Fehlerbehebung beim Thermoformen von thermoplastischen Verbundwerkstoffen
Hinweis:Informationen und Bilder zu diesem Artikel wurden aus dem Kurs „Advanced Forming of Thermoplastic Composites“ des ThermoPlastic Composite Research Center (TPRC) erhalten.
Thermoplastische Verbundwerkstoffe (TPCs) gewannen zuerst mit der Nachfrage nach schnelleren Produktionsraten in der Luft- und Raumfahrt und anderen Leichtbauanwendungen an Bedeutung. Die Teilefertigung in wenigen Minuten machte das Thermoformen (auch bekannt als Stanzen) zum gebräuchlichsten Verfahren für thermoplastische Verbundwerkstoffe und zum ersten, das fliegende Teile in Massenfertigung herstellt (siehe „Innerhalb einer thermoplastischen Verbundwerkstoff-Brühe“ und „Clipzeit für thermoplastische Verbundwerkstoffe …“).
Der Prozess beginnt mit einem Zuschnitt – einem vorverfestigten thermoplastischen Verbundlaminat mit der erforderlichen Lagenorientierung – und umfasst folgende Schritte (Abb. 1):Zuschnittvorbereitung (Schneiden und Fixieren), Zuschnitt Erwärmen, Überführen in die Form, Platinenpositionierung, Umformen, Abkühlen, Entformen des Teils und Besäumen/Schlichten. Der Thermoformprozess ist ein einfaches Konzept, beinhaltet jedoch Komplexitäten und Herausforderungen, die angegangen werden sollten, um wiederholbare, qualitativ hochwertige Verbundteile zu erhalten.
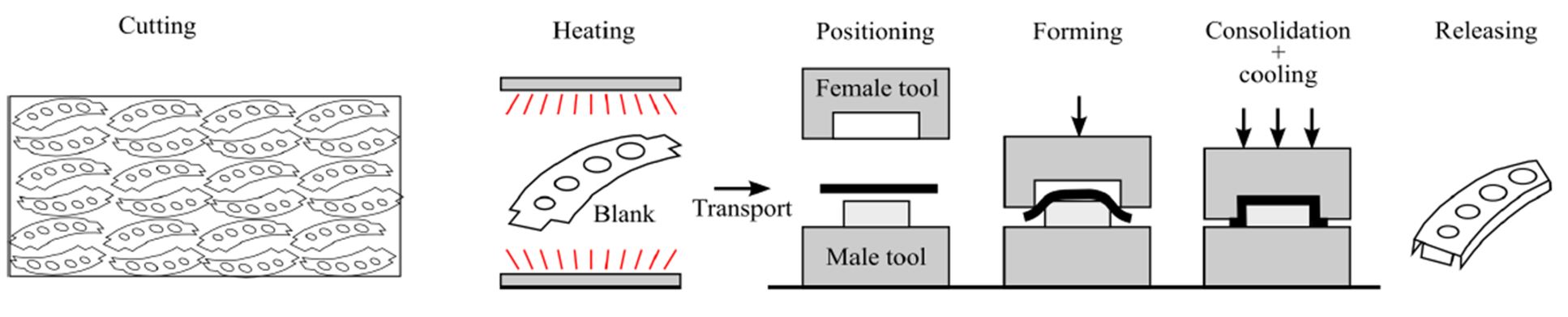
Falten vermeiden
Eine Falte ist ein visuelles und Funktionsfehler. Es kann als eine Biegung des Materials außerhalb der Ebene beschrieben werden. Die Hauptursache sind unzureichende Scherverformungen, wie z. B. Zwischenlagenschlupf und Zwischenlagenscherung, während der Verarbeitung. Faltenbildung tritt überwiegend bei doppelt gekrümmten Oberflächen auf. Ziehen Sie die folgenden Maßnahmen in Betracht, um Falten zu minimieren.
Ausreichendes Vorheizen und schnelle Übertragung. Während der Umformung des Rohlings sollte die Temperatur über der Schmelzetemperatur bleiben (Tm ) der TPC-Matrix, um eine Scherverformung zu ermöglichen. Berücksichtigen Sie, dass die Temperatur während des Transfers von der Vorwärmphase in die Form erheblich sinken kann – möglicherweise bis zu 40-50 °C in drei Sekunden. Daher sollte die Vorwärmung hoch genug sein, damit das Polymer über Tm . bleibt — oder Glasübergangstemperatur (Tg ) für amorphe Polymere — nach dem Transfer und während der Umformung. Ein kalter Rohling verformt sich nicht richtig und entwickelt Falten. Achten Sie jedoch darauf, den Rohling nicht zu überhitzen, um eine Polymerzersetzung zu vermeiden.
Stoff-Webart und -Layup. Harness-Satin (HS)-Stoffe haben aufgrund der leichteren Scherverformung in der Ebene eine bessere Drapierbarkeit, was zur Vermeidung von Falten beiträgt. Die Drapierbarkeit von gewebten Stoffen ist vom höchsten zum niedrigsten:8HS> 5HS> 2 x 2 Köper> Leinwandbindung. 5HS-Gewebe ist oft ein guter Ausgangspunkt, da es Drapierbarkeit und mechanische Leistung in Einklang bringt. Rohlinge, die mit unidirektionalen (UD) Verstärkungen hergestellt wurden, neigen aufgrund der hohen Reibung zwischen den Fasern, die einem Scheren in der Ebene widersteht, stärker zu knittern als HS-Gewebe. Das Zulassen von Scheren in der Ebene ist der Schlüssel zum Erfolg beim Umformen von UD-Rohlingen, insbesondere bei doppelt gekrümmten Oberflächen.
Schichtorientierungen wie [0, 90, ±45]s in einer quasi-isotropen Schichtung gefunden, kann eine Scherverformung hemmen, die Falten verstärkt. Alternativ helfen Kreuzlagen-Layups (z. B. [0, 90]) dabei, Faltenbildung zu vermeiden, da das Scheren nicht durch andere Lagen eingeschränkt wird.
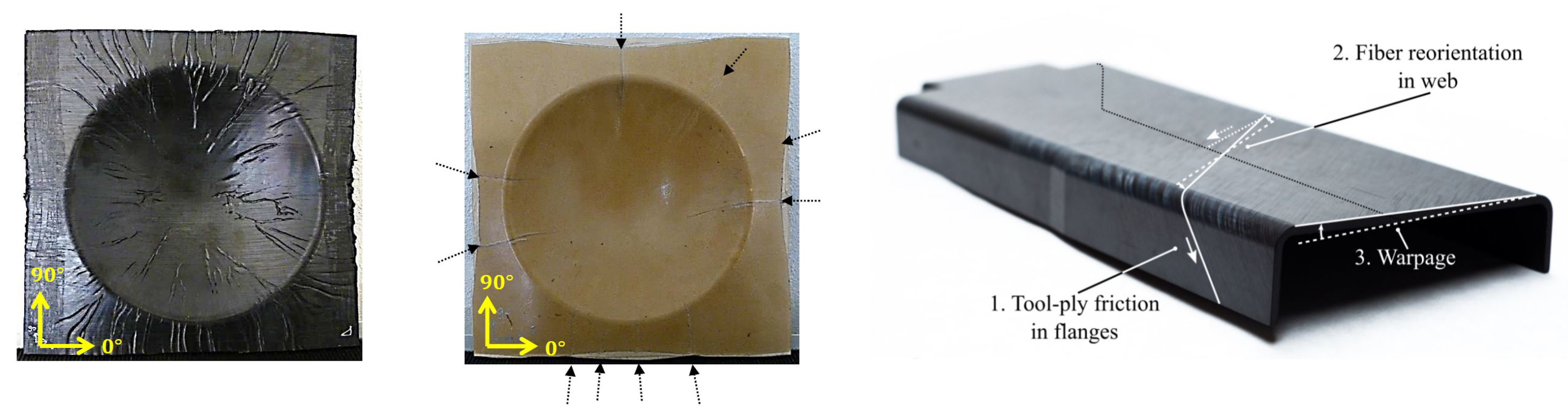
Abb. 2. Vermeidung von Falten und Verwerfungen
Der halbkugelförmige Teil zeigt viele kleine und große Falten mit einem UD-Rohling (links) , während bei einem 8HS-Rohling nur große Falten sichtbar sind (rechts) . Der Verzug in diesem Verbundholm resultierte aus der Neuorientierung der Fasern aufgrund der Werkzeuglagenreibung in den Flanschen. Bildnachweis:„Forming Limits of Thermoplast Composites“ von D.J. Wolthuizen et. al. (links ) und „Schnelle Herstellung maßgeschneiderter thermoplastischer Verbundwerkstoffe durch automatisiertes Lay-up und Stanzformen“ von Tjitse K. Slange (rechts ).
Vorbereitung und Fixierung des Rohlings. Greifer und Spanner können verwendet werden, um den Rohling in Bereichen unter Spannung zu halten, die für eine Biegung außerhalb der Ebene anfällig sind. Das Auffinden der optimierten Konfiguration kann zeitaufwändig sein, da mehrere Iterationen erforderlich sind, aber die Verwendung von Prozesssimulationssoftware hilft. Das richtige Spannen des Rohlings verhindert auch, dass der Rohling durchhängt, was zu Problemen beim Transfer und Umformen führen kann. Zu diesen Problemen gehört, dass der Rohling die Form zu früh berührt, wodurch möglicherweise zu viel Material auf die Form gelegt wird, bevor ein Drapieren auftreten kann, was zu Knicken und Faltenbildung führt. Der Rohling kann auch durchhängen und die Heizung berühren, was den Rohling beschädigen oder den Prozess stoppen kann.
Das Optimieren der endgültigen Geometrie des Rohlings und das Zuschneiden in eine nahezu Endform kann Falten verhindern und Ausschuss reduzieren. Schnitte und Abnäher können auch dazu beitragen, ein Biegen außerhalb der Ebene zu verhindern, indem die Faserspannungen reduziert werden, um eine bessere Formgebung zu ermöglichen.
Herausforderungen beim Formenbau meistern
Beim Thermoformen und ähnlichen Formprozessen kann das Werkzeug selbst eine Herausforderung darstellen. Die richtige Werkzeugkonstruktion kann helfen, Probleme mit Werkzeugkosten, Erwärmung, Teiledefekten und Entformung zu vermeiden.
Formwerkzeugmaterialien. Berücksichtigen Sie bei der Auswahl des richtigen Materials für ein Thermoformwerkzeug die für das endgültige Teil verwendeten Materialien, da diese die erforderliche Werkzeugtemperatur (Tmold .) beeinflussen ). Befolgen Sie beispielsweise die Faustregel TForm =(Tm +Tg )/2 , ein Teil aus verstärktem PPS (Polyphenylensulfid Tm =280°C) erfordert eine TForm von etwa 180 °C. (Amorphe und teilkristalline thermoplastische Polymere haben eine Tg , aber auch teilkristalline Polymere haben eine Tm .) Eine Metallform ist daher erforderlich, um ausreichend Wärme von der Platte der beheizten Presse oder ein beheiztes Werkzeug zum Formen des Teils abzuleiten. Für eine effiziente Teilekühlung ist auch eine Ableitung erforderlich. Für ein Teil, das aus verstärktem PMMA (Polymethylmethacrylat) hergestellt wurde, das einen viel niedrigeren Tg . hat (~100 °C), kann ein Holz- oder Epoxidwerkzeug bei Raumtemperatur ausreichend sein.
Weitere Überlegungen sind die aktuelle Entwicklungsphase und das verfügbare Budget, aber auch die Anzahl der aus dem Werkzeug zu fertigenden Teile. Formwerkzeuge sind bei der Verarbeitung Reibung, hoher Temperatur und Druck ausgesetzt. Da Holz und Epoxid im Vergleich zu Metallen eine geringere Hitzebeständigkeit und Belastbarkeit aufweisen, haben Formen aus diesen Materialien eine kürzere Lebensdauer und sind besser für die Kleinserienfertigung geeignet, während Metallwerkzeuge für die Großserienfertigung bevorzugt werden.
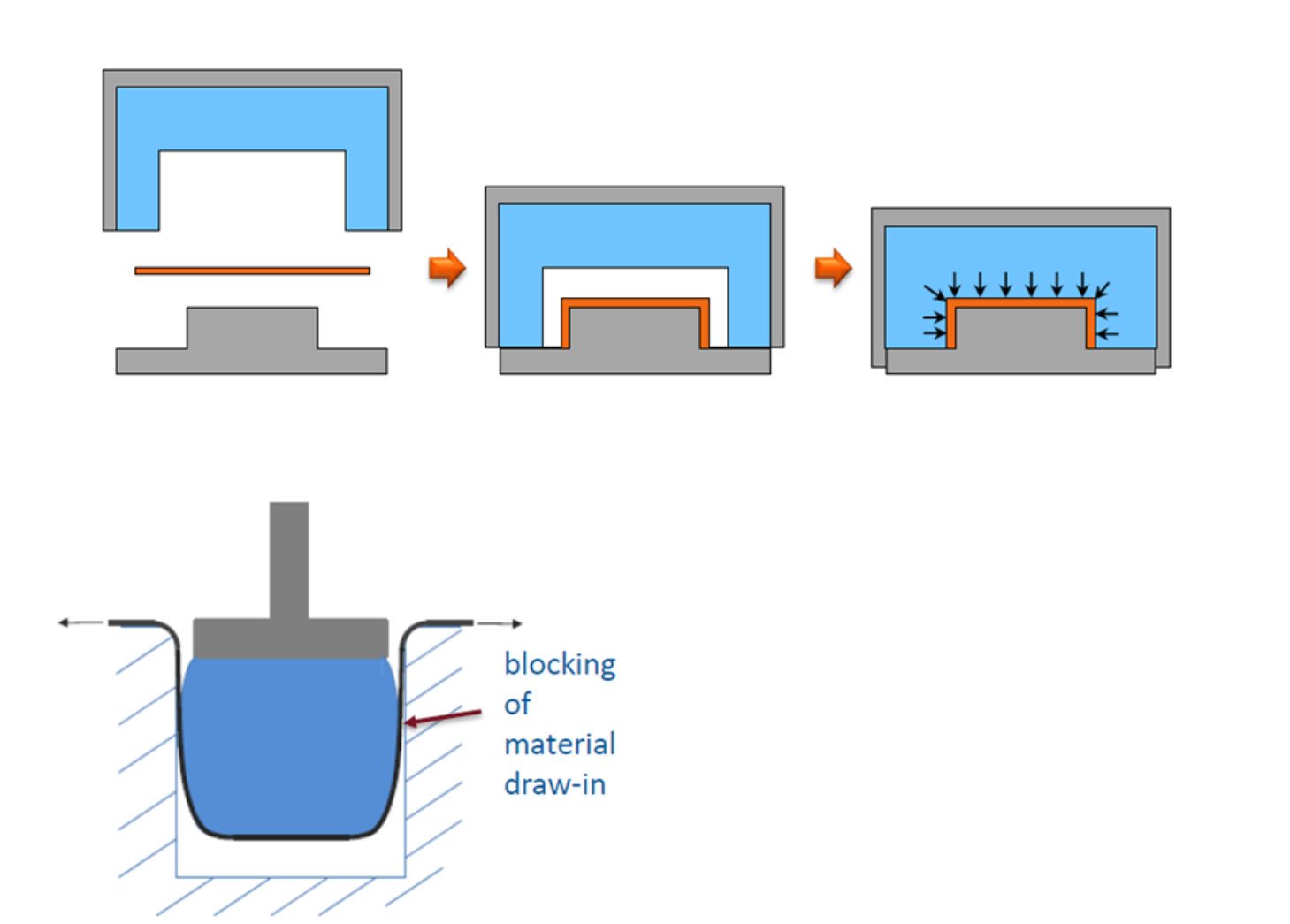
Ein weiteres zu berücksichtigendes Materialsystem für Werkzeuge ist Metall-Gummi , wobei eine Hälfte eines passenden Sets aus Metall und die andere aus Gummi besteht. Dies ermöglicht Produktionsflexibilität und kann für Teile mit größeren Toleranzen verwendet werden. Ein Metall-Gummi-Werkzeug sorgt auch für einen gleichmäßigen hydrostatischen Druck, was in Flanschbereichen und bei Blanks mit Dickenschwankungen, typisch für Tailored Blanks mit mehreren UD-Lagen, von Vorteil ist.
Diese inhärente Anwendung von hydrostatischem Druck ist auch ein Vorteil, wenn das gleiche Teil in mehreren unterschiedlichen Dicken hergestellt wird, wodurch die Kosten für separate Formen für jede Dicke entfallen. Bei der Konstruktion eines Metall-Gummi-Werkzeugs ist es wichtig, auch die folgenden Nachteile und Herausforderungen zu berücksichtigen:
- Die Metallseite des Werkzeugs erzeugt eine glattere Oberfläche im Vergleich zum Gummi.
- Metall-Gummi-Werkzeuge haben einen um eine Größenordnung höheren Wärmeausdehnungskoeffizienten (CTE) als Ganzmetallwerkzeuge.
- Aufgrund der geringeren Wärmeleitfähigkeit im Vergleich zu Metall dauert das Abkühlen etwas länger und führt zu einer stärkeren Verzögerung bei der Reaktion der Temperaturregelung.
- Erhöhter Verschleiß und Alterung führen zu einer kürzeren Lebensdauer im Vergleich zu Ganzmetallwerkzeugen.
Umformen und Entformen. Die richtige Werkzeugkonstruktion sorgt für ausreichenden Druck, optimale Drapierung, hilft Fehler zu vermeiden und fördert die sichere Teileentnahme. Obwohl es viele Probleme beim Umformen und Entformen gibt, sind einige der wichtigsten:
- Druck. Während des Thermoformens kann ein niedriger Druck zu einer schlechten Verfestigung, verringerten mechanischen Eigenschaften und außerhalb der Toleranzen der Teileabmessungen führen. Eliminieren Sie bei einem passenden Metall-Metall-Werkzeug Endanschläge, damit der kontinuierliche Druck auf das Laminat nicht durch die Lücke verhindert wird, die die Endanschläge erzeugen.
- Materialeinzug erlauben . Um eine Ausdehnung der Gummiseite der Form während des Pressens (sogenanntes Barreling) zu vermeiden, die die Bewegung des Materials während des Pressens (Einziehen) blockieren kann, legen Sie den Gummi auf die Matrize des Formwerkzeugs (siehe Abb. 3) .
- Ausbau von Teilen . Gestalten Sie die Form für L-förmige Teile mit dem gewünschten L-Winkel, der zu einem V geneigt ist, um die Reibung mit dem Werkzeug zu reduzieren und eine einfache Entnahme der Teile zu ermöglichen. Verwenden Sie bei kastenförmigen Teilen eine Entformungsschräge von 1-2 Grad für jede Seite; Für tiefere Teile sind möglicherweise höhere Winkel erforderlich.
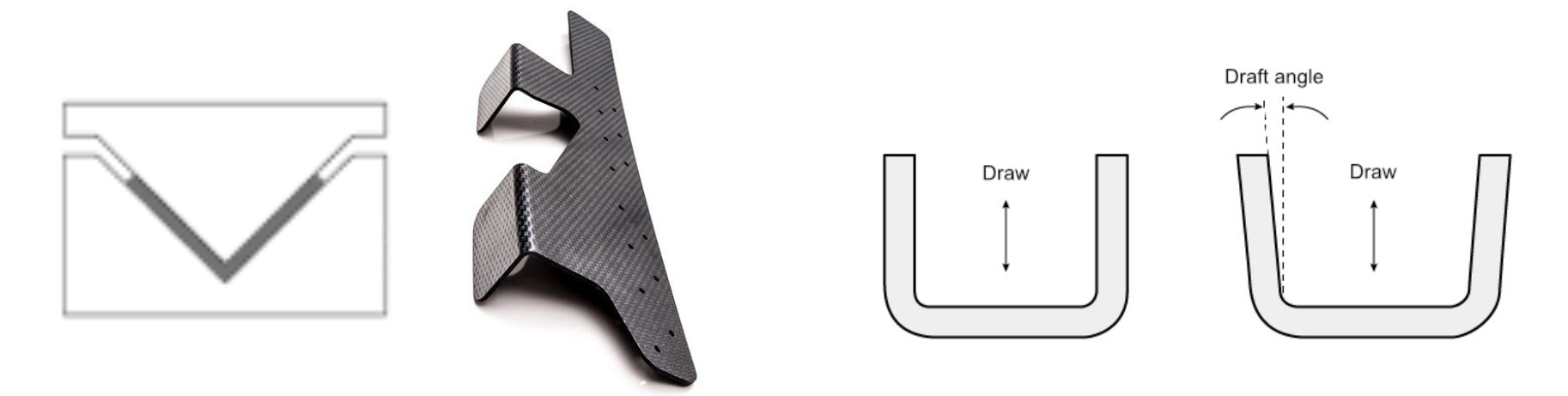
Warpage und Spring-in
Verzug und Einfedern sind Formverzerrungen, die durch anisotrope Materialeigenschaften und ungleichmäßige Harzkühlung verursacht werden, die nach dem Formen des Teils auftreten und zu Teileabmessungen außerhalb der Toleranz führen können, die möglicherweise zu Montageproblemen und zum Verschrotten von Teilen führen. Ein Verzug tritt auf, wenn ein Bereich mit hoher eingeformter Spannung innerhalb eines Teils sich mit einem Bereich geringer eingeformter Spannung schneidet. Dieses Spannungsungleichgewicht wird dadurch aufgehoben, dass der Bereich mit hoher Spannung den Bereich mit niedriger Spannung verformt, was zu einem Durchbiegen oder Verdrehen des Laminats führt.
Das Einfedern tritt in gebogenen Platten oder in Teilen mit Eckabschnitten auf, wenn die eingeformte Spannung dazu führt, dass sich die Wandabschnitte in einem Winkel nach innen verziehen, der geringer ist als der vorgesehene Winkel. Dies geschieht häufig bei Faserverbundwerkstoffen aufgrund ihrer anisotropen Eigenschaften. Auch die Teilegeometrie spielt eine Rolle. Die unterschiedliche Schrumpfung zwischen in der Ebene (niedriger CTE in Faserrichtung) und durchgehender Dicke (hoher CTE der Matrix) kann eine Winkelabnahme von 1-3 Grad verursachen.
Das Beheben von Formverzerrungen kann kostspielig und zeitaufwändig sein. Die Verwendung von Simulations- und Konstruktionswerkzeugen wird für eine schnellere Teileentwicklung dringend empfohlen. Suchen Sie nach den folgenden möglichen Ursachen und Lösungen, wenn Sie mit Verzug konfrontiert sind:
- Prozessparameter . Die Formtemperatur beeinflusst die Dickeneigenschaften, die mit Kristallisation und viskoelastischen Effekten verbunden sind, die den Verzug beeinflussen können. Eine Reduzierung der Werkzeugtemperatur kann das Einfedern verringern, aber die inneren Spannungen erhöhen, was nach dem Lösen zum Einfedern führen kann. Diese Unsicherheit sollte sorgfältig geprüft werden. Hoher Druck und hohe Umformgeschwindigkeit können auch das Einfedern reduzieren und möglicherweise das gegenteilige Problem – das Zurückfedern – fördern, indem sie den Zwischenlagenschlupf begrenzen. Eine längere Verweilzeit kann sicherstellen, dass die Matrix vollständig verfestigt ist und Restwärme eliminiert, wodurch die Schrumpfung nach der Teileentnahme und damit das Einfedern reduziert wird.
- Formendesign . Das Einfedern kann durch Veränderung der Wandwinkel in der Form ausgeglichen werden. Außerdem fördern Metallformen, wie bereits erwähnt, eine gleichmäßigere Kühlung und können dazu beitragen, das Verzugsrisiko zu verringern, insbesondere bei dicken Teilen.
- Layup. Symmetrische Lagen werden häufig verwendet, um den Verzug zu mindern, aber während des Thermoformens kann es zu einer Neuorientierung der Fasern kommen, die zu Asymmetrie und Verzug führt. Eine weitere Manifestation der Asymmetrie ist die Harzwanderung während der Radiusformung (einschließlich Ecken). Dies verursacht eine Faserumverteilung und lokale Veränderungen des Faservolumenanteils, was Anisotropie und Verwerfung fördert. Unterschiedliche Lagen und Lagenfolgen verhalten sich unterschiedlich, da Fasern auf Belastungen reagieren, was wiederum die Verwerfung beeinflusst. Simulations- und Vorhersagetools können helfen, dieses komplexe Materialverhalten anzugehen.
Obwohl der Thermoform-/Stanzprozess mehrere Parameter und ein komplexes Materialverhalten umfasst, gibt es grundlegende Prinzipien und Maßnahmen, die eine erfolgreiche Entwicklung leiten können. Mit zunehmendem Einsatz von thermogeformten TPC-Teilen und insbesondere von UD-Tailored Blanks werden neue Herausforderungen mit innovativen Lösungen und verbesserten Konstruktions-/Simulationswerkzeugen angegangen.
Harz
- Covestro verstärkt Investitionen in thermoplastische Verbundwerkstoffe
- Recycling:Endlosfaserverstärkte thermoplastische Verbundwerkstoffe mit recyceltem Polycarbonat
- Thermoplastische Verbundwerkstoffe bei Oribi Composites:CW Trending, Episode 4
- Thermoplastische Verbundwerkstoffe:Strukturelle Stoßstangenhalterung
- Toray Advanced Composites erweitert seine Fähigkeiten im Bereich thermoplastischer Verbundwerkstoffe
- ACMA veröffentlicht Programm der Konferenz für Thermoplastische Verbundwerkstoffe 2020
- Thermoplastische Tür eine Premiere für Automobilverbundwerkstoffe
- Thermoplastische Verbundwerkstoffe:Malerische Aussicht
- CAMX 2018-Vorschau:TenCate Advanced Composites
- Schweißen von thermoplastischen Verbundwerkstoffen