Fraunhofer IPT entwickelt thermoplastische Verbundwerkstoffe zur Wasserstoffspeicherung, Triebwerksschaufeln und mehr
Die Entwicklung des Fraunhofer IPT umfasst (im Uhrzeigersinn von oben links) thermoplastische Verbundstoff-Flugzeugtriebwerksschaufeln, hybride Metallverbundstrukturen mittels Laserstrukturierung und AFP, Structural Health Monitoring (SHM) von Verbundwerkstoffen und thermoplastische Verbundbandverarbeitungssysteme, wie die PrePro 2D- und PrePro3D-Systeme von Conbility vertrieben. Bildnachweis:Fraunhofer IPT
Im Dezember 2020 habe ich einen Artikel darüber veröffentlicht, wie das Fraunhofer-Institut für Produktionstechnologie (IPT, Aachen, Deutschland) vollautomatisiertes Tapelegen und -formen für thermoplastische kohlenstofffaserverstärkte Polymere (CFK) von Triebwerksfanschaufeln entwickelt. Es stellt sich heraus, dass die In-situ-Konsolidierung (ISC) von thermoplastischen Verbundbändern ein Thema ist, das das Fraunhofer IPT gut kennt, da es diese Technologie zu Beginn gemeinsam mit den ISC-Pionieren Accudyne Systems Inc. (Newark, Del., USA) und Automated . vorangetrieben hat Dynamics, jetzt Trelleborg Sealing Solutions Albany (TSS Albany, Niksayuna, NY, USA). [Weitere Informationen zu diesen ISC-Pionieren finden Sie in „Consolidating Thermoplast aerostructures in place, Part 1 and Part 2“.] „Das IPT ist seit 1988 im Laser-Assisted Tape Winding (LATW) aktiv und bleibt eines unserer Hauptthemen “, erklärt Dr. Henning Janssen, Oberingenieur und Abteilungsleiter für Faserverbundkunststoffe und Lasersystemtechnik am Fraunhofer IPT. Er stellt fest, dass sich die LATW-Technologie stark verändert hat, insbesondere in den letzten 10-15 Jahren. In diesem Blog erfahren Sie mehr über die Entwicklung von LATW und thermoplastischen Verbundwerkstoffen am Fraunhofer IPT sowie die zukünftige Technologieentwicklung des Instituts.
Evolution beim Laserbandwickeln
„Als wir vor 30 Jahren anfingen, war die Lasertechnologie noch nicht reif für die Hochgeschwindigkeitsbearbeitung von thermoplastischen Verbundwerkstoffen“, sagt Janssen. „Man kann sich vorstellen, dass man vor allem auf der Steuerungsseite nur eine analoge Kamera hatte. Jetzt haben wir eine viel bessere Technologie. Als wir beispielsweise 2008 einen kompakten Laserwickelkopf entwickelten, der zur Gründung von AFPT Deutschland (Dörth, Deutschland) führte, mussten wir eine 16-Pixel x 16-Pixel-Kamera verwenden, die eine Bildrate von nur acht . bot Bilder pro Sekunde. Jetzt haben wir problemlos 640 x 480 Pixel und eine Verarbeitung von 50 Bildern oder mehr pro Sekunde.“ Er erklärt, dass dies wichtig sei, „denn bei der von uns entwickelten Laserbandwicklung besteht einer der Hauptvorteile darin, dass man einsehen den Prozess und ändern auch die Rechenleistung innerhalb von Millisekunden. Das verschafft Ihnen beispielsweise einen guten Vorteil, wenn Sie komplexe Geometrien, wie die Kuppel von Druckbehältern, umfahren, wo sich die Wickelgeschwindigkeit verlangsamt und Sie die Laserheizleistung senken müssen. Sie müssen dann nachjustieren, wenn die Wicklung entlang des Tankzylinders wieder an Geschwindigkeit gewinnt. Dies war vor 15 Jahren nicht möglich, weil die Laser-, Steuerungs- und Wärmebildtechnologien noch nicht fertig waren oder zu teuer und auch nicht so leistungsstark waren wie heute.
Janssen fährt fort:„Es hat sich also viel auf der digitalen Seite entwickelt. Jetzt liefern wir beispielsweise so etwas wie einen digitalen Zwilling, mit dem Sie alle Ihre Sensorinformationen auf den Druckbehälter abbilden können, sodass Sie das hergestellte Teil mit dem digitalen Design vergleichen können, um die Teilequalität zu beurteilen und die Leistung vorherzusagen. Der Einsatz virtueller Prozesssensoren und -modelle ermöglicht es uns auch, die Laminatfestigkeit gemäß seiner Verarbeitungshistorie vorherzusagen.“ Dies ist wichtig, da LATW, das thermoplastisches Klebeband verwendet, schnelles Aufheizen und Abkühlen verwendet, wobei die Material- und Teileigenschaften aufgrund des Fehlens eines thermischen Nachbearbeitungsschritts während des Wickelprozesses selbst bestimmt werden, bemerkt er. Daher ist die Fähigkeit zur schnellen Prozesskontrolle von entscheidender Bedeutung.
Auch bei den Materialien habe es Entwicklungen gegeben, sagt Janssen. „Vor zwanzig Jahren gab es nur eine begrenzte Menge an thermoplastischen Verbundbandmaterialien wie APC-2 von Cytec, heute Solvay (Alpharetta, Georgia, USA)“, erklärt er. „Aber jetzt sind viele weitere Materialien für industrielle Anwendungen qualifiziert, und es gibt auch viele Standardmaterialien wie Polypropylen (PP), das mit Kohlefaser und auch mit Glasfasern verstärkt ist, sowie zum Beispiel Polyamid sechs (PA6), das“ wird häufig in der Automobilindustrie verwendet. Inzwischen gibt es auch Anwendungen für LATW, die eher in Richtung Massenproduktion gehen. Zum Beispiel gibt es einen Schub in Richtung Haltehülsen und andere Teile in Elektromotoren. Dies sind einfache thermoplastische Verbundringe oder -rohre, jedoch in Mengen von 10.000 bis 50.000 pro Jahr.“
ambliFIBRE, Rohre für Öl und Gas
Ein Teil der digitalen Steuerung in LATW, die Janssen oben beschrieben hat, wurde im ambliFIBRE-Projekt (2015-2018) entwickelt. „An diesem Projekt waren viele Partner beteiligt“, sagt er, „aber einer war Baker Hughes (Newcastle, England und Houston, Texas, USA) und wir verwendeten unsere LATW-Ausrüstung für ihre nichtmetallischen Rohre.“ Beachten Sie, dass Baker Hughes kurz nach dem Ende von ambliFIBRE im Jahr 2018 sein Joint Venture mit Saudi Aramco (Riad, Saudi-Arabien) ankündigte, um die Verwendung nichtmetallischer Rohre, einschließlich der möglichen Verwendung von kohlenstofffaserverstärktem Kunststoff (CFK), auszuweiten.
Baker Hughes strebt nun an, die Einführung nichtmetallischer Materialien im Energiesektor zu beschleunigen, und es gibt auch andere Unternehmen, die laserbasierte Technologien für Rohre verwenden, wie beispielsweise Magma (Portsmouth, Großbritannien). (Siehe „Thermoplastische Rohre auf dem Vormarsch in der Tiefsee“ und „Magma Global liefert Hochdruck-Verbundrohrleitungen…).
„Auch für Steigleitungen und Flowlines aus thermoplastischen Verbundwerkstoffen ist es üblich, das Laserbandwickeln auch zu verwenden“, sagt Janssen. „Obwohl das in anderen Branchen noch nicht allgemein bekannt ist.“ Er fügt hinzu, dass LATW in letzter Zeit viel Aufmerksamkeit auf Wasserstoffspeichertanks gerichtet habe, aber die Technologie habe bereits eine viel breitere Anwendung.
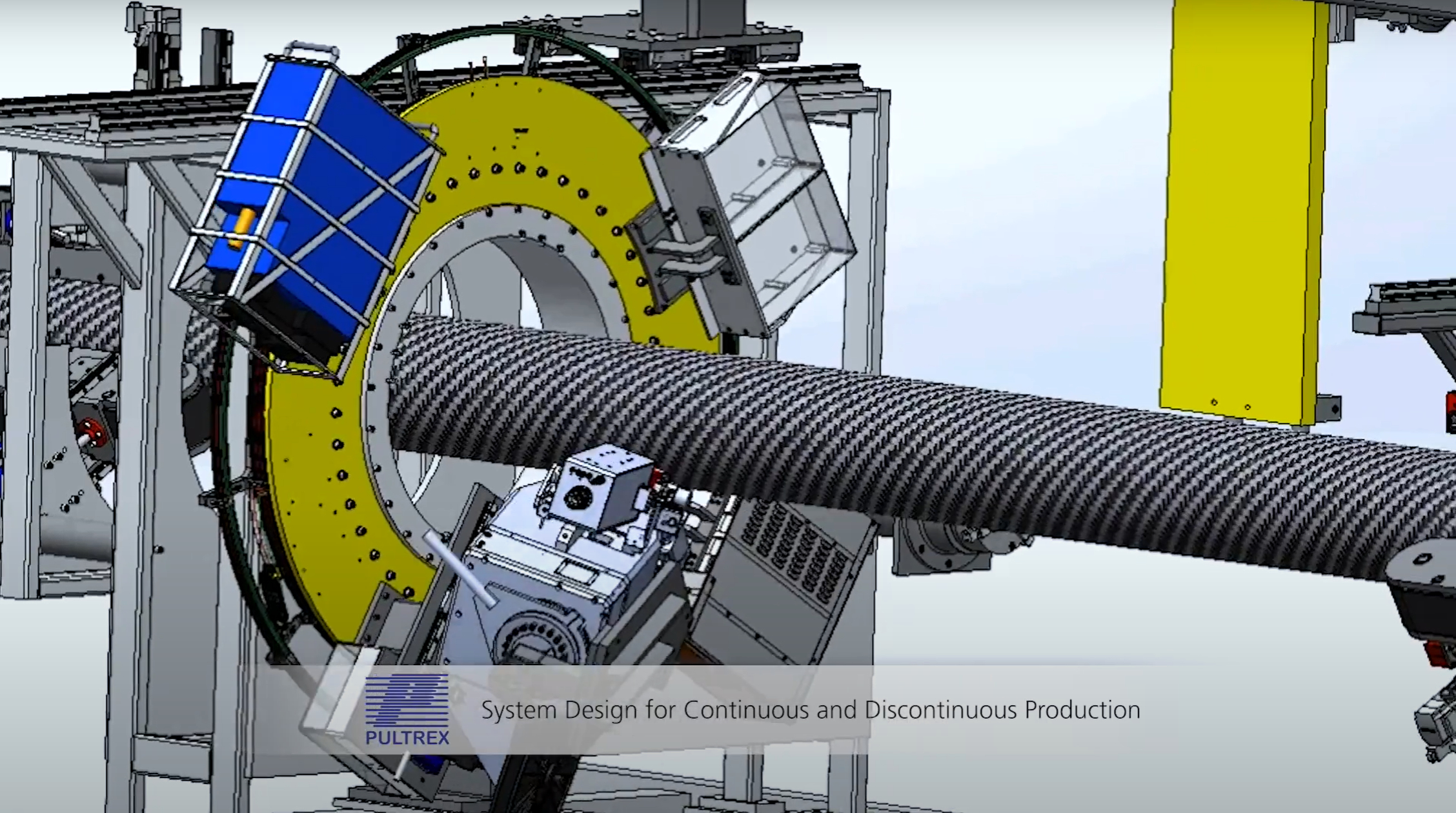
Im Projekt ambliFIBRE hat das Fraunhofer IPT digitale Prozessleitmodelle für das diskontinuierliche (z. B. Tanks) und kontinuierliche Bandwickeln entwickelt, um beispielsweise mehrere Kilometer lange Rohre herzustellen. Bildnachweis:Fraunhofer IPT-Video zum ambliFIBRE-Projekt
„Und was wir vom Fraunhofer IPT für diese Anwendungen anbieten, ist entscheidend“, sagt Janssen. „Natürlich betreiben wir hier in unserem Institut keine komplette Produktionslinie für die kontinuierliche Rohrfertigung, aber wir bieten unseren Kunden Materialprüfung und Produktqualifizierung an. Da ist zum Beispiel die Testpyramide auf Basis der DNV-GL F114, beginnend mit der Qualifizierung und Prüfung des Polymers und der Fasern, über die Skalierung bis hin zur Mikrostruktur bzw. Mesostruktur des Verbundlaminats. Daher führen wir viele Tests auf Coupon-Ebene durch und skalieren dann beispielsweise auf kleinere Rohre und repräsentative Rohre, da das Wickeln Ihnen andere Eigenschaften bietet als das Pressen oder automatisierte Tapelegen (ATL).“
Außerdem merkt er an:„Weil Sie unterschiedliche Spannungen in Ihrem Material haben, werden viele dieser Verbundmaterialien in kleineren Rohren getestet, zum Beispiel 2-3 Zoll bis zu mehreren Metern Länge. Also führen wir diese Prüfung durch und wenden dann unser Prozessverständnis für die reale Teilelänge an, zum Beispiel 2-3 Kilometer. Und das ist sehr interessant, da die Verarbeitungszeit bei dieser Länge einige Tage betragen kann und Sie die Schrumpfung sowie andere Faktoren berücksichtigen müssen, wie z. B. Änderungen der Umgebungslufttemperatur, die sich ziemlich auswirken können.“
LATW in Wasserstoffspeichertanks
Janssen sagt, das Fraunhofer IPT arbeite seit 2000 mit Öl- und Gasunternehmen zusammen. „Und dann haben wir vor acht Jahren herausgefunden, dass dies fast dieselbe Technologie ist, die man für Wasserstofftanks braucht“, erinnert er sich. „Und jetzt haben wir hier am IPT eine große Initiative für die Wasserstoffherstellung und auch für Kohlefaserverbundwerkstoffe in Brennstoffzellen. Wir bauen eine 80-Millionen-Euro-Anlage für die automatisierte Brennstoffzellen-Fertigung auf und investieren außerdem in eine neue, recht große Wickelanlage, um Teile bis zu 7 Meter Länge und 2,5 Meter Durchmesser produzieren zu können, die wir auch nutzen werden für große Druckbehälter.“
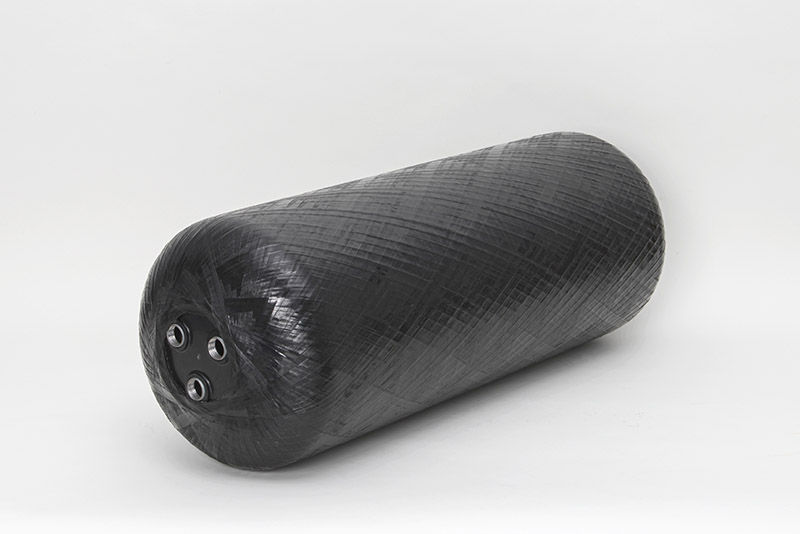
LATW mit thermoplastischen Verbundbändern sei für die Druckbehälterfertigung noch nicht State-of-the-Art, sagt Janssen, „weil die Chemie der Thermoplaste sowie deren Verarbeitung und Haltbarkeit noch erforscht werden. Wir sind jedoch der festen Überzeugung, dass die geringe Durchlässigkeit, Zähigkeit und Recyclingfähigkeit von Thermoplasten wichtig ist.“ Potenzial für Thermoplaste sieht er auch in Druckbehältern des Typs V, die komplett aus Verbundwerkstoff bestehen, aber keinen separaten Thermoplast-Liner verwenden. „Diese könnten eine zukünftige Lösung für einige mobile Wasserstoffspeicheranwendungen wie Brennstoffzellen-Elektro-Lkw darstellen.“
„Wir sehen auch, dass herkömmliche Duroplaste Filament Winding ist hinsichtlich minimaler Wickelwinkel limitiert“, sagt Janssen. „Man muss zum Beispiel die Kuppeln in spiralförmigen Schichten mit nicht viel weniger als 10° Faserwinkel umfahren. Sie können also keine 0°-Verstärkung in einen herkömmlichen Tank mit Filamentwicklung einbauen.“ Er sagt jedoch:„Im klassischen LATW wird das eingehende thermoplastische Prepreg direkt mit dem Substrat verschweißt, sodass Sie in jede gewünschte Richtung gehen können, was Ihnen viel mehr Gestaltungsfreiheit bietet. Derzeit führen wir Projekte mit Partnern aus der Automobilindustrie durch, um thermoplastische Druckbehälter für die Wasserstoffspeicherung zu entwickeln, die sicher, energieeffizient und leicht zu recyceln sind.“
Lüfterblätter aus thermoplastischem Verbundmaterial
Das Fraunhofer IPT hat einen sehr starken Hintergrund im Turbomaschinenbau, sagt Janssen. „Wir haben hier in Aachen die International Center for Turbomachinery Manufacturing (ICTM) eine vorwettbewerbliche Gemeinschaft, in der wir mit den Motorenherstellern und deren Zulieferern gemeinsam in vorwettbewerblichen F&E-Projekten zusammenarbeiten, um Fertigungstechnologien zu entwickeln und zu verbessern.“
Er stellt fest, dass der Fokus in den letzten 20 Jahren hauptsächlich auf der Bearbeitung von Titan- oder Nickelbasislegierungen für fortschrittliche Produkte des Kompressionsbereichs und von Turbinen lag, wie beispielsweise die integrierte Schaufelscheibe (Blisk). In der kalten Sektion wurden in den 1990er Jahren Teile aus Verbundwerkstoffen wie Kohlefaser-Verbundlüfterschaufeln von GE entwickelt und sind jetzt im GE90 und GEnx im Einsatz. „Heute werden Ceramic Matrix Composites (CMC) jedoch als Materialien der nächsten Generation für den heißen Abschnitt von Düsentriebwerken angesehen“, sagt Janssen, „die höhere Temperaturen bei geringerem Gewicht für mehr Effizienz ermöglichen.“
„Die Herstellung von Teilen aus Verbundwerkstoffen ist im Vergleich zu Metall ganz anders“, fährt er fort. „Bei Metall beginnt man mit einer großen Materialmenge und leitet das Teil durch subtraktive Bearbeitung, meistens spanabhebend, ab, damit die Konstruktion nicht so abhängig von der Fertigung ist. Bei Verbundwerkstoffen, die immer einen generativen Prozess erfordern, ist es genau umgekehrt. Daher haben wir uns entschieden, uns aus Sicht der Fertigung mit neuartigen Lüfterblattstrategien zu befassen.“
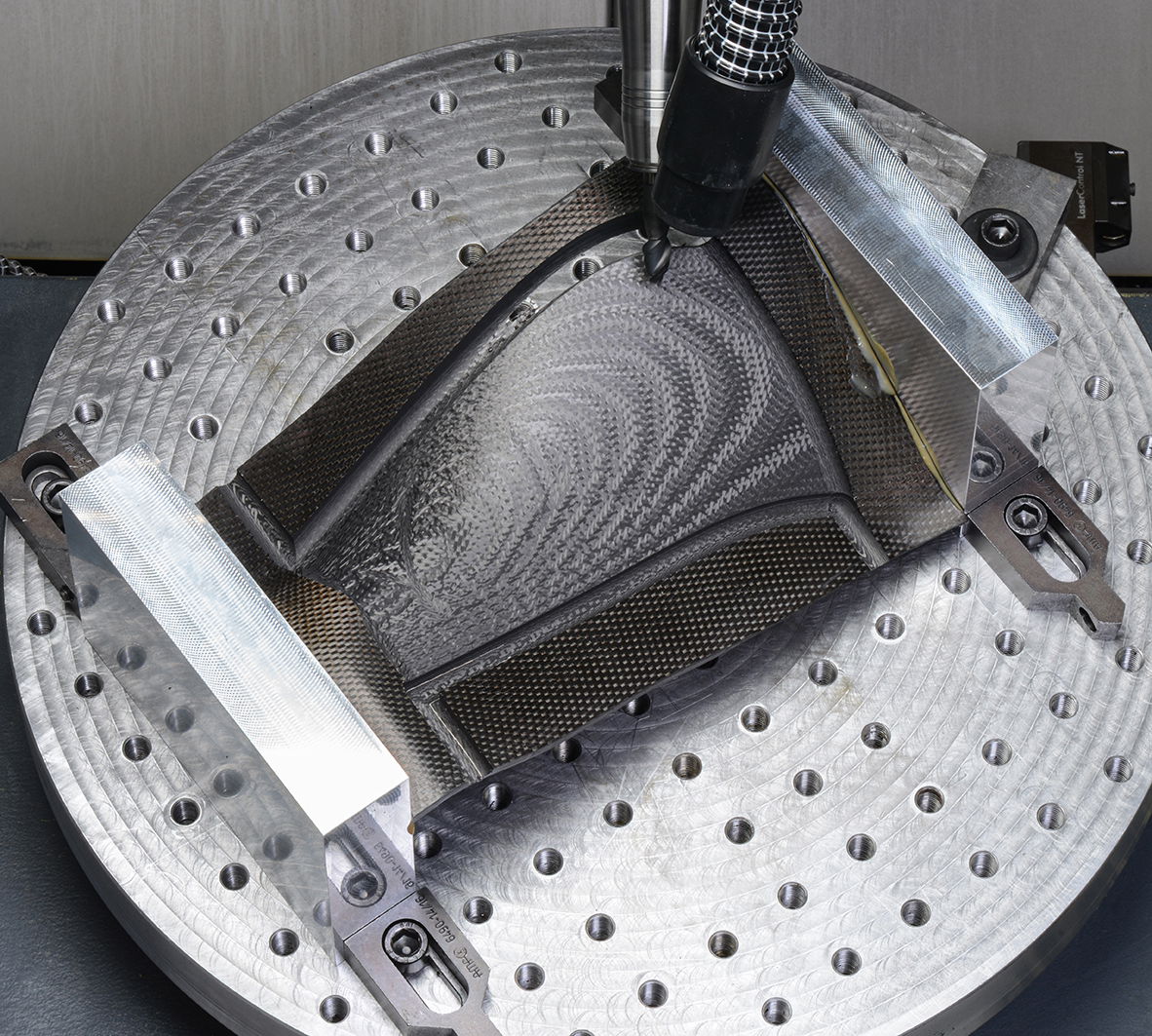
Er weist auch auf das Gemeinschaftsunternehmen Clean Sky 2 hin, bei dem Fraunhofer die Eco-Design-Aktivitäten leitet. Das Fraunhofer IPT konzentriert sich auf das Ökodesign von Motoren, das eine Ökobilanzierung und eine Bewertung der Umweltauswirkungen umfasst. „Deshalb haben wir begonnen, uns mit thermoplastischen Verbundwerkstoffen zu befassen“, erklärt er. „Bisher befinden wir uns auf einem sehr niedrigen TRL [Technologiebereitschaftsgrad]. Im Moment geht es bei der Entwicklung darum, verschiedene Prozessrouten herzustellen und auszuprobieren, wie zum Beispiel das endkonturnahe Layup und ein wenig Thermoformen – was eher einem Kalibrierungsschritt gleicht – und dann die Endbearbeitung in Bezug auf die maschinelle Bearbeitung. Es liegt also noch eine Menge Arbeit vor uns.“
Inzwischen weitet das Fraunhofer IPT seine Expertise in der Bearbeitung von metallischen Triebwerkskomponenten auf Verbundwerkstoffe aus und nutzt seine digitale Technologie zur Überwachung und Bewertung der Bearbeitungsparameter an jeder Schaufel. Aber ist das Ziel bei Verbundwerkstoffen nicht, weg von einer solchen subtraktiven Fertigung hin zu mehr additiver Fertigung für weniger Abfall? „Ja, aber bei einigen Prozessrouten ist eine Bearbeitung erforderlich, um Maßtoleranzen einzuhalten“, sagt Janssen. „Woran wir gerade arbeiten, ist sehr nahe an der Netzform.“
Er weist darauf hin, dass das derzeit entwickelte Design ein 0,75 Zoll dickes thermoplastisches Laminat an der Wurzel und nur 2 Millimeter dick an der Spitze ist. „Und dann gibt es verschiedene Designstrategien, die wir gemeinsam mit den Konstrukteuren diskutieren. Haben Sie auch einen Autoklav oder eine Pressstufe für so hochbelastete Teile? Dies wird auch bei den inneren Spannungen eine Rolle spielen, denn wir wissen, dass sich diese Klinge während der Rotation etwas verwindet. Und natürlich ist Vogelschlag ein zentrales Thema.“ Für Letzteres sieht Janssen die erhöhte Zähigkeit von Thermoplasten als Wegbereiter und weist darauf hin, dass PPS (Polyphenylensulfid)-Verbundstoffe genau aus diesem Grund in Flügelvorderkanten verwendet werden.
Zukünftige Anwendungen für thermoplastische Verbundwerkstoffe
Ich fragte nach der Möglichkeit, thermoplastische Verbundwerkstoffe in Motorgondeln zu verwenden , die möglicherweise dazu beitragen könnte, eine Lösung für vier aktuelle Vorfälle mit Blade-Out zu bieten, bei denen, wie in einer Aviation Week vom März 2021 berichtet, Artikel:
“… Schäden durch Schaufelfragmente, die auf Teile der Triebwerksabdeckung oder der Gondel trafen, lösten eine Reihe von Ereignissen aus, die zum Bruch großer Teile der Struktur, einschließlich Teilen von Triebwerkseinlässen und Lüfterhauben, führten ein Weg." Bei allen vier Unfällen wurde der Flugzeugrumpf beschädigt, und bei Southwest Flight 1380 im April 2018 wurde eines der Fenster verschoben, wodurch ein Passagier ums Leben kam.
„Das Interesse der Industrie, thermoplastische Verbundwerkstoffe im Motorraum einzusetzen, ist groß“, sagt Janssen, „allerdings ist dies eine langfristige Entwicklung.“ Ein Thema für eine solche Entwicklung ist die Zertifizierung durch Luftfahrtbehörden, ein weiterer Bereich, in dem das Fraunhofer IPT aktiv ist. „Wir diskutieren jetzt mit Zertifizierungsstellen, wie wir den Zertifizierungsaufwand reduzieren können, indem wir digital nachweisen, dass neue Herstellungsprozesse aktuellen und sich weiterentwickelnden Standards entsprechen. Das ist also eine neue Denkweise. In der Fertigung des 21. Jahrhunderts stehen so viele Daten zur Verfügung, dass es nicht nur darum geht, einen Prozess oder ein Design durch Tests zu zertifizieren, und das wird dann eingefroren.“ Mit anderen Worten, der Schwerpunkt von Industrie 4.0 und Composites 4.0 liegt heute darin, dass Sensoren und KI-fähige Software kontinuierlich Daten sammeln und Intelligenz entwickeln, die dann die Fertigung kontinuierlich optimiert und diese Intelligenz wiederum im digitalen Thread zurücksendet, um Designs zu verbessern. Dies unterscheidet sich in der Tat stark von der heutigen Fertigung.
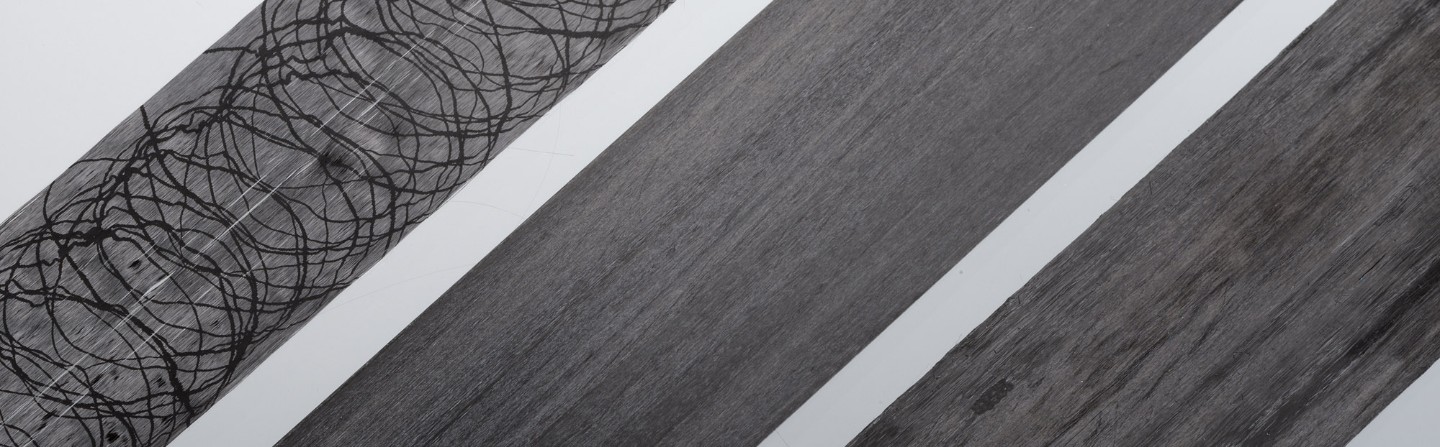
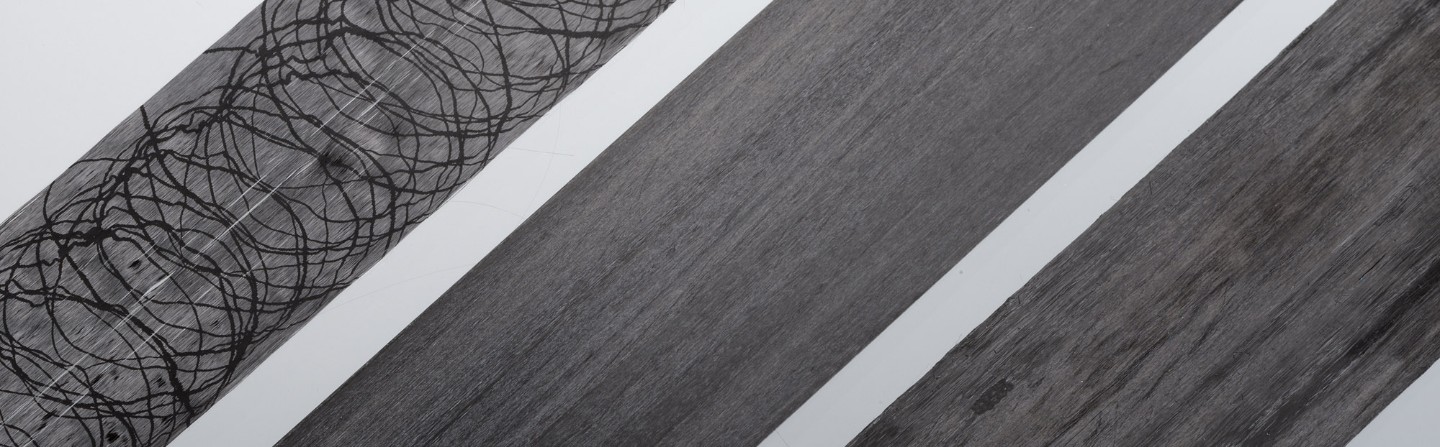
Die Arbeit des Fraunhofer IPT zur Zertifizierung, so Janssen, „könnte dazu beitragen, neue Technologien wie thermoplastische Verbundwerkstoffe für Motorenteile zu ermöglichen – wenn also alle Aspekte, einschließlich Technologie, Design und Risikomanagement, berücksichtigt werden.“ Er behauptet, dass thermoplastische Verbundwerkstoffe ein enormes Potenzial bieten, um wichtige Herausforderungen in einer Vielfalt zu meistern der Industriezweige und stellt fest, dass das Fraunhofer IPT daran arbeitet, die Verarbeitungskomplexität thermoplastischer Verbundwerkstoffe zu überwinden – beispielsweise durch den Einsatz neu verfügbarer digitaler Fertigungsverfahren. „Außerdem lässt sich das Potenzial thermoplastischer Verbundwerkstoffe nur dann voll ausschöpfen, wenn der gesamte Lebenszyklus – einschließlich Wiederverwendung und Recycling – berücksichtigt wird“, sagt Janssen. „Daher arbeitet das Fraunhofer IPT auch am mechanischen Recycling von thermoplastischen Verbundwerkstoffen. Wir sehen, dass es möglich sein wird, hochwertiges Recyclingmaterial zu erzielen, indem sowohl die während der Herstellung als auch während des gesamten Lebenszyklus von Verbundbauteilen anfallenden Daten berücksichtigt werden.“
Harz
- Covestro verstärkt Investitionen in thermoplastische Verbundwerkstoffe
- Bester Lasergravierer 2021 für Messerklingen und Messergriffe
- RECONTRAS-Projekt validiert den Einsatz von Mikrowellen und Laserschweißen, um recycelbare Verbundwerkstoffe zu erhalten
- OTOMcomposite entwickelt Software für die Composites 4.0-Produktion mit lasergestützter Bandplatzierung und -wicklung
- Fehlerbehebung beim Thermoformen von thermoplastischen Verbundwerkstoffen
- Thermoplastische Verbundwerkstoffe:Strukturelle Stoßstangenhalterung
- TPAC und TPRC entwickeln Recyclingprozess für thermoplastische Verbundwerkstoffe
- Schweißen von thermoplastischen Verbundwerkstoffen
- Konsortium für thermoplastische Verbundwerkstoffe strebt die Massenproduktion für die Automobil- und Luftfahrtindustrie an
- RTP Company entwickelt leichte und zähe thermoplastische Compounds