Herstellung der oberen Hälfte des multifunktionalen Rumpfdemonstrators (MFFD)
Dieser Blog folgt einer Präsentation des Deutschen Zentrums für Luft- und Raumfahrt (DLR, Stuttgart und Augsburg) beim Symposium der TU München im vergangenen Herbst und CW 's im gleichen Zeitraum veröffentlichte Zusammenfassung "Moving forward on the Multifunctional Fuselage Demonstrator (MFFD)". Das Projekt wurde auch in einem Vortrag von Lars Larsen um 9:35 Uhr am Tag 3 der ITHEC 2020 beschrieben:„Process Data-driven Advancement of robot-based, Continuous ultraschallschweißen für die staubfreie Montage von Future Fuselage Structures“.
„Die große Herausforderung besteht darin, zu zeigen, dass die Produktionskosten durch den Einsatz von Automatisierung deutlich gesenkt werden können“, erklärt Larsen. Für die obere Hälfte des MFFD beinhaltet dies die in-situ-Konsolidierung durch automatisches Tapelegen/Faserplatzieren (ATL/AFP) zur Vermeidung des Autoklavens und staubfreies/staubfreies Schweißen für die Montage. „Damit soll es zukünftig möglich sein, die Reihenfolge von Bauteil- und Endmontagelinien zu ändern“, sagt Larsen, „so dass Systeme vorher integriert werden können Montage." Dies liegt daran, dass das Schweißen im Gegensatz zur Bearbeitung von Befestigungslöchern keine Späne oder Ablagerungen erzeugt, die vorinstallierte Systeme wie dezentrale elektrische Energie, Innenausstattung usw. beschädigen könnten.
Dieser Blog basiert auf meinem Interview mit Sebastian Nowotny, Leiter Bauteilkonstruktion und Fertigungstechnologien am DLR-Institut für Struktur und Konstruktion (BT, Stuttgart) und Frederic Fischer, Technischer Leiter Thermoplastische Composite-Produktion am DLR-Zentrum für Leichtbau Produktionstechnik ( ZLP, Augsburg). Fischer ist zudem Projektleiter für die MFFD-Obere Hälfte beim DLR.
HINWEIS:In der Abbildung oben beziehen sich gleitgeformte Stringer auf einen Prozess, der in Clean Sky 2 von Applus+ Labaoratories developed entwickelt wurde (Barcelona, Spanien), siehe mein Blog 2017 zum Gleitformen, und heißgepresste Clips beziehen sich auf das Stanzen, siehe:
- Beschleunigung thermoplastischer Verbundwerkstoffe in der Luft- und Raumfahrt
- Thermoplastische Verbundwerkstoffe „clippen“ Zeit, Arbeit an kleinen, aber entscheidenden Teilen
- In einer Brutstätte für thermoplastische Verbundwerkstoffe
Kombination von Struktur, Kabine und Systemen
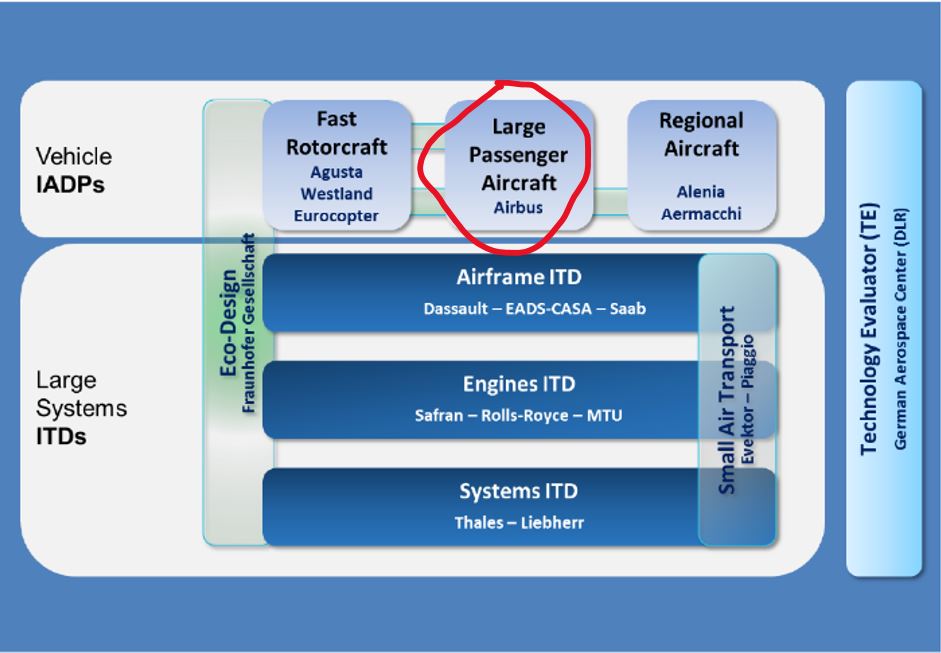
Ich fragte Nowotny nach der Geschichte der oberen Hälfte des MFFD. „Als Clean Sky 2 startete, wurde die erste Aufforderung zur Einreichung von Vorschlägen veröffentlicht“, antwortet er. „Ich glaube, wir haben 2015 angefangen und die Ausschreibung für das Projekt ICASUS gewonnen, das ein Co-Partner-Projekt für das Programm für große Passagierflugzeuge (LPA) war. Das Hauptaugenmerk lag auf der Gestaltung eines multifunktionalen Rumpfes. Damals war es kein thermoplastischer Verbundstoff. Das Hauptziel war es, den Rumpf, die Kabine, die Systeme und die Struktur in einem Designprozess zu kombinieren. Die dort geleistete Arbeit ist also im Grunde das, was jetzt zum multifunktionalen Rumpfdemonstrator (MFFD) geworden ist und ist die technologische Unterstützung für unsere Arbeit im Oberschalenprojekt.“
ICASUS
Das ICASUS-Projekt zielt darauf ab, multifunktionale und hochintegrierte Lösungen für den multifunktionalen Flugzeugrumpf der nächsten Generation, Kabine und Systeme zu entwickeln. Der Herstellungs- und Montageprozess von Single-Aisle-Flugzeugen wird heute durch kostspielige und zeitaufwändige sequenzielle Schritte angetrieben. Insbesondere die Major Component Assembly (MCA) und Final Assembly Line (FAL) sind Engpässe, die schnellere und beschleunigte Prozesse verhindern. Aus diesem Grund wird ICASUS ein neues Konzept für die Herstellung und Montage zukünftiger Single-Aisle-Flugzeuge entwickeln:
- Hochgeschwindigkeitsproduktion von 60 Flugzeugen/Monat;
- Reduzierung der wiederkehrenden Rumpfkosten um 1 Million € im Vergleich zum Referenzmodell A321 ACF („Advanced Cabin Flex“);
- Reduzierung des Rumpfgewichts um 1 Tonne gegenüber dem A321 ACF.
Der Ansatz besteht darin, die ursprünglich autarken Disziplinen Kabine/Ladung, Systeme und Struktur zu kombinieren, um die erfolgversprechendste Kombination und Integration der jeweiligen Funktionen und Anforderungen zu erreichen. Dies soll durch die Verwendung fortschrittlicher Materialien und die Anwendung innovativer Designprinzipien in Kombination mit der fortschrittlichsten Systemarchitektur in Kombination mit der Kabine der nächsten Generation erreicht werden.
Der Hauptgrund ist die deutliche Reduzierung des Kraftstoffverbrauchs durch den Einsatz von Systemen mit geringem Gewicht und Systemarchitektur/-integration. Dies erfordert ein multidisziplinäres Gesamtoptimierungsverfahren sowie die Entwicklung und Anwendung eines ganzheitlichen Industrie 4.0-Ansatzes. Design für automatisierte Fertigung, Automatisierung, Sensorisierung, Datenanalyse und sicheren Datenaustausch soll genutzt werden. Wesentliche Ziele bei der Herstellung des MFFD sind der Nachweis einer wirtschaftlichen und großserientauglichen Fertigung multifunktionaler Verbundstrukturen und die Mitwirkung an Zertifizierungskonzepten für thermoplastische CFK-Verbindungen (z. B. Schweißen).
Wie vereinen Sie Rumpfkabine, Systeme und Struktur zu einem? „Man hätte immer noch diese Disziplinen mit ihren jeweiligen Anforderungen, aber ich denke, das Hauptziel ist der Ansatz, schon in einem frühen Stadium zusammenzuarbeiten“, erklärt Nowotny. „Es gab strenge Regeln für den Entwurfsprozess des Flugzeugrumpfs, die Einschränkungen geschaffen und ein vollständig optimiertes Flugzeugdesign verhindert haben. Die ursprüngliche Idee, Struktur, Kabine und Systeme zu kombinieren, war ein Designprozess, der diese drei Aspekte zusammenführt und dann versucht, das globale Optimum zu finden, nicht nur eines für die Kabine und dann eines für die Struktur und dann eines für die Systeme . Aber natürlich gibt es viele Regeln und das ist kein einfacher Prozess, da er auch eine Zertifizierung beinhaltet.“
„Es ist ein fortlaufender Prozess in dem Sinne, dass eine digitale Plattform eingerichtet wurde und alle europäischen Partner an diesem einzigen digitalen Design mitwirken“, sagt Fischer. „In den letzten Jahren wurde dieses integrierte Design für das MFFD weiterentwickelt. Unser Team liefert die obere Hälfte mit Vorkehrungen für die Kabinen- und Systembefestigung. Die Vision ist es, die Endmontage durch die Lieferung komplett ausgestatteter Hauptkomponenten zu revolutionieren.“
Obwohl das DLR bereits an dem Designprojekt für MFFD beteiligt war, erhielt es erst 2019 den endgültigen Startschuss für das Fertigungsprojekt. Das Konsortium zum Bau der oberen Hälfte umfasst Airbus als Gesamtprojektleiter des MFFD, Premium Aerotec (Augsburg, Deutschland). ). Im vergangenen Jahr, so Fischer, „haben wir das Design der oberen Hälfte verfeinert, um sicherzustellen, dass es mit den ausgewählten Technologien hergestellt werden kann.“
In-situ-Konsolidierung
Während die untere Hälfte des MFFD mit ATL und AFP hergestellt wird, gefolgt von einer Autoklavenkonsolidierung, wird die obere Hälfte während ATL/AFP in-situ-Konsolidierung verwendet. Wieso den? „Um den maximalen Output aus dem Forschungsprojekt zu erzielen, haben wir uns entschieden, die Baseline in Frage zu stellen“, sagt Fischer, „und die Gelegenheit zu nutzen, eine Technologie als Ergänzung zur unteren Hälfte einzusetzen.“ Nowotny fügt hinzu:„Wir haben gezeigt, dass es sich um eine sehr vielversprechende Herstellungsmethode handelt, die sich auf eine schlanke Produktion konzentriert, die Fertigungsschritte reduziert. Aber ich denke, es ist klar, dass es kein einziges Herstellungsverfahren gibt, das allen Zwecken dient. Sie müssen immer noch von Fall zu Fall entscheiden, welches das optimale Herstellungsverfahren für jedes Teil ist.“
Zwei Schweißarten
Eine weitere Wahl für die obere Hälfte war der Einsatz von zwei unterschiedlichen Schweißtechnologien. „Für die Stringer setzen wir roboterbasiertes Ultraschall-Endlosschweißen ein, weil das unserer Meinung nach die am besten geeignete Technologie für wirklich lange Verbindungen und insbesondere für die Stringer-Konfiguration ist“, erklärt Fischer. Für die Integration der Rumpfspanten wurde Widerstandsschweißen gewählt. „Diese Entscheidungen sind das Ergebnis intensiver Analysen, die wir zu Beginn des Projekts zusammen mit Premium Aerotec durchgeführt haben. Wir haben uns die verschiedenen Schweißszenarien angesehen, was und wo verbunden werden musste.“
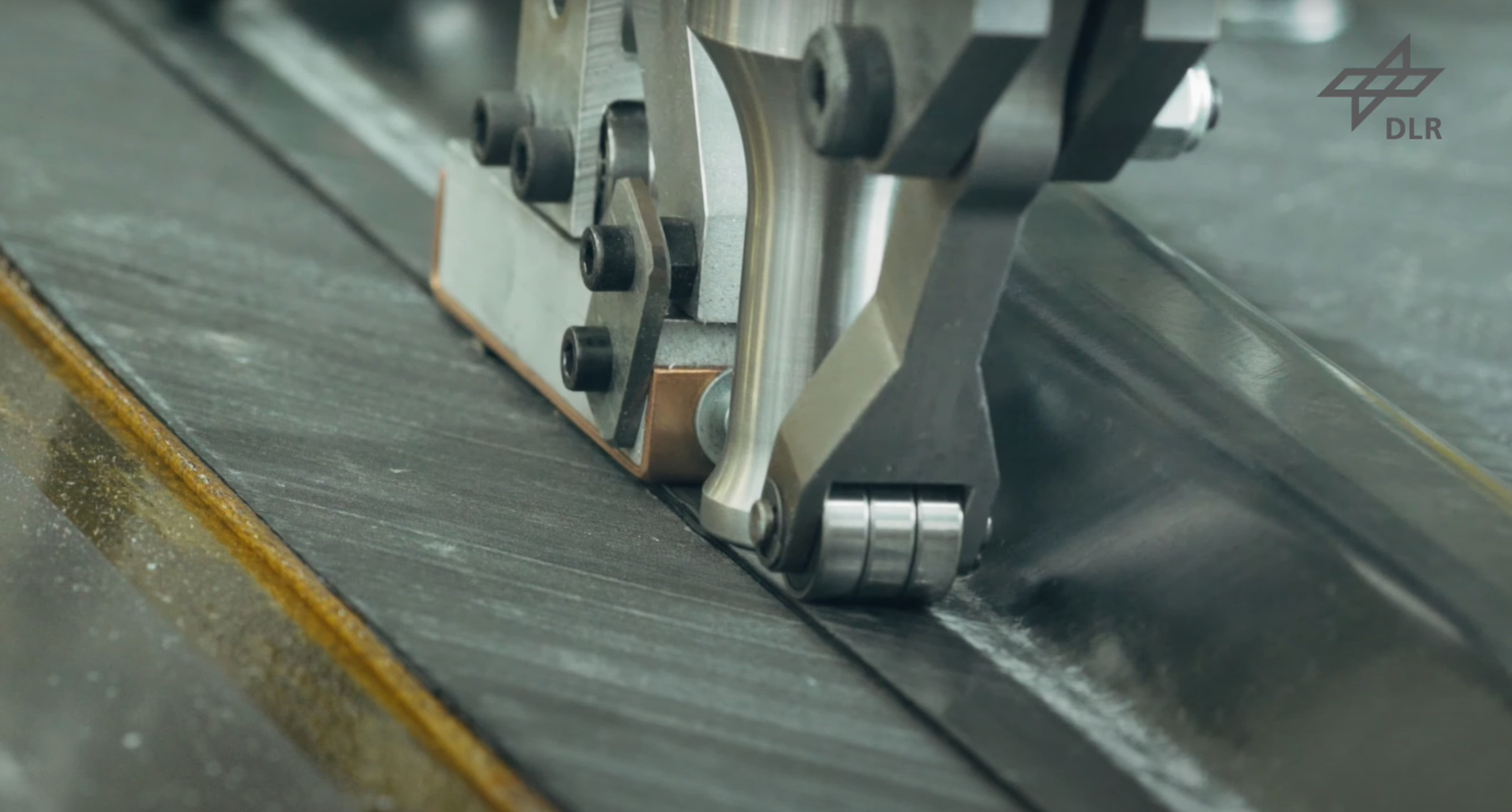
Das vom DLR entwickelte kontinuierliche Ultraschallschweißen verwendet einen Standard-Industrieroboter. Der Schweißendeffektor besteht aus einer vorlaufenden Walze, einer 25-Millimeter-Durchmesser-Sonotrode und einer nachfolgenden Verdichtungseinheit. Der Endeffektor ist mit mehreren Sensoren ausgestattet, was eine Inline-Prozessüberwachung ermöglicht. Durch die Verwendung des Roboters als Manipulator, wie im Video unten gezeigt, können eine Vielzahl von Geometrien, wie beispielsweise ein gebogenes hinteres Druckschott oder Omega-Stringer auf eine Haut geschweißt werden.
„Wir haben also zwei Prozesse mit einem großen Unterschied“, sagt Fischer. „Man ist ein kontinuierliches Prozess und der andere ist ein diskontinuierlicher Prozess. Für die 8 Meter langen Fugen der Z-Stringer haben wir uns für kontinuierliches Ultraschallschweißen entschieden. Und für den hochkomplexen Anwendungsfall – in Bezug auf Zugänglichkeit und Toleranzmanagement – die angesetzten Flansche der Rahmen mit der Haut zu verschweißen, haben wir uns für das Widerstandsschweißen entschieden. Wir werden das Widerstandsschweißelement an die Rahmengeometrie anpassen und vorrüsten und verfügen über ein klammerartiges Schweißwerkzeug, das pneumatisch schließt, die Schweißelemente kontaktiert und dann den Schweißvorgang auslöst.“
Nowotny stellt fest, dass Widerstandsschweißen die höchste Reife und höhere Festigkeit aufweist, was gut zu der höheren Belastung der Verbindungen zwischen Rahmen und Stollen passt. Er weist darauf hin, dass dieser Prozess den Rahmen mit der Haut verschweißt und Schweißen Sie die Klampe sowohl an den Rahmen als auch an den Stringer.
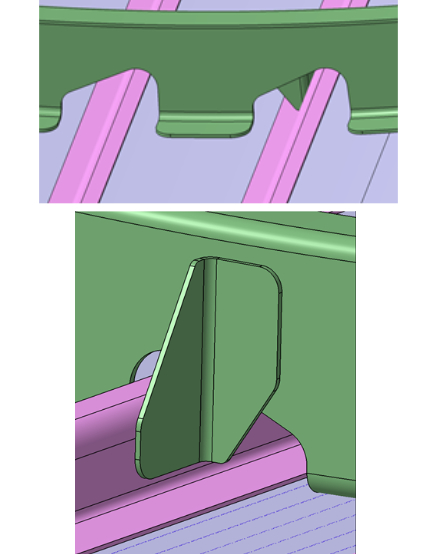
„Wir haben auf der JEC 2017 die Clip-Integration an generischen Teilen gezeigt“, sagt Fischer. Nowotny fügt hinzu:„Und tatsächlich hatten wir 2005-2008 das Projekt HISYS mit der Hochauftriebsabteilung von Airbus Bremen zum Widerstandsschweißen mit dem Thermoplast PEEK (Polyetheretherketon). Wir haben den gesamten Prozess zum Einschweißen der Rippen in die Haut auf TRL 5 gebracht. Die Grundlagen des Prozesses sind also ziemlich gut verstanden und wir können uns jetzt hauptsächlich auf die Anpassung, Automatisierung und Robustheit des Prozesses konzentrieren.“
“ Einer der wichtigsten Enabler für verschiedene Schweißtechnologien – obwohl es sie schon lange gibt – besteht darin, ihre Marktreife für den industriellen Einsatz zu zeigen“, betont Fischer, „einschließlich der notwendigen Automatisierung, Programmierung und Qualitätssicherung“. . Eines der Hauptprobleme, die wir uns ansehen, ist die Gewissheit, dass die Schweißnaht gut ist. Wir wollen sicherstellen, dass wir über die Prozessdaten verfügen, um zu zeigen, dass wir wissen, dass die Schweißnaht dauerhaft funktioniert und dass wir keine nachträgliche ZfP-Prüfung mit Ultraschall oder eine weitere Gesamtprüfung in der fertigen Baugruppe verlangen. Daher ist eines unserer Hauptziele in diesem Projekt die Entwicklung der industriellen Qualitätssicherung.“
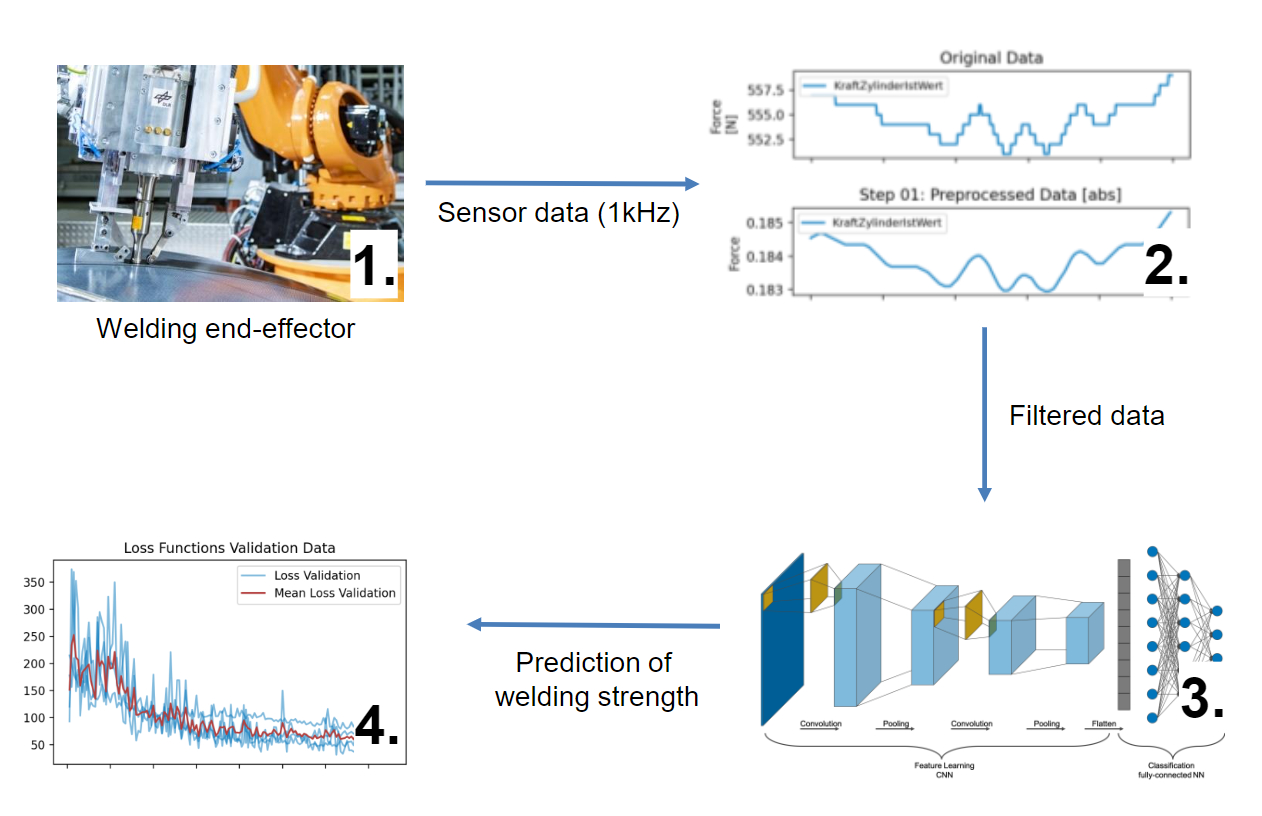
Pivoting zu LM PAEK
Wie in meinem Blog „Proving out LM PAEK Welding for Multifunctional Fuselage Demonstrator“ erläutert, war das Ausgangsmaterial, obwohl das MFFD mit Kohlefaser/PEKK (Polyetherketonketon) begann, bei der 10. Aufforderung zur Einreichung von Vorschlägen (CFP10) im März 2019 auf Kohlefaser/PAEK (Polyaryletherketon) umgestellt. PAEK ist die gesamte Polymerfamilie, in der PEEK, PEKK und LM PAEK enthalten sind. Wie viel Erfahrung hat die obere Hälfte mit LM PAEK? „Wir haben es bereits bei mehreren Herstellungsversuchen eingesetzt“, sagt Fischer. „Die Materialleistung ist sowohl beim Ultraschall- als auch beim Widerstandsschweißen sehr vielversprechend. Das Material befindet sich jedoch noch in der Entwicklung und ein Prozess des gemeinsamen Austauschs in Bezug auf gewonnene Erkenntnisse und die Entwicklung von Verarbeitungsrichtlinien wurde zwischen allen europäischen Partnern und dem Materiallieferanten eingerichtet.“
“ Aber“, fügt Nowotny hinzu, „ich finde es gut, dass wir jetzt diese Materialauswahl haben, denn vor vielen Jahren gab es nur Cytec APC-2 und sonst nichts. Vor allem in Europa konnte man manchmal das Material bekommen und manchmal bekam man „Nein, tut mir leid“. Inzwischen haben wir mehrere Materiallieferanten, die aktiv an den Materialien und auch für die verschiedenen Prozesse arbeiten. Victrex zum Beispiel, wie wir es auf dem Symposium der TU München 2020 gesehen haben, beschäftigt sich jetzt mit der Optimierung für die additive Fertigung. Es gibt auch einige Optimierungsarbeiten für die AFP-In-situ-Konsolidierung und einige für die Sekundärkonsolidierung unter Verwendung eines Autoklaven sowie verschiedene Herstellungsverfahren außerhalb des Autoklaven (OOA). Es passiert also jetzt viel mehr, und das erhöht die Chancen, für jeden Prozess ein gutes Material zu erhalten.“
Zeitplan und nächste Schritte
„Wir haben den Design-Herstellungsprozess für einen Zwischendemonstrator – A320-Durchmesser mit zwei Rahmenbuchten und 950 Millimeter Breite – im Wesentlichen abgeschlossen und werden diese kleinere Halbschale Anfang nächsten Jahres (2021) bauen“, sagt Fischer . „Außerdem haben wir mit der Beschaffung der Werkzeuge für die obere Halbschale in Originalgröße begonnen und treiben unsere Technologien hoch, um sicherzustellen, dass wir die obere Hälfte in Originalgröße termingerecht im Jahr 2022 produzieren können.“ .”
Was beinhaltet dies? Ein Problem sind Montagetoleranzen. „Die Längsfugen an der linken und rechten Seite sowohl der oberen als auch der unteren Rumpfhälfte sind schon seit längerem ausgelegt“, erklärt Fischer. „Davon haben wir bestimmte Anforderungen, und wir müssen sicherstellen, dass unsere Produktionstoleranzen diese Anforderungen erfüllen.“
„Die grundlegende Geschichte dessen, was wir mit der Oberschale versuchen, ist, die effizientesten Wege zur Herstellung von thermoplastischen Verbundwerkstoffen aufzuzeigen und einen Weg zu ebnen, der für zukünftige Flugzeuge mit Aluminium konkurrieren kann“, sagt Fischer. Dies habe das DLR bereits bei der Entwicklung eines geschweißten thermoplastischen hinteren Druckschotts in den Jahren 2018 und 2019 mit Premium Aerotec gezeigt (siehe auch „Neue Horizonte beim Schweißen thermoplastischer Verbundwerkstoffe“). Schweißen und schlanke Produktion sind wichtige Voraussetzungen für Thermoplaste. Und jetzt müssen wir diese Technologien aus dem Labor in die Industrie holen. Und damit die Industrie glauben kann, dass sie diese Schweißtechnologien wirklich nutzen kann, müssen wir zeigen, dass sie in realen Produktionsaufgaben automatisiert, vorhersehbar und zuverlässig gesteuert werden können. Und genau das tun wir.“
Harz
- Die Vorteile der Kleinserienfertigung
- Sind organische Materialien die Zukunft der Kunststoffherstellung?
- So wählen Sie den besten Lieferanten für die Kunststoffherstellung aus
- Montageroboter 101:Das Was, Wo und Wie von Montagerobotern in der Fertigung
- Neues zum Thema Reshoring in der Fertigung
- Die Rolle der Blockchain in der Fertigung
- Die 8 Verschwendungen von Lean Manufacturing
- Was gehört zum Herstellungsprozess?
- Die Zukunft des 3D-Drucks in der Fertigung
- Ist 3D-Druck die Zukunft der Fertigung?