ENGEL stellt IR-Roboterzelle für die Großserienfertigung von leichten thermoplastischen Verbundwerkstoffen vor
Die Fertigungszelle von ENGEL erwärmt und formt mit Infrarotstrahlung drei unterschiedlich dicke Organobleche und formt im gleichen Spritzgießprozess eine hochwertige Sichtfläche.
Quelle | ENGEL
Der Spritzgießmaschinenhersteller und Systemlösungsanbieter ENGEL Austria hat angekündigt, auf der K 2019 (Düsseldorf, Deutschland, 16.-23.10.) eine Infrarot-Härtungstechnologie als Teil seiner Fertigungszelle vorzustellen, die Composites Preforming mit thermoplastischem Einspritzen bietet Umspritzen.
ENGEL stellt im organomelt-Verfahren Demoteile her, die die neuesten Innovationen für Pkw-Türmodule widerspiegeln. Die Fertigungszelle von ENGEL soll weltweit die erste sein, die mit Infrarotstrahlung drei unterschiedlich dicke Organobleche erwärmt und formt sowie eine hochwertige Sichtfläche im selben Spritzgießprozessschritt formt. Die Anlage wird mit drei gleichzeitig arbeitenden ENGEL easix Knickarmrobotern ausgestattet.
„Thermoplastische Verbundwerkstoffe gewinnen beim Leichtbau in der Automobilindustrie zunehmend an Bedeutung“, sagt Dr. Norbert Müller, Leiter des ENGEL Center for Lightweight Composite Technologies.
Dafür gibt es zwei Hauptgründe. Zum einen ermöglicht der konsequente thermoplastische Ansatz eine effiziente Integration der Umformung und Funktionalisierung von faserverstärkten Prepregs, was die Stückkosten senkt. Zum anderen erleichtert die Verwendung ausschließlich thermoplastischer Polymere die Entwicklung von Recyclingstrategien.
„Die Rückführung von Composite-Bauteilen in den Stoffkreislauf am Ende ihrer Lebensdauer ist einer der Schwerpunkte für die Weiterentwicklung im Bereich Elektrofahrzeuge“, so Müller. „Thermoplastische Lösungen werden mittlerweile auch im Flugzeugbau immer häufiger eingesetzt.“
Die Antwort von ENGEL auf das Bedürfnis nach nachhaltigem Transport ist organomelt. Beim Organomelt-Verfahren werden faserverstärkte Prepregs mit thermoplastischer Matrix wie Organobleche und Tapes erhitzt, in das Werkzeug eingelegt, dort umgeformt und direkt mit Thermoplast umspritzt. Das Verfahren wurde bereits in der Großserienfertigung eingesetzt, wobei ENGEL organomelt für die vollautomatische Produktion von Artikeln wie Frontendträgern eingesetzt wird.
Im Zuge der Weiterentwicklung des Verfahrens arbeitet ENGEL gemeinsam mit seinen Kunden und Partnern an der fertigungstechnischen Auslegung von Verbundbauteilen mit gezielter Lastverteilung.
„Zukünftig werden für jedes Bauteil mehrere unterschiedliche Prepregs kombiniert, um die Leichtbaueigenschaften auf die jeweilige Bauteilform sowie die unterschiedlichen Belastungen einzelner Bereiche im Inneren des Bauteils abzustimmen“, erklärt Müller. „Die Fertigungszelle auf der K-Messe wird dieses große Potenzial deutlich demonstrieren.“
Das Formgebungsverfahren wurde in Zusammenarbeit mit dem Automobilzulieferer Brose (Coburg, Deutschland) entwickelt. Laut ENGEL ist die Fertigungszelle derzeit weltweit die einzige Anlage, die drei unterschiedlich geformte Organobleche zwischen 0,6 mm und 2,5 mm Dicke vollautomatisiert mit integrierten IR-Öfen gleichzeitig verarbeiten kann. Durch die gezielte Auswahl der Organobleche auf Basis der Lastverteilung kann den unterschiedlichen Belastungen der einzelnen Bauteilbereiche Rechnung getragen werden – ein Ergebnis, das Brose durch verschiedene Simulationsverfahren mit sichergestellt hat. Das auf der K zu produzierende Demoteil ist beispielsweise im Fensterrahmenbereich steifer als an der Türinnenseite.
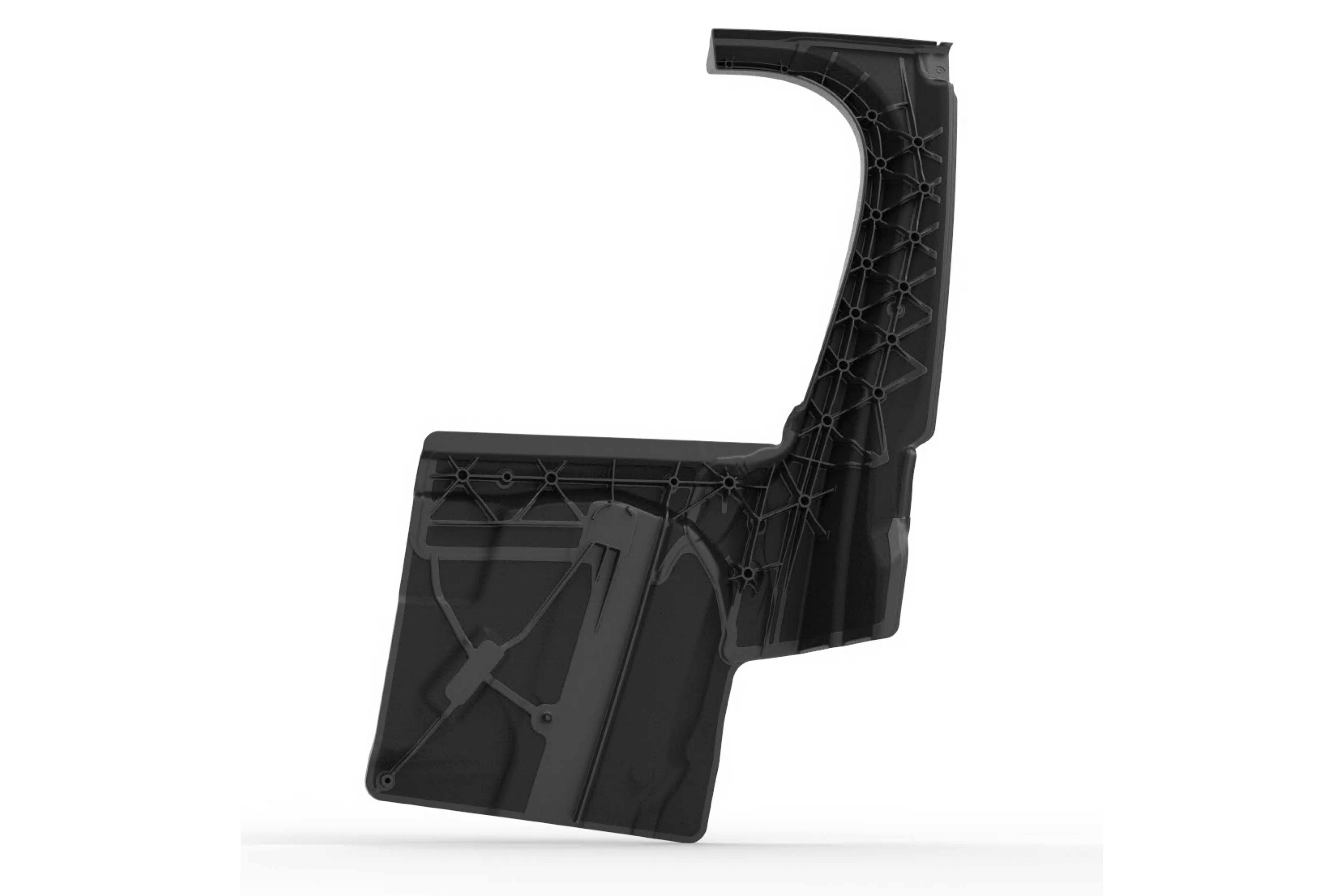
Durch die gezielte Auswahl der Organobleche nach Lastverteilung kann den unterschiedlichen Belastungen der einzelnen Bauteilbereiche Rechnung getragen werden.
Quelle | ENGEL
Integration eines ultrakompakten IR-Ofens
Eine der Herausforderungen bei der Verarbeitung von Organoblechen ist die Erwärmung der Prepregs. Die Zeit, die sie zum Erhitzen und Abkühlen benötigen, hängt von ihrer Dicke ab. Ein schnelles Aufheizen des Materials, ohne es zu beschädigen, ist ebenso wichtig wie ein schneller und unkomplizierter Übergang in die Form für das erhitzte Prepreg. Die organomelt-Fertigungszelle von ENGEL basiert auf einer duo 3660/800 Spritzgießmaschine und beinhaltet aus diesem Grund zwei integrierte IR-Öfen. Direkt über der Schließeinheit befindet sich ein vertikaler IR-Ofen zum Aufheizen des nur 0,6 mm dicken Organoblechs. So gelangt das dünne Organoblech schnell ins Werkzeug, sodass es noch nicht abgekühlt ist und sich nicht mehr verformen lässt. Für die beiden dickeren Organobleche (1 mm und 2,5 mm) kommt ein handelsüblicher, horizontaler IR-Ofen auf einem Podest über der beweglichen Platte zum Einsatz. Diese Anordnung verkürzt den Abstand zwischen Ofen und Form und spart Platz, da der Ofen keine separate Stellfläche benötigt. Beide IR-Öfen wurden von ENGEL selbst entwickelt und gefertigt. Diese und die drei easix-Roboter sind vollständig in die CC300-Steuerung des IMM integriert und können zentral über das Display der Maschine gesteuert werden.
Alle drei Organobleche werden gleichzeitig aufgeheizt. Für das Organoblech-Handling stehen dann zwei der drei easix-Roboter zur Verfügung. Diese befinden sich nebeneinander oberhalb der Spanneinheit. Während der erste Roboter für das Handling der beiden dickeren Organobleche zuständig ist, kümmert sich der zweite Roboter um das dünnste Blech. Während des gesamten Aufheizvorgangs hält er das Organoblech vor das vertikale Strahlungsfeld, damit es nach Ablauf der eingestellten Aufheizzeit in die Form eingelegt werden kann. Der dritte Roboter befindet sich neben der Schließeinheit. Seine Aufgabe ist es, das Formteil zu entnehmen und gleichzeitig eines der drei Organobleche für den Spritzgussprozess in das Werkzeug zu befördern.
Die Organobleche, die vom chinesischen Rohstoffproduzenten Kingfa (Shanghai, China) bezogen wurden, bestehen aus Glasfasern und verwenden als Matrixmaterial Polypropylen. Beim Schließen der Form – gebaut von Georg Kaufmann Formenbau (Remetschwil, Schweiz) – werden die Organobleche umgeformt. Unmittelbar danach werden sie im selben Werkzeug mit glasfaserverstärktem Polypropylen umspritzt. Auf der Rückseite des Bauteils sind Verstärkungsrippen, auf der Sichtseite eine Narbung in Lederoptik eingeformt.
„Durch das direkte Umspritzen der Organobleche erreichen wir eine hervorragende genarbte Lederoptik, die bei Organoblechen bisher als unmöglich galt“, so Müller. „Damit legen wir den Grundstein, um zukünftig große thermoplastische Türkonstruktionen im Organomelt-Verfahren herzustellen.“
Automatisierung spielt eine Schlüsselrolle
Die von ENGEL im Center for Lightweight Composite Technologies entwickelten Produktionslösungen zeichnen sich durch hohe Effizienz und Wirtschaftlichkeit aus – beides wesentliche Voraussetzungen für Anwendungen in der Großserienfertigung.
„Das große Automatisierungs-Know-how von ENGEL spielt eine große Rolle“, sagt Walter Aumayr, Vice President des ENGEL-Geschäftsbereichs Automation and Composite Systems.
Mit drei gleichzeitig arbeitenden ENGEL easix Knickarmrobotern wird die organomelt-Zelle auf dem ENGEL Messestand ein hochmodernes Beispiel für integrierte Composite-Verarbeitung sein und ist die komplexeste Fertigungszelle, die ENGEL jemals präsentiert hat eine Messe.
„Je mehr Prozessschritte wir einbinden und je mehr Einzelsysteme eine Fertigungszelle umfasst, desto komplizierter wird der Gesamtprozess“, sagt Aumayr. „Als Systemlösungsanbieter hat ENGEL daher für eine durchgängige Bedienlogik und ein gemeinsames Datenmanagement in der gesamten Zelle gesorgt, was den Einsatz von Knickarmrobotern deutlich erleichtert. Die easix-Roboter können von den Arbeitern, die beim Spritzgießen in der Werkstatt tätig sind, relativ einfach bedient werden.“
Eine Besonderheit der ENGEL Systeme ist, dass auch die IR-Öfen vollständig in die CC300-Steuerung integriert sind, wodurch eine einheitliche Bedienlogik für den gesamten Prozess gewährleistet ist. Da zudem Spritzgießmaschine, Roboter und Peripherie auf die gleiche Datenbank in der ENGEL Systemlösung zugreifen, sinkt das Fehlerrisiko und die Effizienz steigt. Ohne zusätzliche Hardware können die easix-Knickarmroboter ihre Bewegungen mit den Bewegungen im Werkzeug, beispielsweise von Kernzügen oder Auswerfern, synchronisieren.
„Dadurch können wir vor allem bei Großanlagen sowohl Taktzeiten als auch Investitionskosten reduzieren“, sagt Aumayr.
Harz
- Thermoplastisches Waben-Sandwich zum Umspritzen in dünnere, leichte Verbundwerkstoffe
- Fraunhofer nimmt automatisierte Engel-Produktionszellen für F&E thermoplastischer Verbundwerkstoffe in Betrieb
- Cato Composites erweitert Produktionskapazität für thermoplastische Verbundwerkstoffe
- Karl Mayer startet Produktionslinie für thermoplastische UD-Bänder
- INEOS Styrolution baut Produktionsstätte für thermoplastischen Verbundwerkstoff StyLight
- Hexion führt Zweikomponenten-Epoxidlösung für die Herstellung von Verbundwerkstoffen in der Luft- und Raumfahrt ein
- Thermoplastische Tür eine Premiere für Automobilverbundwerkstoffe
- LANXESS erweitert Produktionskapazität für endlosfaserverstärkte thermoplastische Verbundwerkstoffe
- IRG CosiMo Konsortium für thermoplastische Verbundwerkstoffe enthüllt neue Anlagen
- Konsortium für thermoplastische Verbundwerkstoffe strebt die Massenproduktion für die Automobil- und Luftfahrtindustrie an