Die OOA-infundierte Flügelkiste voranbringen
Da die Luft- und Raumfahrtindustrie ihre Erholung von der COVID-19-Pandemie erwartet, hat sich der vorherige Druck auf eine Hochgeschwindigkeitsproduktion zu einem dringenden Bestreben entwickelt, die Umweltbedrohungen für den Planeten und die Menschen zu verringern. Diese Bemühungen umfassen die Begrenzung der Treibhausgasemissionen, des Energie- und Wasserverbrauchs und die Erzeugung von Abfällen, die nicht recycelt werden können. Obwohl diese Initiativen vor COVID-19 noch im Gange waren, wird ihr Schwerpunkt nun verstärkt, ebenso wie die Notwendigkeit viel niedrigerer Kosten für die Herstellung von Verbundstrukturen. Das paneuropäische Luftfahrtprogramm Clean Sky 2 hat Forschung und Entwicklung in all diesen Bereichen finanziert und eine Vielzahl von faserverstärkten Verbundtechnologien maßgeblich vorangebracht.
In der siebten Aufforderung zur Einreichung von Vorschlägen von Clean Sky 2 (CFP07, Oktober 2017) ist die Anfrage von Airbus Defence and Space (Airbus DS, Cadiz, Spanien) für eine innovative und flexible Pilotanlage zur Herstellung eines hochintegrierten Flügelkasten-Flugdemonstrators mit automatisierter Faser enthalten Platzierung (AFP) und Flüssigharzinfusion.
Es gab andere Demonstratoren von harzinfundierten und/oder außerhalb des Autoklaven (OOA) Wing Boxen, einschließlich einer OOA „blended“ Wing Box, die 2013 von GKN Aerospace (Redditch, Großbritannien) vorgestellt wurde; der Airbus A220-Flügel, der von Spirit AeroSystems Belfast in Nordirland mit Harztransferinfusion in einem Autoklaven hergestellt wird; und der OOA-Flügel von AeroComposit (Moskau, Russland) für die MS-21 Jetliner. Alle diese haben jedoch diskrete, durch Stringer versteifte Beplankungen und Holme mit mechanischen Befestigungselementen zusammengebaut (siehe „Der Weg zu OOA-Flügeln mit minimalen Befestigungselementen“).
Die von Airbus DS geforderte Flügelbox in Clean Sky 2 sollte einen Schritt nach vorne machen, indem die versteifte Unterhaut mit versteiften vorderen und hinteren Holmen integriert wurde, um ein vollständigeres Modul ohne . zu ermöglichen Befestigungselemente zur Montage mit den restlichen Flügelkomponenten weiterzuleiten.
Diese Flügelbox würde auch schmale (0,25 oder 0,5 Zoll breite) trockene Kohlefaserbänder und Hochtemperatur-(180 °C Tg) verwenden ) aushärtenden Harzen, jedoch mit energiesparenden, kostengünstigen Heizsystemen und sensorbasierter digitaler Steuerung und Simulation zur Vorhersage und Steuerung der Verarbeitung, verkürzen Trial-and-Error-Schleifen während der Entwicklung und ermöglichen eine schnelle Schulung des Fertigungspersonals. Diese Digitalisierung würde sich zu einer mobilen Augmented-Reality-Anwendung (App) entwickeln, die auch Benutzer- und Wartungshandbücher, Prozessablaufdefinition, papierlose Prozess- und Teileverfolgung und Projektion von CATIA-Modellen auf das Teil bietet, um die präzise Platzierung von Versteifungsvorformen und Werkzeugeinsätzen zu unterstützen und kohlenstofffaserverstärkte Polymer (CFK) Dichtungsplatten.
Das vielleicht anspruchsvollste Projekt erforderte, dass alle Werkzeuge und Fertigungsausrüstungen tragbar und flexibel sind, einfach an jedem Fertigungsstandort eingesetzt und für andere Teilekonstruktionen und Upgrades angepasst werden können, wenn fortschrittlichere Werkzeug-, Heiz- und Verbundwerkstoffe 4.0-Prozesssteuerungstechnologien verfügbar werden.
Der Themenmanager Luis Rubio, Head of Composite Development Engineering – Technology and Process bei Airbus DS, erklärt:„Der letzte Zweck des Projekts besteht darin, zu zeigen, dass eine alternative Technologie (zu Prepreg und Autoklaven) mit geringeren Kosten, kürzeren Durchlaufzeiten und Der ökologische Fußabdruck kann ähnliche Designtoleranzen und Qualitätsniveaus erreichen.“
MTorres (Torres de Elorz, Spanien) hat geantwortet und sich ohne Partner beworben. „Wir hatten alle Fähigkeiten im eigenen Haus:AFP, Infusion, Trockenbandmaterialien und Automatisierung“, erklärt Sebastian Diaz, Senior Manager für Composite Applied Technologies bei MTorres. Das Unternehmen wurde mit dem Projekt Innovative Infusion Airframe Manufacturing System (IIAMS) ausgezeichnet, das über das Horizon 2020-Programm der Europäischen Union im Rahmen der Finanzhilfevereinbarung Nr. 820845 finanziert wurde, und nahm seine Arbeit im Oktober 2018 auf.
Demonstrator der Außenflügelbox
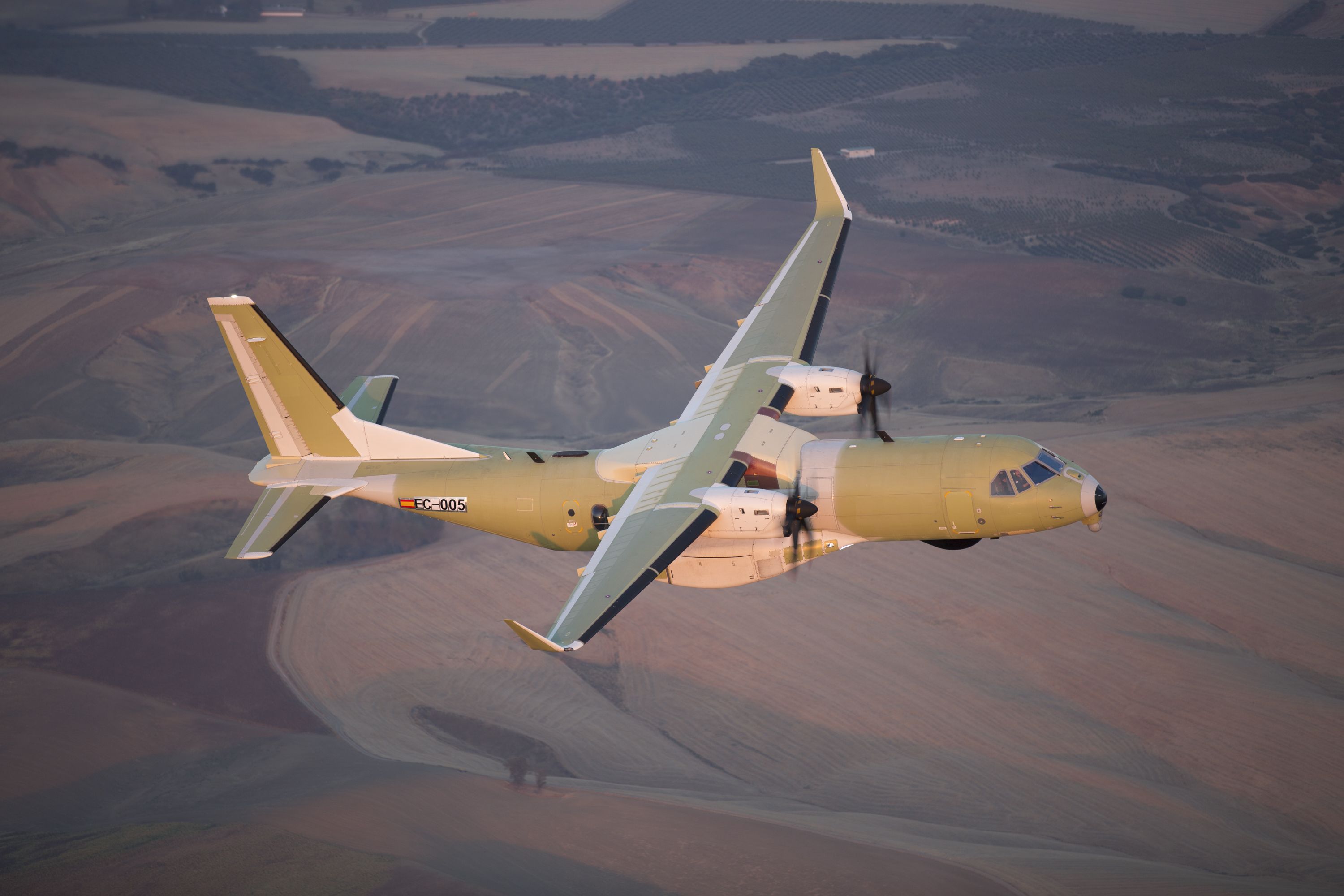
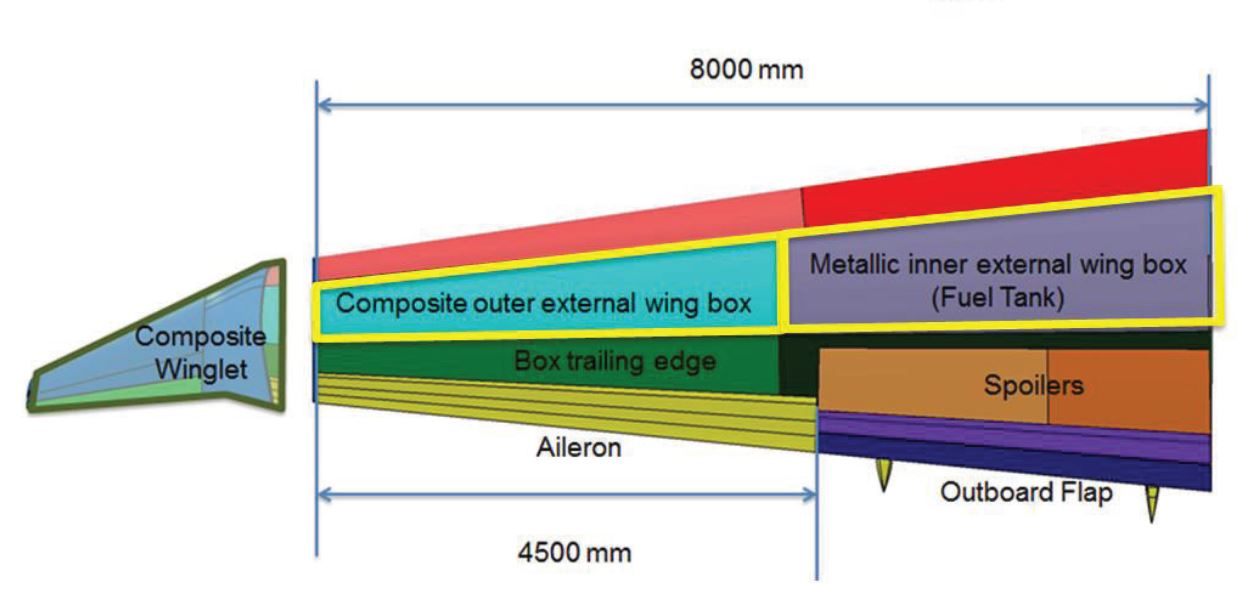
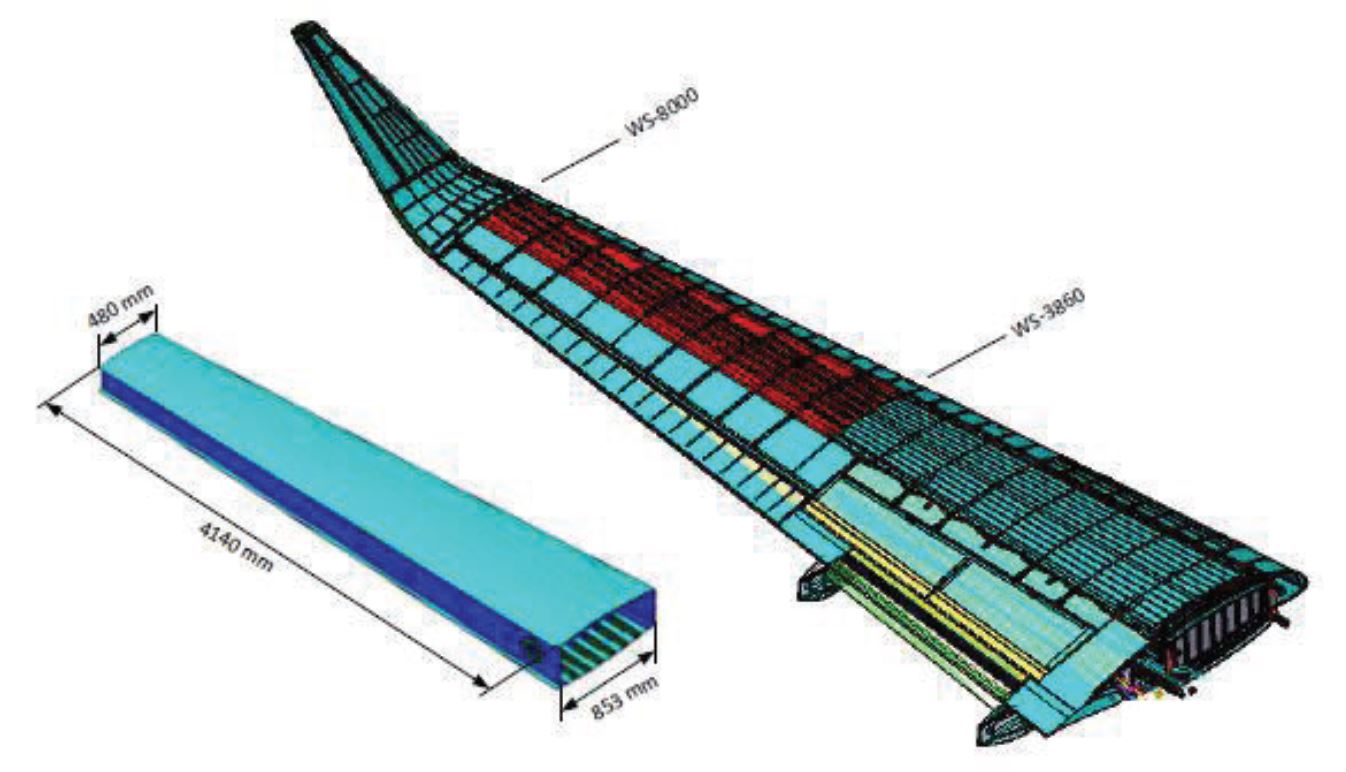
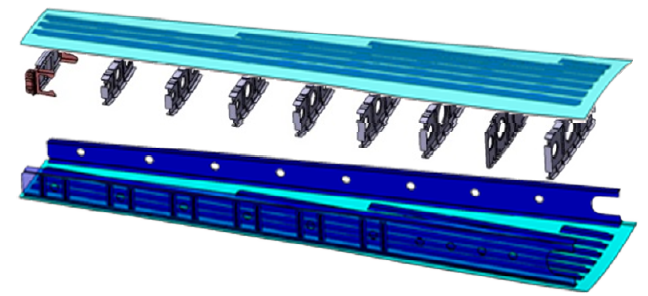
Als Demonstrator wählte Airbus DS eine Außenflügelbox auf Basis seines C-295-Twin-Turboprop-Militärtransporters (Bild 1), hergestellt in San Pablo, Sevilla, Spanien. Diese 4,14 Meter lange Torquebox aus Verbundwerkstoff für Außenborder passt zu einem Innenborder aus Metall Torsionskasten. Die Wingbox aus Verbundwerkstoff wird auch an einem Winglet, einer Vorderkante und einer Hinterkante befestigt.
„Wir sollten zwei 4 Meter lange Demonstratoren herstellen, den rechten und den linken Flügel, die für Flugversuche installiert werden“, sagt Diaz. „Die Herstellung sollte ein One-Shot-Prozess sein, kein sekundäres Bonden. Wir haben nur das „U“ gemacht, bestehend aus der Unterhaut mit sechs integrierten Stringern und den Holmen auf jeder Seite. Die Haut, Stringer und Holme sind alle unterschiedlich dick. Die J-Form der Holme und die Integration ihrer Versteifungen war eine ziemliche Herausforderung in der Herstellung. Wir standen auch vor der Herausforderung, bei diesem Herstellungsverfahren enge Toleranzen und eine genaue Geometrie einzuhalten. Diese Genauigkeit ist entscheidend, vor allem an der Wurzel für die Montage am inneren Flügelkasten und dann auch am Winglet.“
Das Design der innovativen, industriellen Fertigung wurde bei MTorres entwickelt, während Airbus DS die Spezifikationen für die Teilekonstruktion lieferte. „Wir haben problemlos zusammengearbeitet, um den besten Herstellungsprozess zu entwickeln und zu verifizieren, dass dieser Entwurf mit unserem Verfahren hergestellt werden kann und umgekehrt“, sagt Diaz.
Automatisiertes Zentrum für Thermoinfusion (ACTI)
Gemäß der Airbus-DS-Spezifikation müssen alle Werkzeuge und Fertigungsmittel, die zur Herstellung der Flügelbox verwendet werden, tragbar sein, mit Standardfahrzeugen zu anderen Einrichtungen transportiert und ohne besondere Maßnahmen schnell aufgebaut werden können. Dies führte zur Entwicklung des automatisierten Zentrums für Thermoinfusion (ACTI), das die Heißdrapierung der Stringer und Holme durchführt; Infusion der Stringer, Holme und Haut; und Heilungszyklen. Hot-Drape-Forming (HDF) – entwickelt als beheiztes Debulking in Flugzeugstrukturen und als beheiztes Vorformen außerhalb der Luft- und Raumfahrt – entfernt Hohlräume in Layups und wandelt 2D-Rohlinge für die Stringer und Holme in geformte Vorformlinge um (siehe „Hot-Drape-Forming“).
Der ACTI hat eine nutzbare Innenfläche von ca. 5,5 x 2,2 Metern und sieht ähnlich wie ein herkömmliches HDF-System aus, mit Stahlrahmen und einer elektronisch heb- und senkbaren oberen Hälfte, komplett mit Verriegelung und anderen Sicherheitsvorrichtungen. Das Aushärtewerkzeug und mehrere Heißfolienformwerkzeuge sind im ACTI positioniert. „Es wird kein Druck angelegt, nur Vakuum“, bemerkt Diaz. „ACTI verwendet erhitzte Luft mit einem Luftstrom, der definiert wurde, um eine schnelle Wärmeübertragung sowohl beim Heißfolienformen als auch beim Infusionsprozess zu gewährleisten.“
Er stellt auch fest, dass das System selbstnivellierend ist. „Die Steifigkeit der ACTI-Struktur (und des Aushärtewerkzeugs) ist so ausgelegt, dass sie die Toleranzen unter Betriebsbelastung im einfach gelagerten Zustand auf nur zwei Stützabschnitten einhält“, erklärt Diaz. „Das bedeutet, dass die Maßhaltigkeit beim Aufliegen auf dem Boden erhalten bleibt, ohne dass eine weitere Nivellierung oder andere geometrische Abstimmung erforderlich ist. ACTI zeichnet sich außerdem durch einen niedrigen Energieverbrauch und niedrige Herstellungskosten aus.“
Letzteres ist zum großen Teil darauf zurückzuführen, dass der Zusammenbau mehrerer gehärteter Teile durch den Zusammenbau mehrerer Vorformlinge ersetzt wird, die dann infundiert und zu einer einzigen integrierten Struktur gehärtet werden. „Das Aushärtewerkzeug ist auch das Montagewerkzeug“, sagt Diaz. „Alle Elemente sind trockene Preforms, die in das Aushärtungswerkzeug eingebaut und dann in einem Single-Shot-Prozess zusammen infundiert werden.“ Es wird keine Montagelehre benötigt und durch innovative Elemente in den Werkzeugen werden enge Toleranzen erreicht.
Ein weiterer wichtiger Aspekt dieses Ansatzes besteht darin, zerstörende und zerstörungsfreie Prüfungen (NDT) zu entfernen und sich stattdessen auf Prozessdaten zu verlassen, die während der verschiedenen Herstellungsschritte gesammelt wurden, um die Prozessqualität zu überprüfen und Parameter außerhalb der Spezifikationen zu kennzeichnen. Mit dem ACTI verwendete Sensoren erfassen Temperatur, Vakuum, Harzfluss und Aushärtungszustand. „Sowohl die Lufttemperatur als auch die Teiletemperatur werden überwacht“, sagt Diaz. „Das Werkzeug verfügt über integrierte Thermoelemente, die die Temperatur für die Formen und die Teileoberflächen verfolgen.“ Alle Daten werden aufgezeichnet, analysiert und verwendet, um Diagramme zu drucken und Produktionsentscheidungen zu unterstützen.
„Sowohl im IIAMS als auch in zukünftigen Projekten helfen die Daten dabei, die Prozesseinrichtung im Frühstadium zu verbessern“, erklärt Diaz. Harzfluss und Aushärtungszustand werden mit dielektrischen Sensoren von Netzsch (Selb, Deutschland) überwacht, die direkt in die CFK-Aushärtungswerkzeuge eingebaut werden. „Wir brauchten berührungslose Sensoren für die Haut, weil es keinen direkten Kontakt zwischen Harz und Form gibt“, sagt Diaz. „Die Sensoren überwachen die Änderung des dielektrischen Felds, wenn das Harz ankommt und dann während der Aushärtung fest wird. Wir haben diese Daten verwendet, um den Aushärtungszyklus zu verkürzen.“
Später im Projekt wurden die Sensoren und ACTI mit einer von MTorres entwickelten Mensch-Maschine-Schnittstelle (HMI) kombiniert, die eine echte Prozesssteuerung von einem Computer aus ermöglicht, einschließlich Vakuum und Temperatur sowie Harzfluss über Zufuhrventil. Laut Airbus DS besteht das Ziel darin, die Massenproduktion integrierter Primärstrukturen aus Verbundwerkstoffen voranzutreiben, indem der Prozess schlanker und intelligenter gemacht wird.
Leichte Werkzeuge und Portabilität
MTorres produzierte zwei Sätze von Formen – einen für den rechten Flügel und einen für den linken Flügel. „Für Teile mit identischer Geometrie, wie Versteifungen, gab es nur einen Satz“, bemerkt Diaz. „Andere Tools wurden, wenn möglich, geteilt.“
Mit einem einzigen, einteiligen Aushärtewerkzeug wurde die 3D-Form der Haut geformt, auf der alle anderen Preforms platziert wurden. Das rund 4,5 Meter lange Werkzeug wurde in der rechten und linken Ausführung aus CFK gefertigt, sagt Diaz. „Dies erleichtert die Einhaltung von Toleranzen, da wir die Werkzeuge mit dem gleichen Aufbau und der gleichen Verarbeitung wie die Teile konstruiert haben, sodass der CTE dem des endgültigen Teils sehr nahe kommt. Auch diese CFK-Härtungswerkzeuge sind leicht, etwa 200 Kilogramm, und somit mit einem kleinen Elektrostapler fahrbar. Dies wäre unmöglich, wenn wir für ein 4,5 Meter langes Werkzeug Metall verwenden würden.“
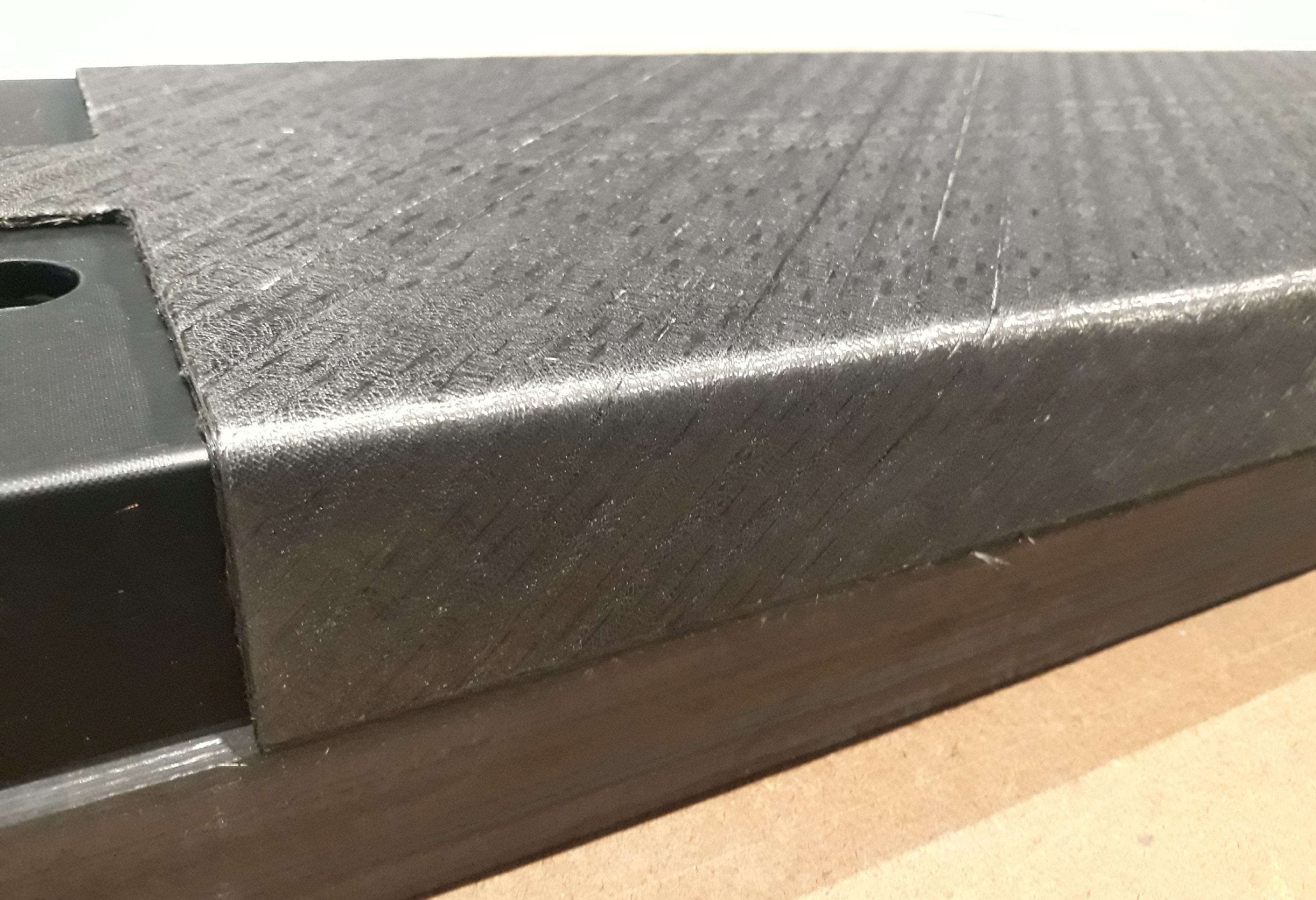
Der Rest der Werkzeuge – Spannzangen, Positionierer und HDF-Werkzeuge – ließen sich leicht von Hand handhaben. HDF der Stringer, Holme und Holmversteifungs-Preforms verwendete IML-Werkzeuge (IML), ebenfalls aus CFK. Während des Gebrauchs wurden diese auf einem Aluminiumtisch montiert und in den ACTI gestellt.
AFP mit neuartigem Trockenfaserband
Alle Strukturelemente des Flügelkastens – Haut, Stringer, Holme, Holmversteifung – wurden mit der MTorres AFP-Technologie für Trockenfaserbänder hergestellt. „In der Ausschreibung hieß es, schnelle und billige Materialien zu verwenden“, sagt Diaz. „Aber kommerziell erhältliche Trockenfaserbänder, insbesondere von den größeren Anbietern, waren nicht so einfach zu beschaffen und wir hatten das Know-how, unser eigenes Material herzustellen (siehe „Neuartiges Trockenband für flüssig geformte Verbundwerkstoffe“). Also haben wir unser 0,5 Zoll breites, 300 Gramm pro Quadratmeter (gsm) trockenes Kohlefaserband aus Mitsubishi Rayon (Tokio, Japan) 50K hochfester (HS) Faser verwendet. Unser Tape wurde entwickelt, um die Infusion, aber auch das Layup mit unseren AFP-Köpfen zu erleichtern und gut zu funktionieren. Wir kennen alle Parameter für AFP-Layup, Hot-Drape-Forming und Harzinfusion, und wenn wir kleine Änderungen vornehmen mussten, konnten wir dies tun, da wir die Bandherstellungslinie zur Verfügung hatten.“
MTorres testete auch seinen Wing-Box-Herstellungsprozess mit 200 g/m² Klebeband von Hexcel (Les Avenières, Frankreich), das aus seiner Intermediate-Modulus (IM)-Faser hergestellt wurde. „Obwohl unser Verfahren mit beiden Arten von Bändern gut funktionieren kann“, sagt Diaz, „war es während der Entwicklungsphase einfacher und kostengünstiger, unser Material im Vergleich zu dem handelsüblichen Material zu verlegen – die Breite und Steifigkeit wurden so konstruiert, dass das Verhalten von Spulen zum Tisch war glatt und schnell. Es war auch leicht verfügbar.“

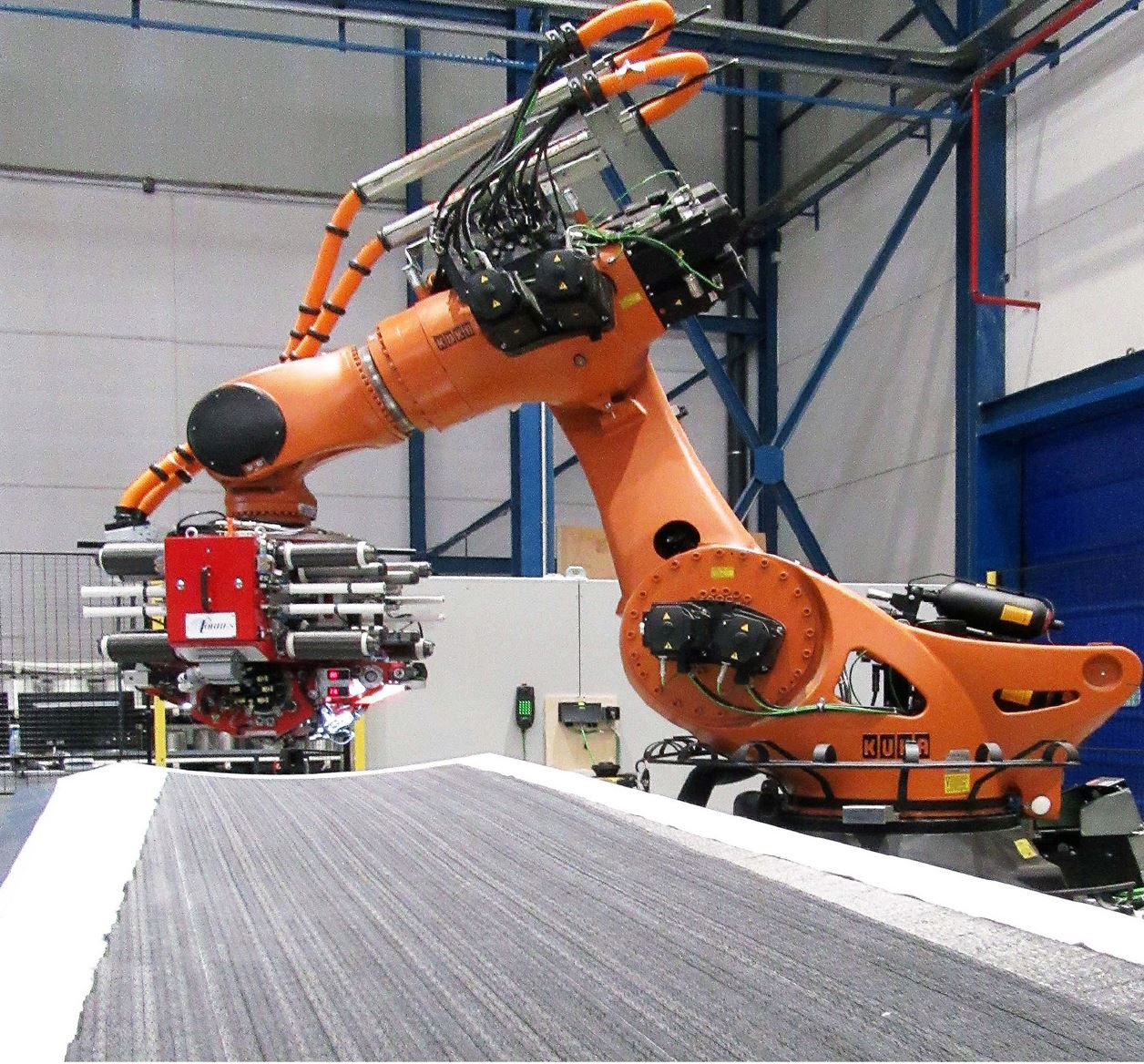
Schritt 1. AFP wurde verwendet, um Flügelkastenhaut (hier abgebildet) sowie 2D-Rohlinge für Stringer, Holme und Holmversteifungen zu verlegen. Bildnachweis, alle Schritte: IIAMS-Projekt, Airbus Defence and Space, MTorres.
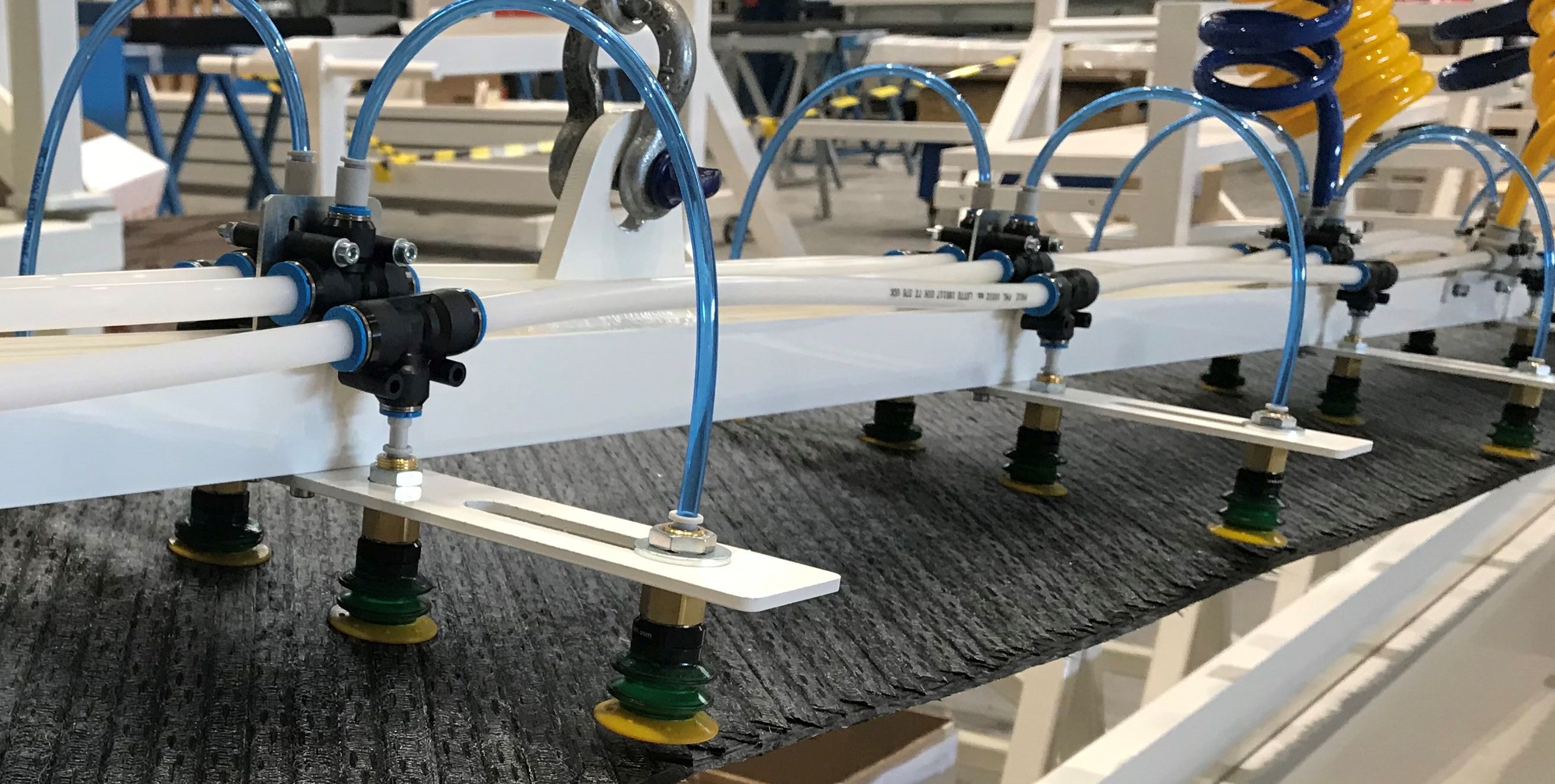
Schritt 2. Flachbandzuschnitte wurden vom Legetisch zu Heißdrapierwerkzeugen transportiert.
Er stellt fest, dass für AFP zwei Strategien verfolgt wurden:eine für die untere Haut und eine andere für die Stringer, Holme und Holmversteifungen. Die Haut (3-6 Millimeter dick) wurde mit . in die endgültige 3D-Form auf das Aushärtewerkzeug gelegt (Schritt 1) eine semipermeable Membran – patentiert von Airbus in seiner Vacuum Assisted Process (VAP)-Infusion. Die Stringer, Holme und Holmversteifungen wurden als flache Zuschnitte (2D) auf einen Vakuumtisch gelegt und dann auf die HDF-Werkzeuge bewegt, um ihre endgültige 3D-Form zu erreichen (Schritt 2).
Beheiztes Vorformen
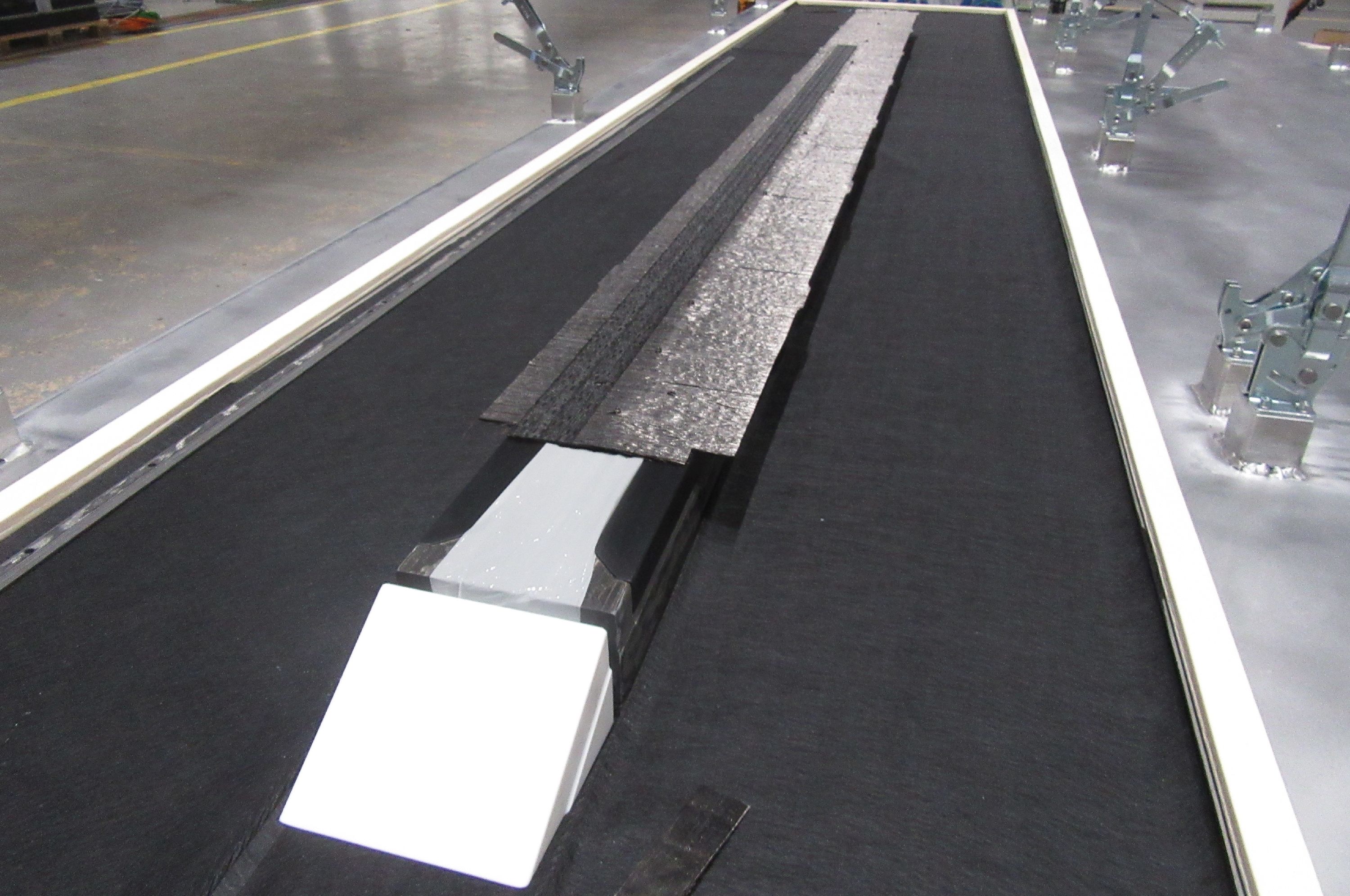
Schritt 3. Stringer-Rohling wird auf das männliche HDF-Werkzeug gelegt.
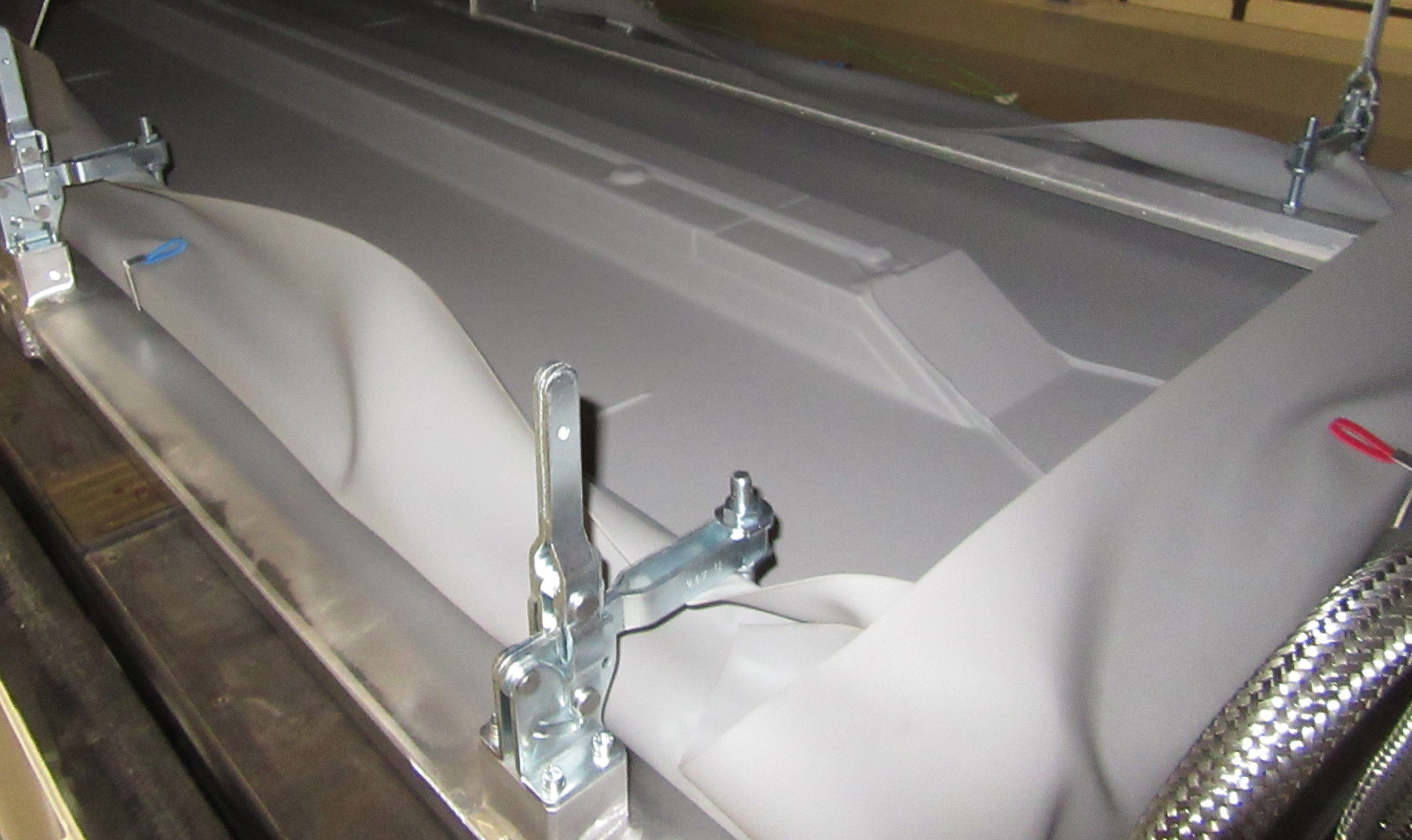
„Die flachen Platinen für die Stringer, Holme und Holmversteifungen haben wir über ein Portal mit Vakuumgreifern vom Legetisch zur Warmformstation transportiert“, erklärt Diaz. „Das automatisierte System kann die Zuschnitte in einem flachen Zustand bewegen und sie faltenfrei auf die männlichen Umformwerkzeuge legen [Schritt 3].“ Die Umformwerkzeuge wurden auf einem Aluminium-Umformtisch installiert, der in das ACTI gestellt wurde. Ein wiederverwendbarer Silikon-Vakuumbeutel (Mosites Rubber Co., Fort Worth, Texas, USA) wurde auf die Rohlinge gelegt, die dann im ACTI auf 130 °C erhitzt und unter Verwendung von Vakuum geformt wurden (Schritt 4). „Vakuum wurde bei Erreichen des Temperatursollwertes nach einer vordefinierten Rampe mittels eines Regelventils sanft angelegt“, sagt Diaz.
Er stellt fest, dass sich Dry Tapes leichter vorformen/heiß drapieren lassen, „weil die Verbindung zwischen den Schichten weicher ist als bei Prepregs. Obwohl es sich um trockenes Material handelt, ist es ist ein HDF/beheiztes Debulking, bei dem der resultierende Vorformling dank der in den Bändern enthaltenen Bindemittel seine Form behält.“
Für die Stringer und Holmversteifungen wurden Rohlinge zu zwei L geformt, die dann Rücken an Rücken auf das Aushärtewerkzeug gelegt wurden, um T-Stringer/Versteifungen zu bilden. Jeder der sechs Hautstringer ist anders und erfordert unterschiedlich geformte Rohlinge, um die Vorformlinge zu erzeugen. Jeder der 24 Holmversteifungen hat auch eine andere Länge.
Der vordere und der hintere J-Holm bestehen aus einem zu einem C geformten Zuschnitt, der zur Innenseite des Flügelkastens zeigt, und einem anderen zu einem Z geformten Zuschnitt, der nach außen gerichtet ist – die beiden werden Rücken an Rücken platziert. Die Holme haben auch sinusförmige Füße an der Außenseite des Flügelkastens (Pfeil in Schritt 7). „Wir haben die Form für die Holmfüße auf dem flachen Legetisch geschnitten, bevor wir den Rohling in die Formstation transportiert haben“, sagt Diaz. „In diesem Bereich konnte nachträglich nichts besäumt oder gefräst werden. Die Rohlinge wurden mit den Holmfüßen an der linken Seite des Werkzeugs und dem oberen Flansch an seiner rechten Seite direkt auf das Patrizenformwerkzeug gelegt.“
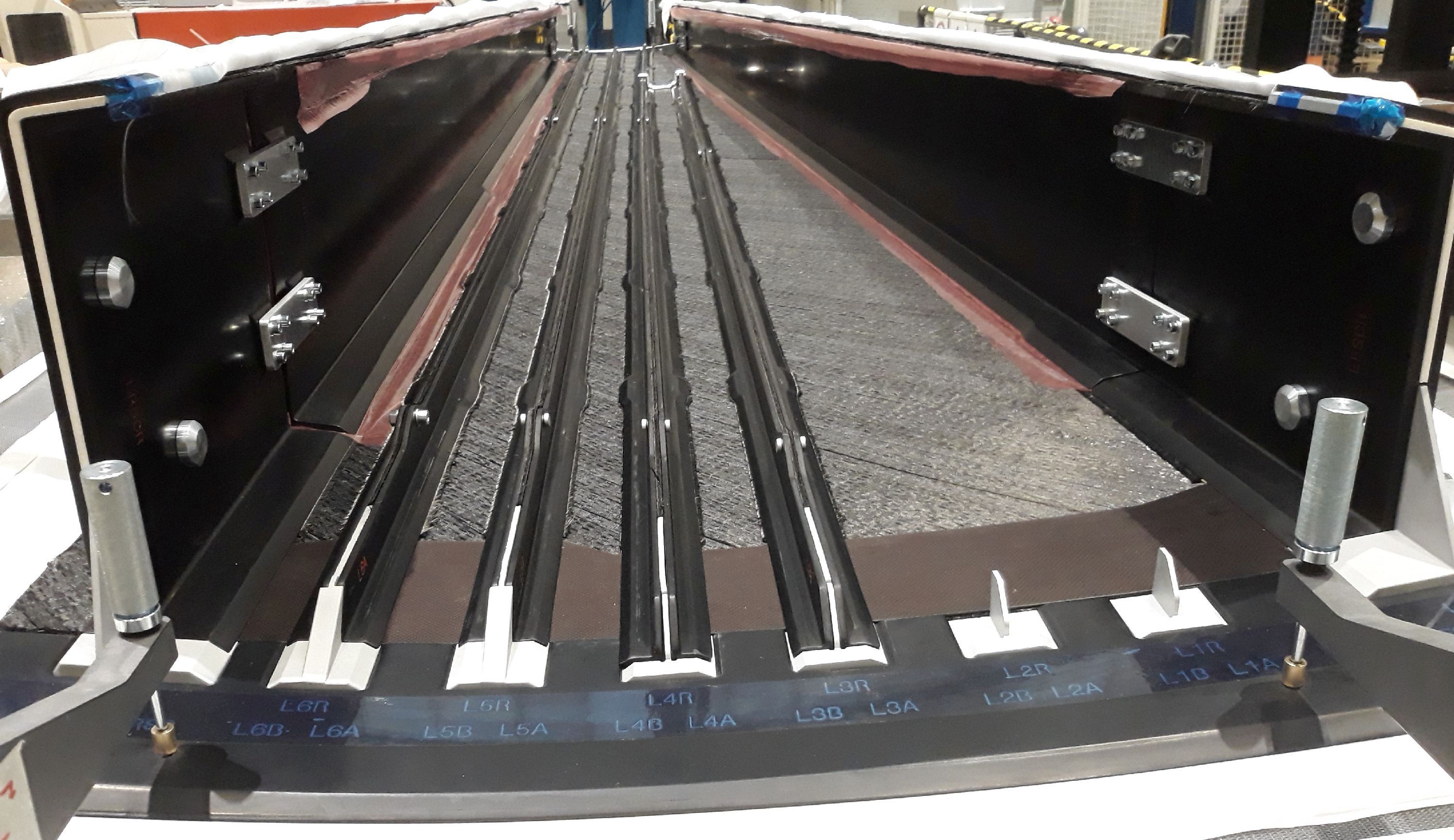
Abb. 3. Präzise Platzierung der Vorformlinge. Vorformlinge für J-Holm und Stringer wurden unter Verwendung von zwei Metallzylindern (ganz links und rechts zu sehen), weißen Positionierern und einer CFK-Kessel mit Ausschnitten für die Stringer/Positioner positioniert. Bildnachweis: IIAMS-Projekt, Airbus Defence and Space, MTorres.
Einmalige Infusion
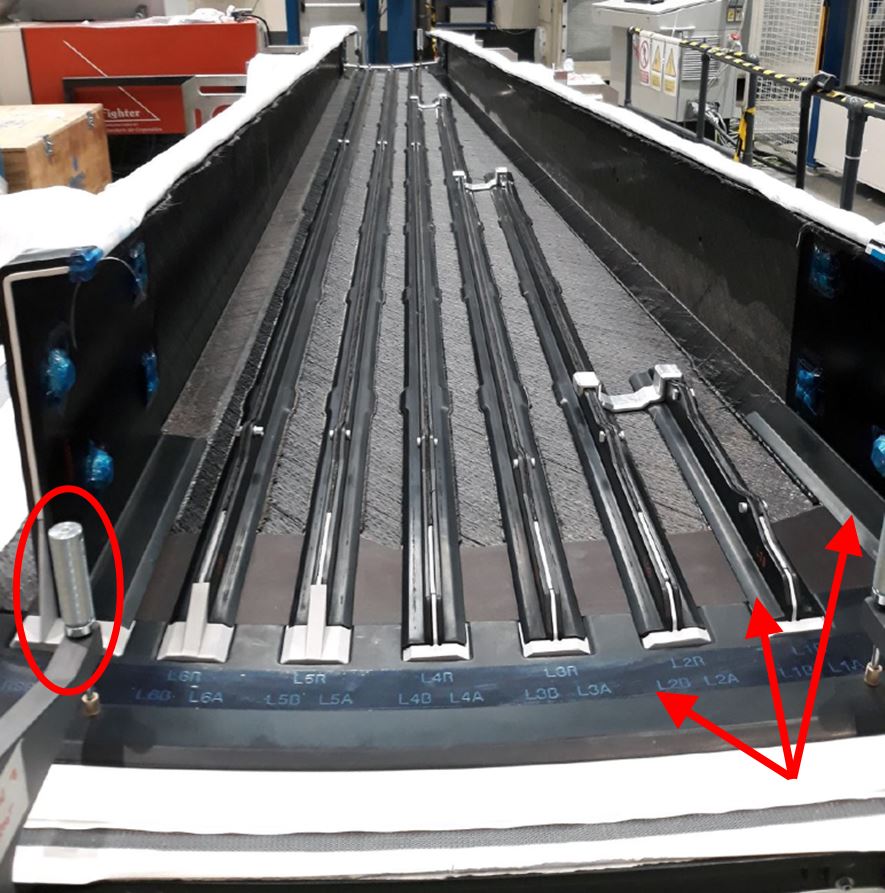
Schritt 5. Stringer- und Holm-Preforms wurden auf der unteren Haut platziert, unterstützt durch zylindrische (eingekreiste ) und weiße Positionierungselemente. Schwarze CFK-Dichtungen (Pfeile ) wurden auch verwendet, um die Stringer und . zu positionieren auf Stringern und J-Horn platziert.
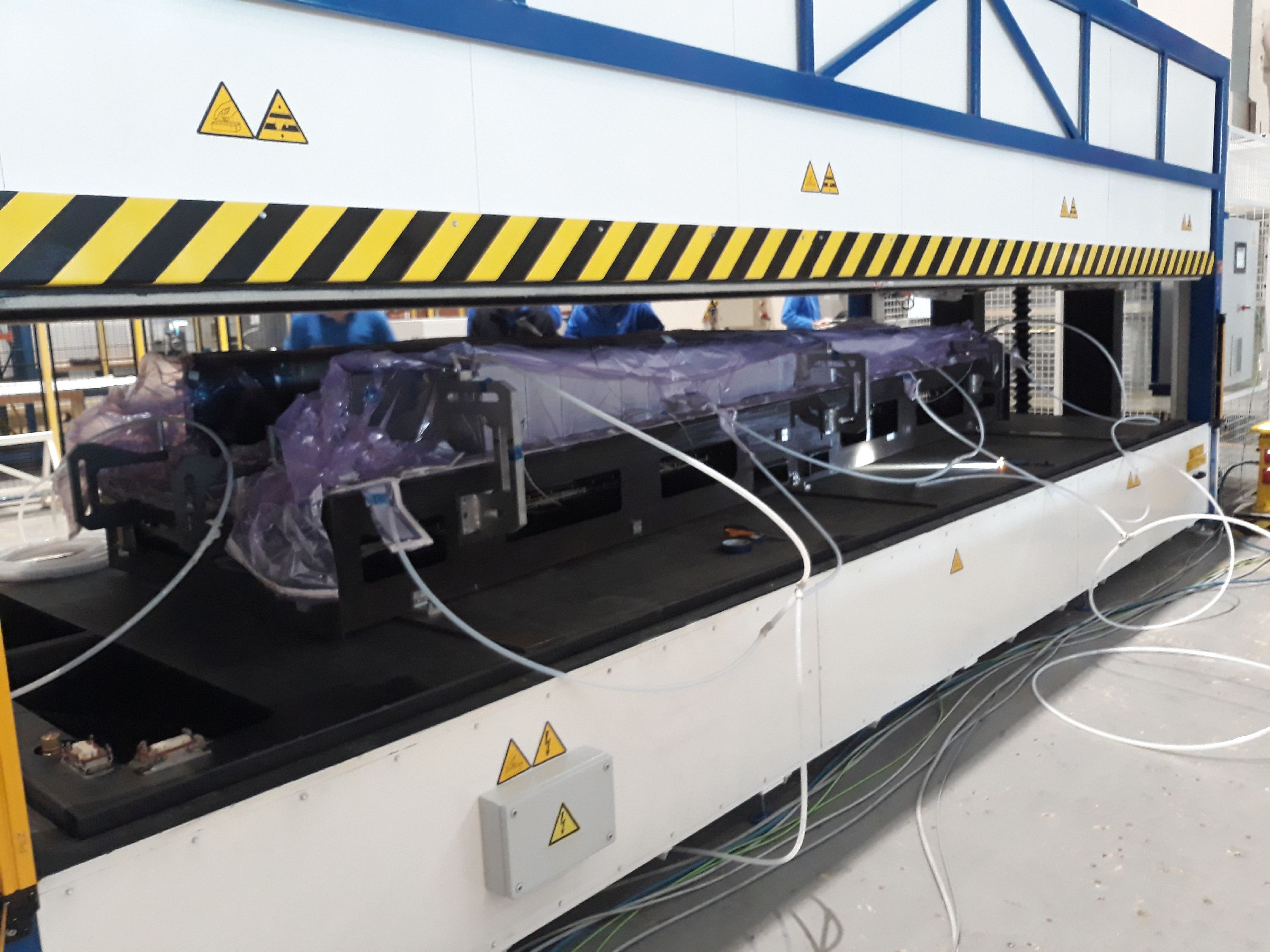
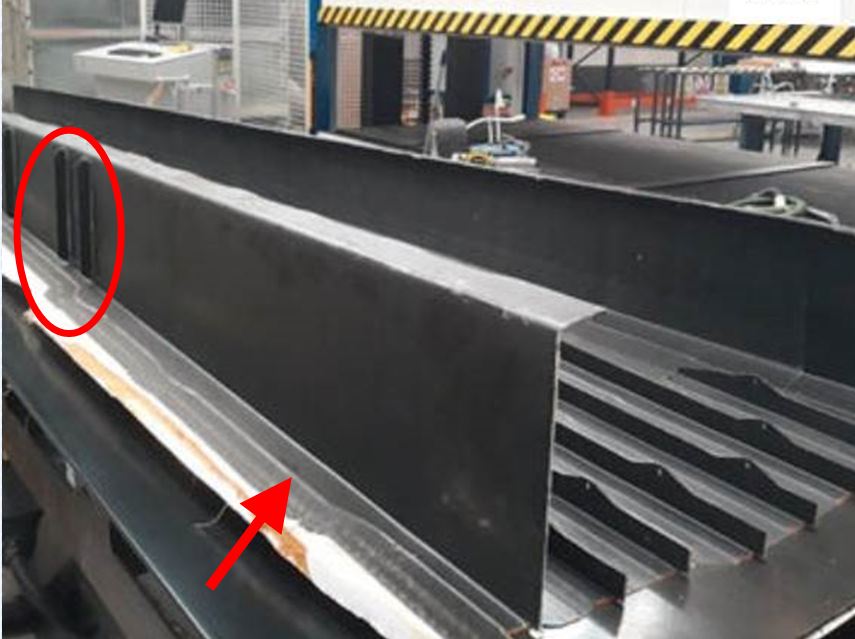
Schritt 7. Der erste Demonstrator, der bei MTorres fertiggestellt wurde, zeigt den J-Holm mit zwei Rippenversteifungen (eingekreist ) und seine sinusförmigen Füße (Pfeil ).
Der nächste Schritt bestand darin, die Vorformlinge für Stringer, Holm und Holmversteifung auf die bereits verlegte untere Flügelhaut zu platzieren (Schritt 5). „Wir haben jede Vorform indiziert, als wir sie auf das Haut- und Aushärtungswerkzeug platziert haben“, sagt Diaz. Zylinder, die als Positionierungselemente fungieren, sind am Ende des Holms links in Schritt 5 und am Ende beider Holme in Abb. 3 zu sehen. Diese Bilder zeigen auch weiße Positionierungsvorrichtungen für die Stringer und J-Holm. Es gab 13 dieser Positionierer in der endgültigen Preform-Baugruppe, und jeder war anders.
Dichtplatten waren auch ein wichtiger Bestandteil des Positions- und Platzierungssystems der Vorformlinge. Sie dienten dem traditionellen Zweck der Aufrechterhaltung eines einheitlichen Drucks und einer gleichmäßigen Temperatur über Regionen mit komplexen Schichten und/oder Geometrien, waren aber auch der Schlüssel für die Infusion, wie unten erörtert. Am Ende der Stringer und Holme ist in Schritt 5 und Bild 3 eine schwarze CFK-Abstützplatte mit Ausschnitten für die Stringer-Preforms zu sehen.
„Die Position der Stringer-Preforms hängt von der Position dieses Cauls ab“, erklärt Diaz. „Zu der von uns entwickelten digitalen Technologie zur Überwachung und Steuerung des Fertigungsprozesses gehörte eine Augmented-Reality-App, die die CATIA-Modelle auf das Layup projizierte. Dies wurde verwendet, um die Platzierung der Druckplatten, der Positionierungselemente und dann der Vorformlinge zu erleichtern. Es zeigte auch die nächsten Schritte, die durchgeführt werden müssen. Die App ermöglicht die Selbsthilfe auf Tablet-Computern, sodass alle Mitarbeiter einfachen Zugriff auf alle Informationen haben.“
Ein letzter Satz schwarzer CFK-Dehnplatten wurde dann oben auf die L-Preforms für die T-Stringer und auch entlang der Innen- und Außenseite jedes J-Holms platziert, die sich nach oben auf den Flansch und nach unten auf den Fuß an der Außenseite des Flügelkasten, wie in Schritt 5 und Abb. 3 gezeigt. „Die Holme verwenden an den Enden auch eine Art Druckplatte auf der Innenseite, um eine erhöhte Genauigkeit in den Verbindungsbereichen zu erreichen“, sagt Diaz. „Alle diese Druckplatten wurden während des HDF-Prozesses verwendet und blieben durch das Layup mit den Preforms verbunden.“
Die fertige trockene Vorformanordnung mit Dichtungsplatten wurde dann mit Abziehlage und einer Vakuumbeutelfolie bedeckt. Die gesamte Anordnung aus Haut, Stringern und Holmen wurde dann in das ACTI gegeben und das Werkzeug auf 120°C erhitzt. Hexcel RTM6 Epoxidharz wurde auf 70 °C erhitzt und vor der Infusion durch eine einzige Harzzufuhrstelle entgast. „Der ACTI war darauf vorbereitet, Harz von vier Standorten aus zuzuführen“, bemerkt Diaz, „aber nach umfangreichen Simulationen und Tests haben wir entschieden, dass es einfacher und billiger ist, einen einzigen Harzeinlass zu haben.“
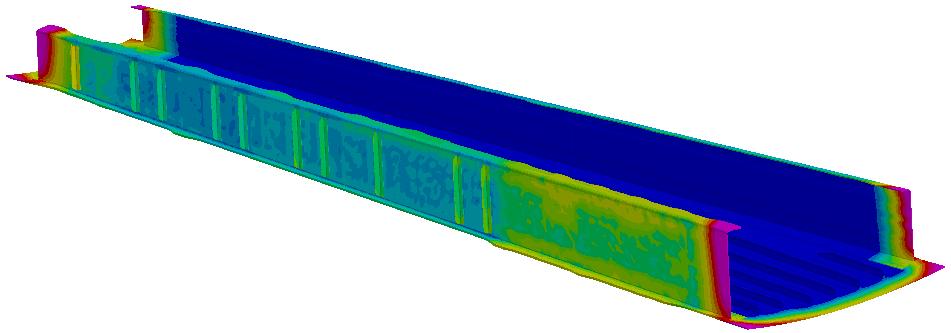
Selbst mit einem einzigen Einlass war der Infusionsprozess sehr komplex und umfasste drei verschiedene Modi. „Wir haben zuerst eine Strömungssimulation mit PAM-RTM-Software [ESI Group, Paris, Frankreich] durchgeführt“, sagt Diaz. „Für eine vollständige Benetzung war eine so komplexe Mischung aus Fließfronten und Parametern erforderlich. Zum Beispiel war der Harzfluss in der Mitte des Flügelkastens schneller, aber es war eine Herausforderung, alle Versteifungen zu benetzen.“
VAP, mit einer semipermeablen Membran, funktionierte gut für die untere Haut, die jedoch entlang der Stringer und an der Innenseite der Holme gegen Hochtemperatur-Strömungsgewebe ausgetauscht wurde. „Die Ecken waren am schwierigsten zu benetzen“, bemerkt Diaz, „aber sie waren auch am kritischsten für die Einhaltung der Toleranzen bei der Montage sowie entlang der Kanten.“ Dies ist in den roten Bereichen der Strömungssimulation in Abb. 4 zu erkennen. „In diesen Bereichen wurde ein maßgeschneiderter Ansatz entwickelt, um die benötigten Abmessungen exakt zu erreichen“, erklärt er. Wir haben auch Vakuumanschlüsse entlang des Umfangs und oben auf den Holmen verwendet.“
Die Infusion war relativ schnell, wie durch Simulationen vorhergesagt, gefolgt von einer zweistündigen Härtung bei 180 °C, wobei nur heiße Luft und keine erhitzten Werkzeuge verwendet wurden. Nach der Entformung wurde jeder Wing-Box-Demonstrator anschließend mittels Ultraschallprüfung (UT) geprüft. Dies geschah im Rahmen der Ergebnisse des IIAMS-Projekts, um die Qualität der Demonstratoren zu analysieren. Die industrielle Anwendung dieses Verfahrens wird jedoch die traditionelle NDT zugunsten digitaler Sensoren und schnellerer Inline-Inspektionstools wie Vision-Systeme reduzieren.
Obwohl der Infusionshärtungszyklus dem einer autoklavgehärteten Prepreg-Flügelbox ähnlich war, sollte die Gesamtzykluszeit laut Diaz kürzer sein. „Wir haben im Nachhinein den Großteil der Montage eliminiert und müssen auch nichts wie bei Prepreg unterfüttern, aber unsere Qualität ist dieselbe. Zum Beispiel benötigt die Verbindung zwischen der letzten Hautschicht und der ersten Schicht eines Stringers keine Klebefolie in der Mitte, um die mechanischen Eigenschaften zu verbessern und Toleranzen zu berücksichtigen.“ Dies ist offensichtlich effizienter, aber er stellt fest, dass die Teileproduktionsrate anfänglich nicht der treibende Faktor war. „Diese Methode konkurriert nicht mit der Fertigung einzelner Teile, sondern mit einer fertigen Flügelkastenbaugruppe.“
Vollständige Demonstratoren, Weg zur Zertifizierung
„Wir hatten nur 18 Monate Zeit, um dieses Projekt abzuschließen, das die Entwicklung des Prozesses und der Werkzeuge sowie die Herstellung der Werkzeuge und Demonstratoren umfasste“, sagt Diaz. „Im 14. Monat hatten wir Ende Februar 2020 den ersten Demonstrator für die Ausstellung auf dem JEC bereit [Schritt 3], aber dann wurde der JEC aufgrund der Pandemie abgesagt. Obwohl das Projekt Ende September 2020 abgeschlossen wurde, konnten wir die Monate, in denen wir aufgrund von COVID-19 nicht arbeiten konnten, in Monat 16 abziehen. Wir konnten diesen sehr engen Zeitplan aufgrund unserer internen Designfähigkeiten und -fähigkeiten einhalten die Werkzeugprototypen mit unseren AFP- und CNC-Fräsmaschinen herzustellen.“
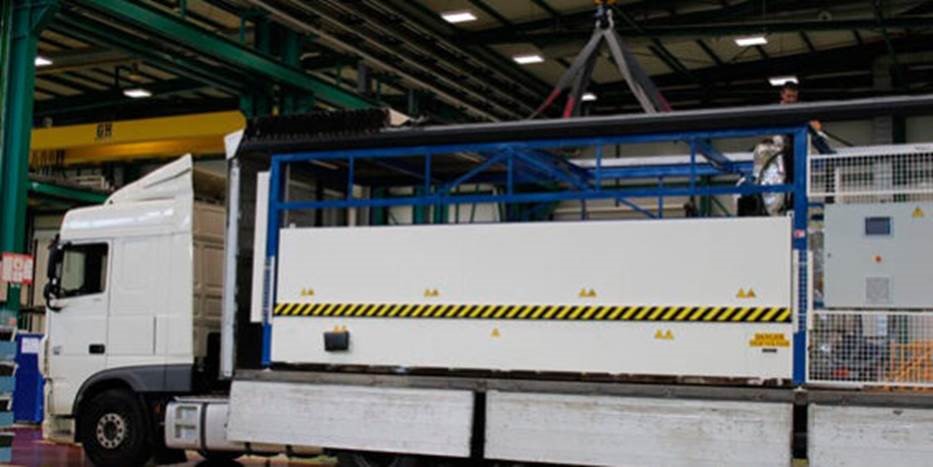
Schritt 8. Die Umform-/Aushärtungsausrüstung von ACTI und die Wing-Box-Werkzeuge wurden auf einen Standard-Umzugslaster gehoben und zu Airbus DS in Cadiz, Spanien, transportiert.
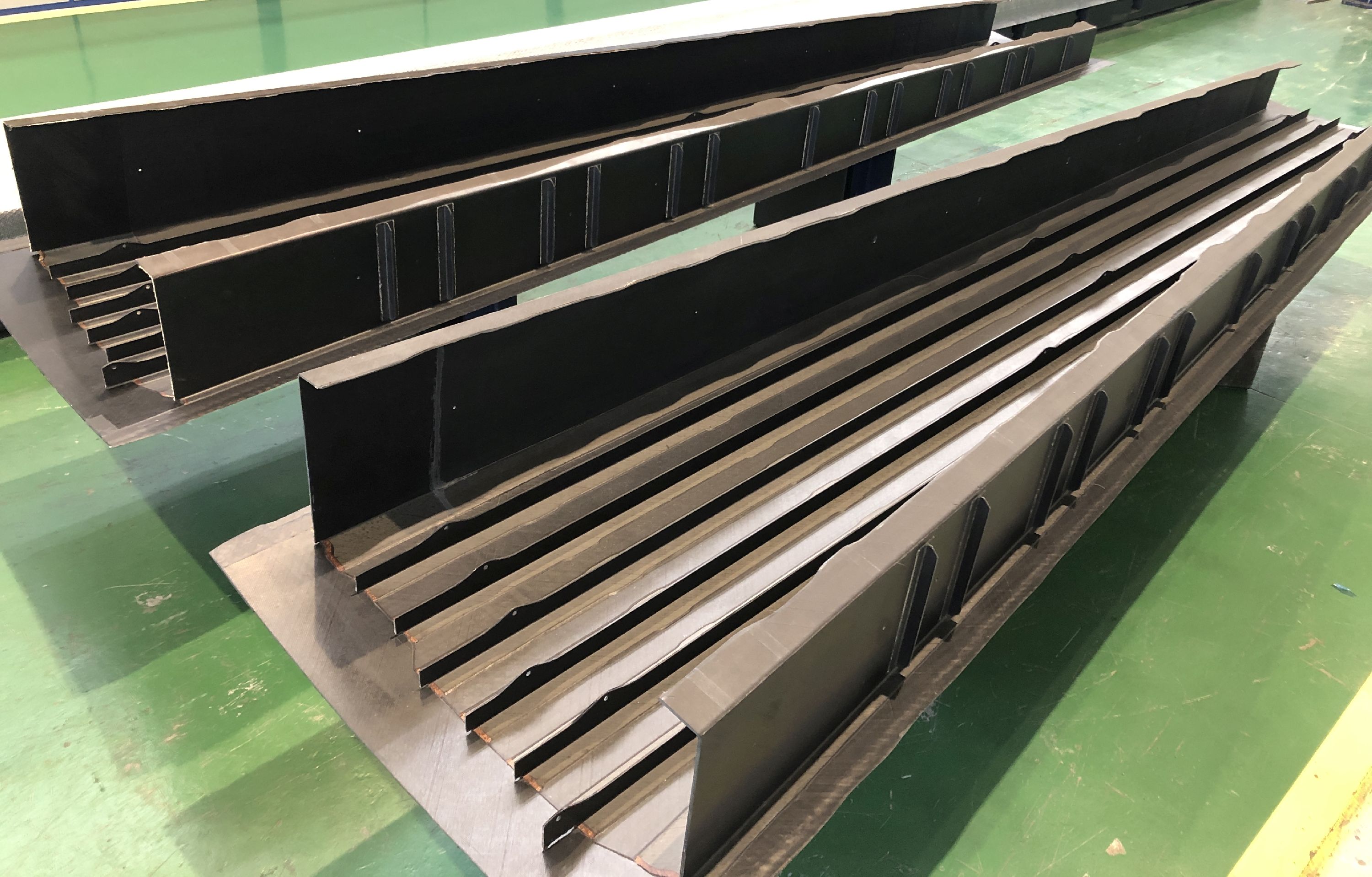
Bei MTorres wurde ein vereinfachter, 1 Meter langer Demonstrator erstellt, um alle Prozessparameter zu überprüfen. Dann wurde der erste Demonstrator in Originalgröße produziert. Werkzeug- und Fertigungsausrüstung wurden dann zu Airbus DS in Cadiz (Schritt 8) verlagert, wo der endgültige Demonstrator produziert wurde. Dies war auch Teil der Projektergebnisse und bewies, dass die Ausrüstung leicht transportiert und an mehreren Standorten installiert werden konnte.
Wie in der Seitenleiste „IIAMS Wing Box Roadmap to Certification“ erläutert, hat Airbus DS eine Schlüsselrolle im Clean Sky-Programm gespielt und wurde vom Co-Leiter des integrierten Technologiedemonstrators (ITD) Green Regional Aircraft (GRA) in Clean Sky, zum Co-Leiter des AIRFRAME ITD sowie zum Leiter des Flight Testbed 2 (FTB#2) in der REGIONAL Integrated Aircraft Demonstrator Platform (IADP) innerhalb von Clean Sky 2. Das FTB#2 wird andere Verbundwerkstoffe und Flugzeugzellen umfassen Entwicklungen, auch im Cockpit und anderen Flügelkomponenten.
Tatsächlich sind alle Projekte zur Vorbereitung des FTB#2 Teil einer umfassenderen, langfristigen Strategie bei Airbus. Ziel ist es, eine zukünftige Turboprop-Flugzeugzelle zu entwickeln, die leichter und effizienter ist, sowie Produktionsprozesse, die billiger und energiesparender sind, Flüssigkeiten und Hilfsstoffe herstellen, aber auch weniger Schrott erzeugen und eine höhere Recyclingfähigkeit bieten.
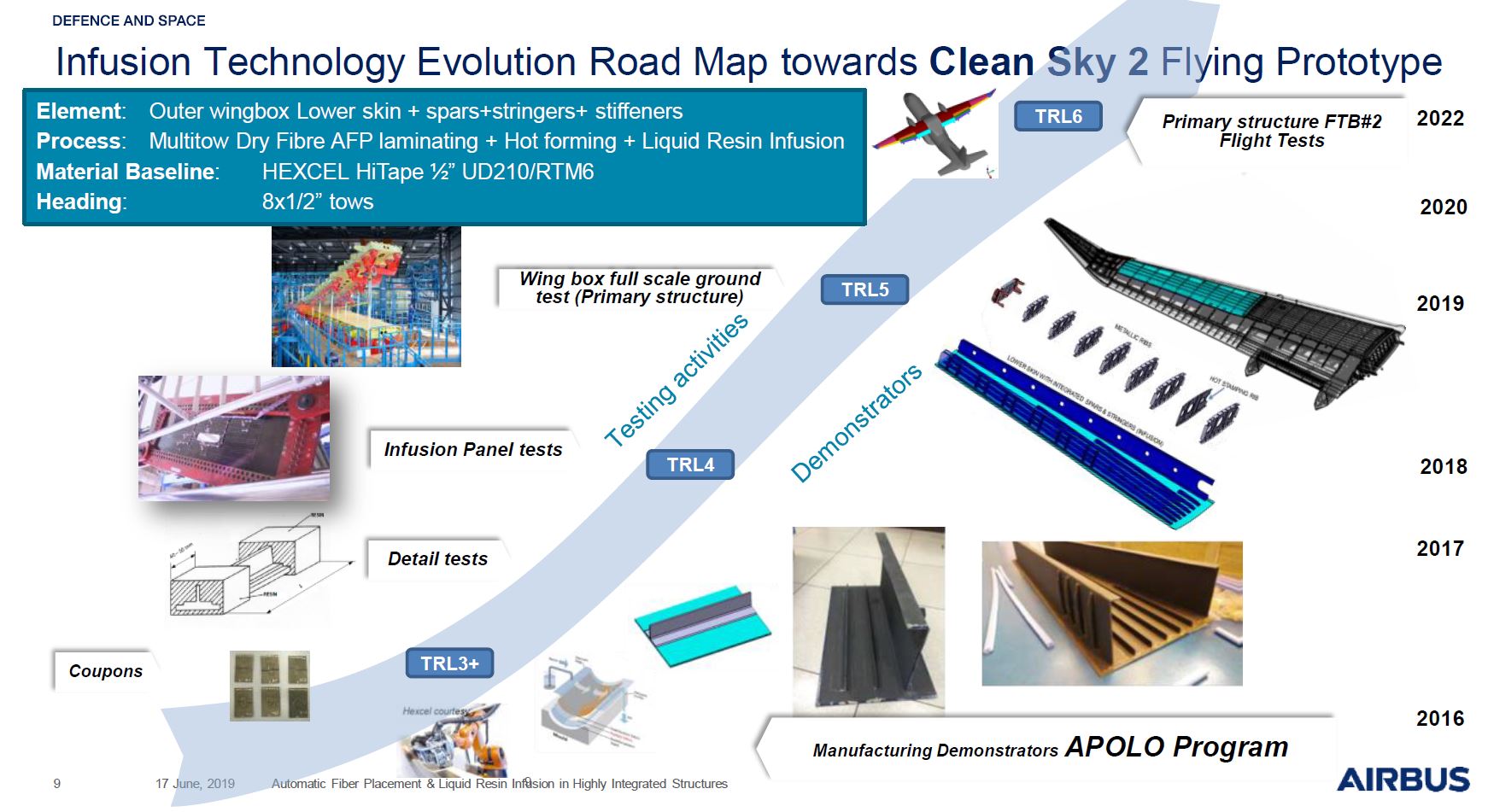
„Schritt für Schritt durchlaufen wir [Airbus DS] die gesamte Testpyramide der Flugzeugstruktur, von Coupons bis hin zu den vollständigen strukturellen Tests des Außenflügels“, erklärt A.E. Jiménez Gahete in einem Materiales Compuestos . vom September 2020 Artikel mit dem Titel „Hochintegrierter Flügelkastenabschnitt von Airbus Defence and Space, hergestellt durch Trockenfaserplatzierung und Flüssigharzinfusion“. Materialcharakterisierungstests, eine Testmatrix für Konstruktionsdetails und Unterkomponententests für zulässige Konstruktionen wurden alle mit positiven Ergebnissen abgeschlossen. MTorres half bei diesen Tests, einschließlich der Herstellung von Testcoupons und -teilen sowie Demonstratoren, um den Herstellungsprozess und die Konstruktionsdetails der Flügelbox zu validieren. Laut Gahete bleiben nur die letzten vollständigen statischen und funktionellen Tests des Außenflügels, um die FTB#2-Qualifikation für den Flug zu erhalten.
„One-Shot-Infusion reduziert Gelenke, verringert das Gewicht und erhöht die Robustheit“, sagt Diaz. „Das neuartige Dry Tape MTorres hat hervorragende Ergebnisse geliefert, sowohl bei der Verarbeitung – AFP, Hot-Drape-Forming und Infusion – als auch bei den strukturellen Eigenschaften des Teils.“ Er merkt an, dass in der Vergangenheit Zweifel bestanden haben, dass harzinfundierte Verbundwerkstoffe die gleichen strukturellen Eigenschaften und Toleranzen wie autoklavgehärtetes Prepreg aufweisen können.
„Die gleichen Toleranzen in einem Einzelschussprozess mit weichen [nichtmetallischen] Werkzeugen zu erreichen, war unsere größte Herausforderung“, räumt er ein. „Aber wir haben bewiesen, dass diese Technologie funktioniert und dass sie die großen Primärstrukturen herstellen kann, die für zukünftige Flugzeuge benötigt werden. Unser nächster Schritt besteht darin, die digitalen Technologien und die Portabilität des Produktionssystems weiter voranzutreiben.“
Harz
- Pigmentpulver haben der Kunststoffindustrie Glanz verliehen
- BLB Industries The BOX SMALL
- Airbus stellt die Fabrik der Zukunft vor
- Sie nehmen an der Edge Supply Chain Conference teil? So schreitet das Supply Chain Management voran
- Die Entwicklung moderner Kunststoffe
- Geschichte der Schraube
- Vespel®:Das Luft- und Raumfahrtmaterial
- Was ist die Kreislaufwirtschaft?
- Technologievorsprung im New-Work-Szenario
- Die beste Wahl:Eine Box Way CNC-Drehmaschine