DLR-Institut für Konstruktion und Konstruktion steigert Reifegrad von thermoplastischen Rumpfstrukturen aus Verbundwerkstoff
Im Projekt „LuFoV-3 TB-Rumpf“ wird die autoklavfreie Verfestigung thermoplastischer Prepreg-Laminate und das Widerstandsschweißen als Technologiebausteine für zukünftige Flugzeugrümpfe weiterentwickelt und validiert. Diese Arbeiten werden vom Deutschen Zentrum für Luft- und Raumfahrt (DLR), Institut für Konstruktion und Konstruktion (Institut BT) in Stuttgart in Zusammenarbeit mit Partnern aus der Luft- und Raumfahrtindustrie, darunter Airbus und anderen Forschungsinstituten, durchgeführt.

Das DLR-Institut BT hat eine vollintegrierte Rumpfkreuzung, bestehend aus Haut, Stringern, Spant und Stollen, demonstriert. Der Demonstrator basiert auf einer außerhalb des Autoklaven (OOA) verfestigten gebogenen Haut mit zusammenverfestigten Stringern und der Integration von Rahmen und Stollen durch Widerstandsschweißen. Die Schweißnähte wurden durch mechanische Tests charakterisiert und die Schweißnaht wurde mit einem Lichtmikroskop weiter untersucht.
TB-Rumpf Reifung OOA Konsolidierung und Schweißen
Stand der Technik zur Verfestigung großflächiger Bauteile aus endlosfaserverstärkten Hochtemperatur-Thermoplasten (z. B. Polyaryletherketon oder PAEK) ist die Autoklavenverfestigung. Durch einen optimierten Prozessaufbau und eine maßgeschneiderte Prozesssteuerung ist es jedoch möglich, eine vollständige Konsolidierung nur mit Temperatur und Vakuumdruck zu erreichen. Der Einsatz von selbstbeheizten Formen oder Öfen kann einen Autoklaven überflüssig machen und damit Kostenvorteile generieren. Das Projekt TB-Rumpf zielt darauf ab, den Prozess namens VCT (Vacuum Consolidation Technique) zu reifen und die Prozessgrenzen einschließlich der maximal möglichen Laminatdicken zu bestimmen.
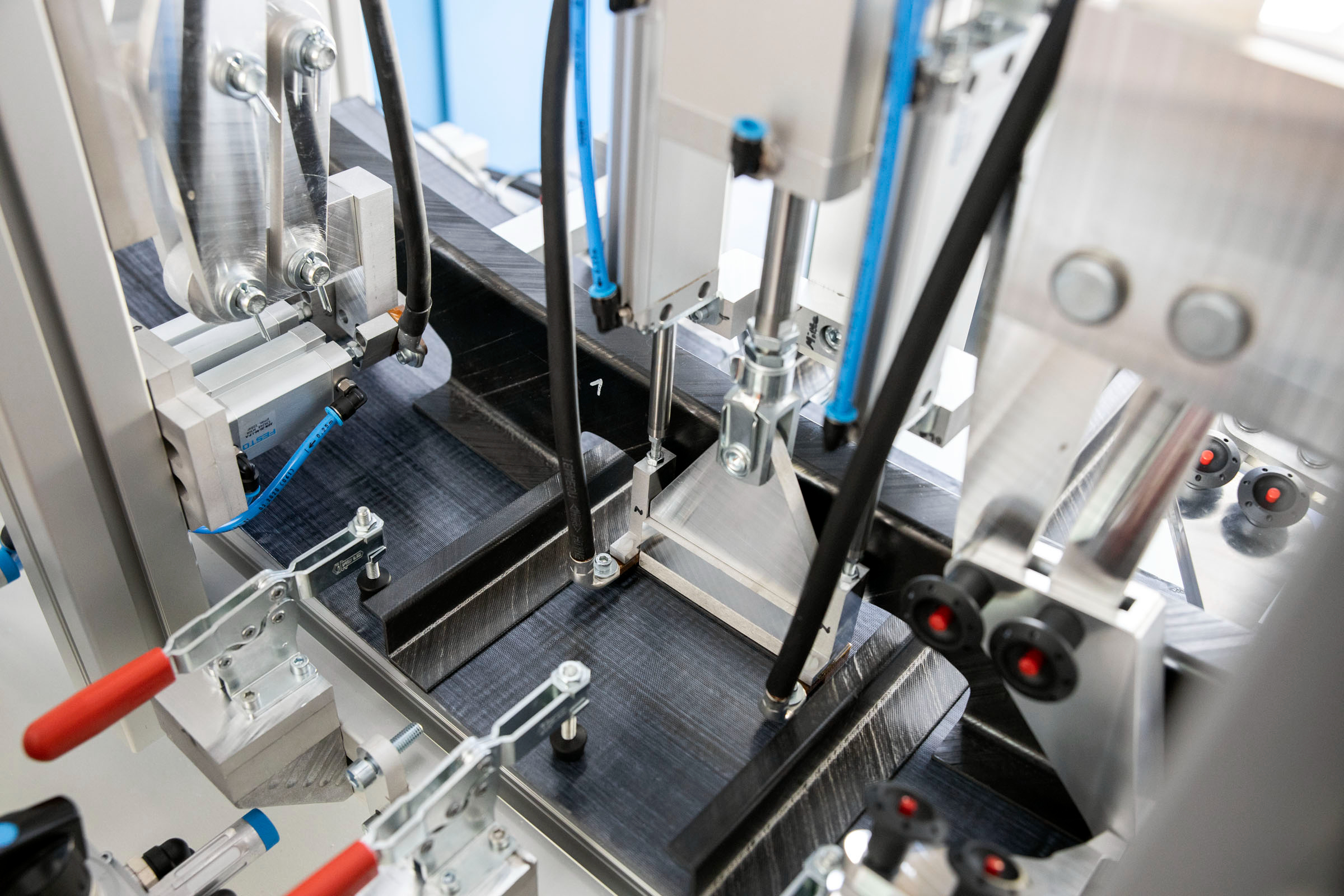
Eine weitere Schlüsseltechnologie für zukünftige Anwendungen fortschrittlicher thermoplastischer Verbundwerkstoffe ist das Schweißen für die Montage. DLR und Airbus haben das Widerstandsschweißen aufgrund seiner Fähigkeit, hochfeste Strukturen zu erzielen, als führende Technologie identifiziert. Im Projekt TB-Rumpf werden der Widerstandsschweißprozess und notwendige Schweißelemente optimiert. Die resultierenden Demonstratoren werden strukturell getestet, um die mechanische Leistung der Verbindung und der geschweißten Verbundlaminate zu validieren.
Untersuchung der Vakuumkonsolidierungstechnik (VCT)
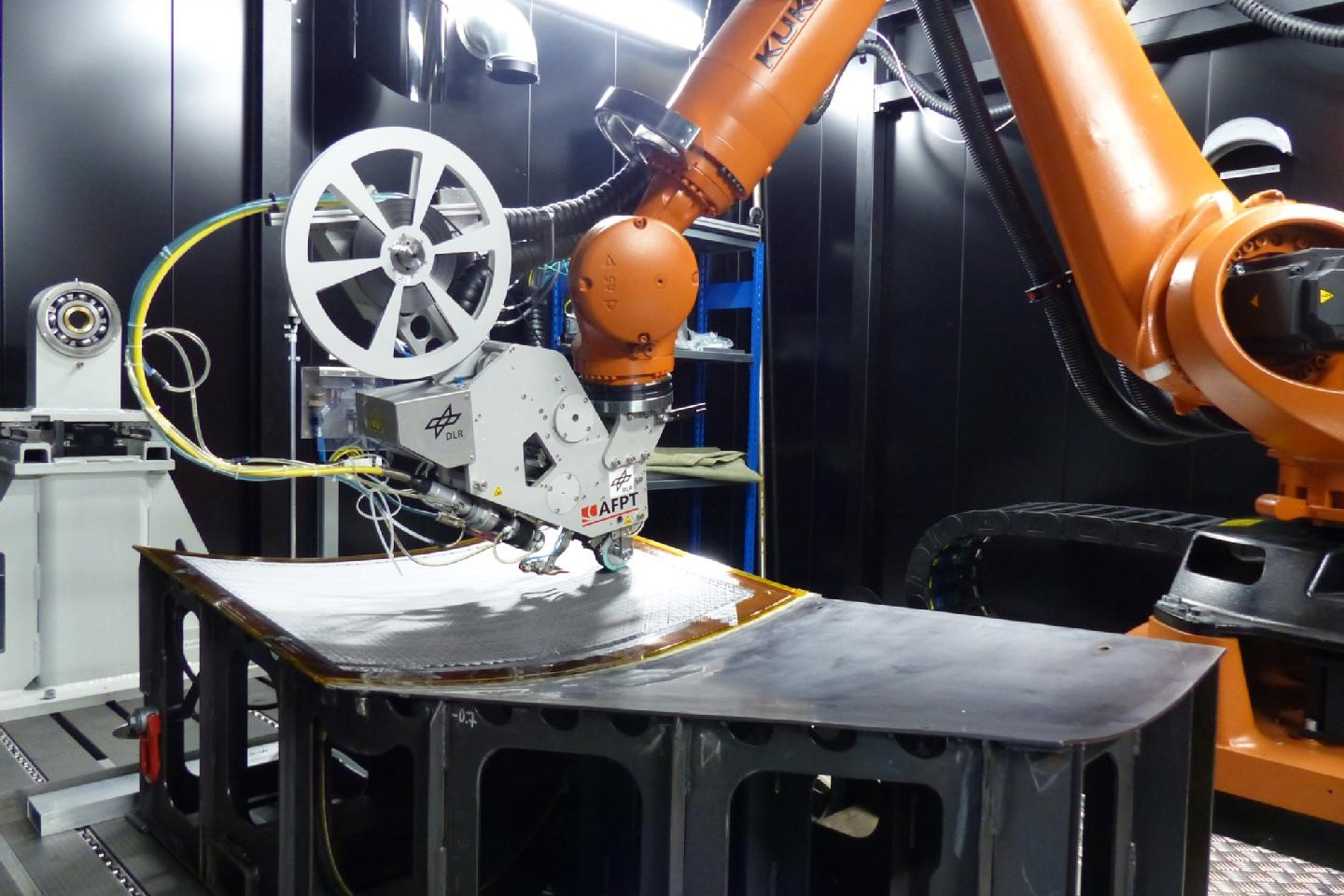
Matthias Horn, Projektleiter beim DLR-Institut BT, erklärt, dass der TB-Rumpf-Demonstrator unidirektionales kohlenstofffaserverstärktes niedrigschmelzendes Polyaryletherketon (LM-PAEK) verwendet. Dieses thermoplastische Verbundband wird mittels automatisierter Faserplatzierung (AFP) verarbeitet, die mit einem KUKA (Augsburg, Deutschland) Roboter mit einem AFPT (Doerth, Deutschland)-Endeffektor und einem 6-Kilowatt-Laser zum Erwärmen des Bandes erreicht wird.
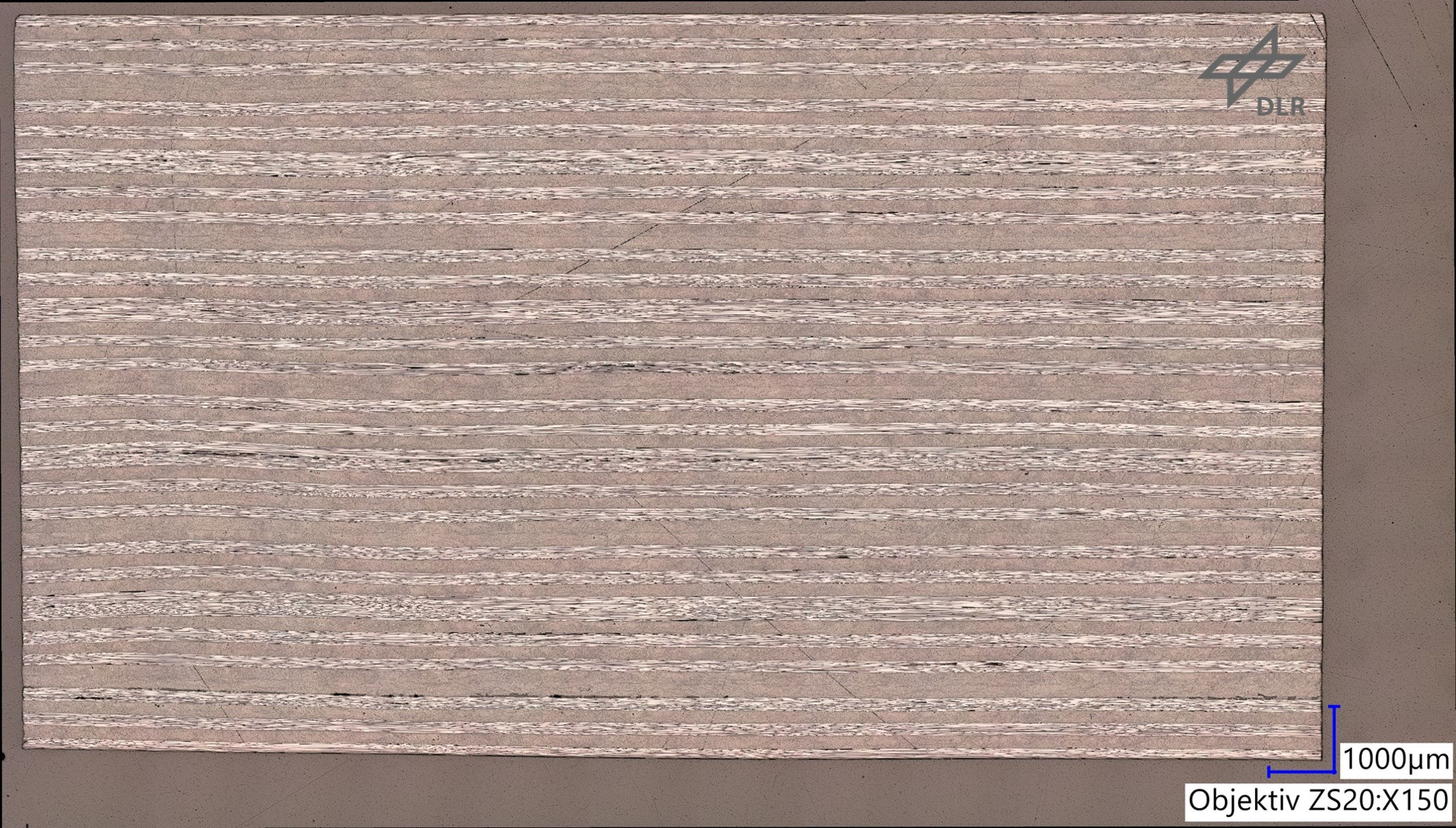
OOA-Konsolidierung mit VCT: „Ziel war es, die Machbarkeit dieses Verfahrens für dicke Laminate zu validieren“, sagt Georg Doll, BT-Forscher am Institut und TB-Rumpf-Leiter für die Konsolidierung. „Wir haben gute Ergebnisse für Laminate mit einer Dicke von bis zu 11 Millimetern ohne Poren oder andere Unvollkommenheiten gezeigt, die durch mikroskopische Querschnitte und Ultraschallprüfung validiert wurden. Der Schlüssel zu diesem Erfolg sind ein optimiertes VCT-Setup, ein maßgeschneiderter Heizzyklus und eine homogene und konstante Prepreg-Qualität.“
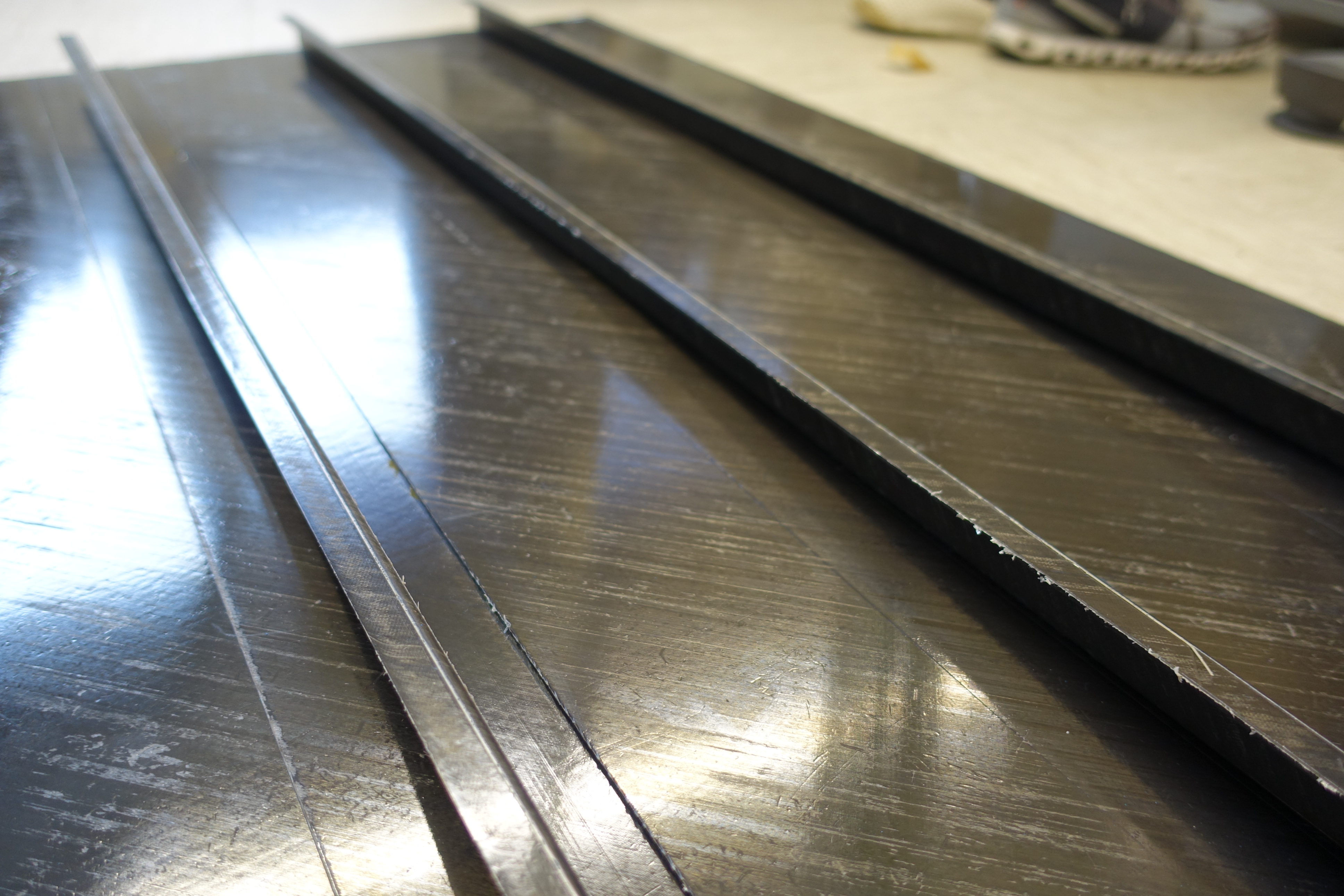
OOA-Co-Konsolidierung von Versteifungselementen: Neben der Verwendung von VCT zur Herstellung von Rumpfhautpaneelen ohne Autoklaven ist es im TB-Rumpf-Projekt auch gelungen, eine Co-Konsolidierung zur direkten Integration der Stringer-Versteifungselemente mit der Haut während eines einzigen VCT-Prozesszyklus zu entwickeln.
AFP-Layup von gebogenen und doppelt gebogenen Formen: Laserbasiertes AFP als komplementäres Verfahren zur VCT wurde unter Berücksichtigung der Prozess- und Materialgrenzen (z. Die Ergebnisse dieser Herstellungsversuche können verwendet werden, um die OOA-Konsolidierung sowie die in-situ-Konsolidierung voranzutreiben, die während der AFP ohne einen zweiten Eingriff erreicht wird.
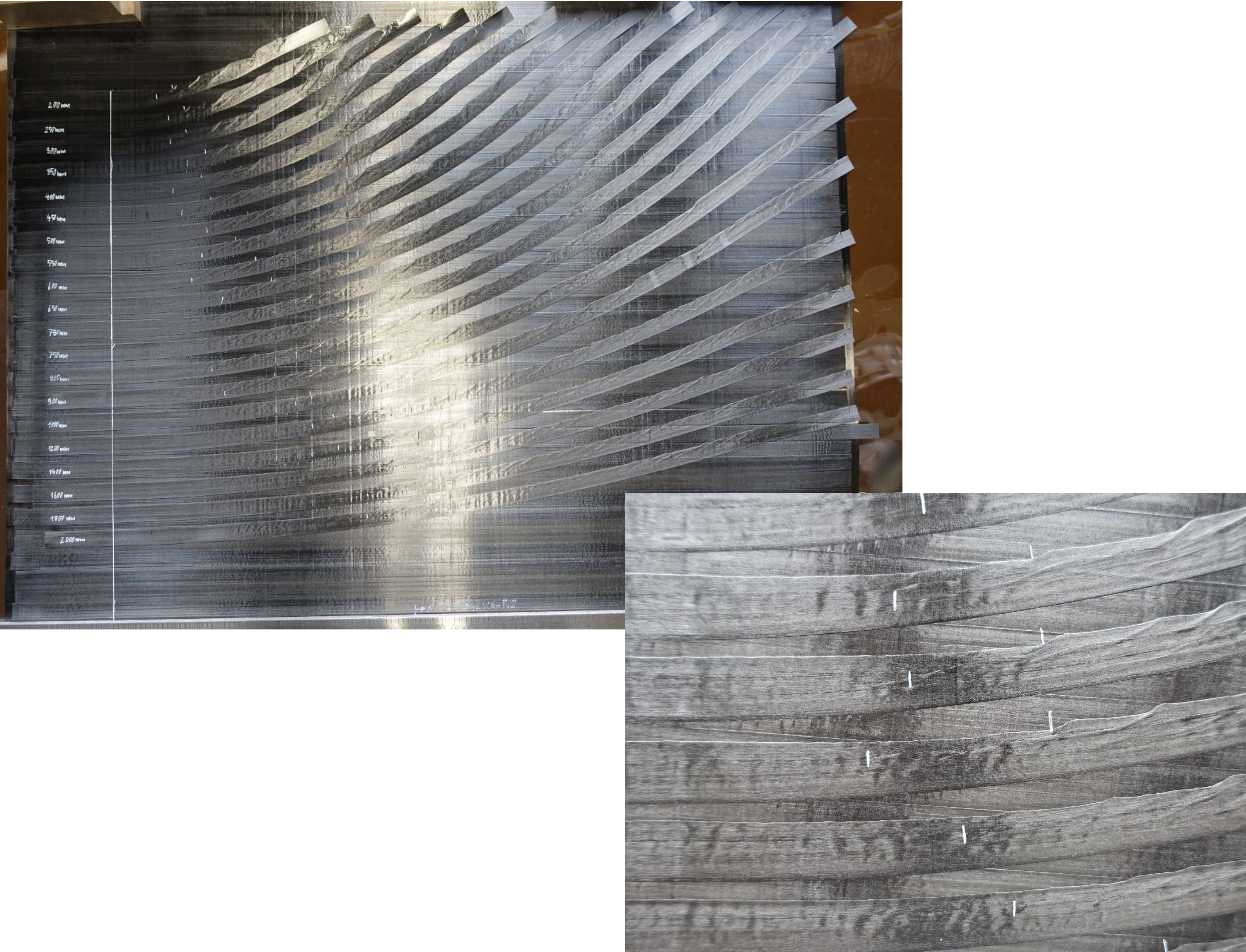
Widerstandsschweißen
„Um strukturelle Rumpfelemente zu integrieren und damit die Produktion zukünftiger thermoplastischer Rumpfkonzepte möglich zu machen, haben wir das Widerstandsschweißen im Hinblick auf erhöhte Prozessrobustheit und optimierte Festigkeitswerte untersucht“, sagt Simon Bauer, Institut BT Forscher und TB-Rumpf Leiter Schweißen. „Der Fokus lag auf einem optimierten Schweißelement-Setup, basierend auf Kohlefaser als Heizelement, und einer verbesserten elektrischen Leitfähigkeit, in Kombination mit den am besten geeigneten Schweißparametern wie Heizzyklus, Temperatur, Druck, Strom und Spannung.“ Widerstandsschweißen wurde verwendet, um die Stollen sowohl am Rahmen als auch an den Stringern zu befestigen; es wurde auch verwendet, um den Rahmen an der Haut zu befestigen.
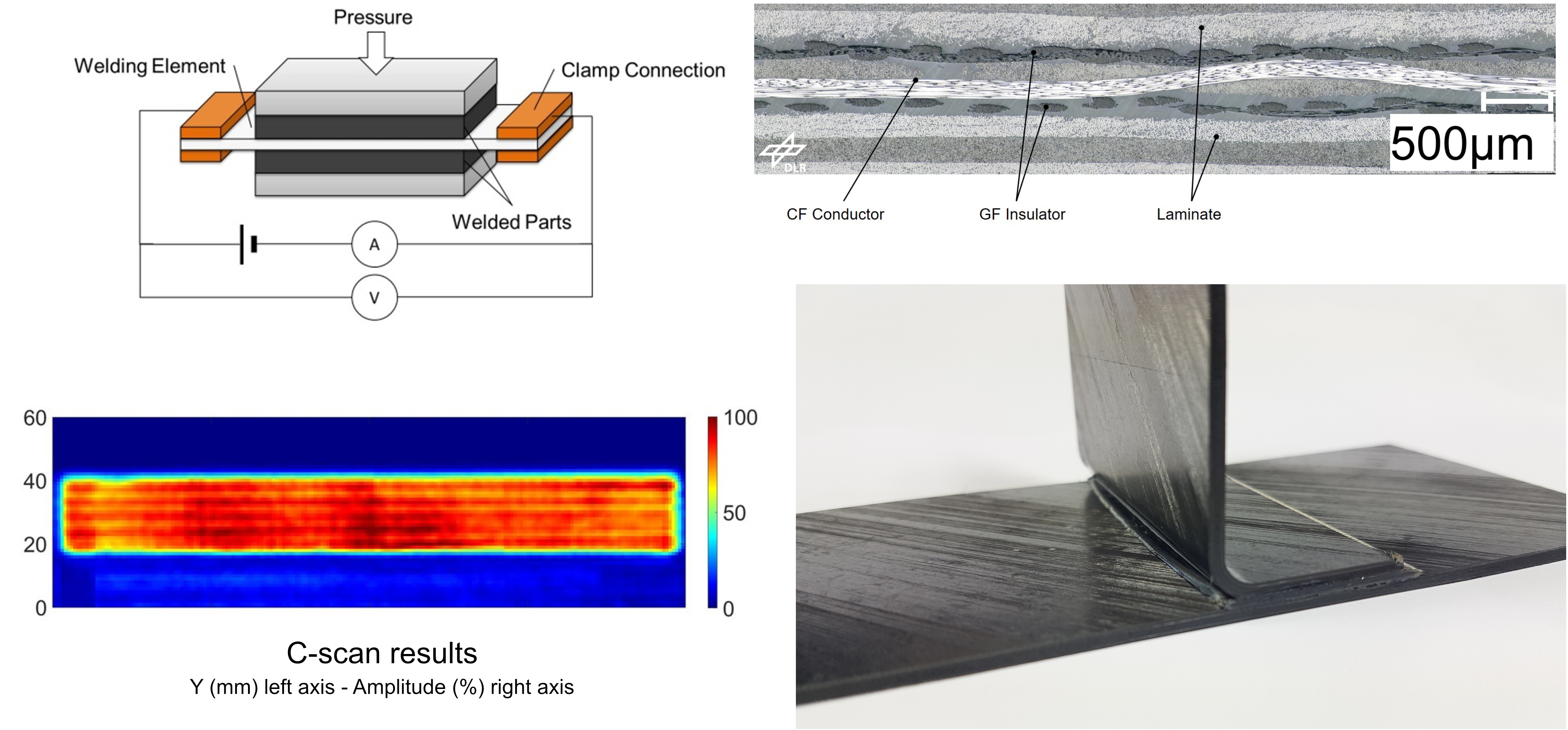
Technologiebausteine für kommende Rumpfdesigns
„Aufgrund der nachgewiesenen Technologiereife können sowohl die Konsolidierung außerhalb des Autoklaven als auch das Widerstandsschweißen eine wichtige Rolle für zukünftige Rumpfkonstruktionen spielen“, unterstreicht Dr. Paul Jörn, Leiter des entsprechenden Airbus-Projekts.
Um die Technologien noch näher an die industrielle Anwendung zu bringen, werden in naher Zukunft weitere herausfordernde Aspekte untersucht. Bei der Vakuumkonsolidierung wird die Größenskalierung und die Übertragung auf doppelt gekrümmte Konturen fokussiert. Beim Widerstandsschweißen werden sowohl Toleranzaspekte als auch Automatisierungsaspekte angesprochen.
Die hier vorgestellten Ergebnisse wurden im Rahmen des Forschungsprojekts TB-Rumpf (FKZ:20W1721D) im Rahmen des Bundesluftfahrtforschungsprogramms V-3, gefördert vom Bundesministerium für Wirtschaft und Energie, erzielt.
Weitere Informationen finden Sie unter dlr.de/bt.
Harz
- Designvorteile von Thermoplasten in Pumpen- und Ventilkomponenten
- Solvay erweitert die Kapazität von thermoplastischen Verbundwerkstoffen
- RECONTRAS-Projekt validiert den Einsatz von Mikrowellen und Laserschweißen, um recycelbare Verbundwerkstoffe zu erhalten
- Thermoplastische Bänder zeigen weiterhin Potenzial für Verbund-Flugzeugstrukturen
- Einfach zu verwendende Kits ermöglichen die Reparatur von Verbundstrukturen im Feld
- Entwicklung von zusammengesetzten Isogitterstrukturen mit innovativer Abscheidungstechnologie
- Designinnovationen verbessern die Effizienz von medizinischen Tischen aus Verbundwerkstoff
- Wing of Tomorrow-Rippen:One-Shot, thermoplastisch, OOA-Konsolidierung
- Konsortium sucht Lösungen für thermoplastische Kohlefaser-Verbundstrukturen
- Schweißen von thermoplastischen Verbundwerkstoffen