Überwindung von Fallstricken bei der Messung dünner, paralleler Optiken
Aufgrund der Nachfrage nach immer kleineren Verbraucherprodukten und Halbleiterbauelementen benötigen Hersteller dünne planare Optiken für eine Reihe von Anwendungen. Dies legt die Verantwortung auf die Material- und Optikhersteller, um sicherzustellen, dass das Glas flach und frei von Materialverformungen ist, die zu Verzerrungen führen und die Funktionalität des Endverbrauchers beeinträchtigen können. Dies bedeutet eine enorme Belastung für Messwerkzeuge, die die Gleichmäßigkeit dünner planarer Optiken messen und bestätigen müssen, um so zu beweisen, dass sie für den Zweck geeignet sind.
Die Messung dünner paralleler optischer Oberflächen kann naturgemäß äußerst anstrengend sein. Solche Optiken zeichnen sich dadurch aus, dass sie weniger als wenige Millimeter dick sind und dadurch Vorder- und Rückseite sehr dicht beieinander liegen. Aus diesem Grund ist es mit der standardmäßigen mechanischen Phasenverschiebungsinterferometrie (PSI) schwierig, zwischen den Oberflächen zu unterscheiden.
Eine fortschrittlichere Lösung ist die Fourier-Transformations-Phasenverschiebungsinterferometrie (FTPSI), die eine einfache Charakterisierung der Vorder- und Rückseite, der Variation der optischen Dicke und der Materialhomogenität von dünnem, planparallelem Glas ermöglicht. FTPSI ermöglicht es, Vorder- und Rückseite zu unterscheiden und die Qualität beider in einer einzigen Messung zu charakterisieren, selbst wenn sie weniger als einen Millimeter dick sind.
Warum FTPSI?
Um zu verstehen, warum FTPSI die bevorzugte Technik zum Messen dünner paralleler Optiken ist, müssen wir uns die alternativen herkömmlichen Messtechniken genauer ansehen und sehen, wo sie zu kurz kommen.
Wenn wir PSI betrachten, das funktioniert, indem ein Lichtstrahl durch eine ideale Referenzoptik (als Transmission Flat [TF] bezeichnet) zu dem zu testenden Teil geleitet wird, sehen wir, dass diese Technik nicht zwischen der Vorder- und der Rückseite einer dünnen parallelen Optik unterscheiden kann . Bei richtiger Ausrichtung erzeugen der TF und das zu testende Teil ein Interferenzmuster, das als Interferogramm aufgezeichnet wird. Die Messsoftware analysiert die durch die Phasenverschiebungen erzeugten Höhenvariationen und rekonstruiert die Oberflächenwellenfront, die den Höhenunterschied zwischen dem TF und dem Testteil darstellt.
Wenn die Vorderfläche eines dünnen, parallelen Teils ausgerichtet ist, wird typischerweise eine zweite Reflexion von der Rückfläche zum Interferometer zurückgeführt. Dies führt zu einem komplexen Streifenmuster, das durch mehrere überlappende Interferogramme erzeugt wird und mit PSI nicht genau analysiert werden kann. (Abbildung 1)

Es gibt Maßnahmen, die ergriffen werden können, um die Situation zu verbessern, aber sie sind zeitaufwändig und fügen dem Gesamtprozess unnötige und potenziell schädliche Schritte hinzu. Dazu gehören das Auftragen von schwarzer Farbe auf die Rückseite, um die Reflexion auszulöschen, das Färben mit einem dunklen Marker oder das Auftragen von Vaseline auf der Oberfläche.
Das FTPSI-Verfahren verneint die Notwendigkeit, die Rückseite der dünnen Optik manuell zu manipulieren, um aussagekräftige und genaue Messungen vorzunehmen. Stattdessen nutzt FTPSI die Reflexion von der Rückseite, um in einer einzigen Messung mehr Informationen über die dünne optische Komponente zu erhalten. Dies ist möglich, da FTPSI keine mechanische Bewegung innerhalb des Testhohlraums erfordert, um die Interferogramme zu erstellen. Stattdessen verlässt sich FTPSI auf die Modulation der Wellenlänge der Laserquelle, um die Messung zu ermöglichen. Jede Kavität im Strahlengang einer FTPSI-Erfassung erzeugt eine eindeutige Interferenzfrequenz, die ihre Kavitätslänge definiert, und dies ermöglicht eine klare Abgrenzung und genaue Charakterisierung der Oberfläche. Algorithmen können dann beide Oberflächen analysieren und ihre Form unabhängig voneinander charakterisieren. (Abbildung 2)

Multi-Surface-FTPSI
Beginnen wir mit den Grundlagen. Ein TF – wie oben erwähnt – wird mit einem Interferometer verwendet, um eine planare Referenz für eine Oberflächen- oder übertragene Wellenfrontmessung herzustellen. Eine Referenzebene (RF) ist eine hochwertige optische Oberfläche, die verwendet wird, um einen Messstrahl mit minimaler Auswirkung auf die gesamte Wellenfront zu lenken.
Die einfachste FTPSI-Messung ist eine Konfiguration mit drei Oberflächen, die aus dem TF – Oberfläche 1 – und dem Testteil – Oberflächen 2 und 3 – besteht (siehe Abbildung 3). In dieser Konfiguration wird ein Ergebnis der Rückseite bereitgestellt, aber es enthält Materialungleichmäßigkeiten aufgrund des Durchgangs des Messstrahls durch das Material des Testteils.
Für Messungen der Rückseite mit höherer Genauigkeit kann eine Konfiguration mit vier Oberflächen verwendet werden, indem eine HF – Oberfläche 4 – hinter der Testoptik platziert wird. In dieser Konfiguration ist die Form der Oberfläche 3 mit der bekannten RF verglichen. Diese Konfiguration erzeugt eine zweite Testkavität zwischen der Rückseite und dem RF und bietet eine direkte Messung der Rückseite ohne die Unsicherheit des Materials im Teil.
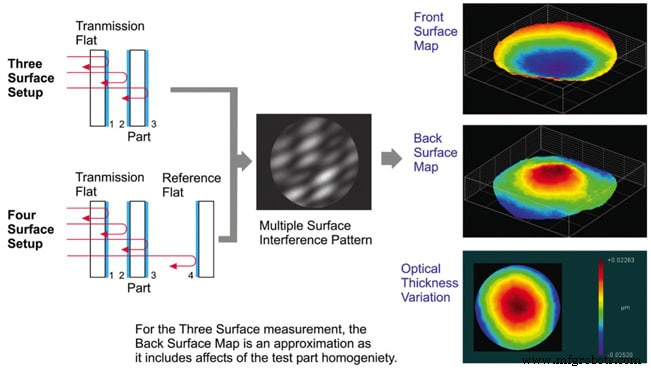
Eine einzelne FTPSI-Messung mit sowohl der drei- als auch der vierflächigen Kavitätskonfiguration umfasst ein Dickenabweichungsergebnis, das eine vollflächige Abbildung der Materialdicke über das Testteil hinweg darstellt.
Materialhomogenität
Die oben beschriebene vierflächige Hohlraumkonfiguration ermöglicht die Charakterisierung der Materialhomogenität des Testteils, ein einzigartiges Merkmal der FTPSI-Technologie. Die Homogenitätsinformationen können erhalten werden, indem zuerst die Kavität mit dem Testteil im Inneren gemessen wird, dann das Teil aus der Kavität entfernt und eine „leere Kavität“-Messung durchgeführt wird, die einen Vergleich zwischen TF und RF ermöglicht.
Im Gegensatz zu anderen Homogenitätsmesstechniken, die nur die nichtlineare Komponente liefern, behält ein FTPSI-Ergebnis einen festen Hohlraum bei und kann daher sowohl die nichtlinearen als auch die linearen Komponenten der Materialhomogenität liefern. Der lineare Anteil ist entscheidend für Anwendungen, die empfindlich auf Strahlausrichtung reagieren, da das Ergebnis verwendet werden kann, um vorherzusagen, wie ein Strahl abweicht, wenn er durch das Testteil geht.
Genauigkeit
Wie bei allen interferometrischen Testmethoden basiert die Messunsicherheit auf einer Reihe von Faktoren, einschließlich der Qualität der Referenzoptik, der Stabilität der Messumgebung und der Montagetechniken.
Bei Teilen mit einem Durchmesser von weniger als 150 mm (6 Zoll) kann die Spitzen-zu-Tal-Oberflächenform der Referenzoptik in der Größenordnung von 2,5 % der Wellenlänge des für die Messung verwendeten Lichts liegen – λ/40. Besitzt das System beispielsweise einen Laser, der rotes Licht bei einer Wellenlänge von 633 nm emittiert, entspricht dies etwa 16 nm. Dadurch liegt das Messergebnis in den meisten Fällen gut innerhalb der Toleranzbandbreite für Dünnglasanwendungen.

Wie das Teil in der Testkavität gehalten wird, ist wahrscheinlich der kritischste Faktor bei der Messung dünner Optiken, genauer gesagt die Montagetechnik und die Montageausrichtung. Das einfache Festklemmen einer dünnen Optik kann unerwünschte Spannungen hervorrufen und dazu führen, dass sich die Optik verbiegt. Unterschiede in der Ausrichtung können insbesondere bei dünnen Teilen aufgrund von Schwerkrafteffekten zu sehr unterschiedlichen Messergebnissen führen. Idealerweise sollte das Teil in der gleichen Konfiguration montiert werden, in der es in seiner Endanwendung verwendet wird, um unerwartete Unterschiede zwischen der beabsichtigten Absicht und der tatsächlichen Leistung zu vermeiden. (Abbildung 4.)
Zusammenfassung
FTPSI ist eine überzeugende Wahl für Optikhersteller, die die Qualität dünner paralleler Optiken sicherstellen müssen. Im Gegensatz zu herkömmlichen mechanischen PSI kann FTPSI die Vorder- und Rückseite unterscheiden und ihre entsprechenden Oberflächeninformationen in einer einzigen, wiederholbaren Messung charakterisieren. Dank Fortschritten sowohl bei der Ausrüstung als auch bei den Algorithmen kann FTPSI die Oberflächenform, Dickenabweichung und Materialhomogenität von Optiken mit einer Dicke von weniger als 1 mm charakterisieren. Angesichts der wachsenden Nachfrage nach dünnen, parallelen Optiken und den Herausforderungen, die mit der genauen Messung dieser Optiken verbunden sind, überwindet FTPSI die Einschränkungen früherer Methoden. Seine Stärke bei der Charakterisierung zusammen mit seiner Benutzerfreundlichkeit machen es zu einer guten Wahl für die optische Messtechnik.
Dieser Artikel wurde von Dan Musinski, Vice President of Strategic Business Development, Zygo Corporation (Middlefield, CT) verfasst. Weitere Informationen finden Sie hier .
Sensor
- Wann ist eine Reparatur keine Reparatur?
- Messen der Oberflächenbeschaffenheit an präzisionsgefertigten CNC-Swiss-Drehteilen
- Bewältigung allgemeiner Herausforderungen beim Schneiden und Schleifen von Aluminium
- Methode misst Temperatur in 3D-Objekten
- Messung aggressiver Startlasten auf Raumfahrzeugen
- Fotoinduzierte Emissionsanalyse zur Identifizierung von Oberflächenverunreinigungen
- Niob-Titan-Nitrid-Dünnschichtbeschichtung
- Messung der Schichtdicke mit einem Mikroskop
- 4 wichtige Schritte zur Überwindung von Materialoberflächenfehlern
- Ebenheitstoleranz in GD&T