Bewältigen Sie die ständigen Herausforderungen der Langstreckenbearbeitung
Eine Reihe aktueller Trends in der Fertigung vergrößern die Schwierigkeit, Präzisionsbohrungen herzustellen und Drehoperationen mit Werkzeugen mit erweiterter Länge durchzuführen. Die Nachfrage nach engeren Toleranzen und fehlerfreier Wiederholgenauigkeit wächst kontinuierlich. Neue Hochleistungswerkstoffe für Werkstücke sind schwieriger zu bearbeiten und erhöhen die Belastung innerhalb des Bearbeitungssystems. Um Zeit und Geld zu sparen, konsolidieren Hersteller mehrere Teile zu einzelnen monolithischen Werkstücken, die die Bearbeitung tiefer Bohrungen und das Drehen komplexer Komponenten auf Multitasking-Werkzeugmaschinen erfordern.
Hersteller, die diese Herausforderungen meistern möchten, müssen alle Elemente ihrer Bearbeitungssysteme untersuchen und Techniken und Werkzeuge anwenden, die den Erfolg sicherstellen. Zu den Schlüsselelementen gehören Maschinenstabilität, Werkzeughalterung, Werkstückspannung und Schneidwerkzeuggeometrie. Im Allgemeinen bilden eine solide Befestigung, starre Werkzeuge und eine sorgfältige Werkzeuganwendung die grundlegende Grundlage für genaue, produktive Bohr- und Drehprozesse mit großer Reichweite.
Hersteller von Öl- und Gas-, Stromerzeugungs- und Luft- und Raumfahrtkomponenten sind erstklassige Kandidaten für aktualisierte Werkzeuge und Techniken, da sie regelmäßig mit großen, komplexen Teilen mit Merkmalen arbeiten, die den Einsatz von Werkzeugen mit verlängerter Länge erfordern. Viele der Teile bestehen aus zähen Legierungen, die schwer zerspanbar sind und dadurch hohe, vibrationserzeugende Schnittkräfte erzeugen. Im Allgemeinen kann fast jeder Hersteller von der Verbesserung der Produktivität und der Reduzierung der Kosten bei Bohrvorgängen mit großer Reichweite profitieren.
BIEGUNG UND VIBRATION
Das Tiefbohren unterscheidet sich von anderen Schneidoperationen dadurch, dass die Schneide in einem größeren Abstand von der Verbindung zur Maschine in der Bohrung arbeitet. Langstrecken-Innendrehoperationen weisen ähnliche Bedingungen auf, und sowohl diese Bohr- als auch Drehoperationen können Löcher mit unterbrochenen Schnitten beinhalten, wie dies bei Werkstücken wie Pumpen- oder Kompressorgehäusen der Fall ist. Der Betrag des resultierenden Werkzeugüberhangs wird durch die Tiefe der Bohrung bestimmt und kann zu einer Durchbiegung der Bohrstange oder des Drehwerkzeugs mit verlängerter Länge führen.
Durchbiegung verstärkt die sich ändernden Kräfte in einem Schneidprozess und kann Vibrationen und Rattern verursachen, die die Oberflächenqualität der Teile verschlechtern, Schneidwerkzeuge schnell verschleißen oder brechen und Werkzeugmaschinenkomponenten wie Spindeln beschädigen und teure Reparaturen und lange Ausfallzeiten verursachen. Die unterschiedlichen Kräfte resultieren aus Unwuchten von Maschinenkomponenten, mangelnder Systemsteifigkeit oder Resonanzschwingungen von Elementen des Bearbeitungssystems. Die Schneiddrücke ändern sich auch, wenn das Werkzeug periodisch geladen und entladen wird, während sich Späne bilden und brechen. Zu den negativen Auswirkungen von Bearbeitungsvibrationen gehören eine schlechte Oberflächengüte, ungenaue Bohrungsabmessungen, schneller Werkzeugverschleiß, reduzierte Materialraten, erhöhte Produktionskosten und Schäden an Werkzeughaltern und Werkzeugmaschinen.
MASCHINENSTEIFIGKEIT UND WERKSTÜCKSPANNUNG
Der grundlegende Ansatz zur Steuerung von Schwingungen bei Bearbeitungsvorgängen umfasst die Maximierung der Steifigkeit der Elemente des Bearbeitungssystems. Um unerwünschte Bewegungen einzuschränken, sollte eine Werkzeugmaschine aus starren, schweren Konstruktionselementen bestehen, die mit Beton oder einem anderen vibrationsabsorbierenden Material verstärkt sind. Maschinenlager und Buchsen müssen fest und fest sein.
Werkstücke müssen innerhalb der Werkzeugmaschine genau positioniert und sicher gehalten werden. Vorrichtungen sollten mit Einfachheit und Steifigkeit als Hauptanliegen entworfen werden, und Klemmen sollten so nah wie möglich an den Schneidvorgängen angeordnet sein. Aus Werkstücksicht sind dünnwandige Teile oder Schweißteile und solche mit freitragenden Abschnitten bei der Bearbeitung anfällig für Vibrationen. Teile können neu gestaltet werden, um die Steifigkeit zu verbessern, aber solche Konstruktionsänderungen können das Gewicht erhöhen und die Leistung des bearbeiteten Produkts beeinträchtigen.
WERKZEUGHALTUNG
Um die Steifigkeit zu maximieren, muss eine Bohrstange oder Wendestange so kurz wie möglich sein, aber lang genug bleiben, um die gesamte Länge der Bohrung oder des Bauteils zu bearbeiten. Der Durchmesser der Bohrstange sollte so groß wie möglich sein, der in die Bohrung passt und dennoch eine effiziente Abfuhr der geschnittenen Späne ermöglicht.
Wenn sich Späne bilden und brechen, steigen und fallen die Schnittkräfte. Die Kraftschwankungen werden zu einer zusätzlichen Schwingungsquelle, die mit der Eigenschwingung des Werkzeughalters oder der Maschine sympathisch zusammenwirken und sich selbst erhalten oder sogar verstärken kann. Andere Quellen solcher Vibrationen sind verschlissene Werkzeuge oder solche, die nicht tief genug gehen. Diese verursachen Prozessinstabilität oder Resonanzen, die sich auch mit der Eigenfrequenz einer Maschinenspindel oder des Werkzeugs synchronisieren, um dann unerwünschte Vibrationen zu erzeugen.
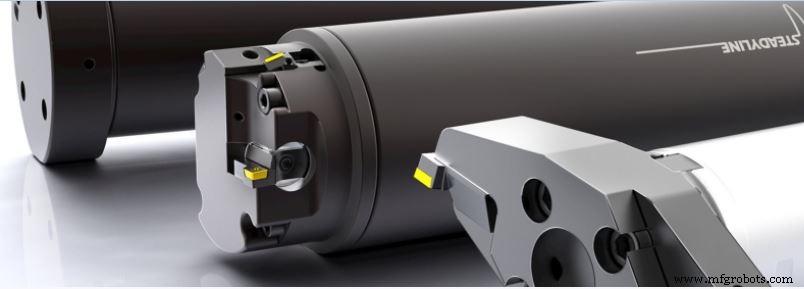
Ein langer Bohrstangen- oder Drehstangenüberhang kann Vibrationen in einem Bearbeitungssystem auslösen. Der grundlegende Ansatz zur Vibrationskontrolle beinhaltet die Verwendung von kurzen, starren Werkzeugen. Je größer das Verhältnis von Stangenlänge zu Durchmesser ist, desto größer ist die Wahrscheinlichkeit, dass Vibrationen auftreten.
Unterschiedliche Stangenmaterialien sorgen für unterschiedliches Schwingungsverhalten. Stahlstangen sind im Allgemeinen vibrationsbeständig bis zu einem Verhältnis von Länge zu Stangendurchmesser (L/D) von 4:1. Schwermetallstangen aus Wolframlegierungen sind dichter als Stahl und können L/D-Verhältnisse von Stangen im Bereich von 6:1 handhaben. Vollhartmetallstangen bieten eine höhere Steifigkeit und ermöglichen Stangenverhältnisse von bis zu L/D von 8:1, zusammen mit dem möglichen Nachteil höherer Kosten, insbesondere wenn Stangen mit großem Durchmesser erforderlich sind.
Eine alternative Möglichkeit, Vibrationen zu dämpfen, beinhaltet einen abstimmbaren Stab. Die Stange verfügt über einen internen Massendämpfer, der so konzipiert ist, dass er mit der unerwünschten Vibration phasenverschoben mitschwingt, ihre Energie absorbiert und die Vibrationsbewegung minimiert. Die Steadyline ® System von Seco Tools (siehe Seitenleiste) verfügt beispielsweise über einen vorab abgestimmten Schwingungsdämpfer, bestehend aus einer Tilgermasse aus hochverdichtetem Material, die über radiale Dämpfungselemente in der Meißelhalterstange aufgehängt ist. Die Dämpfermasse absorbiert Vibrationen sofort, wenn sie vom Schneidwerkzeug auf den Stangenkörper übertragen werden.
Eine komplexere und teurere aktive Werkzeugvibrationskontrolle kann die Form von elektronisch aktivierten Geräten annehmen, die das Vorhandensein von Vibrationen erkennen und elektronische Stellglieder verwenden, um eine sekundäre Bewegung im Werkzeughalter zu erzeugen, um die unerwünschte Bewegung aufzuheben.
WERKSTÜCKMATERIAL
Die Schnitteigenschaften des Werkstückmaterials können zur Schwingungserzeugung beitragen. Die Härte des Materials, eine Neigung zu Aufbauschneidenbildung oder Kaltverfestigung oder das Vorhandensein von harten Einschlüssen verändern oder unterbrechen die Schnittkräfte und können Vibrationen erzeugen. Bis zu einem gewissen Grad können durch die Anpassung der Schnittparameter Vibrationen bei der Bearbeitung bestimmter Materialien minimiert werden.
SCHNEIDWERKZEUGGEOMETRIE
Das Schneidwerkzeug selbst unterliegt einer tangentialen und radialen Auslenkung. Die radiale Auslenkung beeinflusst die Genauigkeit des Bohrungsdurchmessers. Bei der tangentialen Ablenkung wird der Einsatz von der Mittellinie des Teils weg nach unten gedrückt. Besonders beim Bohren von Löchern mit kleinem Durchmesser verringert der gekrümmte Innendurchmesser des Lochs den Freiwinkel zwischen dem Einsatz und der Bohrung.
Die tangentiale Ablenkung drückt das Werkzeug nach unten und weg von der Mittellinie der zu bearbeitenden Komponente, wodurch der Freiwinkel verringert wird. Die radiale Ablenkung verringert die Schnitttiefe, beeinträchtigt die Bearbeitungsgenauigkeit und verändert die Spandicke. Die Änderungen der Schnitttiefe verändern die Schnittkräfte und können zu Vibrationen führen.
Wendeschneidplatten-Geometriemerkmale wie Spanwinkel, Steigungswinkel und Spitzenradius können Vibrationen entweder verstärken oder dämpfen. Wendeschneidplatten mit positivem Spanwinkel erzeugen beispielsweise weniger tangentiale Schnittkraft. Aber die positive Spanwinkelkonfiguration kann das Spiel verringern, was zu Reibung und Vibration führen kann. Ein großer Spanwinkel und ein kleiner Schneidenwinkel erzeugen eine scharfe Schneidkante, die die Schnittkräfte reduziert. Die scharfe Kante kann jedoch Schlagschäden oder ungleichmäßiger Abnutzung ausgesetzt sein, was die Oberflächenbeschaffenheit der Bohrung beeinträchtigt.
Ein kleiner Schneidkanten-Anstellwinkel erzeugt größere axiale Schnittkräfte, während ein großer Anstellwinkel eine Kraft in radialer Richtung erzeugt. Axialkräfte wirken sich nur begrenzt auf Bohrvorgänge aus, daher kann ein kleiner Steigungswinkel wünschenswert sein. Aber ein kleiner Einstellwinkel konzentriert auch die Schnittkräfte auf einen kleineren Abschnitt der Schneidkante als ein großer Einstellwinkel, was sich möglicherweise negativ auf die Standzeit auswirkt. Außerdem beeinflusst der Anstellwinkel eines Werkzeugs die Spandicke und die Richtung des Spanflusses.
Der Wendeschneidplattenradius sollte kleiner als die Schnitttiefe sein, um die radialen Schnittkräfte zu minimieren.
CHIP-KONTROLLE
Das Entfernen der geschnittenen Späne aus der Bohrung ist ein Schlüsselproblem bei Bohrvorgängen. Wendeschneidplattengeometrie, Schnittgeschwindigkeiten und Schnitteigenschaften des Werkstückmaterials beeinflussen alle die Spankontrolle. Beim Aufbohren sind kurze Späne wünschenswert, da sie leichter aus der Bohrung abgeführt werden können und die Kräfte auf die Schneidkante minimieren. Aber die stark konturierten Wendeschneidplattengeometrien, die zum Brechen von Spänen ausgelegt sind, verbrauchen tendenziell mehr Energie und können Vibrationen verursachen.
Operationen, die darauf abzielen, eine gute Oberflächengüte zu erzielen, erfordern möglicherweise eine geringe Schnitttiefe, die dünnere Späne erzeugt, die das Problem der Spankontrolle vergrößern. Eine Erhöhung der Vorschubgeschwindigkeit kann Späne brechen, aber die Schnittkräfte erhöhen und Rattern erzeugen, was sich negativ auf die Oberflächenbeschaffenheit auswirken kann. Höhere Vorschübe können bei der Bearbeitung von kohlenstoffarmen Stählen auch zu Aufbauschneidenbildung führen, daher können höhere Schnittvorschübe zusammen mit einer optimalen inneren Kühlmittelzufuhr eine Lösung zur Spankontrolle beim Aufbohren dieser besser verformbaren Stahllegierungen sein.
SCHLUSSFOLGERUNG
Tieflochbohren und Drehen mit Werkzeugen mit verlängerter Länge sind übliche und wesentliche Metallzerspanungsoperationen. Die effiziente Durchführung dieser Prozesse erfordert eine Bewertung des Bearbeitungssystems als Ganzes, um sicherzustellen, dass die zahlreichen Faktoren, die an der Minimierung von Vibrationen und der Gewährleistung der Produktqualität beteiligt sind, zusammenarbeiten, um maximale Produktivität und Rentabilität zu erreichen.
Zuvor auf der Nachrichtenseite des SECO vorgestellt.
Industrietechnik
- Die Hauptunterschiede zwischen 3-Achsen- und 5-Achsen-Bearbeitung
- Unwucht:Das versteckte Problem, das Maschinenwerkstätten lösen müssen
- Die Herausforderungen des Hartdrehens meistern
- Bearbeitung von Titan:Finden Sie die richtigen Fräswerkzeuge für Superlegierungen
- Oberflächeninspektion in die Hände des Werkzeugmaschinenbedieners legen
- Unterricht in Hochleistungsbearbeitung:Werkzeughalter nicht vergessen
- Die Bedeutung von Kühlmitteln bei der Bearbeitung
- Die Vorteile der 5-Achsen-CNC-Bearbeitung
- Das Herz der Werkzeugmaschine:Werkzeugmaschinenspindeln.
- Bearbeitungsprozess und Werkzeugmaschine verstehen