Werksbesichtigung:Veelo Technologies, Woodlawn, Ohio, USA
Was tun Sie, wenn die Carbon Nanotube (CNT)-Faser, die Ihr Unternehmen zu vermarkten versucht, nicht das bietet Leistung, die von Ihren potenziellen Kunden benötigt wird, zu denen die US Air Force und Boeing (Chicago, Illinois, USA) gehören? Sie schwenken um, gehen zurück zum Reißbrett und nutzen Ihr fortschrittliches Know-how in der Verarbeitung von Materialien und Verbundwerkstoffen, um andere Lösungen zu entwickeln. „Wir verwenden oft Nanomaterialien, aber wir sind keineswegs ein Unternehmen für Nanomaterialien“, sagt Joe Sprengard, CEO von Veelo Technologies. „Wir sind ein Unternehmen für fortschrittliche Materialien, das sich auf elektrisch leitfähige Materialien und nichtmetallische Heizlösungen konzentriert. Der rote Faden zwischen unserem anfänglichen Fokus auf die Entwicklung von CNT-Endlosfasern und -platten und unserem aktuellen Produktportfolio – Blitzschlagschutz (LSP) und elektromagnetische Abschirmung, Heizdecken für die effiziente Verarbeitung von Verbundwerkstoffen und nichtmetallische elektrothermische Enteisungssysteme – ist unsere Fähigkeit neue Materialien zu entwickeln, die nicht nur ein neues Leistungsniveau bieten, sondern auch Gewichts- und Kostenanforderungen erfüllen.“
Das Unternehmen hat von vier auf 24 Mitarbeiter skaliert und ist in eine neue, 20.000 Quadratmeter große Produktionsstätte in Woodlawn, einem Vorort von Cincinnati, 1,6 km vom Hauptsitz von GE Aviation in Evendale und eine Stunde südlich des Air Force Research Laboratory (AFRL) entfernt, umgezogen. auf dem Luftwaffenstützpunkt Wright-Patterson in Dayton, Ohio. Sprengard führt CW 's Tour durch die neue Produktionsstätte von Veelo Technologies, die die Entwicklung des Unternehmens vom Nanomateriallieferanten zum Advanced-Broad-Goods-Spezialisten zum Innovationspartner für zukünftige Verbundwerkstoffe führt.
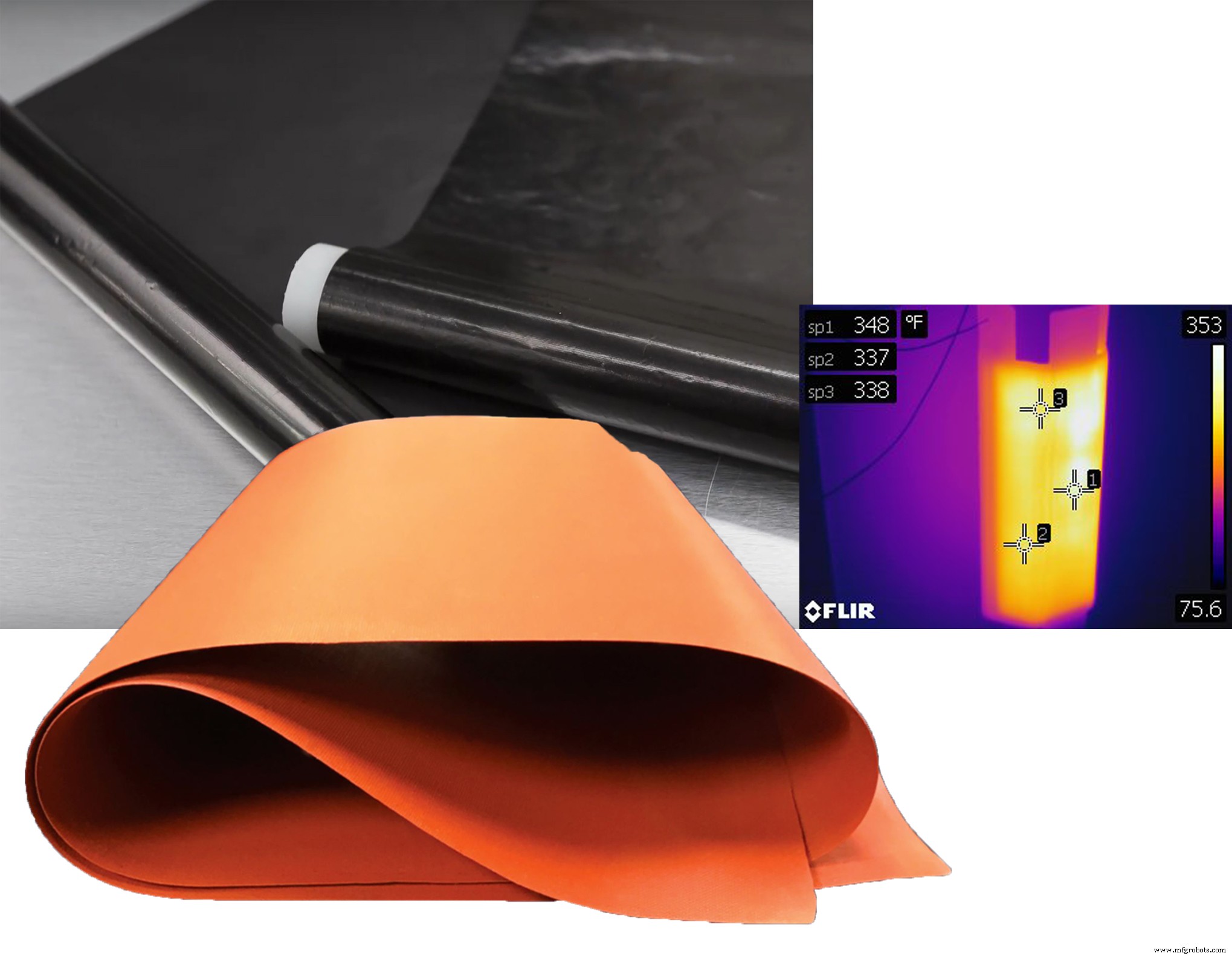
Von Nano- zu multifunktionalen Verbundwerkstoffen und Verarbeitung
Veelo Technologies begann mit der Entwicklung kontinuierlicher CNT-Faserplatten (oben links) hat sich jedoch jetzt weiterentwickelt, um eine Reihe von Materialien in seinen Produkten für den Blitzeinschlagschutz und nichtmetallische Heizdecken für die Verarbeitung von Verbundwerkstoffen und Enteisungssysteme für Flugzeugstrukturen zu verwenden (unten und rechts) .
CNT-Fasern und -Platten
Veelo Technologies wurde ursprünglich als General Nano aus der University of Cincinnati (UC) ausgegliedert. Die Universität hatte 2007 die längsten CNT-Arrays der Welt hergestellt – 18 Millimeter lang Jahre lang versuchten wir herauszufinden, wie wir diese langen CNTs in hochfeste Fasern im Makromaßstab umwandeln können, woran AFRL interessiert war. Aber die Eigenschaften traten nie auf.“
Also wandte sich das Unternehmen um und entwickelte eine Möglichkeit, die CNTs in einen Endlosbogen umzuwandeln. Boeing wurde interessiert und betrachtete die Technologie als eine potenzielle Lösung für den Bedarf an LSP- und elektromagnetischer Interferenz (EMI)-Abschirmung für seine zusammengesetzten Flugzeugstrukturen. „Im Durchschnitt werden Verkehrsflugzeuge alle 1.000 Stunden vom Blitz getroffen“, sagt Sprengard. Obwohl Kohlefaser leitfähig ist, sind die Matrixharze in Verbundwerkstoffen dies nicht. So verließen sich die Flugzeugstrukturen aus kohlenstofffaserverstärktem Polymer (CFK), die Boeing in Rekordzahlen für seine Verkehrsflugzeuge 777 und 787 produzierte, auf Streckmetallfolien und andere metallische Lösungen, um elektrischen Strom schnell zu einer geerdeten Verbindung zu leiten, um Hitzeschäden zu vermeiden . „Aber Metallgewebe sind schwer, erzeugen viel parasitäres Gewicht und können schwierig zu verarbeiten in Verbundteilen sein“, sagt Larry Christy, Produktentwicklungsingenieur von Veelo Technologies.
Bis 2015 hatte Boeing einen unternehmensweiten Vorstoß zur Entwicklung einer LSP-Lösung der nächsten Generation, und General Nano war ein wichtiger Partner. CW besuchte General Nano kurz darauf im Jahr 2016 an seinem ursprünglichen Standort in einem in Cincinnati ansässigen Gründerzentrum, das mehrere Start-ups beherbergte. Christy führte diese Tour durch die Labore des Unternehmens und diskutierte die damals laufende technologische Entwicklung. „Die Wirksamkeit von metallischem LSP und Abschirmung nimmt mit der Frequenz ab“, erklärte er. „Sie müssen die Leitfähigkeit verbessern und die Impedanz reduzieren, aber weniger als 25 Mikrometer dick sein. CNT-zu-CNT-Übergänge erhöhen jedoch den Widerstand innerhalb der Schicht. Von 2014 bis 2016 haben wir die Leitfähigkeit um das Zwölffache verbessert und eine Drop-In-Lösung für die Abschirmung bei einer Frequenz von 200 [Megahertz] MHz mit 25 % Gewichtseinsparung gegenüber Metall nachgewiesen. Aber wir müssen noch die Dicke reduzieren.“
Zu diesem Zeitpunkt hatte das Unternehmen die Möglichkeit entwickelt, ausgerichtete CNTs auf einem 5 Fuß breiten Substrat in Längen von mehreren hundert Fuß herzustellen. Es stellte auch 20 Gramm pro Quadratmeter, 2 Millimeter dickes CNT-Papier und Vliesstoffe her – eine Art CNT-Endlosvlies – unter Verwendung eines Netzwerks von Lohnfertigungspartnern mit Überkapazitäten in ihren Papierherstellungsanlagen. „Dieser Ansatz gibt uns Flexibilität“, erklärte Christy, „und ermöglicht es uns, uns darauf zu konzentrieren, mit unseren Kunden zusammenzuarbeiten, um Funktionen hinzuzufügen und die Eigenschaften und das Format unserer Produkte anzupassen.“ Das Unternehmen wurde auch gebeten, kontinuierliche Bänder herzustellen, die es wiederum über sein gebührenpflichtiges Netzwerk herstellte.
Schwenken Sie sich auf leistungsstarke, breite Güter
Diese Anpassungsfähigkeit und die Bereitschaft, seine Produkte an die Kundenanforderungen anzupassen, war entscheidend, da das Unternehmen etwa ein Jahrzehnt nach seinem Bestehen erkannte, dass seine Zukunft ganz anders aussehen könnte als in der Vergangenheit. Christy erklärte, dass es mehrere Anforderungen gebe, nicht nur für LSP, sondern auch für EMI-Abschirmung. „Man muss die elektrische Leistung für jeden individuell anpassen. Die Eigenschaften von Metallgeweben sind frequenzabhängig und nehmen mit zunehmender Frequenz aufgrund von Leckagen aus den Löchern im Blech ab. Unsere Leistung steigt mit der Häufigkeit, da unsere Produkte durchgehend ohne Löcher und ohne Leckagen sind. CNTs übertreffen Metalle bei hohen Frequenzen und eignen sich daher hervorragend für hochintensive Hochfrequenz-(HIRF)- und Hochleistungs-Satellitenkommunikationsanwendungen. CNTs haben auch keinen Hauteffekt , was bei Metallen ein Problem ist.“ Der Skin-Effekt ist die Tendenz, dass Wechselstrom nicht durch die Mitte eines Leiters wandert, sondern auf seine Oberfläche oder Haut beschränkt ist, wodurch die für die Stromführung verfügbare Querschnittsfläche effektiv reduziert und der Widerstand erhöht wird. Christy fährt fort:„Aber CNTs können bei niedrigen Frequenzen nicht mithalten. Ihre Leitfähigkeit ist einfach nicht hoch genug und der Signalverlust ist zu groß. Wir suchen also nach Hybriden.“
„Das führte zu anderen Plattenmaterialien, die nicht auf Nanomaterialien basieren“, sagt Sprengard. „Wir haben VeeloVEIL entwickelt, eine metallisierte Kohlefaserlösung für LSP, die 70 % leichter ist als expandierte Kupferfolie (ECF) und die Blitzeinschlagsschutzanforderungen der Zone 1A erfüllt.“ Zone 1A umfasst das Radom/Nase, Flügelspitzen, Gondeln und Extremitäten des Leitwerks eines Flugzeugs und muss 200.000 Ampere elektrischem Strom standhalten, wie in den Anforderungen der US-amerikanischen Federal Aviation Administration (FAA) definiert (siehe „LSP-Strategien für zusammengesetzte Flugzeuge“ und „LSP for Verbundstrukturen“). „VeeloVEIL ist viermal leitfähiger und dennoch halb so schwer wie andere metallisierte Vliesstoffe“, fährt er fort. „Dies ist möglich durch die von uns entwickelte Chemie und Materialbearbeitung.“
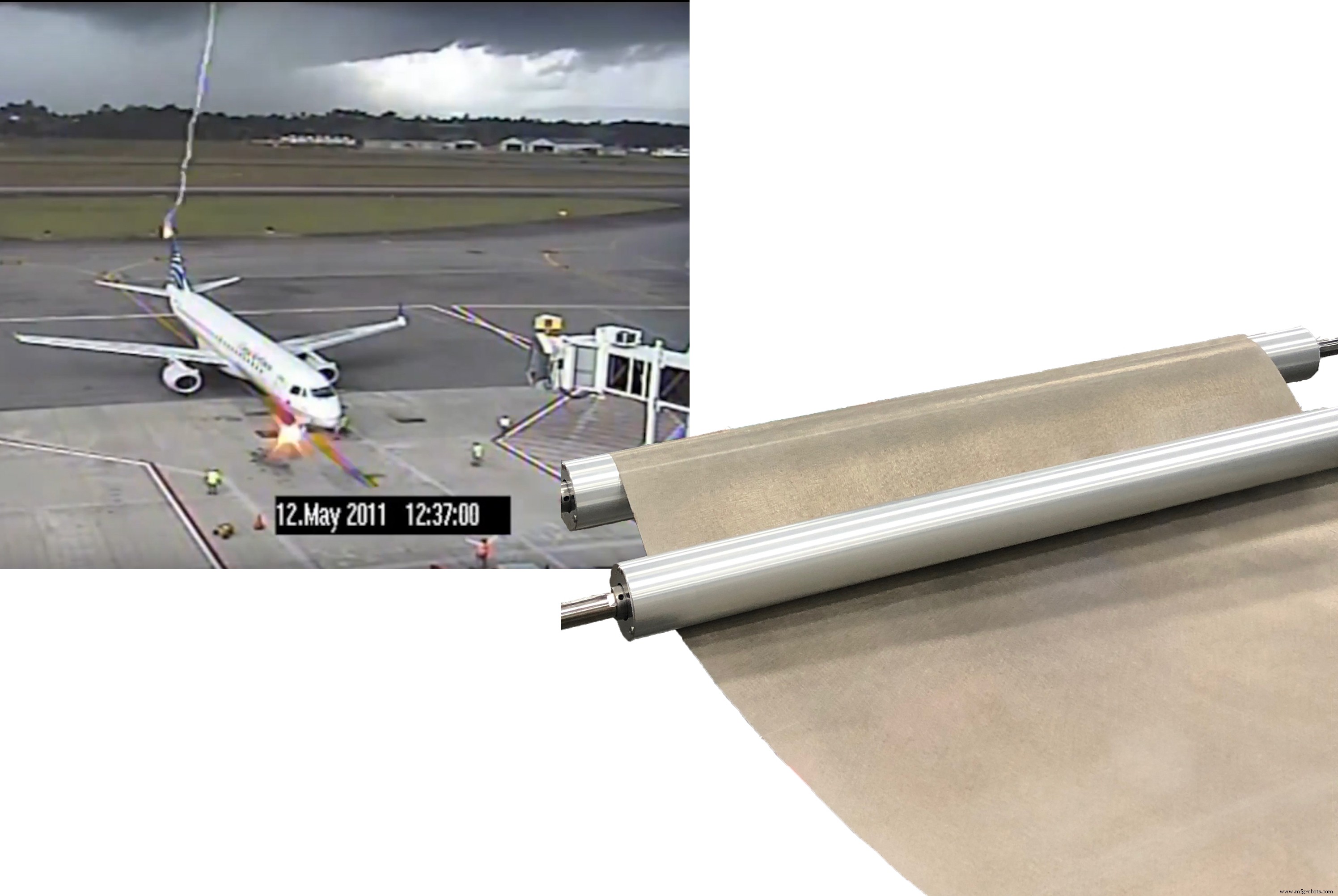
LSP der nächsten Generation für Flugzeugstrukturen
Verkehrsflugzeuge werden im Durchschnitt alle 1.000 Stunden vom Blitz getroffen. VeeloVEIL metallisiertes Kohlefaservlies erfüllt die Anforderungen des Blitzschlagschutzes (LSP) der Zone 1A für Verbundflugzeuge bei 70 % weniger Gewicht im Vergleich zu expandierter Kupferfolie. VeeloVEIL wurde für die Verarbeitung durch automatisierte Faserplatzierungs-/Tapelegemaschinen (AFP/ATL) entwickelt und liefert eine störende Leitfähigkeit in einer einzigen 80 Mikrometer dicken Lage und reduziert die gesamten LSP-Materialien und die Verarbeitungszeit um mehr als 75 %.
Die Luft- und Raumfahrtindustrie verwendet derzeit keinen Kohlefaserschleier für LSP, sagt Sprengard, „weil es keine Produkte gibt, die leitfähig genug sind, um die Anforderungen der Zone 1A zu erfüllen.“ VeeloVEIL wurde entwickelt, um einen spezifischen elektrischen Widerstand von 5-10 Milliohm (ein niedrigerer spezifischer Widerstand bedeutet ein leitfähigeres Material) bei einem Flächengewicht von 40-50 Gramm pro Quadratmeter zu liefern und erfüllt die LSP-Anforderungen von Flugzeugen mit einer einzigen, 80 Mikrometer dicken Lage. „Dadurch ist das Material sehr drapierbar, was zu einer glatten Oberfläche ohne die bei ECF-Produkten häufig erforderliche porenfüllende Nachbearbeitung führt“, bemerkt er. „Dies wiederum ermöglicht es den Herstellern, weniger Beschichtungsharz zu verwenden, was Material- und Herstellungskosten spart. Uns wurde von den drei führenden Flugzeugstruktur-OEMs gesagt, dass VeeloVEIL es ihnen ermöglicht, die gesamten LSP-Materialien und die Bearbeitungszeit von mehr als zwanzig Stunden auf weniger als drei Stunden zu reduzieren.“
VeeloVEIL wird in derselben Produktform wie ECF geliefert, sodass Hersteller es verwenden können, ohne ihre bestehenden Herstellungsprozesse zu ändern. „Alle unsere elektrisch leitfähigen Materialien für Verbundwerkstoffe für die Luft- und Raumfahrt sind so konstruiert, dass sie von [automatisierten Faserplatzierungs-] AFP-Maschinen verarbeitet werden“, sagt Sprengard. Veelo Technologies ist außerdem dabei, VeeloVEIL in ein Standardprodukt für Oberflächenschichten zu integrieren und arbeitet mit Tier-1-Prepreggern für die Luft- und Raumfahrt.
Anpassung der Leitfähigkeit für die Heizung
Während der Entwicklung von VeeloVEIL erkannte das Team von Sprengard, dass die Möglichkeit, die elektrische Leitfähigkeit seiner breiten Produkte maßzuschneidern, auch für elektrothermische Heizanwendungen genutzt werden könnte. Dies öffnete die Tür zu einer weiteren Produktfamilie, VeeloHEAT.
„VeeloHEAT ist ein kohlenstoffbasiertes, nichtmetallisches Material, das zur Enteisung in Flugzeugstrukturen integriert wird“, sagt Sprengard. Beachten Sie, dass dies nicht ist Kohlefaser. „Heute verwenden Flugzeugenteisungssysteme oft Metalldrähte, die Probleme mit der Haltbarkeit haben, insbesondere in Umgebungen mit hoher Ermüdung wie Drehflüglern. Wenn einer der Drähte bricht, funktioniert das System nicht mehr. Diese herkömmlichen Metallenteisungssysteme versagen häufig und müssen zeit- und kostenintensiv repariert werden. Wir haben bewiesen, dass unsere Produkte viel haltbarer sind, was die Ausfallzeiten des Flugzeugs drastisch verringert.“ Er stellt fest, dass diese Produkte tatsächlich auf Rotorblättern von Hubschraubern verwendet werden und ein erhebliches Potenzial für EVTOL-Flugzeuge (Electric Vehicle Takeoff and Landing) haben, die derzeit für die urbane Luftmobilität und die nächste Transportgeneration entwickelt werden.
Kurzfristig sagt Sprengard, dass VeeloHEAT-Produkte im ersten Quartal 2020 zur Frühqualifizierung in einem Verkehrsflugzeug mit festem Flügel fliegen sollen. „Die Attraktivität dieser Technologie ist kein Geheimnis“, sagt er und bemerkt, dass Collins Aerospace (ehemals UTC, das jetzt Teil von Raytheon sein wird) im Januar 2017 eine exklusive Lizenz für CNT-basierte Enteisungssysteme angekündigt hat Markt gut und positionieren sich für die Zukunft. Ihre Investition ist ein guter Hinweis darauf, wohin diese Technologie führt“, fügt Sprengard hinzu.
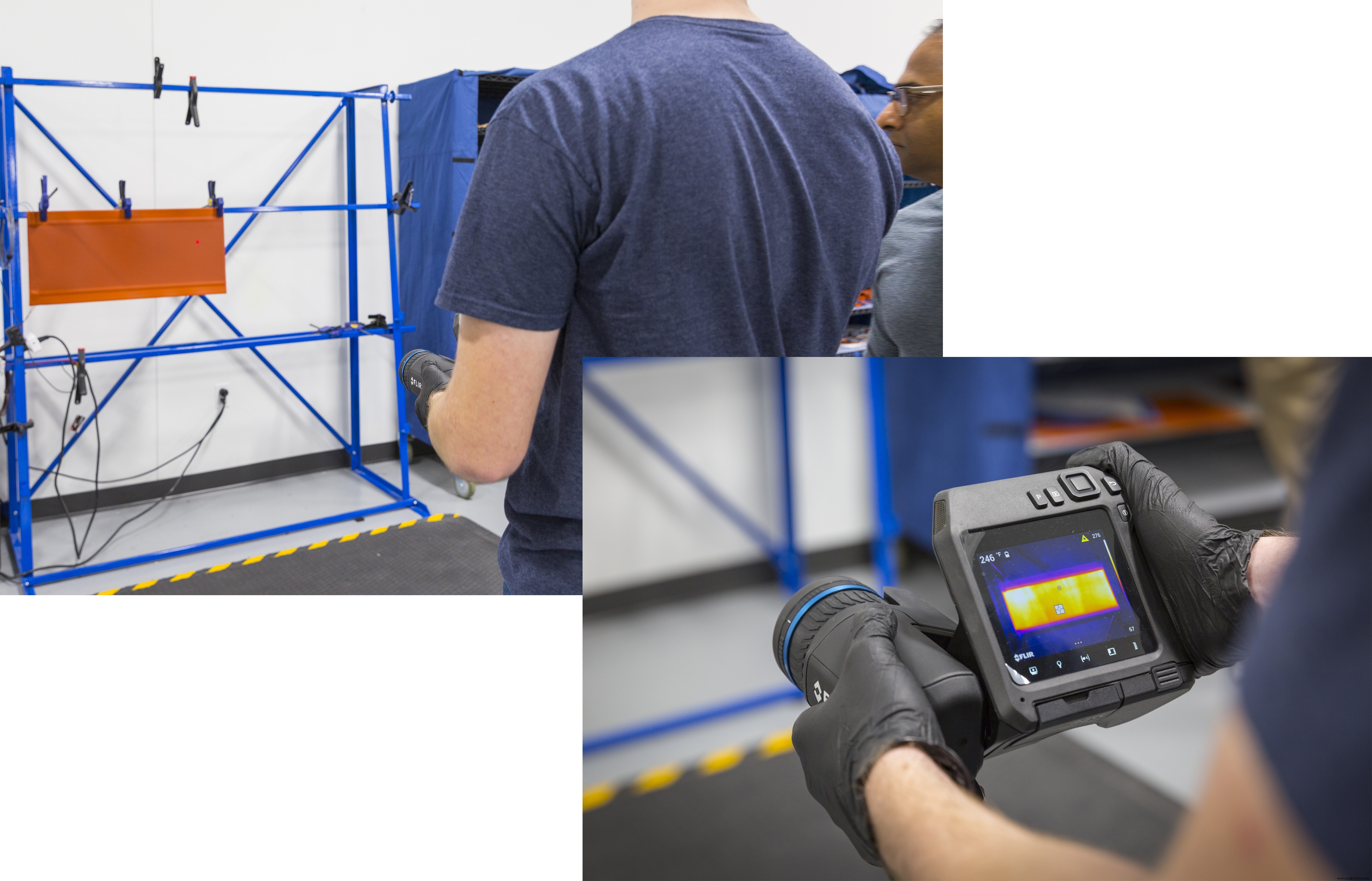
Veelo Technologies testet jedes VeeloHEAT Blanket auf Temperaturabgabe und Gleichmäßigkeit.
Vom Enteisen bis zur Verarbeitung und Reparatur von Verbundwerkstoffen
Herkömmliche Wärmedecken werden seit Jahrzehnten verwendet, um relativ kleine Flächen – typischerweise weniger als 1 Quadratmeter – von Verbundstrukturen während der Reparatur von geklebten Schals auszuhärten. Diese Heizdecken verwenden herkömmliche Metalldrähte, die in Silikongummi oder andere Materialien eingebettet sind (je nach erforderlicher Härtungstemperatur). „Ähnlich wie bei den metallbasierten Enteisungssystemen, wenn ein Draht bricht, werden Heizdecken kurzgeschlossen und funktionieren nicht mehr“, sagt Sprengard. „Wir haben unser kohlenstoffbasiertes Enteisungsprodukt zu einer nichtmetallischen Heizdecke mit unübertroffener Haltbarkeit und Drapierbarkeit sowie Leistung verarbeitet.“ Der Industriestandard für letzteres ist ein Varianzkoeffizient von 3 % (COV), der ein Maß für die Gleichmäßigkeit beim Erhitzen von Produkten von Deck zu Deck und von Kante zu Kante ist. Die VeeloHEAT Decke übertrifft diesen Standard mit der typischen Energieabgabe von 5 Watt pro Quadratzoll.
Die Wärmedecken von Veelo können Temperaturen bis zu 550 °F (288 °C) erzeugen und können netzförmig geformt werden, um Teile und Werkzeuge zu passen. „Diese Fähigkeit ist möglich, weil wir in der Lage sind, Chemikalien zu formulieren und einzigartige fortschrittliche Materialien mit maßgeschneiderten spezifischen Widerständen herzustellen“, bemerkt Sprengard. Veelo Technologies hat diese Technologie in 15 Monaten kommerzialisiert und befindet sich nun in voller Produktion. „Wir sehen ein sehr gutes Wachstum in dieser Produktlinie“, fügt er hinzu, „und produzieren jetzt große Mengen an VeeloHeat Blankets, die verwendet werden, um große Verbundstrukturen aus dem Autoklaven zu verkleben und Ofen, der mehrere Temperaturzonen und andere Verarbeitungsfunktionen nutzt, die unsere Kunden gewünscht haben.“
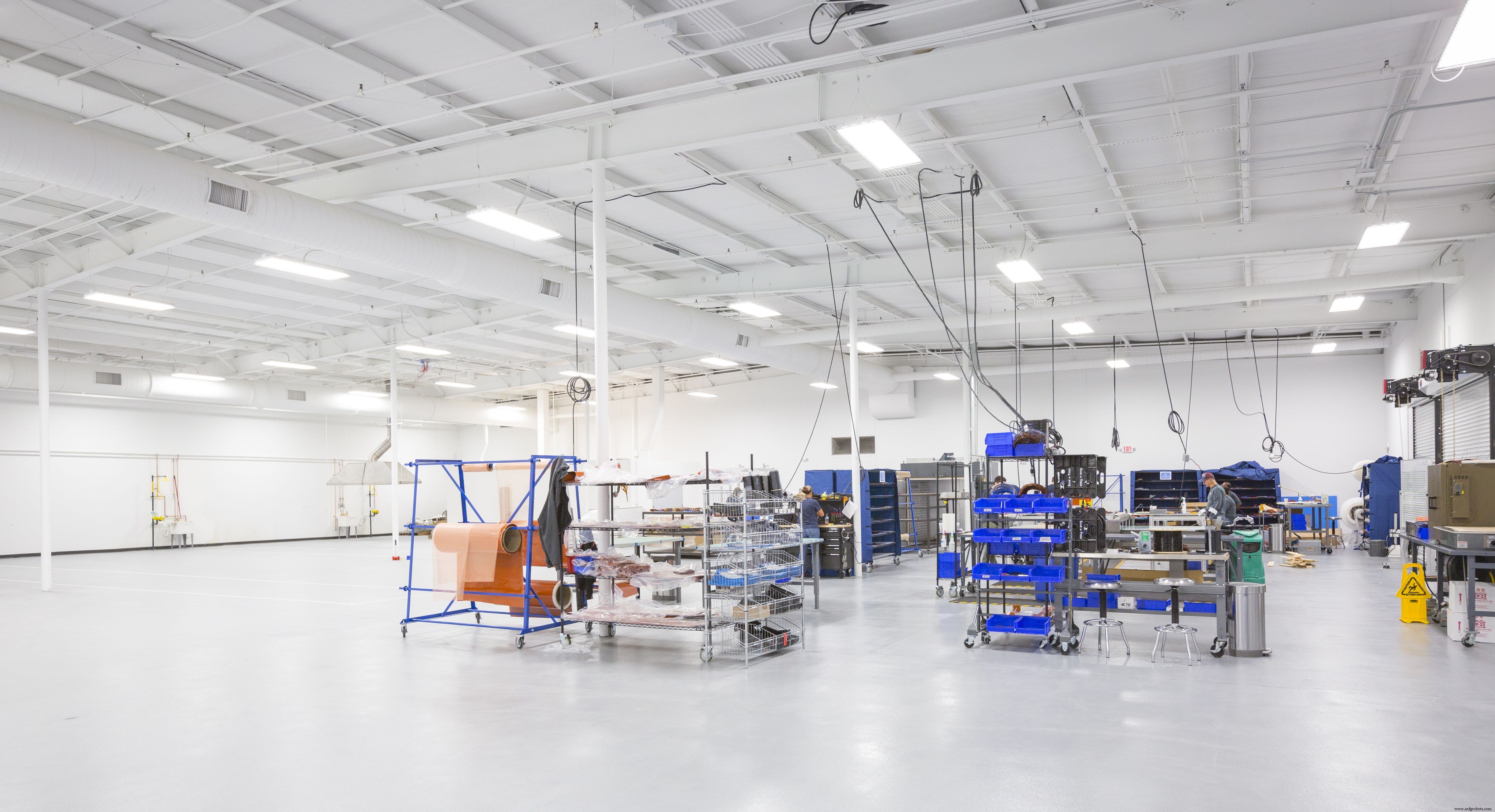
Produktion verlagern und hochfahren
Die neue 20.000 m² große Produktionshalle von Veelo Technologies bietet viel Platz für die Erweiterung der VeeloHEAT Blanket-Produktion, die in Phase eins des Produktionsübergangs verlagert und auf Hochtouren gebracht wurde. Phase zwei wird bis zum dritten Quartal 2019 abgeschlossen sein.
Fertigung nach Kundenwunsch
Im Oktober 2018 erhielt Veelo Technologies die Bestätigung, dass es ein großes Verteidigungsprogramm gewonnen hat, das einen sofortigen Anlauf erforderte. „Zum Glück fanden wir eine nahezu perfekte, bezugsfertige Einrichtung, die bereits mit der Infrastruktur ausgestattet war, die wir für den Startschuss brauchten“, erinnert sich Sprengard. Das Werk in Woodlawn ist mit modernster Umgebungskontrolle, Beleuchtung und durchgehendem Epoxid-Boden ausgestattet – mit Sprengard-Notizen als Standard in der Luft- und Raumfahrt von seinen Betriebstouren des Kunden. „Wir haben keine Abkürzungen genommen – unsere Investition in hochwertigste Materialien und Oberflächen spiegelt unsere langfristige Strategie und Vision für die Zukunft wider“, erklärt er. Diese Investition spiegelt sich auch in der Zugangskontrolle und dem Sicherheitspersonal der Einrichtung wider, die für ihre Verteidigungsverträge erforderlich sind.
Der erforderliche Ausbau der Anlage wurde im 2. Quartal 2019 abgeschlossen, woraufhin Veelo mit der Verlagerung seiner Produktionslinien begann. „Unsere gesamte Ausrüstung läuft fast mit voller Kapazität, was die Planung der Stilllegung für den Umzug aller Linien in die neue Anlage zu einer Herausforderung gemacht hat“, räumt er ein. Das Unternehmen schloss im Juli 2019 die erste Phase seiner Produktionsumstellung ab, indem es die VeeloHEAT Blanket-Linie verlagerte und sie wieder auf die volle Produktion hochgefahren hat.
Die große, offene Produktionshalle des neuen Werks wird von der vorderen Lobby aus erschlossen. Auf der rechten Seite befindet sich der Produktionsbereich für VeeloHEAT Blanket. Vier 4-Fuß-mal 10-Fuß-Layup-Tische werden verwendet, um VeeloHEAT-Folie mit anderen Materialien auf geformte Metallformwerkzeuge zu schichten. Diese Schichten werden dann in einem 10 mal 10 Fuß großen Ofen ausgehärtet, der von JPW Industrial Furnaces (Trout Run, PA, USA) geliefert wird. Die fertigen Gummitücher werden entformt und an elektrische Versorgungsleitungen angeschlossen, die den Einsatz mit computergesteuerten Steuereinheiten (Heißbondern) zum Aushärten von Verbundlaminaten und Reparaturen ermöglichen. Jede VeeloHEAT-Decke wird auf Temperaturabgabe und Gleichmäßigkeit getestet.
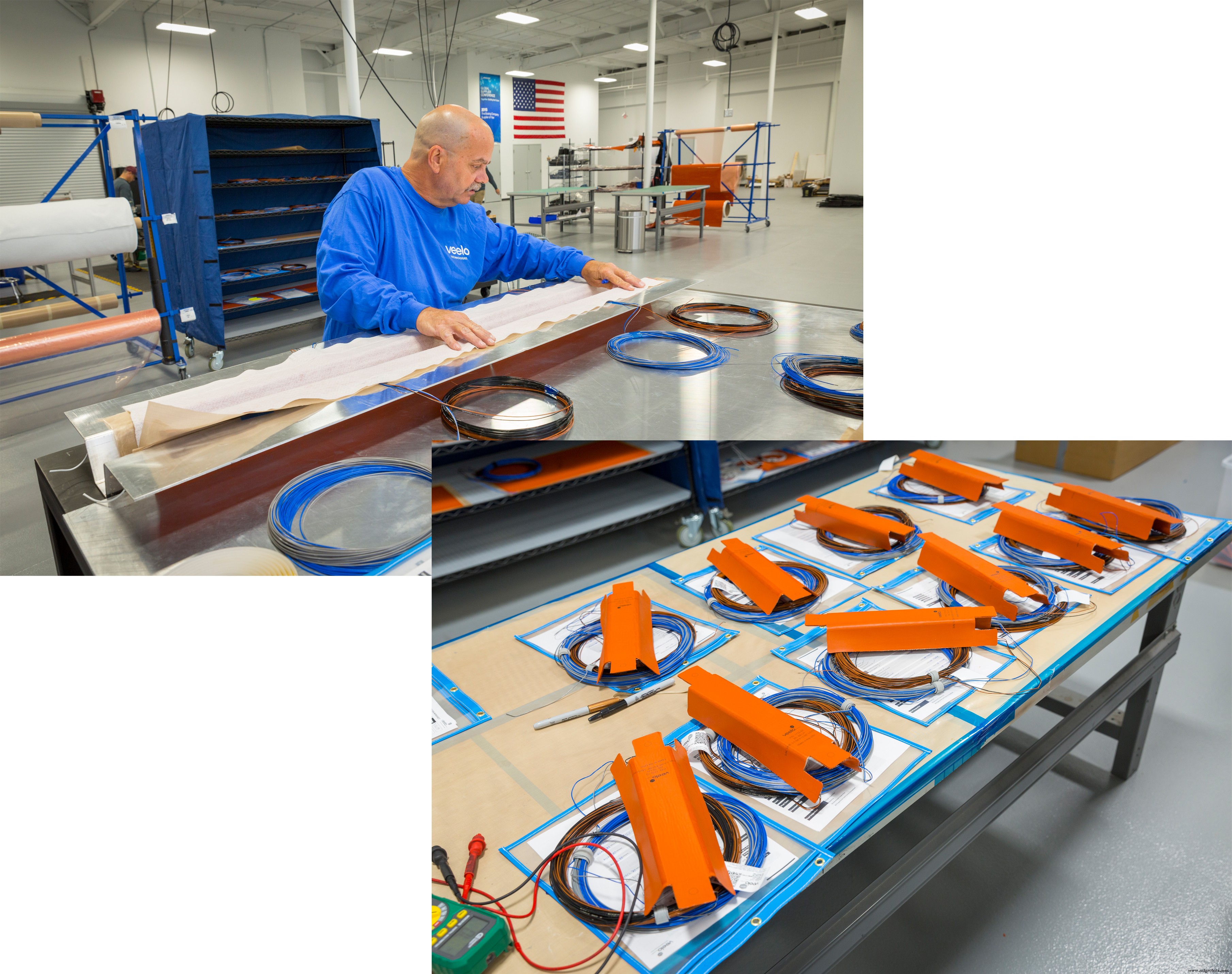
Haltbarere und anschmiegsamere, nichtmetallische Wärmedecken
Obwohl Drähte verwendet werden, um Metallwerkzeuge bei der Herstellung von VeeloHEAT Blankets (oben) zu erhitzen und während der Verbundhärtung und -reparatur elektrischen Strom von computergesteuerten Steuereinheiten (Heißbondern) an die Decken zu liefern, werden im Inneren keine Metalldrähte verwendet. Dadurch können diese nichtmetallischen Heizdecken in 3D-Formen ohne Drahtbrüche, Kurzschlüsse und Probleme bei der Temperaturgleichmäßigkeit (Hot- und Cold-Spots) hergestellt werden. Die kohlenstoffbasierte VeeloHEAT-Folie im Inneren erzeugt Temperaturen von bis zu 550°F (288°C) mit 3% COV bei 5 W/in2.
Direkt hinter dem Produktionsbereich der Heizdecke befindet sich der Produktionsraum für die Nasschemie. Hier werden Industrieanlagen von Silverson Machine (East Longmeadow, Massachusetts, USA) und Netzsch (Burlington, Massachusetts, USA) verwendet, um die fortschrittlichen chemischen Formulierungen zu mischen, die in Veelos Produkten verwendet werden. Als nächstes folgt der Filmherstellungsraum, der ein proprietäres System zur Herstellung von Veelos kohlenstoffbasierter VeeloHEAT-Folie beherbergt, der Schlüsseltechnologie im Inneren der VeeloHEAT-Decke. Wieder links befindet sich der Produktionsbereich von VeeloVEIL. Obwohl zum Zeitpunkt dieser Tour leer, wurden im August sowohl die 15-Zoll- als auch die 36-Zoll-breiten Rolle-zu-Rolle-Fertigungslinien für die VeeloVEIL-Produktion in die neue Anlage umgezogen. Das Unternehmen ist auch dabei, eine 60-Zoll-breite Linie zu konzipieren, um den zukünftigen Bedarf zu decken. Bis Oktober wird Veelo Technologies alle Produktlinien unter einem Dach betreiben und die Produktion steigern.
Lösungen der nächsten Generation
Der Weg zum aktuellen Erfolg von Veelo Technologies war lang und nicht immer geradlinig. „Ja, wir haben mit Nanomaterialien angefangen und verfügen immer noch über eine bedeutende Expertise in diesem Bereich, aber keiner unserer Kunden kümmert sich darum, ob wir Nanomaterialien verwenden oder nicht“, sagt Sprengard. „Es interessiert sie nur, wenn wir eine überzeugende Lösung liefern, die ihre Leistungs- und ROI-Ziele erfüllt. Zum Beispiel Produkte, die es der nächsten Generation von Enteisungssystemen ermöglichen, weniger Strom am Flugzeug zu verbrauchen, was neue Möglichkeiten für Luftfahrzeugdesigns und Betriebseffizienzen eröffnet.“
Sprengard sagt, dass sich alle drei Veelo-Produktfamilien weiterentwickeln und entweder in OEM- und Supplier Qualified Product Lists (QPLs) aufgenommen werden oder als Teilenummer in die Lieferbasis unserer Kunden aufgenommen werden. Obwohl die überwiegende Mehrheit dessen, was das Unternehmen jetzt für duroplastische Verbundwerkstoffe macht, beschäftigt werden, beginnt er, sich auch mit thermoplastischen Verbundwerkstoffen und der additiven Fertigung zu befassen.
Wo konzentriert sich Veelo Technologies für die Zukunft? „Unsere oberste Priorität ist es, unsere bestehenden Aufträge und strategischen Möglichkeiten weiterhin zu erfüllen“, sagt Sprengard. „Der Markt drängt uns, eine neue Nachfrage zu befriedigen, die großartig und herausfordernd ist. Konzentriert zu bleiben ist unsere oberste Priorität.“
Die Ziele, die sich Veelo jetzt gesetzt hat, sind ebenso beeindruckend wie seine Beharrlichkeit und Geduld in 12 Jahren Entwicklung, um diesen Punkt zu erreichen. „Wenn man sich die besten Composite-Lieferanten für die Luft- und Raumfahrt wie Airtech und A&P Technologies ansieht“, sagt Sprengard, „sie sitzen früh in den Entwicklungszyklen ihrer Kunden am Tisch. Ein solcher Innovationspartner zu sein braucht Zeit.“ Er fügt hinzu:„und Engagement.“
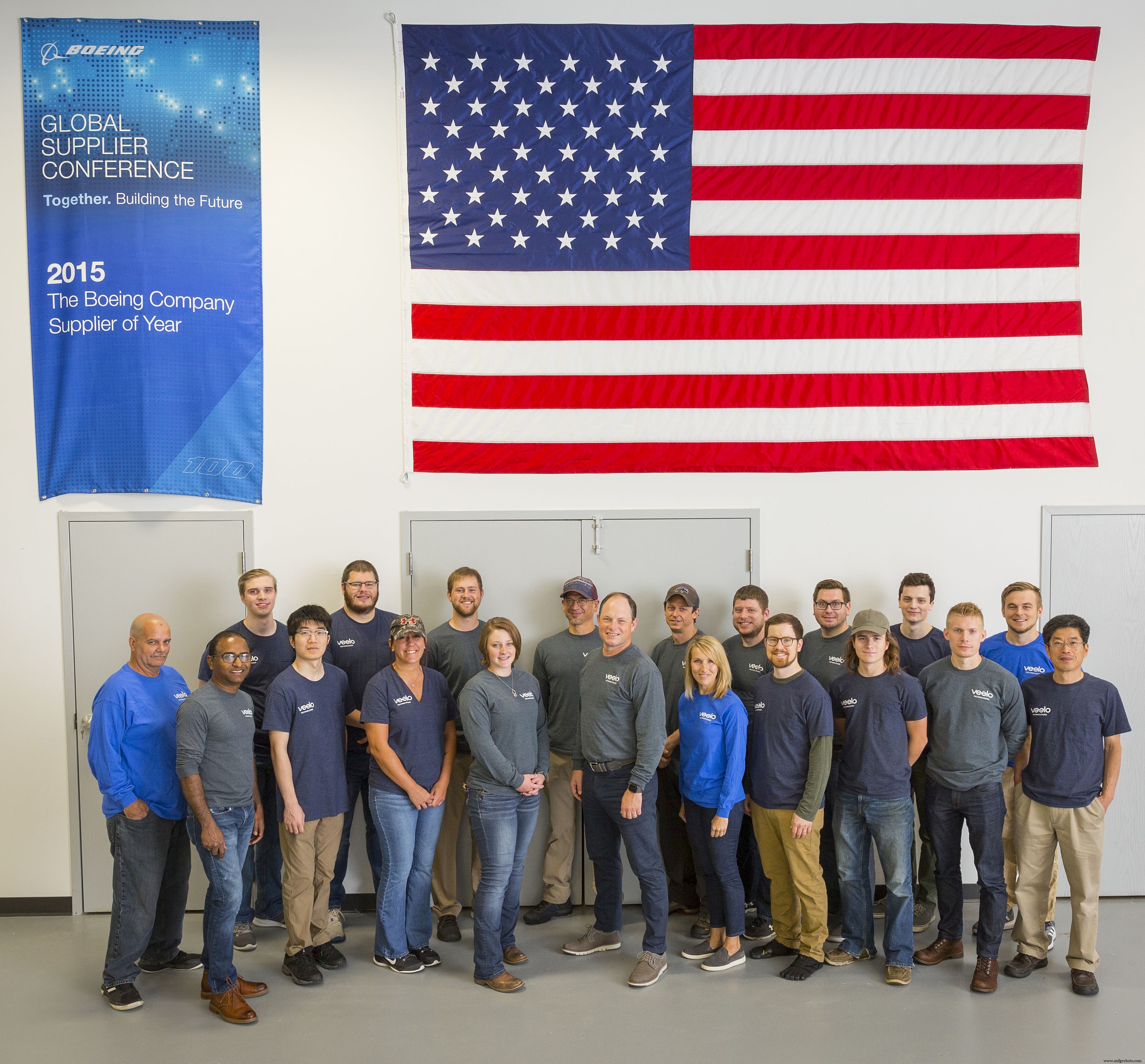
Veelo Technologies ist von vier auf 24 Mitarbeiter angewachsen und hat sich von einem Nanomaterial-Lieferanten über einen Spezialisten für fortschrittliche Produkte zum Innovationspartner für zukünftige Verbundwerkstoffe entwickelt, der 2015 von Boeing als Lieferant des Jahres ausgezeichnet wurde.
Verbundwerkstoff
- Emerson liefert fortschrittliche Automatisierungstechnologien für eine revolutionäre Kunststoffrecyclinganlage
- Einführung zuverlässiger Pflanzen
- Saudisches Elektrizitätswerk zur Verbesserung der Kraftwerkszuverlässigkeit
- Technologien für Industrie 4.0
- Hersteller besuchen Southco für Werksbesichtigung, kontinuierliche Verbesserung Best Practice-Diskussion
- Was ist Anlagenwartung?
- Werkzeugdrehmaschine
- CNC-Drehmaschine
- Plattform für Quantentechnologien mit Gold
- Technologien als Wegbereiter für Industrie 4.0