Umspritzte Hybridteile eröffnen neue Märkte für Verbundwerkstoffe
Komplexität und Stärke. Bauteile wie die B-Halterung für Flugzeuglagerkästen weisen sowohl eine hohe Komplexität als auch eine hohe Festigkeitsanforderung auf – eine Kombination, für die sich die Hybrid-Overmolding-Technik besonders eignet. Quelle, alle Bilder | TxV Aero Composites
Auf dem Luft- und Raumfahrtmarkt ist ein OEM oft bereit, mehr für ein Verbundbauteil zu zahlen, da er weiß, dass sich die Investition aufgrund des geringen Gewichts des Bauteils, einer längeren Lebensdauer durch weniger Verschleiß oder anderer Betriebseinbußen in Kraftstoffeinsparungen auszahlt und Wartungskosten. Diese Sicht des „Produktlebenszyklus“ hat viele Märkte und Anwendungen für Verbundwerkstoffe geöffnet. Ungewöhnlicher ist ein Verbundbauteil, bei dem die Anschaffungskosten selbst geringer sind als bei der Metallausführung. Aber das ändert sich. Einige neue automatisierte Herstellungsverfahren für Verbundwerkstoffe beginnen den Ausschlag zugunsten von Verbundwerkstoffen zu geben, darunter ein von TxV Aero Composites (Bristol, R.I., U.S.) entwickeltes Hybrid-Overmolding-Verfahren.
Als Joint Venture von Tri-Mack Plastics Manufacturing (Bristol, R.I., USA) und Victrex (Thornton Cleveleys, Großbritannien) hat TxV seine Hybrid-Overmolding-Technik zur kommerziellen Produktion weiterentwickelt. Das Unternehmen hat sich mit SFS intec Aircraft Components (Althengstett, Deutschland) zusammengetan, um eine Halterung für Flugzeugablagebehälter neu zu entwickeln und kommerziell zu produzieren, die zuvor aus Aluminium in Luft- und Raumfahrtqualität hergestellt wurde. Die Halterung ist eine eigene Erfolgsgeschichte und zeigt auch das Potenzial von Hybrid-Overmolding und VICTREX AE 250 unidirektionalem Carbonfaser/Polyaryletherketon (PAEK)-Band für wertvolle Gewichts- und Kosteneinsparungen in zahlreichen Luft- und Raumfahrtanwendungen – Vorteile, die durch den Ersatz eines subtraktiven Metallbearbeitungsprozesses durch ein Verbundprozess, bei dem Material hinzugefügt, nicht abgezogen wird.
Von der Subtraktion zur Addition
Maschinisten und Werkstätten, die Metallkomponenten auf CNC-Maschinen herstellen, haben sich selbst als „Chipmaker“ bezeichnet, da ihre Prozesse nicht benötigtes Material von Metallrohlingen entfernen, um Komponenten herzustellen, wodurch Metallspäne entstehen. Diese Späne stellen einen kostspieligen Aspekt der Metallbearbeitung dar, egal ob sie entsorgt, an einen Recyclingbetrieb geschickt oder im eigenen Haus wiederaufbereitet werden. Bei der Dachstaufachhalterung von SFS intec werden 60 bis 70 % des Aluminiums während der mehreren Frässchritte, die für die Bearbeitung erforderlich sind, zu Schrott.
Diese hohe Ausschussrate macht die Rohmaterialkosten für eine Nettoform- oder Endform-Verbundversion der Halterung potentiell niedriger als die Metallmaterialkosten. „Wir können wegen der Späne mit billigerem (pro Pfund) Aluminium konkurrieren; Wenn das Buy-to-Fly-Verhältnis 8:1 beträgt, wird der größte Teil des gekauften Aluminiums zu Schrott“, bemerkt Jonathan Sourkes, Senior Account Manager bei TxV. „Ein weiterer Faktor ist die Zeit, die jedes Bauteil mit dem Fräsen verbringt. Wir können [Verbund-]Teile in Minuten herstellen, nicht in Stunden.“
Abgesehen von den Rohstoffkosten waren Kompositversionen von Komponenten wie der Halterung – die eine komplexe Geometrie aufweisen und eine hohe Tragfähigkeit erfordern – mit historisch verfügbaren Herstellungsoptionen wirtschaftlich nicht realisierbar. Würden die Bauteile einerseits mit einer kostengünstigen Schnittfaserverstärkung in einem Highspeed-Low-Touch-Verfahren wie Spritzgießen hergestellt, würde das Bauteil keine ausreichende Tragfähigkeit erreichen. Auf der anderen Seite, wenn es mit einer höher belastbaren, kontinuierlichen Faserverstärkung über einen langsamen High-Touch-Prozess hergestellt würde, der typischerweise einige manuelle Auflegungen erfordert, wäre die Produktion zu langsam und/oder würde Herstellungskosten verursachen, die das Endprodukt zu teuer.
Aufgrund dieser Hindernisse für neue Verbundwerkstoffanwendungen dieser Art hat die Verbundwerkstoffindustrie insgesamt erhebliche Ressourcen in die Entwicklung automatisierter Prozesse investiert, mit denen solche Komponenten mit angemessen hohen Produktionsraten und mit ausreichender Tragfähigkeit hergestellt werden können, um die Anforderungen und Spezifikationen von Luft- und Raumfahrtkunden zu erfüllen . Mit Blick auf die kommerzielle Produktion solcher Verbundkomponenten wurde TxV im Jahr 2017 speziell zur Beschleunigung der kommerziellen Einführung innovativer Herstellungsverfahren für polyketonbasierte Verbundanwendungen in der gesamten Luft- und Raumfahrtindustrie ins Leben gerufen.
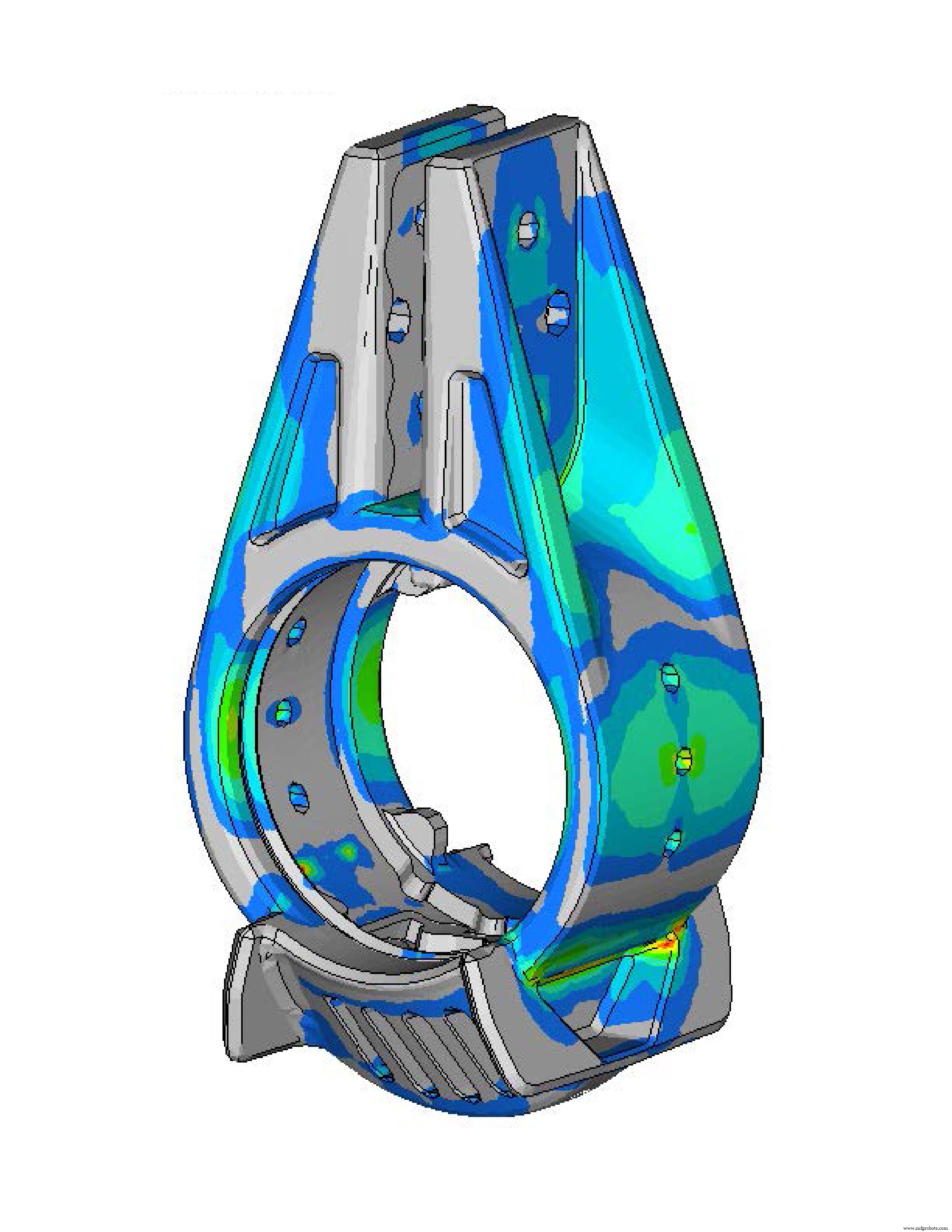
Virtuelles Prototyping. Unter Verwendung proprietärer Daten, die entwickelt wurden, um die Beziehung zwischen Laminat und Overmold zu charakterisieren, iterierte TxV die Layups und Lagenorientierungen, ohne einen physischen Prototyp herstellen und testen zu müssen. Die Iterationen werden fortgesetzt, bis die sichtbaren Spannungen, wie hier dargestellt, im Bereich der angegebenen Lastfälle liegen.
Die umspritzte Hybridlösung von TxV beinhaltet zwei wichtige Fortschritte zum Stand der Technik bei der Herstellung von Verbundkomponenten. Erstens automatisiert es die Herstellung derjenigen Teile des Bauteils, die die Festigkeit oder Steifigkeit einer Endlosfaserverstärkung benötigen. Zweitens nutzt es die Geschwindigkeit des Spritzgießens, um die komplexen Geometrien des Bauteils fertigzustellen. Genauer gesagt produziert es ein maßgeschneidertes Laminat für die Handhabung von Lasten, das dann umspritzt wird, um die endgültigen Teilegeometrien zu funktionalisieren und zu erstellen. Die Hybridtechnik ist laut Sascha Costabel, Head of Innovation bei SFS intec Aircraft Components, „eine gute Option für Bauteile, die hohen mechanischen Belastungen standhalten müssen und Geometrien, die bei konventioneller Bearbeitung mehrere Bearbeitungsschritte erfordern.“
Die Partnerschaft mit SFS intec war eine gute Wahl, sagt Sourkes. „Als weltweit führender Anbieter von Systemanhängen macht SFS immer etwas wirklich Interessantes. Sie sind sehr innovativ und bereit, in neue Technologien zu investieren“, stellt er fest. SFS intec unterhalte auch eine enge Beziehung zu seinen Flugzeugkunden, fügt er hinzu, und sie verfügen über die Fähigkeit, Qualifizierungsprozesse durchzuführen – der Schlüssel zur Einführung einer neu gestalteten Komponente in der Luft- und Raumfahrtindustrie.
Die Flugzeuglagerbehälterhalterung, speziell als „B-Halterung“ bezeichnet, wurde als erste Befestigungskomponente für die Neukonstruktion von Verbundwerkstoffen ausgewählt, da sie repräsentativ für Komponenten ist, deren Konstruktion und Herstellung schwierig sind. Nach kollaborativer Konstruktion, Teilekonzeption und -konstruktion sowie Leistungsmodellierung mit einem Finite-Elemente-Analyse-(FEA-)Tool von Altair (Troy, Michigan, USA) iterierte das Projektteam vom ersten Artikel an, um das Modell zu validieren, zu testen und zu beweisen. Das Design for Manufacturing stand im Mittelpunkt der Entwicklung der Verbundhalterung, die die Fertigungsvorteile des automatisierten Tapelegens für die endlosfaserverstärkten Elemente und des Hochgeschwindigkeits-Spritzgießens für die geschnittenen faserverstärkten Elemente nutzt.
B-Klammern aufbauen
Ein wesentlicher Aspekt des Hybrid-Overmolding-Verfahrens ist die Verwendung unterschiedlicher Polymere derselben Klasse. PAEK dient als Matrixharz für die Endlosfaserverbundteile des Brackets, während in den umspritzten Bereichen Polyetheretherketon (PEEK) verwendet wird. VICTREX PAEK und PEEK zeichnen sich durch überlegene Ermüdungs-, Chemikalien- und Korrosionsbeständigkeit aus; ausgezeichnete Rauch-, Flammen- und Toxizitätsbeständigkeit; schnelle Verformbarkeit; und Schweißbarkeit. VICTREX AE 250, ein niedriger schmelzender PAEK (LM PAEK), bietet eine Schmelztemperatur von 40 Grad C niedriger als die von PEEK. „Wenn geschmolzenes PEEK über die Oberfläche des LM PAEK-Verbundmaterials fließt, ermöglicht die niedrigere Schmelztemperatur eine starke Anhaftung“, erklärt Sourkes.
Spezifische Rohstoffe für die B-Halterung sind VICTREX AE 250 unidirektionales kohlefaserverstärktes PAEK-Band (58% Kohlefaser) in einer Breite von zwei Zoll; und kurzes kohlenstofffasergefülltes VICTREX PEEK 150CA30 (30% Kohlefaser). Diese Materialien speisen die Produktionszellen der Hybrid-Umspritzung, die die Halterungen durch den folgenden mehrstufigen Prozess herstellen.
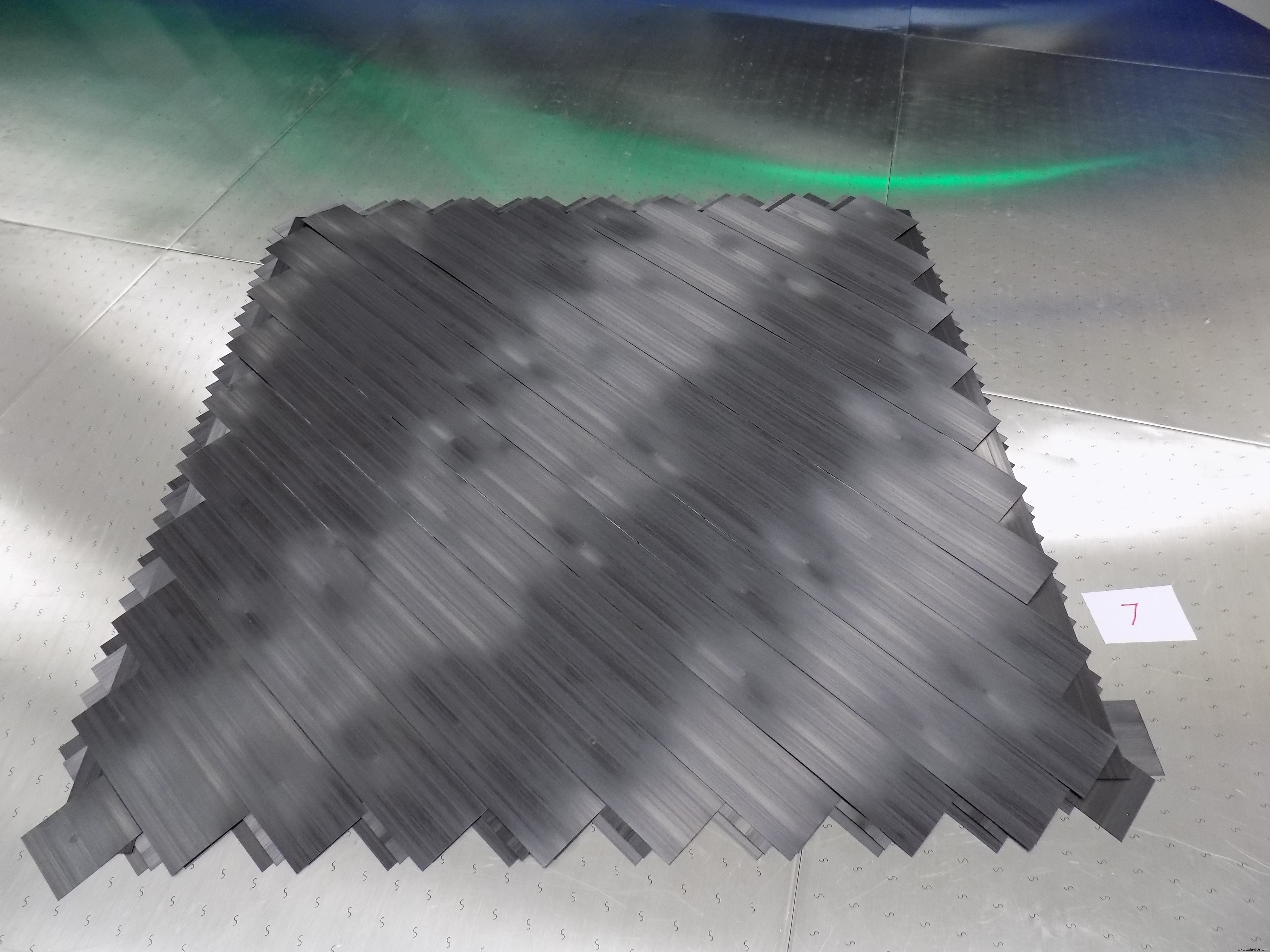
Schritt 1. Eine automatisierte Tapelegeanlage Dieffenbacher Fiberforge 2000 produziert Tailored Laminat Blanks.
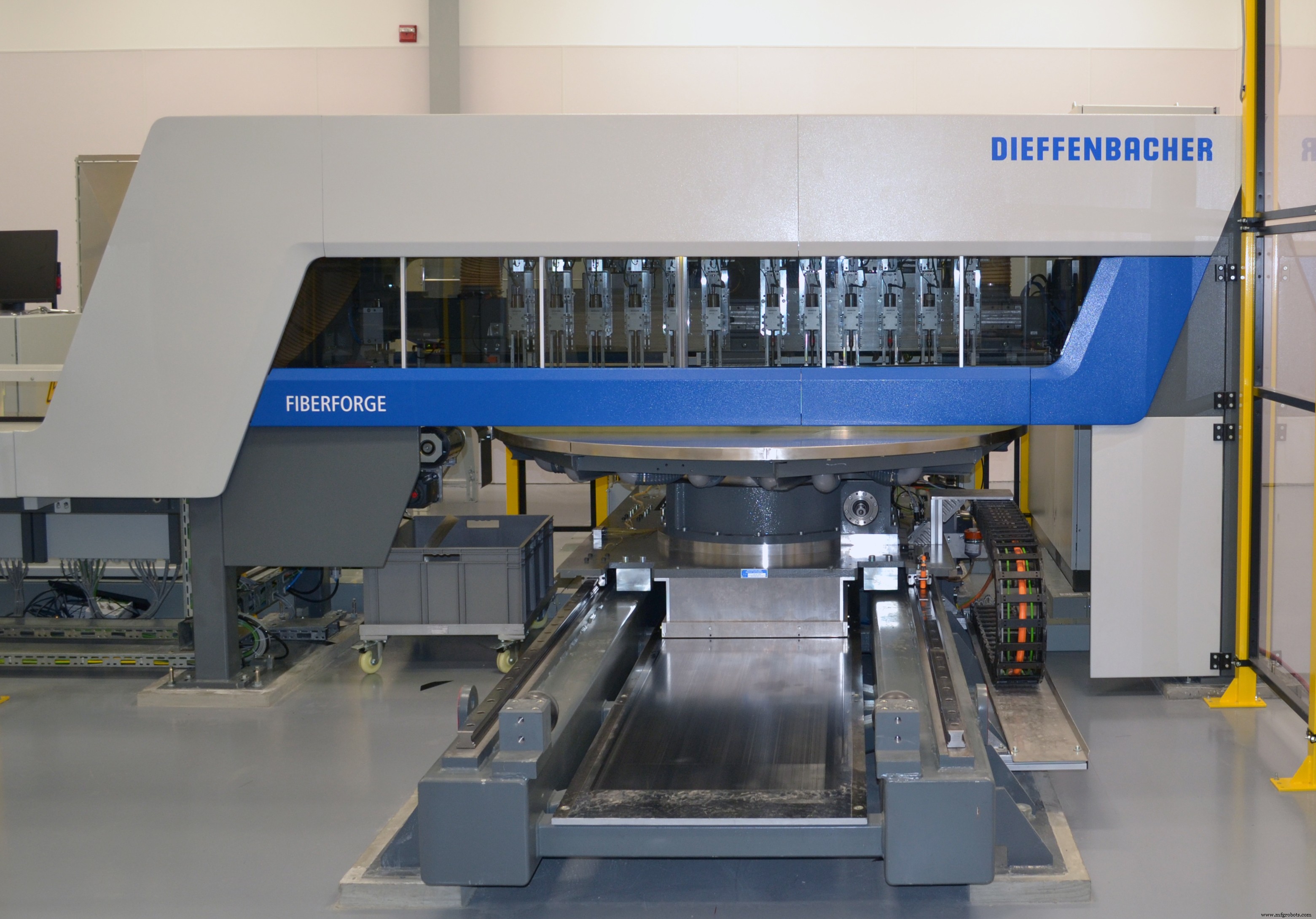
Zunächst werden die Kohlefaser/PAEK-Bänder mit einem Dieffenbacher (Eppingen, Deutschland) Fiberforge 2000 Tapelegesystem zu einem Tailored Blank abgelegt. „Diese Maschine ist derzeit eine der schnellsten Tapelegesysteme der Welt“, bescheinigt Sourkes. Es ist mit Robotern zum Laden und Nachladen von Bandspulen ausgestattet, damit es unterbrechungsfrei laufen kann und die manuelle Berührungszeit minimiert wird. Layup ist so konzipiert, dass Lücken zwischen den Bändern minimiert werden. Jede Lage des B-Bracket-Tailored Blanks wird geprüft, bevor die nächste Lage abgelegt wird. Der Prozess wird in einem umweltkontrollierten Bereich durchgeführt, um das Potenzial für Fremdkörper und Schmutz (FOD) zu minimieren.
Die Tailored Blanks werden dann in einer automatisierten, maßgeschneiderten Zelle konsolidiert, die zum Be- und Entladen der Laminate nur minimale manuelle Handhabung erfordert. In der Zelle pressen aufeinander abgestimmte beheizte Platten eine Platte pressverfestigend, wodurch Hohlräume eliminiert werden. Abgestimmte Kühlplatten kühlen dann die Platte. Die beiden auf Temperatur gehaltenen Plattensätze sind viel effizienter als eine statische Presse mit einem Plattensatz. „Das Ergebnis ist eine drastisch reduzierte Zykluszeit, gemessen in Minuten gegenüber Stunden“, sagt Sourkes.
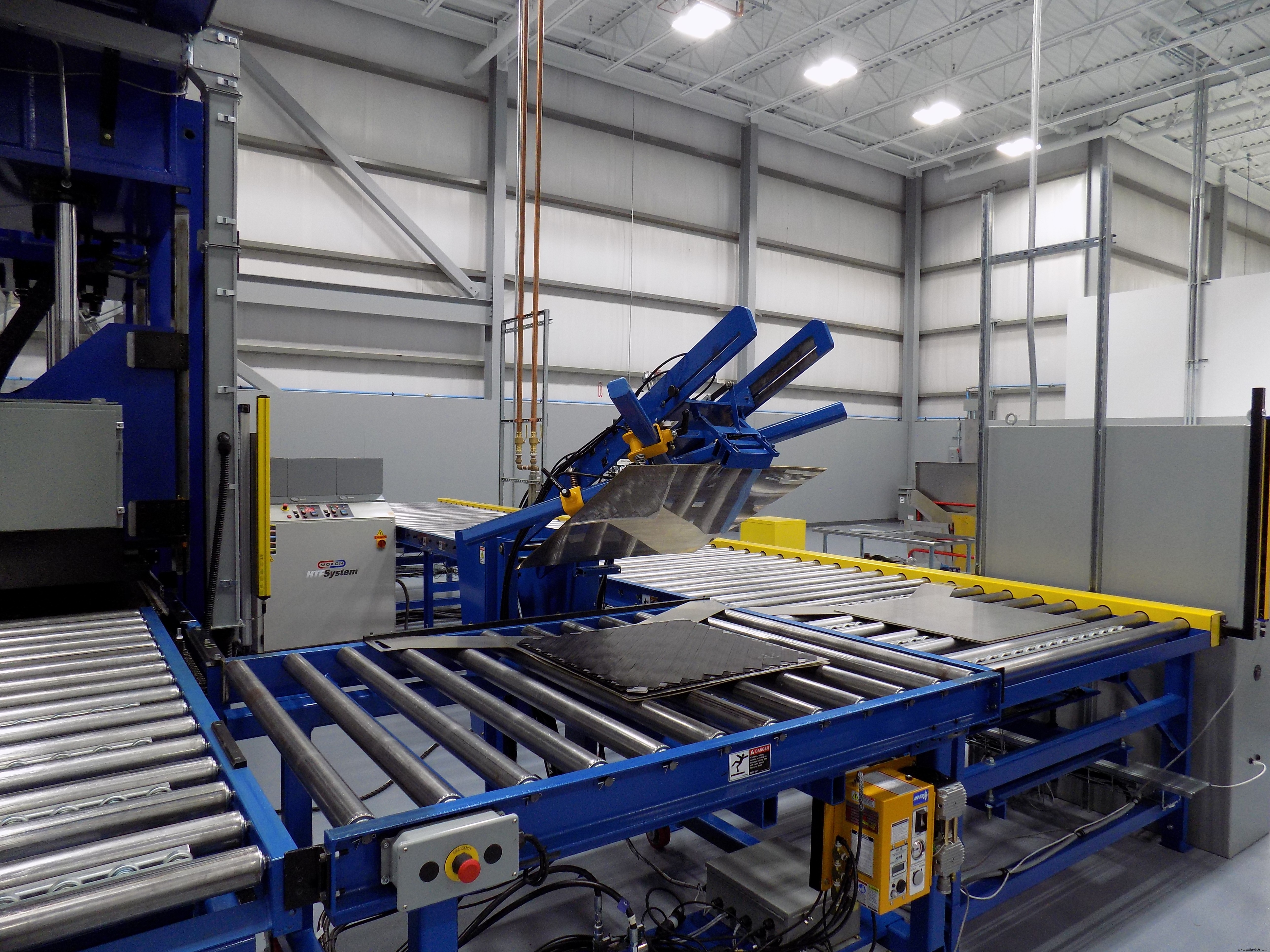
Schritt 2. Maßgeschneiderte Zuschnitte werden in einer automatisierten, maßgeschneiderten Konsolidierungszelle konsolidiert, die über zwei Plattensätze verfügt, die auf Temperatur gehalten werden (einer heiß, einer kalt), um diesen Schritt zu beschleunigen.
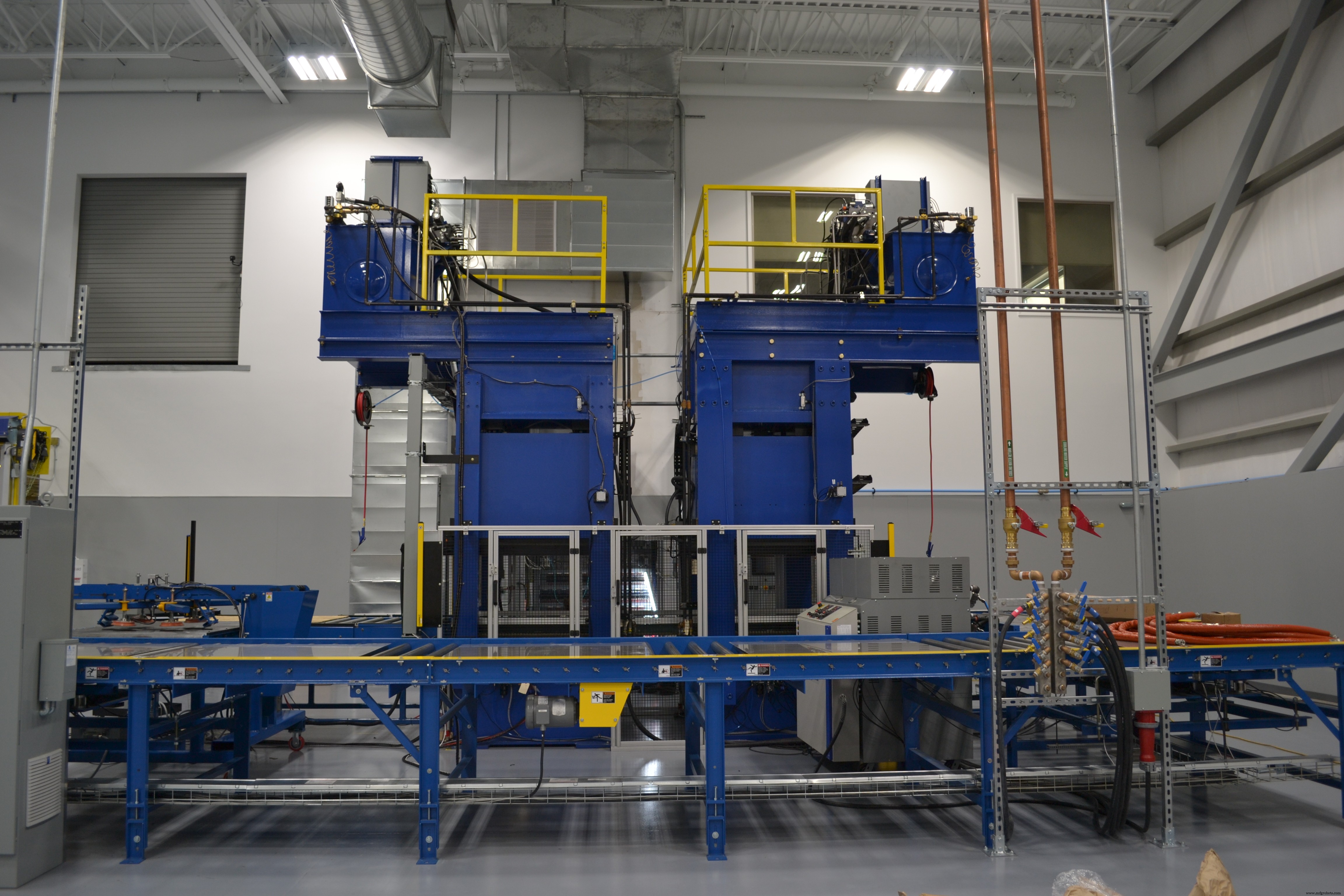
Die konsolidierten Laminatvorformlinge werden dann in einer proprietären Arbeitszelle weiterverarbeitet, um die Primärform des Brackets zu bilden (Schritt 3). Die endgültigen Kohlefaser/PAEK-Einsätze werden dann mit einem Wasserstrahlschneider von Flow International (Kent, Washington, USA) aus den geformten Rohlingen geschnitten (Schritt 4)
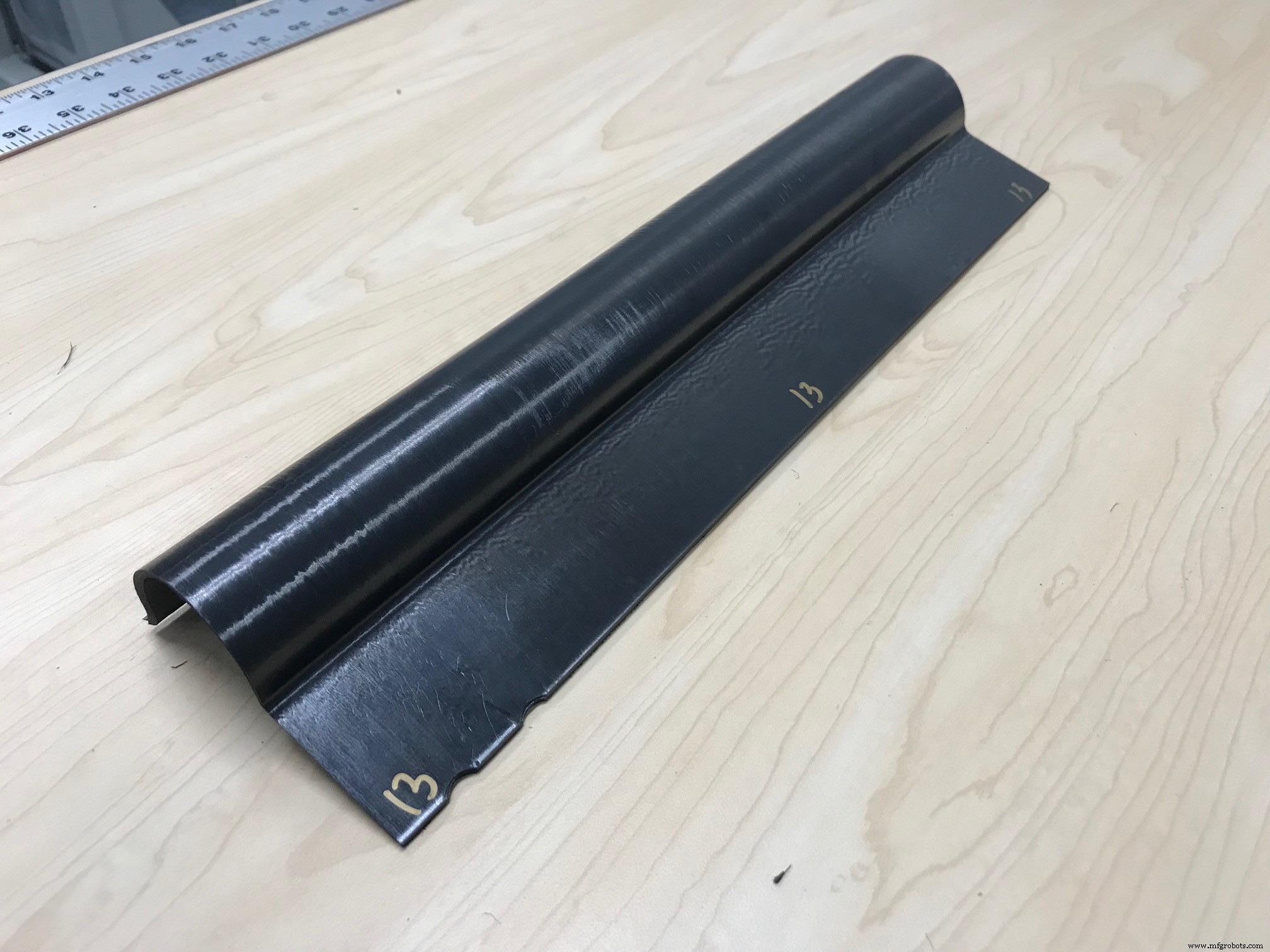
Schritt 3. Eine proprietäre Arbeitszelle bildet die Hauptform der Halterung.
Bei der Bestimmung der Größe des Tailored Blanks weist Sourkes darauf hin, dass für jedes Projekt ein Kompromiss bedacht werden muss. „Wir können das Laminat so dimensionieren, dass wir drei oder vier Rechtecke aus einem einzigen quadratischen Zuschnitt herausziehen können. Indem Sie einen so großen Zuschnitt wie möglich auflegen und ihn dann in Preforms schneiden, maximieren Sie das Buy-to-Fly-Verhältnis; Aber das Schneiden der Preforms bedeutet mehr Zeit für Wasserstrahlschneidvorgänge.“ Beim B-Bracket-Projekt wird jedes konsolidierte Laminat in mehrere Vorformlinge geschnitten
Als nächstes folgt der Überformungsschritt, der mit einer Hochtemperatur-Spritzgießmaschine von Engel (Schwertberg, Österreich) durchgeführt wird (Schritt 5). Die Einsätze werden in eine Spritzgusskavität eingelegt, die dann mit geschmolzenem PEEK gefüllt wird. Die Einsätze werden in eine Spritzgusskavität eingelegt, die mit geschmolzenem PEEK gefüllt ist, das die oberste Schicht der VICTREX AE 250-Laminate zu einem starken schmelzgebundenen Bauteil schmilzt.
Bei Bedarf wird ein Bauteil durch spanende Bearbeitung auf Endkontur fertigbearbeitet. „Obwohl es unser Ziel ist, endkonturnahe Teile zu formen“, gibt Sourkes zu, „ist oft ein minimaler Bearbeitungsgrad im Nachhinein erforderlich, um die Prozessgeometrie zu bereinigen.“ Die Bearbeitung kann mit Wasserstrahl oder CNC-Bearbeitung erfolgen.
Wegweisende Ergebnisse
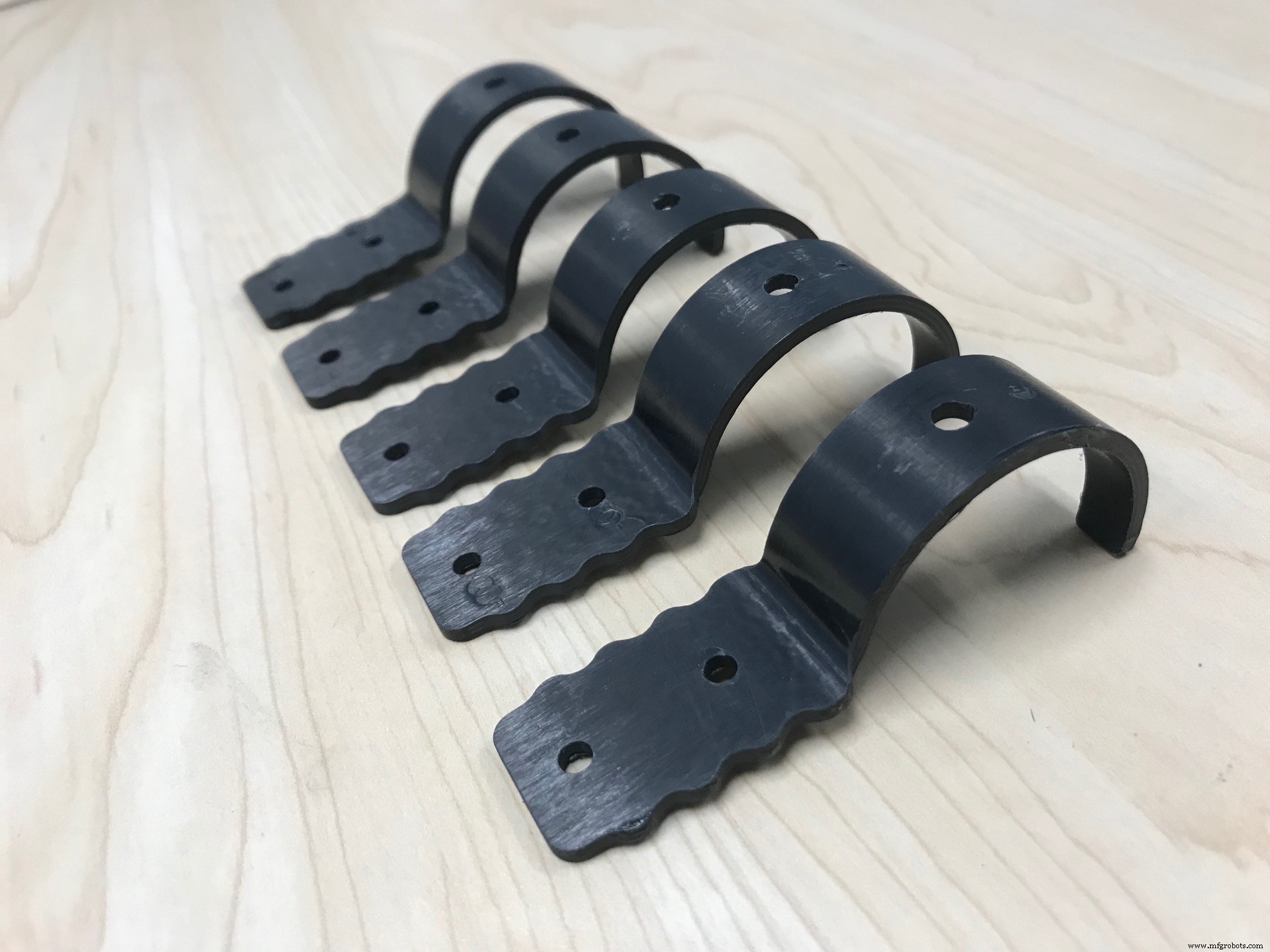
Schritt 4. Ein Wasserstrahlschneider von Flow International schneidet die Kohlefaser/PAEK-Einsätze aus den geformten Rohlingen. In jeder Halterung werden zwei dieser Einsätze verwendet.
Bei der Herstellung der SFS intec Halterung erreicht das TxV Hybrid Overmolding Verfahren Zykluszeiten von drei Minuten und ein Buy-to-Fly-Verhältnis von 1,06:1. „Es ist der effiziente Materialeinsatz und der schnelle Herstellungsprozess, der es uns ermöglicht, wertschöpfende thermoplastische Verbundteile herzustellen und die Systemkosteneinsparungen gegenüber den etablierten Metallkonstruktionen ermöglicht“, betont Sourkes. „Wir ersetzen effektiv einen kostengünstigeren Rohstoff mit einem hohen Buy-to-Fly-Verhältnis und einer erheblichen Bearbeitungszeit durch eine hochtechnisierte Materiallösung.“ Das Ergebnis sind Gewichtseinsparungen im Bereich von 30 bis 40 % und Kosteneinsparungen im Bereich von 20 bis 30 % bei einem ähnlichen Austausch, dh einem Ersatzteil, das den gleichen geometrischen und betrieblichen Spezifikationen wie das vorhandene Bauteil entspricht. „Insbesondere die Gewichtseinsparungen können bis zu 60 % betragen, wenn wir die Möglichkeit haben, ein Teilesystem komplett neu zu gestalten“, bemerkt er.
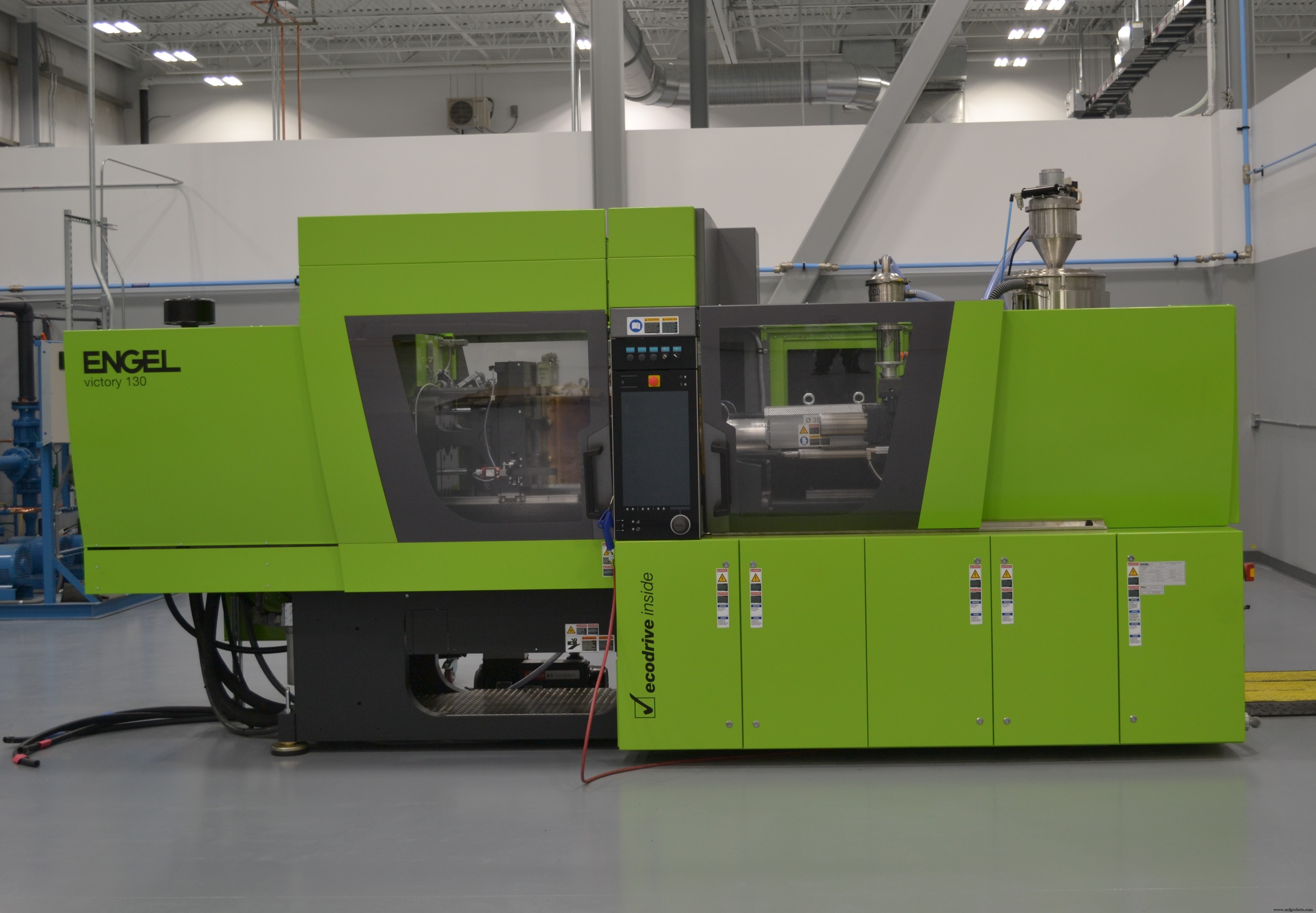
Schritt 5. Eine für das PEEK-Hybrid-Overmolding optimierte Engel-Spritzgießmaschine vervollständigt das Verbundteil durch Umspritzen der Einsätze.
Die Kohlefaser/PAEK/PEEK-Halterung hat auch die Anzahl der Teile konsolidiert:TxV und SFS vereinbarten, eine Spreiznase auf die Unterseite des Teils im gleichen Arbeitsgang zu spritzen, der auch für die Funktionalisierung und das Hinzufügen anderer Funktionen verwendet wurde. Früher wurde die Spreiznase aus PEEK gefertigt und dann von zwei Nieten gehalten. Somit führt die Konsolidierung sowohl zu einer reduzierten Teileanzahl als auch zur Eliminierung eines Montageschrittes.
Die Expertise der beiden Unternehmen, die TxV auf den Markt gebracht haben, hat zweifellos den Erfolg des Hybrid-Overmolding ermöglicht. Sourkes erklärt, dass Victrex nach der Entwicklung des PAEK-Materials und der Verarbeitungstechnologie zunächst mit bestehenden Geschäftspartnern nach Möglichkeiten suchte. „Allerdings verfügten Unternehmen mit Spritzguss-Know-how nicht über das Know-how, um mit endlosfaserverstärkten Verbundwerkstoffen zu arbeiten und umgekehrt.“ Victrex und Tri-Mack arbeiteten mehrere Jahre lang zusammen, bevor sie TxV im Jahr 2017 gründeten und das speziell gebaute Kompetenzzentrum für Polyketon-Verbundwerkstoffe des Unternehmens bauten, das hochautomatisiert und für die Hochgeschwindigkeitsserienproduktion ausgelegt ist.
Auf die Frage, den TxV-Prozess und die Ergebnisse mit einem herkömmlichen Herstellungsansatz zu vergleichen, stellt Sourkes fest, dass das B-Bracket für Standard-Verbundwerkstoff-Herstellungsverfahren nicht geeignet ist. „Dies wäre eine große Herausforderung, ohne die Halterung aus einem Verbundwerkstoffblock zu bearbeiten – was zu teuer wäre“, sagt er.
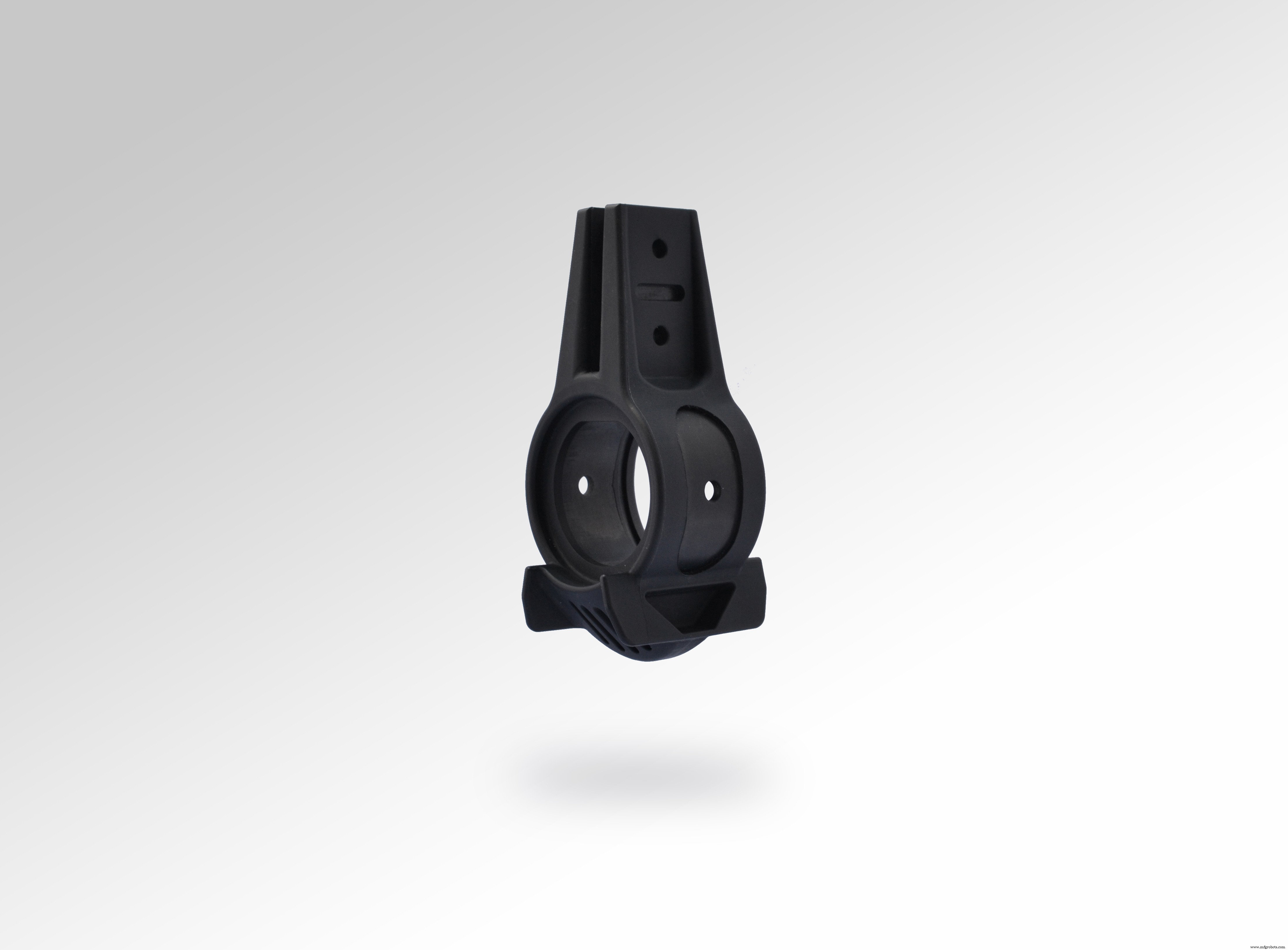
Schritt 6. Die endgültige B-Halterung wird mit einer Zykluszeit von drei Minuten, einem Buy-to-Fly-Verhältnis von 1,06:1 und einer Gewichtseinsparung von 30 bis 40 % produziert.
Qualifizieren und dann fliegen
Die beiden Unternehmen nutzen die Fähigkeit von SFS intec, Qualifizierungen durchzuführen, und haben die Zertifizierung durch „Point Design“ durchgeführt, was bedeutet, dass nur diese spezielle Teilegeometrie die Flugzulassung erhält. Die Teile wurden hergestellt und den im Qualifizierungsdokument aufgeführten Prüfungen unterzogen. „Da es sich bei dem Teil um eine Halterung für einen Überkopfbehälter handelt, werden die Betriebslasten relativ leicht erreicht“, bemerkt Sourkes. „Die Leistungsanforderungen gehen jedoch über diese typischen Belastungen hinaus und müssen einige extreme Start- und Landemanöver abdecken.“ Als CW bei Drucklegung ist das Qualifizierungspaket eingereicht und wartet auf die endgültige Freigabe durch den Spezifikationsverwalter. TxV und SFS intec gehen davon aus, dass das Teil Anfang 2020 fliegen wird.
Sobald die B-Klasse qualifiziert ist, wird TxV auf die Produktionsmengen skalieren. Während das Unternehmen seine bestehende Hybrid-Umspritzungslinie verwendet, um diese Halterungen herzustellen, betont Sourkes, dass das Unternehmen einen doppelten Auftrag hat – sowohl Teile mit der Technologie herzustellen als auch Industriehersteller zu unterstützen, die daran interessiert sind, die Technologie selbst zu übernehmen. Mit anderen Worten, Hersteller von Verbundwerkstoffen können diese Fertigungstechnik in ihren eigenen Einrichtungen anwenden.
Verbundbrackets wie das Produkt von SFS intec haben das Potenzial, einen relativ großen Markt für diese Art von Komponenten zu erobern. Verkehrsflugzeuge verwenden Tausende von Halterungen und Systembefestigungen, die einen erheblichen Kosten- und Gewichtsbeitrag zum Gesamtflugzeug ausmachen. „Wir sind überzeugt, dass thermoplastische Verbundbauteile im Flugzeugbau eine immer größere Rolle spielen werden“, erwartet Costabel.
Faser
- MMF #5:Ein Leitfaden zum Einbetten von Komponenten in 3D-gedruckte Teile
- Eine revolutionäre neue Methode zur Herstellung von Metallteilen
- Wir stellen unser neues Markforged-Material vor:Onyx
- AT&T, Tech Mahindra arbeiten an einer neuen Open-Source-KI-Plattform zusammen
- LANXESS nimmt zwei neue Produktionslinien für thermoplastische Verbundwerkstoffe von Tepex in Betrieb
- Beschleunigung thermoplastischer Verbundwerkstoffe in der Luft- und Raumfahrt
- Nèos International gründet neues Hauptquartier für Verbundwerkstoffe in Großbritannien
- So fertigen Sie feinmechanische Komponenten
- Hochpräzisionskomponenten verstehen
- Endbearbeitung von Teilen und Komponenten