Industrielle Produktionslinie zum Recycling von thermoplastischen Polymeren und Verbundwerkstoffen zu Organoblech
Cetim (Nantes, Frankreich) ist bereits bekannt für seinen QSP (Quilted Stratum Process) für die industrialisierte Produktion (<1 Minute Zykluszeit) von thermoplastischen Verbundteilen sowie für seine QSD (Quilted Stratum Design) Software, die solche Teile optimiert , einschließlich der Wiederverwendung von Produktionsabfällen für das Teil. Seine dritte Basistechnologie ist eine modulare Produktionslinie zur Umwandlung von thermoplastischem Abfall mit und ohne Faserverstärkung in Organoblechplatten, die wünschenswerte Eigenschaften und Kosten bieten.
Pilotlinie in Cetim Grand Est
Dieses Recyclingverfahren für thermoplastische Verbundwerkstoffe wurde von Cetim Grand Est (Mulhouse, Frankreich) entwickelt. 1977 als Cetim Cermat gegründet, fusionierte es 2018 mit CRITT Matériaux Alsace, um Unternehmen in den Regionen Elsass-Lothringen und Champagne-Ardenne in Frankreich technologisch zu unterstützen. „Cetim Grand Est ist verantwortlich für Recyclingtechnologien für Polymere und thermoplastische Verbundwerkstoffe“, erklärt Clément Callens, Business Unit Manager bei Cetim Grand Est für das in Mulhouse ansässige Team Industry of the Future, einschließlich thermoplastischer Prozess- und Online-Überwachungsprojekte. „Wir haben fünfzehn Mitarbeiter in dieser Abteilung und arbeiten mit Universitäten und Unternehmen aus den unterschiedlichsten Branchen zusammen, um interdisziplinäre Teams zu bilden, um herausfordernde Probleme zu lösen.“
„Die Pilotproduktionslinie, die wir in Mulhouse aufgebaut haben, wurde entwickelt, um der Welt zu zeigen, dass dieses innovative thermomechanische Verfahren zum Recycling von Produktionsabfällen möglich ist“, fährt Callens fort. „Diese Linie ist in der Philosophie der QSP ähnlich:ein automatisiertes System, das flexibel und modular ist, das es Unternehmen ermöglicht, die Technologie effizient und kostengünstig einzusetzen. Wir erhalten tatsächlich Schrott von der QSP-Linie in Nantes oder von anderen Kunden und recyceln ihn dann zu verschiedenen Organoblechmaterialien und -platten, mit dem Ziel, die Integrität der Verbundwerkstoffe für eine höhere Leistung im Vergleich zu herkömmlichen Materialien und traditionellen recycelten Verbundwerkstoffen zu erhalten.“
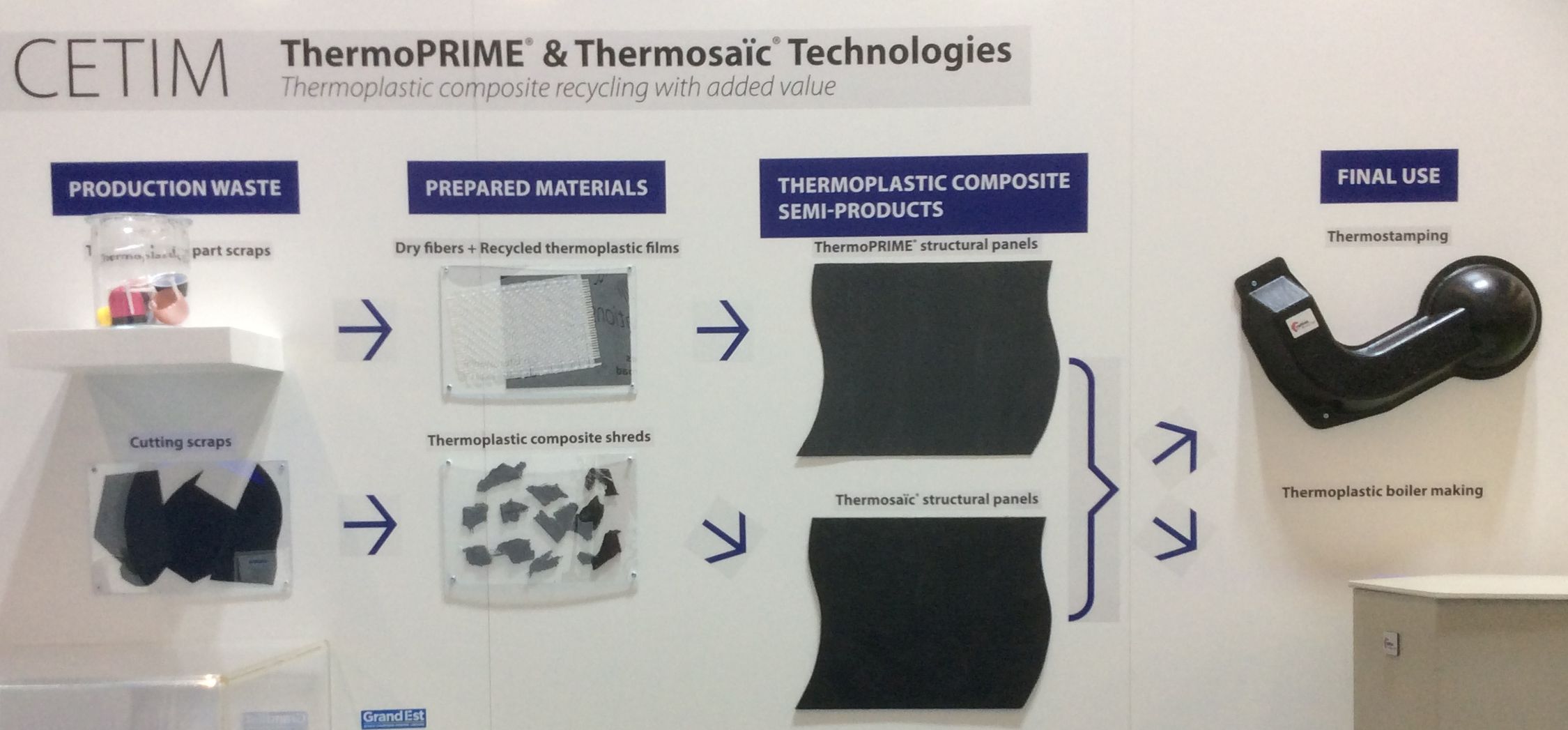
Thermosaïc und ThermoPRIME
Die Linie kombiniert zwei getrennte Ansätze:Thermosaïc und ThermoPRIME.
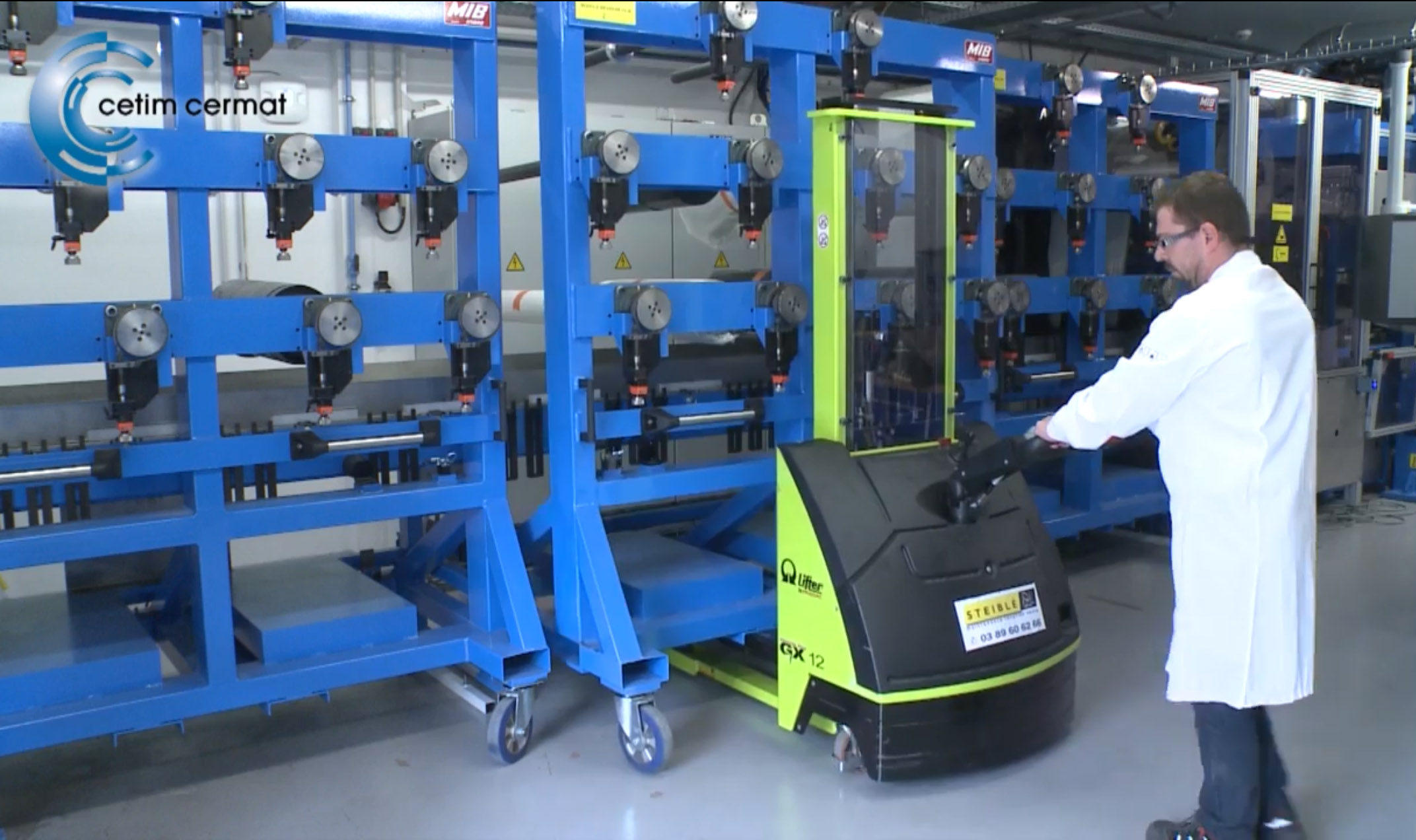
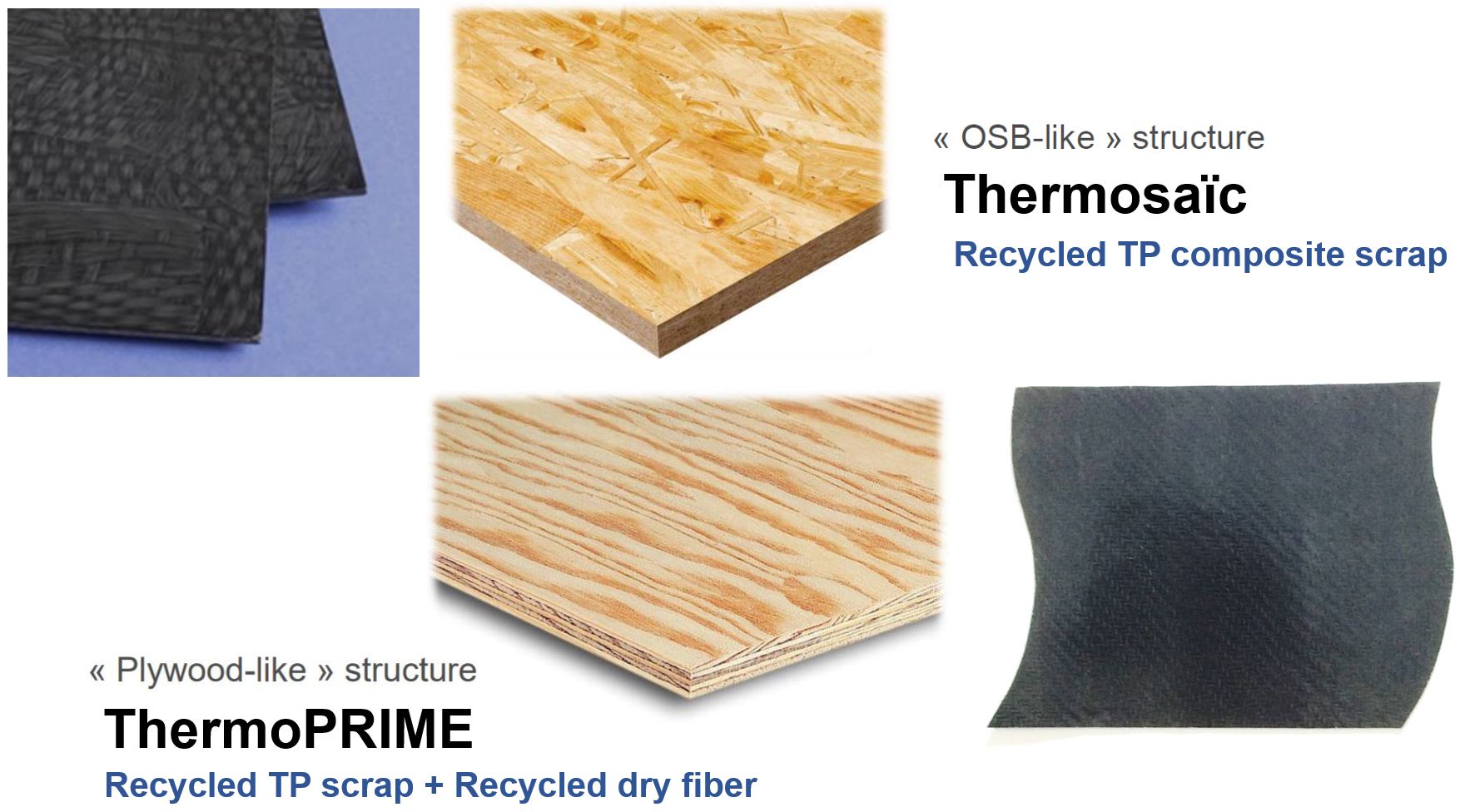
Thermosaïc nimmt Produktionsabfälle aus thermoplastischen Verbundwerkstoffen aus dem Schneiden und Besäumen (oder aus Altteilen) auf, zerkleinert sie grob und verwendet dann einen thermomechanischen Prozess, um die Schnitzel in Organoblech umzuwandeln. „Wir nennen es eine Verbundstrukturplatte“, sagt Callens, „aber es ist im Grunde wie Organoblech.“ Der Begriff Organoblech wurde in Europa entwickelt, um gewebeverstärkte thermoplastische Prepreg-, Semipreg- oder vorverfestigte Rohlinge zu beschreiben, die thermogeformt und zu Verbundteilen umspritzt werden können. Thermosaïc Produkte sind quasi-isotrop und die Faserlänge wird so lang wie möglich gehalten, um die mechanischen Eigenschaften zu maximieren. „Sie liegen in der Mitte zwischen Kurzfaserplatte und klassischem Organoblech“, stellt Callens fest. „Ziel der Technologie ist es, einen guten Kompromiss zwischen der Shred-Größe und den Eigenschaften des Panels zu finden, denn man muss immer Leistung mit Kosten verknüpfen. Der Prozess muss flexibel und kostengünstig sein, also billiger als Neuware.“
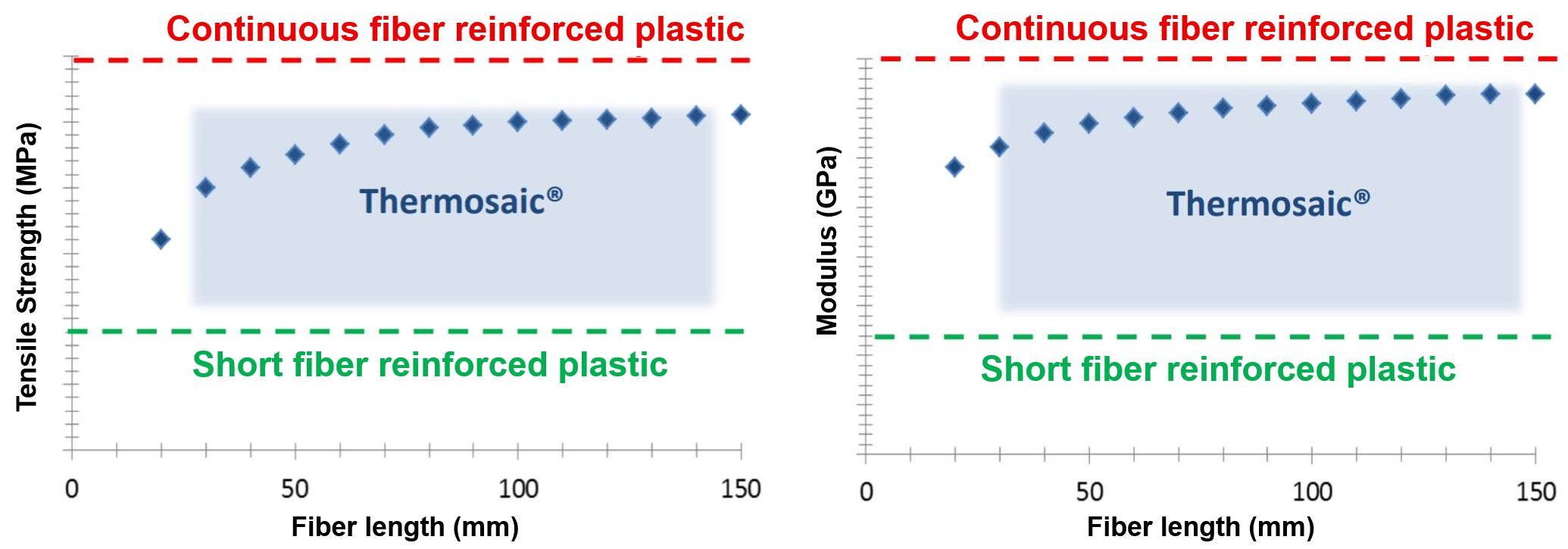
„Wir verwenden dieselbe Prozesslinie, um ThermoPRIME-Strukturplatten herzustellen“, erklärt er. „Es ist das gleiche Grundkonzept, aber bei diesem Ansatz beginnen wir mit unverstärktem thermoplastischen Schrott oder Altteilen, die zu Folien recycelt wurden. Auf dem Markt sind bereits Folien aus unterschiedlichen Materialien erhältlich. Wir fügen dann neue, natürliche, recycelte oder andere trockene Endlosfasern hinzu, um ein Organoblech herzustellen, das die gleichen Eigenschaften wie Neumaterial hat, aber zu geringeren Kosten. Die Faserimprägnierung erfolgt in einem kontinuierlichen Verfahren, das im Vergleich zur Batch-Verarbeitung von klassischem Organoblech kostengünstiger ist.“
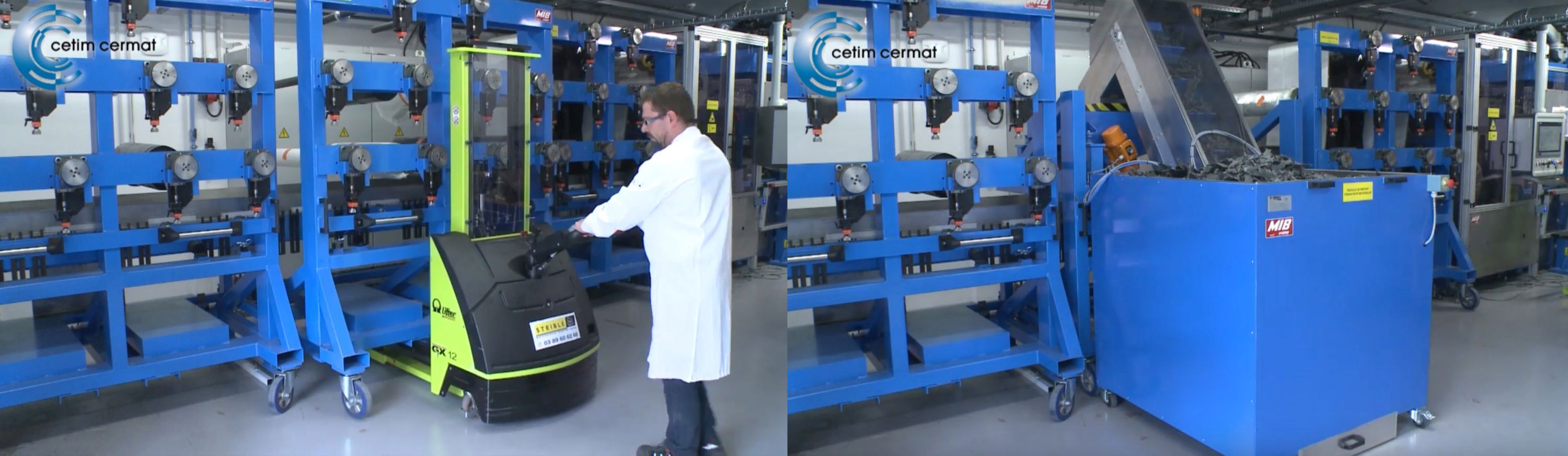
Demonstrationen, Kosteneinsparungen und Lieferkette
Bisherige Demonstrationen haben gezeigt, dass mit leistungsstärkeren Thermoplasten wie PEEK (Polyetheretherketon) oder PPS (Polyphenylensulfid) Kosteneinsparungen gegenüber Materialien wie PP (Polypropylen) erzielt werden, die als Neuware bereits kostengünstig sind. Zusätzlich zu diesen Polymeren hat das Team von Callens PA6 (Polyamid6) verarbeitet und verschiedene Arten von glasfaserverstärkten Polymerrecyclingprodukten entwickelt, in Zusammenarbeit mit Unternehmen, zum Beispiel Porcher (Eclose-Badinières, Frankreich), um produzieren Thermosaïc- und ThermoPRIME-Platten. Das Team arbeitet auch an recycelten kohlefaserverstärkten Polymerplatten.
Wie sehen Sie die Entwicklung der Recycling-Lieferkette? „Wir arbeiten jetzt daran, diese Technologie auf die Industrie zu übertragen, und arbeiten dabei mit Tier-1-Zulieferern und Materialherstellern zusammen“, sagt Callens. „Cetim Grand Est arbeitet mit der Industrie zusammen, um Konzeptnachweise und Machbarkeitsstudien abzuschließen. Außerdem arbeitet das Unternehmen in Zusammenarbeit mit dem Partner des Maschinenherstellers daran, die Linie an die spezifischen Bedürfnisse der Kunden anzupassen und gemeinsam mit den Kunden die optimalen Produktionsmodule und Parameter zu definieren.“
Thermosaïc und ThermoPRIME wurden auf der JEC World 2018 mit dem Innovationspreis für nachhaltige Entwicklung ausgezeichnet. Clément Callens wird voraussichtlich am 12. Mai auf der JEC World 2020 (Paris, Frankreich) weitere Details zu dieser Technologie präsentieren.
Harz
- BASF und Toray in Liefervertrag zur Herstellung von CFRT-Bändern für Automobil- und Industrieanwendungen
- Thermoplastisches Waben-Sandwich zum Umspritzen in dünnere, leichte Verbundwerkstoffe
- Recycling:Endlosfaserverstärkte thermoplastische Verbundwerkstoffe mit recyceltem Polycarbonat
- Anpassung von Ultraschallsensoren für die Optimierung und Steuerung von Verbundwerkstoffprozessen
- OTOMcomposite entwickelt Software für die Composites 4.0-Produktion mit lasergestützter Bandplatzierung und -wicklung
- Karl Mayer startet Produktionslinie für thermoplastische UD-Bänder
- Thermoplastische Tür eine Premiere für Automobilverbundwerkstoffe
- LANXESS erweitert Produktionskapazität für endlosfaserverstärkte thermoplastische Verbundwerkstoffe
- TPAC und TPRC entwickeln Recyclingprozess für thermoplastische Verbundwerkstoffe
- Konsortium für thermoplastische Verbundwerkstoffe strebt die Massenproduktion für die Automobil- und Luftfahrtindustrie an