Industrielles IoT:Aufstieg des digitalen Zwillings im Fertigungssektor
Der Begriff digitaler Zwilling ist nichts anderes als eine Konzeptualisierung der Aufrechterhaltung einer digitalen Übereinstimmung eines physischen Objekts, des Betriebs, unter Verwendung der Daten von intelligenten Geräten wie Sensoren. Der Kanal, der den digitalen Zwilling und seinen physischen passenden Teil verbindet, wird als digitaler Faden bezeichnet. Das digitale Modell wird wahrscheinlich regelmäßig modifiziert und aktualisiert, wobei künstliche Intelligenz und Daten angemessen integriert werden. Darüber hinaus bietet es auch tatsächliche und gleichzeitige virtuelle Realität. Entscheidend ist die Kombination des physischen Objekts mit dem computergenerierten Gegenstück. Als Technologietrend des industriellen IoT steigt, ist die Technologie des digitalen Zwillings heute wichtiger denn je.
Die digitalen Gegenstücke sind mit der Netzwerktechnologie verbunden und ihre Fähigkeit, Probleme zu beseitigen und eine höhere Betriebsleistung bereitzustellen, macht dieses digitale Matching-Teil zur wesentlichen Technologie für jede Organisation.
Indem den Unternehmen eine vollständige digitale Nachbildung der Produkte angeboten wird, ermöglicht die Technologie des digitalen Zwillings der Industrie, physische Probleme in der Ausrüstung frühzeitig zu erkennen, sodass sie geeignete Maßnahmen ergreifen können, um die potenziellen Probleme zu beseitigen, bevor sie auftreten.
Aber eine digitale Nachbildung der Ausrüstung zu erstellen, ist eine entmutigende Aufgabe. Der beste Weg, dies zu erreichen, besteht darin, ein digitales Gegenstück für eine Abteilung in der Fertigungseinheit zu erstellen, es in die Tat umzusetzen und dann mit der Entwicklung des digitalen passenden Teils für andere Bereiche der Fertigungseinheiten fortzufahren.
Darüber hinaus unterscheidet sich der digitale Zwilling vom CAD (Computer Aided Design). Das eigentliche Potenzial des digitalen Pendants besteht darin, dass es schnell die tatsächlich verbreitete Verbindung zwischen der physischen und der digitalen Domäne in der Industrie bieten kann.
Verwandter Beitrag:Eine Zusammenfassung der Marktschätzung und ihrer Phasen
Die Digital-Twin-Technologie verändert das Gesicht der Fertigungsindustrie und senkt dadurch die Kosten; Kontrolle von Vermögenswerten und verringert die durch Geräteausfälle verursachte Ausfallzeit. Der digitale Abgleich eines physischen Objekts in der Industrie spielt eine entscheidende Rolle im industriellen IoT. Diese Technologie erweitert auch neue Möglichkeiten für jedes Unternehmen weltweit. Die digitale Nachbildung nutzt Technologien wie Virtual Reality, indem sie die Daten- und Grafikmodellierung nutzt, um ein virtuelles Modell jeder Ausrüstung perfekt zu erstellen.
Funktionsweise der digitalen Zwillingstechnologie:
In dieser heutigen Technologie sammeln Sensoren, die von den physischen Objekten in der Fabrik begleitet werden, Daten und übertragen die Daten an ihre computergenerierte Nachbildung, und ihre Kommunikation verbessert schließlich die Leistung des physischen Objekts. Das Sahnehäubchen ist, dass das virtuelle Gegenstück erstellt werden kann, lange bevor die Ausrüstung physisch in Fertigungseinheiten gebaut wird.
Um den genauen virtuellen Teil eines bestimmten physischen Produkts zu erstellen, ist es für Ingenieure unerlässlich, Daten aus zahlreichen Quellen wie Fertigungsstatistiken, Informationen über seine Funktionsweise und auch aus Analysesoftware zu sammeln und zu kombinieren. Abgesehen davon sind auch KI-Verfahren erforderlich, die in die computergenerierte Nachbildung bestimmter Geräte einfließen.
Digitale Kopien in der Fertigungseinheit werden auf verschiedenen Ebenen verwendet, wie unten erwähnt:
#1 Komponentenebene:
Diese Ebene des digitalen Zwillings hebt die entscheidende einzelne Komponente im gesamten Herstellungsprozess hervor. Das einzige Teil, das am dringendsten benötigt wird, und der Herstellungsprozess hängt stark von dieser bestimmten Komponente ab.
#2 Asset-Ebene:
Digital Replica in Asset Level entwickelt eine digitale Nachbildung eines bestimmten Teils der Ausrüstung, die in der Produktionsphase verwendet wird.
#3 Systemebene:
Wann immer die Hersteller die gesamte Produktionslinie improvisieren müssen, wird die digitale Nachbildung auf Systemebene implementiert.
#4 Prozessebene:
Die Prozessebene betrachtet den gesamten Lebenszyklus eines Produkts. Angefangen vom Produkt-/Prozessdesign und der Entwicklung über die Herstellung oder Produktion bis hin zum Vertrieb und der Art und Weise, wie der Endbenutzer das Produkt verwendet. Was im Ergebnis bei der Entwicklung aktueller und zukünftiger Produkte hilft.
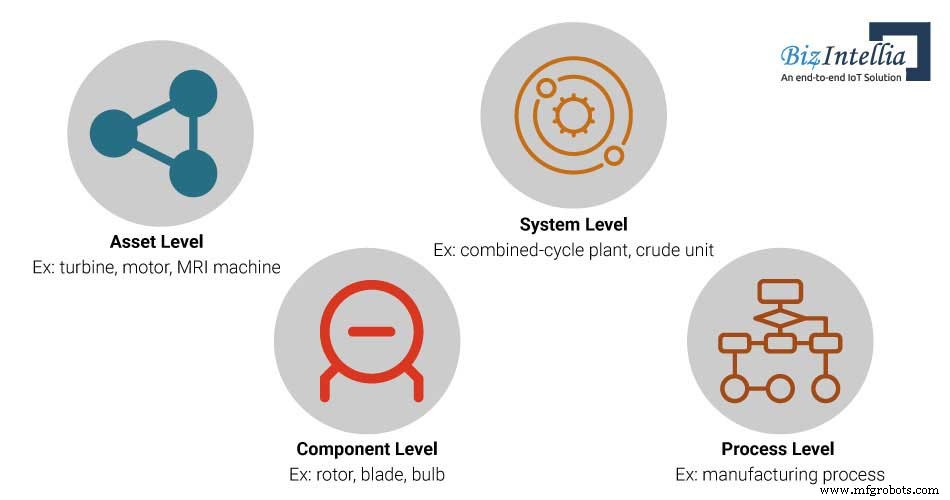
Verwandter Beitrag:5 beste Anwendungen des industriellen IoT im Transportwesen
Konzeptentwurfsplan für digitale Zwillinge:
#1 Konstruieren:
Diese Phase umfasst die Ausstattung eines physischen Objekts mit vielfältigen Sensoren, die Erkenntnisse aus dem physischen Objekt und auch seiner Umgebung messen. Die Messungen werden in 2 Kategorien eingeteilt:
- Betriebsmessungen, die sich auf die physische Leistung der Ausrüstung beziehen, wie z. B. Farbgleichmäßigkeit, Drehmoment, Verschiebung und Zugfestigkeit.
- Die externen Daten, die sich auf den Betrieb der physischen Ausrüstung auswirken, wie Luftdruck, Umgebungstemperatur und Feuchtigkeitsgehalt.
Diese Messungen können mit Hilfe von Encodern in gesicherte digitale Nachrichten umgewandelt werden. Diese digitalen Nachrichten werden dann zu einer digitalen Nachbildung der Ausrüstung übertragen.
#2 Kommunikation:
Diese spezielle Phase realisiert eine nahtlose bidirektionale Konnektivität in Echtzeit zwischen den physischen Prozessen und der digitalen Plattform. Die Netzwerkkonnektivität ist ein entscheidender Faktor, der zur Unterstützung des virtuellen Gegenstücks physischer Geräte einbezogen werden muss. Es beinhaltet weiterhin 3 Elemente:
- Randverarbeitung:
Diese Schnittstelle verbindet Sensoren mit Prozesshistorikern und verarbeitet dann Daten von den Sensoren und leitet sie an die Plattform weiter. Dieses übersetzt proprietäre Protokolle, um die Datenformate verständlich zu machen und die Netzwerkkommunikation zu reduzieren. Die Edge-Verarbeitung beschleunigt die Netzwerkkommunikation, indem die aufgenommenen Daten an den Endpunkten verarbeitet werden.
- Kommunikationsschnittstelle:
Die Kommunikationsschnittstellen helfen, verarbeitete Daten (Informationen) von der Sensorfunktion zur Integrationsfunktion zu übertragen. Je nach Konfiguration des digitalen Zwillings kann der Sensor, der die Erkenntnisse liefert, überall platziert werden:in einem Bergbaubetrieb, in einem Haus, auf einem Parkplatz, fast an jedem Ort.
- Edge-Sicherheit:
Die Einführung neuer Sensoren und Kommunikationsmittel bringt neue Sicherheitsbedrohungen mit sich, die sich schnell weiterentwickeln. Die Notwendigkeit neuer Lösungen, um digitale Zwillinge sicher zu ermöglichen, wird erforderlich sein, wenn die IP-fähigen Assets im Laufe der Zeit wachsen. Die Verwendung von Firewalls, Verschlüsselung, Anwendungsschlüsseln und Gerätezertifikaten sind die gängigsten Sicherheitsansätze.
#3 Aggregation:
Die Datenaggregation kann die Datenaufnahme in ein Data Warehouse/Repository unterstützen, das einfach verarbeitet und für die Analyse vorbereitet werden kann. Die Datenaggregation und -verarbeitung kann sowohl in der Cloud als auch vor Ort erfolgen.
#4 Analysieren:
Eine weitere Phase, die in Aktion tritt, ist die Analyse der Daten. In dieser Phase werden alle Daten gründlich geprüft und ins Auge gefasst. Meistens verwenden Datenanalysten und Wissenschaftler fortschrittliche Analyseplattformen, um Erkenntnisse aus den Daten zu gewinnen, die eine intelligente Entscheidungsfindung ermöglichen.
#5 Erkenntnisphase:
Aus den Analysen generierte Erkenntnisse werden auf Dashboards mit visuellen Darstellungen präsentiert, die geringfügige Unterschiede in der Leistung der analogen physischen Welt und des digitalen Zwillingsmodells in einer oder mehreren Dimensionen hervorheben. Es zeigt die potenziell zu untersuchenden Bereiche an.
Nr. 6 Akt:
Hier nutzen Sie die umsetzbaren Erkenntnisse, die aus dem vorherigen Schritt generiert wurden, und leiten sie an das physische Asset zurück. Die Erkenntnisse passieren Decoder, die die Befehle decodieren, und werden in die Aktuatoren eingespeist, die für die Steuerung und Bewegung von Geräten verantwortlich sind. Die Erkenntnisse können auch in den Back-End-Systemen aktualisiert werden, die die Lieferketten steuern.
Wie legt man den Grundstein mit der digitalen Zwillingstechnologie?
#1 Finden Sie die Möglichkeiten heraus:
Zunächst ist es entscheidend, sich die Bereiche einer Fertigungseinheit vorzustellen und einzugrenzen, die von den Vorteilen der Digital-Twin-Technologie profitieren können. Das Bedarfs- und richtige Szenario kann für jede Produktionseinheit unterschiedlich sein, aber es wird wahrscheinlich die folgenden Merkmale aufweisen:
- Die von Ihnen ausgewählte physische Ausrüstung muss ein entscheidendes Element Ihres Herstellungsprozesses sein, um Geld in die Erstellung eines virtuellen Gegenstücks zu stecken.
- Produkt – Prozessbezogene Probleme können gelöst werden, was möglicherweise einen Mehrwert für das Unternehmen oder den Kunden freisetzen könnte.
Nachdem Sie die Möglichkeiten eingegrenzt haben, muss die Möglichkeit weiter bewertet werden, um Faktoren des Prozesses zu erkennen, die Vorteile des digitalen Zwillings bieten können.
#2 Prozess erkennen:
Der nächste Schritt besteht darin, die Pilotkonfiguration für digitale Zwillinge zu erkennen, die den höchstmöglichen Wert und die hohe Erfolgsquote aufweist. Sie können Faktoren und Abläufe des organisatorischen Änderungsmanagements berücksichtigen, um den besten Kandidaten für das Pilotprojekt zu ermitteln. Unternehmen wählen oft den falschen Ansatz, indem sie tief in den Aufbau eines digitalen Zwillings von hochkomplexen Geräten oder Prozessen einsteigen, und stehen möglicherweise vor Herausforderungen. Stattdessen sollten sie sich darauf konzentrieren, breit statt tief zu gehen:digitale Zwillinge breit im gesamten Unternehmen einzusetzen, was den größten Wert und die größte Unterstützung bringt.
#3 Für den Anfang, gehen Sie eng:
Um den Umfang einzuschränken, kann das Pilotprojekt eine Teilmenge beliebiger Geschäftsbereiche oder Produkte sein. Der begrenzte Umfang sollte zumindest einen Wert für das Unternehmen darstellen. Bei der Entwicklung des Pilotprojekts sollten die Implementierer anpassungsfähig und aufgeschlossen sein. Ein agnostisches Ökosystem ermöglicht Anpassungsfähigkeit und Integration mit den Daten und nutzt neue Partner oder Technologien.
Während Sie unabhängig von Daten (strukturiert und unstrukturiert) und Datenquellen (neue Sensoren oder externe Datenquellen) sein möchten, benötigen Sie eine End-to-End-Lösung, die skalierbar genug ist, um die Erweiterung zu unterstützen.
#4 Pilot erweitern:
Sobald das Pilotprojekt erfolgreich ist, kann es weiter skaliert werden. Jetzt müssten Sie Möglichkeiten identifizieren, wo Sie das Pilotprojekt skalieren und seine Vorteile nutzen können. Vielleicht möchten Sie damit beginnen, benachbarte Prozesse oder Prozesse anzusprechen, die ähnlich sind und Verbindungen zum Pilotprojekt haben. Lernen Sie aus den Fehlern, die während der Pilotentwicklung gemacht wurden, und skalieren Sie sie zügig.
Und ja, vergessen Sie nicht, Ihren Aktionären und größeren Unternehmen den Wert mitzuteilen, der durch die Einführung des digitalen Zwillings entsteht.
#5 Bewerten:
Durch die Überwachung und Messung dieser Lösungen nach ihrer Implementierung können Sie den Wert messen, den der digitale Zwilling liefert. Sie können iterativ Änderungen am zukünftigen digitalen Zwillingsprozess vornehmen und die Ergebnisse beobachten, um die bestmögliche Konfiguration des digitalen Zwillings zu ermitteln.
Zusammenfassung:
Zusammenfassend lässt sich festhalten, dass die Digital-Twin-Technologie, ein hochmoderner Technologietrend, eine entscheidende Rolle bei der Bereitstellung industrieller IoT-Anwendungen spielen wird. Diese neue Technologie wird auch dazu beitragen, der Branche höhere Einnahmen zu verschaffen und unerwünschte Gemeinkosten zu verringern, die aufgrund von Problemen mit Geräten und Prozessen entstehen. Der Trend der Digital-Twin-Technologie trägt auch dazu bei, die Wartungskosten in hohem Maße zu senken. Darüber hinaus erhöht es auch die Konsistenz in der Produktionslinie in einer Organisation. Letztendlich verbessert dieser Technologietrend auch den Kundenservice, der das ultimative Ziel der Industrie ist.
Wenn Sie sich auf die effektive IoT End-to-End-Lösung für Ihr Unternehmen freuen , dann kontaktieren Sie uns , und wir helfen Ihnen weiter bei der Auswahl der richtigen Lösung für Ihre geschäftlichen Anforderungen.
Internet der Dinge-Technologie
- Intelligente Fertigung und das IoT treiben die nächste industrielle Revolution voran
- Digitale Zwillinge können der intelligente Vorsprung für das IoT im Fertigungssektor sein – Teil 2
- Die Leistungsfähigkeit und Fallstricke digitaler Zwillinge in der Fertigung
- IoT World Awards Finalist PTC konzentriert sich auf industrielle AR
- Wie treiben industrielle IoT-Plattformen die Transformation voran?
- Priorisierung des IoT ein Rätsel für digitale Fertigungstechnologien
- Anwendungen von industriellen IoT-infundierten Luftqualitätsüberwachungssystemen
- Kategorisierte Anwendungen von IoT im Transportsektor
- IoT ermöglicht es dem Öl- und Gassektor, operative Exzellenz zu erreichen
- 4 wichtige IoT-Anwendungen in der Fertigung