Experten:Erhöhte Automatisierung entscheidend für die Erfüllung der Flugzeugnachfrage
Allein der kommerzielle Bedarf in den nächsten 20 Jahren deutet auf eine Verdoppelung der Produktionsraten hin
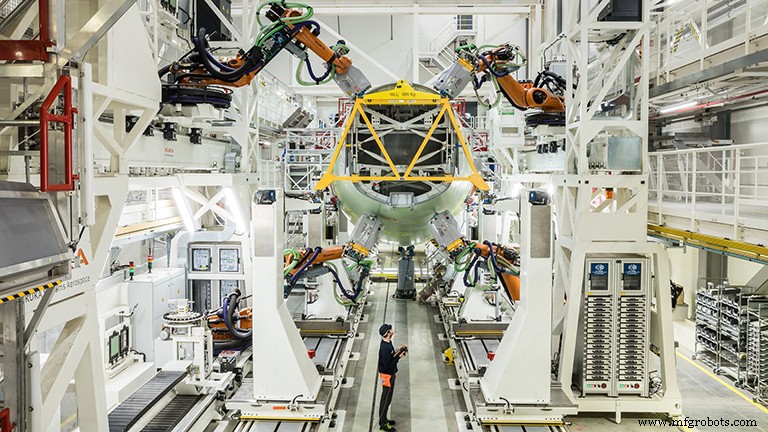
Bevor die Coronavirus-Pandemie das normale Leben auf den Kopf stellte und Verkehrsflugzeuge im Wesentlichen stilllegte, hatte die Luftfahrtindustrie in den nächsten 20 Jahren einen prognostizierten Bedarf an 40.000 neuen Flugzeugen – Flugzeugen, Hubschraubern, Lufttaxis und unbemannten Luftfahrzeugen. Das Volumen umfasst Ersatz für Schiffe, die nach einer durchschnittlichen Lebensdauer von 25 bis 30 Jahren außer Betrieb sind, und kommt zu einem Rückstand von etwa acht Jahren hinzu.
Wenn die Nachfrage nach Flügen ihr vorheriges Niveau wieder erreicht, sobald die Beschränkungen im Zusammenhang mit der Pandemie nachlassen, ist die einzige Möglichkeit, den prognostizierten Bedarf zu decken, eine verstärkte Automatisierung, sagten einige Branchenexperten.
Im Gegensatz zu vielen anderen Branchen ist die Luftfahrtindustrie eine Branche, in der Handarbeit weit verbreitet ist, da es derzeit keine alternativen Herstellungsverfahren gibt, die durchführbar sind. In Anbetracht der Aufzeichnungen von Statista über den jährlichen Anstieg der Nachfrage von 2006 bis 2019 für die weltweite Passagiernachfrage im Luftverkehr (die Steigerungen reichten von 2,4 Prozent bis 8,1 Prozent, mit Ausnahme von 2009 auf dem Höhepunkt der Großen Rezession) und anderer Faktoren, ist eine höhere Effizienz obligatorisch, wenn die Industrie mithalten will.
Forscher versuchen herauszufinden, wie sich einige Prozesse automatisieren lassen, beispielsweise das Handauflegen. Aber es gibt andere automatisierte Maßnahmen, die derzeit verfügbar sind, einschließlich der Projektion von Anweisungen für die Montage auf Arbeitsstationen und für automatisierte Dichtungs-, Befestigungs-, Markierungs- und Materialhandhabungsprozesse.
Allein der Bedarf der kommerziellen Luftfahrt würde eine effektive Verdopplung der Produktionsraten erfordern, sagte John D. Russell, Leiter der Abteilung für Strukturtechnologie am Air Force Research Laboratory.
Zusätzlich zu kommerziellen Flugzeugen erforscht das Militär zerbrechliche Flugzeuge, die zu Tausenden produziert werden könnten.
Schließlich hat das Lufttaxi-Konzept bei traditionellen Luftfahrtunternehmen und Unternehmen wie Uber an Bedeutung gewonnen und würde noch mehr Produktion erfordern.
„Für jeden dieser Fälle höre ich von meinen Kontakten in der Branche, dass die USA derzeit nicht über die Kapazität verfügen“, sagte Russell und warnte davor, dass seine Informationen von vor dem weltweiten Ausbruch des Virus stammten. „Wenn alle drei gleichzeitig wahr werden, muss die Branche kreativ werden, um das Kapazitätsproblem zu lösen.“
„Die große Alternative, die ich höre, ist der Einsatz von Automatisierung zur Steigerung von Produktivität und Durchsatz, insbesondere für die kommerzielle Luftfahrt. Unternehmen erforschen Möglichkeiten, wie die Automatisierung die Dinge verbessern kann, von der Teilefertigung bis zur Montage. Ich habe gehört, dass die Investitionskosten für die Automatisierung geringer sind als die für das Hinzufügen neuer Produktionslinien.“
Russell sagte, er wäre nicht überrascht, wenn die Lufttaxi-Industrie nach Offshore-Produktion suchen würde, da der Fahrzeugpreis wahrscheinlich ein wichtiger Faktor für ihr Geschäftsmodell sei. Er bezweifelt, dass wir ein Offshoring für die kommerzielle Luftfahrt sehen würden, da die Branche aufgrund des hohen Qualifikationsniveaus der Arbeitskräfte wahrscheinlich an etablierten Lieferantenbeziehungen festhalten würde. Offshoring wäre offensichtlich keine Option für Militärfahrzeuge, stellte er fest.
Die Auslieferung von 40.000 Flugzeugen in 20 Jahren würde die Produktion von 2.000 Flugzeugen pro Jahr erfordern, was viel mehr ist als die Auslieferungen vor der Pandemie.
Ein Lieferrückstand entstand, als die Hersteller nicht schnell genug aufrüsten konnten, um die erhöhte Nachfrage zu befriedigen, die durch einen Anstieg des Luftverkehrs verursacht wurde.
Darüber hinaus betrachten Verbraucher Flugreisen jetzt als Notwendigkeit statt als Luxus und haben die Mittel, um für persönliche Reisen zu bezahlen.
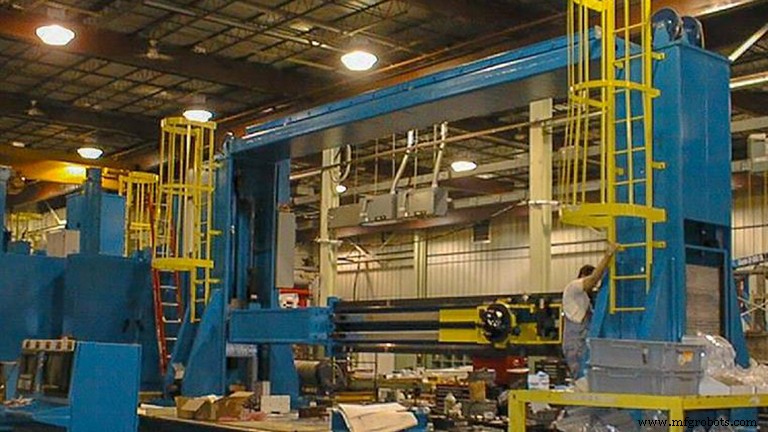
Infolgedessen erweiterten die kommerziellen Fluggesellschaften ihr Angebot, um diesen flughungrigen Verbrauchern Flexibilität bei den Startzeiten zu bieten.
Boeing hatte am 1. Mai einen Auftragsbestand von 5.049 Flugzeugen, während die Auftragsrückstände von Airbus bis zum 31. März auf 7.650 angestiegen waren.
Vor der Pandemie wurde erwartet, dass eine Wiederbelebung des Wettbewerbs zwischen Boeing und Airbus zu einer Rekordauslieferung ihrer äußerst beliebten Schmalrumpfplattformen und einem jährlichen Produktionswachstum von 9,4 Prozent im Jahr 2019 führen würde. Boeing und Airbus sollten voraussichtlich mehr produzieren laut einer Pressemitteilung des Forschungs- und Analyseunternehmens Frost &Sullivan von Mitte Juni 2019 mehr als 1.750 Flugzeuge im vergangenen Jahr, gegenüber 1.606 Einheiten im Jahr 2018.
Bis August jedoch senkten andere diese Zahlen.
Laut einem Artikel in der Zeitung The Guardian war die weltweite Flugzeugproduktion nach dem Flugverbot für Boeings 737-Max-Jet im März 2019 nach zwei tödlichen Abstürzen um ein Viertel zurückgegangen. ADS, die britische Lobbygruppe für Luft- und Raumfahrt, sagte, dass im Juli 2019 88 Flugzeuge ausgeliefert wurden, was einem Rückgang von 24 Prozent gegenüber den Auslieferungen im Vorjahresmonat entspricht, wobei der Rückgang hauptsächlich auf den Einbruch der Produktion von Single-Aisle-Flugzeugen wie der 737 zurückzuführen ist /P>
Bis Ende letzten Jahres hatten Airbus und Boeing zusammen 1243 Flugzeuge ausgeliefert.
Die Branche bemüht sich, diese Zahlen zu erhöhen.
„Die beiden größten Hersteller von Verkehrsflugzeugen, Boeing und Airbus, investieren beide viel zusätzliches Geld in die Steigerung der Produktionsrate“, sagte Bill Bigot, Vizepräsident für Geschäftsentwicklung für Luft- und Raumfahrt und Verteidigung bei JR Automation.
Ende letzten Jahres hat Airbus in Hamburg, Deutschland, die hochautomatisierte Montagelinie für Rumpfstrukturen der A320-Familie implementiert.
Die neue Anlage verfügt über 20 Roboter, ein neues Logistikkonzept, eine automatisierte Positionierung durch Lasermessung sowie ein digitales Datenerfassungssystem, so das Unternehmen.
Neben dem Einsatz von Robotern implementiert Airbus auch neue Methoden und Technologien in der Material- und Teilelogistik, um die Produktion zu optimieren, die Ergonomie zu verbessern und die Durchlaufzeiten zu verkürzen. Dazu gehören die Trennung von Logistik- und Produktionsebene, eine bedarfsgerechte Materialnachschubversorgung und der Einsatz von fahrerlosen Transportfahrzeugen.
Etwa zur gleichen Zeit beendete Boeing jedoch eine vierjährige vollständige Automatisierungsbemühung in seiner Fabrik in Everett, Washington, in der Roboterarme verwendet wurden, um Befestigungselemente an zwei Hauptrumpfabschnitten seiner 777-Jetliner und der 777X einzusetzen, und entschied sich stattdessen für das manuelle Einsetzen von qualifizierte Mechaniker.
Laut veröffentlichten Berichten bohren Roboter die Löcher für die Befestigungselemente immer noch auf einem automatisierten „Flex-Track“-System, was zu einem kombinierten Mensch-Roboter-Prozess führt.
Der Aufwand kann sich am Ende aber auszahlen.
Die gescheiterten Versuche, Robotik einzusetzen, haben Boeing einige wertvolle Lektionen aus seinem „ersten sehr tiefen Eintauchen in diese Art von Technologie“ gelehrt, sagte Jason Clark, ein Boeing-Vizepräsident, der die 777X-Produktion überwacht, gegenüber der Los Angeles Times. „Es hat uns beigebracht, wie man für die Automatisierung entwirft“, wurde Clark in einem Artikel vom November zitiert.
Das neue Verfahren verursacht weniger Verschleiß bei den Arbeitern, da Maschinen, die von Electroimpact Inc. entwickelt wurden, eine der körperlich anstrengendsten Aufgaben der Rumpfmontage erledigen:laut dem Artikel der Times:Löcher durch Metall bohren.
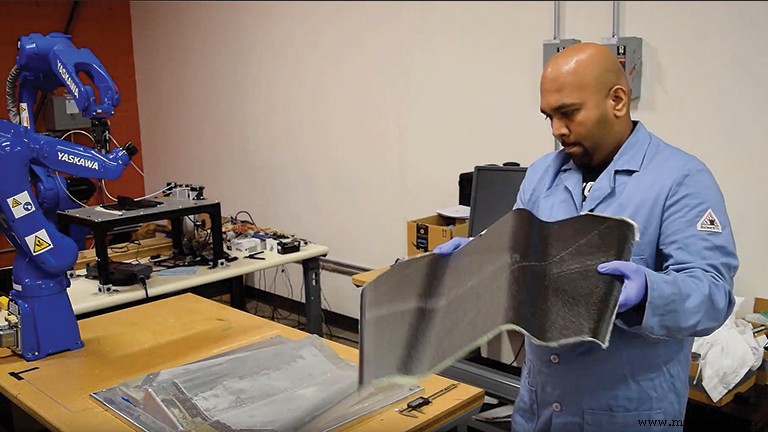
Außerdem „haben wir Teile des Aufbaus neu gestaltet, um Nieten durch weniger schwierige Formen von Befestigungselementen zu ersetzen und so die Ergonomie weiter zu verbessern“, sagte ein Unternehmenssprecher.
Nicht alle Maßnahmen zur Produktionssteigerung beinhalten neue Linien und Roboter.
In seinem Werk in North Charleston, S.C., rüstete Boeing Mechaniker mit Exoskeletten aus, um die Belastung durch anhaltende Überkopfarbeiten zu reduzieren; setzte laut Reuters Bluetooth-fähige intelligente Schraubenschlüssel ein, um sicherzustellen, dass Arbeiter das richtige Drehmoment auf eine Mutter aufbringen, und nutzte die virtuelle Realität für Mechaniker, um neue Werkzeuge zu testen.
Können Roboter Handauflegen übernehmen?
Bevor Rumpfstrukturen nach Hamburg oder in die Fabriken von Boeing im US-Bundesstaat Washington geliefert werden, werden sie in automatisierten Verbundherstellungsprozessen (ACM) hergestellt, einschließlich automatisierter Faserplatzierung und automatisierter Tape-Layup.
ACM eignet sich für mittelgroße oder große Teile wie Rümpfe, Flügel und Schotte, die ebenfalls entweder flach oder leicht konturiert sind.
Aber kleine und mittelgroße Verbundwerkstoffteile werden von Hand hergestellt, ein sehr ineffizienter Prozess, der viel Material verschwendet.
Das ist eine große Sache, denn diese Teile – Clips, Halterungen, I-Träger und Zugangstüren – können bis zur Hälfte des Gewichts einer Struktur ausmachen und für nur ein Flugzeug in die Tausende gehen.
„Außerdem müssen diese Teile, die von Hand aufgelegt werden müssen, gekürzt und gestanzt, gequetscht werden, was auch immer“, sagte Les Cohen, ein Berater für Verbundwerkstoffe. „Das bedeutet, dass Ihr Buy-to-Fly-Verhältnis ein Faktor von 2 sein kann:Wenn Sie mit einem Material arbeiten, das 40 US-Dollar pro Pfund kostet, sind es effektiv 80 US-Dollar pro Pfund Material.“
Ein Team der University of Southern California hat kürzlich ein Demonstrationsprojekt zur Automatisierung des Layup mit Roboterarmen abgeschlossen.
Obwohl es keine Automatisierung gibt, gibt es immer noch Raum, um die im Flugzeugbau verwendeten Materialien zu verbessern.
Die Industrie versteht, dass das Autoklavieren von Teilen, die beim Debulking alle paar Schichten in Arbeit sind, zusammen mit dem Aushärten des letzten Teils viel Zeit in Anspruch nimmt. Schnell härtende Harze, die die Eigenschaften von im Autoklaven gehärteten Teilen haben, aber ohne den Autoklavenprozess, sind die Antwort, aber sie sind nicht verfügbar, sagte Cohen. Mit Investitionen von durchschnittlich bis zu fünf Jahren und geschätzten Kosten von 10 Millionen US-Dollar für die Entwicklung neuer Materialien ohne Garantie, dass sie akzeptiert werden, ist es verständlich, dass diese Herausforderung nicht bewältigt wird, sagte er.
4. Industrielle Revolution startet langsam in der Luft- und Raumfahrt
Industrie 4.0 mit ihrem Versprechen von höherer Produktivität und Qualität könnte auch dazu beitragen, die Luftfahrtproduktion anzukurbeln, aber die Industrie hat sich nur langsam an die vernetzte, digitalisierte und datengesteuerte Welt der vierten industriellen Revolution angepasst.
„Ich würde sagen, dass die Dinge jetzt in der Produktion online gehen und Ergebnisse liefern. Wir sind sehr daran interessiert und gerade an dem Punkt angelangt, an dem wir dies auf Programmebene einführen und einer Fabrik wirklich etwas geben können, das sich absolut auf ihre Effizienz auswirkt“, sagte Andrew Purvis, Projektmanager für Verbundwerkstoffe und Automatisierung bei Electroimpact Inc. „Wenn Sie beginnen, die Daten zu sammeln und die Zahlen zu zerkleinern, finden Sie in diesem Datenberg viel Gold und oft auch Diamanten, Dinge, die Ihre Produktion wirklich ankurbeln.“
Reif für die Automatisierung ist die Qualitätsseite der Produktion, sagte Purvis.
Electroimpact baut die Qualitätsüberwachung in Systeme mit Inspektionstechnologie ein, die alles misst, was seine AFP-Maschinen tun, während sie ein Teil bauen oder drucken. Die automatische Inspektion ermöglicht einen Prozess, den das Unternehmen „kontinuierliche Optimierung“ nennt.
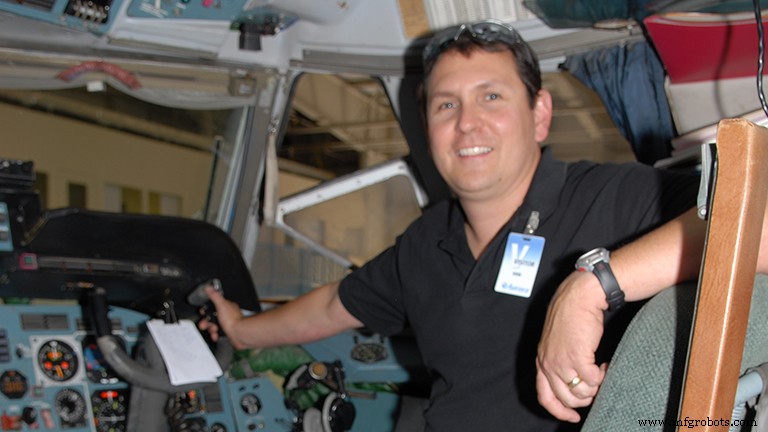
„Das System kalibriert sich tatsächlich selbst, indem es beobachtet, was es tut, und es passt sich kontinuierlich an“, sagte er. „Als ob eine AFP-Maschine oder ein Drucker die Ausgabe mit einer Kamera oder Sensoren betrachten und sagen könnte:‚Hey, ich habe bemerkt, dass du anfängst, ein wenig abzudriften, also werde ich das kompensieren‘.“
Zum jetzigen Zeitpunkt ist die Einführung von Industrie 4.0 eher ein Streben als eine Errungenschaft, was zum Teil auf die Auswirkungen auf Cybersicherheit und Datenmanagement zurückzuführen ist, sagte Mick Maher, Präsident des Beratungsunternehmens Maher Associates.
„Ich glaube nicht, dass die Luft- und Raumfahrtindustrie langsamer vorankommt als jede andere Branche“, sagte er. „Ich denke, Industrie 4.0 ist noch zu unreif, um die Zügel an dieser Stelle zu übergeben. Automatisierung ist jedoch ein wichtiger Bestandteil von Industrie 4.0. Aber genauso wie es Teile der Automatisierung gibt, die ausgereift sind, wie Tape Placement, Fiber Placement, gibt es noch viel Entwicklungsbedarf.“
Große Gewinne zu erzielen
Randy Rounkles, technischer Direktor für Luft- und Raumfahrt bei JR Automation, war zuvor bei Spirit Aerosystems, wo er Teil eines Teams war, das Anfang 2019 Industrie 4.0 einführte.
Die Legacy-Zielproduktion bei Spirit, einem früheren Boeing-Werk, das 2005 veräußert wurde, betrug 21 Flugzeuge pro Monat, basierend auf seinen physischen Einschränkungen und seiner Größe, sagte Rounkles. Bevor er ging, betrug die monatliche Produktion des Werks 57 Flugzeuge, dazu trugen zusätzliche Schichten, mehr Mitarbeiter und eine stärkere Automatisierung bei, insbesondere bei der Befestigung.
„Eines der (letzten) Projekte vor meiner Abreise war die Erhebung von Industrie 4.0-Daten zur Gerätenutzung, und das hat das Gesicht dieses Unternehmens tatsächlich verändert, indem es verstanden hat, was seine Geräte tun und wozu sie in der Lage sind“, sagte Rounkles. "Und es hatte einen erheblichen Einfluss auf die Kapitalausgaben für zukünftige Zinsen."
„Digitales Dilettantismus“
Auf der ganzen Welt wird an der Anwendung von Industrie 4.0 in der Luft- und Raumfahrtfertigung geforscht, aber die Einführung ist langsam und die aktuelle Flugzeugproduktion ist eher analog als digital, sagte Russell von AFRL.
„Unternehmen versuchen sich an der Digitalisierung, um spezifische Schwachstellen wie Asset-Tracking zu lösen, aber nur wenige Hersteller haben eine echte unternehmensweite Industrie-4.0-Umgebung“, sagte er.
In Bezug auf den aktuellen Stand von Industrie 4.0-Komponenten wird die additive Fertigung für Werkzeuge und nicht strukturelle Teile untersucht, einige Prozesse werden durch den Einsatz von Robotern automatisiert, und im Hinblick auf die Datenanalyse wurde F&E durchgeführt, um die zerstörungsfreie Prüfung zu verbinden Daten zurück zu den Originalmodellen, um die Auswirkungen von Herstellungsfehlern auf die Teileleistung zu verstehen, sagte Russell.
In dem auf YouTube geposteten Video glättet ein Kuka-Roboterarm mit einer End-of-Arm-Rolle die Schicht aus Prepreg-Verbundwerkstoff über der vorherigen Schicht, während zwei Roboter mit Greifern das Material auf beiden Seiten straff halten.
Wie viele Handlaminierkünstler haben sich dieses Äquivalent einer dritten Hand gewünscht, das in der Aufnahme der intelligenten Roboterzelle demonstriert wurde?
Die Zelle und die gesamte Technologie dahinter ist ein Demonstrationsprojekt von Satyandra K. Gupta, einem Maschinenbau- und Informatikprofessor an der University of Southern California, seinen Kollegen und Studenten. Sie haben das Teil auf der Grundlage von Vorschlägen von Boeing, Lockheed Martin und United Technologies hergestellt, mit dem Ziel, die Machbarkeit der Automatisierung zu bewerten. Testergebnisse zu Teilen, die mit ihrer Roboterautomatisierung hergestellt wurden, wurden an die drei Unternehmen gesendet, sagte Gupta.
„Im Moment ist die größte Herausforderung, der sich alle in der Luft- und Raumfahrt gegenübersehen, der Mangel an Arbeitskräften“, sagte er.
Mit Roboterarmen beim Layup könnte ein menschlicher Bediener mehrere Zellen gleichzeitig überwachen, erklärte er. Dies würde nicht nur die Kapazität erhöhen, sondern könnte möglicherweise den Schritt der Volumenreduzierung im Teileherstellungsprozess eliminieren und gleichzeitig die Qualität gewährleisten.
Das liegt daran, dass für ein hypothetisches kritisches Teil aus 100 Lagen Prepreg das in Bearbeitung befindliche Teil verpackt und alle drei (oder fünf) Lagen einer Vakuumanwendung unterzogen werden muss, um sicherzustellen, dass keine Hohlräume vorhanden sind, für insgesamt 33 Debulkings.
Aber mit Robotern kann der Druck des Roboterwerkzeugs im Gegensatz zur menschlichen Hand gemessen werden, sodass die Qualität gewährleistet ist und der Prozess schneller ablaufen kann.
Die Automatisierung des Prozesses macht ihn nicht nur konsistent und rationalisiert. Handlaminieren ist eine mühsame Arbeit, die körperlich anstrengend ist.
Gupta und sein Team arbeiteten über zweieinhalb Jahre und integrierten die Roboterarme mit End-of-Arm-Tooling, Computervision, Kraftmessung, Algorithmen für künstliche Intelligenz, fortschrittlichen Steuerungen und einer Mensch-Maschine-Schnittstelle. Ihre Demonstrationsteile bestanden aus bis zu 15 Schichten einer Standard-Kohlenstofffaser-Prepreg-Schicht auf Epoxidbasis.
Der herausforderndste Teil ihrer Arbeit war die Integration der Computer-Vision in Echtzeit.
„Sie müssen die Kamera dazu bringen, zu sehen, welche Defekte sich bilden“, sagte Gupta. „(Jetzt) wenn der Roboter eine Falte sieht, zieht er das Blatt manchmal in diese Richtung, dann in diese Richtung … “
Wenn die Zelle auf ein Problem stößt, das sie nicht beheben kann, benachrichtigt sie einen menschlichen Bediener mit einem Piepton, einer E-Mail oder einem Text.
Aber das ist nur wenn nötig.
„Manchmal verläuft der gesamte Prozess reibungslos“, sagte Gupta.
Schau, Ma, keine Hände! (End-of-Arm-Tooling führt automatisiertes Pre-Preg-Layup durch)
Der vor drei Jahren eröffnete Zubau Rego-Fix beinhaltet fortschrittliche energie- und ressourcenschonende Eigenschaften. Dazu gehören ein spezielles Luftwechsel-Ventilatorsystem, eine Holzpelletsheizung, mehrere fortschrittliche Klimaanlagen, ein „grünes“ Dach und der Einsatz von sowohl natürlicher als auch sensorgesteuerter Beleuchtung.
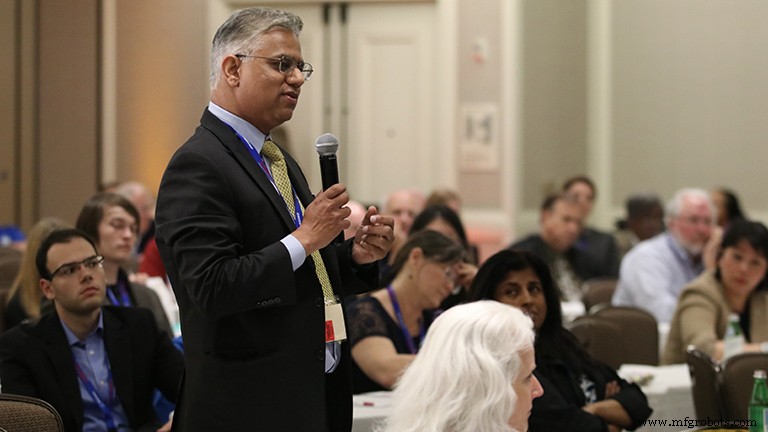
Sieben Mal pro Stunde tauscht die Air-Change-Lüfteranlage die Luft innerhalb des Neubaus aus. Es entzieht der Produktionshalle Abwärme – Wärme, die hauptsächlich von den großen Luftkompressoren erzeugt wird, die für die Werkzeugmaschinen des Unternehmens erforderlich sind. Während der kalten Monate, die den Rest des Jahres ausmachen, wird die zurückgewonnene Abwärme dann zum Erwärmen der einströmenden Frischluft verwendet, die das System von außerhalb des Gebäudes ansaugt und in die Produktionshalle zirkuliert.
Darüber hinaus trägt zirkulierendes Wasser in einem geschlossenen System dazu bei, die Luftkompressoren in der Fertigungshalle während des Betriebs kühl zu halten. Beim Kühlprozess wird das Wasser heiß und dieses erwärmte Wasser wird dann in einem 1849-Gallonen (7007-l)-Tank gespeichert. Dieses Wasser wird verwendet, um das Gebäude über ein in die Böden der Bürobereiche des Gebäudes eingebautes Heizsystem weiter zu heizen.
Die Anlage umfasst auch ein 390-kW-Heizsystem, das Holzpellets anstelle von fossilen Brennstoffen verbrennt. Die Pellets sind ein Nebenprodukt der Holz- und Möbelindustrie, die in der Gegend weit verbreitet sind. Das System verbraucht sehr wenig Pellets, da es als Backup zu den anderen Heizquellen fungiert und nur bei extrem niedrigen Außentemperaturen eingesetzt wird.
Im Sommer sorgt eine energiesparende Progressiv-Klimaanlage mit drei Einheiten im Zusammenspiel mit dem Unterflursystem und dem Luftaustauschsystem dafür, dass der Anbau kühl bleibt. Die Luftaustauscheinheit entzieht dem Gebäude Wärme und kaltes Wasser zirkuliert durch das Bodensystem.
Steigt die Temperatur innerhalb des Gebäudes über ein bestimmtes Niveau, schaltet sich eine der Einheiten der progressiven Klimaanlage ein, um das Bodensystem und die Luftwechseleinheit zu unterstützen. Die Klimaanlagen sind drehzahlgeregelt, d. h. wenn die Temperatur weiter steigt und die erste Klimaanlage ihre Grenze überschreitet, wird die zweite Klimaanlage im System aktiviert. Und wenn wiederum die zweite Einheit ihre Drehzahlgrenze erreicht, wird die dritte Einheit aktiviert. Sobald das Gebäude abzukühlen beginnt, schalten sich die einzelnen Klimageräte in umgekehrter Reihenfolge ab.
Die Außenwände des Gebäudes sind komplett isoliert. Im Gegensatz zu typischen Dachdesigns ist das eine, für das sich Rego-Fix entschieden hat, ziemlich ungewöhnlich mit hohen Dämmeigenschaften. Es wird als „grünes“ oder „bepflanztes“ Dach bezeichnet und ist mit Erde bedeckt, auf der tatsächlich Rasen wächst. Zusätzlich zu seinem Isolierwert fängt das Dach Regenwasser auf, das dann in einem 50.000-l-Tank (13.200 Gallonen) gesammelt und für die Toilettenspülung in den Toiletten des Gebäudes verwendet wird.
Zusammen sorgen alle Heiz- und Kühlfunktionen des Gebäudes für konstante und konstante Umgebungstemperaturen im Produktionsbereich. Dies hat einen entscheidenden Herstellungsvorteil. Die konstante Temperatur trägt dazu bei, eine gleichbleibende Werkzeugmaschinengenauigkeit für die Herstellung der hochpräzisen Werkzeughaltesysteme des Unternehmens aufrechtzuerhalten.
Zur weiteren Energieeinsparung verfügt das neue Produktionsgebäude über viele große, dreifach verglaste Isolierfenster, die viel natürliches Licht hereinlassen. Darüber hinaus sind die Fenster mit Jalousien ausgestattet, die sich automatisch öffnen und schließen. Dies ist eine große Hilfe, um das Gebäude im Sommer kühl zu halten. Während die Schirme viel Wärme abhalten, sind sie perforiert, um Licht hereinzulassen.
Wo zusätzliche Beleuchtung benötigt wird, werden LED-Energiesparleuchten zusammen mit Bewegungssteuerungsaktivierung verwendet. Es gibt keine Wandschalter im Gebäude, und das Licht geht nur an, wenn Bereiche besetzt sind, und schaltet sich aus, wenn dies nicht der Fall ist.
Automatisierungssteuerung System
- Die Zukunft der Automatisierung in der Luftfahrtindustrie
- Wie die Automatisierung im Jahr 2020 alle Arten der Fertigung revolutioniert
- Die Rolle von Robotik und Automatisierung in Industrie 4.0
- Automatisierung und die Modeindustrie:Eine stille Revolution
- Automatisierung in der Industrie 4.0
- Weltweite Pkw-Nachfrage sinkt laut Umfrage um 11 %
- STAEDTLER:Der Wert der Automatisierung in der Fertigungsindustrie
- Nachfrage nach Automatisierung, Roboterspitzen
- Bewältigung des großen Bedarfs an Automatisierung von Verbundwerkstoffen
- Wie können Roboter Unternehmen helfen, die steigende Nachfrage zu befriedigen?