Große Verbundabdeckungen schützen viel Wasser
Die Wasserspeicherung und -lieferung in Bogotá, Kolumbien, ist wie in jedem großen Stadtgebiet kompliziert. Die Herausforderung besteht nicht in der Versorgung, denn die Stadt mit etwa 9 Millionen Einwohnern erhält jedes Jahr 824 Millimeter Regen und der Fluss Bogotá fließt durch die Stadt. Die Herausforderung besteht darin, dieses Wasser aufzufangen, aufzubereiten und dann so zu speichern, dass es trinkbar bleibt und bei Bedarf für Anwohner und Unternehmen verfügbar ist. Zu diesem Zweck hat Empresa de Acueductos y Alcantarillados (Unternehmen für Aquädukte und Kanalisation, EAAB, Bogotá) im Laufe der Jahre eine Reihe von 59 Tanks in der ganzen Stadt gebaut, um aufbereitetes Wasser zu speichern und die Versorgung der Kunden sicherzustellen.
Einige dieser Tanks sind echte Tanks – vollständig geschlossen, um das Wasser vor äußeren Einflüssen zu schützen. Andere, viele von ihnen älter, sind massive Betonbecken, die mit einer Reihe abnehmbarer Abdeckungen vor den Elementen geschützt sind. Ein solcher Tank, Casablanca genannt, befindet sich im Stadtteil Ciudad Bolivar im südlichen Teil von Bogotá und versorgt eine Bevölkerung von etwa 3 Millionen Menschen. Casablanca, der größte Wasserspeicher im EAAB-Netzwerk und der größte Wasserspeicher in Kolumbien, misst 144 Meter (472 Fuß) lang x 110 Meter (361 Fuß) breit x 9 Meter tief und hat eine Kapazität von 143.000 Kubikmetern ( 38 Millionen Liter) Wasser. Der Tank wird von einem Betonteiler geteilt, der in seiner Mitte verläuft, so dass das Wasser in zwei gleichen Abschnitten gespeichert wird.
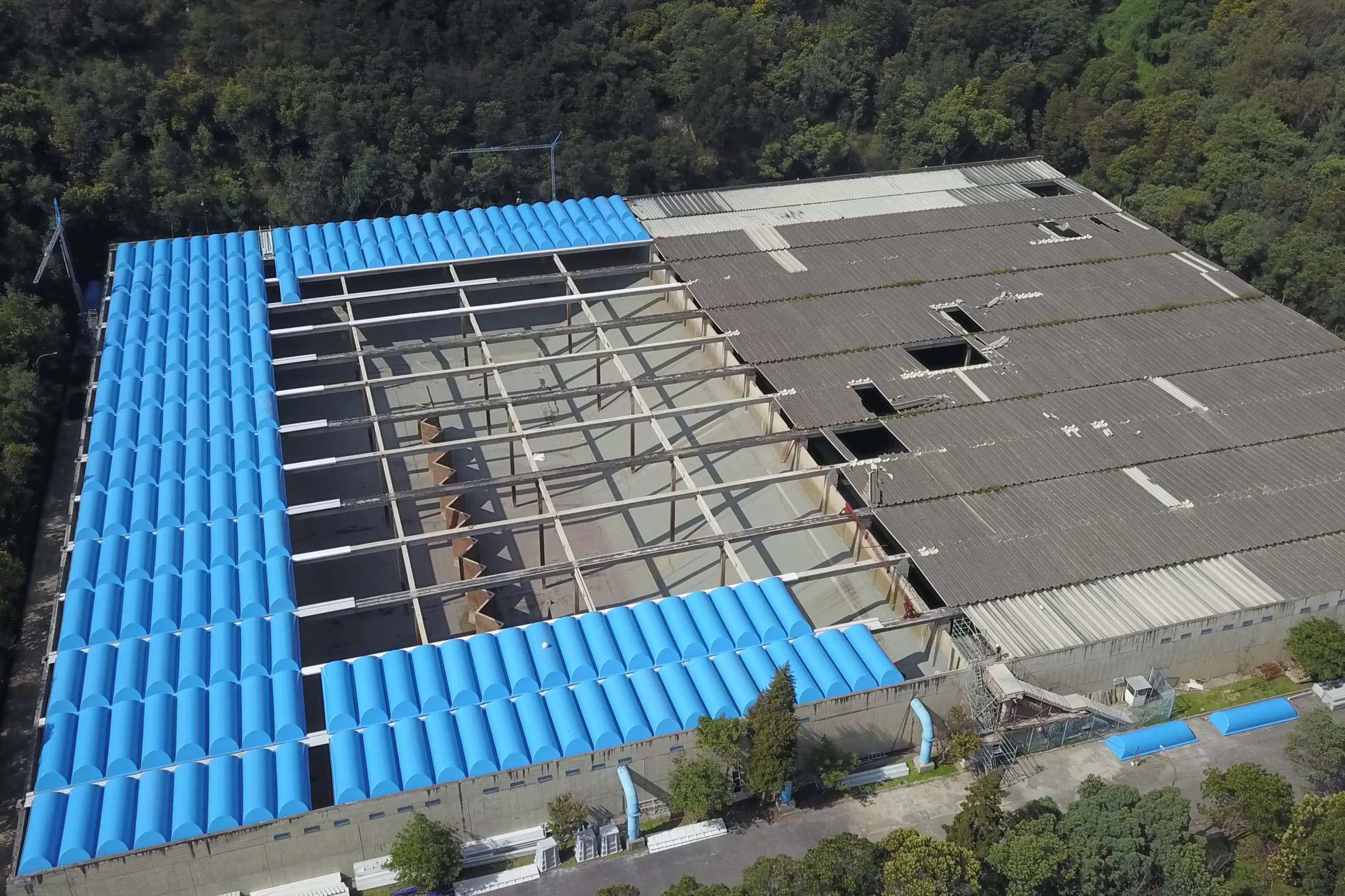
Die Pflege des 66-jährigen Casablanca ist keine leichte Aufgabe. Im Jahr 2009 wurde entdeckt, dass durch Risse im Betonboden des Tanks 360.000 Liter (95.000 Gallonen) Wasser pro Stunde entweichen konnten . Betonreparaturen mit Polyurea-Beschichtung reduzierten die Leckage auf null. Casablanca hatte jedoch noch ein Problem oberhalb des Betons. Das Wasser im Tank wurde durch eine Reihe von Abdeckungen geschützt, die aus einer Mischung aus Beton und Asbest bestanden, was eine erhebliche Bedrohung für die Wasserqualität und die menschliche Gesundheit darstellte. Auch die alten Abdeckungen waren störanfällig und teuer in der Wartung. EAAB musste die alten Abdeckungen durch eine sicherere, leichtere und haltbarere Alternative ersetzen.
Große Cover und viele davon
EAAB entschied sich für eine Verbundwerkstofflösung für die Abdeckungen, wurde jedoch sofort durch den Umfang des Projekts herausgefordert. Casablanca wird von einer Reihe von Betonpfeilern durchzogen, die ein Netzwerk von Balken tragen, auf denen die Decken ruhen. Diese Träger haben einen Abstand von etwa 7,2 Metern (23,6 Fuß), daher müssten die neuen Abdeckungen selbsttragend sein und diese Spannweite abdecken, um die vorhandene Infrastruktur zu nutzen. EAAB schlug vor, solche Abdeckungen mittels Light Resin Transfer Moulding (LRTM) herzustellen. Die Herausforderung? Verbundstrukturen dieser Größe, die für diese Anwendung benötigt werden, wurden noch nie über LRTM in Kolumbien hergestellt. Viele Verarbeiter waren einfach nicht in der Lage, das Projekt zu übernehmen.
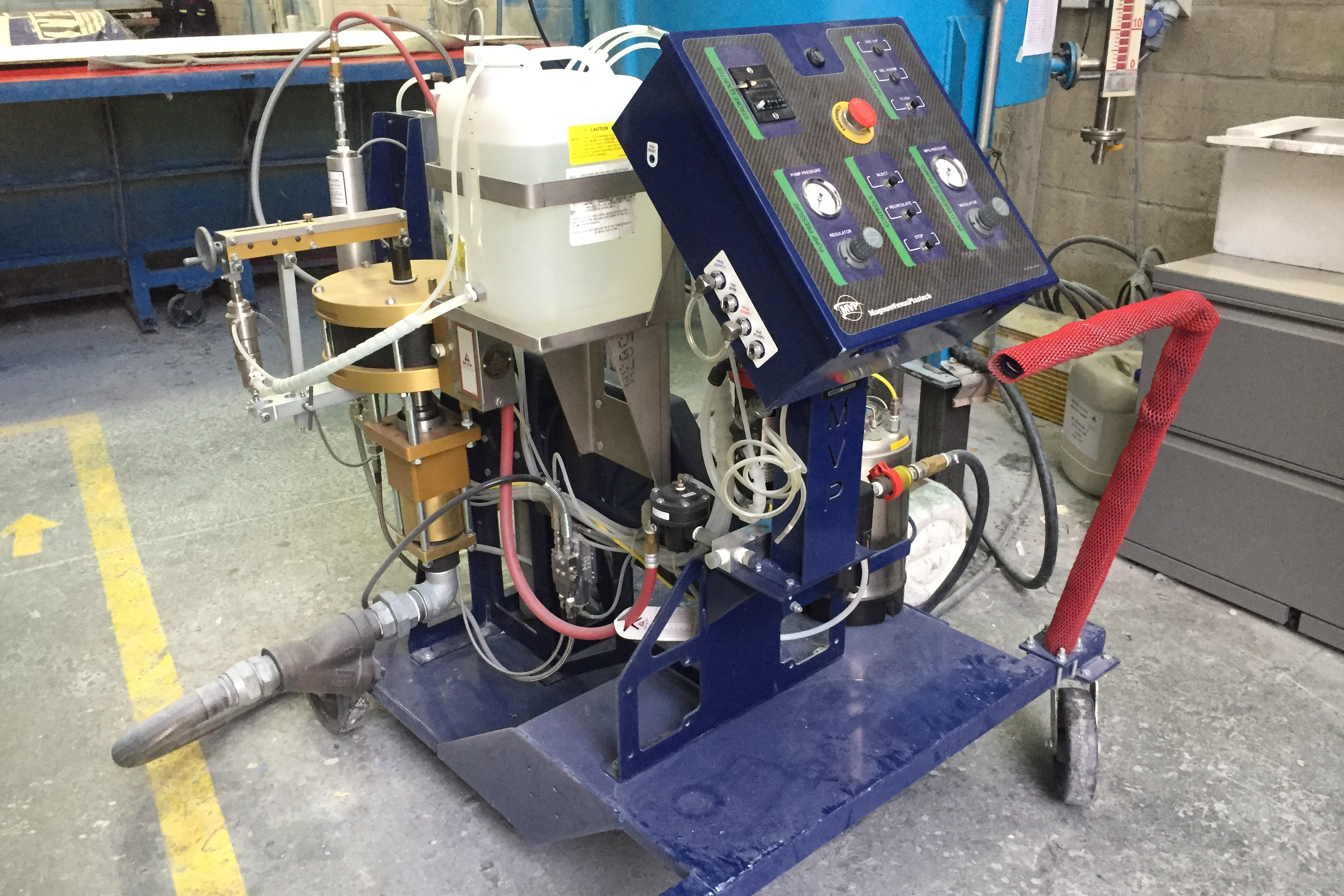
Die Ausnahme war Innovative Engineering Solutions oder Soling, ein Hersteller von Verbundwerkstoffen mit Sitz in La Estrella, Antioquia, Kolumbien, südlich von Medellín. Soling wurde 2014 von Javiar Moreno gegründet, der mehrere Unternehmen zur Herstellung von Verbundwerkstoffen in und um Kolumbien besitzt und betreibt. Rodrigo Vergara, Engineering Coordinator bei Soling, sagt, dass die Größe der Abdeckungen für viele Hersteller kein Grund war. „Damit hatte in Kolumbien aufgrund der Größe des Teils niemand Erfahrung“, stellt er fest. „Es ist das größte in Kolumbien hergestellte Verbundbauteil.“ Für Moreno war jedoch die Größe der Cover eine interessante Herausforderung. „Für unseren Besitzer [Moreno]“, sagt Vergara, „wurde ein Traum wahr. „Unmöglich“ ist ein Wort, das er nicht versteht. Er sagte:‚Wir werden das machen!‘ Ich sagte ‚OK!‘.“
Soling schlug eine spezifische Lösung für das Casablanca-Projekt vor:Eine Serie von 840 gewölbte, rechteckige Verbundkonstruktionen, die jeweils 7,6 Meter lang und 2,4 Meter breit sind (24,9 x 7,9 Fuß). Das halbkreisförmige Kuppeldesign wurde gewählt, sagt Vergara, weil „die geometrische Form, die den größten mechanischen Widerstand hat, ein Umfang ist. Dies war der Hauptfaktor, um sicherzustellen, dass die Abdeckungen selbsttragend waren. Auf der anderen Seite mussten wir den einfachsten Weg finden, sie vom Produktionsstandort zum Montageort zu transportieren, der 260 Meilen entfernt war.“
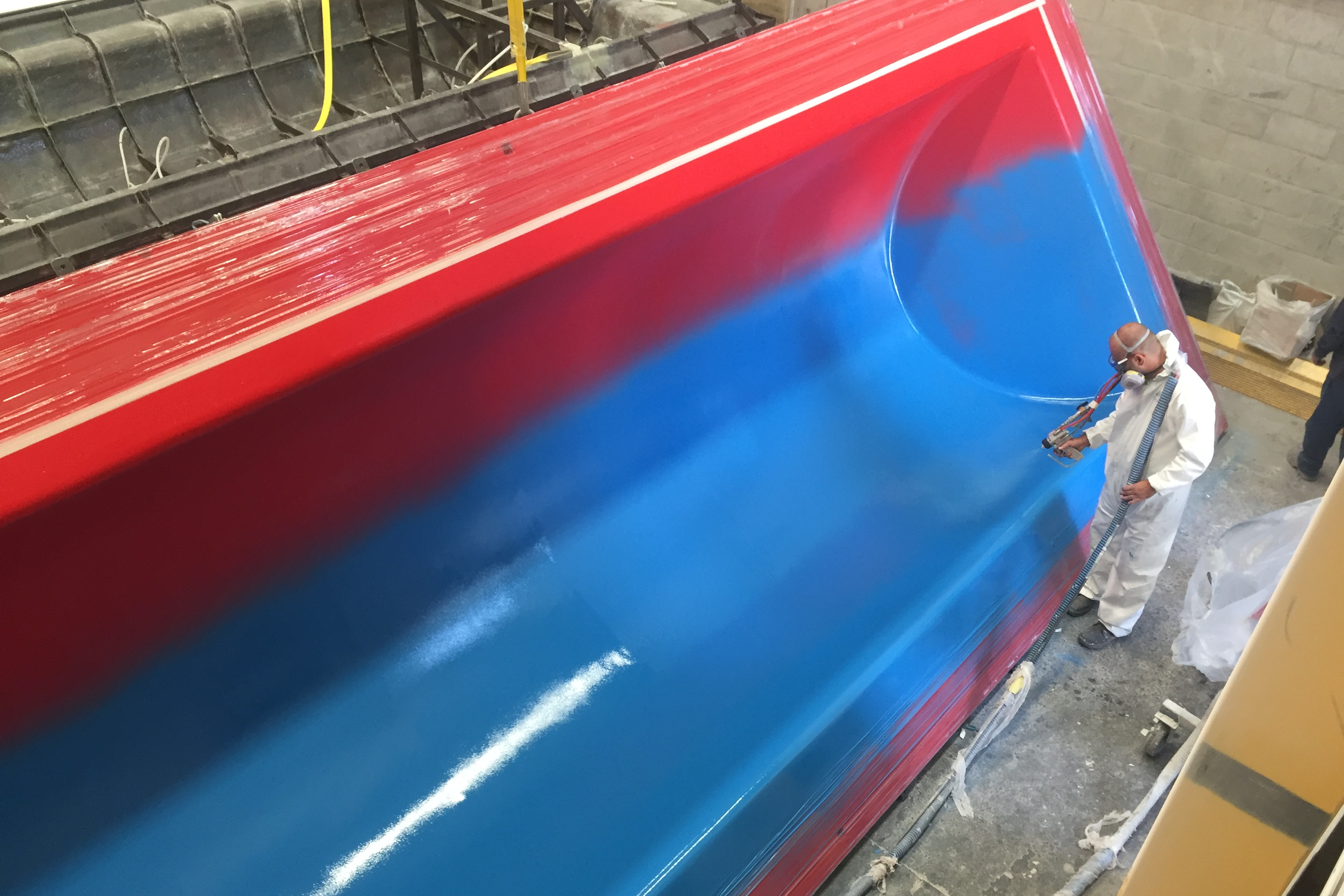
Die Bezüge würden über LRTM mit einem blauen Gelcoat auf der Außenseite und einem weißen Gelcoat auf der Innenseite gemäß EAAB-Spezifikation hergestellt. Bestehend aus Glasfasergewebe und einem Polyesterharz, würde die Abdeckung mit einer Oberfläche von 28,5 Quadratmetern (207 Quadratfuß) 320 Kilogramm (705 Pfund) wiegen, wovon 208 Kilogramm Harz wären. Mit einem Design in der Hand und der Verpflichtung, die Bezüge zu liefern, machten sich Vergara und Soling an die Arbeit.
Die perfekte Deckung aufbauen
Soling hat das Projekt Casablanca natürlich nicht ohne Hilfe übernommen. Die Zusammenarbeit mit dem Unternehmen war ein Liefernetzwerk, das einen Händler, einen Materiallieferanten und einen Ausrüstungslieferanten umfasste. Der Distributor, Minepro SAS (Medellín, Kolumbien), leistete technische Unterstützung und arbeitete mit dem Ausrüstungslieferanten Magnum Venus Products (MVP, Knoxville, Tennessee, USA) zusammen, der Pumpen und Hilfsgeräte für den LRTM-Prozess lieferte. Die Materiallieferanten sind Andercol (Medellín), das die Polyesterharzmatrix, Gelcoats und technischen Support lieferte, und Jushi (Tongxiang City, China), das die E-Glasfasergewebe lieferte.
Die Fertigung beginnt natürlich mit dem Werkzeugbau. Die Frage war, wie viele Formen das Projekt benötigt. Um dies zu ermitteln, musste Soling laut Vergara zunächst das Herstellungstempo ermitteln, um die Lieferanforderungen von EAAB zu erfüllen. Dies wiederum wurde durch die Anforderungen auf der Baustelle beeinflusst. Um eine potenzielle Verschmutzung der Wasserversorgung während der Installation der neuen Abdeckungen zu vermeiden, stimmte EAAB zu, die Hälfte von Casablanca, über die die Abdeckungen geliefert und abgelassen wurden, zu leeren. Die Reduzierung der Wasserspeicherkapazität von Casablanca um die Hälfte stellt eine Herausforderung dar. Daher musste EAAB die Lieferung und Installation so schnell wie möglich durchführen.
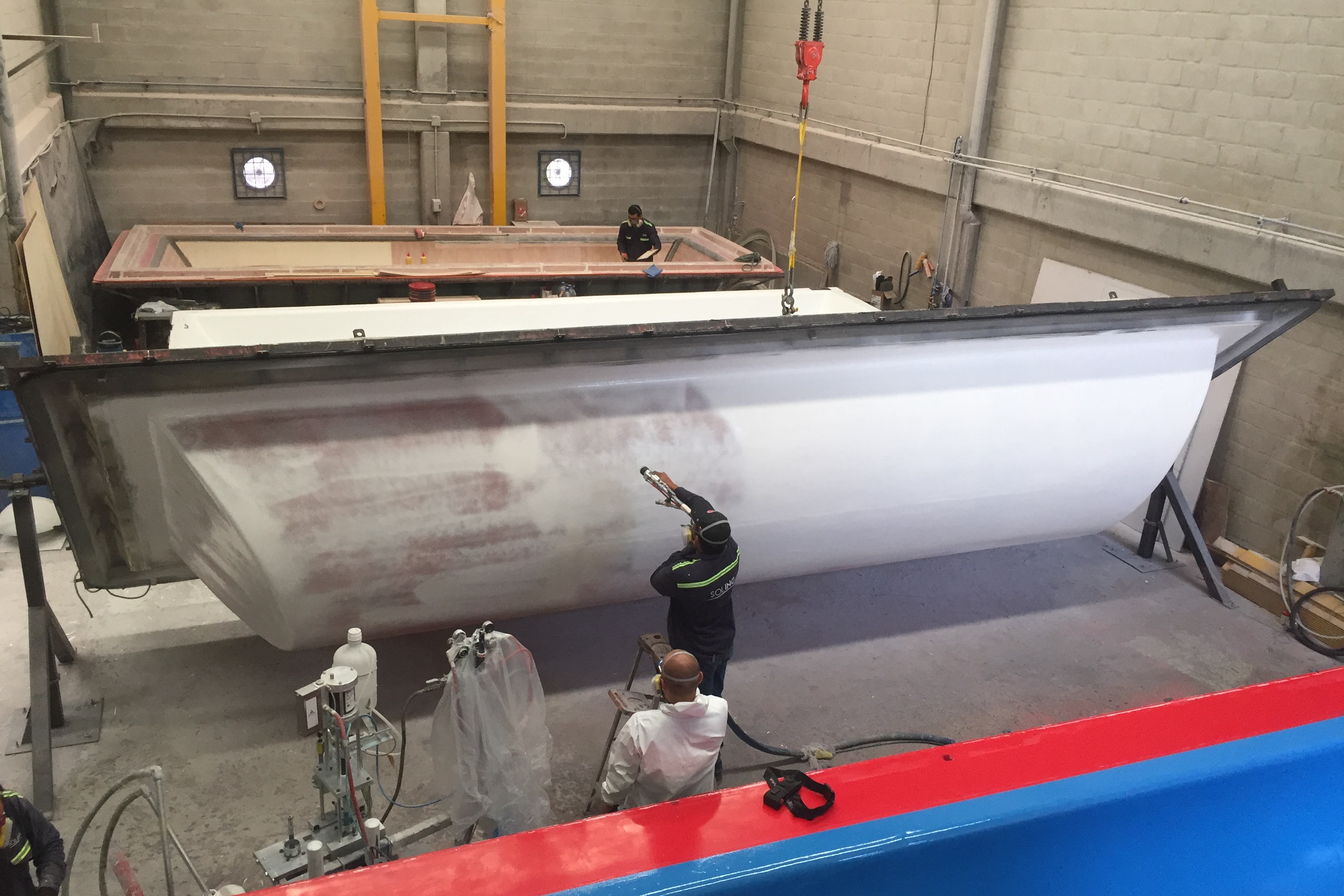
Soling, der mit EAAB zusammenarbeitet, erklärt Vergara, hat sich auf einen Produktionsplan festgelegt, der jeden Tag sechs Umschläge liefern würde. In einer Anlage mit drei Acht-Stunden-Schichten pro Tag waren dafür zwei Formen erforderlich, von denen jede eine Abdeckung pro Schicht herstellen konnte. Die Formen, sagt er, wurden im eigenen Haus gebaut und bestanden aus einem männlichen/weiblichen Glasfaserverbund-Design, das von einer Stahlträgerstruktur unterstützt wurde.
Mit dem Bau von Formen begann Soling dann damit, festzulegen, wie die Kuppeln speziell hergestellt werden sollten. In Zusammenarbeit mit Minepro und MVP sagte Vergara, dass beschlossen wurde, jede Form über zwei Harzeinspritzöffnungen mit einem Vakuumanschluss zu versorgen. Für die Harzinjektion empfahl MVP die Verwendung seiner Patriot Innovator-Pumpeneinheit für das Hochvolumen-Resinspritzpressen (RTM), die in der Lage ist, die für jede Abdeckung erforderliche große Harzmenge zu fördern. MVP lieferte auch seine Turbo Autosprue-Ventile sowie Universalkupplungen, Dichtungen und Formzubehör.
Um mit der Produktion einer Abdeckung zu beginnen, so Vergara, wurde die Matrize der Form mit weißem Gelcoat und die Patrize der Form mit blauem Gelcoat besprüht. Wie bereits erwähnt, wurden beide Gelcoats von Andercol geliefert. Als nächstes wurden die von Jushi gelieferten E-Glasmatten und -stoffe von Hand in die weibliche Hälfte der Form gelegt. Anschließend erfolgte das Absenken der Patrize der Form in die Matrize mittels Kran, wobei die beiden Hälften zusammengeklemmt wurden. Nachdem das Vakuum angelegt wurde, begann die Harzinjektion. Vergara sagt, dass die Injektion jeder Abdeckung in etwa 40 Minuten abgeschlossen war, gefolgt von einer Aushärtung bei Raumtemperatur. Nachdem jede Abdeckung entformt wurde, wurde sie auf die endgültigen Abmessungen zugeschnitten und in die Oberfläche des Abdeckungsflansches wurden Zuführungskanäle zur Regenwasserminderung geschnitten.
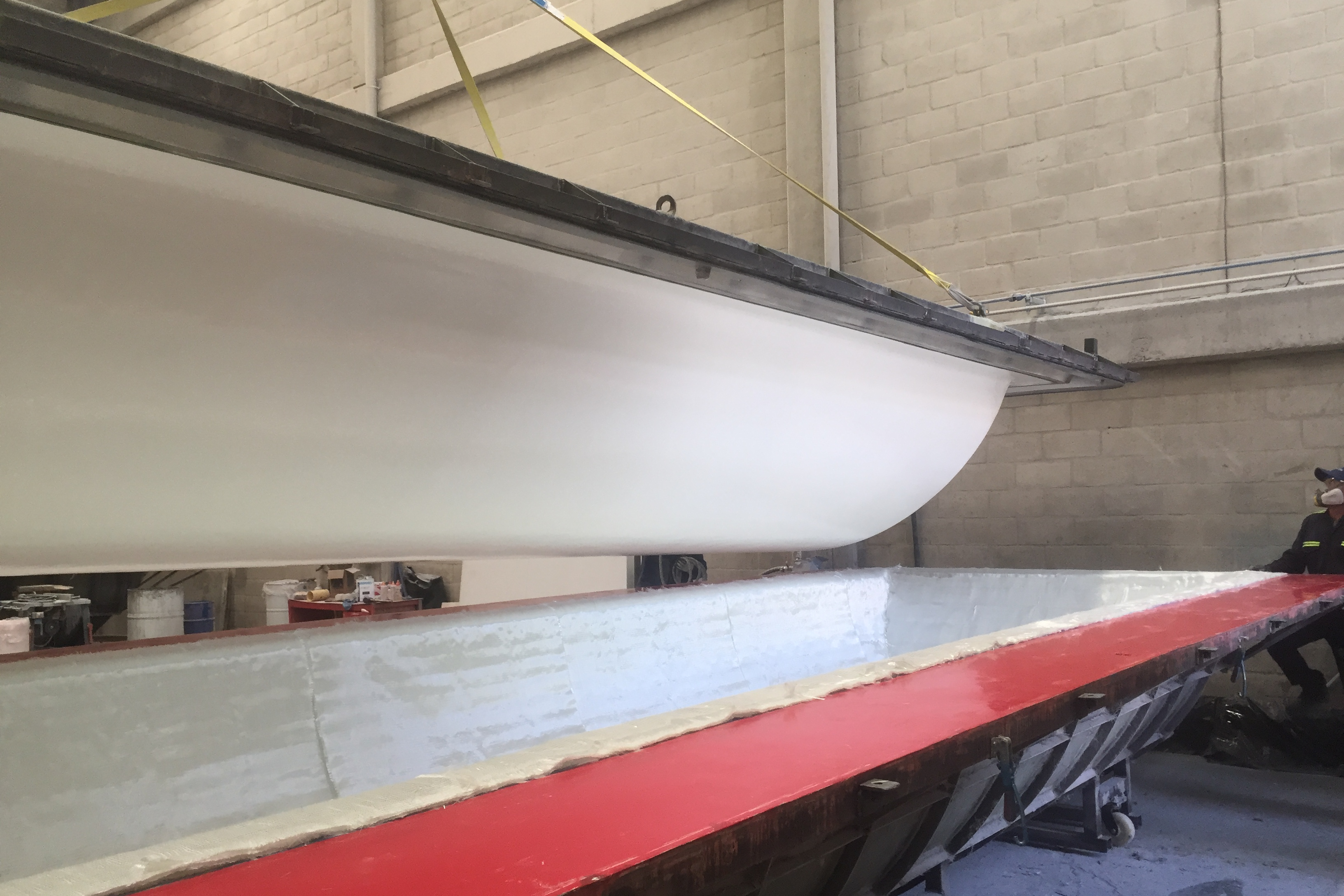
Laut Vergara stellten die schiere Größe der Bezüge in Kombination mit strengen Gewichts- und Maßanforderungen die größte Herausforderung für ihre Herstellung dar. Die Bestimmung der Position der Einspritzöffnung und die Verwaltung des Einspritzzeitpunkts erforderten viel Versuch und Irrtum und die Beratung mit technischen Experten. Letztendlich entschied sich Soling jedoch, so Vergara, für einen Herstellungsprozess, der sich als äußerst wiederholbar und zuverlässig erwies.
„Die größte Herausforderung war das Gewicht der Elemente, die wir installieren wollten, da wir die Tragfähigkeit der bestehenden Konstruktion nicht überschreiten konnten“, sagt Vergara. „Dafür mussten alle Teile die gleichen Eigenschaften haben, sowohl in der Geometrie als auch im Gewicht. Die einzige Möglichkeit, diese Bedingungen zu gewährleisten, bestand darin, einen Prozess zu verwenden, der die Wiederholbarkeit garantiert.“
Fertige Abdeckungen wurden die 418 Kilometer (260 Meilen) von Solings Werk in der Nähe von Medellín zur Baustelle Casablanca in Bogotá verschifft und dann per Kran montiert, auf die Tragkonstruktion abgesenkt und von Arbeitern positioniert, die auf den Balken standen, auf denen die Abdeckungen ruhen würden. Obwohl die Abdeckungen nicht mechanisch an den Stützstrukturen befestigt sind, können sie laut Vergara auch nicht bewegt oder entfernt werden, es sei denn, es ist etwas sehr Ernstes passiert.
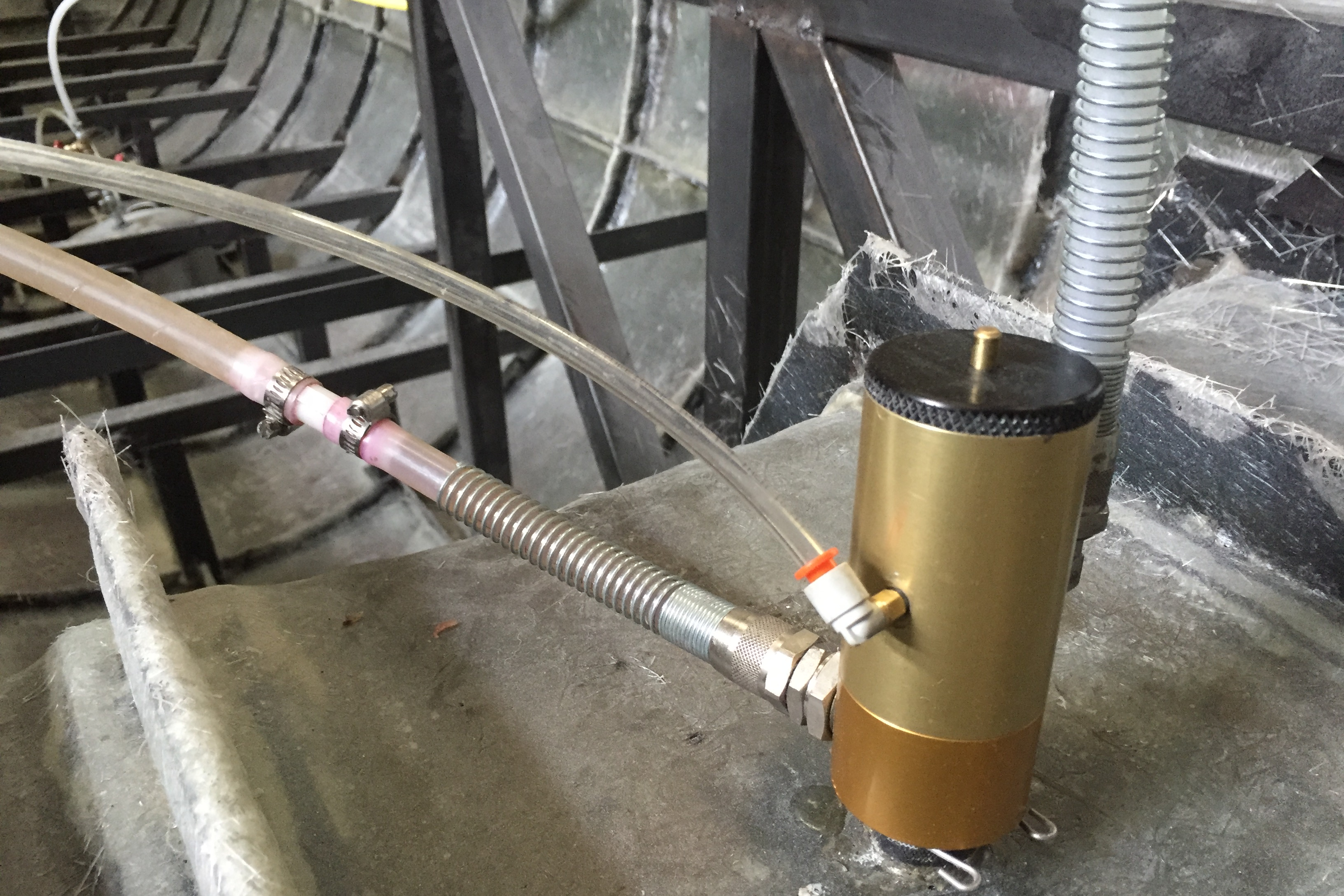
Soling begann Anfang 2019 mit der Konstruktion der Abdeckungen und begann 2020 mit der Herstellung der ersten Abdeckungen. Die Coronavirus-Pandemie und gelegentliche mechanische Herausforderungen führten dazu, dass die Produktion eingestellt und wieder aufgenommen wurde, aber Vergara sagt, dass Soling die Produktion aller 840 Abdeckungen über einen Zeitraum von 7 bis 8 Monate, Fertigstellung Ende 2020. Es wird erwartet, dass die neuen Abdeckungen wesentlich länger halten und viel weniger Wartung erfordern als die, die sie ersetzt haben.
Das Casablanca-Projekt, so Vergara, hat die Fähigkeiten von Soling als Hersteller hochwertiger, leistungsstarker, großer Verbundstrukturen unter Beweis gestellt und Türen zu anderen Möglichkeiten geöffnet. „Dieses Projekt war eine Herausforderung, bei der wir Paradigmen aufbrechen mussten, die besagten, dass Teile dieser Größenordnung mit dieser Herstellungsmethode nicht hergestellt werden könnten, und wir haben es trotzdem geschafft“, sagt er. „Für die Zukunft von Soling ist ganz klar:Es gibt kein Projekt, zu dem wir nicht in der Lage sind.“
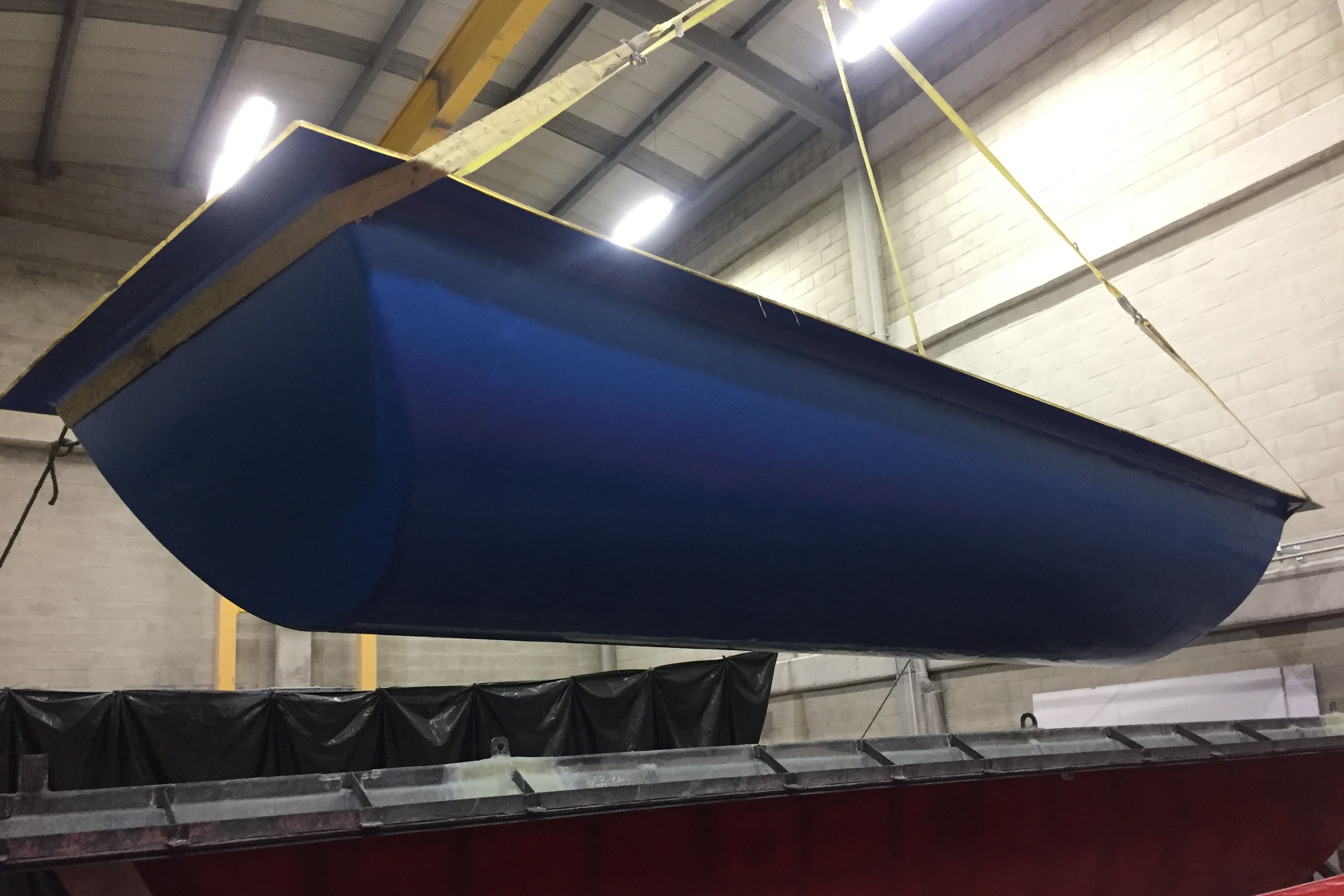
Harz