Hochfester 3D-Druck – isotrope Füllung Teil 2
Aktualisierung: Wenn Sie mehr darüber erfahren möchten, wie verschiedene Füllungen Ihren Teil auf verschiedene Weise stärken können, und die Wissenschaft dahinter, besuchen Sie uns am 21. Juni um 11 Uhr EDT zu einem Webinar (hier anmelden)!
Anmerkung des Autors:Dies ist der zweite Beitrag unserer zweiteiligen Serie zum Entwerfen der stärksten Teile mit Eigers Isotrop Fibre Fülltyp unter Verwendung von Kohlefaser auf dem Mark Two. Unser vorheriger Beitrag erläuterte den Hintergrund, warum wir Verstärkungen in unserem spezifischen isotropen Muster drucken. In diesem Beitrag erfahren Sie, wie Sie diesen Fülltyp am besten anwenden, um die stärksten Teile mit der effizientesten Nutzung unserer Kohlefaser-3D-Drucktechnologie herzustellen.
Zuvor haben wir die Grundlagen der Verbundverstärkung sowie die Anwendung verschiedener Faserorientierungen in Eiger behandelt. Jetzt ist es an der Zeit, über die Effizienz der Verstärkung zu sprechen – 3D-Druck der stärksten Teile ohne unnötiges Gewicht oder unnötige Kosten. Das Verstärken einer Schicht mit der Isotropen Faserfüllung von Eiger verleiht dieser Schicht Festigkeit und Steifigkeit – aber brauchen Sie diese Festigkeit dort tatsächlich? Wir zeigen Ihnen, dass die Lage einer Schicht im Verhältnis zu den auf das Gesamtteil aufgebrachten Lasten wahrscheinlich der wichtigste Aspekt bei der Konstruktion für eine effiziente Verwendung der Bewehrung im hochfesten 3D-Druck ist.
Bevor wir uns mit der eigentlichen Verstärkung befassen, ist es wichtig zu verstehen, wie physische Teile reagieren, wenn eine Kraft oder Last auf ihre äußeren Geometrien ausgeübt wird. Betrachten wir als Beispiel einen einfach gestützten Träger – einen Träger, der an beiden Enden von unten gestützt wird, wobei ein Ende frei entlang des x . verschoben werden kann Achse, wie im Bild unten.
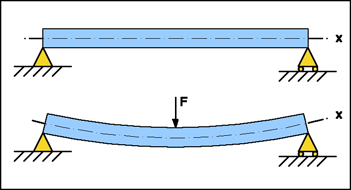
Wenn Sie eine Kraft anwenden F zum Balken, beginnt sich der Balken um einen Betrag nach unten zu biegen oder abzulenken, der sowohl von der Größe von F als auch von der Geometrie und den Materialeigenschaften des Balkens abhängt. Wenn Sie sich die durch die Kraft F generated erzeugten inneren Spannungen ansehen würden In einem repräsentativen Seitenprofilabschnitt des Trägers, der einer Biegung ausgesetzt ist, würden Sie feststellen, dass die Seite des Trägers, die der nach unten zeigenden Last am nächsten ist, eine Kompression erfährt, während die am weitesten entfernte Seite des Trägers eine gleiche Kraft erfährt, jedoch unter Zug.

Das obige Diagramm zeigt die inneren Biegespannungen σ über die Dicke des Balkens, wobei ein längerer Pfeil anzeigt, dass die Biegespannung größer ist. Es ist sofort klar, dass beim Biegen die höchsten Biegespannungen an der Ober- und Unterseite des Trägers entwickelt werden, wobei die Mittellinie des Trägers, die neutrale Achse genannt wird, keine Kraft erfährt. Die entgegengesetzten Richtungen der Pfeile auf beiden Seiten der neutralen Achse geben die Richtung der Kraft – Druck oder Zug – an, die der Bereich des Balkens erfährt. Insgesamt bedeutet dies, dass Sie bei der Optimierung der Verwendung von hochfestem Material in einem Teil, das einer Biegung ausgesetzt ist, dieses Material vorrangig dort platzieren sollten, wo die höchsten Kräfte auftreten – in der Nähe der Oberfläche des Trägers. Diese einfache Tatsache ist der Grund für die Konstruktion von I-Trägern und Sandwichpaneelen.
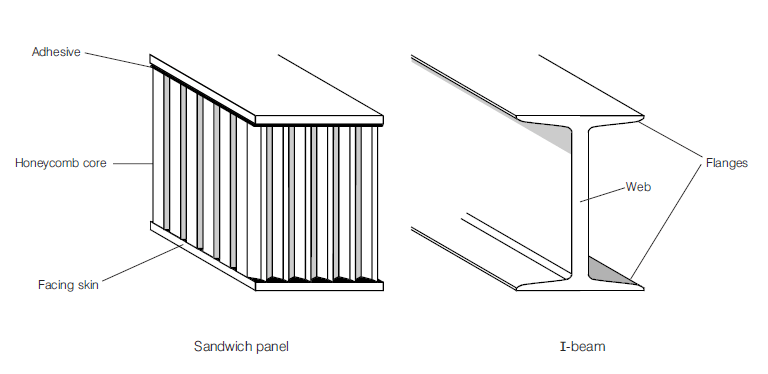
Die Entwicklung sowohl von I-Trägern als auch von Sandwichelementen resultierte aus dem Wunsch, eine hochfeste, hochsteife Platte oder einen Träger mit minimalem Gewicht herzustellen. Wie wir gesehen haben, treten die höchsten Biegekräfte an den Außenflächen eines Trägers auf, sodass das Hinzufügen von hochfestem Material an diesen Flächen den Biegekräften am besten standhält. In der Nähe der Trägermitte tragen hochfeste Materialien jedoch nicht annähernd so viel zur Gesamtfestigkeit des Trägers bei, da sie viel geringeren Kräften ausgesetzt sind. Diese Materialien fügen immer noch die gleiche Menge an Gewicht hinzu, jedoch wird die Gesamtfestigkeits-pro-Gewicht-Effizienz von Bereichen nahe der neutralen Achse stark verringert. Die I-Träger-Geometrie wurde entwickelt, um einen Einmaterial-Metallträger mit hohem Festigkeits-Gewichts-Verhältnis bereitzustellen. Das Aufkommen fortschrittlicher Materialien ermöglichte die Entwicklung einer Mehrmaterial-Sandwichplattenkonstruktion, die die normalerweise vom I-Träger-Steg (dem vertikalen Teil des I-Trägers) aufgenommenen Kräfte über eine viel größere Fläche verteilt und viel leichtere Kernmaterialien zu verwenden, da die auftretenden Kräfte nicht auf eine einzige Bahn konzentriert werden müssen.
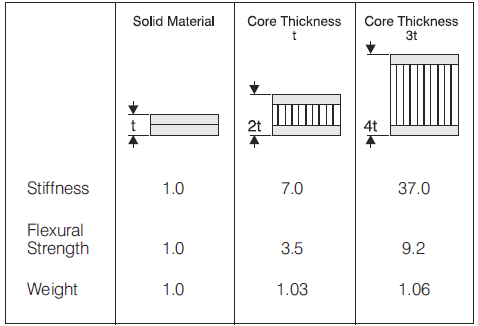
Überlagerung von Sandwichelementen
Lassen Sie uns nach all der Theorie in die Verstärkungsteile in Eiger eintauchen. Standardmäßig versucht Eiger, eine Sandwichplatte zu erstellen, wenn Sie Fasern auf der externen Seite "Teileansicht" hinzufügen, die Sie zum ersten Mal beim Öffnen eines Teils aus Ihrer Eiger-Bibliothek finden.
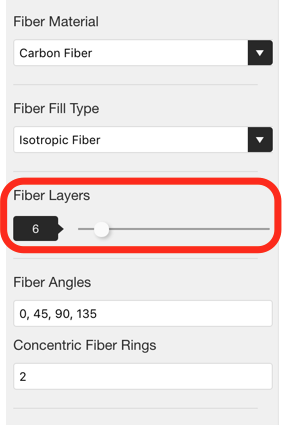
Die Hälfte des 'Faser-Layers'-Wertes, den Sie zum Hinzufügen zu einem Teil ausgewählt haben, wird automatisch zu den unteren Ebenen des Teils über den ersten vier (standardmäßig) Ebenen hinzugefügt, die als massive Kunststoff-Bodenebenen konfiguriert sind, und die andere Hälfte der Faserschichten werden an der Oberseite des Teils hinzugefügt, unter den oberen vier (wiederum standardmäßig) Schichten, die als feste Kunststoffschichten konfiguriert sind. Dieser Algorithmus funktioniert hervorragend, wenn der Teil, den Sie verstärken möchten, symmetrisch zu einer Ebene parallel zum Druckbett ist, wie zum Beispiel das Fahrwerk der Snotbot-Drohne, das ein Team am Olin College gedruckt hat.
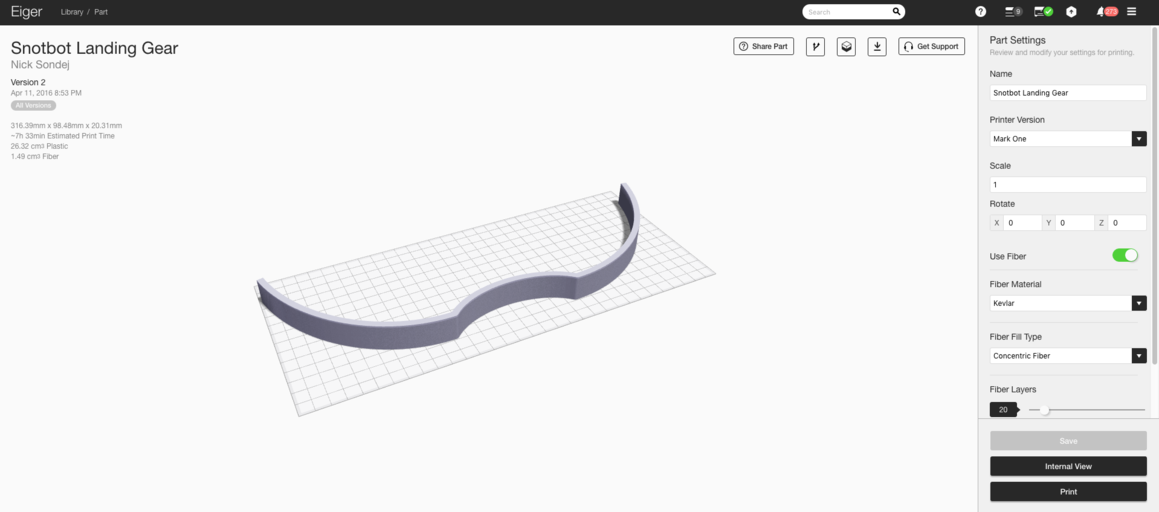
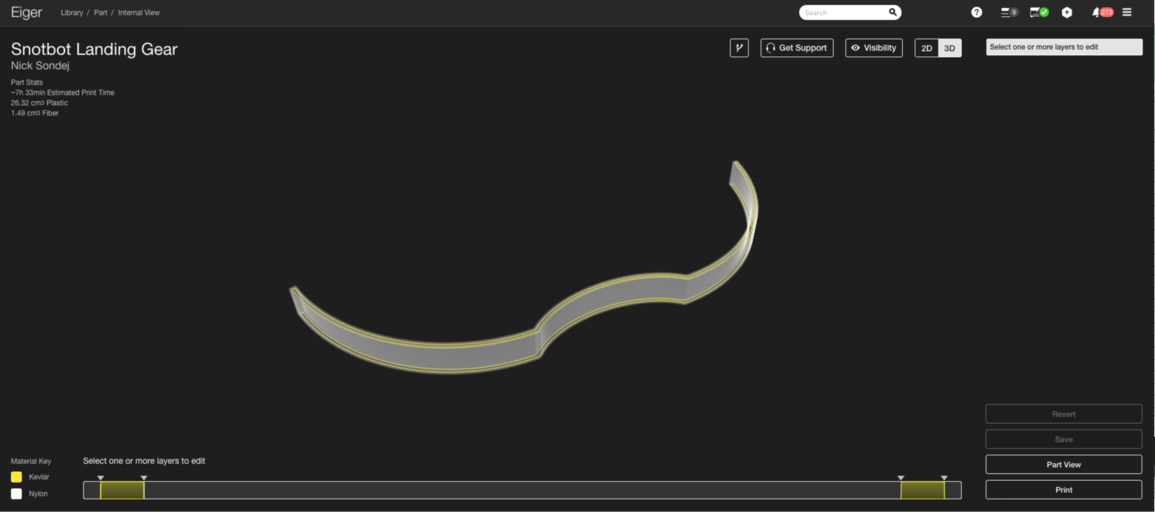
Wie Sie auf den Fotos oben sehen können, fügte der Algorithmus oben und unten 10 Schichten Kevlar-Verstärkung hinzu. Da das Teil um eine XY-Ebene symmetrisch ist, führte der Standard-Faserlagenalgorithmus zum gewünschten Verhalten, der Sandwichplattenverstärkung.
Aber was passiert, wenn Ihr Teil die oben beschriebene Symmetriebedingung nicht erfüllt? In diesem Fall bietet der Standardalgorithmus nicht die gewünschte Verstärkung, wie im Fall des Motorradbremshebelteils, das wir oft als Stärkedemonstrator auf Messen verwenden.
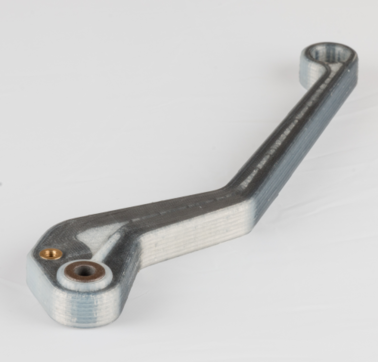
Wie Sie im folgenden Screenshot sehen können, fügt der Standard-Faseralgorithmus Fasern an der Unterseite des Teils hinzu, fügt jedoch keine Fasern an der Oberseite des Teils hinzu, an denen sie benötigt werden, um die Sandwichplatte fertigzustellen, da der kleine erhöhte Grat, an dem die Bronze Buchse gepresst wird, führt zu einer Asymmetrie des Teils. Wir möchten, dass die Faser weiter von der oberen Schicht des Teils entfernt ist als von der Unterseite des Teils, um die größtmögliche Sandwichplatte zu produzieren.
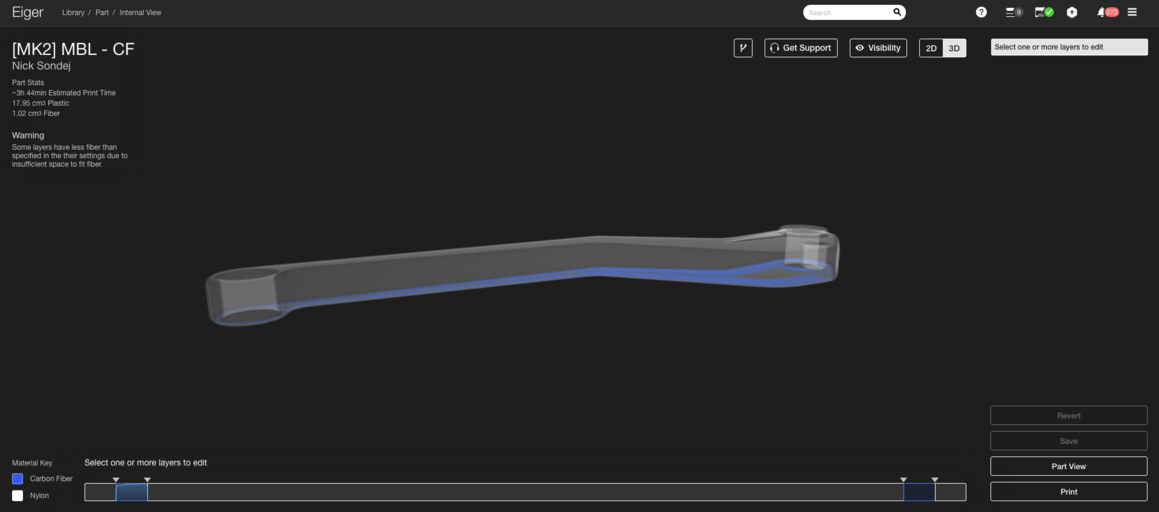
Dies bringt uns zur ersten allgemeinen Richtlinie für die Verstärkung der stärksten Teile auf Ihrem Markforged-Drucker – versuchen Sie, die größten Sandwichplatten, die Sie können, zuerst in einem Teil zu erstellen, indem Sie isotrope Faserfüllung mit einem oder zwei konzentrischen Ringen in Schichten mit dem größten Abstand verwenden sie.
Im Fall des obigen Motorradbremshebels bedeutet dies, dass Sie die obere Schichtgruppe nach unten verschieben sollten, bis Fasern oben am Hebelkörper verlaufen, wie in der folgenden Abbildung zu sehen.
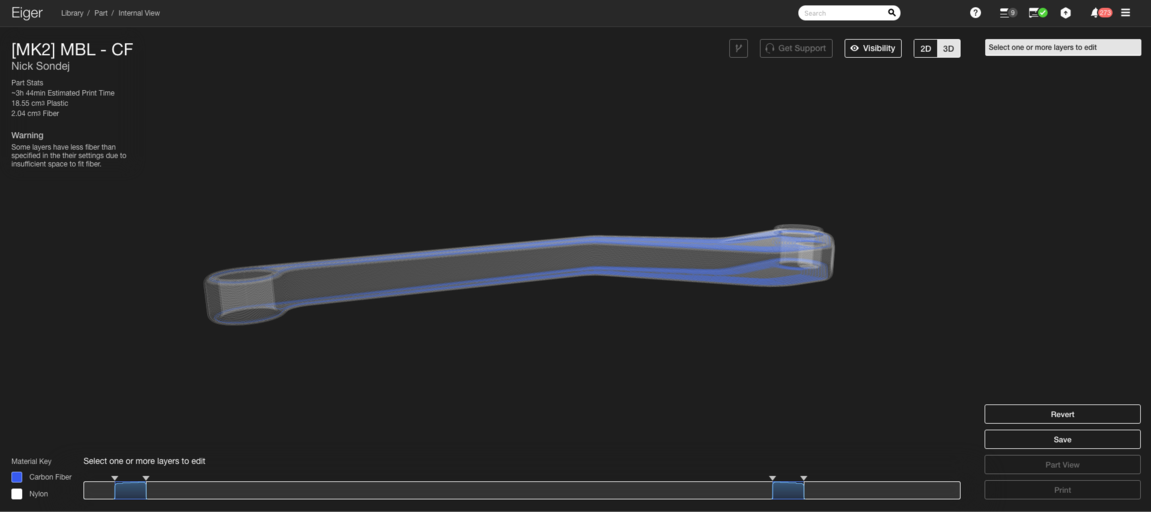
Was passiert, wenn Sie mehrere, potenziell überlappende Bereiche haben, die reif für die Sandwichplattenkonstruktion sind, wie bei diesem Kurbelarm aus dem 2016-Design des UW-Madison Human Powered Vehicles Teams?
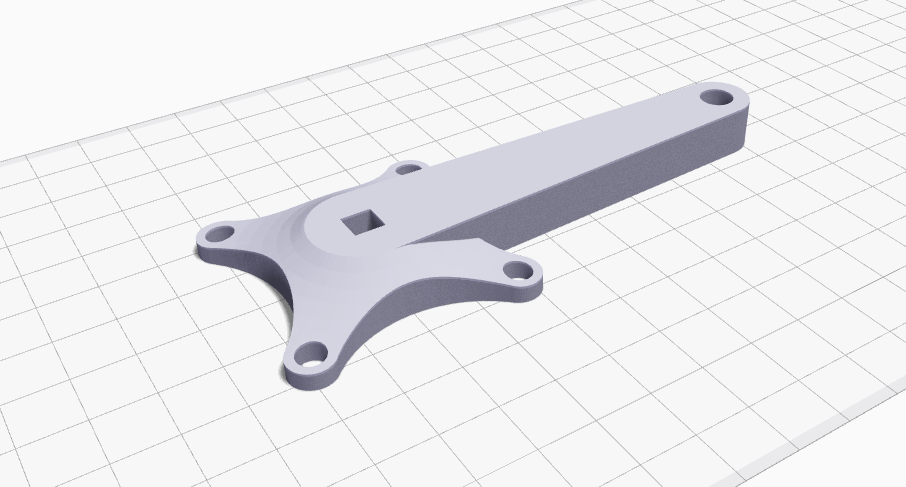
Es gibt eindeutig mehrere Bereiche, die zu Sandwichpaneelen werden könnten – es gibt die Ober- und Unterseite des Arms selbst (der längere Teil der Struktur) sowie die oberen und unteren Abschnitte des vierzackigen Flansches, die ebenfalls von einer Verbundverstärkung profitieren würden . Da die Schrauben durch alle vier Löcher geführt werden, würde die Zugabe von Fasern den von den Schrauben erzeugten Spannungskegeln besser widerstehen. Während Sie möglicherweise eine gründliche (und langwierige) Belastungssimulation durchführen können, um die besten Stellen zum Hinzufügen von Fasern zu finden, ist es am einfachsten (und wahrscheinlich am effizientesten), einfach mit dem Bau von Sandwichelementen zu beginnen. Zuerst lassen wir den Standard-Faseralgorithmus vier Schichten isotroper Faserfüllung an der Ober- und Unterseite des Teils hinzufügen.
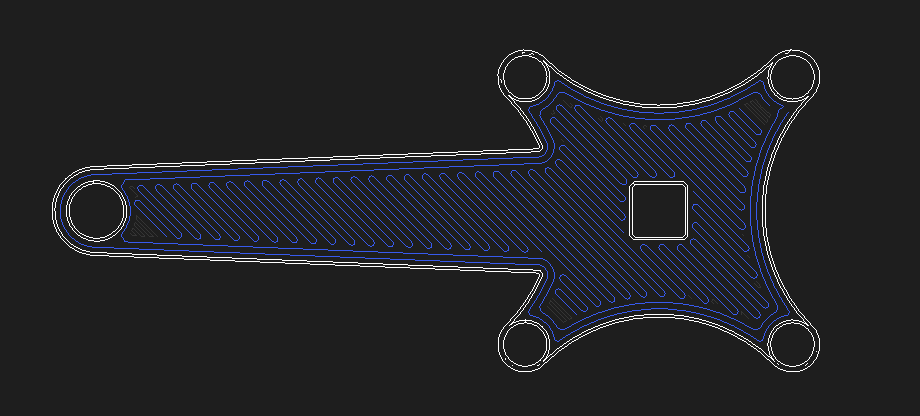
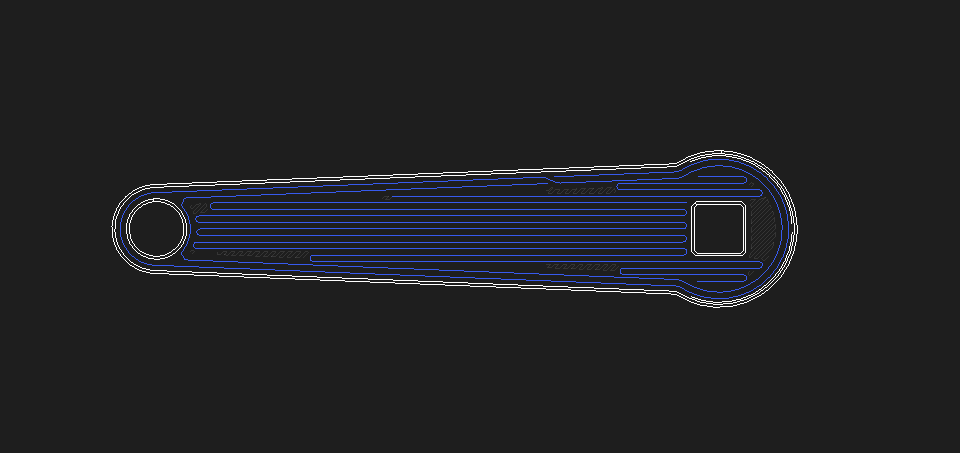
Diese beiden Schichten haben sehr unterschiedliche Querschnittsflächen, was nicht ganz ideal ist (es ist am besten zu versuchen, Sandwichpaneel-Hautschichten mit ungefähr gleicher Querschnittsfläche zu haben, wenn die Geometrie dies zulässt), aber die größtmögliche Sandwichpaneel in der zu verstärken Teil bedeutet, dass dieser Kurbelarm den großen Biegebelastungen des Beins eines Radfahrers besser standhalten kann.
Wir müssen auch den Flansch mit den vier Löchern verstärken, die diesen Kurbelarm mit der eigentlichen Kurbel verbinden. Wenn wir uns nur auf den Flansch konzentrieren, haben wir den Boden bereits verstärkt, als wir im ersten Schritt das gesamte Teil verstärkt haben, wir müssen nur eine Gruppe von Schichten etwa 25 Schichten in das Teil hinein verstärken, wo der Flansch endet. Aber wenn wir dort eine Lagengruppe hinzufügen, haben wir drei separate Faserlagen. Wir haben nur über Sandwichpaneele mit zwei Verbundschalen gesprochen, eine auf jeder Seite – haben wir eine der Sandwichpaneele ruiniert?
Dies bringt uns zu unserer zweiten Richtlinie – unser Konzept der „Sandwichplatten“ ist nicht nur additiv, und wir können eine Sandwichplatte über eine größere oder kleinere legen, indem wir die zusammengesetzte „Haut“-Schicht des vorherigen Sandwichs wiederverwenden.
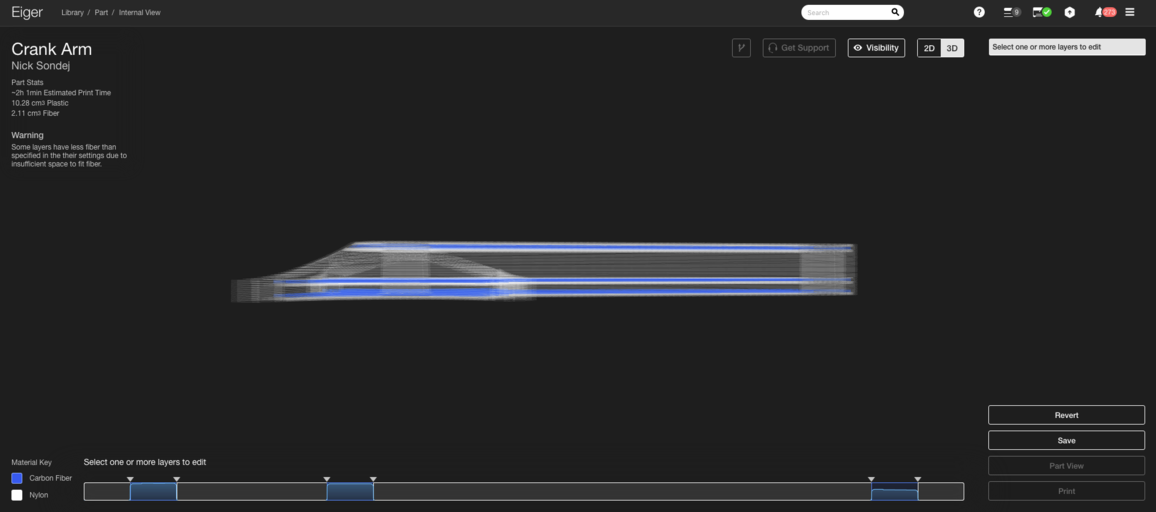
Daraus ergibt sich die Konfiguration in der Abbildung oben, mit einer dünneren Sandwichplatte, die den Kurbelarmflansch verstärkt, und einer dickeren Sandwichplatte, die das Gesamtteil verstärkt. Beide Sandwichpaneel-Ausführungsformen verwenden die Gruppe der Kohlenstoffverstärkungsschichten an der Unterseite des Teils als ihre untere Hautschicht.
Zu diesem Zeitpunkt ist das Teil bereits extrem stark, aber da Fahrradkurbelarme ziemlich komplizierten Torsionsbelastungsmustern ausgesetzt sind, werden wir eine weitere Faserschicht hinzufügen. Dies liegt daran, dass durch bestimmte aufgebrachte Torsionslasten Schubspannungen verursacht werden können. Im Gegensatz zu Biegespannungen haben Schubspannungen eine maximale Größe an der neutralen Achse oder Mittelebene eines Teils, und da es schwer vorherzusagen ist, ob der Kurbelarm diesen Belastungsbedingungen ausgesetzt ist, ist es am einfachsten, einfach eine weitere Verbundschichtgruppe um die Mittelebene herum hinzuzufügen des Kurbelarms.
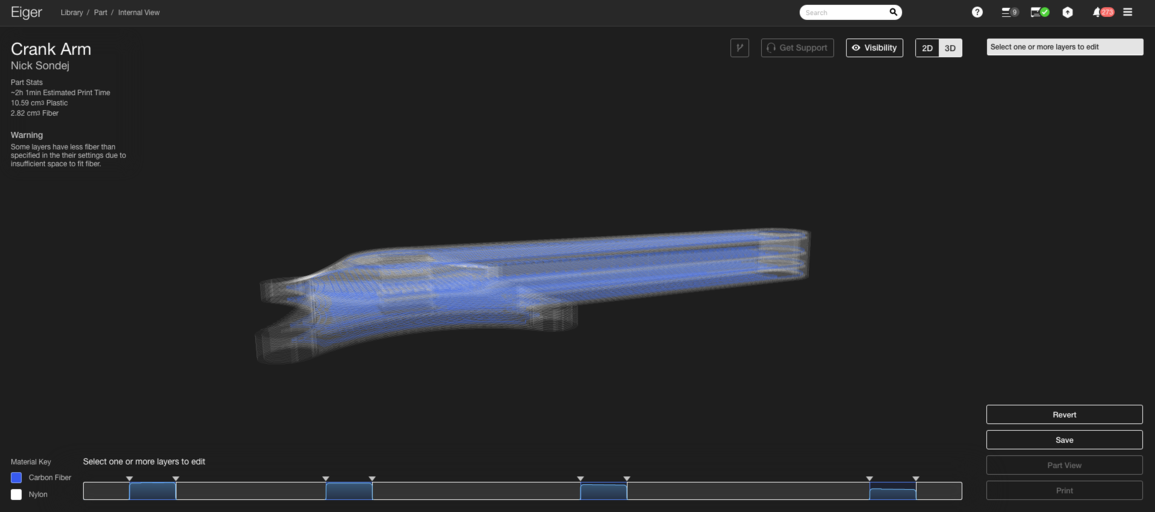
Dies führt zu der endgültigen Konfiguration, die im obigen Bild zu sehen ist – mit vier separaten Fasergruppen, die eine Reihe von Sandwichpaneelen bilden. Dies ist eine der stärksten Konfigurationen, die wir produzieren können, während gleichzeitig ein insgesamt leichtes Teil erhalten bleibt.
Zusammenfassend sind unsere drei Richtlinien für hochfesten 3D-Druck mit Faserverstärkung:
1. Erstellen Sie zuerst die größte und dickste Sandwichplatte mit isotroper Faserfüllung
2. Sie können Sandwichpaneele hinzufügen und überlagern, um ein Teil vollständig zu verstärken
3. Das Hinzufügen einer Gruppe von isotropen Faserschichten in der Mittelebene kann bestimmten Torsionsbelastungsmustern besser widerstehen
Diese Richtlinien sind nicht narrensicher und es wird immer Ausnahmen geben, aber sie sind ein guter Ausgangspunkt, wenn Sie Ihre stärksten Teile entwerfen.
Möchten Sie einen Teil selbst verstärken? Erfahre noch heute mehr über die Mark Two!
3d Drucken
- Stressfreie Reinigung für den FDM-Druck
- Warum CT-Scannen ein wichtiger Bestandteil des erfolgreichen 3D-Drucks wird
- Wie die 3D-Drucktechnologie ein wichtiger Bestandteil von Industrie 4.0 sein wird
- 6 wichtige Designüberlegungen für den 3D-Metalldruck
- Ist der 3D-Druck bereit für die Endfertigung?
- 3D-Druck und Prototyping
- Erstellen von Mehrkörper-STL-Dateien für den 3D-Druck
- So positionieren Sie Ihr Modell für den 3D-Druck
- Hochgeschwindigkeits-3D-Druck mit AION500MK3
- 3D-Drucktechnologien (Teil 2)