Was ist Formsand? - Arten und Eigenschaften
Was ist Formsand?
Formsand, auch Gießereisand genannt, ist Sand, der, wenn er angefeuchtet und komprimiert oder geölt oder erhitzt wird, dazu neigt, sich gut zu verdichten und seine Form zu behalten. Es wird im Sandgussverfahren zur Vorbereitung des Formhohlraums verwendet.
Das beim Formen verwendete Hauptrohmaterial ist Formsand, da es mehrere Haupteigenschaften aufweist, die mit anderen Materialien nicht erhalten werden können. Als Formsand werden körnige Partikel bezeichnet, die durch den Abbau von Gesteinen infolge der Einwirkung von Naturkräften wie Frost, Wind, Regen, Hitze und Wasserströmungen entstehen. Felsen haben eine komplexe Zusammensetzung und Sand enthält die meisten Elemente der Felsen.
Aus diesem Grund unterscheidet sich Formsand in verschiedenen Teilen der Welt erheblich. In der Natur kommt es am Grund und an den Ufern von Flüssen und Seen vor. Formsand wird nach Art seiner Herkunft in verschiedene Kategorien eingeteilt.
Die Hauptbestandteile von Formsanden sind:
- Kieselerde (SiO2) – 86 bis 90 %,
- Aluminiumoxid (Al2O3) – 4 bis 8 %,
- Eisenoxid (Fe2O3) – 2 bis 5 % mit kleineren Mengen der Oxide von Ti,
- Mn
- Ca und einige alkalische Verbindungen.
Natursand/Grünsand
Er wird auch Grünsand genannt und aus natürlichen Ressourcen gewonnen. Es enthält Wasser als einziges Bindemittel. Es hat den Vorteil, dass es den Feuchtigkeitsgehalt über einen langen Zeitraum beibehält, einen breiten Arbeitsbereich des Feuchtigkeitsgehalts aufweist und ein einfaches Ausbessern und Fertigstellen von Formen ermöglicht.
Grünsand ist ein Aggregat aus Sand, Bentonitton, pulverisierter Kohle und Wasser. Seine Hauptverwendung ist die Herstellung von Formen für den Metallguss. Der größte Teil des Aggregats ist immer Sand, der oft eine einheitliche Mischung aus einer Form von Kieselsäure ist.
Es gibt viele Rezepte für den Tonanteil, aber alle treffen unterschiedliche Balancen zwischen Formbarkeit, Oberflächenbeschaffenheit und der Fähigkeit des heißen geschmolzenen Metalls, zu entgasen. Die typischerweise als Seekohle bezeichnete Kohle, die in einem Anteil von weniger als 5 % vorhanden ist, verbrennt teilweise an der Oberfläche des geschmolzenen Metalls, was zum Ausgasen von organischen Dämpfen führt.
Sandguss ist aufgrund der Einfachheit der verwendeten Materialien eine der frühesten Formen des Gießens. Aufgrund derselben Einfachheit bleibt es immer noch eine der billigsten Methoden, Metalle zu gießen. Andere Gießverfahren, wie z. B. die mit Kokille, weisen eine höhere Qualität der Oberflächenbeschaffenheit auf, sind jedoch teurer.
Grünsand (wie andere Gießsande) wird normalerweise in sogenannten „Kolben“ aufbewahrt, die nichts anderes als Kisten ohne Boden oder Deckel sind. Die Kiste ist in zwei Hälften geteilt, die im Gebrauch aufeinander gestapelt werden. Die Hälften werden als Cope bzw. Drag Flask bezeichnet.
Nicht jeder Greensand hat eine grüne Farbe. Wird jedoch in dem Sinne als „grün“ angesehen, dass es in nassem Zustand verwendet wird (ähnlich wie grünes Holz). Laut der Website der Cast Metals Federation besteht eine alternative Gießmethode darin, den geformten Sand vor dem Gießen des geschmolzenen Metalls durch Hitze zu trocknen. Dieses Trockensandgussverfahren führt zu einer steiferen Form, die besser für schwerere Gussteile geeignet ist.
Synthetischer Sand
Es ist künstlicher Sand, der durch Mischen von relativ tonfreiem Sand, Bindemittel (Wasser und Bentonit) und anderen Materialien nach Bedarf erhalten wird. Es ist besser, Sand zu formen, da seine Eigenschaften durch Variation des Mischungsgehalts leicht gesteuert werden können.
Die Zusammensetzung von grünem Kunstsand für Stahlguss ist wie folgt.
Neuer Quarzsand – 25 %, alter Sand – 70 %, Bentonit – 1,5 %, Dextrin – 0,25 % und Feuchtigkeit – 3 bis 3,5 %.
Die Zusammensetzung von trockenem Kunstsand für Stahlguss ist wie folgt.
Nettoquarzsand – 15 %, alter Sand 84 %, Bentonit – 0,5 % und Feuchtigkeit – 0,5 %.
Daneben gibt es bestimmte Sorten von Spezialsanden wie Zirkonit, Olivin etc. Diese Spezialsande sind teurer als Quarz und werden daher nur dort eingesetzt, wo ihr Einsatz gerechtfertigt ist.
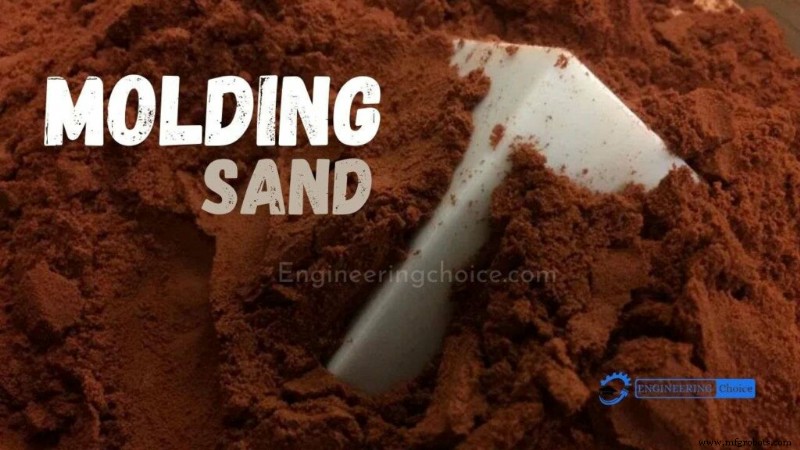
Formsandarten
Formsande können auch nach ihrer Verwendung in verschiedene Typen eingeteilt werden:Hintersande, Kernsande, Trockensande, Vorsatzsande, Grünsande, Lehmsande, Trennsande, Systemsande.
1. Grundsand oder Bodensand
Stützsand oder Estrichsand wird verwendet, um den Decksand zu unterstützen und wird verwendet, um das gesamte Volumen des Formkastens zu füllen. Unterlagesand wird manchmal als Schwarzsand bezeichnet, da alter, wiederholt verwendeter Formsand durch die Beimischung von Kohlenstaub schwarz gefärbt ist und beim Kontakt mit dem geschmolzenen Metall brennt.
2. Kernsand
Kernsand wird zur Herstellung von Kernen verwendet und wird manchmal auch als Ölsand bezeichnet. Kernsand ist sehr reichhaltiger Quarzsand, gemischt mit Ölbindemitteln wie Kernöl, das aus Leinöl, Harz, leichtem Mineralöl und anderen Bindemitteln besteht. Pech oder Mehle und Wasser können aus wirtschaftlichen Gründen auch in großen Kernen verwendet werden.
3. Trockener Sand
Grünsand, der nach der Herstellung von Formen und Kernen in einem geeigneten Ofen getrocknet oder gebacken wurde, wird als Trockensand bezeichnet. Es besitzt mehr Festigkeit, Steifigkeit und thermische Stabilität. Trockener Sand wird hauptsächlich für größere Gussteile verwendet. In diesem Sand hergestellte Formen werden als Trockensandformen bezeichnet.
4. Sand gegenüberstellen
Sichtsand bildet die Stirnseite der Form. Es befindet sich neben der Oberfläche des Modells und kommt beim Gießen der Form mit geschmolzenem Metall in Kontakt. Die anfängliche Beschichtung um das Modell herum und damit für die Formoberfläche wird durch Abdecksand gegeben. Verblendsand hat eine hohe Feuerfestigkeit. Verblendsand wird aus Quarzsand und Ton hergestellt, ohne Verwendung von bereits verwendetem Sand.
Beim Verputzen von Sand werden verschiedene Formen von Kohlenstoff verwendet, um zu verhindern, dass das Metall in den Sand einbrennt. Eine Vorsatzsandmischung für Grünsand aus Gusseisen kann aus 25 % frischer und speziell aufbereiteter und 5 % Meereskohle bestehen.
Sie werden manchmal mit 6-15-mal so viel feinem Formsand gemischt, um Verkleidungen herzustellen. Die Decksandschicht in einer Form liegt normalerweise zwischen 20 und 30 mm. 10 bis 15 % der gesamten Formsandmenge ist der Vorsatzsand.
5. Grünsand
Grünsand ist auch als gehärteter oder natürlicher Sand bekannt, der eine frisch hergestellte Mischung aus Quarzsand mit 18 bis 30 % Ton und einem Feuchtigkeitsgehalt von 6 bis 8 % ist. Ton und Wasser liefern die Bindung für grünen Sand. Es ist fein, weich, leicht und porös.
Grünsand ist feucht, wenn er in der Hand gedrückt wird, und er behält die Form und den Eindruck, den er unter Druck geben würde. Mit diesem Sand hergestellte Formen benötigen keine Unterlage und sind daher als grüne Sandformen bekannt.
Grünsand ist leicht verfügbar und besitzt niedrige Kosten. Grünsand wird üblicherweise für die Herstellung von Eisen- und Nichteisen-Gussteilen verwendet.
6. Lehmsand
Lehmsand ist eine Mischung aus Sand und Ton mit Wasser zu einer dünnen plastischen Paste. Lehmsand besitzt bis zu 30-50% hohen Ton und 18% Wasser. Muster werden nicht zum Lehmformen verwendet, und die Form wird durch Sweeps geformt. Lehmsand wird insbesondere für Lehmformen verwendet, die für große Graugussteile verwendet werden.
7. Abschiedssand
Trennsand ohne Bindemittel und Feuchtigkeit wird verwendet, um zu verhindern, dass der Grünsand an dem Muster klebt, und um auch zu ermöglichen, dass der Sand an der Trennfläche die Oberkante abtrennt und zieht, ohne zu haften. Trennsand ist sauberer, tonfreier Quarzsand, der denselben Zweck erfüllt wie Trennstaub.
8. System-Sand
In mechanisierten Gießereien, in denen maschinelles Formen eingesetzt wird. Mit Systemsand wird der gesamte Formkasten gefüllt. In maschinellen Sandaufbereitungs- und Handhabungseinheiten wird kein Vorsatzsand verwendet. Durch die Zugabe von Wasser und speziellen Additiven wird der Altsand gereinigt und reaktiviert.
Dies wird als Systemsand bezeichnet. Da die gesamte Form aus diesem Systemsand besteht, müssen die Eigenschaften wie Festigkeit, Durchlässigkeit und Feuerfestigkeit des Formsandes höher sein als die des Hintergußsandes.
Eigenschaften von Formsand
Die grundlegenden Eigenschaften, die in Formsand und Kernsand erforderlich sind, sind Haftvermögen, Kohäsion, Kollabierbarkeit, Fließfähigkeit, Trockenfestigkeit, Grünfestigkeit, Permeabilität, Feuerfestigkeit, beschrieben wie unter.
1. Haftfähigkeit
Das Haftvermögen ist eine Eigenschaft des Formsandes, an Fremdmaterial, wie z. B. anhaftendem Formsand, an der Innenwand des Formkastens haften zu bleiben.
2. Zusammenhalt
Kohäsion ist die Eigenschaft von Formsand, aufgrund derer die Sandkornpartikel innerhalb des Formsandes zusammenwirken und sich anziehen. Dadurch wird die Bindefähigkeit des Formsandes verbessert, um die Grün-, Trocken- und Warmfestigkeitseigenschaften von Form- und Kernsand zu erhöhen.
3. Zusammenfaltbarkeit
Nachdem das geschmolzene Metall in der Form erstarrt ist, muss die Sandform zusammenklappbar sein, so dass eine freie Kontraktion des Metalls auftritt, und dies würde natürlich das Reißen oder Reißen des sich zusammenziehenden Metalls vermeiden. In Ermangelung der Kollabierfähigkeit wird die Kontraktion des Metalls durch die Form behindert und führt somit zu Rissen und Sprüngen im Gussteil. Diese Eigenschaft wird in Kernen dringend benötigt.
4. Trockenfestigkeit
Sobald das geschmolzene Metall in die Form gegossen wird, verdunstet die Feuchtigkeit in der Sandschicht neben dem heißen Metall, und diese trockene Sandschicht muss eine ausreichende Formfestigkeit aufweisen, um eine Erosion der Formwand während des Fließens zu vermeiden geschmolzenes Metall. Die Trockenfestigkeit verhindert auch die Vergrößerung des Formhohlraums durch den metallostatischen Druck des flüssigen Metalls.
5. Fließfähigkeit oder Plastizität
Fließfähigkeit oder Plastizität ist die Fähigkeit des Sandes, sich zu verdichten und sich wie eine Flüssigkeit zu verhalten. Es fließt beim Rammen gleichmäßig in alle Teile des Musters und verteilt den Rammdruck gleichmäßig in alle Richtungen.
Im Allgemeinen widerstehen Sandpartikel der Bewegung um Ecken oder Vorsprünge. Im Allgemeinen nimmt die Fließfähigkeit mit abnehmender Grünfestigkeit zu und umgekehrt. Die Fließfähigkeit nimmt mit abnehmender Korngröße des Sandes zu. Die Fließfähigkeit variiert auch mit Feuchtigkeit und Tongehalt im Sand.
6. Grüne Stärke
Nachdem Wasser darin eingemischt wurde, muss der Grünsand eine ausreichende Festigkeit und Zähigkeit aufweisen, um die Herstellung und Handhabung der Form zu ermöglichen. Dazu müssen die Sandkörner adhäsiv sein, d. h. sie müssen in der Lage sein, sich an einem anderen Körper zu befestigen und. daher haften Sandkörner mit hoher Haftfähigkeit an den Seiten des Formkastens.
Außerdem müssen die Sandkörner die Eigenschaft haben, die als Kohäsion bekannt ist, d. h. die Fähigkeit der Sandkörner, aneinander zu haften. Aufgrund dieser Eigenschaft kann das Modell aus der Form herausgenommen werden, ohne dass die Form bricht, und es tritt auch keine Erosion der Formwandoberflächen während des Fließens von geschmolzenem Metall auf.
Die Grünfestigkeit hängt auch von der Kornform und -größe, der Menge und Art des Tons und dem Feuchtigkeitsgehalt ab.
7. Durchlässigkeit
Permeabilität wird auch als Porosität des Formsandes bezeichnet, um das Entweichen von Luft, Gasen oder Feuchtigkeit zu ermöglichen, die in der Form vorhanden sind oder erzeugt werden, wenn das geschmolzene Metall hineingegossen wird. Alle diese während des Gieß- und Erstarrungsvorgangs entstehenden Gase müssen entweichen, sonst wird das Gussteil defekt.
Die Durchlässigkeit ist eine Funktion von Korngröße, Kornform, Feuchtigkeit und Tongehalt im Formsand. Das Ausmaß des Stampfens des Sandes wirkt sich direkt auf die Durchlässigkeit der Form aus. Die Durchlässigkeit des Schimmelpilzes kann durch Entlüften mit Entlüftungsstäben weiter erhöht werden.
8. Feuerfestigkeit
Feuerfestigkeit ist definiert als die Fähigkeit von Formsand, hohen Temperaturen standzuhalten, ohne zu zerfallen oder zu verschmelzen, wodurch ein einwandfreies Gießen ermöglicht wird. Es ist eine sehr wichtige Eigenschaft von Formsanden. Die Feuerfestigkeit kann nur begrenzt erhöht werden.
Formsand mit schlechter Feuerfestigkeit kann auf der Gussoberfläche einbrennen und es kann keine glatte Gussoberfläche erhalten werden. Der Grad der Feuerfestigkeit hängt vom Gehalt an SiO2, d. h. dem Quarz, und der Form und Korngröße der Partikel ab.
Je höher der SiO2-Gehalt und je gröber die Kornvolumenzusammensetzung, desto höher ist die Feuerfestigkeit des Form- und Kernsandes. Die Feuerfestigkeit wird durch den Sinterpunkt des Sandes und nicht durch seinen Schmelzpunkt gemessen.
9. Verschiedene Eigenschaften von Formsand
Zusätzlich zu den oben genannten Anforderungen sollte der Formsand nicht am Gussstück haften und nicht chemisch mit dem Metall reagieren. Formsand muss wirtschaftlich günstig und in der Natur leicht verfügbar sein. Es muss aus wirtschaftlichen Gründen wiederverwendbar sein. Seine Wärmeausdehnungskoeffizienten müssen ausreichend niedrig sein.
Herstellungsprozess
- Was ist Formsand? - Arten und Eigenschaften
- Aluminiumarten:Klassifikationen, Eigenschaften und Anwendungen
- Was ist Polieren, Eigenschaften und Arten des Polierens?
- Was ist Engineering Tolerance, Types and Fit?
- Was ist Laserstrahlbearbeitung? - Typen und Arbeitsweise
- Was ist Löten? - Typen und wie man lötet
- Was ist Rapid Prototyping? - Arten und Funktionsweise
- Was ist additive Fertigung? - Typen und Arbeitsweise
- Was ist Formsand?
- Arten von Metallen und ihre Eigenschaften