Gebaut für Geschwindigkeit:Qualitativ hochwertige Flugzeugtriebwerke pünktlich herstellen
In diesem ersten Artikel einer Reihe über den Bau von Flugzeugen konzentrieren wir uns auf Triebwerksteile und -komponenten und heben die realen Probleme hervor, bei deren Lösung Werkzeughersteller ihre Kunden täglich unterstützen. Wir werfen auch einen genauen Blick darauf, was derzeit in und um die Herstellung von Luft- und Raumfahrtteilen vor sich geht.
Wie steht es derzeit um die Luft- und Raumfahrtindustrie? Der Drang, Flugzeuge schnell zu bauen und pünktlich zu liefern, ist sehr real – aber es ist nicht ohne Hindernisse oder Kosten.
Auf der Teileherstellungsebene können hitzebeständige und Verbundwerkstoffe ausgesprochen schwer zu schneiden sein. Laut drei großen Werkzeugherstellern, die wir befragt haben, müssen Luft- und Raumfahrthersteller daher in ihrer Verfahrenstechnik, Maschinenprogrammierung und Werkzeugauswahl sehr strategisch vorgehen.
Strategisch zu werden ist sehr zutreffend für all die komplexen Komponenten, aus denen ein Düsentriebwerk besteht, bei denen einzelne geschmiedete Teile im Wert von 75.000 US-Dollar die Norm sind – und die Verschrottung eines Teils eine teure, unerwünschte Option ist. Geschwindigkeit ist zwar unerlässlich, hat aber keinen Vorrang vor vorhersagbaren, zuverlässigen Ergebnissen.
Luft- und Raumfahrt und Verteidigung:Produktionssteigerung bedeutet, dass fortschrittliche Werkzeugstrategien erforderlich sind
„Da wir sehen, dass Erstausrüster die Produktionsraten erhöhen, besteht weiterhin das Risiko, dass Zulieferer Schwierigkeiten beim Hochfahren der Produktion haben“, sagt Robin Lineberger, Leiter der Aerospace-Sparte von Deloitte, im Bericht „2019 Global Aerospace and Defense Industry Outlook“. „Um diese Herausforderung zu meistern, sollten Hersteller erwägen, sich stärker auf die Stärkung der Lieferkette, ein effektives Programmmanagement und den Einsatz fortschrittlicher Technologien zur Steigerung von Produktivität und Effizienz zu konzentrieren.“
In seinem Bericht erwartet Deloitte, dass das Jahr 2018 mit etwa 1.600 Flugzeugen für das Jahr abgeschlossen wird – und prognostiziert für 2019 weitere 100 Flugzeuge. Die Produktionsnachfrage erfordert häufig den Einsatz von Maschinen mit höherem Durchsatz und Multitasking. Die erwähnten „fortgeschrittenen Technologien“ umfassen alles, von sensorbasierter In-Prozess-Messtechnik über Hochgeschwindigkeits-Mehrachsenbearbeitung bis hin zu hochentwickelten Spezialwerkzeugen, die für alle Materialspezifikationen bestimmt sind, die diese stark regulierte Branche aufwirft.
Was Deloitte nicht betont, ist, dass es sechs Monate bis zu einem Jahr dauern kann, bis eine fortschrittliche 5-Achsen-Maschine geliefert wird. Während diese nachbestellt sind, arbeiten einige Subunternehmer mit bestehenden 3-Achsen-Systemen oder anderen veralteten Maschinen – und viele „Lieferanten“ fertiger Luft- und Raumfahrtteile müssen ihre Werkzeugstrategien überdenken, während sie warten, erklären Werkzeughersteller.
„Sie wollen schnellere Fertigungsmethoden“, sagt Bill Durow, Global Engineering Manager mit Schwerpunkt Luft- und Raumfahrt bei Sandvik Coromant. „Sie wollen sie beim Schruppen oder Schlichten mit höheren Geschwindigkeiten betreiben. Heute werden Motoren in einer Menge produziert, die wir in der Branche noch nie zuvor gesehen haben.“
Es ist heute sehr gut möglich, die richtigen Sorten und Einsatzwerkzeuge zu finden, die speziell für hitzebeständige Superlegierungen, auch bekannt als „HRSAs“, entwickelt wurden. Aber es gibt noch eine Lernkurve über diese neueren Materialien und die Geometrien, die zu deren Schneiden benötigt werden, sagen die Werkzeughersteller.
Werkzeuge, die beispielsweise zum Schneiden von 4140-Stahl entwickelt wurden, sind wahrscheinlich nicht die besten Werkzeuge zum Schneiden von Inconel, Titan oder kohlefaserverstärktem Kunststoff oder „CFK“. In den letzten Jahren wurden einige statische und rotierende Motorkomponenten, die früher aus Titan bestanden, nun aus Keramikmatrix-Verbundwerkstoffen oder „CMCs“ hergestellt, sagen Ingenieure von Seco Tools.
„Die Kunst bei all dem ist die Synergie, alles zusammenzufügen“, sagt Dave Todd, Western Zone und Aerospace Manager bei Seco Tools. „Unsere heutigen Fähigkeiten in der Luft- und Raumfahrt haben sich verändert, und wir sind viel mehr zu einem Beratungsunternehmen geworden, das mit Technologiepartnern, erstklassigen Zulieferern und Hochschulen zusammenarbeitet … Ein Großteil der Verfahrenstechnik wird außerhalb unseres Technologiezentrums durchgeführt.“
Alle drei Werkzeughersteller verfügen über Testlabore, in denen sie potenzielle Lösungen für ihre Kunden erproben. Alle drei ziehen es auch vor, eine Mischung aus laborbasierten Tests und Vor-Ort-Tests durchzuführen, um sicherzustellen, dass die genauen Strategien auf der tatsächlichen, physischen Produktionslinie funktionieren.
Denken Sie über Möglichkeiten zur Herstellung von Teilen in der Luft- und Raumfahrt und Verteidigung nach? Lesen Sie „Manufacturing 101:Becoming part of the Aerospace Industry.“
Das Problem und Lösungen für das Wärmemanagement in der Schneidzone
Die Kraftstoffeffizienz treibt die Nachfrage nach leichteren Komponenten mit hitzebeständigen Materialien voran, die schwer zu bearbeiten sein können. Ein Teil des Impulses für eine effizientere Motorleistung ist die Umwelt:Eine sauberere Verbrennung ist auch effizienter.
„Die technischen Anforderungen ziehen es auf die Lieferantenebene herunter – was bedeutet, dass Sie eine schnellere Reaktionszeit auf die Werkzeugtechnologie haben müssen, um fortschrittliche Materialien zu unterstützen“, sagt Scott Causey, Marktsegmentspezialist bei Seco Tools. „Und einige der Materialien erfordern möglicherweise eine völlig andere Werkzeugstrategie zum Schneiden, einfach aufgrund ihrer Komplexität:Ein normales HRSA-Material verwendet nicht dieselbe Schneidstrategie wie ein Keramikmatrix-Verbundwerkstoff.“
Ein CMC-Material ist geschichtet und kann bei unsachgemäßer Handhabung leicht brechen.
Aber denken Sie auch daran:Hitzebeständiges Material – das hervorragend für die Effizienz eines wahnsinnig heißen Turbinenstrahltriebwerks ist – erzeugt auch beim Schneiden viel Hitze. Die Werkzeugqualitäten erfordern selbst ein gewisses Maß an Hitzebeständigkeit, um die Arbeit überhaupt zu erledigen.
Um den Bedarf an Kühlmittel zu decken, ist die Zufuhr durch das Werkzeug zu einem wesentlichen Detail bei Werkzeugen für die fortschrittliche Bearbeitung geworden. Werkzeughersteller finden ständig neue Innovationen in der Kühlmittelzufuhr – einschließlich einiger Werkzeuge, die mehrere Anschlüsse haben, um an den unmittelbarsten Schneidstellen zum effektivsten Zeitpunkt zu liefern.
Apropos Kühlmittel:Wohin geht die Reise in der Kühltechnik? Finden Sie es heraus in „ Die Zukunft der Metallbearbeitungsflüssigkeiten, Maschinenschmierstoffe und Kühlmittel .“
Flugzeugmotoren im Rampenlicht
Die Geometrien, die zum Schneiden von Motorteilformen und -materialien benötigt werden, erfordern dimensionales Denken. Es gibt einzigartig geformte Triebwerksblisks und Tragflügel, die verschiedene Materialien kombinieren können – zum Beispiel einen Verbundstoff mit Titan.
Um dem entgegenzuwirken, entwickeln und testen diese Hersteller eine ganze Reihe von Sorten, die darauf ausgelegt sind, die anspruchsvollsten Materialien zu schneiden – Inconel, HRSAs, Titan und viele andere. Und es gibt noch einen anderen Weg:Sie bauen nach Bedarf kundenspezifische Luft- und Raumfahrtwerkzeuge. Diese kundenspezifischen Tools werden oft zu Standardproduktlinien für alle Kunden.
Drei der großen Werkzeughersteller beschreiben, wie die OEM-Spezifikationen und einzigartigen Geometrien von Luft- und Raumfahrtteilen kundenspezifische Werkzeuge dazu gebracht haben, zu Standardproduktlinien zu werden, die sich einmal in der Praxis bewährt haben. Alle drei Hersteller haben Programme für die Luft- und Raumfahrt – und sehr spezifische Teile, die für die heutigen Anwendungen von Triebwerkskomponenten optimiert sind, darunter:Blisk/Laufräder, Strömungsprofile, Turbinenscheiben, Turbinengehäuse, Spulen, Lüftergehäuse und Wellen.
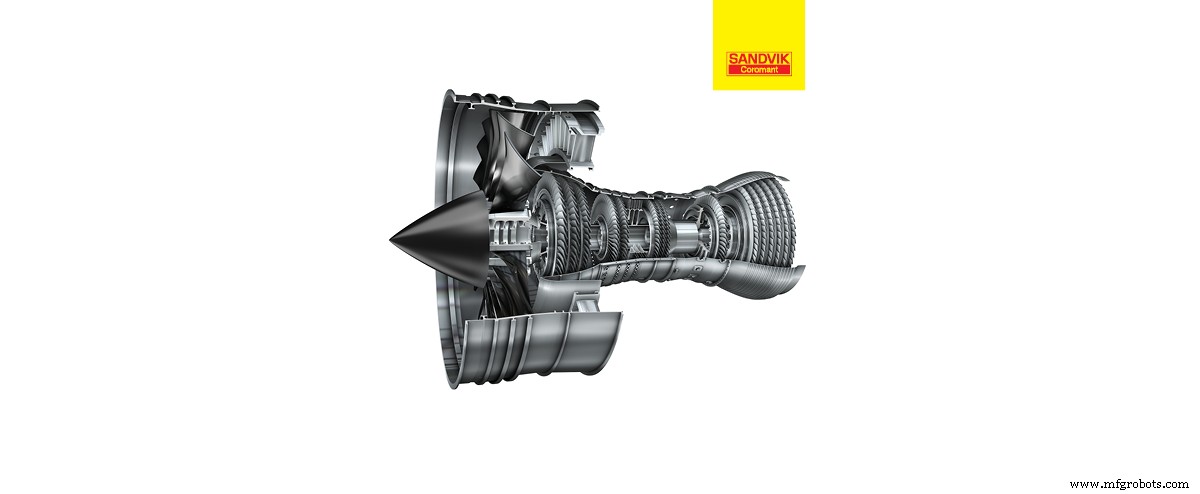
Hier sind vier Beispiele für reale Motorkomponenten, bei denen die richtigen Werkzeuge Wirkung zeigten. Alle umfassen Tier-1-Luftfahrthersteller mit durchschnittlich 35 bis 40 Maschinen in ihrer Werkstatt, die 365/24/7 laufen. Dies sind keineswegs die einzigen Bereiche des Angebots an Motorkomponenten für diese Hersteller.
Sandvik Coromant Bewältigt die Produktivität in Blisks
Herausforderung: Es dauerte sieben Tage, um eine Blisk herzustellen. Das Teil auf Nickelbasis hatte eine tiefe Klinge und einen schmalen Schlitz. Das Schruppen der langen Reichweite erwies sich mit herkömmlichen Fräsansätzen als unwirksam. Die Chip-Verpackung war übermäßig. Maschinen stürzten ab.
„Wir haben gesehen, was sie taten, gerade Schaftfräser bei vollem Schlitz zu verbrennen:Hin und her, hin und her, hin und her“, sagt Durow. „Sie hatten überflüssige Werkzeuge, sie brachten sie zum Nachschleifbetrieb und verwendeten sie dann wieder … Es kostete viel Zeit und es wurden viele Schaftfräser benötigt.“
Lösung: Ein Vollhartmetall-Stechwerkzeug, ähnlich dem, was in der Gesenk- und Formenbearbeitung gemacht wurde. Zusätzlich wurde dann ein zweites Werkzeug mit kleinerem Durchmesser verwendet, um die Höcker zu säubern.
„Wir brachten unser Teststück zurück ins Labor und kamen auf die Idee, die Tauchroutinen zu verwenden“, sagt Durow. „Es hat wirklich, wirklich gut funktioniert. Und das Schöne war, dass wir mit der sekundären Reinigung fast eine weitere Halbfertigbearbeitung eliminiert haben.“
Ergebnis: Vier Tage kürzer als die siebentägige Blisk-Fertigung mit Schruppen und Vorschlichten. Es wurde schließlich auch zu einem Standardangebot für Blisk-Anwendungen.
Kennametal spart eine große Anschaffung mit einem Air Foil
Herausforderung: Eine unregelmäßig geformte Luftfolie aus Inconel wurde in einem elektrochemischen Bearbeitungsprozess oder „ECM“ geschnitten, bei dem das Werkstück von einem Wismutlegierungsmaterial gehalten wurde. Aggressive Schnitte des Rohmaterials waren nicht möglich, daher war die Produktion langsam. Pulsierende Kräfte verursachten Rattern und Vibrationen – und eine geringe Werkzeuglebensdauer.
Lösung: Entwickelte eine Schnittstrategie, die die Helix, die Schneidenzahl und die Mikrogeometrie des Werkzeugs anpasste, um das Abstoßen in schwerere Schnitte zu minimieren. Für leichtere Schnitte haben sie die Helix erhöht und den Durchmesser und die Anzahl der Rillen geändert, um sicherzustellen, dass durch die Drehung drei Kontaktpunkte vorhanden sind.
Ergebnis: Reibungsloser Schnitt, längere Standzeiten und erhöhte maximale Zerspanungsraten. Der Kunde konnte die Bestellung einer neuen Maschine im Wert von 1 Million US-Dollar stornieren, die kurz vor der Bestellung stand.
Seco-Tools Übernimmt die Kontrolle über geschnittene Rillen in einer Motorscheibe
Herausforderung: Probleme bei der Spankontrolle durch das Schneiden tiefer Rillen in wärmebehandeltem Inconel 718 in einer Kompressorscheibe, die die Lüfterflügel hält. Routinen mit tiefem Eintauchen führen zu Werkzeugbruch und schlechter Standzeit.
Lösung: Ein multidirektionales Dreh- und Einstechsystem kombiniert mit Hochdruck-Kühlmittel. Eine Zickzack-Rampen-Geometrie-Schnittstrategie half dabei, Späne zu verdünnen, Hitze zu reduzieren und eine beträchtliche Standzeit zu erreichen.
Ergebnis: Eine Reduzierung der Zykluszeit um 15 bis 20 Prozent. Erlangte die Kontrolle über den Prozess und verringerte den Aufwand für manuelle, zeitaufwändige Eingriffe.
Kennametal eliminiert Vibrationen in einem Motorgehäuse
Herausforderung: Entfernen eines ganzen Zolls Titan für ein Motorgehäuse, aber es konnte nicht gedreht werden. Es gab zu viel Schneidkraft und wenig Produktivität von bestehenden Werkzeugen. Es war schwierig, bestimmte Funktionsbereiche zu umgehen.
„Motorgehäuse sollten rund sein, richtig? Aber das sind sie wirklich nicht“, sagt Mark Francis, Projektmitarbeiter für Luft- und Raumfahrt und Verteidigung bei Kennametal. „Sie sind vollgestopft mit Funktionen, die es unmöglich machen, einfach einen einfachen Drehzyklus durchzuführen … Ich würde sagen, in 80 % der Fälle wird Material durch Fräsen geschnitten.“
Lösung: Verwenden Sie ein Spezialwerkzeug, das um den Durchmesser passt und gleichzeitig Vibrationen und Abdrücke eliminiert.
Ergebnis: Eine stabile, zuverlässige Produktionslinie mit vorhersagbarer Zerspanungseffizienz. Benutzerdefinierte Tools, die zum Standard werden.
Die Bedeutung des Produktionsprozesses und der Kosten pro Komponente
Denken Sie daran:Die meisten Tier-1-Zulieferer von Luft- und Raumfahrtteilen verwenden nicht genau die gleichen Bearbeitungsanlagen – auch wenn sie möglicherweise die gleichen Teile nach den gleichen OEM-Spezifikationen bauen. Werkzeughersteller und Metallbearbeitungsspezialisten müssen jede Bearbeitungsumgebung und Konstruktionsstrategien verstehen, die für jede einzigartige Bearbeitungsumgebung funktionieren.
Unabhängig davon wollten alle drei Werkzeughersteller, die Konkurrenten sind, eines ganz deutlich machen:Der Schwerpunkt sollte auf den Produktivitätsgewinnen durch den Einsatz der richtigen Werkzeuge liegen, die sich wirklich auf Produktivität und Genauigkeit auswirken sollen. Sie glauben auch, dass eine ganzheitlichere Betrachtung der Kosten pro Komponente dazu beiträgt, die pünktliche Auslieferung von immer mehr Flugzeugen zu gewährleisten.
Der Beweis, sagen sie, liegt in der Produktivität.
Sind die Produktionsraten in der Luft- und Raumfahrt real? Beteiligen Sie sich am Gespräch drüben im Metallbearbeitungsforum . [Registrierung erforderlich]
Industrietechnik
- Qualitätsverbesserung in der Fertigung:Entlastung für Betriebsleiter
- Hamilton Aerospace für Wartungsschulungen gelobt
- Motorkabel für Antriebe mit variabler Drehzahl
- Arbeitsausrüstung:Ist es Zeit für ein Upgrade?
- 7 Anzeichen dafür, dass es Zeit für ein Generator-Upgrade ist
- 3 Zeichen, die darauf hinweisen, dass es Zeit für das Zurückspulen des Motors ist
- Worauf Sie bei einem Urethan-Fertigungspartner achten sollten
- Plädoyer für 5G in der Fertigung
- Warum Operational Intelligence der Schlüssel zum Treffen von Geschäftsentscheidungen ist
- Sensorfolie für die Luft- und Raumfahrt