Neues Hybridkonzept zur Betätigung von Unterwasserventilen
In Öl- und Gas-Unterwasserfördersystemen wird ein Unterwasser-Weihnachtsbaum auf den Bohrlochköpfen montiert. Jeder Baum steuert die Öl- und Gasförderung seines jeweiligen Bohrlochs über mehrere Prozessventile. Jedes Prozessventil wird von einem Subsea Valve Actuator (SVA) angesteuert, der in jedem Betriebszustand, auch bei Stromausfall, das Ventil sicher schließen muss.
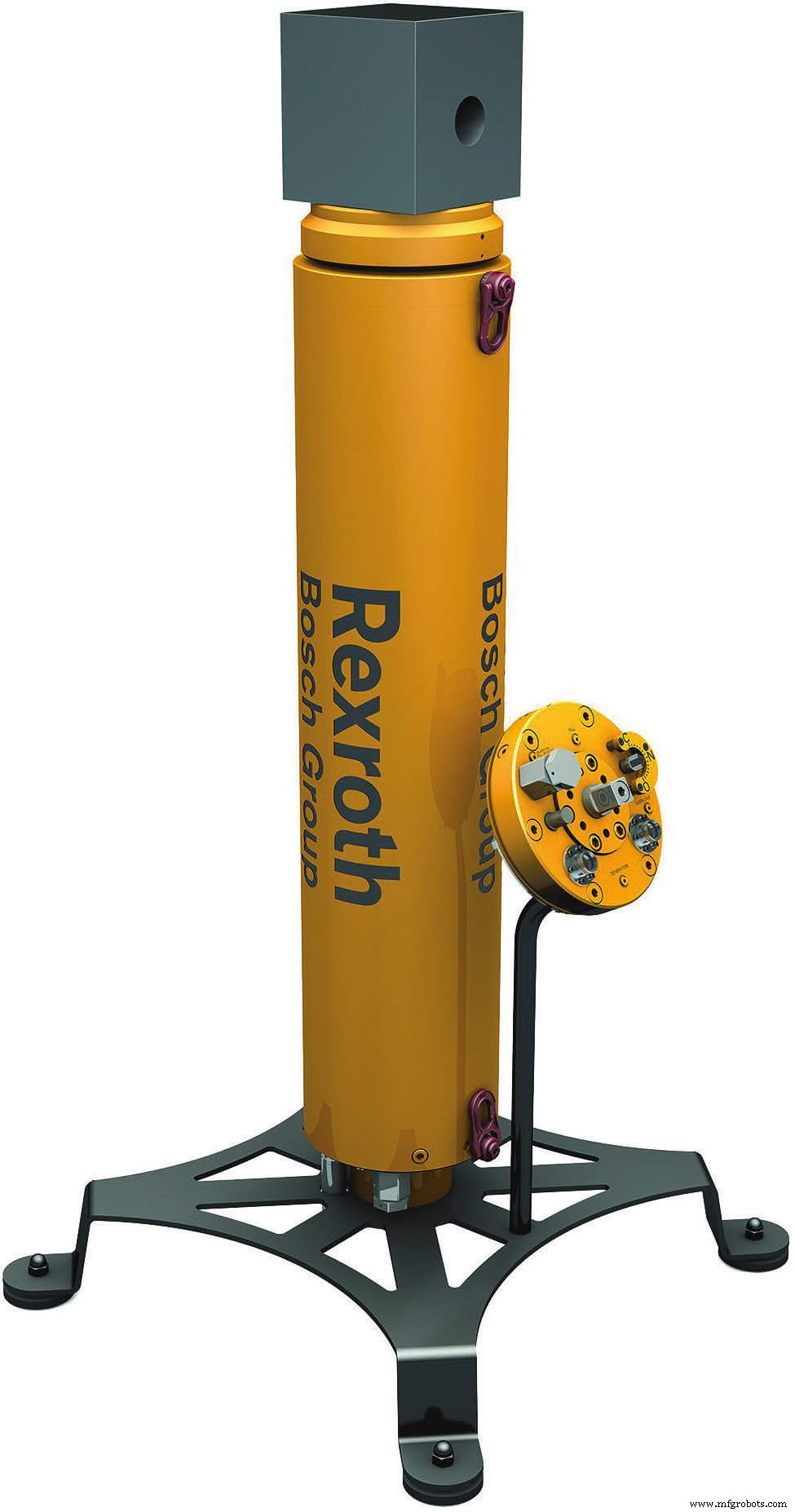
Die Anforderungen an Subsea-Fördersysteme sind extrem hoch. Betriebsverfügbarkeit und -sicherheit sind besonders wichtig für Unterwassersysteme, die Öl und Gas fördern, um Mensch und Umwelt zu schützen. Darüber hinaus wird der Schutz des Meeres vor Verschmutzung durch die Entsorgung von Hydraulikflüssigkeit, die in konventionellen SVAs verwendet wird, nun ebenfalls zu einer Schlüsselpriorität.
Ein neues Konzept für ein Hybrid-SVA kombiniert Elektromechanik und Elektrohydraulik in einer kompakten Einheit für Tiefseeanwendungen wie z Druck von bis zu 300 bar in einer Salzwasserumgebung, verbrauchen bis zu 75 Prozent weniger Energie und arbeiten 24 Stunden am Tag über eine Lebensdauer von 25 Jahren mit begrenzten Wartungsmöglichkeiten.
Eigenständige Achsen mit hydrostatischem Antrieb
Der neu entwickelte SVA bietet eine energieeffiziente und sichere Alternative zu den bisher verwendeten traditionellen hydraulischen oder elektromechanischen Stellantrieben, die den Absperrschieber öffnen und schließen (Abbildung 2). Hybrid-SVAs sind in sich geschlossene Module mit einem eigenen geschlossenen Flüssigkeitskreislauf, der nur wenige Liter umweltfreundliche Hydraulikflüssigkeit enthält. Ein Elektromotor mit variabler Drehzahl treibt eine langlebige Hydraulikpumpe an, die den zur Betätigung eines Hydraulikzylinders erforderlichen Durchfluss erzeugt. Die Stange des Zylinders ist mechanisch mit dem Schieberschaft des Brunnens gekoppelt, um ihn nach Bedarf zu öffnen oder zu schließen.

Ein Sicherheitsventil mit mechanischer Feder im Inneren des SVA sorgt dafür, dass der Zylinder auch bei Stromausfall sicher in die Sicherheitsstellung einfährt, ohne dass eine externe Stromversorgung oder Batterien erforderlich sind. Zusätzlich kann der Zylinder über einen Override von einem Unterwasserroboter extern angetrieben werden. Alle Schlüsselkomponenten des Antriebsstrangs sind redundant verbaut. Insgesamt bieten SVAs mit der redundanten Steuerung, der ausfallsicheren Feder und den Eingriffsmöglichkeiten von außen Sicherheit auf verschiedenen Ebenen.
Die Vorteile einer hybriden SVA werden deutlich, wenn man die Lösung mit dem aktuellen Stand der Aktorik vergleicht. Die überwiegende Mehrheit der weltweit eingesetzten Unterwasser-Aktuatoren basiert noch immer auf konventioneller Hydraulik. Diese gemeinsame Konstruktion hat sich in den vergangenen 50 Jahren durch ihre Langlebigkeit und Langzeitsicherheit bewährt. Die Betreiber möchten jedoch den Aufwand reduzieren, der für die Handhabung des Bohrlochventils erforderlich ist, da herkömmliche Hydraulik normalerweise große, zentrale Hydraulikaggregate (HPUs) auf der Oberseite erfordern. Diese versorgen die Antriebe der Brunnenventile über kilometerlange Leitungen, sogenannte Umbilicals, und Jumper mit Flüssigkeit. Bei einer Arbeitstiefe von 3.000 Metern können sich allein in den Leitungen mehrere hundert Liter Flüssigkeit ansammeln. Darüber hinaus erfordert dieser herkömmliche Aufbau zusätzliche hydraulische Akkumulatoren und Wegeventile, um die Betätigung zu steuern und zu befehlen.
Alternativ versuchen Gerätelieferanten, rein elektromechanische Lösungen zu konzipieren. Diese müssen lediglich über Stromkabel versorgt und über eine Datenleitung mit einem Aktuator-Steuermodul (ACM) verbunden werden, das sich entweder auf der Oberseite oder auf dem Meeresboden befindet. Elektromechanische Lösungen haben jedoch sicherheitstechnische Nachteile, da sie keine Möglichkeiten eines externen mechanischen Eingriffs für Anpassungen haben. Und aufgrund ihrer geringeren Leistungsdichte im Vergleich zu hydraulischen Systemen benötigen sie auch größere Gehäuse und elektrische Batterien. Das Design führt zu hoher Reibung, was zu mechanischem Verschleiß an der Kraftübertragung führt und die erforderliche Betriebsdauer von 25 Jahren verkürzt. Aus diesen Gründen haben elektromechanische Lösungen einen entscheidenden Nachteil für Unterwasseranwendungen, wenn eine ausfallsichere Notschließung benötigt wird.
Bis zu 75 Prozent weniger Energieverbrauch
Die Hybrid-SVA vereint die Vorteile hydraulischer und elektromechanischer Lösungen und eliminiert bestehende Nachteile. Der dezentrale, in sich geschlossene Flüssigkeitskreislauf bedeutet, dass das obere HPU, das Unterwasser-Hydrauliksteuermodul und kilometerlange Versorgungsleitungen für die Flüssigkeit nicht mehr erforderlich sind. Der SVA benötigt eine Stromversorgung und eine Datenleitung gemäß den Spezifikationen der Subsea Instrumentation Interface Standardization (SIIS) – ähnlich wie die elektromechanischen Aktuatoren.
Während des Betriebs erzeugt eine hocheffiziente rotierende Hydraulikpumpe mit konstanter Verdrängung und variabler Verdrängung eine Strömung, um den reibungsarmen Zylinder anzutreiben. Das Hydrauliksystem wird vereinfacht, da keine Proportionalventile benötigt werden, was die Energieeffizienz deutlich erhöht. Im Vergleich zu rein elektromechanischen Aktoren verbrauchen SVAs bei Spitzenleistung bis zu 75 Prozent weniger Strom.
Betrachtet man alle Aktuatoren, die zum Betrieb eines Unterwasserfeldes verwendet werden, kann eine enorme Kostenersparnis allein für die elektrische Infrastruktur (Stromkabel, Transformator, Frequenzumrichter usw.) gegenüber beispielsweise der Verwendung von elektromechanischen Aktuatoren erreicht werden ( Abbildung 3). Der die Hydraulikpumpe antreibende Elektromotor kann dann bei gleicher Stellkraft der Aktuatoren deutlich kleiner ausgelegt werden, was wiederum Bauraum und Kosten spart. Weitere Kosteneinsparungen können auch erzielt werden, wenn die hydraulische Versorgungsleitung durch eine elektrische Versorgungsleitung ersetzt wird, und es besteht keine Notwendigkeit, Hydraulikflüssigkeit zu entsorgen, die für herkömmliche hydraulische Aktuatoren erforderlich ist.

Darüber hinaus bietet der SVA Condition-Monitoring-Möglichkeiten mit eingebauter Sensorik, die die Betriebszustände innerhalb des Stellantriebs kontinuierlich erfasst und an die übergeordnete übergeordnete Steuerung meldet. Anschließend können Trends analysiert werden, wodurch Abweichungen frühzeitig erkannt und behoben werden können.
Bewährte Technologie aus industriellen Anwendungen
Das Funktionsprinzip für die SVA stammt aus der akzeptierten Verwendung von in sich geschlossenen Achsen, die häufig in industriellen Anwendungen zu finden sind. Einzelkomponenten für die SVA werden in Großserien unter Qualitätsmanagementsystemen, wie sie auch in Industriemaschinen eingesetzt werden, gefertigt. Diese Standardisierung reduziert Kosten und schafft eine langfristige Verfügbarkeit für die Produktion. Darüber hinaus haben sich die im SVA verwendeten Sensoren und Elektroniken durch den Einsatz in Kraftfahrzeuganwendungen als zuverlässig erwiesen. Wo erforderlich, wurden Modifikationen an den Komponenten vorgenommen, um für den Tiefseeeinsatz in Tiefen bis zu 6.000 Metern geeignet zu sein. Das System und die Kernkomponenten erfüllen auch die speziellen Anforderungen der verschiedenen Klassifikationsgesellschaften für den Marine-, Offshore- und Subsea-Einsatz.
Innerhalb des SVA gibt es aufgrund des redundanten Druckausgleichssystems auf jeder Tiefe zwei Bar Überdruck. Dies verhindert das Eindringen von Salzwasser und die Notwendigkeit großer Gehäuse mit druckneutraler Bauweise. Zusätzlich zu den Standardanforderungen werden innerhalb der Achse nur unterseetaugliche Kabel und Verbindungen verwendet. Alle nicht unterseetauglichen elektrischen Komponenten sind zusätzlich mit druckfesten Teilen mechanisch und elektrisch gekapselt.
In enger Zusammenarbeit mit führenden Gerätelieferanten und -betreibern wurde die neueste Simulationstechnologie eingesetzt, um den Machbarkeitsnachweis und Prototypen für Feldversuche zu erstellen. Diese innovative Antriebstechnologie kombiniert das Beste aus Elektromechanik und Hydraulik, um eine sichere und zuverlässige Bewegungssteuerung auf dem Meeresboden zu gewährleisten und die Vision einer „All-Subsea-Factory“ Wirklichkeit werden zu lassen.
Dieser Artikel wurde von Dr. Alexandre Orth, Head of Marine &Subsea Technologies, und Amadeu Placido Neto, Test Engineer, bei Bosch Rexroth Corp. (Plymouth, MI) verfasst. Weitere Informationen finden Sie hier .
Sensor
- AeroLas erforscht neue Spinntechnologie für thermoplastisches Hybridgarn
- Neuerungen bei MEMS-Sensoren für Wearables
- Intelligentere pneumatische Ventile verbessern Automatisierungssysteme
- Neue Funktionen für griffunterstützende Handschuhe
- Fragen und Antworten:Eine neue Methode für den 3D-Druck winziger Gelstrukturen
- 4 Anwendungen für hydraulische Klemmen
- Was ist ein Ablassventil?
- Eine Einführung in motorisierte Kugelhähne
- Den Ventiltrieb eines Autos verstehen
- Wie funktioniert ein hydraulisches Durchflussregelventil?