Qualitätssicherung für den 3D-Metalldruck:3 häufige Herausforderungen lösen
Qualitätssicherung (QA) ist wohl der wichtigste und zugleich einer der anspruchsvollsten Schritte im 3D-Druck.
Da der 3D-Druck zunehmend in industriellen Hochleistungsanwendungen eingesetzt wird, muss die Technologie konstant und zuverlässig qualitativ hochwertige Teile mit den erforderlichen Eigenschaften für anspruchsvolle Anwendungen liefern. Wenn es um den 3D-Metalldruck geht, stellt dies jedoch eine ständige Herausforderung für viele Hersteller dar, die in die Technologie investieren möchten.
Der heutige Artikel befasst sich mit einigen der wichtigsten Herausforderungen, denen Unternehmen beim Versuch gegenüberstehen um QS-Prozesse für 3D-gedruckte Metallteile einzurichten und einige der verfügbaren Lösungen zu erkunden.
Herausforderung 1:Sicherstellung der Qualität Ihrer Materialien
Die Sicherstellung, dass ein 3D-gedrucktes Teil den Standards anspruchsvoller Anwendungen entspricht, hängt stark von der Qualität des verwendeten Materials ab.
Die Materialqualifizierung ist jedoch eine ständige Herausforderung für Unternehmen, die Metallpulver herstellen oder verarbeiten. Ein Faktor, der den Prozess erschwert, ist die Notwendigkeit, die Reinheit von Metallpulvern zu erhalten, die für die additive Fertigung verwendet werden.
Dies gilt insbesondere für sicherheitskritische Anwendungen wie Flugzeugteile oder medizinische Geräte, bei denen das Material verwendet werden, müssen zu 100 % frei von Verunreinigungen sein. Verunreinigungen können die Eigenschaften des fertigen Teils verändern, was wiederum zu einem fehlgeschlagenen Druck führen kann.
Metallpulver können jedoch auf verschiedene Weise verunreinigt werden.
Die Gefahr einer Kontamination kann beispielsweise während des Druckprozesses selbst oder bei Lagerung, Transport und Handhabung entstehen. Nehmen wir das erste Beispiel:Es könnten zum Beispiel Reste eines anderen Pulvers auf der Bauplatte zurückbleiben, was zur Vermischung von zwei verschiedenen Pulvern führt. Die gründliche Reinigung der Bauplatte nach jedem Produktionslauf ist daher ein wichtiger vorbeugender Schritt.
Ein weiteres Risiko besteht darin, dass Pulver, das beim Druckprozess übrig bleibt, wiederverwendet wird. Während die Möglichkeit, Pulvermaterial wiederzuverwenden, dazu beitragen kann, Verschwendung zu reduzieren, ist es wichtig zu beachten, dass eine wiederholte Wiederverwendung von Pulver auf diese Weise möglicherweise die Zusammensetzung der Partikel verändern kann, da Feuchtigkeit, Sauerstoff und Stickstoff absorbiert werden.
Es werden zwangsläufig für die additive Fertigung geeignete Testmethoden benötigt, um sicherzustellen, dass keine Kontamination vorliegt.
Lösung:Ziehen Sie eine CT-Untersuchung in Betracht
Eine der genauesten Methoden zur Erkennung von Kontaminationen in Metallpulvern ist die Computertomographie (CT).
Ein CT-Scanner nimmt Hunderte von Röntgenbildern aus verschiedenen Blickwinkeln auf, aus denen ein 3D-Bild erstellt wird. Moderne CT-Scanner können Details bis zu drei Mikrometern erfassen, wobei einige hochauflösende microCT-Scanner auf einer viel kleineren Mikrometerskala arbeiten und eine Voxelgröße von bis zu 0,5 Mikrometer erreichen.
Aktuelle microCT-Geräte können Metalle von Aluminium und Titan bis hin zu schwereren Metalllegierungen wie Edelstahl und Inconel untersuchen.
Wenn sie zur Qualifizierung von Metallpulvern für den 3D-Druck verwendet werden, können CT-Scanner Ingenieuren detaillierte Daten zur Pulvermikrostruktur zur Verfügung stellen. Diese Daten können verwendet werden, um Fremdpartikelverunreinigungen zu erkennen sowie Partikelgrößen- und -formverteilungen zu messen und die Porosität im Inneren der Partikel zu erkennen. Anhand dieser Informationen können Ingenieure die Anwendbarkeit des Pulvers für die Produktion bestätigen.
Ein Unternehmen, das CT-Scandienste für die additive Fertigung anbietet, ist Expanse Microtechnologies.
In einem Interview mit AMFG stellt James Hinebaugh, Präsident und Mitbegründer des Unternehmens, fest, dass „Pulver der wichtigste Punkt in der gesamten Lieferkette der additiven Fertigung sind. Zu verstehen, was ein gutes Pulver ausmacht, das sich gut verteilen und drucken lässt, ist ein zentrales Anliegen für Unternehmen.
„Es ist wichtig zu verstehen, 1) ob es eine ideale Morphologie oder eine ideale Größe oder morphologische Verteilung gibt, die gut interagieren können mit einer Vielzahl von Beschichtern und Druckern und 2) wie wir Fehler in Pulvern wie Einschlüsse und intrapartikuläre Porosität reduzieren können, die, wie Studien gezeigt haben, oft in einem Teil eingeschlossen werden und während des Druckprozesses nicht aus dem Teil entweichen können.“
Dies sind die beiden Bereiche, die Expanse Microtechnologies mit seiner proprietären MicroCT-Scanlösung adressiert.
Das Unternehmen hat fortschrittliche Bildverarbeitungsmethoden entwickelt, mit denen es in der Lage ist, detaillierte Berichte über Materialporosität, Partikel- und Porenmorphologie sowie Größen- und Formverteilungen von Partikeln zu erstellen.
Mit diesen Informationen können Benutzer der additiven Fertigung alle Rohstoffprobleme erkennen und die Zusammenhänge zwischen den verwendeten Materialien und dem Qualitätsniveau der gedruckten Komponenten verstehen.
Das Testen und Qualifizieren von Rohstoffen für die additive Fertigung kann zwar eine Herausforderung darstellen, ist jedoch einer der wichtigsten Schritte zur Sicherstellung der Qualität eines additiv gefertigten Teils. Derzeit bietet das CT-Scannen eines der robustesten und nützlichsten Werkzeuge zur Validierung von AM-Rohmaterialien.
Herausforderung 2:Prozesskontrolle etablieren
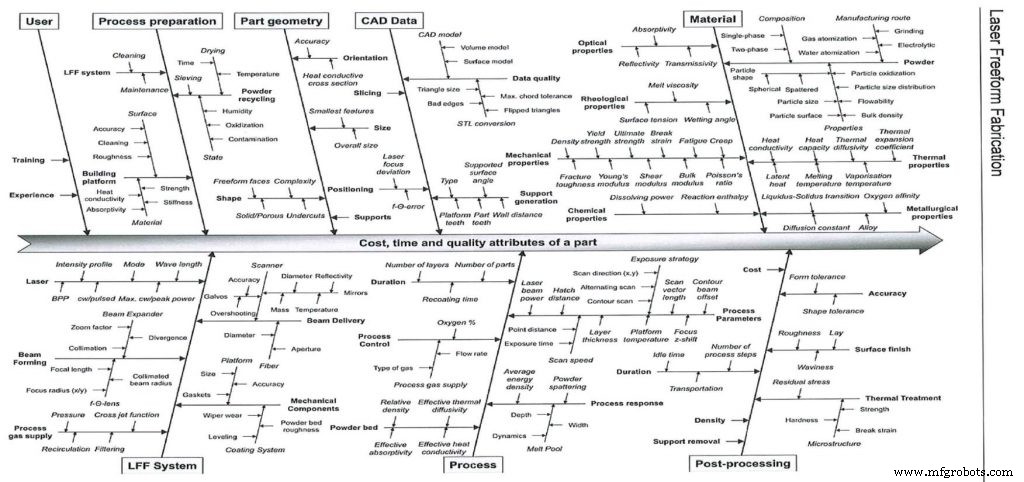
Beim Metall-3D-Druck – und insbesondere bei Pulverbett-Fusionstechnologien – gibt es eine Vielzahl von Variablen, die die Form und Struktur eines Teils beeinflussen können. Diese Variablen umfassen den gesamten AM-Workflow, vom Design über die Bauvorbereitung bis hin zur Nachbearbeitung.
Nehmen wir den Druckprozess als Beispiel. Hier sind nur einige der Parameter, die über Erfolg oder Misserfolg des Prozesses entscheiden, der Weg und die Intensität des Lasers und die Geschwindigkeit der Recoater-Klinge des Druckers. Andere Faktoren sind das Design der Stützstrukturen und sogar Feinheiten wie die Anzahl der Recyclingvorgänge des Pulvers.
Obwohl diese Liste nicht annähernd vollständig ist, hat jeder Faktor einen Einfluss auf das Ergebnis einer Konstruktion und Abweichung in irgendeiner Weise können die Qualität des Endteils beeinträchtigen.
Derzeit ist Trial-and-Error der gebräuchlichste Ansatz, um mit einer Vielzahl von Variablen umzugehen, um einen Prozess zu erreichen, der reproduzierbare Ergebnisse liefert. Teile. Dies kann jedoch eine mehrfache Herstellung des endgültigen Teils sowie umfangreiche Tests des Teils selbst beinhalten.
Dieser Ansatz ist natürlich ein sehr teurer und ineffizienter Prozess und macht einen der Hauptvorteile der Technologie zunichte – die Möglichkeit, kleine Chargen von Teilen kostengünstig herzustellen.
Unternehmen müssen daher einen nachhaltigeren und praktikableren Ansatz zur Prozesskontrolle und Qualifizierung additiv gefertigter Teile verfolgen.
Lösung:Entwickeln Sie ein geschlossenes Qualitätskontrollsystem
Drei Elemente müssen zusammenkommen, um einen schnelleren, zuverlässigeren und nachhaltigeren Qualitätssicherungsprozess für 3D-gedruckte Teile zu ermöglichen. Dazu gehören Build-Planung, Build-Monitoring und Feedback-Steuerung.
- Bauplanung
Eine Möglichkeit, den Druckprozess besser zu verstehen, ist die Simulation. Mithilfe von Simulationen können Ingenieure testen, wie sich ein Teil in einer virtuellen, digitalen Umgebung verhält, bevor ein Design an den Druck gesendet wird.
Die Simulation des AM-Prozesses ermöglicht es Ingenieuren, die komplexen Prozesse zu analysieren, die während des Druckprozesses auftreten.
Da der 3D-Metalldruck anfällig für Probleme wie Verziehen und Verziehen ist, bietet die Simulation beispielsweise wichtige Erkenntnisse darüber, wie sich ein Teil während des Druckprozesses verzieht. Ein weiteres Beispiel ist die Simulation, um genau zu bestimmen, wie das Material schmilzt und erstarrt.
Ingenieure können diese Daten dann verwenden, um den Bau zu planen und die erfolgreichsten Teileorientierungs- und Unterstützungsstrategien auszuwählen.
Abgesehen davon hat Simulationssoftware ihre Grenzen. „In jede Simulationssoftware sind heute gewisse Annahmen eingebaut, die die Genauigkeit einschränken, die sie liefern kann. Das ist derzeit wahrscheinlich der größte Nachteil:Sie können nicht so genau sein, wie Sie es sich wünschen“, sagt Dave Conover, Chief Technologist von ANSYS, kürzlich in einem Interview mit AMFG.
Die Simulationstechnologie entwickelt sich jedoch schnell weiter, und Softwareanbieter entwickeln ihre Angebote ständig weiter. Letztendlich wird die Integration von Simulationssoftware in der Entwurfs- und Planungsphase dazu beitragen, Trial-and-Error zu vermeiden und gleichzeitig die Wahrscheinlichkeit von Druckfehlern erheblich zu reduzieren.
- Überwachen des Builds
In-Prozess-Überwachungssysteme können den Teilqualifizierungsprozess weiter unterstützen. Sensoren und Kameras können verwendet werden, um mehrere Aspekte des Baus in Echtzeit zu messen, um den Bauprozess zu dokumentieren und sicherzustellen, dass die Anforderungen erfüllt werden.
Bei Pulverbett-AM-Prozessen können Kameras die Größe und Temperatur des Schmelzbades erfassen, was sich direkt auf Mikrostruktur, Materialeigenschaften, Oberflächenbeschaffenheit und Gesamtleistung des Teils auswirkt.
Ingenieure kann dann anhand dieser Daten die Wahrscheinlichkeit von Fehlern wie Verzug oder Rissbildung vorhersagen und rechtzeitig in den Prozess eingreifen, bevor die Fehler auftreten. Da diese Daten dokumentiert sind, kann dies dazu beitragen, Prozessbedingungen zu vermeiden, die in Zukunft zu diesen Fehlern führen können.
Derzeit gibt es eine begrenzte Anzahl von In-Process-Monitoring-Technologien, die für AM optimiert sind.
Sigma Labs ist ein Unternehmen, das eine Lösung für die prozessbegleitende AM-Qualitätssicherung anbietet. Sein PrintRite3D-Qualitätssicherungssystem für die additive Fertigung kombiniert PrintRite3D SENSORPAK-Multisensoren und -Hardware mit einem PrintRite3D INSPECT-Softwaremodul.
Diese vielseitige Kombination, die als IPQA-Technologie geschützt ist, ermöglicht die Optimierung der Schmelzbadbedingungen während des AM-Prozesses, indem Sensordaten verwendet und prozessinterne Qualitätsmetriken erstellt werden. Durch die statistische Analyse von Prozessdaten können Berichte zur Teilequalität erstellt und zur Validierung der Wiederholbarkeit verwendet werden.
Zukünftig plant das Unternehmen, ein ANALYTICS-Softwaremodul hinzuzufügen, das sich auf die Nutzung von Big Data-Analysen konzentriert. Das Modul wird in der Lage sein, aussagekräftige und umsetzbare Informationen aus den während des Druckprozesses gesammelten Daten zu extrahieren, um die prozessinterne Qualitätskontrolle weiter zu vereinfachen.
Was die 3D-Drucker selbst betrifft, so verfügen einige bereits über eine integrierte In-Prozess-Überwachung. Der 3D-Druckerhersteller EOS bietet beispielsweise die Monitoring-Suite EOSTATE an. Die Hard- und Softwarelösung basiert auf vier verschiedenen Überwachungsmodulen, darunter System und Laser, PowderBed, MeltPool und Exposure OT (optische Tomographie), die qualitätsrelevante Daten in Echtzeit erfassen können.
Mit EOSTATE Exposure OT bietet EOS nach eigenen Angaben als einziger Hersteller von Metallpulverbettsystemen seinen Kunden ein Qualitätssicherungstool mit integrierter optischer Tomographie.
Dieses Überwachungssystem verwendet eine Kamera, die Lichtemissionen im nahen Infrarotspektrum erfasst, ähnlich einer Wärmebildkamera. Es kann jedes Teil während des gesamten Bauprozesses Schicht für Schicht vollständig abbilden, unabhängig von seiner Geometrie und Größe. Mit diesem Ansatz können Ingenieure den Bereich der nachweisbaren Phänomene, die für die Qualität von AM-Teilen relevant sind, erweitern.
MTU Aero Engines ist ein Unternehmen, das diese Überwachungslösung bereits in seinen Serienproduktionslinien für AM . einsetzt Teile von Flugzeugtriebwerken.
- Den Kreislauf schließen
Das Erfassen und Dokumentieren der Parameter während des Druckprozesses ist entscheidend. Aber die Fähigkeit, auf diese Informationen in Echtzeit zu reagieren – ein Prozess, der als Feedback-Steuerung bekannt ist – macht diesen Ansatz noch effektiver.
Feedback-Steuerung, auch als Closed-Loop-System bekannt, bezeichnet die Fähigkeit, Abweichungen während des Druckprozesses zu erkennen und das System automatisch anzupassen, um diese zu kompensieren. Die Kontrolle über den Bauprozess ermöglicht es Herstellern, konsistente Geometrien, Oberflächengüten und Materialeigenschaften zu erzielen, die die Qualität untermauern.
Ein Unternehmen, das einen rückkopplungsgesteuerten AM-Prozess entwickelt hat, ist Velo3D. Nachdem Velo3D über 92 Millionen US-Dollar an Finanzmitteln aufgebracht hatte, erschien im vergangenen Sommer mit der Veröffentlichung seiner End-to-End-Metall-AM-Lösung. Es umfasst den Velo3D Sapphire 3D-Drucker, die Flow-Druckvorbereitungssoftware und die vom Unternehmen als Intelligent Fusion-Technologie bezeichnete Technologie.
Da diese Schlüsselelemente eng miteinander verzahnt sind, ermöglicht die Technologie die Simulation von thermischen Prozessen, die Vorhersage der Druckleistung und die Verarbeitung mit geschlossenem Regelkreis. Dadurch kann das Sapphire-System Teile mit anspruchsvollen Geometrien wie Überhängen praktisch ohne Stützstrukturen wiederholt und konsistent produzieren.
Die Flow-Software von Velo3D spielt eine wesentliche Rolle bei der Ermöglichung dieser Vorteile. Die Software führt eine Pre-Print-Simulation und -Korrektur durch, optimiert das Design und passt die Geometrie und Teileausrichtung an. Dies hilft bei der Vorbereitung der Feile und gleicht eventuelle Verformungen aus, damit das Teil richtig herauskommt. In-situ-Prozessmesstechnik, begleitet von einer geschlossenen Schmelzbadregelung, arbeitet im Tandem mit Software und steigert letztendlich den Erfolg im ersten Teil auf über 90 %.
Herausforderung 3:Reduzierung menschlicher Fehler
Menschliches Versagen ist wohl der größte Risikofaktor, um sicherzustellen, dass ein 3D-gedrucktes Teil alle erforderlichen Standards erfüllt.
Das liegt daran, dass der 3D-Druck immer noch mehr menschliche Eingriffe erfordert, als Sie vielleicht erwarten, vom Design und Entfernen von Stützen bis hin zur Nachbearbeitung und manuellen Überprüfung, ob die Anforderungen in jeder Phase erfüllt sind.
Dieses Maß an menschlichem Eingreifen erhöht unweigerlich das Risiko, dass das letzte Teil kompromittiert wird.
Nehmen wir als Beispiel die Postproduktionsphase.
Sobald ein Build fertig ist, muss er ausgepackt werden und die verschiedenen Teile, die in diesem Build gedruckt wurden, müssen identifiziert und überprüft werden, bevor sie zur Nachbearbeitung gesendet werden.
Der Produktionsingenieur, der diese Aufgabe durchführt, muss normalerweise auf ein gedrucktes Arbeitsblatt zurückgreifen, im Wesentlichen ein 2D-Bild mit seinem physischen Gegenstück abgleichen und eine Liste von Anforderungen manuell abhaken.
Dieser Inspektionsansatz ist nicht nur zeitintensiv, sondern nimmt auch die Transparenz des Arbeitsablaufs aus der Gleichung.
Doch viele Unternehmen, die AM einsetzen, finden es schwierig, das Handbuch zu ändern Aufgaben in einen schnelleren, genaueren und automatisierten Prozess.
Da die Reduzierung der Wahrscheinlichkeit menschlicher Fehler so wichtig ist, um die Qualität von 3D-gedruckten Teilen sicherzustellen, besteht eine Möglichkeit, dies zu erreichen, darin, mithilfe digitaler Methoden so viele Prüfschritte wie möglich zu automatisieren.
Lösung:Workflow-Software für die additive Fertigung implementieren
Workflow-Software bietet eine digitale, zentralisierte Plattform, die Projekt- und Produktionsteams bei der Verwaltung ihrer AM-Produktionsprozesse unterstützt.
Im Rahmen der Qualitätssicherung kann Workflow-Software oft den kompletten Rahmen bieten, um Unternehmen dabei zu unterstützen, sicherzustellen, dass die Anforderungen für alle Teile erfüllt werden.
Zusätzlich können Produktionsleiter mit Workflow-Software den Prozess der Teileprüfung papierlos und rückverfolgbar machen. Anstatt jedes Teil manuell zu inspizieren, können physische Teile mit ihren digitalen 3D-Gegenstücken verglichen werden.
Das Postproduktionsmanagement-Tool von AMFG bietet beispielsweise einen 3D-Viewer, der alle Teiledaten enthält, sodass Benutzer ein Teil und seine Eigenschaften genauer untersuchen können.
Das Tool ermöglicht es Benutzern, das Verhältnis von erfolgreichen zu fehlgeschlagenen Teilen zu verfolgen. Als fehlgeschlagen markierte Teile werden automatisch in die interne Produktionswarteschlange der Plattform zurückgeführt, um reproduziert zu werden. Der größte Vorteil davon besteht darin, dass Benutzer jede an einem Teil ausgeführte Aktion verfolgen können, wodurch die Notwendigkeit des Qualitätsmanagements um Rückverfolgbarkeit und Verantwortlichkeit erweitert wird.
Gibt es branchenweite QA-Standards für AM?
Bisher haben wir gesehen, dass das Verständnis für die Qualifizierung von Prozessen, Materialien und die Umsetzung digitaler Strategien der Schlüssel dazu ist, sicherzustellen, dass Unternehmen vom 3D-Druck für die Produktion profitieren können.
Industrieweite Standards werden eine Schlüsselrolle dabei spielen dieser Prozess. Bei der traditionellen Fertigung sind Standards bereits an der Tagesordnung, die Unternehmen helfen, die Qualität ihrer Produkte sicherzustellen und Gemeinsamkeiten zu finden. Natürlich hatte die traditionelle Fertigung Jahrzehnte, wenn nicht Jahrhunderte Zeit, um entsprechende Standards zu entwickeln.
3D-Druck hingegen ist noch ein relativ neues Verfahren und viele Normen und Zertifizierungen befinden sich noch in der Entwicklung. In Zukunft muss die Industrie Testmethoden, Protokolle und Referenzdaten entwickeln, um die Kosten und den Zeitaufwand für die Qualifizierung von AM-Materialien, -Prozessen und -Teilen zu reduzieren.
Glücklicherweise ist dies ein Bereich, der sich schnell entwickelt. Erst letztes Jahr hat AMST International seinen F3303-Standard veröffentlicht, der Möglichkeiten zur Qualifizierung von Maschinen und Prozessen skizziert, die zum Herstellen von Teilen mittels Laser- oder Elektronenstrahl-Pulverbettschmelzen verwendet werden. Es wurde auch festgestellt, dass bereits ein zusätzlicher Standard zur Unterstützung der Teilequalifizierung, Qualitätssicherung und Nachbearbeitung von Pulverbettschmelzteilen in Arbeit ist.
Zusammen mit ASTM International arbeitet das National Institute of Standards and Technology (NIST) an der Entwicklung von QS-Standards für die AM-Industrie. Zum Beispiel startete das NIST das AM-Teilequalifizierungsprojekt, das sich auf „die Messungen, Methoden und messtechnischen Systeme konzentriert, die erforderlich sind, um robuste Nachbearbeitungsmessungen zu erstellen, ein solides Verständnis der mechanischen Leistung zu entwickeln und AM-Teile zu qualifizieren“.
Qualität im Blick
Die Sicherstellung der Materialqualität und die Prozesskontrolle sind entscheidend, um mit 3D-Druck konstant hochwertige Metallteile herzustellen.
So komplex dies zunächst erscheinen mag, Hersteller können sich trauen, denn es gibt Lösungen zur Unterstützung des Qualitätssicherungsprozesses, unterstützt durch die Weiterentwicklung branchenweiter Standards.
Wenn Sie sich diesen Herausforderungen stellen und die richtigen Lösungen für Ihr Unternehmen strategisch implementieren, können Sie die Vorteile des 3D-Drucks für hochwertige, anspruchsvolle Anwendungen deutlich nutzen.
3d Drucken
- Es wird erwartet, dass feuerfeste Metallpulver Rohstoffe für den 3D-Druck werden
- Feuerfeste Metallpulver VS 3D-Drucktechnologie
- In Anbetracht dessen, was die neue Metalldrucktechnologie für AM bedeutet
- Qualitätskontrolle in Echtzeit:Welches System ist das richtige für Sie?
- Unterstützungsstrukturen für den 3D-Druck mit Metall – ein einfacherer Ansatz
- H.C. AMPERPRINT von Starck:ein neues Werkzeug für den 3D-Metalldruck
- Welche Metall-3D-Druckpulver können Sie im Jahr 2020 verwenden? [Leitfaden]
- 6 wichtige Designüberlegungen für den 3D-Metalldruck
- Designtipps für den 3D-Druck mit direktem Metall-Lasersintern
- Technologieüberblick:Wann Sie sich wirklich für den Metall-3D-Druck entscheiden sollten