Rotationstransfer bietet Drehen mit vollem Außendurchmesser zwischen den Zentren
Winemas RV10 Flexmaster erreicht kurze Zykluszeiten durch der dynamische Direktantrieb des Rundschalttisches; Die Schaltzeit des Tisches liegt unter 0,3 Sekunden. Bildnachweis:Winema
Hochproduktive Werkstätten werden oft von Rundtaktmaschinen angezogen, weil sie in der Lage sind, Präzisionsteile schnell herzustellen. Aber stellen Sie sich vor, Sie fügen der Transfermaschine eine Drehoperation hinzu, die als getrennte Zelle läuft, die frei von den Antriebs- und Bearbeitungsfaktoren ist, die sich auf die anderen Stationen auswirken. Diese zusätzliche isolierte Drehzelle soll eine hochpräzise Konzentrizität bieten, indem sie das Drehen über die gesamte Länge des Teils ermöglicht, im Vergleich zum Wenden eines Teils und dem Durchführen einer Rückseitendrehung oder dem Bewegen des Teils in eine andere Spannposition, um es fertigzustellen.
Mit der Rundtaktmaschine RV10 Flexmaster von Winema können Anwender die gesamte Außenkontur eines Werkstücks ohne Positionierungsfehler mit einer Genauigkeit im Mikrometerbereich bearbeiten. Die Präzisionsdrehzelle (PTC) ermöglicht es laut Tobias Rapp, Vertriebsleiter bei Winema, ein Teil zwischen Spitzen oder durch Spannzangen zu spannen, während das Außendrehen auf der Maschine sowie das Bohren abgeschlossen werden.
Laut Rapp bietet diese kompakte, steife und stabile Maschine schnelle Zykluszeiten und Umrüstzeiten für Kleinteile (2 bis 12 mm Durchmesser) aus verschiedenen Metallen in Form von Stangen, Coils und Platinen. Es eignet sich besonders für hochvolumige Anwendungen in der Automobil-, Luft- und Raumfahrt- und Elektroindustrie, aber auch für Teilefamilien oder Kleinserien aufgrund seiner schnellen Umrüstzeiten und hohen Flexibilität. Er fügt hinzu, dass die Teileproduktion für Elektrofahrzeuge (EV) eine beliebte Anwendung für den RV10 in Europa ist, wo die Regierung die EV-Produktion vorantreibt.
Kleine Teile, kleiner Platzbedarf
Winema mit Sitz in Großselfingen, Deutschland, begann 2013 mit der Entwicklung des RV10 Flexmaster. Zum Zeitpunkt seiner Entwicklung war auf dem Markt für Präzisionsdrehteile in den USA eine mechanische Rundtaktmaschine in Zapfenbauweise erhältlich, die für Benutzer mit nur einem Teil konzipiert war zu bearbeiten und konnten nicht einfach umgerüstet werden, sagt das Unternehmen. Allerdings veränderte sich der Markt. Es zeigte sich, dass eine vollständige CNC-Transfermaschine gefragt war. Es war der Meinung, dass Maschinenwerkstätten eine Großserienfertigung für mehr Lose kleiner Teile sowie eine Maschine mit schneller Umrüstung als eine mechanische Maschine benötigten
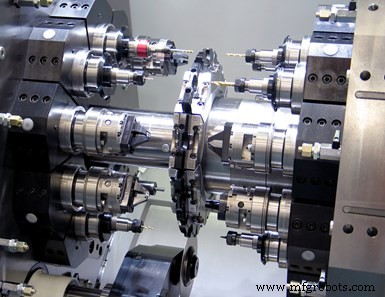
Der RV10 Flexmaster bietet die Möglichkeit zur Durchführung Fräs- und Bohroperationen mit bis zu vier Radialstationen (Gewindefräsen und Konturfräsen). Dank Flansch-Winkelkopfoperationen (z. B. Breitenfräsen) können Operationen wie Mehrkantfräsen, Schlitzen, Teilfrontbohren, Kreiskonturfräsen usw. durchgeführt werden.
konnte nicht liefern. Daher sagt Winema, dass es diese Lücke mit einer kleinen, kompakten und stabilen Voll-CNC-Transfermaschine gefüllt hat, die für Präzision, Flexibilität und schnelle Umrüstzeiten (normalerweise 30 bis 60 Minuten, aber je nach Teil zwischen 15 und 120 Minuten) ausgelegt ist Anforderungen).
Diese Zapfen-Transfermaschine mit 10 Spannstationen wurde speziell für die Bearbeitung von Teilen mit einem Durchmesser von 12 mm und einer Länge von 80 mm und kleiner entwickelt. Der RV10, der kleinste Flexmaster, hat ebenfalls eine kleine Stellfläche von 2,4 m × 1,2 m und ist 2,1 m hoch. Die Maschine wiegt 20.000 lbs, was laut Rapp eine notwendige Steifigkeit für die Bearbeitung kleiner, komplexer Teile ist.
Eher Drehen als Transfer
In einer herkömmlichen Rundtaktmaschine ist es normalerweise unmöglich, einen vollständigen Außendrehprozess durchzuführen, da das Spannfutter, das das Werkstück hält, einen Teil der Außenseite des zu bearbeitenden Teils behindert. Die Präzisionsdrehzelle des RV10 kann das Werkstück jedoch mit einem unabhängigen Koordinatensystem in den PTC übergeben, wo es isoliert einen Drehprozess ausführen kann. Beim Drehen zwischen Spitzen bleibt die genaue Rundlaufgenauigkeit über die gesamte Länge des Werkstücks konstant, die laut Rapp für diese Maschine 20 Mikrometer beträgt. Diese hohe Rundlaufgenauigkeit findet man normalerweise bei Drehmaschinen und Mehrspindelmaschinen, nicht aber bei Rundtaktmaschinen.
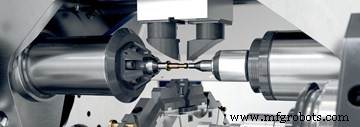
Die Präzisionsdrehzelle (PTC) des RV10 kann das Übertragen Sie das Werkstück mit einem unabhängigen Koordinatensystem in den PTC, wo es isoliert einen Drehvorgang ausführen kann.
Obwohl Mehrspindler eine so hohe Rundlaufgenauigkeit erzeugen können, erklärt Rapp, dass der RV10 eine bessere Option sein kann. „Mehrspindler können nur von einer Seite bearbeiten, dann lösen sie das Werkstück, um es umzudrehen, um es wieder in die Spindel in der Spannbacke einzulegen“, sagt er. „Dabei verlierst du Zykluszeit, und die Zeiten für weitere Operationen summieren sich.“
Der PTC der Maschine verfügt über zwei Drehwerkzeuge mit Capto-Schnittstellen. Optional können in jede Maschine drei PTCs integriert werden.
Weitere Vorteile
Die RV10 Flexmaster mit Hochdruck-Kühlschmierstoffzufuhr bietet viele Vorteile für die Bearbeitung kleiner, komplexer Teile, insbesondere für das bereits erwähnte Drehen mit hohen Stückzahlen. Ein weiterer Vorteil ist jedoch die Vielzahl von Metallen, die mit dieser Technologie bearbeitet werden können. Laut Rapp wurde es auf einer Reihe von Metallen (einschließlich Stählen, Kupfer, Messing und Titan) getestet und dabei für jedes eine lange Standzeit erreicht, was für Rundtaktmaschinen entscheidend ist.
Während herkömmliche Rundtaktmaschinen nur ein Teil bearbeiten, kann die RV10 mit ihrer Doppelzufuhrfunktion zwei Teile gleichzeitig bearbeiten. Zwei Coils, Stäbe oder Platinen können gleichzeitig zugeführt werden. Wenn dies der Fall ist, wird also die Hälfte der Bearbeitungsstationen/Spindeln einem Teil gewidmet und die andere Hälfte der Stationen/Spindeln dem zweiten Teil. Um die Zykluszeit zu verkürzen, verarbeiten die meisten Benutzer laut Rapp nur jeweils ein Teil.
Während der Bearbeitung eines Teils kann die Maschine 4 bis 50 Teile pro Minute ausgeben. Bei gleichzeitiger Verarbeitung von zwei Teilen werden jedoch 10 bis 80 Teile pro Minute ausgegeben.
Winema | winema.de
Industrielle Ausrüstung
- CNC-Drehen einfacher machen
- Mehrachsen-Drehzentrum bietet erhöhte Flexibilität
- Schrägbett-Drehzentren
- Vertikaldrehzentrum mit beweglicher, umgekehrter Spindel
- Vertikale Drehzentren geeignet für kleine und große Teileserien
- Drehzentrum verfügt über Revolver mit vier Positionen
- Drehen ist optional
- CNC-Drehzentren
- Wälzfräsen auf einem Drehzentrum
- Vertikale Dreh- und Schleifzentren