OptiPath- und Force-Module von CGTechs erweisen sich als komplementär
Vor drei Jahren sprach der Vericut-Softwareentwickler CGTech mit den Programmierern Don Lahr und Mike Triplett von der Ultra Machining Company (UMC) für Luft- und Raumfahrt und Medizintechnik über ihre Verwendung des wissensbasierten Bearbeitungsmoduls OptiPath von Vericut. Die Männer hatten vor Kurzem ein Update installiert, das eine Anpassung enthielt, die sie CGTech in ihrem Namen vorgenommen hatten.
Die Verbesserungsanforderung – Vericut SCR Nr. 16986 – vereinfachte Änderungen der Vorschubgeschwindigkeit durch Makrovariablen, auf die der Bediener zugreifen kann, optimierte Setups und beseitigte die Notwendigkeit, das Programmierbüro für eine einfache Variablenanpassung einzubeziehen.
Lahr und Triplett sind heute noch bei UMC, ebenso wie Cory Mahn, ein 12-jähriger Mitarbeiter, der kurz nach dem Anpassungsupdate in die Programmierabteilung kam. Zu dieser Zeit gab es einige Diskussionen über das neu veröffentlichte Force-Modul von CGTech, ein physikbasiertes Werkzeugweg-Optimierungstool, das die Zykluszeiten um 25 % oder mehr reduzieren soll, aber UMC hatte keine unmittelbaren Pläne für eine Implementierung.
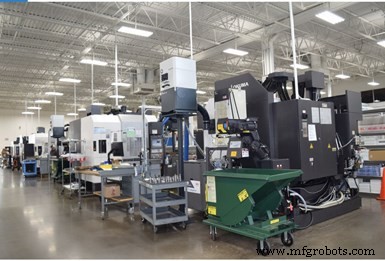
UMC, ein Jobshop für Luft- und Raumfahrt und Medizintechnik in Monticello, Minnesota, beherbergt Dutzende moderner CNC-Werkzeugmaschinen. Das Unternehmen verwendet Vericut von CGTech seit mehr als 15 Jahren.
Diese Pläne änderten sich im Februar 2020, als das Unternehmen seinen ersten Force-Testlauf für einen ziemlich lang andauernden Auftrag durchführte. „Wir haben die Zykluszeit für diese eine Teilenummer um etwa 10 % verkürzt, wodurch das Unternehmen letztendlich fast 13.000 US-Dollar eingespart hat“, sagt Lahr. Die Ergebnisse waren beeindruckend genug, dass das obere Management zustimmte, in die Software zu investieren. „Es ist keine so große Einsparung wie die, die wir seither mit Force erzielt haben, aber es hat definitiv einigen die Augen dafür geöffnet, wie wertvoll es ist, voranzukommen.“
Bei dem fraglichen Werkstück handelt es sich um ein medizinisches Bauteil aus Edelstahl 304L mit Abmessungen von etwa 2 × 3 × 0,5 Zoll. Das größte von UMC verwendete Werkzeug ist ein 0,75-Zoll-Hartmetall-Schaftfräser mit vier Schneiden, der kleinste nur 1/32 Zoll, mit axialen Schnitttiefen von 0,001 oder 0,002 Zoll pro Durchgang. Lahr merkt an, dass Force beim Schruppen und Vorschlichten den größten Nutzen brachte, aber er fügt hinzu, dass es selbst bei sehr kleinen Werkzeugen wie den oben beschriebenen dazu beitrug, die Werkzeugwege so weit zu optimieren, dass der Fräserbruch auf Null sank, während sich die Zykluszeit oft verbesserte . „Es gibt definitiv auch einen Vorteil für die Standzeit“, fügt er hinzu.
Site-Updates und ein Automatisierungs-Push
Die jüngsten Änderungen bei UMC beeinflussten auch die Entscheidung des Unternehmens, mit der Nutzung von Force zu beginnen. Das Unternehmen befindet sich nach wie vor in zweiter Generation in Familienbesitz, die Mitarbeiterzahl hat sich jedoch auf knapp 200 Personen verdoppelt. Auch die Zahl der CNC-Werkzeugmaschinen hat zugenommen. Es gibt jetzt eine Handvoll Okuma M460V-5AX fünfachsige vertikale Bearbeitungszentren, ein Paar Okuma vierachsige MB-46VAE vertikale Bearbeitungszentren und drei Matsuura MX-520 fünfachsige Bearbeitungszentren – zwei mit Palettenpools mit vier Stationen /P>
Aufgrund des Fachkräftemangels stellen UMC und andere Lohnfertiger fest, dass die automatisierte Maschinenbeschickung von Jahr zu Jahr wichtiger wird.
Trotz der gestiegenen Mitarbeiterzahl ist die Shopfloor-Automatisierung auf dem Vormarsch. „Es ist schwierig, Facharbeiter zu finden, deshalb haben wir einige unserer Dreh- und Fräsmaschinen mit Robotern ausgestattet“, sagt Mahn. „Dies bietet die Möglichkeit, in einigen Fällen leicht oder sogar unbeaufsichtigt zu laufen, obwohl unsere Losgrößen ziemlich klein sind. Wir haben auch unsere Werkstückspannung auf einigen der Maschinen verbessert und führen Offline-Werkzeugvoreinstellungen durch.“
Vergleich von OptiPath und Force
Zum jetzigen Zeitpunkt hat das Unternehmen 20 verschiedene Teilenummern mit Force optimiert. Bisher lagen die Zykluszeitverbesserungen zwischen 3 und 28 %, aber Lahr weist schnell darauf hin, dass UMC seine Investition drei- oder viermal innerhalb des ersten Jahres amortisieren wird.
Diejenigen, die mit der Werkzeugwegoptimierung vertraut sind, fragen sich vielleicht:Wenn UMC bereits OptiPath verwendet, warum sollte es dann in Force investieren? Schließlich versprechen beide Produkte kürzere Zykluszeiten und verbesserte Standzeiten, und beide lösen Probleme mit Fräserdurchbiegung, Rattern in Ecken und ähnlich unerwünschten Bearbeitungsereignissen. Bedeutet dies, dass die Investition von UMC in OptiPath eine Geldverschwendung war? Überhaupt nicht, erklärt Gene Granata, Produktmanager von CGTech für Vericut.
„Force und OptiPath sind unterschiedliche Produkte, die unterschiedliche Optimierungsansätze verwenden, sich aber gegenseitig ergänzen“, sagt er. „OptiPath zum Beispiel führt keine Messung von Schnittkräften durch. Stattdessen verwendet es entweder eine volumetrische Optimierungsmethode oder eine, die die Spandicke misst. Force misst auch die Spandicke, verfügt aber über zusätzliche Kontrollen und Ausgleiche, einschließlich der Überwachung der Schnittkräfte oder der Spindelleistung, und sagt die Werkzeugdurchbiegung voraus. In beiden Fällen wird der Materialabtrag konstant gehalten, indem die Vorschubgeschwindigkeit angepasst und die Werkzeugwegbewegungen nach Bedarf unterteilt werden, um konsistente, nahezu ideale Bearbeitungsbedingungen für jedes Werkzeug aufrechtzuerhalten.“
Unterschiedliche Tools für unterschiedliche Situationen
Letztendlich haben beide Softwarekomponenten ihre eigenen optimalen Anwendungsfälle. Granata empfiehlt die Verwendung von Force in harten, schwer zu bearbeitenden Materialien, wo leichte, sofortige Spitzen in der Werkzeugbelastung große Probleme mit Schneidwerkzeugen und Maschinenspindeln bedeuten können. Andererseits empfiehlt er OptiPath für weiche Metalle wie Aluminium, Weichstahl und Grauguss, bei denen das primäre Ziel darin besteht, das Material so schnell wie möglich zu entfernen (anstatt eine konstante Spanlast aufrechtzuerhalten), oder für Situationen, in denen das Werkzeug schneidet Bedingungen nähern sich niemals unsicheren Schnittkraft- oder Spindelleistungsniveaus.
Laut Granata verwenden viele OptiPath-Kunden weiterhin ihre bewährten OptiPath-Strategien, wenn sie mit der Force-Optimierung beginnen, insbesondere bei härteren oder schwer zu bearbeitenden Materialien, und verwenden OptiPath beim Schneiden mit bestimmten Werkzeugen, die diese Optimierungsmethode bevorzugen. Allerdings betont er, dass es keinen einheitlichen Ansatz für die Programmierung gibt.
„Es hängt von den Strategien ab, die Benutzer bevorzugen“, sagt er. „Wenn Sie ein OptiPath-Power-User sind, sind Sie wahrscheinlich eher geneigt, die Force-Optimierung zu Ihrer OptiPath-Lizenz hinzuzufügen und beide aufzurufen. Sie haben dann die Wahl eine Tool-für-Tool-Basis, die zu verwenden ist. Programmierer können sogar Strategien während eines Werkzeugwegs ändern, um die effektivste Optimierung zu erreichen. Die beiden ergänzen sich, um die bestmöglichen Optimierungsstrategien anzubieten.“
Die Erfahrungen des UMC-Programmierteams scheinen diese Theorie zu stützen. Mahn stellt fest, dass Force die Zykluszeit bei Aufträgen, die das Team zuvor über OptiPath ausgeführt hat, um durchschnittlich 5 bis 6 % weiter verkürzt hat. Als Nebeneffekt haben Mahn und Lahr auch festgestellt, dass Force ihre gesamte Programmierzeit verkürzt. „Mit Force müssen wir bei der Werkzeugwegerstellung in unserer CAM-Software nicht ganz so genau sein“, sagt Lahr. „Die vielleicht größte Anpassung für mich war, Force sein Ding machen zu lassen. Es schlägt oft eine Vorschubgeschwindigkeit vor, die mindestens doppelt so hoch ist wie die, die ich verwendet hätte, aber wenn Sie es einfach loslassen, macht Force es richtig.“
Industrielle Ausrüstung
- Rutronik:drahtlose Multiprotokoll-SoCs und -Module von Redpine Signals
- Timken erwirbt QM-Lager und Antriebstechnik
- Additive Fertigung mit Verbundwerkstoffen in der Luft- und Raumfahrt und Verteidigung
- Erfolgsgeschichte:Schneller ROI und Unternehmenswachstum
- Drei Schritte zum Umgang mit Lieferantenrisiken und höherer Gewalt
- Top 5 Unterscheidungsmerkmale eines Experten- und führenden Formenbauerteams
- Werkzeugdrehmaschine
- CNC-Drehmaschine
- Unternehmen für Telekommunikation und Internetdienste, WBL Services, setzt Fluke Connect® ein
- Was ist Interoperabilität und wie kann mein Unternehmen sie erreichen?