Wellen schlagen mit Drehmaschinenautomatisierung
Als Stolz des Staates Badger ist Mercury Marine lokal einfach als „Merc“ bekannt. Die 81 Jahre alten Wurzeln dieser amerikanischen Ikone verleihen ihr eine reiche Geschichte, die sie zum Stolz der Gemeinde und zum Liebling der Bootsöffentlichkeit macht. In der Zwischenzeit macht sein Erfolg Merc zum Neid seiner Konkurrenten. Mercury Marine ist ein weltweit führender Hersteller aller Arten von Schiffsantriebssystemen – eine 2,6 Milliarden Dollar schwere Abteilung der Brunswick Corp., die mehr als 5.200 Mitarbeiter an mehreren Standorten auf der ganzen Welt beschäftigt.
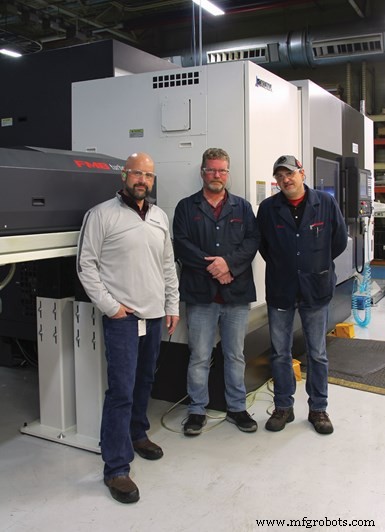
Jason Noworatzky, Bill Cusick und Chris Erke ( L-R) sind Teil des Teams, das alle Zahnräder und Wellen für die weltweit eingesetzten Innen- und Außenbordantriebe von Mercury Marine herstellt.
Mehr als 80 Jahre innovative Entwicklung von Bootsmotoren haben den Standort Fond du Lac, Wisconsin, zu einer äußerst bekannten Quelle für Ingenieurskunst und Produktionsexzellenz gemacht. Der heutige weitläufige Campus neben der Interstate 41 verfügt über mehr als 2,5 Millionen Quadratfuß Fläche, die alle Arten von Ingenieur- und Fertigungsdisziplinen zusammen mit den etwa 3.300 Personen umfasst, die alles möglich machen.
In Werk 4 werden alle Zahnräder und Wellen für alle Innen- und Außenbordantriebe von Mercury Marine hergestellt, die in seinen Werken auf der ganzen Welt hergestellt werden. Dieses gewaltige Unterfangen umfasst Kardanwellen, Antriebswellen, Lenkwellen, Vorwärtsgänge, Rückwärtsgänge und Ritzel für alle MerCruiser-Innenbordmotoren und Z-Antriebsmotoren, MerCruser Alpha- und Bravo-Z-Antriebe, Mercury-Dieselmotoren und Diesel-Z-Antriebe, den Mercury SportJet und alle Außenbordmotoren. Verantwortlich für das Team aus Fertigungsingenieuren, Wirtschaftsingenieuren und Programmierern, das für diese schwere Aufgabe benötigt wird, ist Jason Noworatzky, Engineering Manager von Werk 4. Für alles, was mit dem Herstellungsprozess von Wellen und Zahnrädern zu tun hat, erstellen und etablieren Herr Noworatzky und sein Team die Herstellungs- und Qualitätsverfahren sowie die erforderlichen Kapitalausgaben, um die Teile effizient zu produzieren und vor allem die strengen Spezifikationen von Mercury zu erfüllen . Als nächstes wählen sie die besten Maschinen und Automatisierungen basierend auf Geschwindigkeit, Arbeitskosten und Teileperfektion aus. „Qualität – darauf bauen wir den Prozess auf“, sagt Herr Noworatzky.
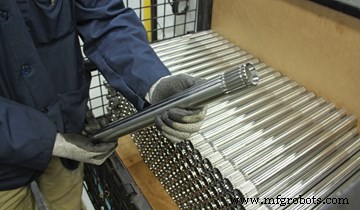
Dieser Abschnitt der Lenkwelle für die Außenbordmotoren des Unternehmens wurde ursprünglich in einer Fünf-Maschinen-Zelle mit zwei Bedienern produziert, wird aber jetzt von einer Drehmaschine mit zwei Revolvern und zwei Spindeln bearbeitet, die mit einem Stangenlader und einem Entlader kombiniert ist.
Ein besonders arbeitsintensives Bauteil ist ein hohler Abschnitt von Steuerwellen, die in Außenbordmotoren von Mercury Marine verwendet werden. Der bisherige Prozess war eine Mehrmaschinenzelle. Den Anfang machte eine einspindlige Drehmaschine mit einem Revolver und einem Reitstock mit Stangenlader. Es würde dann für einen Bohrmaschinenbetrieb zu einer anderen Maschine transportiert. Als nächstes wurden die Teile für einen spitzenlosen Schleifvorgang zu einer anderen Maschine bewegt und dann zu einem abschließenden Wälzfräsvorgang transportiert. Diese Teilefertigungsmethode wurde über Jahrzehnte angewendet. „Ich bin seit 25 Jahren hier und es wurde immer so gemacht“, sagt Bill Cusick, Fertigungsingenieur. Dieser frühere Zellenprozess mit mehreren Maschinen verwendete zwei Bediener.
Schließlich stellte sich heraus, dass die Maschinen in diesen Zellen ersetzt werden mussten. Auf der Suche nach einer modernen Lösung untersuchte Herr Cusick neue und moderne Maschinen. „Die Technologie hat endlich aufgeholt, sodass wir jetzt alle Prozesse in einer Maschine anwenden konnten“, bemerkt Herr Cusick. „Wir mussten sie nicht mehr auf den alten Wälzfräsmaschinen fahren.“
Chris Erke, leitender Programmierer, äußert sich zum Qualitätsproblem. „Es ist schwierig, die wahre Position und den Rundlauf von einer Maschine zur anderen zu halten, anstatt alles in einer Maschine zu erledigen, wo Sie es kontrollieren können.“
Eine feine Balance
„Ein großer Teil dieses Schrittes war für uns die Qualität“, sagt Herr Cusick. „Das bedeutet, in einer Maschine erledigt.“ Das Team musste einen feinen Balanceakt zwischen Maschinenkapazität und -fähigkeiten, Anzahl der Maschinen und den prognostizierten Produktionsanforderungen vollbringen. Nachdem eine Art Scoreboard erstellt wurde, hat sich eine Lösung durchgesetzt. Herr Cusick ging zu Morris Midwest, dem vertrauenswürdigen lokalen Werkzeugmaschinenhändler des Unternehmens, und begann ein Gespräch über den Austausch der alten Zellen mit fünf Maschinen. „Wir haben ein SOW (Statement of Work) erstellt, das erklärt, dass wir eine Drehmaschine wollten, die unseren Bearbeitungsprozess vollständig durchführt“, sagt Herr Cusick. „Wir hatten eine ziemlich gute Vorstellung davon, was es unserer Meinung nach bedeuten würde, die benötigte Zykluszeit beim Hinzufügen der zusätzlichen Operationen zu erreichen.“
Herr Cusick und Herr Erke teilten Morris Midwest mit, dass sie glaubten, dass eine Drehmaschine mit zwei Revolvern und zwei Spindeln in Kombination mit einem Stangenlader und einem Entlader funktionieren würde. „Mit den neuen Technologien dachten wir nicht, dass es ein Problem sein würde, es so zu produzieren, dass es an einem Ende geht und fertig herauskommt“, bemerkt Herr Erke. „Wir wussten ziemlich genau, wie man es komplett macht, aber Morris Midwest wählte die richtige Maschine aus, führte die gesamte Technik durch und kümmerte sich um alle Abflüsse.“
Der Aufstieg von Frankenlathe
2017 wurde die erste neue Kombinationszelle aus Stangenlader/Drehmaschine/Entlader an Werk 4 geliefert. Aufgrund ihrer Größe und Leistungsfähigkeit wurde die neue Okuma LT3000 EX liebevoll „Frankendrehmaschine“ genannt. Bald darauf wurde eine zweite Zelle (ein exaktes Duplikat von Nummer eins) neben der ersten positioniert und vom Ladenpersonal schnell als „Braut von Frankenlathe“ bezeichnet.
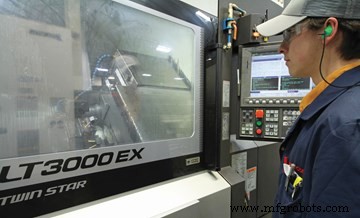
Drei Okuma LT3000 EX-Drehmaschinen mit Stangenladern und Entlader, wurden hinzugefügt, um die Produktion der Wellen zu bewältigen.
Die „Frankendrehmaschinen“ werden beide von Maschinen von Edge Technologies flankiert, was den Prozess zu einem echten einmaligen technologischen Vorteil macht. Die in dieser aktuellen Konfiguration verwendete Automatisierung war das fehlende Teil, das für die Herstellung des Teils „eins und fertig“ mit der erforderlichen Qualität benötigt wurde. Die Okuma LT3000 EX ist eine Drehmaschine mit offener Architektur, ein hochflexibles zweispindliges Drehzentrum in der 8-Zoll-Spannfutterklasse. Diese multifunktionale horizontale Doppelspindelmaschine integriert Dreh- und Fräs-/Bohrfunktionen auf allen Revolvern.
Die ersten beiden Zellen wurden mit Stangenladern FMB Turbo 5-65 ausgestattet. Dies sind Einheiten im Magazinstil, die Stangen mit einer Länge von bis zu 12 Fuß zuführen und über ölgefüllte Kanäle verfügen, die einen hydrodynamischen Lagereffekt um sich drehende Stangen für einen reibungslosen Lauf erzeugen. Die Magazinspeicherkapazität beträgt 11 Zoll bei den Standardeinheiten. Mit der Teilelänge und Zykluszeit für diesen Wellenabschnitt kann der Okuma während einer Schicht eine ganze Reihe von Rohren in linearer Länge verarbeiten, daher fügte Edge Technologies den Edge BarLift hinzu, ein erweitertes Magazinladesystem, das über zusätzliche 28 Zoll Material verfügt längerer Betrieb, ohne dass der Bediener den Feeder von Hand beladen muss.
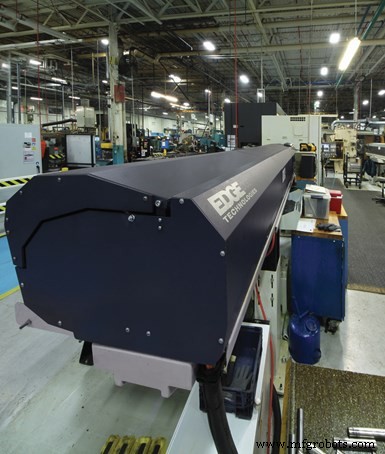
Der FMB Turbo 5-65 12 Fuß Stangenlademagazine im Magazinstil verfügen über ölgefüllte Kanäle, die einen hydrodynamischen Beringeffekt um sich drehende Stangen für einen reibungslosen Lauf erzeugen.
„Wir hatten in der Vergangenheit vielleicht eine oder zwei Drehmaschinen mit einem Entlader, aber dies ist bei weitem der größte Schritt bei dem Mainstream-Produkt, das wir gemacht haben (einem Entlader),“ sagt Herr Noworatzky. „Wir können dieses Teil nicht fallen lassen, weil es die Keile beschädigen würde. Das fertige Teil hat Anforderungen an die Oberflächenbeschaffenheit.“
Die Zellen eins und zwei wurden 2017 installiert und mit FleXsys LE (Load/Extract)-Einheiten von Edge Technologies für den Teileentladeprozess ausgestattet. Diese Einheit ist für die Automatisierung größerer Teile konzipiert – insbesondere Arbeiten mit langen Wellen. Es wurde entwickelt, um auf Teillänge geschnittenes Stangenmaterial mit einem Durchmesser von bis zu 2,5 Zoll und einer Länge von 37 Zoll für die Produktion mit einspindligen CNC-Drehmaschinen zuzuführen und zurückzuziehen. Das 12-Fuß-Rohrmaterial wird mit dem FMB Turbo 5-65 in die Hauptspindel des Okuma eingeführt.
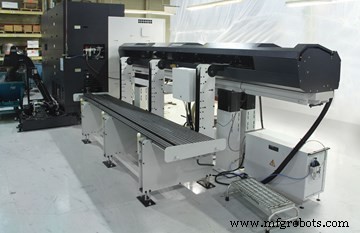
Das erweiterte Magazinladesystem Edge BarLift verfügt über eine zusätzliche 28 Zoll Schaft für längeres Laufen ohne Bedienereingriff.
Frankenlathe 3:Der Aufstieg der Automatisierung
Die dritte Zelle kam Ende 2019 mit dem neuen Rebel 80 Servo Unloader, dem zuletzt entwickelten automatischen Teileentnahmesystem von Edge Technologies zum Entnehmen von Teilen in einem Durchmesserbereich von 8 bis 80 mm. Dies ist eine vielseitigere Einheit als die vorherige Version, die auf den Zellen eins und zwei läuft. Die älteren Einheiten hatten kein Steuerungssystem, das mit der Drehmaschine kommunizieren würde, wie dies bei den FMB-Stangenlademagazinen der Fall ist. Eine zusätzliche Programmierung des FleXsys LE war erforderlich. Obwohl die Einheiten nach der Anpassung gut liefen, bat Mercury Marine Edge Technologies, eine aktualisierte Entladekonfiguration bereitzustellen, die diesen Mangel beheben würde. Die Entwicklung des Rebel 80 Servo Unloader war die Antwort. Edge hatte an dem neuen Entlader gearbeitet und machte das Kommunikationsproblem zu einer Hauptpriorität für die Mercury-Installation. Jetzt kommunizieren und funktionieren in der dritten Zelle der Okuma LT3000 EX, der FMB-Stangenlader und der Edge-Entlader als eine Maschine mit Industrie 4.0-Optimierung.
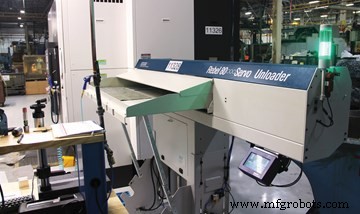
Während die ersten beiden Drehmaschinen mit FleXsysLE ausgestattet waren Entlader, der für die Automatisierung größerer Teile ausgelegt ist, verfügt der dritte Okuma über den Rebel 80 Servo Unloader, der für die Entnahme von Teilen mit einem Durchmesser von 8 bis 80 mm ausgelegt ist und über optimierte Kommunikationsmöglichkeiten mit dem Stangenlader und der Werkzeugmaschine verfügt.
Der Rebel 80 Servo Unloader bietet mehrere Möglichkeiten zum Entfernen von Teilen mit verschiedenen Methoden zum Anbringen des Abziehers an dem Teil, um es von der Gegenspindel abzuziehen. Diese Geräte sind als Endeffektoren bekannt. Zu den verfügbaren Endeffektor-Mechanismen gehören Stangenspannzangen für das Greifen des Außendurchmessers, Erweiterungs-Innengreifer, Dreipunkt-Außengreifer, Vorschubfinger, Winkelgreifer, Elektromagnete für ferromagnetische Materialien und spezielle technische Lösungen für profiliertes und unregelmäßig geformtes Material.
Um die Teileoberflächen zu schützen, legt die V-Ablage im Fall der Keile an der Lenkwelle die Wellen sanft auf der Oberfläche des Magazins ab, die mit einem nichtmetallischen Material bedeckt ist. Der Neigungstisch ist verstellbar, sodass der Entlader Teile mit großem Durchmesser „einfach entladen“ kann.
Der Rebel 80 Servo Unloader verfügt über eine axiale Verschiebungsbahn, die es ermöglicht, dass die Einheit zum Wechseln der Spindelbuchse und zum Wartungszugang zur Rückseite der Drehmaschine leicht von der Drehmaschine weggeschoben werden kann. Es ist mit einer Fernbedienung und einer Dialogsteuerung mit Touchscreen und menügesteuerter Programmierung ausgestattet. Die Steuerung speichert auch unbegrenzt viele Teileprogramme.
Auch die dritte Zelle profitierte von einer Weiterentwicklung der Stangenlademagazin-Technologie. Der FMB Turbo 5-65 war als A-Modell mit dem neuen Führungskanalsystem mit automatischer Anpassung ausgestattet. Die Polyurethan-Führungskanäle passen sich automatisch an den richtigen Durchmesser an, sodass ein Führungskanal Stangendurchmesser von 5 mm bis 65 mm führen kann. Diese Funktion gibt Mercury Marine die Möglichkeit, ohne Änderungen des Führungskanalsatzes schnell auf andere Wellendurchmesser umzustellen. Dieses Design hilft bei schnellen Einstellungen für die Just-in-Time-Produktion.
Neben der Steigerung der Teilequalität bieten diese Zellen den Vorteil, dass Arbeitskosten gesenkt und die Stellfläche besser genutzt werden. Im Idealfall hätte Herr Noworatzky ein unbeschriebenes Blatt, um seine Produktionshalle nach seinen Wünschen umzugestalten. Er erklärt, dass die beiden Dinge, die sein Team antreiben, darin bestehen, Operationen zu kombinieren und zu versuchen, die Arbeit zu teilen.
Für die Zukunft ist Herr Noworatzky der Ansicht, dass das Hinzufügen von Automatisierungen wie Stangenladern und -entladern, die bei diesen Drehmaschinen eingesetzt werden, die Norm sein wird. „Ich sehe von jetzt an keine neuen Zellen mehr hier rein, die nicht über irgendeine Art von Automatisierung verfügen. Ob FANUC-Roboter, Portalsystem, Stangenlader oder Entlader.“ Er sagt voraus, dass es etwas sein wird, um den Arbeitsaufwand zu minimieren, der für die Erledigung einer Arbeit erforderlich ist. „Arbeit ist eine Prämie“, schließt Herr Noworatzky.
Aufgrund des höheren technischen Fachwissens, das für den Betrieb solcher Zellen erforderlich ist, bietet Mercury Marine den Mitarbeitern Schulungen an, um ihre Fähigkeiten zu verbessern. „Es erfordert einen höheren Bedienerlevel“, sagt Herr Noworatzky. Um dies zu erreichen, schickt Mercury seine Bediener zu einer örtlichen Volkshochschule, wo sie sich für Bearbeitungskurse der Stufen 1 und 2 anmelden. Sobald sie abgeschlossen sind, können sie testen, um die NIMS-Zertifizierung zu erhalten.
Mercury Marine | mercurymarine.com
Edge-Technologien | 314-692-8388 | edgetechnologies.com
Über den Autor
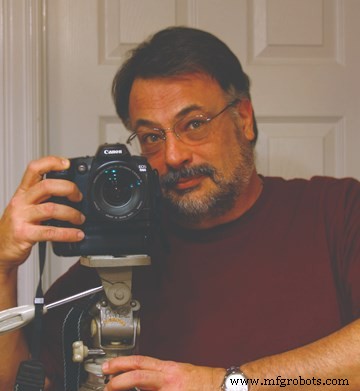
Kevin Shults
Kevin Shults ist Werbe- und Designprofi. Er verfügt über 24 Jahre Erfahrung in der Werkzeugmaschinenindustrie, von denen er die letzten 20 Jahre als Marketingleiter für einen OEM in der Präzisionsbearbeitungsindustrie tätig war. Kontaktieren Sie Herrn Shults unter [email protected].
Industrielle Ausrüstung
- Geld verdienen mit CNC-Fräsern
- Evolution der Testautomatisierung mit künstlicher Intelligenz
- Geschäftsautomatisierung mit Low-Code-Plattformen
- Verbesserung des Kundenerlebnisses mit intelligenter Automatisierung
- Standard-Drehmaschine mit Touchscreen-Steuerung
- Drehmaschine mit CNC
- CNC-Drehmaschine mit hydrostatischem Linearführungssystem
- Mehrfachwerkzeug-Drehmaschine mit Polymerbasis – SNK
- Schrägbett-Drehmaschine verfügt über eine Steuerung mit Verifizierungsgrafiken
- Drehmaschine für manuellen Betrieb mit CNC-Unterstützung