Automatisches Websystem für Hochleistungsanwendungen mit hohem Volumen
Ein seit langem bestehendes Hindernis für die weit verbreitete Einführung von Verbundwerkstoffen, insbesondere in der Automobilindustrie, ist die Notwendigkeit einer Massenproduktion und niedrigerer Kosten, als dies mit vielen Arten von Verbundwerkstoff-Herstellungsverfahren möglich ist. Das Startup-Unternehmen WEAV3D Inc. (Norcross, Georgia, USA) versucht, diese Probleme mit seinen kontinuierlichen Verstärkungsgitterstrukturen aus thermoplastischem Verbundwerkstoff zu lösen, die in einem automatisierten Webprozess hergestellt werden, der abfallfrei, kostengünstig und, prognostiziert WEAV3D Inc. , ein Wegbereiter für die Massenproduktion.
Vom Konzept zur Kommerzialisierung
Christopher Oberste, Gründer und CEO von WEAV3D Inc., entwickelte während seiner Promotion das erste Konzept für seine Technologie. in Materialwissenschaften und Ingenieurwissenschaften am Georgia Institute of Technology (Georgia Tech, Atlanta) im Jahr 2014. Sein Studium der Polymer- und Fasertechnik und ein Praktikum bei GKN Aerospace North America (Tallassee, Ala., USA) weckten das Interesse an Thermoplasten und großvolumige Prozesse wie Formpressen und Verbundwerkstoffe für die Luft- und Raumfahrt. Diese Arbeit führte zur Entwicklung seiner ersten Iteration für einen automatisierten Hochgeschwindigkeits-Webprozess für thermoplastische Verbundverstärkungsgitterstrukturen. Mit Hilfe und Unterstützung seines Ph.D. Berater Dr. Ben Wang, Oberste, beantragte und erhielt Zuschüsse zur Entwicklung und Vermarktung seiner Idee von der Georgia Research Alliance und dem Innovation Corps (NSF I-Corps)-Programm der National Science Foundation.
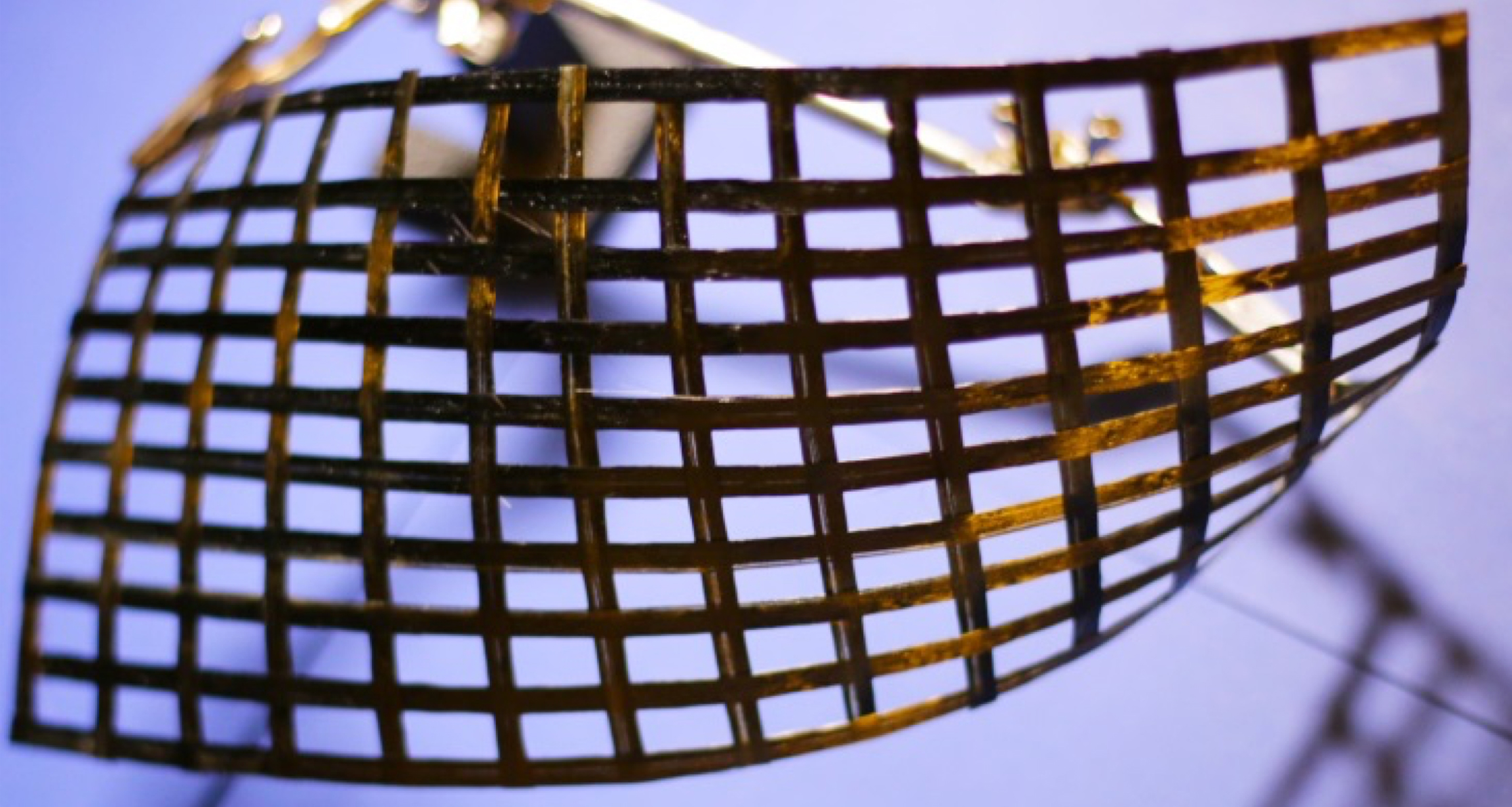
In den nächsten zwei Jahren arbeitete Oberste mit MBA- und Jurastudenten an der Kommerzialisierung der Technologie durch ein kollaboratives Programm am Georgia Tech namens TI:GER (Technological Innovation:Generating Economic Results). Bis 2017 gründeten Oberste und Mitbegründer Lewis Motion, ein ehemaliger Hubschrauberpilot der US-Küstenwache, WEAV3D Inc. heute beschäftigt das Unternehmen drei Vollzeit- und vier Teilzeitkräfte.
Angesichts des Hintergrunds von Oberste und Motion in der Luft- und Raumfahrt war der ursprüngliche Plan, die thermoplastischen Verbundwerkstoffe von WEAV3D als Verstärkungsstrukturen in Luft- und Raumfahrtkomponenten zu qualifizieren. Oberste erklärt jedoch, dass er und sein Team im Rahmen des NSF I-Corps-Stipendiums eine Reihe von 100 Interviews mit potenziellen Industriekunden durchführen mussten, was zu einer anderen Richtung führte. „Wir haben viele Discovery-Interviews in der Luft- und Raumfahrt geführt … aber wir haben immer wieder gehört, dass der Weg für Startups in die Luft- und Raumfahrt, insbesondere mit einem neuen Herstellungsverfahren, sehr schwierig ist. Die Adoptionszeit ist wirklich lang und es ist sehr teuer. Viele Unternehmen sterben, bevor sie es überhaupt auf den Markt schaffen können“, erklärt er.
Nach Gesprächen mit Unternehmen anderer Branchen entschieden sich Oberste und sein Team, ihren Fokus auf den Automobil- und Baumarkt zu verlagern. Er sagt:„Als wir anfingen, mit Leuten [in der Automobilindustrie] zu sprechen, stellten wir fest, dass in diesem Bereich ein wirklich großer ungedeckter Bedarf bestand, da die Automobilisten eine große Nachfrage nach Gewichtsreduzierung haben, aber auch preisbewusst sind . Sie sagten uns, dass die meisten der verfügbaren konventionellen Herstellungsverfahren für Verbundwerkstoffe nicht in der Lage waren, das benötigte Volumen zu den gewünschten Kosten bereitzustellen.“ Von dort aus machte sich Oberste daran, seine Technologie weiterzuentwickeln, um eine Lösung für die Herstellung von großvolumigen Verbundteilen zu niedrigen Kosten zu sein.
Das Ergebnis ist das markenrechtlich geschützte Rebar for Plastics-Konzept von WEAV3D. Mit einem automatisierten Web- und Konsolidierungsprozess fertigt WEAV3D maßlich abstimmbare, thermoplastische Verbundgitterstrukturen, die so konzipiert sind, dass sie einfach als Verstärkungsmaterial in ein Kunststoff- oder Betonteil durch Formpressen, Spritzgießen oder andere gängige Massenprozesse integriert werden können. Basierend auf Simulationsmodellen, sagt Oberste, ermöglicht dieser Ansatz die Produktion von Automobilteilen mit einer Leistung auf der Ebene von Stahl- oder Aluminiumblechen, die jedoch leichter und 30-75% kostengünstiger in der Herstellung sind als aus Organoblech hergestellte Verbundteile, automatisiertes Tapelegen ( ATL) oder Hand-Layup-Prozesse.
Der WEAV3D-Prozess
Der WEAV3D-Prozess beginnt mit handelsüblichen, thermoplastischen unidirektionalen (UD) Bändern. Oberste sagt, dass das Verfahren jede Art von Thermoplast und Verstärkungsfasern verarbeiten kann:„Unser Sweet Spot für die meisten Arbeiten, die wir im Automobil- und Bausektor durchgeführt haben, liegt bei Polypropylen [PP], Polycarbonat [PC], Polyethylenterephthalat [PET] oder Polyamid [PA]-Raum. Auch bei Verstärkungsfasern sind wir sehr agnostisch, wobei Glas- und Kohlefaser natürlich am beliebtesten sind.“ Er sagt, das Team habe auch einige Arbeiten mit leitfähigen Metallbändern durchgeführt und forscht an Bändern mit eingebetteter Faseroptik.
Die Pilotmaschine von WEAV3D in Originalgröße ist standardisiert, um ein 25 Millimeter breites oder 1 Zoll breites Band zu verarbeiten, obwohl Oberste sagt, dass die Maschine Bänder mit einer Breite von nur 5 Millimetern (0,2 Zoll) Breite mit der Verwendung von Adaptern und breiter verarbeiten kann Bänder mit Umrüstung. Auf der aktuellen Maschine können Gitter bis zu einer Breite von 1,5 Metern (60 Zoll) und einer Dicke von bis zu fünf Schichten in jeder für die Anwendung erforderlichen Länge hergestellt werden.
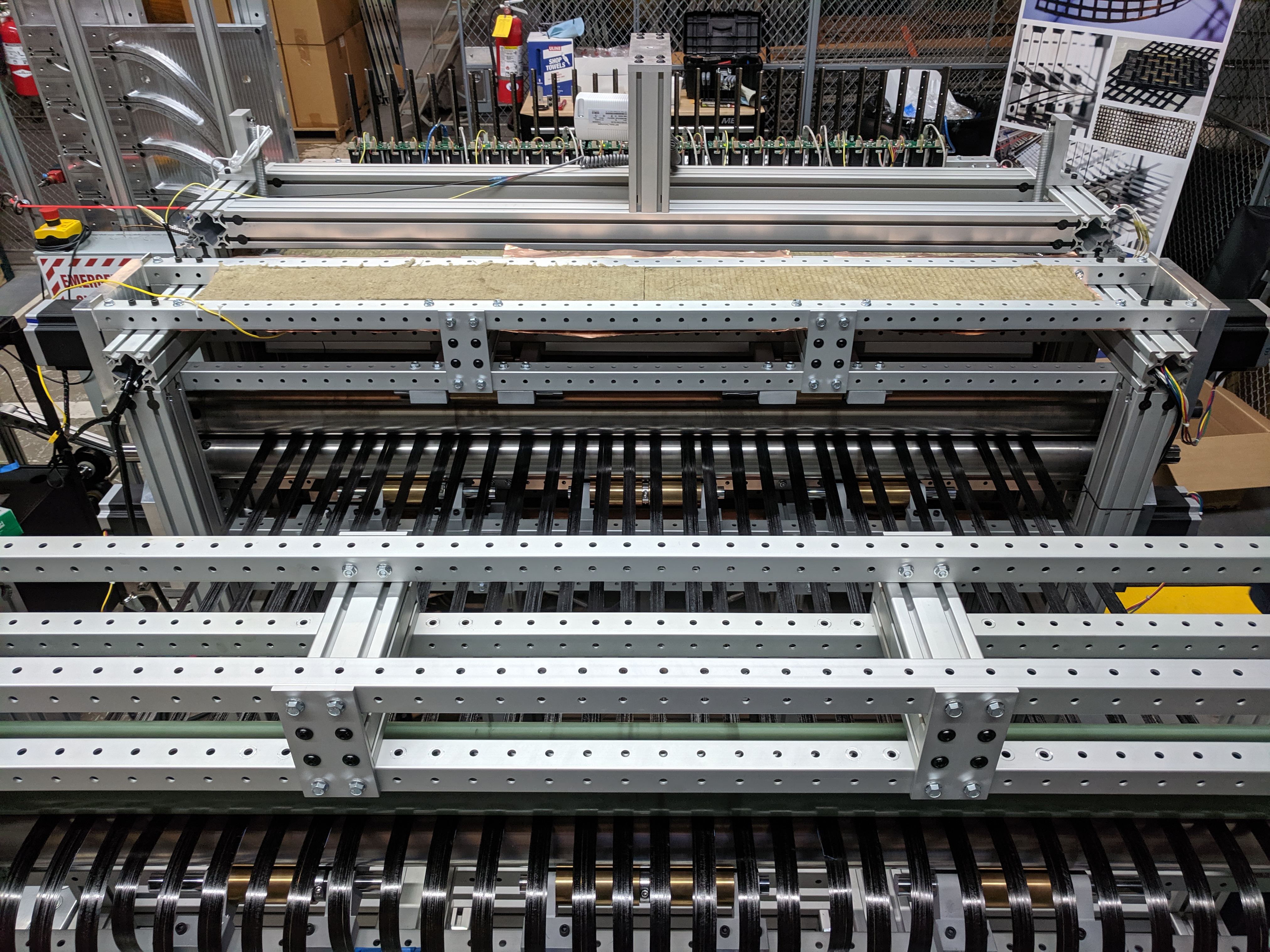
Die im November 2017 eingereichte Patentanmeldung des Unternehmens beschreibt das WEAV3D-System als „eine Maschine zur kontinuierlichen Herstellung eines gewebten Verbundstoffs mit kontrollierbarer innerer Gewebegeometrie“. Von Spulen, die auf die Maschine geladen werden, werden UD-Bänder in eine Reihe von unabhängig steuerbaren Kettköpfen eingefädelt. Jeder Kopf enthält mehrere Bandkanäle, die ein Kettfach bilden, einen Raum zwischen den Kettbändern für die einzufädelnden Schußrichtungsbänder. Ein Einfügestapel gibt unidirektionale Bänder in Schussrichtung durch das Kettfach ab, um ein Verbundgewebe zu bilden. Das gewebte Gitter wird dann unter einer Infrarot-(IR)-Lichtquelle und dann durch Kompressionsrollen gezogen, um die Bandschichten an den Verflechtungspunkten zu verfestigen und miteinander zu verbinden. Je nach Kundenwunsch wird die resultierende Struktur als flaches Blech oder als Rolle bereitgestellt oder WEAV3D bietet zusätzliche Besäum- und Preforming-Dienstleistungen an.
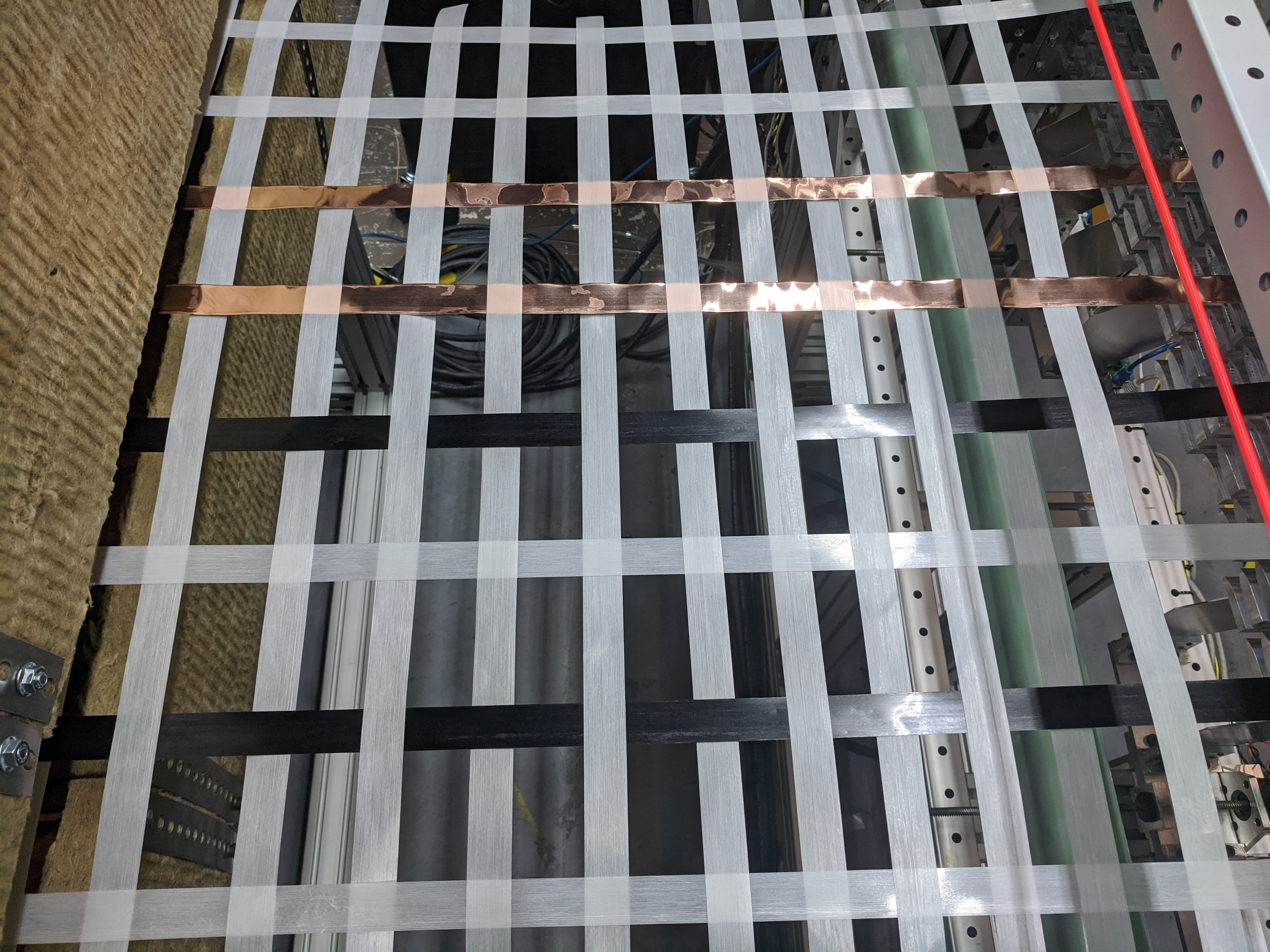
Einer der wichtigsten Vorteile des WEAV3D-Verfahrens ist laut Oberste die hohe Abstimmbarkeit der Gitterstruktur für unterschiedliche Anwendungen. Dazu gehört das Mischen verschiedener Materialien an verschiedenen Stellen sowie das Anpassen der Dichte oder des Abstands zwischen den Bändern der Gitterstruktur. „Wir können die Gitterstruktur wirklich für die Anforderungen des Endprodukts optimieren und gleichzeitig die Gesamtkosten minimieren.“
Nach der Auslieferung an den Kunden können die Gitter in Polymerbetonbauteile integriert oder zu einem endgültigen Automobilverbundteil formgepresst, thermogeformt oder spritzgegossen werden. Der WEAV3D-Prozess kann auch unterschiedlichen Komplexitätsgraden gerecht werden. Für relativ einfache Teile erklärt Oberste:„Dieses Gitter kann mit einem Laminierprozess kombiniert und dann als Co-Forming-Schritt tiefgezogen werden. Bei mäßig komplexen Teilen können wir Co-Forming oder Preforming im Formpressen durchführen, sei es thermoplastisches Formpressen oder SMC-Formpressen. Und dann können wir bei den sehr komplexen Teilen das Gitter tatsächlich in jede gewünschte Form vorformen, es in ein Werkzeug legen und dann dieses Teil umspritzen.“
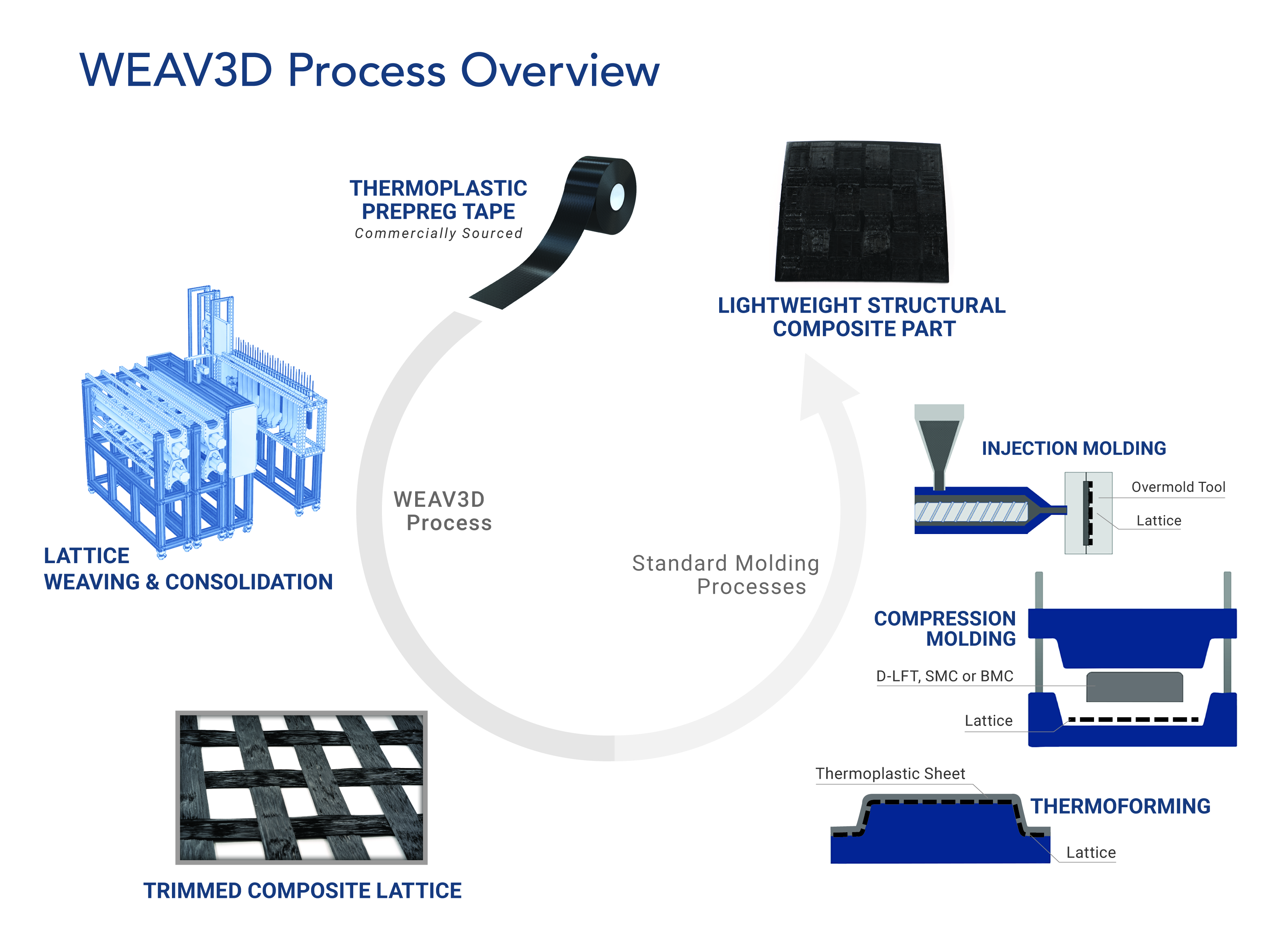
„Der große Fokus für uns im Verbundwerkstoff-Ökosystem liegt darin, dass wir ein Game-Changer für die Großserienproduktion sind“, fügt er hinzu. Das genaue Volumen hängt von der Anwendung ab, aber Oberste schätzt, dass die WEAV3D-Maschinen für Gitterteile, die zur Verstärkung von Automobiltürverkleidungen dimensioniert sind, zwischen 200.000 und 500.000 Einheiten pro Jahr produzieren können.
Darüber hinaus hat das Produkt WEAV3D auch verbesserte mechanische Eigenschaften beim Verstärken eines Verbund- oder Kunststoffteils gezeigt. „Die Kombination eines WEAV3D-Gitters mit bestehenden Kurzfaser-Kunststoffen oder Langfaser-Verbundwerkstoffen kann die Festigkeit, Steifigkeit und Zähigkeit des resultierenden Produkts erheblich erhöhen“, sagt Oberste ein besonderes Teil. „Bei einigen Anwendungen ermöglicht diese Leistungssteigerung eine deutliche Reduzierung der Teiledicke oder der Verrippung, was sich in einer Gewichtsreduzierung niederschlägt.“
Stahlbetongräben:Erste kommerzielle Anwendung
In den ersten Jahren lag der Fokus des Start-ups auf der Herstellung eines Herstellungsverfahrens und speziell für die Automobilindustrie geeigneten Materialien, wobei Oberste Ideen hat, wie diese Technologie in kommerziellen Innenraumkomponenten der Luft- und Raumfahrt, unbemannten Verteidigungsflugzeugen, Schienenverkehr, Fracht eingesetzt werden könnte Transport- und Schiffsanwendungen.
Für seine erste kommerzielle Anwendung, die im November 2020 angekündigt wurde, begann WEAV3D jedoch mit dem Baumarkt und verwendete Glasfaser/PET-Verstärkungen für ein Polymerbetongrabensystem, das von Oldcastle Infrastructure (Atlanta, Georgia, USA) hergestellt wird.
Das Grabensystem von Oldcastle, das zum Verlegen von Versorgungskabeln in städtischen Gebieten, Bahnhöfen oder Industrieanlagen verwendet wird, muss in der Lage sein, 16.000-Pfund-Belastungen von darüber fahrenden Fahrzeugen zu widerstehen. Zuvor wurde der Graben mit maßgefertigten, in den Beton eingelassenen Stahldrahtkörben bewehrt. Laut Oberste waren diese Stahlkörbe jedoch beide teuer in der Sonderanfertigung und da Oldcastle Gräben in verschiedenen Größen herstellt, hatten die Stahlkörbe nicht immer die richtigen Abmessungen, um die Entwässerungslöcher des Grabens richtig zu verstärken . „Da wir mit unserem Verfahren das Gitter wirklich für die Anforderungen der Anwendung optimieren können, konnten wir die Gittergeometrie abstimmen – zum Beispiel um sicherzustellen, dass wir die Abflusslöcher am Boden des Grabens verstärkt und am Boden des Grabens verstärkt haben. Enden des Grabens, damit er während der Handhabung vor Stößen geschützt ist“, sagt er.
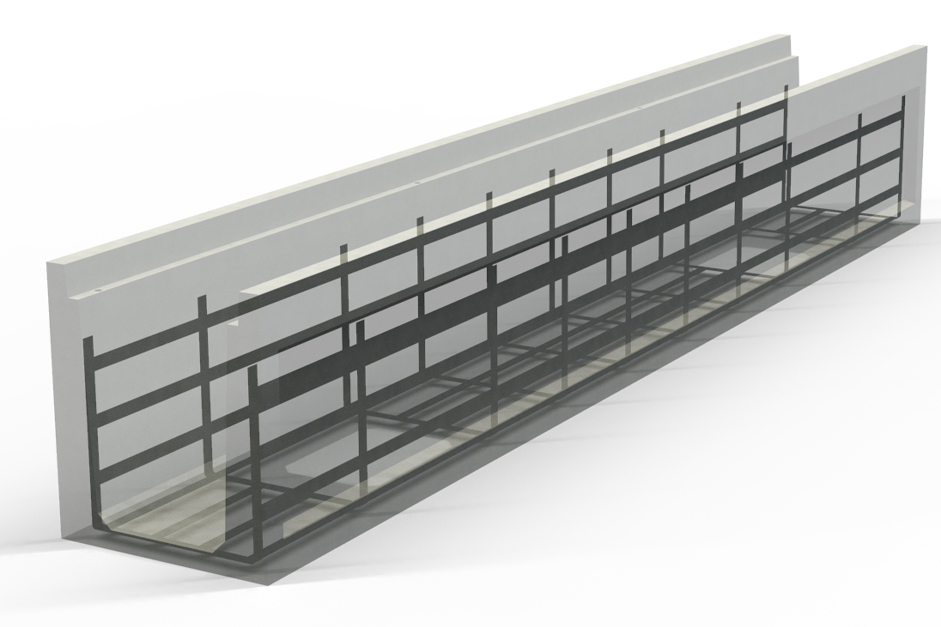
Darüber hinaus war es laut Oberste eine der größten Herausforderungen des Projekts, ein thermoplastisches Bandmaterial zu finden, das eine Klebeverbindung mit dem Polymerbeton eingehen kann, anstatt sich nur auf eine mechanische Schnittstelle zu verlassen, wie dies bei Stahlkäfigen der Fall ist Verstärkung. Das ausgewählte Polyethylenterephthalatglycol (PETG)-Material WEAV3D bildet eine echte adhäsive Grenzfläche zwischen den beiden Materialien, die bei der Spannungsübertragung hilft und die Wahrscheinlichkeit eines Bruchs verringert. „Selbst wenn ein Bruch auftritt“, fügt er hinzu, „ist es viel weniger wahrscheinlich, dass sich ein Bruch durch die Struktur ausbreitet, weil er diese adhäsive Grenzfläche überwinden muss.“
WEAV3D produziert die für diese Anwendung konzipierten Gitter als U-Kanal-Vorform, die Oldcastle dann in eine Gießform legt, wo Polymerbeton darüber gegossen wird, gefolgt vom Aushärten und Entformen, um die endgültige Stahlbetonstruktur zu erzeugen.
Im Baubereich plant WEAV3D, seine Gitter auf andere Polymerbetonanwendungen wie Gehäuse und Deckel auszudehnen. Im Oktober 2020 erhielt WEAV3D in einem gemeinsamen Antrag mit der Western Ontario University und dem Bauingenieurbüro Entuitive vom National Sciences and Engineering Research Council of Canada einen Zuschuss zur Durchführung von Forschungsarbeiten zur Bewertung der Verwendung der WEAV3D-Gitter als Verstärkung in traditionellem Portlandzement. auch auf Betonbasis. Ziel sei es, Gitter zu entwickeln, die als Verstärkung für Nichtwohngebäudedecken und Fassaden verwendet werden können, sagt Oberste.
WEAV3D der nächsten Generation:Fahrzeuggeschwindigkeiten
Mit Forschungsgeldern der NSF wird derzeit eine neue Generation der WEAV3D-Maschine entwickelt, die auf die Anforderungen des Automobilbaus zugeschnitten ist. Laut Oberste wird es voraussichtlich 2022 online gehen. Verbesserungen des neuen Systems sollen die Produktionsgeschwindigkeit des aktuellen Systems verdreifachen, einschließlich des Ersatzes von IR-Heiz- und Kompressionswalzen durch effizienteres Ultraschallschweißen.
Gleichzeitig haben Oberste und sein Team Gespräche mit US-amerikanischen und europäischen Tier 1s und OEMs der Automobilindustrie über den Einsatz von WEAV3D-Produkten zur Verstärkung von Kunststoffplatten aufgenommen, von Interieurkomponenten bis hin zu Pickup-Heckklappen. „Eines der Ziele ist es, innerhalb von Kunststoffformteilen ein Gitter als strukturelles Skelett hinzuzufügen, um deren Festigkeit und Steifigkeit zu verbessern und metallische Halterungen und Versteifungen zu ersetzen, auf die sich Konstrukteure derzeit verlassen“, sagt Oberste. WEAV3D arbeitet auch an Demonstrationsartikeln von Automobilkarosserieteilen und anderen Komponenten, um die Vorteile des Materials zu demonstrieren.
Harz
- Portwell:19-Zoll-System zielt auf Videowandanwendungen ab
- Heim-/Hotelüberwachungssystem mit automatischer Steuerung
- Hochleistungsverbundwerkstoffe in Israel
- EconCore lizenziert Fynotej für NA-Automobilanwendungen und macht Fortschritte bei Hochleistungsthermoplasten (HPT)
- Solvay bringt Hochleistungs-Kohlefaserband für Offshore-Öl- und Gasanwendungen auf den Markt
- Kalibriersystem für die automatisierte Faserplatzierung
- Hochleistungslaser der nächsten Generation
- Systemintegratoren für automatisierte Verpackungen
- Paket- und Paketsortiersystem automatisiert durch KI
- Die nächste Dimension von Hand-Auge-Anwendungen – Bewegung