Revolution des Kostenparadigmas für Verbundwerkstoffe, Teil 2:Formen
Das Unterprogramm RAPM innerhalb des Tailorable Feedstock and Forming (TFF)-Programms von DARPA hat analytische Daten aus der aktuellen/vergangenen Produktion sowie empirische Daten aus eigenen Umformversuchen für mehrere Teile zusammengestellt, um diese Kurven zu generieren. Ziel ist es, den Handelsraum für Verbundteile und -prozesse besser zu verstehen.
Quelle für alle Bilder:The Boeing Co., DARPA
Das Programm Tailorable Feedstock and Forming (TFF) wurde 2015 von der Defense Advanced Research Projects Agency (DARPA, Arlington, Virginia, USA) ins Leben gerufen, um eine schnelle, kostengünstige und flexible Herstellung kleiner, komplex geformter Verbundteile für die Verteidigung zu ermöglichen Flugzeug. Dieses 48-monatige Programm zielte darauf ab, die Kostenwettbewerbsfähigkeit von Verbundwerkstoffen zu erhöhen, um deren Gewichtseinsparungen und Korrosions- und Rissbeständigkeit gegenüber bearbeitetem Aluminium zu nutzen. In Teil 1 dieser Serie, CW untersuchte die Vision von TFF und sein Unterprogramm Tailorable Universal Feedstock for Forming (TuFF), das ein kurzfaseriges Plattenmaterial mit hohen mechanischen Eigenschaften und metallähnlicher Umformbarkeit entwickelte.
In diesem Artikel verlagert sich der Fokus vom Rohstoff zum Umformen mit dem zweiten Unterprogramm von TFF:RApid High-Performance Manufacturing (RAPM, ausgesprochen „wrap-em“), geleitet von The Boeing Co. (Chicago, Illinois, USA). Das Programm begann im Juli 2016 und hat seine Ergebnisse in zahlreichen Veröffentlichungen präsentiert, darunter 6 Vorträge und zwei Präsentationen auf der SAMPE 2019. Das Ziel von RAPM, wie die Boeing Technical Fellows und Hauptforscher Gail Hahn und Tom Tsotsis erklärten, ist es, „das Kostenparadigma für kleine Verbundteile, die den weit verbreiteten Einsatz in Verteidigungsanwendungen ermöglichen.“
„Wir haben mit dieser Vision begonnen, Luft- und Raumfahrtleistung mit automobiler Effizienz zu erreichen“, sagt Hahn. Das Programm arbeitete mit Automobilherstellern von Verbundwerkstoffen und -teilen zusammen, darunter Solvay Composite Materials (Alpharetta, Georgia, USA) und SGL Composites (Ried und Ort im Innkreis, Österreich), aber das Erreichen von Luft- und Raumfahrteigenschaften war nicht immer einfach. „Obwohl bei niedriger Temperatur schnell härtende Epoxide für Automobilanwendungen leicht erhältlich sind, erfüllen sie die Anforderungen der Luft- und Raumfahrt nicht annähernd“, sagt Tsotsis. RAPM hat neue, schnell härtende, zweiteilige Epoxide verwendet, die auf Harzinfusionsteile in Luft- und Raumfahrtqualität abzielen. Allerdings konnte das Spritzgusssystem bei SGL anfangs 130°C nicht überschreiten, was das Erreichen des Ziels von 30 Minuten Werkzeugzeit verhinderte.
„Unser Ziel war es, eine maximale Werkzeugzeit von 30 Minuten zu erreichen, um den Einsatz einer Hochgeschwindigkeits-Arbeitszelle zu ermöglichen, um die Kosten auf Systemebene zu senken und mit bearbeitetem Aluminium konkurrenzfähig zu sein“, sagt Tsotsis. „Bei Boeing haben wir entschieden, dass dies alles erfüllen würde, was wir für Verteidigungsanwendungen sahen“, fügt Hahn hinzu. „Warum hier setzen, wenn wir mit Thermoplasten 2 bis 6 Minuten schaffen? Weil Thermoplaste eine noch höhere Verarbeitungstemperatur mit entsprechenden Werkzeugbeschränkungen erfordern, und unser Ziel ist es, unserer Lieferkette viele Optionen zu geben.“
Im weiteren Verlauf des Programms öffnete es sich für Luft- und Raumfahrtmaterialien und -hersteller und sogar für experimentelle Systeme wie Solvays XEP-2750. „Wir dachten ursprünglich, wir könnten dieses System vollständig evaluieren, wie wir es mit CYCOM 5320-1 in unserer Arbeit mit dem DARPA-Programm ‚Non-Autoclave Manufacturing Technology‘ von 2007 bis 2012 getan haben“, sagt Hahn. Obwohl derselbe Grad der Bewertung nicht möglich war, wurde XEP-2750 jetzt von Solvay als CYCOM EP-2750 kommerzialisiert (siehe Online-Seitenleiste „Neuartiges Prepreg für das Formpressen in RAPM ”) und profitierte von den zahlreichen RAPM-Teilversuchen und gewonnenen Erkenntnissen.
„Alles, was ich will, sind ein paar Verfahren für kleine Verbundteile, die in einer Handelsstudie gegen Aluminium gewinnen können“, sagt Jeff Hendrix, Berater für Verbundwerkstoffindustrie und TFF-Programm, über seine Ziele für RAPM. Ist RAPM also erfolgreich? CW untersucht die Bemühungen des Programms, Hunderte von Teilen herzustellen, vergleicht mehr als ein Dutzend Konfigurationen von Luft- und Raumfahrtteilen mit mehreren Materialien und Prozessen und verfolgt gleichzeitig Methoden zur Reduzierung von Zeit und Kosten.
Programmrahmen
In Zusammenarbeit mit wichtigen Industriepartnern testete RAPM Teile in drei Hauptbereichen:
- Harzinfusion mit HITCO Carbon Composites (Gardena, Kalifornien, USA) und SGL Composites
- Duroplastisches Prepreg Umformen mit Solvay Composite Materials (Heanor, Großbritannien und Anaheim, Kalifornien, USA), Fiber Dynamics (Wichita, Kanada, USA) und Reinhold Industries (Santa Fe Springs, Kalifornien, USA)
- Thermoplastisches Umformen mit ATC Manufacturing Inc. (Post Falls, Idaho, USA) und TxV Aero (Bristol, R.I., USA)
Umformversuche wurden in zwei Phasen abgeschlossen:einer anfänglichen Phase „Manufacturing Development“ (Abb. 1) gefolgt von nachfolgenden „Challenge and Transition“ (C&T)-Teilen (Abb. 2) bis hin zur Challenge erste Entwicklungen und Übergang Kandidaten mit Potenzial, gegen bearbeitetes Aluminium zu gewinnen.
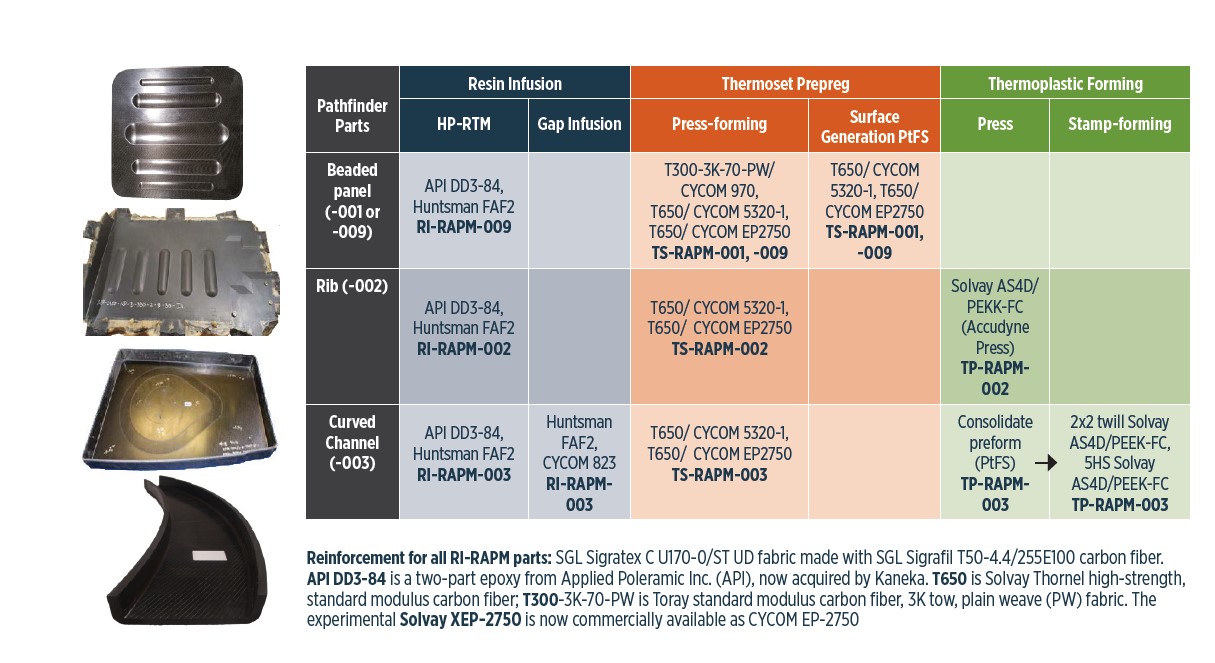
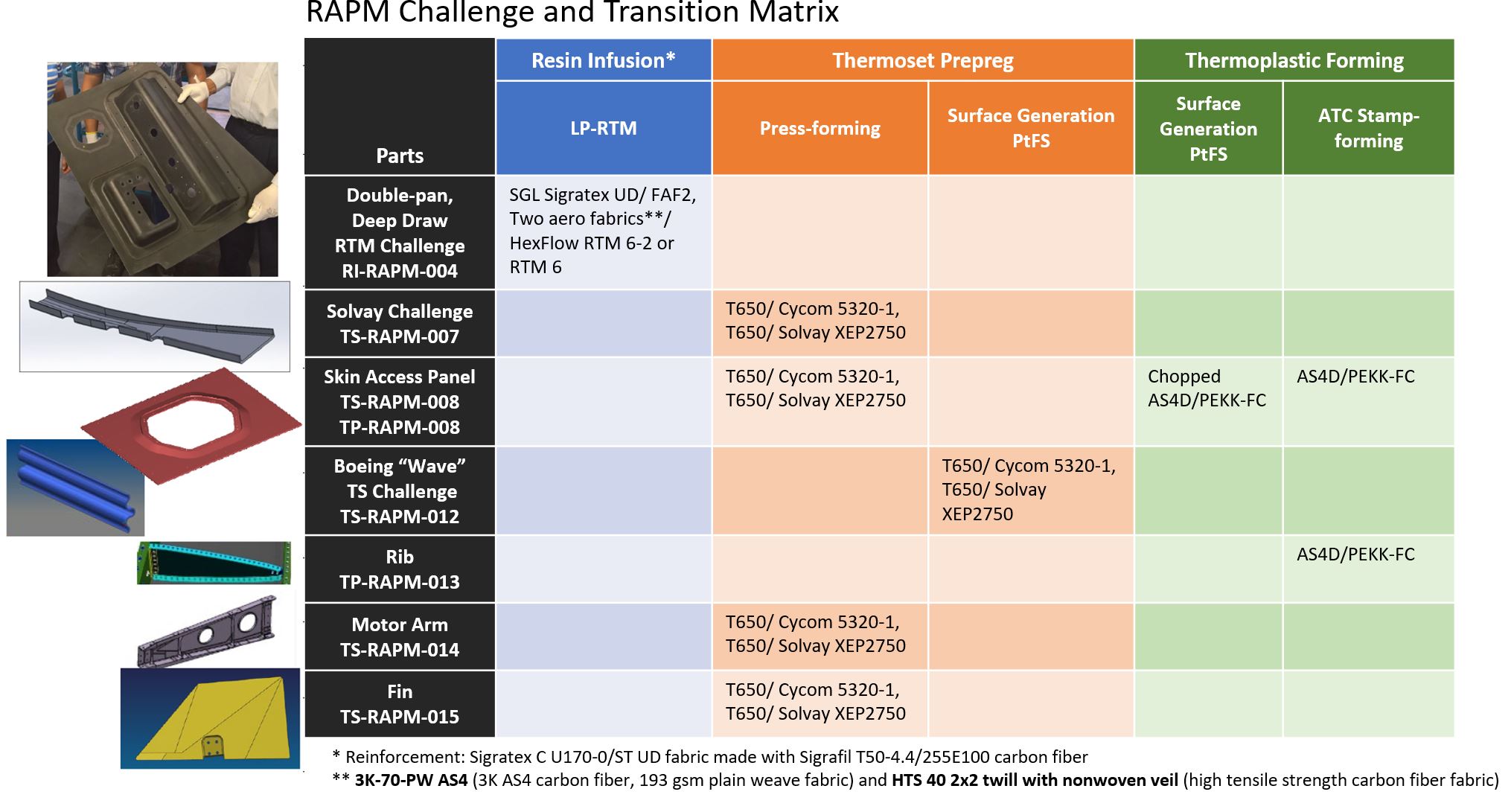
Fertigungsentwicklung Versuche verwendeten drei Hauptteilkonfigurationen:Wulstplatten (es gab zwei Arten), eine Rippe mit Polstern (Schichtaufbau) und ein gebogener C-Kanal. Diese integrierten Merkmale, die bei Teilen der Luft- und Raumfahrt üblich sind, die zu Herausforderungen bei der Herstellung führen können:Die Wulstplatte wies mehrere Merkmale außerhalb der Ebene sowie Auf- und Abwärtspolster und eine vertikale Kante auf; die Rippenplatte hatte eine Polsterung mit mehreren 90-Grad-Kanten sowie eine Jogging-Einfassung an einer der Kanten; und der C-Kanal hatte einen unterschiedlichen Innen- und Außenradius, unterschiedliche Krümmungen in den Flanschen und signifikante Lagenabfälle in der Bahn.
Ziel war es, für jedes der drei Gleise Design- und Herstellungsrichtlinien zu entwickeln. „Bei diesen ersten Versuchen sah es nicht sexy aus“, erinnert sich Hahn. „Aber sie halfen dabei, akzeptable Radien und Teilegeometrien zu bestimmen, die Teile ohne unerwünschte Faserverzerrung sowie optimale Kombinationen von Parametern wie aufgebrachte Spannung, Temperatur, Druck und Zeit am Werkzeug produzieren würden.“
Alle drei RAPM-Material- und Prozesstracks umfassten Versuche mit einem pixelierten Heizsteuerungs- und Werkzeugsystem für die Oberflächengeneration (Rutland, Großbritannien) Production to Functional Specification (PtFS) (siehe Online-Seitenleiste „RAPM-Entwicklung mit PtFS .). “), angesiedelt bei Boeing R&T in St. Louis, Missouri, USA. „Dies geschah, weil wir nach einer Arbeitszelle suchten, die alle drei Arten von Materialien/Prozessen in einer flexiblen Tarifumgebung abdecken konnte“, sagt Hahn. „Wir konnten verschiedene Ansätze und Kosten für die Temperaturregelung untersuchen.“ Die Boeing PtFS-Zelle hat eine maximale Temperatur von 440 °C, eine Schließkraft von 150 Tonnen und ein effektives Teilevolumen von 750 x 750 x 100 Millimeter.
Obwohl die ursprüngliche Vision darin bestand, TuFF-Kurzfaserplatten zu verwenden, da diese zu Beginn nicht verfügbar waren, ging RAPM mit Ersatzmaterialien vor. Dies ist tatsächlich von Vorteil für die Verbundwerkstoffindustrie, da die Surrogate Materialien umfassen, die besser reflektieren, was außerhalb dieses Projekts verwendet und entwickelt wird:Automobilorganobleche und für die Luft- und Raumfahrt geeignete Prepregs, experimentelle Epoxide, teilkristalline Thermoplaste und geschnittene Prepreg-Compounds. Somit beziehen sich die Ergebnisse und Erkenntnisse auf alle Arten von Verbundwerkstoffherstellern, nicht nur auf die im Verteidigungsbereich.
Track 1:Harzinfusion/RTM-Herstellung
Die Versuche zur Herstellungsentwicklung in diesem Bereich begannen mit automobilähnlichen Materialien und Prozessen. Die Teile wurden von SGL Composites unter Verwendung von Hochdruck-Harzspritzpressen (HP-RTM, 300 bar) und C T50 Standardmodul, 50K Carbonfaser-Gelege (SGL Carbon in Wackersdorf, Deutschland) in dreiteiligen Konfigurationen hergestellt:RI-RAPM-009 , RI-RAPM-002, RI-RAPM-003 (Abb. 1). Diese wurden verwendet, um Preform-Parameter zu identifizieren, die für hochwertige Fertigteile erforderlich sind. Gap-Infusion (Kompressions-RTM oder C-RTM) wurde auch für RI-RAPM-003 von Boeing St. Louis mit seinem PtFS-System getestet.
Computergestützte Strömungsmodellierung wurde verwendet, um die Infusion dieser Teile besser zu verstehen, das Prozessverhalten zu analysieren, um Materialien und Prozessparameter zu optimieren und Einspritzszenarien zu bewerten.
Werkzeugansätze wurden dahingehend bewertet, wie und wann Spannung auf verschiedene Arten von Vorformgeometrien aufgebracht werden sollte, um die Faserverzerrung zu minimieren. Diese Designänderungen wurden für eine modifizierte C-Kanal-Geometrie validiert, gefolgt von Computertomographie (CT)-Analysen. Die gewonnenen Erkenntnisse wurden in der anschließenden C&T-Phase angewendet und auf Niederdruck-RTM (LP-RTM) umgestellt, um die Kosten zu senken.
Bei diesen Pathfinder-Teilversuchen wurden Delaminationen in mehreren der Tiefziehradien festgestellt. Tsotsis glaubt, dass diese durch eine Kombination aus unzureichender anfänglicher Aushärtung des Harzes im Werkzeug verursacht wurden – weil das Dampfheizsystem von SGL die Temperatur im Werkzeug auf 130 °C begrenzte – und thermischen/mechanischen Spannungen außerhalb der Ebene während der Teileentnahme. „Da die Harzfestigkeit noch nicht ausreichend entwickelt war, hätten diese Anomalien wahrscheinlich durch vollständiges Aushärten des Werkzeugs beseitigt werden können“, schlägt er vor. „SGL konnte nicht beide Zeiten bei Tool und erfüllen Luft- und Raumfahrteigenschaften, bis dem Werkzeug Ölheizung (im Gegensatz zu nur Dampf) hinzugefügt wurde, was eine Härtung über 130°C ermöglicht“, bemerkt Hahn. Dies wurde nach den Entwicklungsversuchen in der Fertigung hinzugefügt.
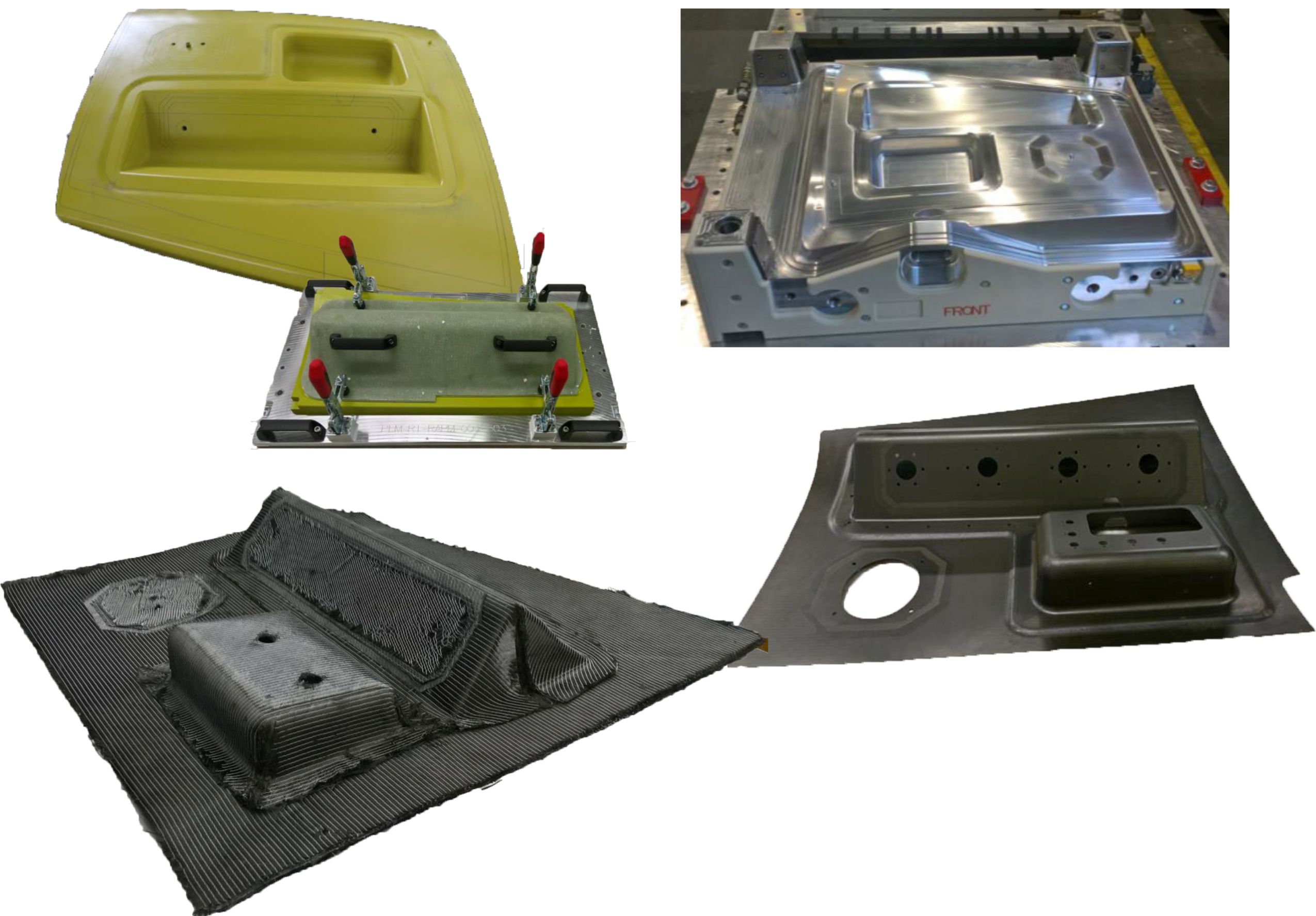
Deep-Draw-Challenge-Teil
Die Ergebnisse der Herstellungsentwicklungsversuche wurden dann verwendet, um Herausforderungs- und Übergangsversuche zu entwickeln. Die Modellierung wurde auch für das Tiefzieh-Herausforderungsteil RI-RAPM-004 (Abb. 3) abgeschlossen, das zwei Tiefziehvorgänge aufweist:einen rechteckigen Bereich von 5 Zentimetern und einen Bereich von 10 Zentimetern, der von einer rechteckigen in eine V-Form übergeht. Inspiriert von einer Produktionswannenbaugruppe sorgte seine komplexe Geometrie für einen ungleichmäßigen Harzflussweg. Huntsman (Basel, Schweiz) führte die Strömungsmodellierung mit PAM RTM-Software (ESI Group, Paris, Frankreich) für einen LP-RTM-Prozess mit FAF2-Zweikomponenten-Epoxid (Huntsman, The Woodlands, Tex., USA) und SGL Carbon NCF 150 . durch -Gramm pro Quadratmeter biaxiale und 190-Gramm pro Quadratmeter unidirektionale (UD) Verstärkungen.
RI-RAPM-004 besteht aus einer Preform für die Haut, einer für jeden der Tiefziehabschnitte sowie zwei Aufbaubereichen (Abb. 3). Für diese Preform-Elemente wurden verschiedene Layups verwendet, um die vorgesehenen Plattendicken zu erfüllen (siehe „Herstellung der Teile mit komplexer Geometrie von RAPM .). “).
„Niederdruck-Preforming und LP-RTM ermöglichten den Einsatz kostengünstiger Werkzeuge (im Vergleich zu Stahl):Das Preform-Werkzeug mit handbetätigten Spannern wurde mit Raku-Tool-Material auf Polyurethanbasis (RAMPF Tooling Solutions, Grafenberg, Deutschland); das Aushärtewerkzeug wurde aus 5083 Aluminium hergestellt.
Anfängliche RI-RAPM-004-Versuche zeigten eine unerwartete Anomalie in der Strömung in der Nähe des Austritts, die die Oberflächenlagen anhob und eine Faserverzerrung verursachte. Das Vertauschen von Einlass und Auslass hat das Problem behoben. Nach Infusion und anfänglicher Härtung in einem 130°C-Werkzeug wurden die Teile 60 Minuten bei 180°C nachgehärtet und dann maschinell in die Endform gebracht. Zehn hochwertige Teile wurden für C-Scans mit automatisierten Ultraschallsystemen (AUSS) an Boeing geliefert.
Die fertigen Challenge-Teile zeigten eine vollständige Konsolidierung, eine ausgezeichnete Faserausrichtung und eine gute Qualität. Die Teile zeigten eine Glasübergangstemperatur von 197 °C und einen Faservolumenanteil (FVF) von 49,5%, typisch für den verwendeten NCF. Die Stückzahl beim Auflegen von Teilen wurde im Vergleich zum aktuellen Prepreg-Verfahren um mehr als zwei Drittel reduziert, und der Berührungsaufwand sank um schätzungsweise 90 %. RAPM hat die Herausforderung auch mit für die Luft- und Raumfahrt qualifizierten Harzen und Geweben gemacht – um die Anpassungsfähigkeit der von ihm entwickelten Werkzeuge und Prozesse zu testen – und Teile hergestellt, die die Produktionsanforderungen für die zerstörungsfreie Prüfung (ZfP) bestanden haben.
Track 2:TS-Prepreg-Formung

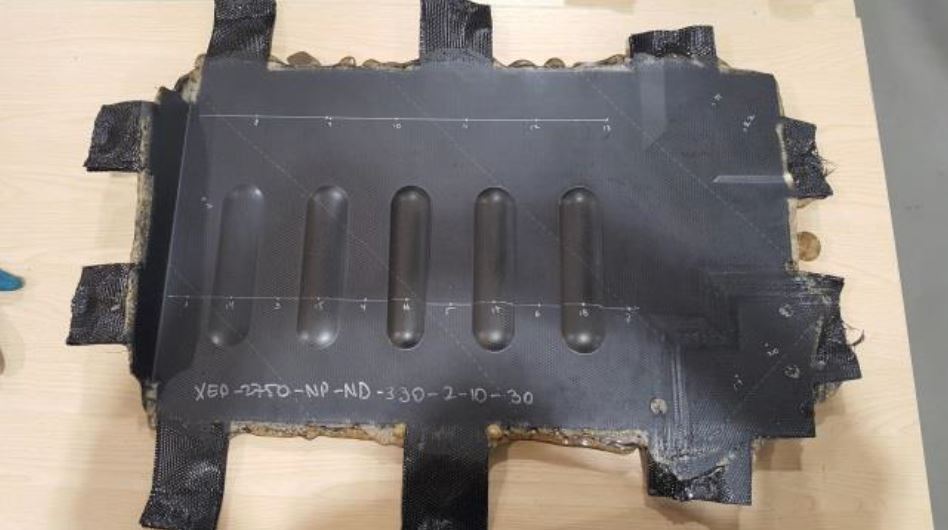
Drei duroplastische (TS) Prepreg-Teile für die Fertigungsentwicklung wurden im Anwendungszentrum von Solvay in Heanor, Großbritannien, unter Verwendung von Federrahmenstanzen und/oder Doppelmembranumformung (DDF) hergestellt. Alle drei Teile wurden unter Verwendung von Epoxid-Prepregs auf Basis von Solvay-Harzen hergestellt, darunter CYCOM 5320-1, CYCOM 970 und das CYCOM EP-2750-Luft- und Raumfahrtsystem. „CYCOM 5320-1 ist unsere erste Wahl für Teile außerhalb des Autoklaven (OOA), wird aber auch als qualifiziertes System für den Autoklaven verwendet“, sagt Hahn. „CYCOM 970 ist eine Lösungsmittel- versus Hotmelt-Prepreg-Option, und [CYCOM] EP-2750 ist unser System für das Pressformen, weil es für die Physik und Kinetik des Prozesses optimiert ist, der, wie wir gezeigt haben, die besten Teile produziert.“
Spring-Frame-Stanzen und DDF sind isotherme Formpressverfahren, bei denen duroplastische Prepregs geschnitten, zusammengestellt und zu einem 2D-Preform konsolidiert werden. Der Vorformling wird dann vorgewärmt, in passende Metallwerkzeuge transportiert und in einer herkömmlichen hydraulischen Plattenpresse in Form gebracht. Der Vorformling kann durch einen Federrahmen (Abb. 4) unter Spannung gehalten werden, wodurch die durch Materialkompressionszonen während des Formens verursachte Faltenbildung reduziert wird. Alternativ klemmt DDF den Vorformling zwischen zwei Membranen, wodurch das Reinigen und Trennen der Form überflüssig wird. Der Vorformling wird auf eine der Membranen geklebt und hält sie im Wesentlichen unter Spannung, wenn auch nicht so direkt oder konfektionierbar wie mit einem Federrahmen. In RAPM wurden Federtyp, Lage und Spannung für jedes Teil ebenso wie der Federrahmen mittels Simulation optimiert. Zum Beispiel verwendet die Wulstplatte TS-RAPM-009 einen Rahmen, der sich nach oben und unten bewegen kann, um die Formung der Charge parallel zum Pressenschließen anzupassen.
RAPM minimierte die Teile-auf-Werkzeug-Zeit, indem formstabile Teile nach einer 15-30-minütigen anfänglichen Härtung und anschließender Chargennachhärtung entfernt wurden, um die Leistungsfähigkeit zu erhöhen. Teilefamilien wurden auch mit einem einzigen Toolset untersucht – z. B. einem C-Kanal mit drei unterschiedlichen Flanschwinkeln entlang der Länge eines Flügels – um die Zellnutzung zu maximieren. Andere Ziele, die den RAPM TS-Ansatz leiten, waren:
- Automatisiertes Sortieren und Formen zur Minimierung der Handarbeit
- Mechanische Leistung in der Luft- und Raumfahrt mit 177°C Aushärtung
- Stahlwerkzeug für>1.000 Teile pro Werkzeugsatz.
Entwicklung zum Herausforderungsteil "Welle"
Es wurden Entwicklungsteile für die Herstellung von Duroplast-Prepregs geformt, wobei jeweils eine Variable indexiert wurde, bis eine ausreichende Teilequalität erreicht war. Variablen wie Schließgeschwindigkeit der Presse, Schließposition und Schließdruck wurden mit dem Ziel bewertet, das Material an der richtigen Stelle in der Rheologiekurve zu verfestigen, um einen internen hydrostatischen Druck zu erzeugen, das Harzausbluten zu minimieren und ein zu weites Fortschreiten der Aushärtung zu verhindern, um Risse zu vermeiden Induktion. Nachdem die Umformparameter eingestellt waren, wurden drei bis fünf Teile hergestellt, um die Wiederholbarkeit des Prozesses zu überprüfen und dann auf Qualität getestet. Die gesickten Platten zeigten aufgrund hoher Verfestigungsdrücke (20,7 bar) eine Porosität von <0,5 %. Es wurden auch wiederholbare, hochwertige Rippen hergestellt.
Die gewonnenen Erkenntnisse wurden dann auf das gewellte „Wellen“-Herausforderungsteil TS-RAPM-012 angewendet, um das Formpressen von dicken (6,3 Millimeter Nenndicke) UD-Laminaten in Formen mit engem Krümmungsradius (12,7 Millimeter) zu demonstrieren. Um die Anforderungen zu erfüllen, verwendete das Teil ein quasi-isotropes UD-Band aus Kohlefaser mit mittlerem Modul (IM7; Hexcel; Stamford, Connecticut, USA). Äußere Lagen aus Glasfasergewebe des Typs 108 und Solvay THORNEL T650 Standard-Modulus-Carbonfaser in einem 8-Harness-Satingewebe schützen die UD-Fasern und verhindern galvanische Korrosion auf der Seite, die mit einem Metallteil verbunden ist. Die Verwendung von Solvay CYCOM 5320-1 Epoxidharz ermöglichte kürzere (≤ 30 Minuten) isotherme Härtungszyklen mit einer 2-stündigen freistehenden Nachhärtung bei 177°C.
Das Wellenherausforderungsteil wurde unter Verwendung der PtFS-Arbeitszelle von Boeing und P20-Stahlformflächen mit integrierten Vakuum- und Harzdichtungen geformt. Der Werkzeughohlraum war dünner als die nominale Laminatdicke, um Schwankungen im Harzgehalt des Materials zu berücksichtigen und den hydrostatischen Innendruck für hochwertige Teile aufrechtzuerhalten.
Drei Prozessparameter wurden getestet, darunter Kaltumformung (Vorformen von Lagen ohne Hitze), Heißdebulk-Vorverfestigung und Vorwärmen des Vorformlings. Die Kaltumformung wurde als zeitaufwendig und nicht hilfreich abgelehnt. Zur Vorverfestigung wurden die Laminate zu einer Platte mit einem gewebten Glasfaser-Entlüfter vakuumverpackt und unter vollem Vakuum in einem 116°C-Ofen für 40 Minuten entbaucht. Obwohl eine automatisierte Infrarotvorwärmung Standard für die industrielle Produktion ist, umfasste das Vorwärmen in diesen Versuchen das Einlegen des Vorformlings in die heiße Form (179 °C) und das Schließen so weit wie möglich ohne Berührung für 3 Minuten. Das Teil wurde dann formgepresst.
Versuch 8 der neun abgeschlossenen (#0-8) ergab das qualitativ hochwertigste Teil, was hauptsächlich auf die Vorkonsolidierung zurückzuführen ist. Daraus entnommene Proben entsprachen der Dicke (ein Problem bei anderen Teilen) und der Laminatqualität mit einem Faservolumen von 59-63% und einem Hohlraumgehalt von 0-0,6%.
Track 3:Blasenförmige TP-Rippe und C-Kanal
RAPM wählte die Rippe TP-RAPM-002 aus den Entwicklungsversuchen in der Fertigung, um das einstufige Formpressen vom Rohmaterial bis zum fertigen komplexen Teil zu demonstrieren, und den gebogenen Kanal TP-RAPM-003 für einen zweistufigen Ansatz. Boeing St. Louis formte die -002-Rippe unter Verwendung einer Accudyne Systems (Del., USA)-Presse und konsolidierte Rohlinge für den -003-C-Kanal unter Verwendung der PtFS-Ausrüstung. In einem zweiten Schritt stanzte ATC Manufacturing die C-Kanal-Rohlinge in Teile.
Für die -002-Rippe verwendete RAPM ein 12 Zoll breites UD-Band von Solvay:12K AS4D Kohlefaser (Hexcel, Stamford, Connecticut, USA) verstärktes Polyetherketonketon (PEKK). Das verwendete -003 C-Kanal-Gewebe von Cramer Fabrics Inc. (Dover, N.H., USA):3K AS4 (Hexcel) ungeschlichtete Kohlefaser in einem 2x2-Köper, pulverbeschichtet mit Polyetheretherketon (PEEK); Faserflächengewicht beträgt 250 Gramm/m²; Harzgehalt beträgt 42%.
Probleme bei der thermoplastischen (TP) Umformung
TP-Verbundwerkstoffe werden bei höheren Temperaturen verarbeitet als Duroplaste – z. B. 390 °C für PEEK und 375 °C für PEKK – was eine Reihe von Problemen aufwirft. Werkzeugmaterialien, die diesen hohen Prozesstemperaturen standhalten können, sind begrenzt. Außerdem macht es der große Temperaturunterschied zwischen der Teilebearbeitung und dem Entfernen schwierig, eine gleichmäßige Werkzeugtemperatur aufrechtzuerhalten. Abhilfe schaffen Hitzeeinlagerungen und/oder langsamere Rampen nach oben und unten, die die Zykluszeiten verlängern.
Die hohen Temperaturen stellen auch eine Herausforderung für den Wärmeausdehnungskoeffizienten (CTE) dar. Der WAK des Werkzeugmaterials unterscheidet sich oft von dem des TP-Laminats, was dazu führen kann, dass das TP-Laminat vom Werkzeug wegschrumpft, der ausgeübte Druck verringert und eine vollständige Verfestigung verhindert wird. Außerdem ist der CTE des TP-Laminats entlang der Kohlefaser konstant, jedoch eine bilineare Kurve senkrecht zur Faser. Dies führt zu unterschiedlicher Schrumpfung in der Ebene und außerhalb der Ebene, wenn sich das TP-Laminat erwärmt und abkühlt, und sollte auch bei der Werkzeugkonstruktion berücksichtigt werden.
TP-Laminate können auch von Werkzeugen schrumpfen, wenn das Harzvolumen mit dem Übergang von flüssig zu fest abnimmt. Während dieser Abkühlphase, wenn eine kritische Harzmatrixkristallisation auftritt, ist eine genaue Kontrolle der Temperaturgleichmäßigkeit und des Laminatdrucks erforderlich, um hochwertige Eigenschaften des fertigen Teils zu gewährleisten.
Ein weiteres Problem besteht darin, dass Werkzeuge vollständig abgedichtet werden müssen, um die geschmolzene TP-Flüssigkeit während des Formens aufzunehmen. „Ein Werkzeug bei 375°C bis 390°C abzudichten ist schwierig, da es nur sehr wenige anpassungsfähige Dichtungen gibt, die dieser Temperatur standhalten und TP-Umformdrücke von 300 bis 500 psi oder mehr“, sagt Hahn. „Wir sind auf Metalldichtungen oder aufeinander abgestimmte Metallwerkzeuge beschränkt, um die Dichtungseigenschaften bereitzustellen. Elastomer-Werkzeuge wären unglaublich vorteilhaft, aber alle aktuellen Elastomere zersetzen sich bei TP-Umformtemperaturen.“
Boeing St. Louis benötigte neuartige Werkzeuge, um während der Konsolidierung in einer hydraulischen Presse, die nur über eine vertikale Betätigung verfügte, einen horizontalen Druck auf die vertikalen Elemente der Rippe zu erzeugen. Seine Lösung war eine dünne Aluminiumblase (ein ähnliches System wurde verwendet, um TP-RAPM-003 zu bilden, Fig. 5). Bei hohen Temperaturen mit inertem Argongas unter Druck gesetzt, expandierte die Blase, um während der Konsolidierung gleichmäßigen Druck auf alle Teileoberflächen auszuüben.
Ober- und Unterwerkzeuge wurden aus Edelstahl 410 hergestellt, der dem WAK in der Ebene des UD-Kohlefaser/PEKK-Laminats entsprach. Während des Presszyklus kam das Oberwerkzeug mit der Aluminiumblase nach unten und presste das Layup langsam in die Matrize des Unterwerkzeugs. Die Blase hatte eine Unterdimensionierung von 30% gegenüber der endgültigen Teildicke, um die Masse des nicht verfestigten Bandvorformlings in diesem einstufigen Verfahren aufzunehmen. Dieses Werkzeug wurde in eine konventionelle Presse mit elektrischen Heizpatronen eingebaut, die in 12 unabhängig gesteuerten Zonen – plus den sechs Hauptzonen der Pressenplatte – verdrahtet waren, um die Werkzeugoberflächentemperatur in den Flanschen und dem Steg der Rippe zu steuern.
Diese Umformversuche ergaben Verbundteile mit passablen NDI-Ergebnissen. Das Design des Blasenwerkzeugs erfordert jedoch eine Weiterentwicklung, um das Umformen des Layups in die engen Innenradien des Teils zu verbessern und auch eine gleichmäßige Oberflächendicke beizubehalten.
Konsolidieren von PEEK-Geweberohlingen
Für den gebogenen C-Kanal TP-RAPM-003 hatte das verwendete pulverbeschichtete PEEK 2x2 Köpergewebe einen relativ hohen Bauschfaktor. Boeing St. Louis first consolidated the layup, which dropped from 32 to 24 plies along the length of the part, into a flat blank with a tapered cross-section, and then sent the blanks to ATC Manufacturing, which stamped the final part with vertical flanges.
As with the rib, Boeing used a forming bladder and steel top and bottom tools. The bladder was changed to AZ31 magnesium, which better resists rupture versus aluminum. The C-channel tool was designed to operate within the Surface Generation PtFS forming cell to enable more rapid heating and cooling versus the conventional press with cartridge heaters used for the rib.
The C-channel tooling approach was developed to increase flexibility for multiple parts. The layup was placed onto the bottom tool, which was heated to the material’s glass transition temperature (Tg ) to maintain pliability without melting. A volume reducing frame that included a pressure-sealing gasket was placed on top of the bottom tool, leaving a cavity slightly larger than the part layup (Fig. 5). Heat and hydraulic pressure were applied from the top tool through the bladder to the layup. Once at forming temperature, argon gas was applied to the bladder, forcing it down into the frame cavity to apply pressure to the tapered blank. The tool temperature was then increased through the melt phase of the material while maintaining bladder pressure, which prevented material from flowing across the lower tool while in melt phase.
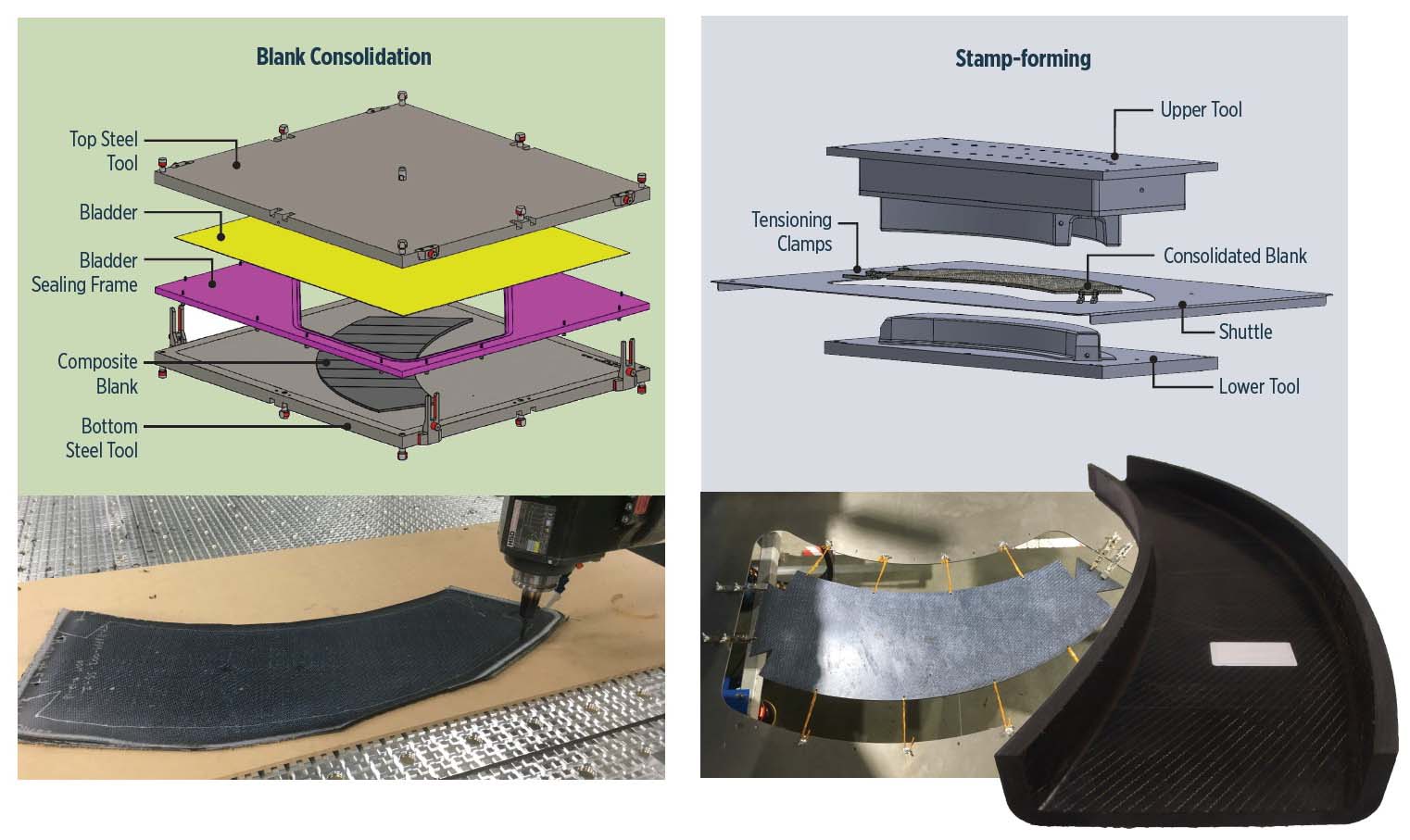
Preforming cycle time comprised 55 minutes for bladder and TP charge to reach process temperature and 30 minutes to cool below the PEEK crystallization temperature. Pressure ranged from 1.4 to 9.7 bar and was maintained manually from a high-pressure tank with a valve. With the recent incorporation of a pressclave system into the PtFS cell, autoclave-like control of vacuum and pressure (±3 psi) in the press mold cavity will be automated in the future.
TP stamp-forming
Consolidated blanks for the -003 C-channel were sent to ATC Manufacturing for stamp-forming, in which the blank is heated sufficiently above melt temperature to ensure polymer flow. It was then transferred to a rapidly closing press to form and cool the part quickly. The forming tool in the press is kept at constant temperature, enabling rapid cycle times by eliminating ramp-up and cool-down. The tool temperature must be between melt temperature and Tg to develop the required level of thermoplastic matrix crystallinity in a short time, yet ensure the part can be removed without deformation. A series of blanks with implanted thermocouples was used to validate the complete thermal cycle for stamp-forming the C-channel.
Forming simulations using Aniform software (Enschede, Netherlands) showed the highly drapable PEEK fabric blank still posed a risk of wrinkling in compression areas, namely the inner (smaller radius) flange. Thus, a tensioning system (Fig. 5) comprising shuttle plate and clips held the blank in tension as the matched metal tools closed to form it. Despite this, the flange face in compression still showed buckling as fiber was pushed inward at the inner radius. “All three RAPM tracks struggled to make this part,” Hahn contends. “Its geometry was extreme, and not so indicative of a real part, but more designed to push what we could achieve in formability.”
The manufacturing development trials led to challenge and transition parts that included multiple versions of the TP-RAPM-008 skin access panel, the TP-RAPM-013 rib with joggles on the flanges and a bladder study using three different geometries of the TP-RAPM-017 panel (Fig. 2). Boeing St. Louis produced all of these except for the TP-RAPM-013 rib, which ATC produced. “Even though this part was made with UD tape, which is typically more challenging to form versus fabric, we were able to form these parts very well,” says Trevor McCrae, R&D director for ATC Manufacturing. Overall, the TP forming trials showed that stamp-forming can produce complex geometries that might not be possible with conventional compression molding.
Learning to cut cost vs. aluminum
RAPM has demonstrated novel forming capability in all three tracks and amassed numerous lessons learned, ranging from how to position pad-ups to prevent slippage during compression molding to guidelines for part geometry to maximize quality and minimize tooling cost. “Understanding the effects of out-of-plane features, radius-to-thickness ratio and distance between geometric details becomes key as you move to small parts,” Hahn observes. “Standardizing features such as radii, curves and flange angles can help mitigate cost drivers, for example, reducing tooling costs, the number of forming trials during development and the need for multiple scans during NDI (nondestructive inspection) by enabling a standard AUSS shoe for a family of parts.”
Another cost driver RAPM highlighted was the time-consuming pre-consolidation step during TS prepreg compression molding. “Low-bulk and higher resin content prepregs widen the process window and increase repeatability for high-quality parts,” Hahn explains. “Solvay has developed a patent-pending ‘transformer film’ which can be applied to lower-impregnation prepregs before compression molding as a method of guaranteeing hydrostatic pressure in the mold cavity during consolidation.”
Although RAPM won’t officially end until fall 2020, followed by additional published results, findings so far for selected parts, which are based on real defense programs, show that composites can compete with machined aluminum (Fig. 6). Though the selected resin infusion and TP parts reduce recurring costs — e.g., materials, machine time, etc. calculated over total parts per family assuming non-recurring infrastructure is in place — the TS-RAPM-012 wave assembly actually shows a 7% increase vs. machined aluminum. However, it does achieve desired weight savings, and at a premium that is actually within the margin mandated by Hendrix:“No one is going to pay 2X for the weight savings composites offer; they must cost within 10 percent of aluminum.” However, he does concede, “There are still non-recurring time and cost issues to figure out, such as tooling and the development required to successfully form the shape.”
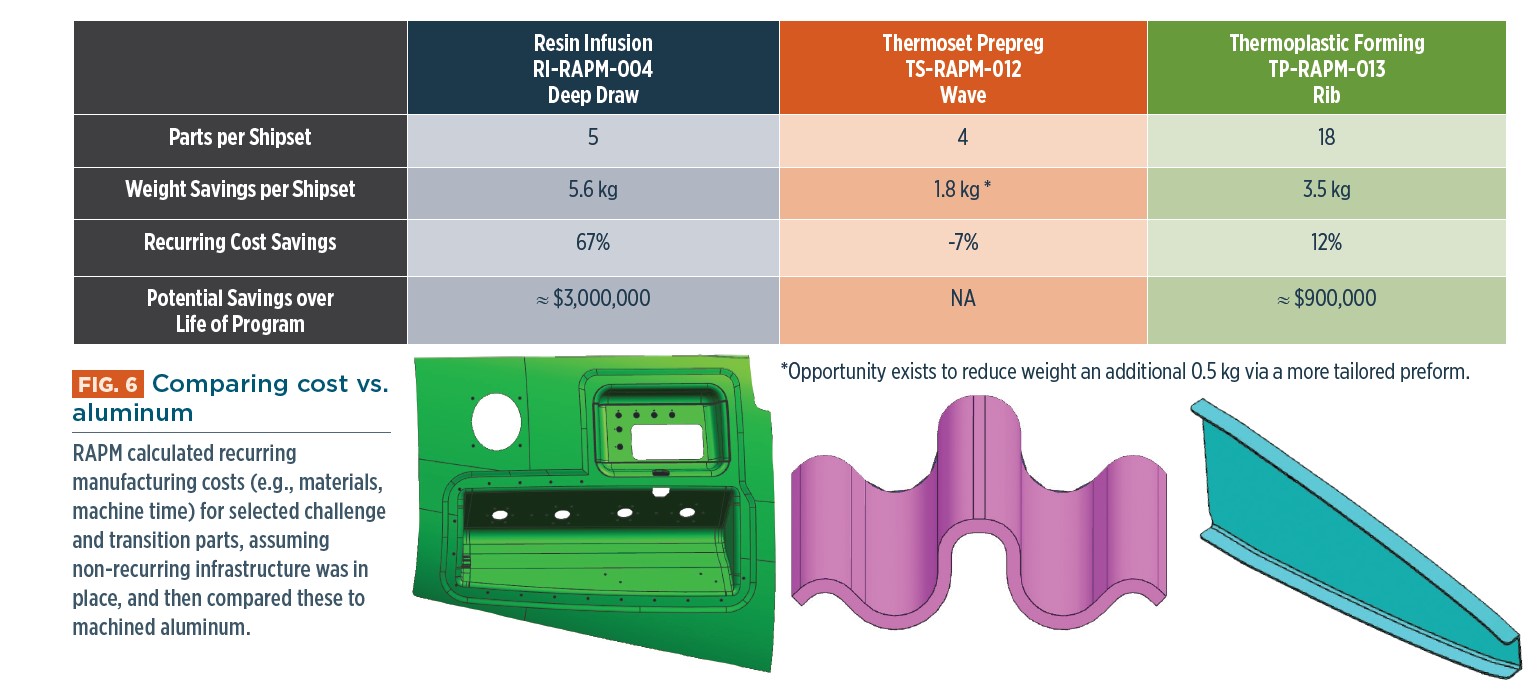
Expanding options
Although resin infusion wins for large parts, says Hahn, TS and TP stamping look pretty good for small parts. “Initial tooling cost for resin infusion is hard to overcome unless the metal parts are very complex, requiring a lot of machining,” she explains.
“Thermoplastics look good for high volume, but a subcontractor for a given program might not be set up to do thermoplastics. However, thermoset stamping might be a very good option, even for low-volume replacement parts. Because defense applications are so wide-ranging, it is important to have more than one material and process in a trade discussion.” Hahn notes that RAPM has opened up new materials and proven aerospace materials can work in automotive-type processes. “We also brought in new manufacturers.”
Hendrix agrees that RAPM’s aerospace and automotive manufacturing exchange was beneficial. Further, he was impressed with Solvay’s and SGL’s ability to form complex shapes without fiber distortion or other defects. “What it takes to make aesthetic auto parts actually has benefits,” he concedes. “You can’t have wrinkles or bad surface finish; they have to be perfect. But it still took multiple trials and significant development for them to form the RAPM parts. I’m not sure defense programs will want to invest in this non-recurring engineering if they’re dealing with small quantities. The economics will be on a case-by-case basis, but tooling and development remain issues we need to address.” Hahn adds, “We are publishing lessons learned, enabling more informed trade studies with expanded options and establishing a reasonably open basis for industry discussion.” CW will continue this discussion with an update once RAPM wraps up later this year.
Harz
- 6 Möglichkeiten, die Kosten des 3D-Drucks zu senken
- Die Frage zur Vertragspflege – Teil I
- Verbundwerkstoffherstellung:Die Herstellung von Verbundwerkstoffen
- Die Ökonomie des 3D-Drucks
- Auf den Spuren der Geschichte polymerer Materialien, Teil 13
- Die Vorteile eines Firmenpalettenprogramms
- ACMA veröffentlicht Programm der Konferenz für Thermoplastische Verbundwerkstoffe 2020
- SAMPE 2018-Keynote blickt in die Zukunft der Verbundwerkstoffe
- Die Kosten der CNC-Bearbeitung
- Der Wert des Feingusses (Teil 2)