9 häufige PCB-Lötfehler und Lösungen
Unzureichende Lochfüllung
Wenn es um das Löten von Leiterplatten geht, gehören unzureichende Löcher zu den häufigsten Problemen auf Leiterplatten, die aus vorgebohrten Löchern bestehen, die zum Befestigen von Teilen auf der Leiterplatte verwendet werden. Kurz gesagt, wenn nicht genügend Lot erforderlich ist, um die auf der Platine gebohrten Löcher zu füllen, dann findet eine Unterfüllung in den Gräben statt, was bedeutet, dass das Lot nach dem Abkühlen nicht richtig an der Leiterplatte haftet.
Glücklicherweise können jedoch Fälle von unzureichender Lochfüllung behoben werden. Als PCB-Designer können Sie ein solches Problem am besten beheben, indem Sie sicherstellen, dass Sie Ihre Platine vor dem Löten mehreren Tests unterziehen. Überprüfen Sie die Art des Flussmittels, das Sie verwenden, und vergessen Sie nicht, sicherzustellen, dass eine ausreichende Flussmittelmenge vorhanden ist, um die gesamte Platine zu bedecken. Außerdem ist unbedingt darauf zu achten, dass der Durchmesser der Pins und die Größe der Pads zusammenpassen.
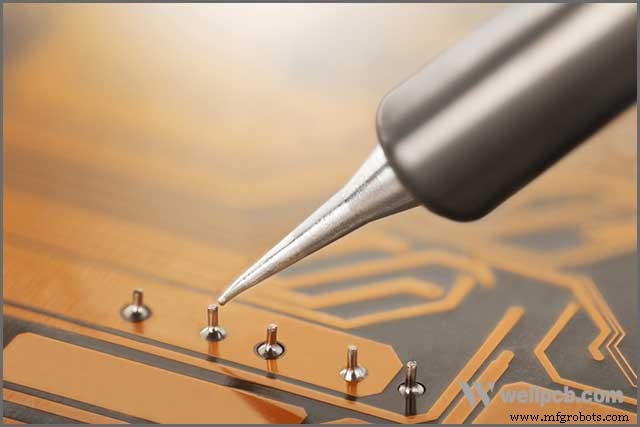
Eine Lücke in der Lötstelle
Beim Löten von Leiterplatten kommt es im Elektronikbau auf die richtige Lage der Lötstellen auf der Platine an. Schwache Lötverbindungen mit Lücken darin führen entweder dazu, dass das Gerät nicht wie gewünscht funktioniert, oder es besteht die Möglichkeit, dass die Lötverbindung zeitweise abfällt. Leider sind Unterschiede in der Lötstelle typische Wellenlötfehler, mit denen viele Löttechniker für Leiterplatten konfrontiert sind.
1. Es ist jedoch noch nicht alles verloren, denn es gibt einige Hinweise, die Designern bei der Entwicklung von Lötstellen helfen können. Hier sind einige davon:
2. Stellen Sie sicher, dass alle zu lötenden Oberflächen fettfrei und sauber sind
3. Stellen Sie sicher, dass die zu lötenden Komponenten fest sitzen, um Bewegungen während des Lötvorgangs zu vermeiden, da dies zu Lücken in der Lötstelle führen kann
4. Bevor Sie Änderungen zulassen, vergewissern Sie sich, dass das Lot an der Verbindung abkühlt
5. Sobald Sie den Lötkolben sofort loswerden, um trockene Knochen und damit Lücken in den Lötstellen zu vermeiden
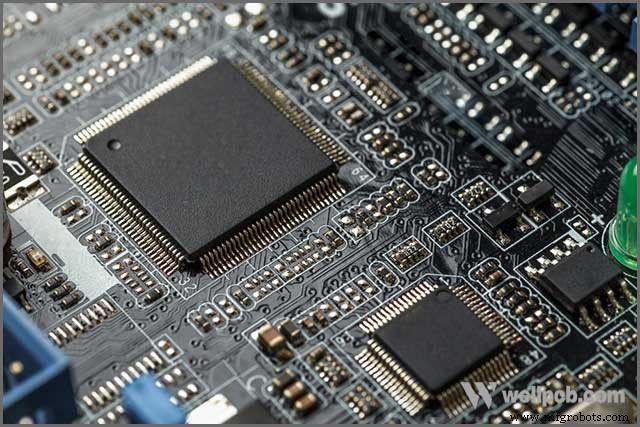
Pad-Abstand
Wenn es eine Möglichkeit gibt, das Bohren von Löchern auf Ihrer Leiterplatte zu vermeiden, sollten Sie dies im Allgemeinen tun. Aber manchmal lässt es sich nicht verhindern, Löcher in Ihr Board zu bohren. Meistens werden Sie Löcher in die Leiterplatte bohren, wenn Sie ein Pitchpad benötigen. Pitchpads haben Materialien, die beim Zusammensetzen schmelzen. Wenn es um das Löten von Leiterplatten geht, wird die Verwendung der besten Pitchpad-Materialien zu einer großen Herausforderung. Einige von ihnen sind nicht gut und der Aufgabe gewachsen.
Um die oben genannten Probleme zu vermeiden, ist es jedoch wichtig, sich einige Zeit zu nehmen, um die Pitch-Pads richtig aufzulegen, bevor Sie mit dem Lötprozess beginnen. Darüber hinaus müssen Sie als Designer, der hervorragende Ergebnisse erzielen möchte, möglicherweise auf Teilungen von nur 0,55 mm zurückgreifen.
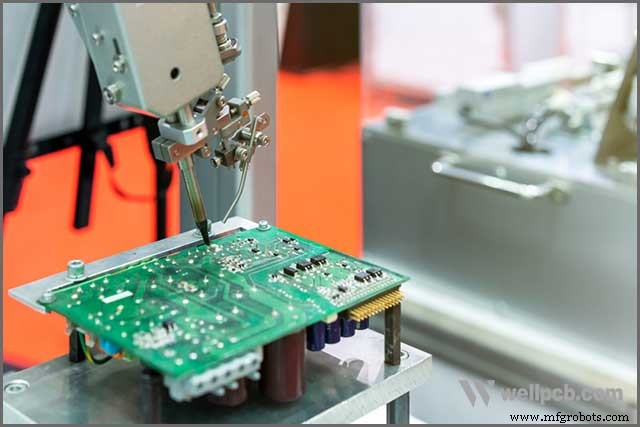
Aufbringen von Lötstopplack
Lötstopplack ist ein fester Bestandteil der Leiterplattentechnologie. Lötstoppmasken oder Lötstopplacke auf der Leiterplatte erfüllen mehrere wesentliche Funktionen, die es wert sind, erwähnt zu werden. Beispielsweise schützt Lötstopplack eine Leiterplatte vor mechanischen Belastungen und Korrosion. Es schützt die Platine auch vor mechanischen Problemen während des Wellenlötprozesses.
Beim Wellenlöten von Leiterplatten ist das Aufbringen von Lötstopplack jedoch eine große Herausforderung, der sich viele Löttechniker für Leiterplatten stellen müssen. Nur die Bereiche, die geschweißt werden müssen, sollten für das Wellenlöten freigelassen werden, um Defekte auf der Platine zu vermeiden. Aber auch hier ist das reduzierte Auftragen von Schweißlack ein häufiger Fehler, mit dem viele PCB-Designer konfrontiert sind.
Verfärbung der Lötstoppmaske
Auch wenn der Fleck auf dem Lötstopplack ein kosmetisches Problem darstellen kann, müssen seine Ursachen von Ihrem Hersteller gründlich untersucht werden. Verfärbte Kostüme lassen sich leicht auf Ihrer Leiterplatte, auf dem Lötstopplack, dem Förderband oder sogar in der Wellenlötanlage erkennen. Häufige Ursachen für verfärbte Lötmasken sind die Verwendung unterschiedlicher Flussmittelkomponenten, das Mischen mehrerer Chargen von Leiterplatten während des Wellenlötens und das Ändern des Lötmaskentyps oder seiner Dicke während des Prozesses.
Auch die Verfärbung der Lötstoppmaske ist ein bekannter Fehler beim Wellenlöten, der vielen Leiterplattenherstellern begegnet. Um sicherzustellen, dass es nicht zu Verfärbungen der Lötstoppmaske kommt, müssen Hersteller den Bereich der von ihnen verwendeten PCB-Löttemperaturen im Auge behalten, die Verwendung unterschiedlicher Flussmittel vermeiden und sich an die gleiche Lötstoppmaskendicke halten.
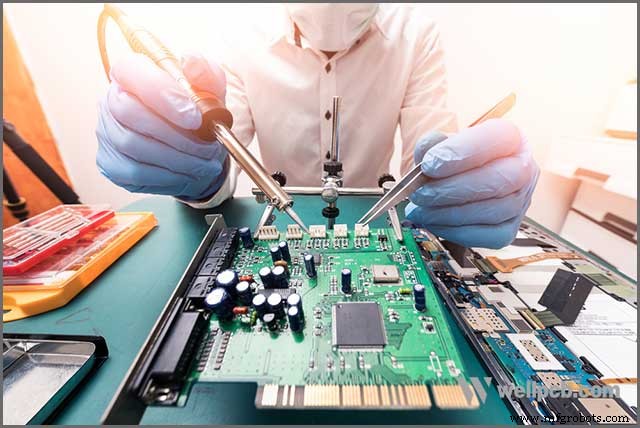
Schlechte Penetration
Flussmittel muss in den plattierten Durchgangslöchern vorhanden sein, damit sich effektiv eine Lötverbindung an der Oberseite der Platine bilden kann. Wenn Sie perfekte Vorwärmbedingungen erreichen, ist die Flussdurchdringung nützlich, was zu einer hochwertigen Leiterplatte führt. Schlechte Durchdringung kann entweder durch unzureichendes Vorwärmen oder reduziertes Auftragen von Flussmittel verursacht werden.
Um Fälle von schlechter Penetration zu vermeiden – insbesondere wenn es sich um Flussmittel handelt – ist es wichtig sicherzustellen, dass Sie die richtige Menge an Flussmittel verwenden, anstatt ein niedriges Flussmittel zu verwenden. Darüber hinaus ist eine ausreichende Vorwärmung erforderlich, um sicherzustellen, dass das Material in die vorgesehenen Bereiche der Platte eindringt.
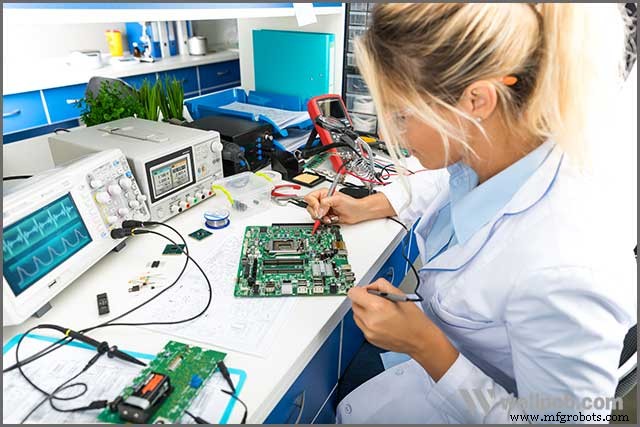
Angehobene Komponenten
Erhabene Bauteile, auch Tombstones genannt, sind die oberirdischen Teile einer Leiterplatte beim Wellenlöten. Einige der häufigsten Ursachen für erhöhte Elemente oder Grabsteine sind:
1. Verwendung von Zutaten mit einigen unterschiedlichen Anforderungen an Temperatur und Löttyp.
2. Falsche Leitungslängen und Versuch, Wellenlöten durchzuführen, insbesondere bei flexiblen Leiterplatten, die sich biegen, während der Rest der Teile flach bleibt.
Um die Biegung der Leiterplatte richtig zu korrigieren, müssen Sie zusätzlich zu den thermischen Kräften die Art der verwendeten Leiterplatte überprüfen. Wenn Sie falsche Leitungslängen adressieren möchten, müssen Sie möglicherweise auf das Lötbad schlagen, um sie durch das Durchgangsloch herauszudrücken. Schließlich ist es wichtig, die thermischen Toleranzen Ihrer Leiterplatten und aller ihrer Teile zu überprüfen. Bauteile mit unterschiedlichen Löttemperaturen können sich beim Wellenlöten abheben. Aber um solche Fälle zu vermeiden, ist es wichtig sicherzustellen, dass die verwendeten Zutaten die gleichen Anforderungen haben.
Lötkugelphänomen
Lötkugeln stellen eine weitere Herausforderung dar, der sich PCB-Designer gegenübersehen, insbesondere beim Wellenlöten. Die Lötkugelbildung tritt auf, wenn sich kleine Lötmittelpartikel wieder anlagern. Besonders nahe an den Anschlussdrähten der Leiterplatte. Einige der zugrunde liegenden Ursachen für Balling beim Schweißen sind die Verwendung eines Hochtemperaturlots. Herunterfallendes Lot, wenn es von der Platine getrennt wird, und flüssige Gase, die auf die Platine zurückspritzen.
Es gibt Mittel, um gewöhnliche Lötballenprobleme zu beheben. Eine der besten Möglichkeiten, um gewöhnliche Probleme mit Lötkugeln zu beheben, liegt jedoch weit zurück beim Design der Leiterplatte. Bei der Auswahl der Lötmaske, die Sie bei der Erstellung Ihrer Leiterplatte verwenden möchten. Versuchen Sie so weit wie möglich, nach einem zu suchen, bei dem die Wahrscheinlichkeit gering ist, dass das Lot daran haften bleibt. Darüber hinaus müssen Sie möglicherweise auch die Luftmenge, die in den Löttank strömt, und das Verhältnis von Stickstoff in der Umgebung Ihres Löttanks überprüfen.
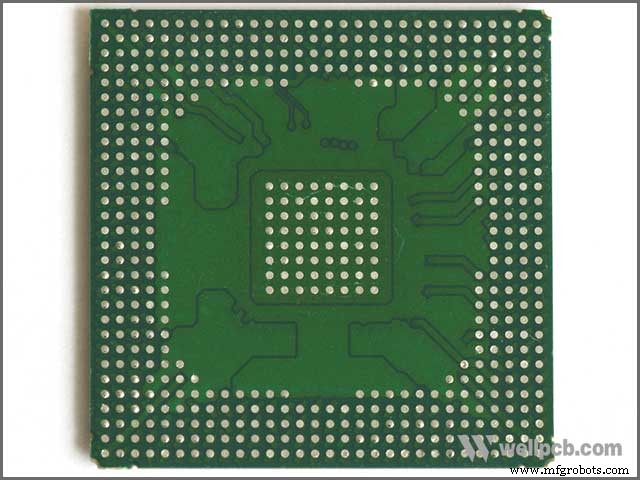
Lötmarkierung erzeugen
Bei der Herstellung von Leiterplatten sind Lötmarken ein Sammelbegriff für die Positionsreferenzierung. Lötstopplacke bestehen aus kleinen gefüllten Kupferkreisen und einem durchsichtigen Bereich von der Lötstoppschicht. Manchmal wird es schwierig, beim Wellenlöten einen Lötfleck zu erzeugen.
Um sicherzustellen, dass die Positionsreferenzierung korrekt durchgeführt wird, ist es wichtig, die richtigen Maschinen oder Geräte zu verwenden, um Lötmasken für die Positionsreferenzierung zu erzeugen.
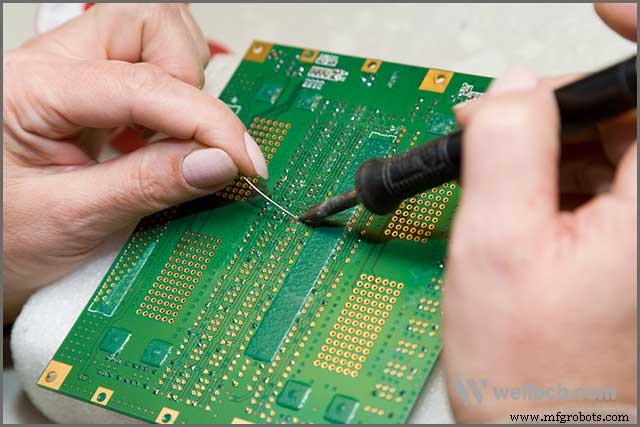
Zusammenfassung
Da haben Sie also zehn aktuelle Wellenlötfehler und ihre Lösungen. Die oben genannten Probleme sind häufige Probleme, die eine hohe Wahrscheinlichkeit haben, ein ansonsten hervorragendes PCB-Design zu ruinieren. Aber auch hier müssen Sie sich darüber im Klaren sein, dass die oben genannten Fälle möglicherweise nicht immer von Ihnen ausgehen.
Manchmal kann Ihr Hersteller schuld sein, wenn Sie nach einem Designer auf dem Markt suchen, der Sie bei Ihrem nächsten Leiterplattenprojekt unterstützt. Dann ist WellPCB Ihre ideale Wahl. Wir bei WellPCB können alle Wellenlötfehler und andere Probleme beheben, die während der Herstellung auftreten können. Zögern Sie nicht, uns so schnell wie möglich zu kontaktieren. Gerne besprechen wir alle Ihre Fragen.
Industrietechnik
- Was ist Löten? - Typen und wie man lötet
- PCB Masling und Delaminierung
- So vermeiden Sie nicht benetzende Defekte
- 3 Häufige Ursachen für den Ausfall von Elektromotoren und ihre Lösungen
- Häufige Bauunfälle und Verletzungen
- Notfallverfahren für führende PCB-Defekte
- Die häufigsten Probleme beim PCB-Design und ihre Analyse
- Auswirkung von schlecht ausgeführten, mit Lötmasken verschlossenen Vias auf Via-Kupfer von PCB und Lösungen
- Rückschläge und Lösungen im HF-PCB-Design
- Hochgeschwindigkeits-PCB-Design-Herausforderungen zur Signalintegrität und ihre Lösungen