Die Evolution des Crimpens von Hydraulikschläuchen
Von ihren bescheidenen handbetriebenen Anfängen bis hin zu IoT-fähigen Maschinen sind hydraulische Schlauchpressen ein wichtiges Ausrüstungsteil, das jeder Anwender von Fluidtechnik verstehen sollte.
Sie werden kaum jemanden in dieser Hydraulikbranche finden, der noch nie eine Hydraulikschlauchleitung hergestellt hat. Hydrauliktechniker verdienen ihren Lebensunterhalt mit der Herstellung von Rohrleitungen in verschiedenen Konfigurationen. Trotzdem haben sich wahrscheinlich sogar Designer und Ingenieure in der Schule im Rahmen einer Einführungsklasse zu diesem Thema die Hände schmutzig gemacht. Meistens schneiden Fluidtechnik-Profis ihre Zähne im örtlichen Schlauchgeschäft, bevor sie sich durch die Reihen eines Händlers oder Herstellers bewegen. Dennoch sind viele von Ihnen, die dies jetzt lesen, mit den Techniken vertraut, die zum Crimpen eines Hydraulikschlauchs verwendet werden.
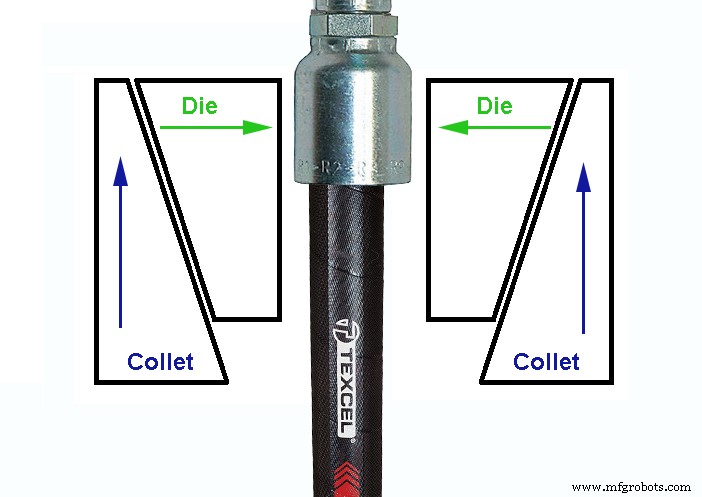
Wie zu erwarten war, hat die Schlauchcrimpausrüstung ihren Ursprung in bescheidenen Anfängen. Jede Maschine, die in der Lage ist, eine radiale Kraft auf den Außendurchmesser einer Schlauchendhülse auszuüben, würde den Zweck erfüllen. Schon früh nutzten die Ingenieure bei ihren Konstruktionen die Konus- und Sitzanordnung für die Crimpeinsätze, ein System, das auch heute noch am beliebtesten ist. Die Spannzange fungiert als Sitz, und wenn sie gegen die Kegelform der Matrizen drückt, werden die Matrizen nach innen gedrückt (siehe Abbildung 1).
Handschläge kamen zuerst
Solange Sie entweder die Matrizen oder Spannzangen drücken können, um den gewünschten nach innen gerichteten Kraftvektor zu erreichen, bietet die konische Form einen mechanischen Vorteil, um das Zusammendrücken der Schlauchendhülse zu unterstützen. Die erste Schlauchcrimptechnologie nutzte die gute altmodische menschliche Kraft, um das gewünschte Ergebnis zu erzielen. Frühe Gesenkpressen wurden durch Drehen eines großen T-Griffs, Drehen einer Maschinenschraube durch einen festen Kopf und Drücken des Endes gegen den zweiteiligen Matrizensatz betrieben.
Im Falle dieser tragbaren Handdrücker bewegen sich die Matrizen nach unten gegen die feststehende Spannzange, und wenn sich die Matrizen nach unten bewegen, werden sie auch nach innen zusammengedrückt. Der Techniker muss das Schlauchende vorsichtig mit einer Hand halten, während er den Griff mit der anderen Hand dreht. Sobald die Matrizen das Fitting fest genug greifen, verwendet der Techniker dann beide Hände, um die Crimpzange zu spannen, bis sie aufsitzt. Es ist wichtig, nur die für die Anwendung passenden Düsen und Schlauchenden zu verwenden.
Diese tragbaren, handbetriebenen Einheiten bieten nicht die gleiche Technologie für den automatischen Crimpdurchmesser wie neue Systeme, die Mikrometer verwenden. Sie klemmen die Einheit einfach fest, bis die zweiteiligen Matrizen den Boden erreichen, und hoffen, dass Sie Ihre Crimp-Spezifikation erreichen. Das Messen des Crimps bietet dem Techniker immer noch die Bestätigung, dass der Crimp innerhalb der Spezifikation liegt, aber er muss sich auf seine Erfahrung mit dem Gerät verlassen, um konsistent genaue Ergebnisse zu erzielen. Ich sollte auch erwähnen, dass viele Techniker auch heute noch tragbare Handschmiedemaschinen verwenden.
Hydraulik erhöht Geschwindigkeit und Leistung
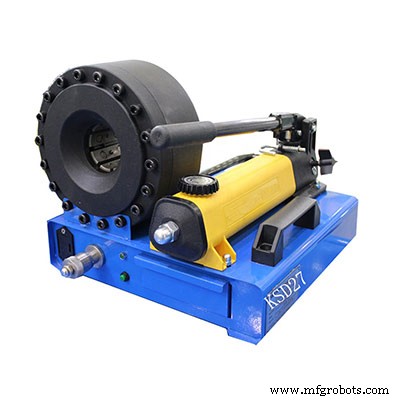
Etwas an einer hydraulisch angetriebenen Schlauchquetschmaschine ist befriedigend. Eine vollelektrische Maschine fühlt sich einfach nicht richtig an, wie ein fleischloser Burger oder ein Mazda Miata mit Automatikgetriebe. Das Hinzufügen einer hydraulischen Leistungsdichte zur Crimpmaschine bot dem Techniker eine schnellere und leistungsfähigere Methode zum Crimpen von Schlauchenden. Die Spannzange an der hydraulischen Crimper ist im Wesentlichen ein ringförmiger Hydraulikzylinder. Teilweise drücken zwei Zylinder auf einen solchen Ring. Die von den Zylindern erzeugte Kraft schiebt entweder die Spannzangen oder die Matrizen und zwingt letztere, sich mit hoher Kraft um das Schlauchende zu schließen.
Die Hauptschwierigkeit bei frühen Crimpmaschinen war ihre mangelnde Vielseitigkeit. Die verwendeten Matrizen waren spezifisch für das Schlauchende und ermutigten den Techniker oder Schlauchhändler, nur Produkte desselben Herstellers zu verwenden. If a shop wished to use various hoses and ends, a method to vary the crimp diameter had to offer variability in the crimp OD while still offering accuracy down to the thousandths of an inch.
Rather than limit the technician to fixed diameter dies, instead offering dies capable of a range of internal diameters brought in that variability to allow multiple types and sizes of assemblies. Instead of an exact diameter of, say, 0.733 in., the dies now offer a range from 0.700-0.788 in. for example. What could previously only crimp a ½ in. hose end may now crimp 1- and 2-wire hose from 3/8 to ½ in.
Dies designed for variable diameter applications present the challenge of accuracy, of course. The dies can only bottom out on their smallest setting, which may not always be helpful for any hose or fitting the shop offers. Crimp machine designers had to engineer a method to stop the crimping procedure at the desired size accurately. No technician is skilled enough to stop the hydraulic pump by feel with 0.002 in. accuracy or better.
Accurate and repeatable
Installing an adjustable limit switch offered the most accurate and repeatable solution to the variable die set. An adjustable micrometer attached to the limit switch allows the technician to set the depth of the limit switch to within a thousandth of an inch or less. When the crimp actuator contacts the limit switch, the pump stops automatically. So long as the micrometer has been calibrated, the crimp diameter is both accurate and precise for every single operation.
Hydraulic crimpers using the micrometer were the standard for decades, offering precise control to make hose assembly quick and straightforward. Much of the advancement, until recently, has been improvements to the practicality of the machine. Dual-stage hydraulic pumps provided the technician with rapid die travel until the clamping pressure was met, where the stages switched to the smaller, high-pressure pump for maximum force.
Convenient die storage systems to offer rapid and precise tooling changes also sped up the pace for busy hose shops changing between sizes. A die-set loader offered the technician ease of pulling dies from their holder where they’re inserted into the crimper before being clamped in place. The tidy die storage and replacement systems so widespread today beat the old habit of sifting through drawers or bins where every die of every size mingled with no organization.
Electronic control
Just as the rest of the industry moved towards electronic control, so too did the hose crimping machine. Some technicians found the traditional dial-micrometer hard to read and adjust, and often found itself out of calibration. Linear position sensors replaced the limit switches, and then the adjustment option went digital. A small LCD screen shows the crimp setting, which increased accuracy and reduced the chance for error. The precision of the linear transducer all but guarantees perfect, repeatable crimps.
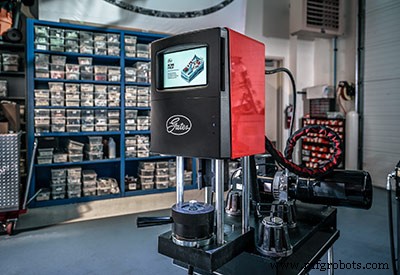
Some hydraulic hose assembly equipment manufacturers have produced semi-automated hose assembly stations. One such machine requires only that the operator load the parts into the machine. The operator loads the stems and ferrules separately, two at a time, and then inserts the hose ends into the machine. The operator starts the sequence that inserts the stems into the pre-cut hose ends along with the ferrules.
The operator unclamps the hose assembly, and if it’s long enough, simultaneously inserts each end into the automatic crimper. A moment later, the technician pulls out a complete hose assembly. If the hose length isn’t long enough to span the gap and into the two openings, the ends are done individually but in parallel. The insertion and crimping functions are completed while the technician works on the opposing operation. Capable of two hundred complete hose assemblies per hour, this machine quickly offers a return on its investment.
Crimpers get smart
The industrial world continues to find new and creative ways to utilize Industry 4.0 concepts, and hose crimping technology is no different. Busy hose shops require speed and versatility, leaving little time for thumbing through catalogues looking for crimp specs. Many top crimp manufacturers offer high-end machines with touch screen HMIs employing wireless links to the manufacturer database.
This system might not be impressive for the technician who has memorized the crimp specs for their standard 100R1 or 100R2 assemblies. But when they’re asked to crimp various assemblies of stainless wrapped thermoplastic hose, they’ll be elated to know the required die information pulls up on the touchscreen. A quick selection of hose, dash size and stem results in readily available crimp specs populated right into the crimper settings.
Just like the fluid power industry at large, crimping technology will continue to advance. Expect to see augmented reality identify the hose and fittings visually, such as with QR codes, then automatically populate crimp specifications. Expect hydraulic hose crimping technology to become more versatile, more productive and more easily maintained.
Industrielle Ausrüstung
- Hydraulischer zu elektrischer Aktuator:Diskussion der Grundlagen
- Ersetzen eines Hydraulikschlauchs
- Die Entwicklung von Houston Dynamic Service
- Die Entwicklung des 3D-Sehens
- Warum ist mein Hydraulikschlauch undicht?
- Wie man einen Hydraulikschlauch von einem Traktor trennt
- So identifizieren Sie die richtigen Hydraulikschlauchanschlüsse
- Was bestimmt die Drehzahl eines Hydraulikmotors
- wo ist die Hydraulikpumpe eines Traktors
- Was bestimmt die Drehzahl eines Hydraulikmotors?