Episode 29:John McQuilliam, Prodrive Composites
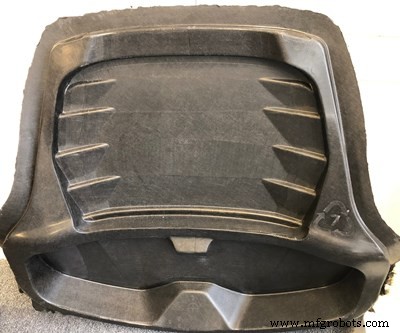
Beispiel für ein mit dem P2T-Verfahren von ProDrive hergestelltes Tertiärteil. CW Foto | Scott Francis
In dieser Folge von CWTalks interviewt CW-Seniorredakteur Scott Francis John McQuilliam, Chefingenieur bei Prodrive Composites (Milton Keynes, Großbritannien), Designer und Hersteller fortschrittlicher leichter Verbundwerkstoffe für eine Vielzahl von Anwendungen, darunter Automobil, Motorsport, Luft- und Raumfahrt, Marine und Verteidigung und andere Fachbereiche.
John ist ein Formel-1-Autodesigner aus Großbritannien, der mit zahlreichen Motorsportunternehmen zusammengearbeitet hat. Er kam 2017 als Chefingenieur der Composites-Sparte zu Prodrive. John spricht über den primären bis tertiären (P2T) Prozess des Unternehmens, der das Recycling vereinfacht und Verbundmaterialien das Potenzial gibt, drei oder mehr Nutzungsdauern zu erfüllen.
Sie können sich die vollständigen CW Talks anhören Interview oben oder besuchen Sie:
- CW-Gespräche:iTunes
- CW-Gespräche:Google Play
Auszug aus der Folge
KW: Hallo John, und willkommen zu CW Talks, dem Composites-Podcast. Ich glaube, es war im März, als ich Prodrive Composites besuchte und ein wenig von Ihrem P2T-Prozess sehen konnte, der für primär bis tertiär steht.
JM: Stimmt. Der erste Schritt ist die Herstellung des Primärteils, und das ist der Großteil unserer Arbeit, die wir derzeit ausführen. Dies sind also Teile, die aus irgendeinem Grund Frischfasern, ein Spezialharz oder eine bestimmte Art von duroplastischem Harz erfordern. Ich würde es also als traditionelle Verbundteile bezeichnen ... es sind Teile, deren Design oder Herstellung wir nicht besonders ändern würden, aber wir würden sie sicherlich ändern, um sie leichter recycelbar zu machen.
KW: Okay. Und das sind normalerweise die leistungsstärkeren Teile?
JM: Ja. Sie würden also aus Duroplast hergestellt … Wir würden einfach das Design ändern, damit das Abfallmaterial von der Herstellung der Teile und letztendlich das Teil am Ende seiner Lebensdauer recycelt werden kann, damit wir die enthaltenen Kohlefasern wiederverwenden können innerhalb dieser Teile. Der Thermoplast kommt also in der zweiten Stufe ... die Anfangsstufen können duroplastisch oder thermoplastisch sein, aber das Wichtigste ist, dass wir die Fasern wiedergewinnen können. Um die Fasern aus den Primärteilen, wie bereits erwähnt, zurückzugewinnen, ändern wir die Designmaterialien auf jeden Fall auf etwas, aus dem die Fasern leichter zurückgewonnen werden können. Wir sprechen also wirklich über eine verstärkte Verwendung von Non-Crimp-Stoffen, mehr unidirektionale Materialien, Dinge, bei denen der Produktionsabfall und das Bauteil, wenn sie für den Faserrückgewinnungsprozess durchlaufen, eine bessere Ausbeute an längeren hochwertigen Fasern ergeben.
KW: Können Sie den Rückgewinnungsprozess für diese Primärkomponente ein wenig beschreiben und was kennzeichnet dann den resultierenden Sekundärteil?
JM: Ja. Das Recycling- oder Rückgewinnungsverfahren für die Primärteile ist also ein Verfahren vom Verbrennungstyp. Das Abfall-Prepreg – das Prepreg-Abschnitt – oder die Altteile gehen in einen Ofen und das gesamte Harz wird abgebrannt, wobei die Kohlefasern zurückbleiben. Und diese Kohlefasern werden durch eine Reihe von Prozessen zu einer Vliesmatte mit konstanter Dicke und zufälliger Ausrichtung verarbeitet – so dass sie am Ende in der Lage ist, eine quasi-isotopische Plaque herzustellen.
KW: Ist dies der Prozess, den ELG [ELG Carbon Fibre] für Sie übernimmt? Behandeln sie die Pyrolyse?
JM: Ja, ELG macht diesen Teil davon. Also schicken wir ihnen unsere Abfallreste und einige Einzelteile und sie verwandeln sie dann wieder in einen der Vorläufer, einen der Teile, aus denen wir unsere Sekundärteile herstellen.
KW: Kannst du mir etwas über diese Nebenteile erzählen und was sie ausmacht?
JM: So besteht bei den Sekundärteilen die Verstärkung hauptsächlich aus den recycelten Kohlefasern mit einem dezenten Einsatz von Frischfasern, wenn dies in bestimmten Bereichen erforderlich ist. Der Großteil der Verstärkung besteht jedoch aus recycelten Fasern. Und dann stellen wir einen reaktiven Thermoplast vor. Dies ist also ein flüssiges Harz, mit dem wir, sagen wir, die Verstärkungen aufgießen. Dann gibt es einen Aushärtungsprozess und wir erhalten ein fertiges Bauteil, das bei relativ niedrigen Temperaturen und atmosphärischem Druck verarbeitet wird, und wir erhalten so ein gutes Bauteil.
KW: Ein Teil dessen, was P2T ermöglicht, ist dieses Harzsystem, das Sie als „reaktives thermoplastisches Harz“ beschrieben haben. Kannst du unseren Hörern noch ein bisschen erklären, was du damit meinst?
JM: Reaktiver Thermoplast ist also in gewisser Weise einem duroplastischen Harz sehr ähnlich. Also mischen wir es unmittelbar vor der Herstellung des Bauteils. Und die Mischung enthält zwei oder drei flüssige Komponenten. Jedes davon ist eine Flüssigkeit. Und wenn sie sich mit der Zeit und ein wenig Temperatur verbinden, polymerisieren sie tatsächlich zu einem echten Thermoplast. Und es sind die thermoplastischen Eigenschaften, die ein späteres Recycling ermöglichen. Und der Vorteil, dass es sich um einen reaktiven Thermoplast im Gegensatz zu einem herkömmlichen Thermoplast handelt, ist die Tatsache, dass wir effektiv einen Thermoplast herstellen und gleichzeitig die Verstärkungsfasern umgeben , sollten wir sagen, duroplastische Prozesse. Es braucht nicht die hohen Temperaturen und die hohen Drücke, die Sie erhalten, wenn Sie entweder einen geschmolzenen Thermoplast in eine Faservorform einspritzen oder ein Thermoplast-Prepreg nehmen, bei dem der Thermoplast und die Fasern bereits kombiniert wurden, und sie dann bei hoher Temperatur und hohem Druck wieder montieren , typischerweise in metallischen Formen. So vermeiden wir die Komplexität und Kosten der Formwerkzeuge, die für die Verarbeitung von Thermoplasten oberhalb des Schmelzpunktes erforderlich sind, und vermeiden die Schwierigkeiten aufgrund der hohen Viskosität des geschmolzenen Thermoplasts mit Verformung und Bewegung der Verstärkung im Formhohlraum.
KW: Und ich schätze, das führt zu Kosteneinsparungen, Zeiteinsparungen und bedeutet im Grunde genommen einiges für die Produktion...
JM: Du hast es, ja. Das Produktionsverfahren ist also dem, was wir in der traditionellen Duroplastenindustrie tun, ähnlich, aber die Werkzeugkosten sind viel niedriger als für die Verarbeitung eines herkömmlichen Thermoplasts erforderlich. Und das ist für die meisten unserer Kunden ein großer Vorteil. Sie möchten keine Vorabinvestitionen in Formwerkzeuge für Thermoplaste tätigen – oder Formwerkzeuge einfach für Thermoplaste.
KW: Sehen Sie dies also als Wegbereiter für mehr Massenproduktion?
JM: Natürlich glauben wir, dass es ein Wegbereiter für eine höhere Produktion ist. Die Zykluszeiten können kürzer sein als beim herkömmlichen Duroplast, da kein Hochfahren auf eine Verarbeitungstemperatur, kein Verweilen und dann ein erneutes Abkühlen erforderlich sind, bevor Sie die Form umdrehen können. Daher sehen wir durch die Verwendung dieses Verfahrens im Vergleich zu unseren herkömmlichen ofen- oder autoklavgehärteten Komponenten Preisvorteile.
KW: Und natürlich ist eines der aufregenden Dinge, dass Sie diesen Sekundärteil von dort aus wieder recyceln können. Was also charakterisiert diesen Tertiärteil im Lebenszyklus dieses Materials?
JM: Ich würde also sagen, dass das Sekundärteil, das ein echter Thermoplast ist, in andere Formen umgeformt werden kann und normalerweise in kleine Stücke geschnitten und dann in die Kavität zwischen der Heizform gelegt und in eine neue Form gepresst wird. Somit besteht die Möglichkeit, alle überflüssigen Sekundärteile, alle Produktionsabfälle aus den Sekundärteilen, zu nehmen und zu einem anderen faserverstärkten Kunststoffbauteil oder faserverstärkten Polymerbauteil umzuformen.
KW: Und von da an sind diese tertiären Teile nicht unbedingt das Ende der Straße für dieses Material, selbst dann...
JM: Das ist richtig ... Wir denken also, dass diese Tertiärteile, weil sie thermoplastisch sind, fast unendlich oft umgeformt werden können. Der Prozess des Zerschneidens in Formpaletten, sagen wir Formteile, hat eine Abriebrate der Faser… daher würden einige der mechanischen Eigenschaften sinken, aber andere mechanische Eigenschaften wie die Steifigkeit, die Wärmeausdehnungsrate und die Verformung Die Temperatur würde ziemlich gut gehalten werden. So erhält man immer noch ein qualitativ hochwertiges faserverstärktes Bauteil — nicht mit der ursprünglichen Festigkeit eines Endlosfaserbauteils oder gar eines relativ langen Faserbauteils — aber es bleiben auf jeden Fall die Vorteile in Bezug auf Steifigkeit, Wärmeausdehnung und die Verwindungstemperatur, die es sehr lohnenswert machen die Tertiärteile mal wieder aufbereiten.
Faser
- Die 10 wichtigsten Fortschritte in der Fertigungstechnologie für Verbundwerkstoffe
- Damals und heute:Eine kurze Geschichte der Verbundwerkstoffe
- Auf was man bei Herstellern von Verbundwerkstoffen achten sollte
- Thermoplastische Verbundwerkstoffe bei Oribi Composites:CW Trending, Episode 4
- AMRC und Prodrive arbeiten zusammen, um die Herstellung recycelbarer Verbundkomponenten voranzutreiben
- Hochleistungsverbundwerkstoffe in Israel
- Folge 17:Gino Francato, Sabic; Arno van Mourik, Airborne; John OConnor, Siemens
- Episode 26:Achim Fischereder, Hexcel
- Nationale Composites Week:Nachhaltigkeit
- Nèos International gründet neues Hauptquartier für Verbundwerkstoffe in Großbritannien