Wie wird Lean Manufacturing in einer CNC-Fertigung angewendet?
Viele Maschinenwerkstätten entstehen ständig, da der Markt für kundenspezifische Teile exponentiell wächst, und dies lässt uns viele CNC-Werkstätten zur Auswahl. Natürlich möchten wir alle die beste Qualität für unsere Teile bekommen, also würde ich, wenn ich eine CNC-Maschinenwerkstatt in meiner Nähe wählen würde, nach der mit einem Wettbewerbsvorteil suchen, der das beste Preis-Leistungs-Verhältnis bietet. Dazu gehören hohe Verarbeitungsqualität, schnelle Bearbeitungszeit und pünktliche Lieferung. Damit eine Einrichtung unter anderem diesen Wettbewerbsvorteil erzielen kann, muss sie Effizienz in ihre Prozesse integrieren, und einer der etabliertesten und effektivsten Wege dafür ist die Anwendung von Lean-Manufacturing-Prinzipien.
Anpassung von Lean-Manufacturing-Prinzipien in einer CNC-Fertigung
Was ist Lean Manufacturing in einer CNC-Fertigung?
Erstens, wenn wir von Lean Manufacturing sprechen, beziehen wir uns auf die Maximierung der Produktion einer CNC-Werkstatt durch Minimierung der während des Produktionsprozesses anfallenden Abfälle. Diese Methodik stammt aus den bewährten Verfahren, die Toyota bereits in den 1930er Jahren in seiner Produktionslinie angewendet hat, wobei das Hauptziel darin besteht, Verschwendung im Betrieb zu vermeiden.
Durch die Entwicklung dieser Methode seit ihrer Entdeckung identifizieren Branchenexperten die 8 Hauptkategorien von Industrieabfällen, die als AUSFALLZEITEN abgekürzt werden können:Defekte, Überproduktion, Wartezeiten, Nichtnutzung von Talenten, Transport, Bestandsüberschuss, Bewegungsabfall und Übermäßige Verarbeitung.
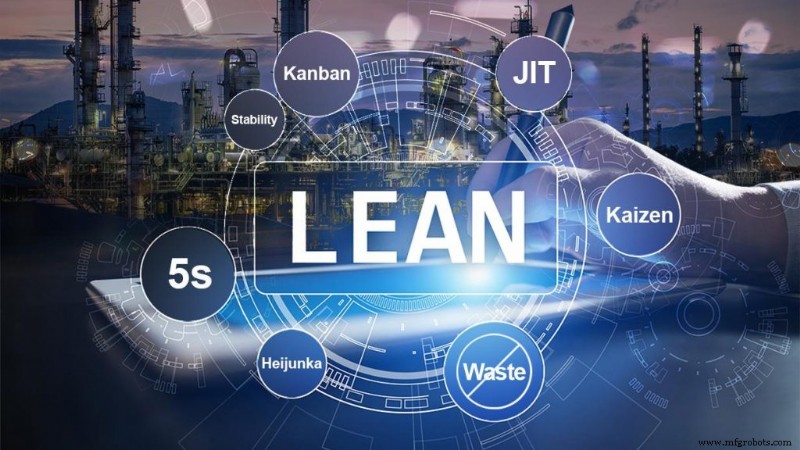
1. Mängel
In einer CNC-Maschinenwerkstatt kann dies Ausschussteile aufgrund von Maßungenauigkeiten, unerwünschter Oberflächenbeschaffenheit und anderen Mängeln am bearbeiteten Teil umfassen. Diese Defekte werden normalerweise durch verschiedene Faktoren wie schlechte Bearbeitungsparameter, Maschinenfehlfunktionen, minderwertige Werkzeuge, nicht kalibrierte Instrumente und schlecht geplante Bearbeitungsprozesse verursacht.
2. Überproduktion
Dieser Industrieabfall stammt aus dem Überangebot, weil Teile blind so produziert werden, dass die produzierten Teile die Nachfrage übersteigen. Dies ist manchmal auf schlechte Planung und unkoordinierte Bestellungen von Teilen zurückzuführen.
3. Wartezeit
Dies ist eine Verschwendung, da ungenutzte Zeit stattdessen für wertvolle Produktionsschritte verwendet werden kann. Einige Beispiele sind Produktionsstopps aufgrund der Nichtverfügbarkeit von Materialien und aufgrund von Maschinenausfällen. Die Wartezeiten in der Produktion können durch schlechte Planung, unvorhergesehene Maschinenstillstände und vieles mehr verursacht werden.
4. Nichtnutzung von Talenten
Dazu gehört auch das Versäumnis, die Talente und Fähigkeiten eines Mitarbeiters effektiv einzusetzen.
5. Transport
Dies ist eine Art von Abfall, der durch übermäßigen Transport von einem Prozess zum anderen gekennzeichnet ist. Mit anderen Worten, Transportabfälle sind die unvernünftigen Schritte in einem Prozess, die im Austausch gegen einen effizienteren Schritt eliminiert oder verbessert werden können.
6. Bestandsüberschuss
In CNC-Bearbeitungsanlagen kommt diese Verschwendung neben der Überproduktion, bei der überschüssige Bestände zu Verlusten für eine CNC-Werkstatt führen können. Denken Sie daran, dass produzierte Teile, die in einem Lager stecken, für ein Unternehmen keine Rendite erzeugen und deshalb als Industrieabfall gelten.
7. Bewegungsverschwendung
Dies erstreckt sich auf die unnötige Bewegung von Ressourcen, die dem Produkt als Ganzes keinen Mehrwert verleihen. In einer CNC-Fertigung umfasst dies die nicht-strategische Platzierung verschiedener Werkzeuge, Materialien und Arbeitsstationen.
8. Übermäßige Verarbeitung
Bei der Herstellung von maschinell bearbeiteten Teilen umfasst die übermäßige Bearbeitung unnötige Prozesse, die für die Anforderungen des Kunden keine Bedeutung haben. Dies ist normalerweise das Ergebnis eines schlecht konstruierten Bearbeitungsprozesses.
Diese unterschiedlichen Verschwendungen führten uns zu den Hauptgrundlagen, die von Maschinenwerkstätten bei der Implementierung von Lean Manufacturing verwendet werden können, und diese sind:
- Ermitteln der Erwartungen und Anforderungen des Kunden an seine Teile
- Abbildung des Wertstroms einer CNC-Fertigung
- Schaffung eines effizienten Ablaufs
- Aufbau eines effektiven Pulls
- Streben nach kontinuierlicher Exzellenz
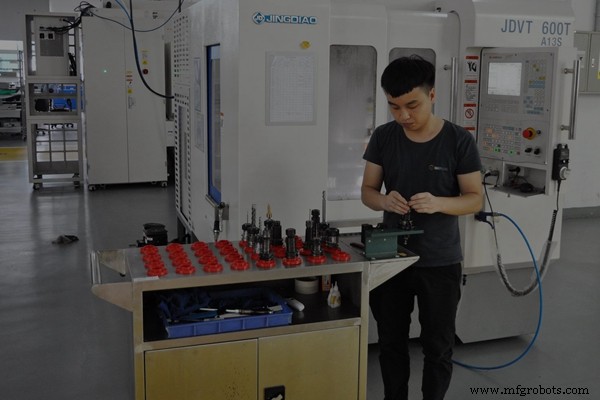
7 Möglichkeiten, wie eine CNC-Fertigung Lean-Prinzipien umsetzen kann
1. Maximierung der Werkzeugeffizienz (Werkzeugauswahl)
Die Werkzeugeffizienz ist ein kritischer Faktor für eine Maschinenwerkstatt, da dieser einzelne Faktor die Qualität der von jeder CNC-Maschine hergestellten Teile beeinflussen oder beeinträchtigen kann. Es ist wichtig, die richtigen Werkzeuge auszuwählen, um eine hohe Schnittqualität zu gewährleisten und im Gegenzug fehlerhafte Teile aufgrund einer schlechten Werkzeugauslastung zu minimieren.
2. Intelligent sein mit Bearbeitungsparametern und Bearbeitungsprozessen
Fertigungsingenieure planen ihre Parameter (z. B. Vorschubgeschwindigkeit, Schnittgeschwindigkeit, Schnitttiefe usw.) sorgfältig so, dass sie den größtmöglichen Nutzen aus der CNC-Maschine, dem Material und den Werkzeugen ziehen. Zusätzlich zu den Parametern ist es wichtig, die effektivste Anordnung für verschiedene Bearbeitungsverfahren zu entwerfen. Dadurch wird Verschwendung im Zusammenhang mit Fehlern, Bewegung und übermäßiger Verarbeitung minimiert.
3. Konsequente Umsetzung der periodischen und vorbeugenden Wartung
Maschinenstillstände sind bei weitem einer der Hauptgründe für unnötige Produktionsunterbrechungen in der Fertigungslinie, weshalb die sorgfältige Einhaltung geplanter Wartungsarbeiten ein Muss ist. Unvorhergesehene Ausfallzeiten werden durch regelmäßige Wartung und Überprüfung der verschiedenen Geräte erheblich reduziert, was zur Reduzierung von Wartezeiten, Defekten und ungenutzten Talenten führt.
4. Just-in-Time-Produktion (JIT)
JIT wird durch intelligente Planung und Terminierung für verschiedene Ressourcen erreicht. Eine weitere Hauptursache für das unnötige Warten in einer CNC-Werkstatt ist die Nichtverfügbarkeit von Rohmaterialien, an denen gearbeitet werden kann. Um dies zu verhindern, planen Planer die effektivsten Methoden in Bezug auf den Zufluss, die Verarbeitung und den Abfluss verschiedener Ressourcen.
5. Organisation für Produktivität
Es ist wichtig, die Organisation und Platzierung verschiedener Instrumente, die bei der Produktion von CNC-Teilen benötigt werden, strategisch zu planen. So einfach wie die Anwendung von 5S (Sortieren, Ordnen, Glänzen, Standardisieren und Erhalten) in einer Arbeitsumgebung kann einen erheblichen Unterschied in der Organisation eines Arbeitsablaufs bewirken. Dies eliminiert Verschwendungen in Bezug auf Bewegung und nicht genutzte Ressourcen.
6. Strategisches Anlagenlayout
In einer CNC-Maschinenwerkstatt ist das Anlagenlayout eines der wichtigsten Dinge, die ernst genommen werden müssen, um unnötige Verschwendung durch übermäßigen Transport zu vermeiden. Beispielszenarien wären:Regale für Rohmaterialien sollten in der Nähe der Stanzvorgänge aufgestellt werden, Maschinen sind so angeordnet, dass sie das Teil leicht zum nächsten Bearbeitungsprozess transportieren, Endbearbeitungsgeräte werden in der Nähe des Verpackungsbereichs aufgestellt.
7. Kontinuierliche Verbesserungsinitiativen
Schließlich ist die Unterstützung der Best Practices des CNC-Shops. Langfristig sind CNC-Werkstätten, die ihre Prozesse kontinuierlich verbessern, in der Lage, die hochwertigsten Teile mit vielversprechenden Lieferverpflichtungen zu liefern.
CNC-Maschine
- Geschichte der CNC-Maschinen
- es von CNC-Maschinen
- Wie Sie CNC-Teile kaufen
- ter in einer Maschinenhalle:wie sich die Temperatur auf die CNC-Leistung auswirkt
- Wie haben CNC-Maschinen die moderne Fertigung verändert?
- Wie CNC-Maschinen die Fertigung verändert haben
- Wie haben sich CNC-Maschinen auf die Fertigung ausgewirkt?
- So wählen Sie eine zuverlässige CNC-Bearbeitungswerkstatt für CNC-Teile aus
- Wie man eine schlanke Fertigung wieder auf Kurs bringt
- Luft- und Raumfahrtfertigung – Wie wir Qualität erreichen