Wing of Tomorrow-Rippen:One-Shot, thermoplastisch, OOA-Konsolidierung
Das 2015 gestartete Wing of Tomorrow (WOT)-Programm von Airbus hat in den letzten sechs Jahren kostengünstigere Material-, Fertigungs- und Montagetechnologien mit höherem Durchsatz für Single-Aisle-Tragflächen von Verkehrsflugzeugen erforscht (siehe CW frühere Berichterstattung über das WOT-Programm).
Laut Arnt Offringa, Direktor des GKN Aerospace Global Technology Center Netherlands (Hoogeveen), GKN Aerospace (Bristol, Großbritannien) war sehr aktiv im WOT-Programm, einschließlich der Entwicklung eines Flügelholm-Demonstrators, der mittels Resin Transfer Moulding (RTM) und vier Aluminium-Flügelrippen hergestellt wurde. Ein weiterer Technologiedemonstrator, der kürzlich von GKN Aerospace geliefert wurde, umfasste die Entwicklung sowohl einer kostengünstigen thermoplastischen Verbundrippe als auch eines innovativen, modularen Pressensystems für die One-Shot-Herstellung außerhalb des Autoklaven (OOA).
Der Sprung zu Thermoplasten
Im Jahr 2018 begann GKN Aerospace mit internen Diskussionen über Materialien und Fertigungstechnologien, die zur Herstellung von fünf Demonstratoren verwendet werden könnten
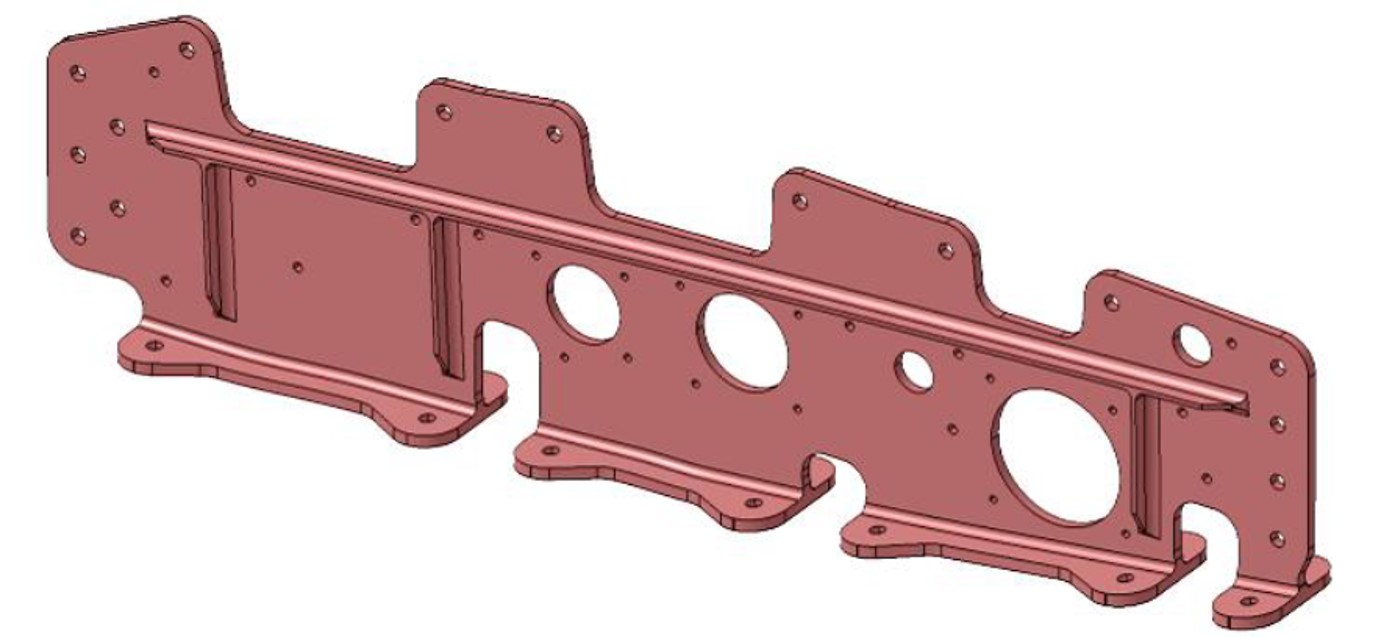
Die Rippe entwerfen. Um ein dünnes, leichtes Teil zu ermöglichen, enthält das Rippendesign (oben) die Stoßverbindungstechnologie von GKN (unten) mit spritzgegossenen Versteifungsfüllern (Mitte, grün dargestellt).
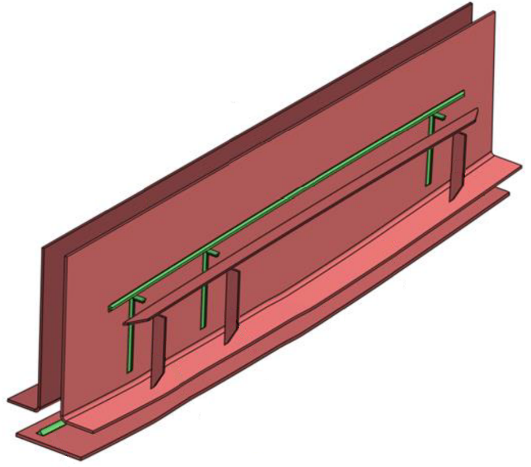
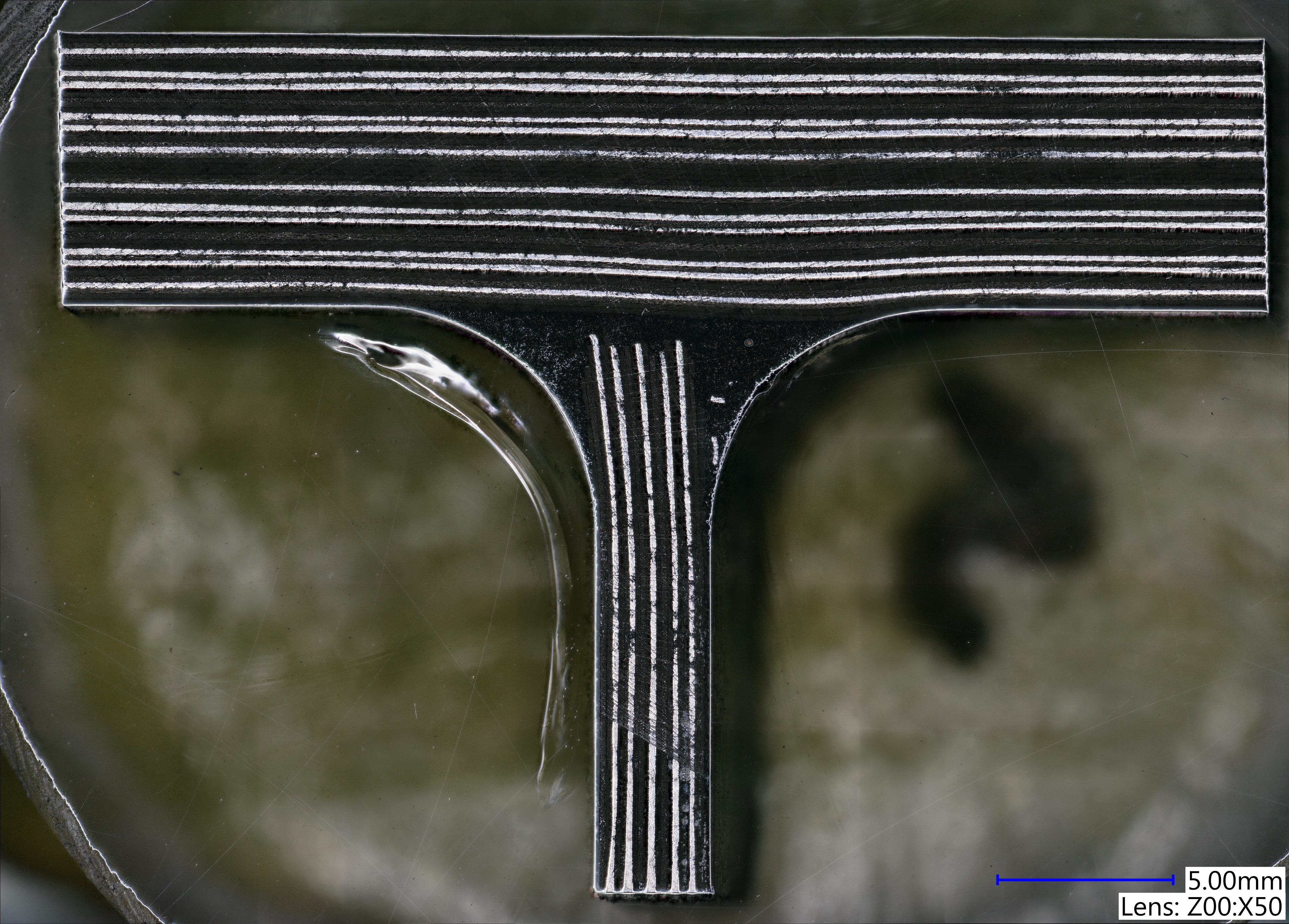
Rippen für das WOT-Programm. GKN Aerospace verglich mehrere Materialoptionen, darunter duroplastische und thermoplastische Verbundwerkstoffe. Aluminium, das traditionelle Material für die Rippen von Verkehrsflugzeugen, wurde ausgewählt, um vier größere Innenrippen herzustellen, aber für die kleinere Außenrippe entschied sich das Unternehmen, eine Verbundwerkstoffoption zu prüfen. Offringa merkt an, dass die Entwicklung einer Verbundrippe, die mit Aluminium konkurrieren kann, ein logischer Schritt ist, da der WOT-Demonstrator ein Verbundflügel sein wird.
„Eine Verbundrippe an einem Verbundflügel ist aus mehreren Gründen von Vorteil“, sagt er. „Erstens bedeutet die Verwendung von Verbundwerkstoffen mit Verbundwerkstoffen, dass es keinen Unterschied in der Wärmeausdehnung zwischen den Materialien gibt, wie bei einer Metallrippe an einem Verbundflügel oder umgekehrt. Zweitens haben Sie keine Probleme oder Bedenken in Bezug auf Korrosion. Verbundwerkstoffe bedeuten auch weniger Gewicht. Nicht zuletzt erleichtert die Verwendung von Verbundwerkstoffen die Inspektion.“
Offringa erklärt, dass typische Metallrippen nach der Montage des letzten Flügels eine visuelle Inspektion durch den Menschen erfordern. Aufgrund der Lage der Rippen im Inneren des Flügels bedeutet dies jedoch, dass große elliptische Luken in die untere Flügelhaut geschnitten werden müssen, damit Menschen den Flügel betreten können, um sie zu inspizieren. „Wenn Sie sich für eine Verbundrippe entscheiden, haben Sie weniger Ermüdung in den Rippen und weniger potenzielle Ermüdungsrisse, die Sie inspizieren müssen. Die Inspektion wird viel einfacher und weniger intensiv, und Sie müssen keine Luken mehr in die Flügelhaut einbauen. Es wird eine durchgehende Flügelhaut sein“, sagt er.
Gewichtsreduzierung, Korrosionsbeständigkeit und weniger invasive Inspektionsvorteile könnten entweder aus duroplastischen oder thermoplastischen Verbundwerkstoffen gewonnen werden. „Wir haben eine interne Studie durchgeführt und Gewicht, Kosten und Industrialisierung untersucht. Nach dem Vergleich der verschiedenen Technologien haben wir uns für Thermoplaste entschieden, da sie das größte Potenzial und den besten Business Case in Bezug auf die Kosten hatten“, sagt Offringa .
Aufgrund der Nähe zum Airbus-Flügeltechnologiezentrum Filton, Großbritannien, in dem der WOT-Demonstrator getestet wird, ist die Niederlassung von GKN Aerospace in Bristol, Großbritannien, der Hauptknotenpunkt der WOT-Arbeit des Unternehmens. Angesichts des Know-hows von GKN Aerospace Netherlands im Bereich Thermoplaste aus seiner Zeit als Fokker Technologies haben sich die beiden Teams von GKN Aerospace jedoch für den Rippen-Demonstrator zusammengeschlossen. „Das Design wurde in Großbritannien gemacht, aber die Fertigungsentwicklung wurde in den Niederlanden durchgeführt, daher war es eine wirklich schöne Zusammenarbeit zwischen den verschiedenen Teams bei GKN Aerospace“, sagt Offringa.
Sue Partridge, Leiterin des WOT bei Airbus, bemerkt:„Die Zusammenarbeit mit Partnern ist ein wichtiger Aspekt des Wing of Tomorrow-Programms. Durch die Kombination unserer Ressourcen können wir Lösungen entwickeln, die die Fähigkeiten unserer beiden Unternehmen für ein besseres Ergebnis nutzen.“
Für die an Airbus gelieferten WOT-Rippen verwendete GKN Aerospace APC Kohlefaser/Polyetherketonketon (PEKK-FC)-Bänder von Solvay (Brüssel, Belgien), die auf der schnell kristallisierenden Formulierung Novaspire PEKK-FC (FC) des Unternehmens basieren. Offringa stellt fest, dass das niedrigschmelzende Carbonfaser/Polyaryletherketon (PAEK)-Material von Toray Advanced Composites (Morgan Hill, Kalifornien, USA) ebenfalls als Option für zukünftige Rippenstrukturen evaluiert wird.
Entwurf einer Flügelrippe der nächsten Generation
Es gibt mehr als 20 Rippen auf einem typischen Single-Aisle-Flugzeugflügel. Die Demonstratorrippe aus thermoplastischem Verbundwerkstoff ist die 14. auf dem Demonstratorflügel; die anderen werden alternative Materialien und Verfahren demonstrieren.
Thermoplastische Verbundrippen werden oft durch Stanzformen für kleine Flugzeuge hergestellt, sagt Offringa. GKN Aerospace schloss jedoch das traditionelle Stanzformen als Option für die WOT-Rippe aus, da die Tragflächen von Verkehrsflugzeugen selbst bei schmalen Körpern wie dem WOT-Demonstrator sehr hohen Druck- und Zugbelastungen ausgesetzt sind.
„Wenn Sie im herkömmlichen Sinne eine thermoplastische Rippe stanzen würden, müssten Sie eine sehr dicke Rippe mit einem dicken Steg herstellen, um sie stärker zu machen, damit sie den auf sie einwirkenden Kräften standhalten kann“, sagt Offringa. und dies ist angesichts der Gewichtsreduktionserfordernisse nicht bevorzugt. Außerdem wäre es durch das Stanzformen nicht möglich, eine doppelseitige untere Flanschkomponente an der Rippe zu erzeugen, wo das Teil mit der unteren Flügelhaut verbunden ist; eine zusätzliche Komponente müsste hergestellt und mit dem Rest der Rippe verschraubt werden. GKN Aerospace benötigte einen Herstellungsprozess, der dem Team mehr Flexibilität für das Design ermöglichte.
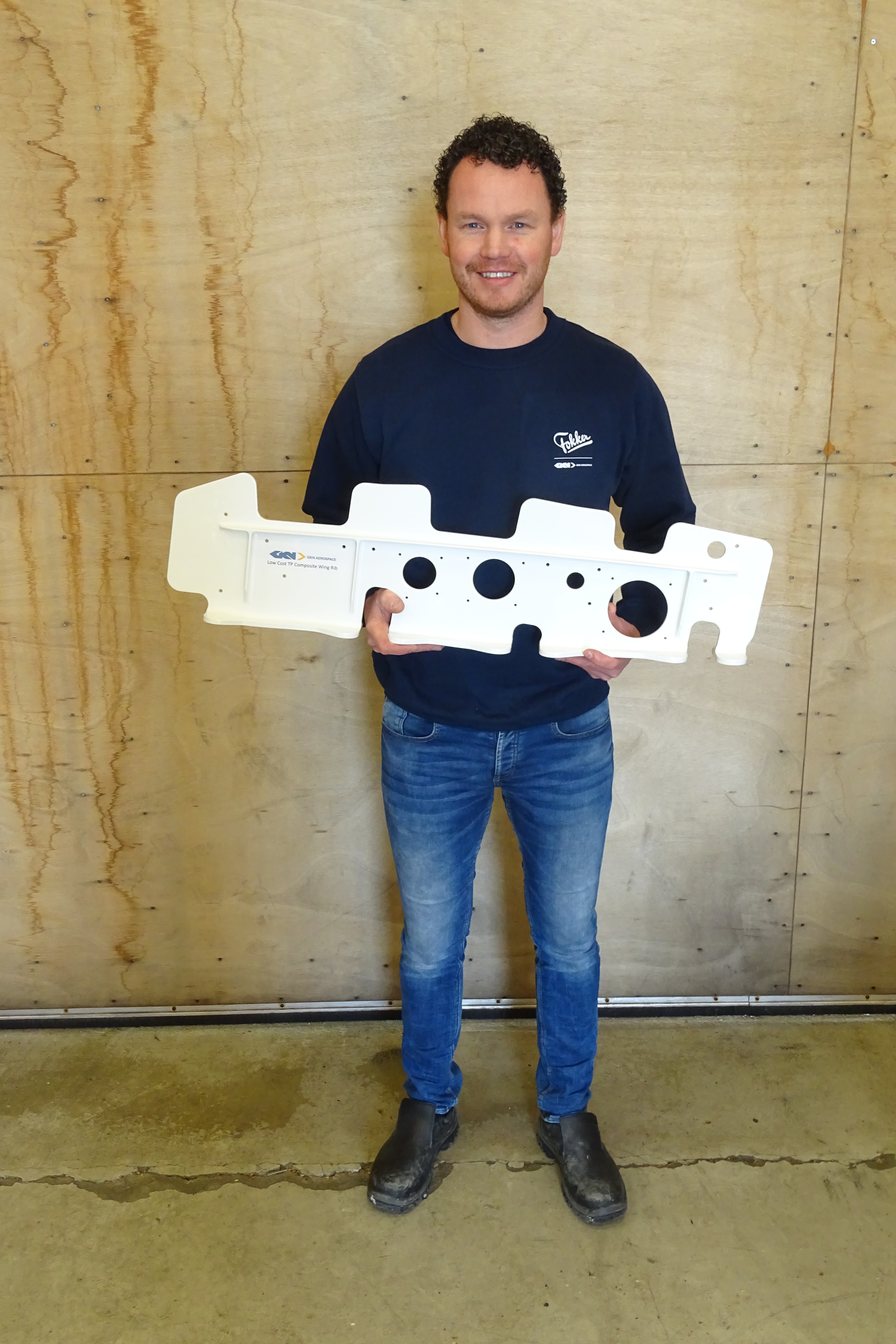
Die 90 Zentimeter lange, 24 Zentimeter hohe thermoplastische Rippe von GKN Aerospace verfügt über einen vertikalen Steg und einen bidirektionalen 8 Millimeter dicken Flansch, der sich von der Unterseite der Rippe erstreckt. Um den Gewichtsanforderungen gerecht zu werden, ist die Bahn nur 7 Millimeter dick. Um ein Knicken zu verhindern und die Steifigkeit zu erhöhen, wird der Steg durch 3 Millimeter dicke Versteifungselemente unter Verwendung der Stoßverbindungstechnologie von GKN Aerospace verstärkt, die flache Versteifungsvorformen und spritzgegossene „Füllstoffe“ verwendet, um eine starke, kontinuierliche Verbindung zu schaffen (siehe „Thermoplastische“ primäre Flugzeugstrukturen machen einen weiteren Schritt nach vorne“, um mehr über den Einsatz dieser Technologie auf einer Gulfstream-Rumpfplatte zu erfahren, die mit Kohlefaser/PEKK-FC-Bändern von Solvay hergestellt wurde).
„Wir wussten, dass wir, wenn wir diese Form aus Verbundwerkstoffen herstellen und sie robust machen könnten, ein sehr leichtes Design mit der gewünschten Gewichtsreduzierung haben würden. Aber das Problem war, wie kann man eine so komplizierte Form kostengünstig und mit hohen Raten herstellen? Hier setzen wir unsere Anstrengungen ein, um dieses neue Produkt zu entwickeln“, sagt Offringa.
Einstufige OOA-Fertigung
Der Prozess baut auf Technologien auf, die GKN Aerospace zuvor für das TAPAS-Projekt (Thermoplastische Affordable Primary Aircraft Structure) und für eine Rumpfplattenentwicklung für Gulfstream verwendet hat, die die Stoßverbindungstechnologie des Unternehmens verwendet. Für die WOT-Rippe hat GKN Aerospace einen OOA, einstufigen Konsolidierungsprozess entwickelt. „Wir haben unsere bisherige Arbeit auf die nächste Stufe gehoben, indem wir zum ersten Mal den Autoklaven verlassen haben“, bemerkt Offringa.
Zuerst werden unidirektionale (UD) thermoplastische Bänder auf die richtige Breite geschnitten, und ein Laminator wird verwendet, um die flachen Elemente zu zwei L-förmigen Bahnvorformlingen vorzuformen. Die Stegpreforms, ein flacher Preform für den Flansch sowie kleinere Preforms und spritzgegossene Füllelemente, aus denen die Stringer bestehen, werden alle in ein Werkzeug geladen, das in einer modularen Co-Consolidation-Presse platziert wird, die einem Resin Transfer Moulding ähnelt (RTM) drücken. Die Presse schließt und ein Blasensystem wird verwendet, um Druck aus horizontaler und vertikaler Richtung zu erzeugen und den Druck in einem Autoklaven zu simulieren. Ein integriertes Widerstandsheizsystem bringt den Verbundstoff kurz auf Schmelztemperatur, bevor er zur Konsolidierung abgekühlt wird.
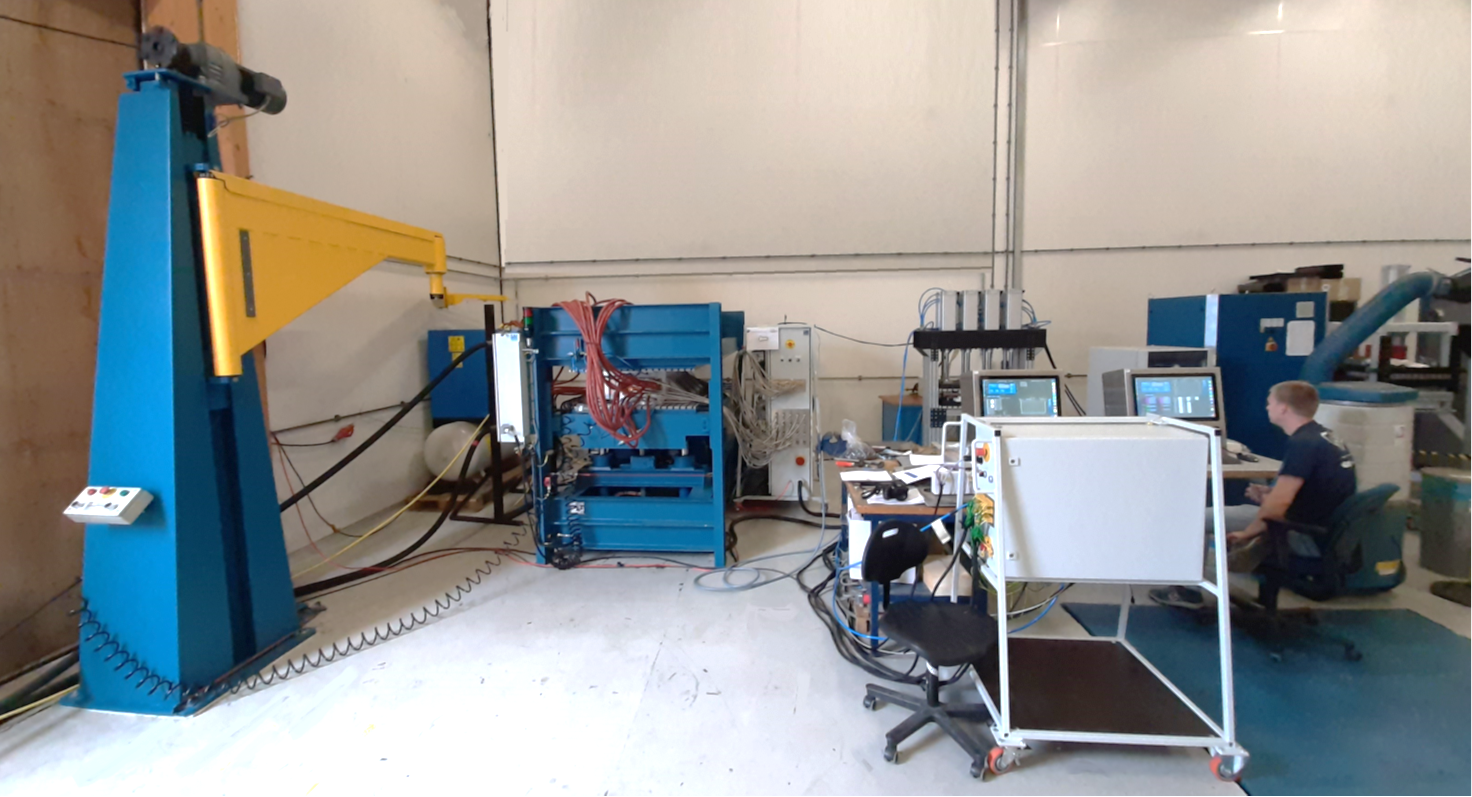
„Wir haben die meiste Entwicklungsarbeit in die Abstimmung und Optimierung der Werkzeuge gesteckt“, sagt Offringa. Das System ist modular aufgebaut; Die Werkzeuge können ausgetauscht werden, um Rippen mit unterschiedlichen Abmessungen oder andere Arten von Teilen aufzunehmen, während das gleiche Heiz- und Kühlsystem beibehalten wird. Obwohl für diese Rippen nicht erforderlich, kann die im Technologiezentrum von GKN Aerospace entwickelte Presse bis zu 6 Meter lange Teile aufnehmen, die auch andere Platten oder Träger enthalten können.
Bei der Verarbeitung von Thermoplasten ist das Prozessleitsystem entscheidend. Thermoplaste schmelzen bei höheren Temperaturen als Duroplaste und müssen in einem kontrollierten, konsistenten Prozess gekühlt werden, um den Verzug zu minimieren und die Kristallinität zu maximieren. „Es ist sehr wichtig, den genauen Prozess von Anfang bis Ende zu kontrollieren“, sagt Offringa. „Das Thermomanagement des Heizkreislaufs ist sehr wichtig.“ (Weitere Informationen zu den Problemen und der Bedeutung der Prozesskontrolle bei der Verwendung von Thermoplasten finden Sie in der Seitenleiste „Thermoplastische (TP) Umformung“ in diesem Artikel).
Spezielle Werkzeugfunktionen werden verwendet, um ein leichtes Lösen der dünnen integrierten Versteifungen vom Werkzeug zu ermöglichen. Das entformte Teil hat eine nahezu Endform und wird dann beschnitten, um das fertige Teil zu bilden. Von Werkzeug rein zu Werkzeug raus dauert der gesamte Vorgang ca. 45 Minuten. Das bedeutet, dass mit einer Presse etwa 15 Flügelrippen in einer 8-Stunden-Schicht hergestellt werden können.
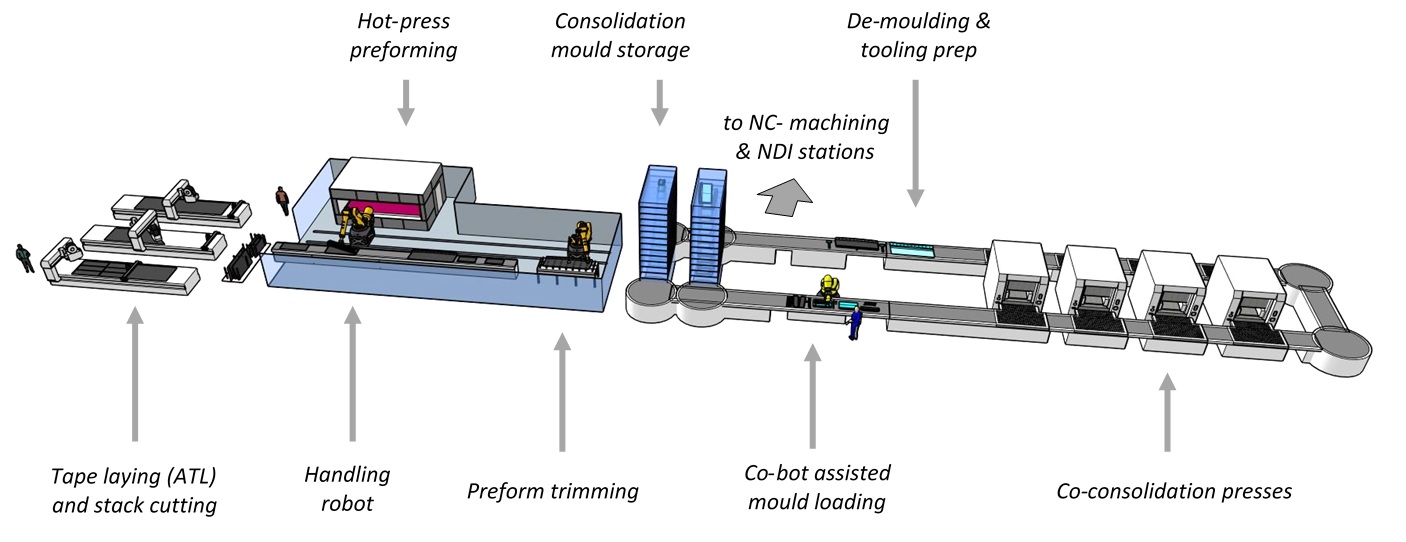
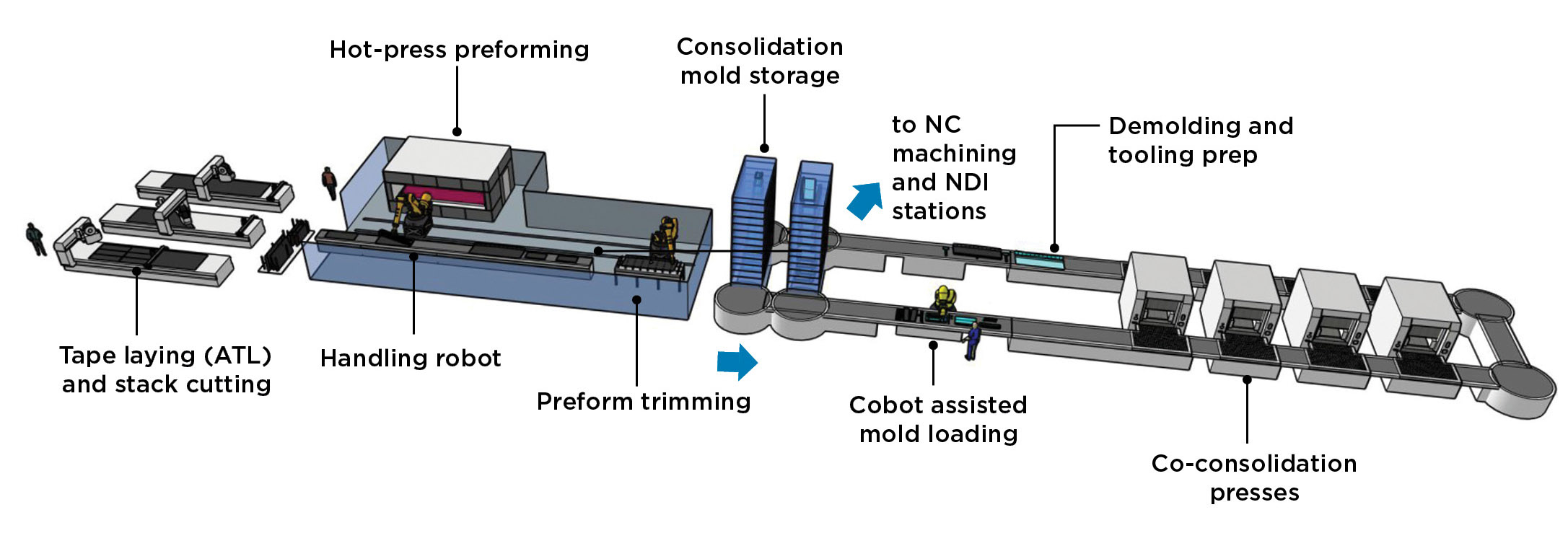
„Am Ende ist es ein einfacher Herstellungsprozess“, bemerkt Offringa. „Wir machen viele Dinge gleichzeitig:Preforms mit unterschiedlichen Formen zusammen zu konsolidieren, die Unterseite der Rippe mit einem bidirektionalen Flansch zu versehen und gleichzeitig das Steg mit der Stumpfstoßtechnologie zu versteifen. Letztendlich nehmen wir aber alle Elemente des Materials, legen sie in ein Werkzeug und erstellen ein homogenes Teil in einem Arbeitsgang.“
Tests, Lieferung und mehr
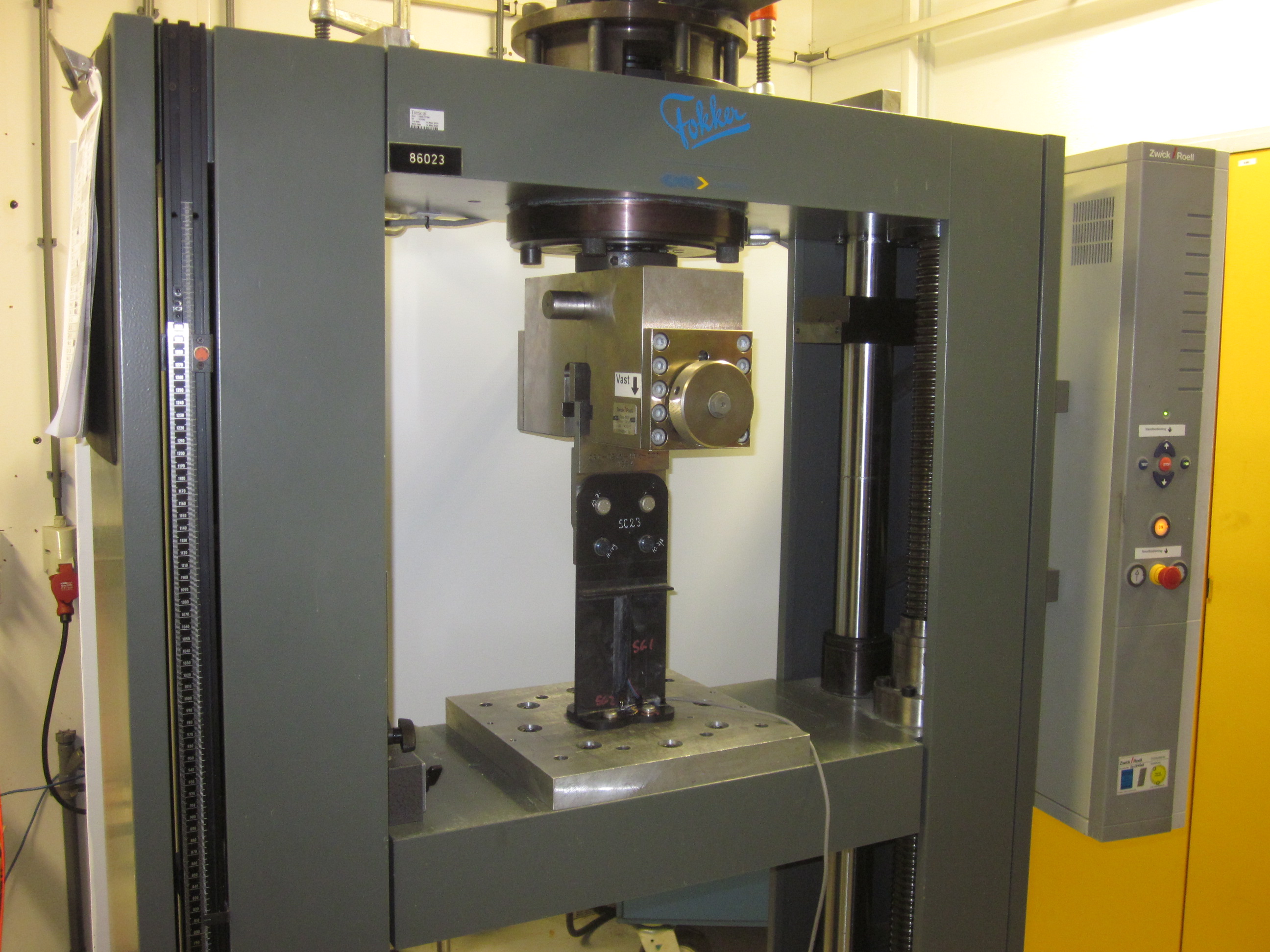
Testen. Unterkomponenten wurden in den GKN-Werken in Isle of Wight und Hoogeveen getestet, um die Anforderungen an die Zug- und Druckfestigkeit zu erfüllen.
Ende 2019 wurden Rippenteilkomponenten in den Anlagen von GKN Aerospace auf der Isle of Wight und in Hoogeveen getestet, und Offringa sagt, dass sie die Zug- und Druckbelastungsanforderungen „mit großem Abstand“ erfüllt haben. Er fügt hinzu:„Es ist stark, es ist hart, es ist einfach herzustellen. Dies ist ein Konzept, das genau so ausgefallen ist, wie wir es uns erhofft hatten.“ Im Vergleich zu einer Aluminiumversion bietet die thermoplastische Verbundversion laut Offringa erhebliche Gewichtseinsparungen und ist kostengünstig.
Das Unternehmen hat Airbus drei Rippen geliefert, von denen eine auf dem WOT-Demonstrator montiert und getestet wird. GKN Aerospace arbeitet weiterhin an der Optimierung seiner Prozesse und Materialien für kommerzielle Luftfahrtrippen, sowohl für Wing of Tomorrow als auch darüber hinaus.
Harz
- Durchgehend faserverstärkter thermoplastischer Verbundwerkstoff vollständig aus natürlichen Ressourcen hergestellt
- Solvay erweitert die Kapazität von thermoplastischen Verbundwerkstoffen
- Fraunhofer nimmt automatisierte Engel-Produktionszellen für F&E thermoplastischer Verbundwerkstoffe in Betrieb
- DLR-Institut für Konstruktion und Konstruktion steigert Reifegrad von thermoplastischen Rumpfstrukturen aus Verbundwerkstoff
- Solvay schließt die Installation der Anlage in South Carolina ab und erweitert die US-Kapazität für thermoplastische Verbundwerkstoffe
- INEOS Styrolution baut Produktionsstätte für thermoplastischen Verbundwerkstoff StyLight
- Xenia führt thermoplastische CF/PP-Composite-Compounds ein
- Thermoplastische Verbundrohre auf dem Vormarsch in der Tiefsee
- NIARs NCAMP-qualifizierender TenCate thermoplastischer Verbundwerkstoff
- TenCate feiert den Zusammenschluss des Konsortiums für thermoplastische Verbundwerkstoffe in Brasilien