerutsche, die zu einem Förderband führt, kann Teile außerhalb der Maschine sammeln und ausliefern.
Eine CNC-programmierbare Rückseitenbearbeitung mit drei Stationen Schlitten ermöglicht Vorgänge wie Einzelpunktdrehen und Gewindeschneiden sowie andere Vorgänge mit Standardwerkzeugen.
- Rückwärtsbearbeitungsachse mit drei Stationen. Diese CNC-programmierbare Achse ermöglicht Operationen wie Einzelpunktdrehen, Bohren und Gewindeschneiden, konturiertes Einstechen, Keilnuträumen, Bohren und starres Gewindeschneiden mit Standardwerkzeugen. Hinzu kommen vier unabhängige Gegenspindeln, die Schnellwechsel-Werkzeugschnittstellen für Werkzeuge wie Bohrer, Anbohrer, Gewindebohrer und Reibahlen sowie die Möglichkeit zur Offline-Werkzeuglängenvoreinstellung bieten. Für diese Spindeln sind die Spannzangengrößen ER16, ER20 und ER25 verfügbar.
- Servogetriebene Abgreifspindel. Diese Achse ist in Schritten von 0,0001 Zoll programmierbar und bietet eine Eilganggeschwindigkeit von 1.000 ipm. Die Aufnahme von runden, sechseckigen und anderen unregelmäßigen Formen ist möglich, und das Spannzangenschließen wird pneumatisch über M-Codes betätigt.
Das Unternehmen ist der Ansicht, dass das Hybrid-Maschinenkonzept sowohl von denjenigen angenommen werden sollte, die an das traditionelle Davenport-Design gewöhnt sind, als auch von Personen, die besser mit CNC-Programmierung und Touchscreen-Schnittstellen vertraut sind. Ebenso ist es der Ansicht, dass die Maschine mit schnellen Umrüstmöglichkeiten eine Alternative zu Werken sein kann, die derzeit andere Arten von Ausrüstung für Produktionsläufe mit mittlerem Volumen verwenden, während es weiterhin gut für Arbeiten mit hohem Volumen geeignet ist, bei denen komplexe Teile hergestellt werden.
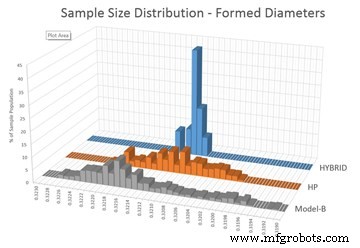
Diese Grafik zeigt die verbesserte Prozesssteuerung des Hybrid Maschine erzielt im Vergleich zu den Modell B- und HP-Maschinen des Unternehmens (basierend auf Daten aus einem Bearbeitungstest eines identischen Messingteils).
Industrielle Ausrüstung
- CNC-Fräser-Produktionsprozess
- Definition, Prozess und Typen von Fräsmaschinen
- Mehrspindelfunktionen Verbesserte Benutzerfreundlichkeit, Wartung
- Werkzeugmaschinen verfügen über eine integrierte Steuerung
- Kurvengesteuerte Drehmaschine mit sechs Spindeln bietet Geschwindigkeit und Zuverlässigkeit
- Multitasking-Drehzentrum bietet hohe Geschwindigkeit und Steifigkeit
- Steuerungspaket beschleunigt die Produktion
- Neue Steuerung verbessert Vorschubgeschwindigkeiten bei überholten Altmaschinen
- Fagor CNC erfüllt die Genauigkeitsanforderungen von Maschinenwerkstätten in der Luft- und Raumfahrt
- Ein unkonventioneller Ansatz für die Mehrspindler-Produktion