Die verbundene Steuerung
Das Internet und Cloud-basiertes Computing verändern die Art und Weise, wie Hersteller CNC-Werkzeugmaschinen betreiben. Ist Ihr Shop darauf vorbereitet?
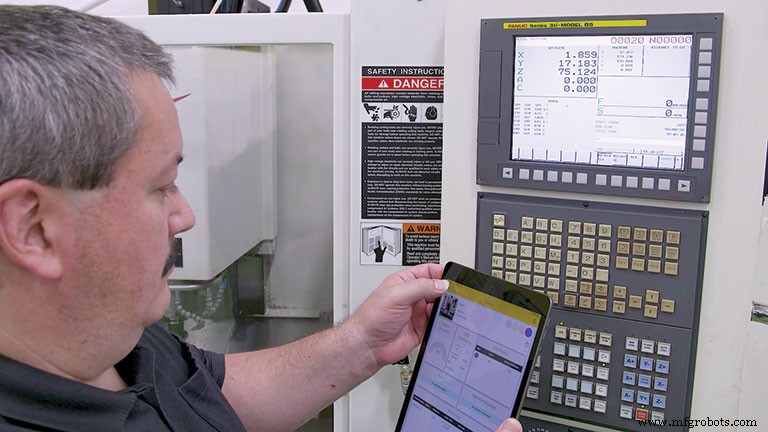
Ethernet-Ports tauchten erstmals vor mehr als 20 Jahren auf CNC-Drehmaschinen und Bearbeitungszentren auf. Der MTConnect-Kommunikationsstandard für Werkzeugmaschinen feierte sein offizielles US-Debüt auf der IMTS 2010 in Chicago. Kurz darauf begannen Hersteller, über Cloud Computing und das industrielle Internet der Dinge (IIoT) zu sprechen, Begriffe, die zum Mainstream wurden, als der deutsche Wirtschaftswissenschaftler Klaus Schwab 2015 ein Papier veröffentlichte, in dem er feststellte, dass die Welt in eine vierte industrielle Revolution eingetreten sei.
Willkommen im Jahr 2021. Für Besitzer von Maschinenhallen, CNC-Programmierer und Fertigungsingenieure sollte inzwischen klar sein, dass sich die Zerspanungsindustrie in den letzten zwei Jahrzehnten erheblich verändert hat. CNC-Werkzeugmaschinen sind viel intelligenter als früher und in der Lage, erhebliche Datenmengen über alles zu generieren, was hinter dem Glas vor sich geht. Auch die Fertigungssoftware ist intelligenter geworden und bietet Interoperabilität und Cloud-basierte Funktionen, von denen man um die Jahrhundertwende nur träumen konnte.
Ob all diese technische Zauberei eine gute Sache ist oder nicht, steht zur Debatte. Einige mögen argumentieren, dass das Leben in der Fertigung bereits herausfordernd genug ist – wer braucht Big Data und intelligente Maschinen, wenn der Tag kaum genug Stunden hat, um Teile aus der Tür zu bringen? Andere sehen Industrie 4.0 und alles, was damit verbunden ist, als den klaren Weg nach vorne für Hersteller, und jeder, der sich nicht darauf einlässt, wird bald aus dem Geschäft sein.
FOCAS gewinnen
Die Wahrheit liegt irgendwo dazwischen. Paul Webster, Director of F.A. Engineering bei FANUC America Corp. mit Hauptsitz in Rochester Hills, Michigan, stellte fest, dass CNC-Werkzeugmaschinen schon vor dem Jahr 2000 netzwerk- und internetfähig waren. Shops, die sich dafür entscheiden, diese Funktion zu ignorieren, kommen immer noch gut voran, vielen Dank, und werden dies auch in den kommenden Jahren tun. Und doch würden nur wenige argumentieren, dass die Konnektivität von Werkzeugmaschinen und die dadurch ermöglichte größere Transparenz der Bearbeitungsprozesse niemals eine schlechte Sache sind und den Unterschied zwischen einem profitablen Job und einem Job ausmachen können, den Sie genauso schnell vergessen werden.
„Wir haben unsere FOCAS API (Application Programming Interface) in den frühen 90er Jahren sowie Glasfaser- und dann Ethernet-Ports eingeführt, sodass der Anschluss einer CNC schon seit geraumer Zeit einfach ist“, sagte er. „Der schwierige Teil war schon immer herauszufinden, welche Daten Sie benötigen und was Sie damit machen werden, sobald Sie sie haben.“
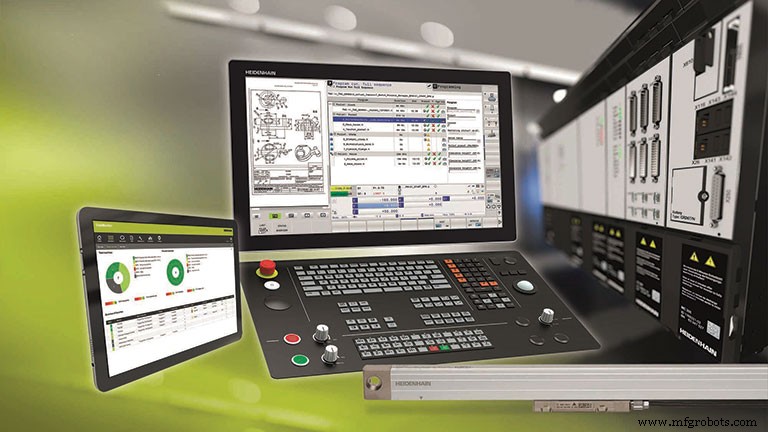
Zu diesen Daten gehören Alarmhistorien, Vorschubgeschwindigkeiten und Spindel-Override-Einstellungen, Servomotor- und Spindeltemperaturen, Stromverbrauch, Makrovariablen und vieles mehr, die alle kontinuierlich und automatisch von der Werkzeugmaschine abgerufen werden können. Hinzu kommen verschiedene vom Bediener bereitgestellte Eingaben – Auftragsnummer, Produktionsstatus, Schneidwerkzeugverbrauch und sogar Informationen zur Teilequalität – und es wird nicht schwieriger, ein vollständiges Bild der Fertigungsaktivitäten zu erhalten, als einen Blick auf das Dashboard der Überwachungssoftware zu werfen, die diese Daten sammelt .
Im Fall von FANUC ist dies MT-LINKi, eine markenunabhängige Analyseplattform, die mehr als 1.000 CNC-Werkzeugmaschinen gleichzeitig überwachen kann, sowie FASData, ein Produktionsüberwachungsprogramm. Andere Hersteller von Steuerungen bieten ähnliche Lösungen an, ebenso wie viele Werkzeugmaschinenhersteller, Lieferanten von Schneidwerkzeugen und Softwareentwickler von Drittanbietern. Alle bieten die Möglichkeit, einen zugegebenermaßen riesigen Datenberg zu sammeln und auf eine für Menschen sinnvolle Weise darzustellen, sodass sie auf Trends und potenzielle Probleme reagieren können, lange bevor sie sich negativ auf das Produktionsniveau auswirken können.
Das Cloud-Rätsel
Dann stellt sich die Frage, wo der beste Ort ist, um diese Daten zu speichern und die zu ihrer Analyse verwendete Software unterzubringen. Sollten sich beide in der Cloud in einer externen Hosting-Einrichtung befinden und von dedizierten Hardware- und Softwarespezialisten verwaltet werden? Oder ist eine „On-Premise“-Installation angemessener, die alle internen IT-Talente des Shops nutzt?
Webster und die anderen für diesen Artikel Befragten stimmten weitgehend darin überein, dass ersteres zwar oft der sicherere und kostengünstigere Ansatz ist, viele Betriebe jedoch skeptisch bleiben, wenn Teileprogramme und Produktionsdaten ihre Einrichtung verlassen. Dasselbe gilt für Gisbert Ledvon, Direktor für Geschäftsentwicklung für Werkzeugmaschinen bei Heidenhain Corp. mit Sitz in Schaumburg, Illinois. Er merkte an, dass Kunden die StateMonitor-Software des Unternehmens überall dort installieren können, wo sie es wünschen, fördert jedoch Installationen vor Ort, wann immer dies möglich ist.
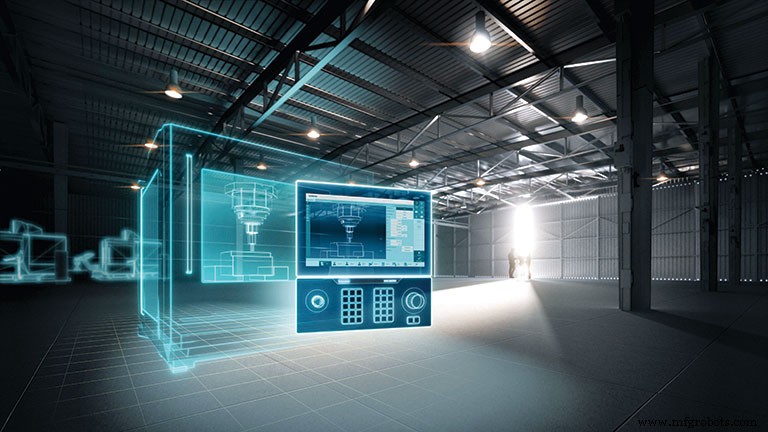
„Unsere Philosophie ist, dass Kunden ihr geistiges Eigentum schützen sollten, und für uns bedeutet das, ihre Werkzeugmaschinen und Softwaresysteme mit einem ordnungsgemäß gesicherten Unternehmensnetzwerk zu verbinden“, sagte er. „Es gab viele Fälle, in denen Geschäfte gehackt und zu Lösegeldzahlungen gezwungen wurden. Zugegeben, diese Angriffe werden normalerweise per E-Mail und nicht über die Werkzeugmaschinensteuerung durchgeführt, aber es gibt dennoch Anlass zur Sorge. Aus diesem Grund bietet die NTMA (National Tooling and Machining Association) Seminare an, die Herstellern zeigen, wie sie sich gegen diese Art von Cyberkriminalität schützen können.“
Trotzdem räumt Ledvon ein, dass die Cloud ein Technologietrend ist, der nur noch an Fahrt gewinnen wird. Um die damit verbundenen Risiken zu mindern, sind gute IT-Verwaltungspraktiken erforderlich. Installieren Sie eine robuste Firewall zwischen dem Netzwerk des Shops und der Außenwelt. Vermeiden Sie direkte CNC-zu-Cloud-Verbindungen, indem Sie externe Dateien, Softwareprogramme und Patches auf einen sicheren internen Server herunterladen und sie dann vor der Verteilung mit Antivirensoftware überprüfen. Schulen Sie alle Computerbenutzer darin, Passwörter zu verwalten, bösartige E-Mails und Websites zu erkennen und Unternehmensinformationen zu schützen. Die Liste geht weiter.
„Wenn man bedenkt, dass die Steuerung das Nervenzentrum jeder Werkzeugmaschine ist, bin ich nicht der Meinung, dass der Komfort des Cloud-Zugriffs das Risiko wert ist, dem Internet ausgesetzt zu sein“, sagte Ledvon. „All dies hält Hersteller jedoch nicht davon ab, eine Industrie 4.0-Strategie umzusetzen. Auf jeden Fall sollten sie ihre Werkzeugmaschinen vernetzen und Daten für die Analyse sammeln. Dadurch erhalten sie die Informationen, die sie benötigen, um Maschinen schneller einzurichten, Zykluszeiten zu verkürzen, die Werkzeuglebensdauer zu maximieren und alle anderen Vorteile zu nutzen, die die heutigen CNC-Steuerungen und Softwaresysteme bieten.“
Eingeborenes Talent
Ein weiterer Bestandteil von Industrie 4.0 ist der digitale Zwilling, der sich in diesem Fall auf ein virtuelles, aber hochgenaues und umfassendes Abbild einer CNC-Werkzeugmaschine bezieht. Laut Vivek Furtado, Head of Digitalization – Machine Tools bei Siemens Industry Inc., Elk Grove Village, Illinois, rationalisieren digitale Zwillinge das Design und den Einsatz von CNC-Maschinen und machen die Hersteller letztendlich effizienter.
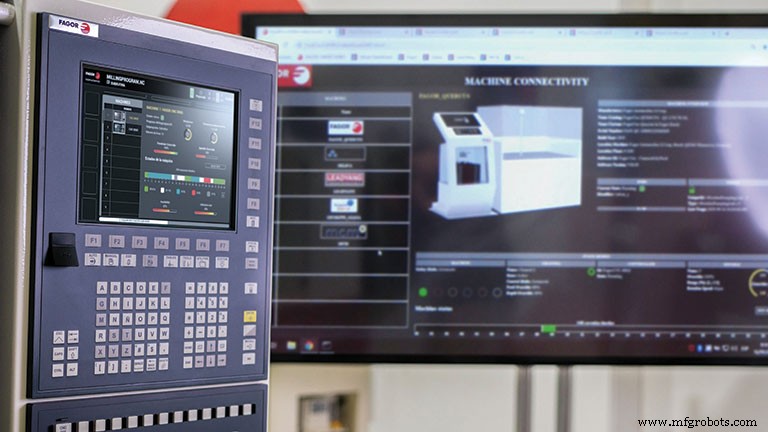
„Unsere SINUMERIK One-Steuerung ist als Digital Native bekannt, da sie von Grund auf für die Unterstützung des digitalen Zwillings und anderer Basistechnologien entwickelt wurde“, sagte er. „Sie gibt Herstellern von CNC-Werkzeugmaschinen die Möglichkeit, eine virtuelle Version einer Drehmaschine oder eines Bearbeitungszentrums zu erstellen, die alle Kinematiken und Betriebseigenschaften enthält. Dies reduziert die Entwicklungszeit und die Entwicklungskosten erheblich und stellt sicher, dass das Produkt die Anforderungen der Endbenutzer erfüllt.“
Digital-Twin-fähige Regler dienen anderen Zwecken. Sie beschleunigen die Einarbeitung neuer Mitarbeiter und verringern die Wahrscheinlichkeit, dass eine teure Werkzeugmaschine kaputt geht. Sie ermöglichen es Kalkulatoren, Aufträge genauer zu kalkulieren, Ingenieuren optimierte Fertigungsprozesse zu entwickeln und CNC-Programmierern die G-Code- und Schneidwerkzeugauswahl zu validieren, bevor sie Arbeiten an die Werkstatt senden. Sobald sie dort angekommen sind, erleichtern sie den Betrieb von Werkzeugmaschinen mit verbesserter Grafik und größerer Benutzerfreundlichkeit.
Jeder, der über ein High-End-CAM-System oder eine PLM-Software verfügt, könnte sagen, dass er das meiste davon ohne eine fortschrittliche CNC-Steuerung bewerkstelligen kann. Und obwohl es keinen Zweifel gibt, dass die Fähigkeiten dieser und anderer Softwareplattformen in den letzten Jahren dramatisch zugenommen haben, stellen Werkzeugmaschinen, die am digitalen Faden teilnehmen, Maschinenwerkstätten ein wichtiges Werkzeug zur Verfügung, eines, das den Datenaustausch verbessert und den Kreis der Interoperabilität schließt. P>
Anpassen und überwinden
Abgesehen von Digital Twinning schlug Furtado vor, dass CNC-Steuerungen viel intelligenter und benutzerfreundlicher werden, mit Funktionen und Merkmalen, die jeder Smartphone-Benutzer wiedererkennen wird. „Die meisten von uns erinnern sich, dass wir früher unsere Telefone benutzt haben, um Leute anzurufen“, sagte er. „Heute können Sie Ihre Gesundheit überwachen, nach Informationen suchen, Produkte bestellen und so weiter. Neuere Controller-Generationen bieten ähnliche Funktionen. Sie sind in der Lage, Informationen zu verarbeiten und Daten so aufzubereiten, dass sie von ihren menschlichen Bedienern oder anderen Systemen effektiver genutzt werden können.“
Diese Intelligenz erstreckt sich auch auf den Bearbeitungsprozess. Siemens, FANUC und Drittanbieter von Lösungen wie Caron Engineering bieten adaptive Steuerungsfunktionen, die kontinuierlich Spindel- und Achslasten, Maschinenvibrationen und ähnliche Faktoren überwachen, die sich auf die Lebensdauer von Schneidwerkzeugen und die Teilequalität auswirken. Diese intelligenten Systeme passen dann die Bearbeitungsparameter in Echtzeit an, optimieren den Materialabtrag und eliminieren potenzielle Probleme.
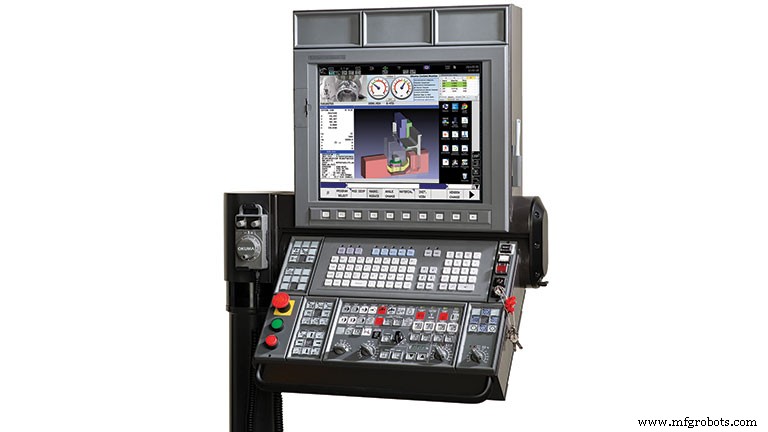
Fagor Automation Corp., Elk Grove Village, Illinois, ist ein weiterer Steuerungsanbieter, der den Industrie 4.0-Preis im Visier hat. Harsh Bibra, General Manager für Nordamerika bei Fagor, erklärte, dass seine ARFS-Steuerung (Adaptive Real-time Feed and Speed) all dies und mehr leistet, merkte jedoch an, dass diese Art von sensorbasierter Technologie auch für vorausschauende Wartung verwendet werden kann.
„Wir bieten auch unser i4.0 Connectivity Pack an“, sagte er. „Dadurch können Benutzer natürlich Bearbeitungsdaten sammeln, aber auch Dinge tun wie zustandsbasierte Warnungen senden, die Werkzeugmaschine abstimmen und ihre Firmware aktualisieren, Parametereinstellungen ändern und so weiter, alles von einem mobilen Gerät oder Remote-Computer aus.“
Der größte Engpass
Bibra sieht große Veränderungen vor sich. Neben dem verstärkten Einsatz von IIoT-fähigen Sensoren und Beschleunigungssensoren in Werkzeugmaschinen sowie intelligenter Steuerungen werden auch die Fabriken selbst intelligenter. Künstliche Intelligenz (KI), die weit über die gerade erwähnten adaptiven Fähigkeiten hinausgeht, wird sich durchsetzen und Türen zur automatisierten Entscheidungsfindung öffnen, die für eine weit verbreitete Lights-Out-Fertigung erforderlich ist.
All dies wird angesichts der Entwicklung und anschließenden Einführung von 5G-Mobilfunknetzen buchstäblich an Geschwindigkeit gewinnen, schlug Bibra vor. Diese werden nicht nur die Internetbandbreite erhöhen und die Latenzzeiten verringern, sondern möglicherweise auch die zuvor erwähnten Hacking-Befürchtungen lindern. „Steuerungen der Zukunft werden mit 5G ausgestattet sein und die von ihnen generierten Daten können dann drahtlos mit Geschwindigkeiten von bis zu 10 Gigabit pro Sekunde (Gbit/s) an sogenannte Edge Devices gesendet werden“, sagte er. „Wir gehen davon aus, dass diese Technologie innerhalb weniger Jahre die Art und Weise, wie Hersteller Informationen aus der Fertigung sammeln, grundlegend verändern wird.“
Die Kehrseite von Industrie 4.0 ist der Mangel an qualifizierten Arbeitskräften, die fortschrittliche Technologien verstehen und damit arbeiten können. Bibra sagte, dass eine Umschulung erforderlich sein wird, wenn die Hersteller technisch versierter werden. Allerdings sollten Bedenken hinsichtlich des Stammeswissens und des Erfahrungsverlusts aufgrund von Mitarbeiterabgang und Pensionierung zur alten Geschichte werden.
Besuch des Stores
Jim Kosmala, Vice President of Engineering and Technology bei Okuma America Corp., Charlotte, N.C., führt einen Großteil der heutigen zunehmenden Konnektivität auf die Verwendung von PC-basierten Steuerungen zurück. „Viele Leute vergessen, dass Okuma nicht nur ein Werkzeugmaschinenhersteller ist, sondern auch seine eigenen Servosysteme und Steuerungen herstellt. Diese laufen unter Microsoft Windows und verwenden einen Intel-Chip, die beide eine einfache Konnektivität bieten.“
PC-basierte Steuerungen machen es auch einfach, verschiedene Softwareprogramme auf der Steuerung zu installieren – zu Beginn der COVID-Pandemie konnten Okuma-Kunden beispielsweise mit anderen über Microsoft Teams zusammenarbeiten, Bildschirme teilen oder anderen nach Bedarf die Fernsteuerung überlassen. „Das ist die ganze Idee hinter unserem App Store“, sagte Kosmala. „Benutzer können alles, was sie brauchen, direkt auf die OSP-Steuerung herunterladen und installieren, wodurch die Notwendigkeit eines separaten PCs entfällt. Es stellt völlig neue Möglichkeiten für Zusammenarbeit und Konnektivität dar.“
Eine dieser Apps ist Connect Plan von Okuma, mit der Benutzer CNC-Werkzeugmaschinen überwachen und Betriebsdaten sammeln können. Es funktioniert mit fast allen Marken und Jahrgängen von Werkzeugmaschinen sowie mit Robotern und anderen Formen der Automatisierung. Laut Kosmala verwendet Connect Plan jedoch einen KI-Algorithmus, um sich die verfügbaren Informationen anzusehen und Trends zu identifizieren, die einem Menschen entgehen könnten.
Denken Sie an den Leiter einer Drehabteilung, der nach wochenlangem Blick auf Datenerfassungsberichte und Dashboards feststellt, dass eine bestimmte Drehmaschine dank der Kaffeegewohnheit des Bedieners jeden Morgen immer 10 Minuten zu spät anläuft oder dass die Spindeltemperatur an der Mühle am nächsten liegt Die Versandabteilung fällt jedes Mal, wenn sie die Ladetür öffnen. Kosmala erklärte, dass KI diese Trends viel schneller aufgreift als ein Mensch, wodurch Vorgesetzte in der Lage sind, potenzielle Problembereiche früher anzugehen. Darüber hinaus werden diese Informationen in einer Datenbank gespeichert, sodass kein Wissensverlust entsteht, wenn der Vorgesetzte das Unternehmen verlässt.
„Deming sagte uns, dass Sie ohne Daten nur eine andere Person mit einer Meinung sind“, sagte Kosmala. „Bei IIoT und Industrie 4.0 geht es darum, diese Daten zu sammeln und zu nutzen, um sie letztendlich in Wissen umzuwandeln. Das ist der erste Schritt für jeden auf dieser Reise. Wir haben jetzt virtuelle Konferenzen und die Möglichkeit, den Maschinenstatus oder das Produktionsniveau von überall aus zu überprüfen, und Zugriff auf Remote-Tools, die die Automatisierung vereinfachen. Wenn Sie das tun können, ohne in die Anlage gehen zu müssen, umso besser. Es dreht sich alles um die Steigerung der Effizienz und der Maschinenverfügbarkeit, die beide mit modernen CNC-Steuerungen leichter zu erreichen sind.“
Automatisierungssteuerung System
- Was mache ich mit den Daten?!
- Demokratisierung des IoT
- Die Zukunft der Rechenzentren
- Die Grundlagen elektrischer Schalttafeln
- Maschinelles Lernen im Feld
- Integration des industriellen Internets der Dinge
- Die Cloud im IoT
- Am Rande des Ruhms:Ermöglichung eines neuen Internet-Maschinenzeitalters
- Decoder ermöglicht die vernetzte Überwachung der Daten jeder Maschine
- Die vielen Vorteile intelligenter IIoT-vernetzter Fabriken