Was ist der Unterschied zwischen Bohren, Reiben und Aufbohren in der CNC-Bearbeitung?
Verglichen mit der Außenflächenbearbeitung sind die Bedingungen der CNC-Bearbeitung sind viel schlechter, und es ist schwieriger, Löcher zu bearbeiten als Außenkreise zu bearbeiten. Das liegt daran:
- Die Größe des für die Lochbearbeitung verwendeten Werkzeugs ist durch die Größe des zu bearbeitenden Lochs begrenzt, und die Steifigkeit ist gering, was zu Biegeverformung und Vibrationen neigt;
- Bei der Bearbeitung eines Lochs mit einem Werkzeug mit fester Größe wird die Größe des Lochs oft direkt durch die entsprechende Größe des Werkzeugs bestimmt, und der Herstellungsfehler und der Verschleiß des Werkzeugs wirken sich direkt auf die Bearbeitungsgenauigkeit des Lochs aus;
- Bei der Bearbeitung von Löchern befindet sich der Schnittbereich innerhalb des Werkstücks, die Spanabfuhr und die Wärmeableitung sind schlecht und die Bearbeitungsgenauigkeit und Oberflächenqualität sind nicht einfach zu kontrollieren.

1. Bohren
Bohren ist der erste Prozess zur Bearbeitung von Löchern in festen Materialien, und der Durchmesser der Löcher beträgt im Allgemeinen weniger als 80 mm. Es gibt zwei Arten des Bohrens:Die eine ist die Rotation des Bohrers; der andere ist die Drehung des Werkstücks. Die durch die beiden obigen Bohrverfahren erzeugten Fehler sind unterschiedlich. Wenn beim Bohrverfahren mit rotierendem Bohrer der Bohrer aufgrund der Asymmetrie der Schneidkante und der unzureichenden Steifigkeit des Bohrers abweicht, wird die Mittellinie des bearbeiteten Lochs schief oder verzerrt. Es ist nicht gerade, aber der Lochdurchmesser ist unverändert; Im Gegensatz dazu bewirkt die Abweichung des Bohrers bei der Bohrmethode, bei der das Werkstück gedreht wird, dass sich der Lochdurchmesser ändert, während die Mittellinie des Lochs immer noch gerade ist.
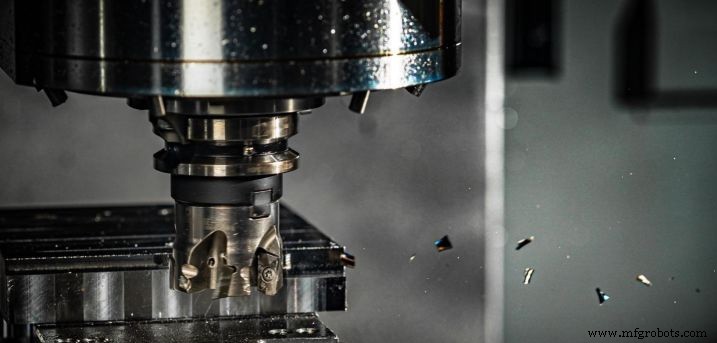
Zu den häufig verwendeten Bohrwerkzeugen gehören Spiralbohrer, Zentrierbohrer, Tieflochbohrer usw., unter denen der am häufigsten verwendete Spiralbohrer ist, und seine Durchmesserspezifikation ist wie im Bild gezeigt.
Aufgrund struktureller Einschränkungen sind sowohl die Biegesteifigkeit als auch die Torsionssteifigkeit des Bohrers gering, verbunden mit einer schlechten Zentrierung, die Bohrgenauigkeit ist gering und erreicht im Allgemeinen nur IT13 ~ IT11; Die Oberflächenrauheit ist ebenfalls groß und Ra beträgt im Allgemeinen 50 ~ 12,5 μm, aber die Metallentfernungsrate beim Bohren ist groß und die Schneideffizienz ist hoch. Bohren wird hauptsächlich verwendet, um Löcher mit geringen Qualitätsanforderungen zu bearbeiten, wie z. B. Schraubenlöcher, Gewindebohrungen, Ölbohrungen usw. Bei Bohrungen mit hohen Anforderungen an die Bearbeitungsgenauigkeit und Oberflächengüte sollten diese durch Reiben, Reiben, Bohren oder Schleifen in der anschließenden Bearbeitung erreicht werden.
2. Reiben
Reiben ist eine der Endbearbeitungsmethoden von Löchern, die in der Produktion weit verbreitet ist. Für kleinere Löcher ist Reiben eine wirtschaftlichere und praktischere Methode als Innenschleifen und Feinbohren.
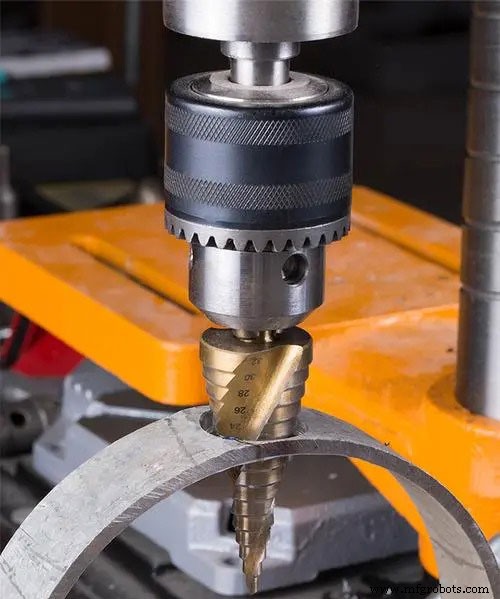
Reibahle
Reibahlen werden im Allgemeinen in zwei Typen unterteilt:Handreibahlen und Maschinenreibahlen. Der Griff der Handreibahle ist gerade, das Arbeitsteil länger und die Führungsfunktion besser. Die Handreibahle hat zwei integrale Strukturen und einen einstellbaren Außendurchmesser. Es gibt zwei Arten von Maschinen-Reibahlen, Schaft-Typ und Hülsen-Typ. Reibahlen können nicht nur runde Bohrungen bearbeiten, sondern auch konische Bohrungen können mit Kegelreibahlen bearbeitet werden.
Reaming-Technologie und ihre Anwendung
Das Reibaufmaß hat großen Einfluss auf die Qualität des Reibens. Wenn die Zugabe zu groß ist, die Belastung der Reibahle groß ist, die Schneidkante schnell stumpf wird, es nicht einfach ist, eine glatt bearbeitete Oberfläche zu erhalten, und die Maßtoleranz nicht einfach zu garantieren ist; Wenn das Aufmaß zu klein ist, Wenn die Werkzeugspuren des vorherigen Prozesses nicht entfernt werden können, verbessert dies natürlich nicht die Qualität der Lochbearbeitung. Im Allgemeinen beträgt die Toleranz für grobe Scharniere 0,35 bis 0,15 mm und für die feinen Scharniere 01,5 bis 0,05 mm.
Um die Bildung von Aufbauschneiden zu vermeiden, wird üblicherweise mit niedrigeren Schnittgeschwindigkeiten (v <8m/min bei Schnellarbeitsstahl-Reibahlen für Stahl und Guss) gerieben. Der Wert des Vorschubs hängt von der zu bearbeitenden Blende ab. Je größer die Blende, desto größer der Wert des Feeds. Wenn die Schnellarbeitsstahl-Reibahle Stahl und Gusseisen verarbeitet, beträgt der Vorschub normalerweise 0,3 bis 1 mm/U.
Beim Reiben von Löchern müssen diese gekühlt, geschmiert und mit geeigneter Schneidflüssigkeit gereinigt werden, um Aufbauschneidenbildung zu vermeiden und Späne rechtzeitig zu entfernen. Im Vergleich zum Schleifen und Bohren hat das Reiben eine hohe Produktivität und es ist einfach, die Genauigkeit des Lochs sicherzustellen; Reiben kann jedoch den Positionsfehler der Lochachse nicht korrigieren, und die Positionsgenauigkeit des Lochs sollte durch den vorherigen Prozess garantiert werden. Stufen- und Sacklöcher sind zum Reiben nicht geeignet.
Die Maßgenauigkeit des Reiblochs beträgt im Allgemeinen IT9 bis IT7 und die Oberflächenrauheit Ra beträgt im Allgemeinen 3,2 bis 0,8. Für mittelgroße Bohrungen mit hohen Präzisionsanforderungen (z. B. IT7-Präzisionsbohrungen) ist das Bohren-Aufweiten-Reiben-Verfahren ein typisches Bearbeitungsschema, das häufig in der Produktion verwendet wird.
3. Langweilig
Bohren ist ein Bearbeitungsverfahren, bei dem ein Schneidwerkzeug verwendet wird, um ein vorgefertigtes Loch zu vergrößern. Die Bohrarbeiten können auf einem Bohrwerk oder einer Drehbank durchgeführt werden.
Langweilige Methode
Es gibt 3 verschiedene Bearbeitungsmethoden zum Bohren.
(1) Das Werkstück dreht sich und das Werkzeug wird vorgeschoben. Der größte Teil des Bohrens auf der Drehmaschine gehört zu dieser Bohrmethode. Die Prozesseigenschaften sind:Die Achslinie des Lochs nach der Bearbeitung stimmt mit der Rotationsachse des Werkstücks überein, die Rundheit des Lochs hängt hauptsächlich von der Rotationsgenauigkeit der Werkzeugmaschinenspindel ab und der axiale Geometriefehler des Lochs hängt hauptsächlich ab von der Vorschubrichtung des Werkzeugs relativ zur Rotationsachse des Werkstücks. Positionsgenauigkeit. Dieses Bohrverfahren eignet sich für die Bearbeitung von Löchern, die Koaxialitätsanforderungen mit der Außenfläche haben.
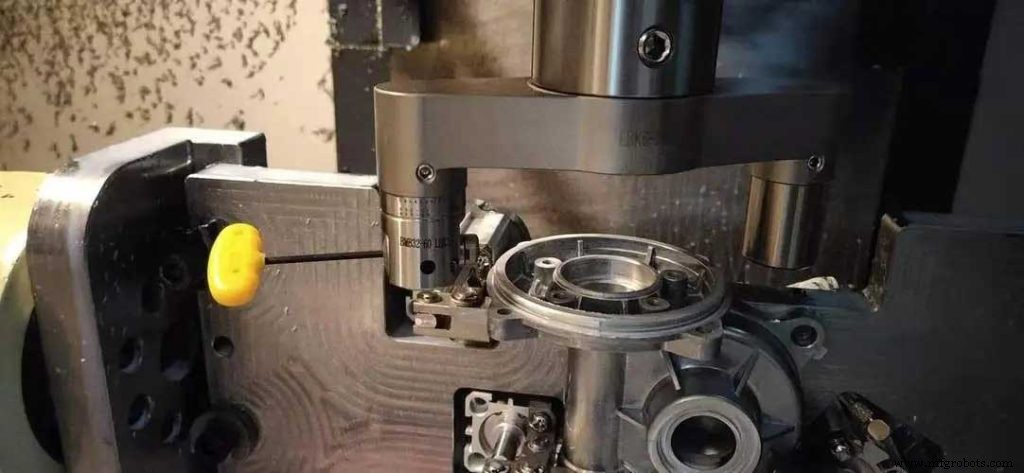
(2) Das Werkzeug dreht sich und das Werkstück führt eine Vorschubbewegung aus. Die Spindel der Bohrmaschine treibt das Bohrwerkzeug an, um sich zu drehen, und der Arbeitstisch treibt das Werkstück an, um eine Vorschubbewegung auszuführen.
(3) Wenn sich das Werkzeug dreht und eine Vorschubbewegung ausführt, wird diese Art von Bohrverfahren zum Bohren verwendet. Die Überhanglänge der Bohrstange wird geändert, und die Kraft und Verformung der Bohrstange werden ebenfalls geändert. Der Lochdurchmesser ist klein und bildet ein sich verjüngendes Loch. Außerdem nimmt die Überhanglänge der Bohrstange zu, und die Biegeverformung der Hauptwelle aufgrund ihres Gewichts nimmt ebenfalls zu, und die Achse des maschinell bearbeiteten Lochs wird entsprechend gebogen. Diese Bohrmethode ist nur für kurze Löcher geeignet.
Diamantbohren
Im Vergleich zum gewöhnlichen Bohren zeichnet sich das Diamantbohren durch einen geringen Rückschnitt, einen kleinen Vorschub und eine hohe Schnittgeschwindigkeit aus. Es kann eine hohe Bearbeitungsgenauigkeit (IT7~IT6) und eine sehr glatte Oberfläche (Ra beträgt 0,4~0,05) erzielt werden. Das Diamantbohren wurde ursprünglich mit Diamantbohrwerkzeugen bearbeitet und wird heute im Allgemeinen mit Hartmetall-, CBN- und synthetischen Diamantwerkzeugen bearbeitet. Hauptsächlich für die Bearbeitung von Werkstücken aus Nichteisenmetallen, aber auch für die Bearbeitung von Gusseisen und Stahl.
Die üblicherweise verwendeten Schneidwerte für das Diamantbohren sind:Der Rückschnittbetrag beim Vorbohren beträgt 0,2 bis 0,6 mm und das Endbohren 0,1 mm; die Vorschubgeschwindigkeit beträgt 0,01 bis 0,14 mm/r; Die Schnittgeschwindigkeit beträgt 100 ~ 250 m / min bei der Bearbeitung von Gusseisen. 150~300m/min für Stahl, 300~2000m/min für die Bearbeitung von NE-Metallen.
Damit beim Diamantbohren eine hohe Bearbeitungsgenauigkeit und Oberflächenqualität erreicht werden kann, muss die verwendete Werkzeugmaschine (Diamantbohrmaschine) eine hohe geometrische Genauigkeit und Steifigkeit aufweisen. Die Hauptwelle der Werkzeugmaschine wird normalerweise von Präzisions-Schrägkugellagern oder hydrostatischen Gleitlagern und schnell rotierenden Teilen getragen. Es muss genau ausbalanciert sein; Darüber hinaus muss die Bewegung des Zuführmechanismus sehr stabil sein, um sicherzustellen, dass der Arbeitstisch eine stabile und langsame Zuführbewegung ausführen kann.
Diamantbohren hat eine gute Verarbeitungsqualität und eine hohe Produktionseffizienz und wird häufig bei der Endbearbeitung von Präzisionsbohrungen in der Massenproduktion verwendet, z. B. Motorzylinderbohrungen, Kolbenbolzenbohrungen und Spindelbohrungen an Spindelkästen von Werkzeugmaschinen. Es sollte jedoch beachtet werden, dass bei der Bearbeitung von Eisenmetallprodukten mit Diamantbohren nur Bohrwerkzeuge aus Hartmetall und CBN verwendet werden können und Bohrwerkzeuge aus Diamant nicht verwendet werden können, da die Kohlenstoffatome im Diamant eine große Affinität haben mit Eisengruppenelementen. , die Standzeit ist gering.
Bohrwerkzeug
Bohrwerkzeuge können in einschneidige Bohrwerkzeuge und zweischneidige Bohrwerkzeuge unterteilt werden.
Technologische Eigenschaften und Anwendungsbereich des Aufbohrens
Im Vergleich zum Bohr-Aufweit-Reib-Prozess ist der Durchmesser des Lochs nicht durch die Größe des Werkzeugs begrenzt, und das Bohren hat eine starke Fehlerkorrekturfähigkeit. Die Bohr- und Positionierflächen sorgen für eine hohe Positionsgenauigkeit.
Verglichen mit dem Außenkreis des Bohrlochs sind aufgrund der geringen Steifigkeit und großen Verformung des Werkzeughaltersystems die Wärmeableitungs- und Spanabfuhrbedingungen nicht gut, und die thermische Verformung des Werkstücks und des Werkzeugs ist relativ groß. Die Bearbeitungsqualität und Produktionseffizienz des Bohrlochs sind nicht so hoch wie die des äußeren Kreises.
Basierend auf der obigen Analyse ist ersichtlich, dass das Bohren einen breiten Verarbeitungsbereich hat und Löcher verschiedener Größen und unterschiedlicher Genauigkeitsniveaus bearbeiten kann. Bei Bohrungen und Lochsystemen mit großen Durchmessern und hohen Anforderungen an Maß- und Lagegenauigkeit ist das Aufbohren fast die einzige Bearbeitung. Methode. Die Bearbeitungsgenauigkeit beim Bohren beträgt IT9~IT7 und die Oberflächenrauheit Ra. Das Aufbohren kann auf Werkzeugmaschinen wie Bohrwerken, Drehbänken und Fräsmaschinen durchgeführt werden. Es hat den Vorteil der Flexibilität und ist in der Produktion weit verbreitet. In der Massenproduktion werden zur Verbesserung der Bohreffizienz häufig Bohrmatrizen verwendet.
Industrietechnik
- Was ist der Unterschied zwischen Cloud und Virtualisierung?
- Was ist der Unterschied zwischen Sensor und Wandler?
- Was ist der Unterschied zwischen FRP und Fiberglas?
- Was ist der Unterschied zwischen Schrauben und Bolzen?
- Was ist der Unterschied zwischen einem TS und einem HSS?
- Python vs. PHP:Was ist der Unterschied zwischen Python und PHP?
- Python 2 vs. Python 3:Was ist der Unterschied zwischen Python 2.x und Python 3.x?
- Was ist der Unterschied zwischen Schalung und Schalung?
- Was ist der Unterschied zwischen elektronisch und elektrisch?
- Unterschied zwischen Bohren, Bohren und Reiben