Reduzierung der Kosten für Endlosfaser-3D-Druckmaterialien
Das DLR-Institut für Faserverbundwerkstoffe und Adaptive Systeme (Braunschweig) ist eine führende Forschungseinrichtung im Leichtbau und verfolgt neue Technologien in vier strategischen Feldern:Design to Certification, Digitalisierung und Industrie 4.0, Recycling und additive Verbundstrukturen. CW berichtete Anfang des Jahres über das EmpowerAX Innovation Lab des Instituts, um den Transfer der additiven Extrusion in die Industrie für 3D-gedruckte Verbundwerkstoffe zu beschleunigen, zu stärken und auszuweiten. schließt außerdem eine Reihe von F&E-Projekten ab, darunter die Simulation der additiven Extrusion, die Modifizierung von Thermoplasten für eine verbesserte Leistung beim 3D-Druck und die Herstellung von Druckerfilamenten mit Endlosfasern.
Dieses letzte Projekt mit dem Titel ENDLOSEFFEKT („endloser Effekt“) soll die Herstellbarkeit, Qualität und Kosten von endlos langen faserverstärkten Materialien verbessern. „Die Verfügbarkeit von vorimprägnierten Endlosfaser-Druckfilamenten ist begrenzt“, erklärt Maik Titze, verantwortlich für die additive Fertigung am DLR-Institut für Faserverbundwerkstoffe und Adaptive Systeme in Braunschweig. „Diese begrenzte Verfügbarkeit und Vielfalt an verwendbaren Materialien sowie die Materialpreise stellen eine Anwendungsbarriere dar. Wir wollten eine Imprägnierdüse so konstruieren, dass die gleiche Ausrüstung, die zur Herstellung von standardmäßigen, mit geschnittenen Fasern gefüllten Filamenten für FDM [Fused Deposition Modeling] verwendet wird, auch endlosfaserverstärkte Filamente produzieren kann. Diese Ausrüstung wäre für Unternehmen gedacht, die 3D-Druckerfilamente herstellen, mit dem Ziel, die Kosten des 3D-Drucks mit endlosfaserverstärkten Materialien zu senken.“
Derzeit werden die meisten endlosfaserverstärkten 3D-Druckerfilamente von denselben Unternehmen hergestellt, die Endlosfaserdruckmaschinen verkaufen, wobei jedes Material für ein bestimmtes Drucksystem entwickelt und optimiert wurde. Diese Materialien sind in der Regel etwas teuer.
„Unsere Idee ist es, mit Trockenfasern jeder Größe zu beginnen, beispielsweise 1K-Carbonfaserkabel bis zu 50K, und dann die direkte Schmelzimprägnierung aus handelsüblichen thermoplastischen Pellets oder Granulaten durch Extrusion zu verwenden, da dies sehr kostengünstig ist“, sagt Titze. „Sie müssen weder Polymerpulver oder -folien herstellen, noch teure Pressen oder Hunderte von Walzen verwenden, um die Faser zu imprägnieren. So wird die Verarbeitung viel zugänglicher und erschwinglicher.“
Anstelle von Pressen, Bändern und Walzen hat das DLR ein System mit Ultraschall entwickelt. „Wir verwenden eine 19,5-Kilohertz-Sonotrode, die Schwingungen in den geschmolzenen Thermoplast umleitet, der die Faser umgibt“, erklärt Titze. „Dies die Matrix und die Verstärkung bei 19.500 Mal pro Sekunde, was zu einer sehr guten Imprägnierung führt.“
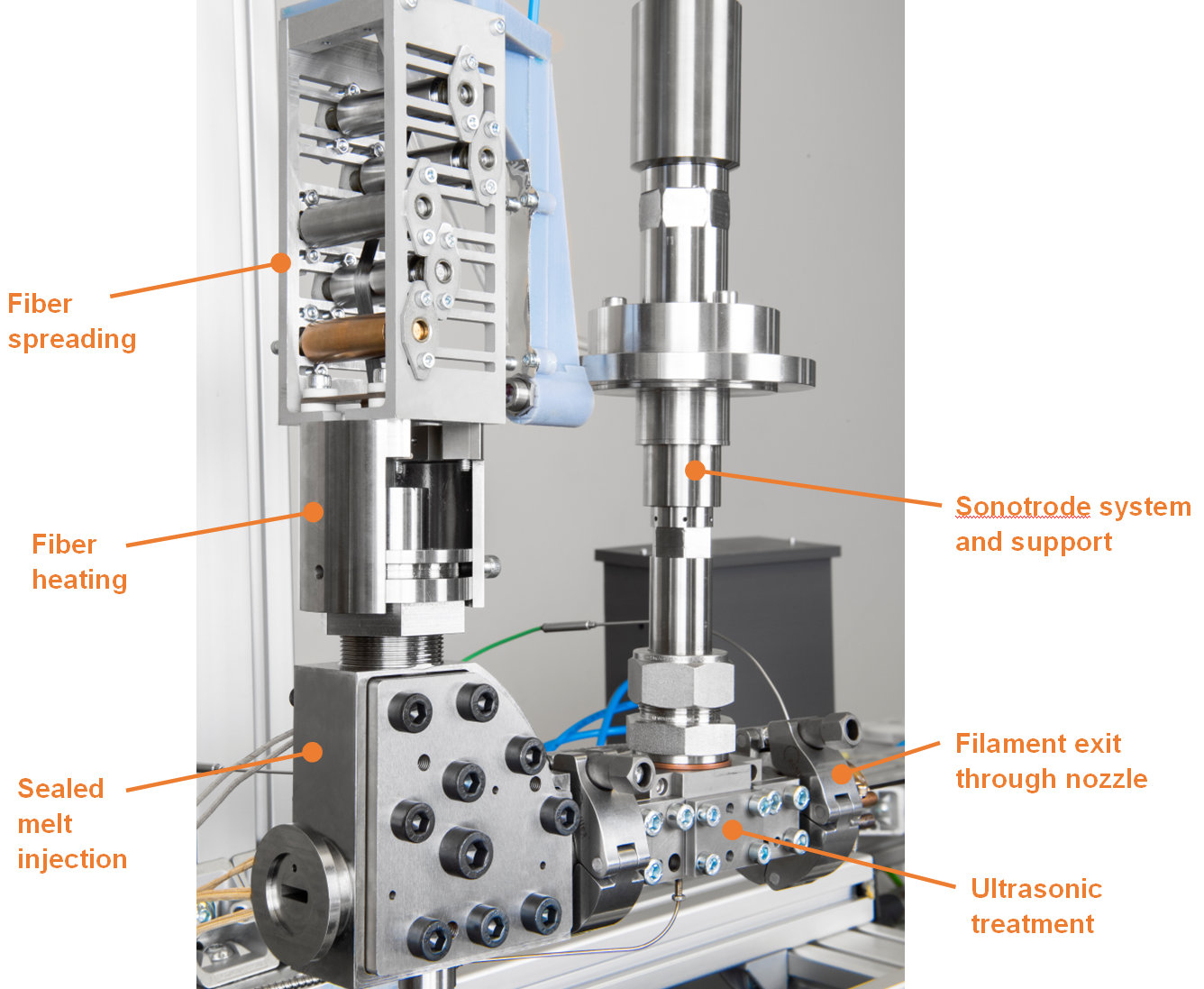
Der Prozessweg beginnt mit der Faserausbreitung und Erwärmung (Abb. 1). Diese Verstärkung wird dann einer abgedichteten Kammer zugeführt, in die das geschmolzene Polymer eingespritzt wird. Wenn die Faser diese Kammer passiert, überzieht geschmolzenes Harz die Faser. „Faser und Polymer gelangen dann in eine Ultraschallkammer, die mit 80 Millimetern Länge sehr klein und kompakt ist“, sagt Titze. „Die von der Sonotrode ausgehende Schwingung versetzt das faserverstärkte Polymerfilament in Schwingung, das dann in beliebiger Form aus der Düse austritt. Die Düse kann beispielsweise rund oder flach sein.“
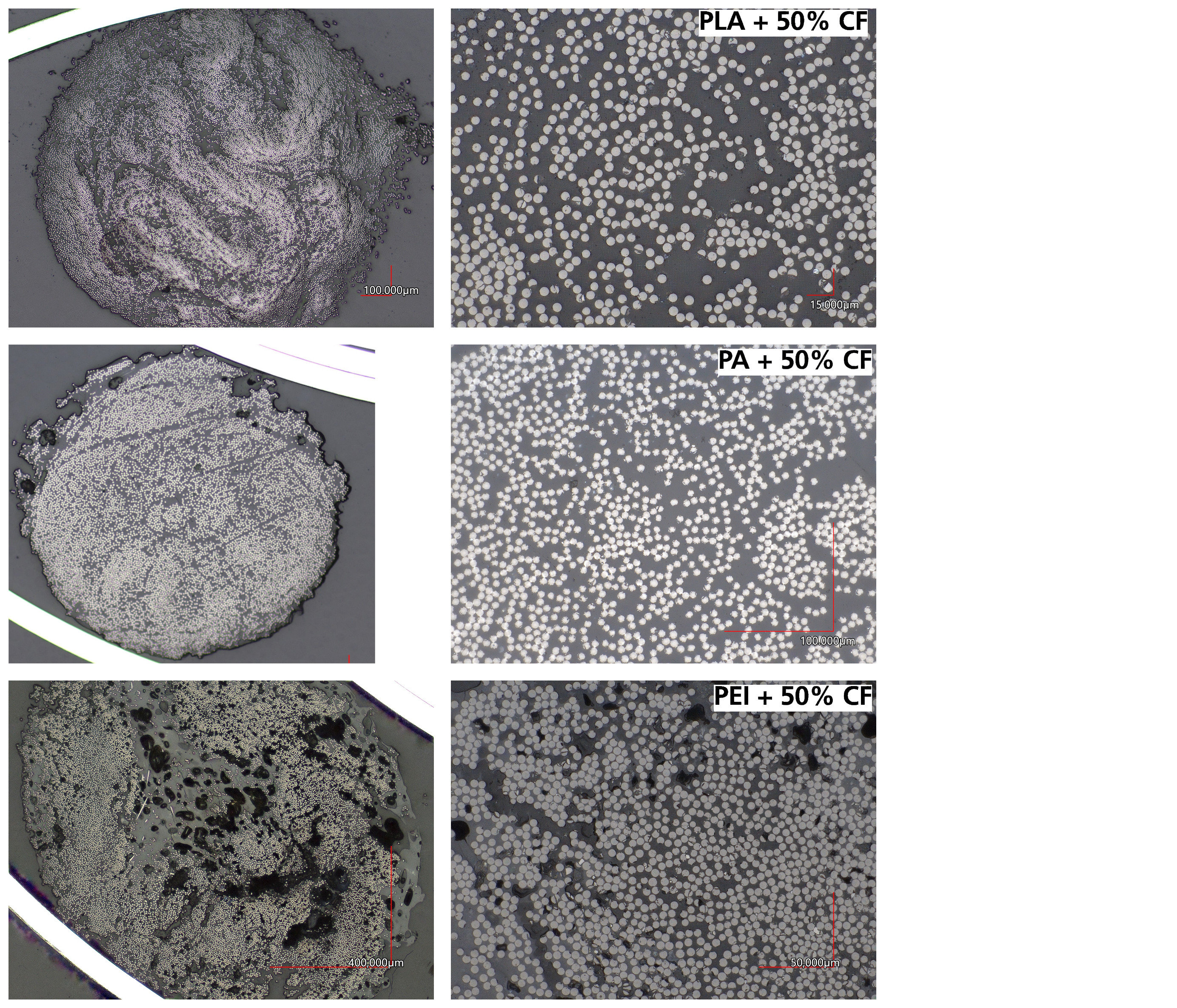
Die mikroskopischen Aufnahmen in Abb. 2 zeigen 12K-Kohlenstofffasern imprägniert mit Polymilchsäure (PLA), Polyamid (PA) und Polyetherimid (PEI) bei 50 % Faservolumen. Das Faservolumen ist durch die Gestaltung der Düsendüse einstellbar (30-50%), sagt Titze. „Wir glauben, dass bis zu 60 % möglich sein werden. Insgesamt ist noch mehr Arbeit am Prozess erforderlich, aber wir haben gezeigt, dass er mit guten ersten Ergebnissen funktioniert und eine Liniengeschwindigkeit von 5 Millimeter/Sekunde.“ Er räumt ein, dass dies langsam und nicht wirtschaftlich ist, aber im Juni sollte ein neues Gerätedesign getestet werden, das bereits 3 Meter/Minute erreichen soll.
„Normalerweise liegen die Geschwindigkeiten eher bei 10 Metern/Minute“, sagt Titze. „Die Technologie soll aber auch eine flexible Produktion neuer Materialkombinationen ermöglichen, sodass eine etwas geringere Geschwindigkeit dazu beitragen könnte, kleinere Auflagen bezahlbar zu machen.
Das vom DLR entwickelte Verfahren sei nicht auf ein Material selektiv, es könne jede Faser oder jedes Polymer verwendet werden, sagt Titze. „Dies ist wichtig, da Prozesse weiter hybridisieren und neue Materialien benötigt werden. Materialien für den 3D-Druck müssen wettbewerbsfähiger werden, sonst wird der 3D-Druck mit Endlosfasern keine große Zukunft haben. Durch die Verwendung von thermoplastischen Pellets oder Granulaten können wir die Kosten deutlich senken und die Geräte passen auf einen kleinen Bauraum, sodass auch kleine Unternehmen sie umsetzen können.“
Das DLR-Institut für Faserverbundwerkstoffe und Adaptive Systeme hat dieses Projekt im Oktober 2019 gestartet und wird es im Januar 2022 abschließen. „Unser Ziel ist es, die Technologie weiter zu miniaturisieren und in einen Druckkopf zu integrieren“, sagt Titze. „Das wäre also eine Direktimprägnierung inline mit dem Druck. Beide Ansätze in die Industrie übertragen wird.“ Er erklärt, dass das DLR als staatliche Non-Profit-Organisation nichts „verkaufen“ werde und deshalb exklusive Rechte. „Unser Ziel ist es, Druckkopflieferanten einzubeziehen, um die Materialpreise auf breiter Front zu senken und die industrielle Anwendung der additiven Fertigung mit Endlosfasern zu erweitern.“
Harz
- Die versteckten Vorteile der Reduzierung der Materialkosten für den 3D-Druck
- 6 Möglichkeiten, die Kosten des 3D-Drucks zu senken
- 5 Trends, die den Markt für 3D-Druckmaterialien im Jahr 2019 prägen
- Reduzierung der Gesamtbetriebskosten
- Kosten von Kohlefaser:Warum sich die Qualität lohnt
- Kohlenstoffkosten:Faktoren, die den größten Einfluss haben
- Die Rolle von Kohlefasern in Luft- und Raumfahrtmaterialien
- Die kontinuierliche Faserherstellung verwischt die Grenze zwischen 3D-Druck und AFP
- 3D-Druckverbundwerkstoffe mit Endlosfasern
- Die besten flexiblen Materialien im 3D-Druck