Recycelte thermoplastische Verbundwerkstoffe für die Produktion
Die Recyclingfähigkeit ist ein seit langem versprochener Vorteil der Verwendung von thermoplastischen Verbundwerkstoffen (TPCs). Aber es muss noch in großem Maßstab kommerziell genutzt werden. Der Materiallieferant TenCate Advanced Composites und das ThermoPlastic Composites Research Center (TPRC) haben sich 2016 mit dem Tier-1-Hersteller GKN Fokker zusammengetan, um einen solchen Prozess zu demonstrieren. PPS) Material aus der Produktion des Gulfstream G650 Höhen- und Seitenruders von GKN Fokker. Die Produktionsabfälle wurden zerkleinert und dann mit einem von TPRC entwickelten Verfahren und einer Form formgepresst. Die Zugangstürverkleidung wies geformte Versteifungsrippen, Dickenvariationen und eingeformte Löcher mit Vorsprüngen auf. (Ein Vorsprung ist ein hervorstehendes Element, das ein Befestigungselement in das Loch führt). Die Verwendung des wiedergewonnenen Materials ermöglichte ein leichtes Teil mit größerer eingegossener Funktionalität und gleichzeitig einen geschlossenen Herstellungsprozess, da die Zugangstürverkleidung dann an der Vorderkante des Gulfstream G650-Ruders verwendet wurde. Das Projekt wurde 2016 mit einem JEC Innovation Award ausgezeichnet.
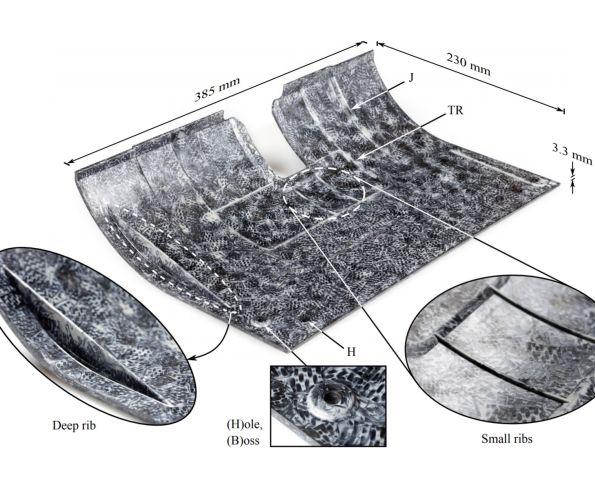
Zugangstürverkleidung 2016 demonstriert wird aus Cetex CF/PPS-Schrottmaterial hergestellt und verfügt über Versteifungsrippen und eingeformte Löcher mit Vorsprüngen. QUELLE | TPRC.
Seitdem wurde eine neue Organisation gegründet, das ThermoPlastic Composites Applications Center (TPAC). „Das TPRC wurde vor zehn Jahren gegründet und arbeitet hauptsächlich in der TPC-Grundlagenforschung für die Luft- und Raumfahrtindustrie“, erklärt Thomas de Bruijn, Forscher für Leichtbaustrukturen am TPAC. „Das TPAC wurde ungefähr zu zwei gegründet Jahren und hat eine angewandte Arbeitsweise. Es ist mit der Universität Sachsen und auch mit KMU verbunden. Wir konzentrieren uns darauf, Kosten zu senken, indem wir kostengünstigere Prozesse entwickeln. Zusammen bilden diese beiden Gruppen TPC NL, eine intelligente Industrie, ein digitales Innovationszentrum für die TPC-Technologie.“
Die Beteiligung des TPAC und auch die kontinuierliche F&E von TenCate haben gezeigt, dass diese Art der Closed-Loop-Fertigung nicht nur möglich, sondern auch wirtschaftlich vorteilhaft ist. Der Fokus liegt zunächst auf CF/PPS-Materialien, und die Forschung wird in Zusammenarbeit mit Industriepartnern durchgeführt, um die Umsetzung dieser durch TPC-Recycling verbesserten Teileproduktion zu unterstützen.
Die tatsächlich entwickelten Prozesse unterscheiden sich jedoch. TenCate hat sich auf kürzeres Fasermaterial konzentriert, das als Fließschicht verwendet wird, um geformten geometrischen Merkmalen und Funktionalität zu Endlosfaserteilen hinzuzufügen. Inzwischen haben TPRC und TPAC versucht, eine größere Faserlänge beizubehalten und ein teigartiges Material zu schaffen, das zu Teilen mit besseren mechanischen Eigenschaften formgepresst werden kann, als dies mit herkömmlichen Kurzfaser-Compounds möglich wäre.
TenCate – Organoblechteile mit verbesserter Fließschicht
„Vor drei Jahren haben wir begonnen, einen größeren Teil unseres F&E-Budgets in Recycling zu investieren“, sagt Frank ten Napel, TenCate Produktmanager für Thermoplaste. „Dabei geht es nicht nur darum, ein ‚grünes Label‘ zu bekommen. Wir sind davon überzeugt, dass die Verwendung von Recyclingmaterial in Ihrem Teil sehr reale wirtschaftliche und konstruktive Vorteile bietet. Wir können einem Teil eine Geometrieebene zuweisen, die wir sonst nicht erreichen könnten. Durch das Auftragen einer Fließschicht aus recyceltem Material können wir Versteifungsrippen mit variabler Dicke über das Teil sowie Vorsprünge um Löcher formen, die durch Befestigungselemente induzierte Lasten verteilen. All dies ermöglicht die Verwendung von weniger Endlosfasermaterial für dünnere, leichtere und kostengünstigere Teile im Vergleich zur reinen Verwendung von Neumaterial.“ Er stellt fest, dass diese geformten Eigenschaften mit Endlosfasermaterialien schwer zu erreichen sind, „aber durch die Kombination von Endlosfasern und lokalisiertem Umspritzen erhalten Sie mehr Gestaltungsfreiheit.“
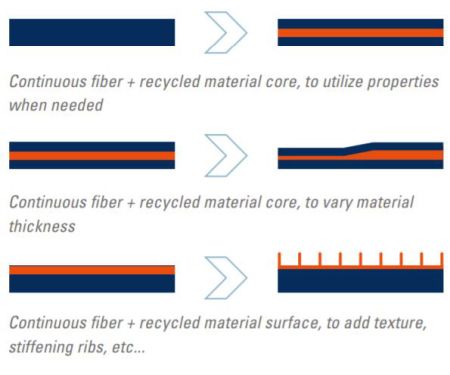

Dieser halterungsartige Demonstrator zeigt beide Seiten desselben Teils und hebt eine konventionelle gewebte Organoblechschicht und eine recycelte TPC-Fließschicht hervor. Letztere verfügt über Versteifungsrippen und Noppen für Einsätze. QUELLE | TenCate
TPC-Zyklus-Projekt
Dieses vierjährige Projekt begann im September 2015 und umfasst Partner aus der gesamten Lieferkette von thermoplastischen Verbundwerkstoffen (TPC):
- TenCate Advanced Composites (Toray Group) – Materialien
- GKN Fokker Aerostructures – Tier-1-Design und Herstellung von Luft- und Raumfahrtstrukturen und -baugruppen
- Dutch Thermoplastic Components (DTC) – SME Design und Herstellung von Rippen, Stringern, Halterungen, Clips, Boxen für die Luft- und Raumfahrt
- Cato Composites – KMU-Fertigung und Konstruktion von Teilen für die Luftfahrt-, Automobil-, Verteidigungs-, Sport- und Verbrauchermärkte
- Nido RecyclingTechniek (NRT) – Technologie zur Zerkleinerung und Zerkleinerung von zu recycelnden Materialien/Teilen
TPC-Cycle wird von TPAC und der Saxion University of Applied Sciences, insbesondere ihrer Leichtbau-Forschungsgruppe, gefördert und von Regieorgaan SIA, Teil der niederländischen Organisation für wissenschaftliche Forschung (NWO), finanziert.
Thomas de Bruijn ist TPC-Cycle-Projektleiter und Forscher für Leichtbaustrukturen bei Saxion/TPAC. Er erklärt, dass es viele Treiber für den Start des TPC-Cycle-Projekts gab. „Wir konnten eine Zunahme der Verwendung von Endlosfaser-TPCs feststellen, insbesondere für die Stanzformung, wie in Clips und Klammern. Mit dieser Zunahme wird die Menge an postindustriellem Abfall beträchtlich. Recycling war also notwendig, sowohl für die Umwelt als auch wirtschaftlich, aber auch um den Vorschriften zu entsprechen. Zum Beispiel verlangt die europäische Gesetzgebung für Altautos, dass 95 % des in Autos verwendeten Materials recycelt werden.“ Auch Airbus habe sich Recycling- und End-of-Life-Ziele gesetzt und diese an seine Lieferanten kommuniziert. „Die Lieferkette sollte nicht nur sagen, dass sie diese Ziele erreichen kann, sondern diese Fähigkeit auch mit Demonstratoren beweisen“, fügt de Bruijn hinzu.
„Wir haben auch gesehen, wie TPCs außerhalb der Luft- und Raumfahrt wachsen, in Anwendungen wie Lebensmittelkisten, Möbeln und Industriekomponenten, weil sie kürzere Zykluszeiten, leichte und intelligentere Strukturen bieten“, sagt de Bruijn.
Er fährt fort:„Wir wollten eine wirtschaftlich tragfähige Recycling-Prozesskette beweisen, aber nicht nur das Mahlen, das Downcycling ist. Wir wollten hohe Leistung. Daher haben wir uns für einen Mischansatz mit geringer Scherung entschieden, um eine Faserlänge von 0,5 bis 1,0 Zoll beizubehalten. Für die Steifigkeit benötigen Sie nur ein paar mm Länge. Aber für Festigkeit und Schlagfestigkeit braucht man mehr als 0,5 Zoll Länge.“ Neben der Beibehaltung der Faserlänge bestand eine weitere wichtige Herausforderung darin, eine gute Homogenität beim Mischen der Materialien und im recycelten Endprodukt zu erreichen.
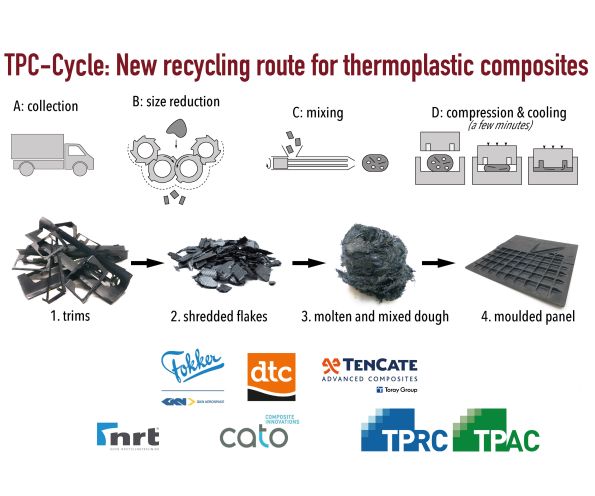
„Das Ziel ist es, Abfälle zu sammeln, zu 0,5-1,0-Zoll-Flocken zu zerkleinern und in einen homogenen Teig zu verwandeln, der extrudiert und direkt in eine Formpresse überführt wird“, erklärt TPRC-Forscher und Ph.D. Schüler Guillaume Vincent. „Die Verarbeitung des Teigs erfolgt über die Zuführung von Flocken und frischem Polymergranulat in einen scherarmen Mischer, wodurch der Fasergewichtsanteil auf 25-40% reduziert wird.“ Er stellt fest, dass der Prozess dem in der Automobilindustrie üblichen Direktcompoundieren von Langfaser-Thermoplasten (D-LFT) sehr ähnlich ist. „Allerdings erfordern D-LFT-Verfahren Investitionen in Millionenhöhe und werden daher nur in der Hochserienfertigung eingesetzt. Wir haben unseren Ansatz modifiziert, indem wir kleinere Maschinen verwendet haben, aber wir erhalten ähnliche Ergebnisse. Unsere Volumina sind im Vergleich zu D-LFT-Prozessen gering.“
Vincent beschreibt ein Beispiel, wo sich die Einbeziehung der kompletten Recycling-Wertschöpfungskette auszahlt:„NRT hat uns geholfen, uns mit Herstellern größerer Zerkleinerungsmaschinen wie Untha zu verbinden.“ Dies ist ein wichtiger Teil der Skalierung des Prozesses für die Serienteileproduktion.
Die erste in Entwicklung befindliche Prozesskette ist für CF/PPS. Vincent sagt, dass TPC-Cycle Simulationsmodelle und Analysemethoden entwickelt hat, um die Faserlänge und die Faserverteilung im recycelten Material zu charakterisieren. „Wir verstehen auch, wie sich diese Materialeigenschaften auf die Eigenschaften des Formteils übertragen“, beobachtet er. Dies ist in der Tat der Schwerpunkt seines Ph.D. Dissertation, die Ende 2019 veröffentlicht wird.
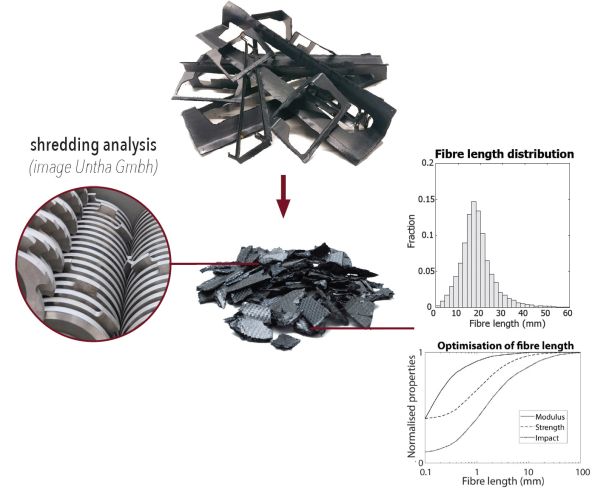
Der TPC- Das Projekt Cycled hat eine komplette Prozesskette für das Recycling thermoplastischer Verbundwerkstoffe entwickelt, einschließlich der kostengünstigen Zerkleinerung und Charakterisierung der Faserlänge und -verteilung. QUELLE | TPRC/TPAC.
Dieser recycelte Teig wird manchmal als Bulk Molding Compound (BMC) bezeichnet. In der Vergangenheit war BMC eine teigartige Mischung aus kurzen Glasfasern (<25 mm), duroplastischer Harzpaste und Füllstoffen, die zu Verbundteilen formgepresst wurde. Mit weniger Faservolumen und mehr Fließfähigkeit im Vergleich zu Sheet Moulding Compound (SMC) bot es auch etwas geringere mechanische Eigenschaften. TenCate hat Duroplast und Thermoplast verkauft BMC seit Jahren, wobei letzteres ein Verfahren ist, bei dem zerhackte unidirektionale Prepreg-Bänder in eine Form ausgebreitet und gepresst werden. „Unser Produkt ist eigentlich ganz anders“, behauptet Vincent. „Bei konventionellem thermoplastischem BMC gibt es in der Regel keine Vermischung und erfordert einen langen Erwärmungs- und Konsolidierungszyklus. Wir haben festgestellt, dass Sie beim Mischen ein homogeneres Produkt und weniger Spannungskonzentrationen im Teil erhalten, also höhere Eigenschaften. Mit konventionellem thermoplastischem BMC erhält man dickere Flocken mit matrixreichen Bereichen an den Enden, die Spannungskonzentrationen im Verbundlaminat erzeugen.“
Der Mischprozess mit geringer Scherung entwirrt die Flocken in Schichten und trennt dann die Schichten in Bündel und die Bündel in lose Fasern. Außerdem wird Polymer beigemischt, um den Fasergehalt zu verringern, um bessere Fließeigenschaften zu erzielen und das Material leichter zu Formen zu verarbeiten.
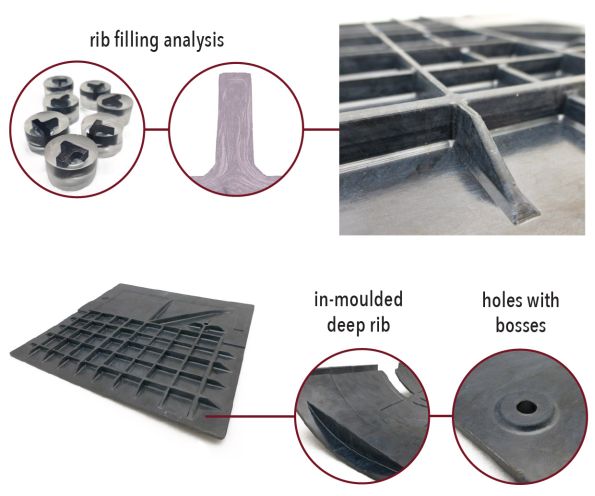
„Der Teig wird extrudiert und dann robotergesteuert in eine offene, isotherme [beheizte] Pressform gelegt“, erklärt de Bruijn. „Nach dem Mischen sind die Fasern im Teig zufällig ausgerichtet. Beim Pressen werden die Fasern jedoch durch den Materialfluss neu ausgerichtet. Diese Ausrichtung ist geringer als bei Mischungen mit kürzeren Fasern, die spritzgegossen werden, aber sie ist von Teil zu Teil ähnlich. Dies ist eines unserer weiteren Studienthemen.“
Kosten
Die bisher entwickelte TPC-Cycle-Prozesskette erscheint wirtschaftlich sinnvoll. „Wir hoffen, zu einem späteren Zeitpunkt im Jahr 2019 beantworten zu können, um wie viel wir die Teilekosten senken können“, sagt de Bruijn. „Das ist aber komplex, weil man einen Markt braucht und das recycelte Material verkaufen muss.“ Er stellt fest, dass es viele wirtschaftliche Faktoren gibt. Beispielsweise werfen die meisten Hersteller heute Produktionsabfälle einfach weg. Die lokalen Kosten für die Entsorgung auf einer Deponie betragen 80 € pro Tonne (90 USD). „Aber dieses weggeworfene Material hat einen Wert“, sagt de Bruijn. „Außerdem müssen Sie die Kosten für das Sammeln des Abfalls, das Schreddern, das Mischen und dann das Pressen zu neuen Teilen berücksichtigen. Aber auch hier handelt es sich um einen endkonturnahen Prozess mit kurzen Zykluszeiten aufgrund des isothermen Werkzeugs.“ Mit anderen Worten, es sollte eine drastische Reduzierung oder Eliminierung der sekundären Endbearbeitung und Bearbeitung erfolgen. De Bruin sagt, dass TPC-Cycle jetzt eine Kostenanalyse und eine Lebenszyklusanalyse durchführt.
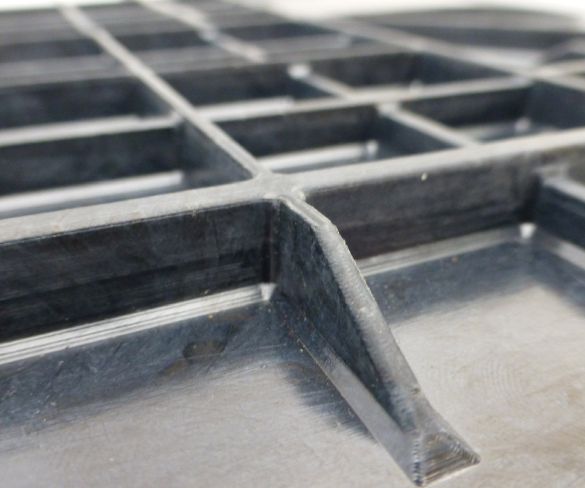
QUELLE | TPRC/TPAC
Clean Sky ZURÜCKSETZEN
Ein drittes Projekt, das die Bedeutung der Arbeit von TenCate und auch im TPC-Cycle-Projekt unterstreicht, ist das RESET-Projekt, das von Januar 2016 bis Dezember 2017 lief und vom Leitat Technological Institute in Barcelona, Spanien, koordiniert wurde. Es scheint, dass RESET im Rahmen von Clean Sky (2008-2016) begonnen und während Clean Sky 2 (2017-2021) abgeschlossen wurde.
Die Programme Clean Sky und Clean Sky 2 gliedern sich in eine oberste Stufe innovativer Flugzeugdemonstrationsprogramme (siehe Fahrzeug-IADPs in der Abbildung unten) und eine untere Stufe in innovative Technologiedemonstratoren (siehe Large System ITDs in der Abbildung unten). RESET wurde im Rahmen der Airframe-ITD abgeschlossen, insbesondere des Arbeitspakets (WP) A-3.4 Eco-Design for Airframe.
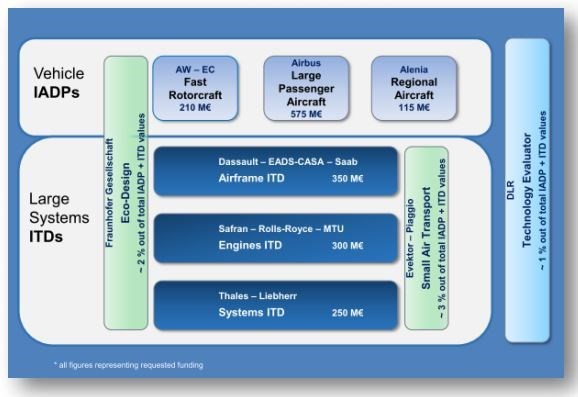
QUELLE:Clean Sky 2 Gemeinsame Technik Vorschlag
Für mehr Details, siehe „Demonstratoren für thermoplastische Verbundwerkstoffe – EU-Fahrplan für zukünftige Flugzeugzellen“
Laut der Clean Sky-Projektleiterin Elena Pedone hat das RESET-Team bei Leitat einen Prozess entwickelt, um zuvor gebrauchtes Flugzeugverbundmaterial zu recyceln und daraus neue Teile herzustellen. Sie verglichen diese recycelten Teile mit kommerziell hergestellten und fanden heraus, dass sie ähnliche mechanische Eigenschaften aufwiesen. „Die in diesem Projekt entwickelte Technologie könnte in den nächsten Jahren realistisch im Luftfahrtsektor vermarktet werden und möglicherweise auf andere Wirtschaftssektoren übergreifen“, sagt Pedone.
Während des RESET-Projekts wurden die Arbeiten zur Untersuchung der Auswirkungen von thermoplastischen PEEK- und PPS-Matrixmaterialien und der chemischen Natur der Kohlefaserverstärkung abgeschlossen. Die Verstärkungsform wurde untersucht, einschließlich der Faserlänge und gewebt im Vergleich zu Vlies. Der Einfluss des Fasergehalts (Verhältnis Polymer zu Faser) wurde ebenfalls untersucht.
In einem zweiten Arbeitspaket war das Hauptziel die Konditionierung und Charakterisierung von recyceltem CF/PPS auf Extrusionsbasis und den daraus resultierenden geformten Verbundwerkstoffen. Zwei Teile – ein thermoplastisches Bracket und ein thermoplastischer Stollen – wurden durch Spritzgießen und zwei weitere durch Thermoformen hergestellt, erklärt Leitats wissenschaftliche Koordinatorin des Projekts Claudia Aguilar. Diese Teile wurden dann getestet. „Die mechanischen Eigenschaften des Materials waren mit denen des kommerziellen Gegenstücks vergleichbar“, sagt Aguilar.
Das RESET-Projekt behauptet, einen Recyclingprozess demonstriert zu haben, der TPC-Abfälle aus der Flugzeugproduktion auffangen und als Rohstoff für die Herstellung neuer Flugzeugteile verwenden kann. „Bis zu 70 % des recycelten Materials wurden verwendet, um eine neue Familie von Verbundwerkstoffen herzustellen“, sagt Aguilar. Sie fügt hinzu:„Der Recyclingprozess von RESET ermöglicht es der europäischen Luftfahrt, den ökologischen Fußabdruck zu begrenzen und die Produktionskosten neuer Flugzeugteile zu senken. Daher macht das Projekt die Luftfahrtindustrie wettbewerbsfähiger und umweltfreundlicher.“
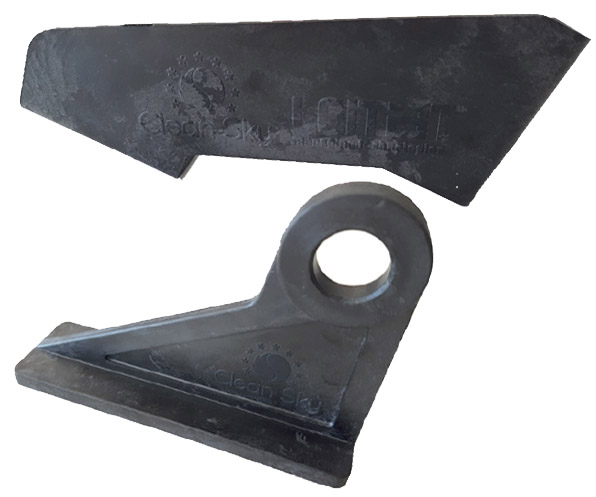
Halterung (links) und Stollen (rechts) aus recyceltem CF/PPS-Material, demonstriert vom Clean Sky RESET-Projekt. QUELLE | Leitat Technologisches Institut
TPC-Zukunft beginnt mit Design
Die Behauptung von TenCate und TPRC/TPAC ist, dass diese jetzt demonstrierten Recyclingverfahren nicht nur grün, sondern auch wirtschaftlich attraktiv sind. Welche Investitionen sind also erforderlich? „Das hängt vom Produktionsvolumen ab“, sagt Ten Napel von TenCate. „Die benötigten Zerkleinerungsmaschinen sind weder groß noch teuer und das Verfahren wurde so entwickelt, dass es ziemlich einfach ist.“ Beeinflusst der Matrixtyp die Recyclingfähigkeit? „Nein“, sagt Ten Napel, „aber in Bezug auf die Wirtschaftlichkeit sind Kohlefasern und PPS, PEEK oder PEKK aufgrund ihres höheren Wertes gegenüber den letzteren tragfähiger als Glasfasern und Polypropylen.“
„Ich denke, wenn dies von der Industrie aufgegriffen wird, sollte es beim Design beginnen“, fährt er fort. „Die größte Hürde ist derzeit die Denkweise der Ingenieure. Tatsächlich mit recyceltem Material zu entwerfen (oder diese teilweise in ein neues Produkt zu verwandeln) ist für sie ziemlich neu.“
Ten Napel räumt ein, dass TenCate Teile weder kommerziell entwickelt noch herstellt, „aber wir versuchen, Designer zu inspirieren, bei der Entwicklung ihrer neuen Teile und Strukturen so zu denken.“ Er nennt die Innenausstattung von Flugzeugen sowie Zugangsplatten und Zugangstüren als niedrig hängende Früchte für die Wiederverwendung von recyceltem Material. „Wenn wir uns als Branche an die Wiederverwendung unseres eigenen Schrotts und Abfalls gewöhnen können, können wir den nächsten Schritt gehen und uns überlegen, wie wir Altteile ansprechen können.“
Das Mantra des Recyclings von thermoplastischen Verbundwerkstoffen – einfach Schleifen und Umformen – kann durchaus übernommen werden, sagt Ten Napel, aber wirtschaftlich oft wenig sinnvoll. „Wir haben einen besseren Prozess demonstriert und einen, der tatsächlich kostengünstigere Teile und Gesamtprogramme erstellen kann. Wir haben uns entschieden, dieses Wissen zusammen mit dem TPRC und TPAC zu verbreiten, um die Industrie zu inspirieren, was mit thermoplastischen Verbundwerkstoffen alles möglich ist.“ Wenn thermoplastische Verbundwerkstoffe im großen Stil eingesetzt werden sollen, ist Recycling als fester Bestandteil der Produktion keine Option mehr, sondern eine Notwendigkeit.
Harz
- Recycling:Endlosfaserverstärkte thermoplastische Verbundwerkstoffe mit recyceltem Polycarbonat
- Thermoplastisches Biomaterial „Feinabgestimmt“ für medizinische Anwendungen
- Karl Mayer startet Produktionslinie für thermoplastische UD-Bänder
- INEOS Styrolution baut Produktionsstätte für thermoplastischen Verbundwerkstoff StyLight
- Hexion führt Zweikomponenten-Epoxidlösung für die Herstellung von Verbundwerkstoffen in der Luft- und Raumfahrt ein
- Thermoplastische Tür eine Premiere für Automobilverbundwerkstoffe
- LANXESS erweitert Produktionskapazität für endlosfaserverstärkte thermoplastische Verbundwerkstoffe
- CAMX 2018-Vorschau:TenCate Advanced Composites
- Schweißen von thermoplastischen Verbundwerkstoffen
- TenCate feiert den Zusammenschluss des Konsortiums für thermoplastische Verbundwerkstoffe in Brasilien