McLaren, Bcomp verwenden natürliche Verbundfasern in F1-Rennsitzen
Laut McLaren aus Großbritannien ist ein neuer bahnbrechender Durchbruch, der den Motorsport und darüber hinaus weiter verändern könnte, ein Naturfaser-Rennsitz, der als das allererste Formel-1-Autoteil (F1) aus erneuerbaren Textilfasern gilt.
In Zusammenarbeit mit dem nachhaltigen Leichtbauhersteller Bcomp (Fribourg, Schweiz) soll der neuartige Rennsitz für Carlos Sainz und Lando Norris die mechanischen Eigenschaften von Flachsfasern durch die Gewebearchitektur optimieren und einen Sitz mit der erforderlichen Festigkeit und Steifigkeit, aber mit 75 % weniger CO2 Fußabdruck im Vergleich zu seinem Kohlefaser-Pendant. Ähnlich wie bei der Einführung des ersten Autos mit einem Kohlefaser-Monocoque-Chassis – dem McLaren MP4/1 Formel-1-Rennwagen (F1) von 1981, der das Rennwagendesign bis heute stark beeinflusst haben soll – die Flachsfasern sind deutlich günstiger, reduzieren Vibrationen, erhöhen die Sicherheit und sind eine nachhaltigere Alternative.
„Der Einsatz von Naturfaserverbundwerkstoffen ist das jüngste Beispiel für wegweisende Innovationen bei Verbundwerkstoffen bei McLaren“, erklärt McLaren F1-Teamchef Andreas Seidl. „Diese Lösung bietet nicht nur eine gleichwertige Leistung wie Kohlefaser, sie stellt einen weiteren Schritt nach vorne in unserem sich entwickelnden Nachhaltigkeitsprogramm dar und unterstreicht gleichzeitig unser Engagement, die F1 bei der Umsetzung ihrer ehrgeizigen Nachhaltigkeitsstrategie in die Tat umzusetzen.“
„Die F1 ist seit Jahrzehnten ein Innovationslabor für Technologie, die nicht nur den Motorsport, sondern auch die Automobilindustrie und darüber hinaus verändert hat“, ergänzt James Key, technischer Direktor der McLaren F1. „Der Sport muss den Weg der Entwicklung immer umweltfreundlicherer Optionen fortsetzen, und unsere Entwicklung und Anwendung von Naturfaserverbundwerkstoffen ist ein Beispiel dafür, wie wir diesen Weg sowie die fortlaufende Entwicklung hin zu sauberer Mobilität beschleunigen.“
McLaren wird hauptsächlich zur Herstellung von Leinen verwendet und stellt fest, dass Flachs eine unglaublich vielseitige Pflanze ist. Außerdem ist Flachs ein CO2 -neutraler Rohstoff und seine Fasern sind biologisch abbaubar. Am Ende der Lebensdauer des Sitzes kann er beispielsweise zu einem neuen Basismaterial zermahlen oder ohne Restmüll thermisch recycelt werden, anstatt auf einer Deponie zu landen.
Inspiriert von den dünnen Adern auf der Rückseite der Blätter soll die proprietäre powerRibs-Technologie von Bcomp eine 3D-Gitterstruktur auf einer Seite der Sitzfläche bereitstellen, die dann zur Verstärkung des gesponnenen und gewebten Flachsfaser-Verstärkungsgewebes ampliTex von Bcomp verwendet wird. Die powerRibs werden durch das Verzwirnen von Flachsfasern zu einem dicken Garn hergestellt und sollen als Rückgrat des damit verbundenen ampliTex Flachsgewebes dienen.
Nach Angaben des McLaren F1-Teams wurde das ursprüngliche Kohlefaser-Sitzdesign von Bcomp nachgebaut, und das neue Design wurde von McLaren optimiert und hergestellt. Der Sitz wurde dann ohne Probleme in der Vorsaison getestet.
„Nachhaltigkeit und Dekarbonisierung sind ein globales Thema, und es ist fantastisch zu sehen, wie sich der Motorsport auf Kohlenstoffalternativen einlässt und so den Weg für eine breite Einführung in groß angelegte Mobilitätsanwendungen ebnet“, sagt Christian Fischer, CEO und Mitbegründer von Bcomp, die Meinung des McLaren-Teams. „McLaren war schon immer ein Vorreiter im Sport, sowohl in Bezug auf Verbundwerkstoffe als auch auf Nachhaltigkeit. Es fühlt sich an wie die perfekte Ergänzung und eine große Ehre, mit einer so prestigeträchtigen Marke zusammenzuarbeiten.“
Warum also hat McLaren damit begonnen, Naturfasern in einen leichten und nachhaltigen Rennsitz zu verwandeln, im Gegensatz zu anderen Teilen des Autos?
Nach Angaben des Teams sahen sie eine klare Chance, die Technologie in diesem Bereich des Autos basierend auf dem aktuellen technischen F1-Reglement einzusetzen. Seit 2019 ist laut McLaren-Team ein Mindestfahrergewicht von 80 Kilogramm vorgeschrieben. Wenn ein Fahrer darüber hinaus weniger wiegt, muss er mit Ballast auf das Mindestgewicht gebracht werden. Anstatt jedoch zuzulassen, dass dieser Ballast in anderen Bereichen des Autos platziert wird, was die Gewichtsverteilung verbessern könnte, muss er sich in unmittelbarer Nähe des Fahrersitzes befinden.
„Mit der Einführung des neuen Reglements im Jahr 2019 ist der Sitz nun Teil des Gewichtsbudgets des Fahrers und daher überdimensioniert“, erklärt Steve Foster, leitender Ingenieur für Verbundwerkstoffe bei McLaren. „Und da Carlos und Lando 72 beziehungsweise 68 Kilogramm wiegen, gibt es viel Spielraum dafür. Dies bedeutete, dass bei Bedarf ein Spielraum für die Verwendung von zusätzlichem Bioverbundmaterial vorhanden war, um eine ausreichende Festigkeit und Steifigkeit dieser sicherheitskritischen Komponente zu gewährleisten.“
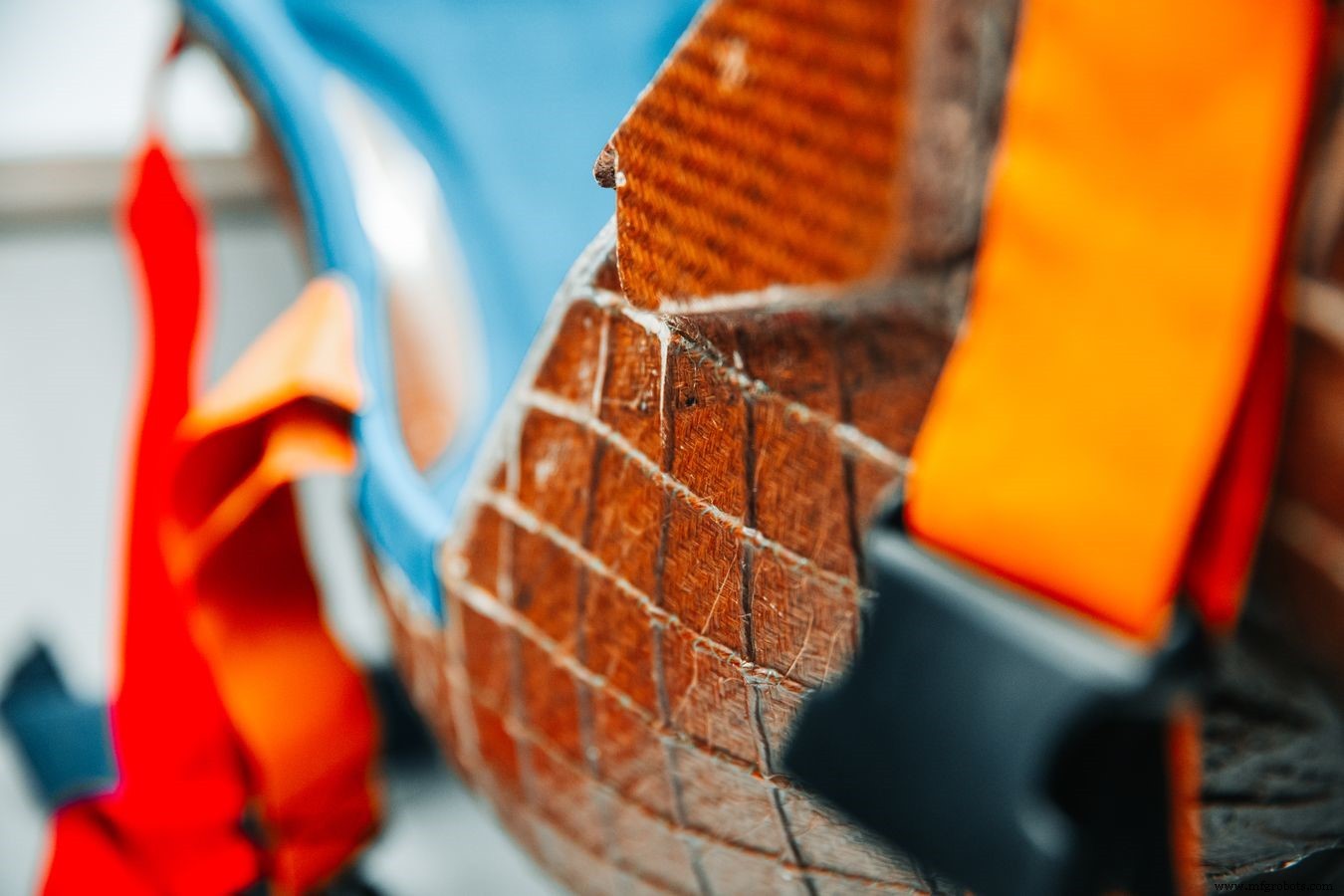
Diese ausreichende Festigkeit und Steifigkeit, fügt McLaren hinzu, ist auf die röhrenförmige Struktur aus Flachsfasern zurückzuführen, die eine geringe Dichte und eine hohe Steifigkeit bieten sollen, was die Möglichkeit bietet, Gewicht zu reduzieren und gleichzeitig die Schwingungsdämpfung sowie die Bruch- und Torsionsfestigkeit zu verbessern und Kompression. Das Team fügt hinzu, dass Flachsfasern erheblich leichter sind und 9 % leichter sind als vergleichbare Carbonmaterialien.
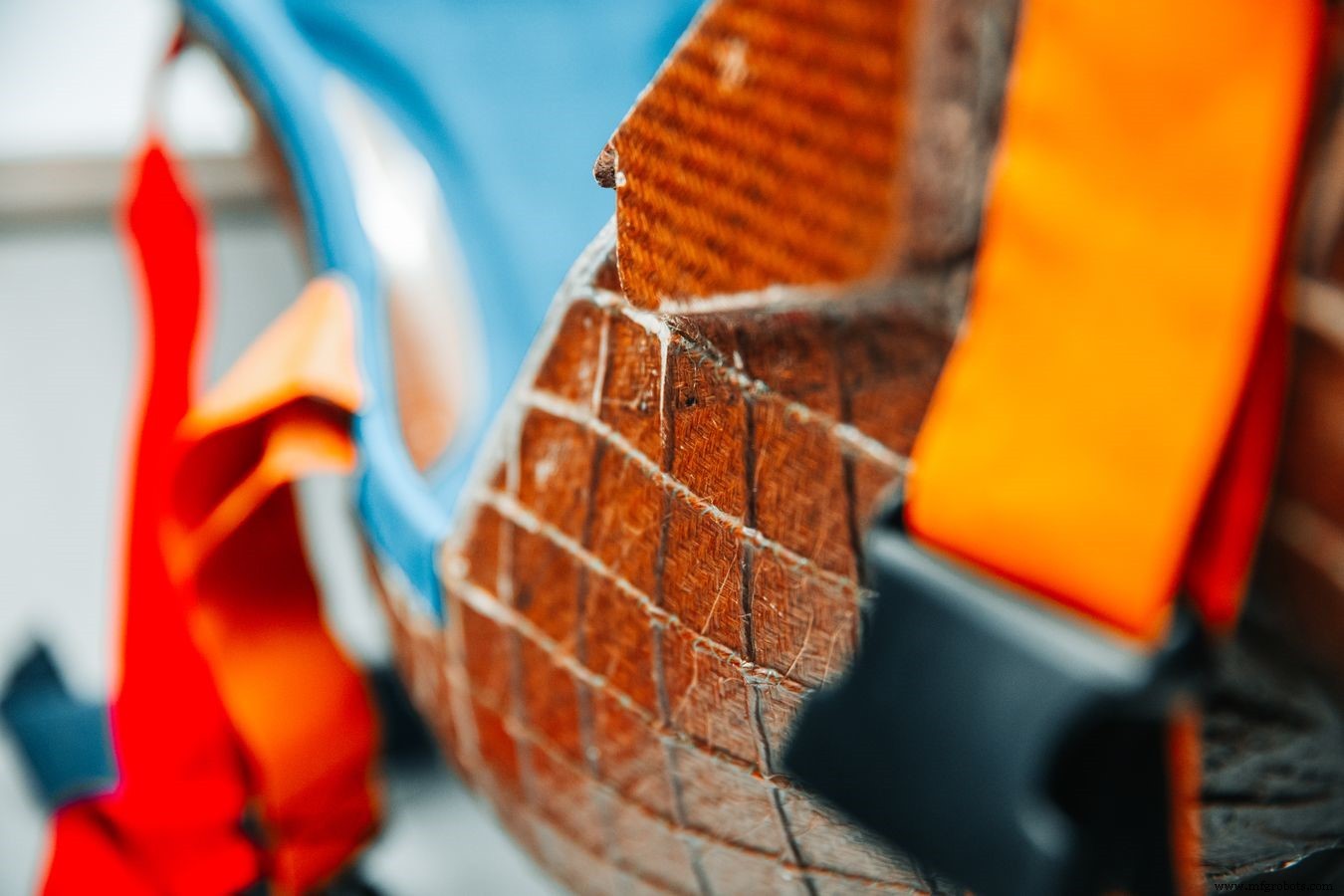
„Und wenn wir ‚deutlich besser‘ sagen, meinen wir dank des ampliTex-Flachsgewebes und der powerRibs-Technologie von Bcomp fünfmal besser“, sagt das Team. Durch die höhere Schwingungsdämpfung und Schlagfestigkeit eignet sich das Naturfasermaterial hervorragend für den Einsatz im Fahrersitz. Es verbessert den Komfort und reduziert Vibrationen im Cockpit, die auf den Fahrer ermüdend wirken können, insbesondere über eine Renndistanz und insbesondere auf Strecken mit aggressiven Bordsteinkanten.
Die Sicherheitsverbesserung der Flachsfaser macht sie zu einer weiteren Verbesserung in McLarens Augen. Es wird gesagt, dass es im Gegensatz zu Kohlefasern nicht zu Sprödbrüchen und Splittern neigt, wenn es bricht. „Der Verbund aus ampliTex und powerRibs ist nicht so zerbrechlich, und während er noch bricht, bleiben die weicheren Trümmer mit Hilfe der powerRibs an der Hauptstruktur haften, die helfen, die Energie abzuleiten“, erklärt Fischer. Das duktile Bruchverhalten soll auch in anderen Aspekten von F1-Rennwagen vielversprechend sein, einschließlich der Frontflügel-Endplatten und des Bodens, da es Ablagerungen und das Risiko von Pannen bei Kollisionen auf der Strecke reduzieren könnte.
Darüber hinaus müssen viele F1-Teams mit einer Budgetobergrenze, die bis 2021 eingeführt wird, die Kosten senken und gleichzeitig die Leistung beibehalten und verbessern. Teams müssen noch intelligenter arbeiten, sagt das McLaren-Team, und mit den Lösungen von Bcomp, die die Rohstoffkosten im Vergleich zu herkömmlicher Kohlefaser um bis zu 30 % senken, könnten die erheblichen Kosteneinsparungen Budget freisetzen, um andere Möglichkeiten zur Verbesserung der Fahrzeugleistung zu erkunden .
„Wir sehen erhebliches Potenzial in den unkritischen, semistrukturellen Bereichen des Autos, wie dem Fahrersitz, sowie außerhalb des Autos“, sagt Fischer. Und gerade Letzteres verrät Foster, wo die unmittelbaren Möglichkeiten für die weitere Verbreitung von Naturfaserverbundwerkstoffen liegen:„Bei intelligentem Einsatz reduzieren die Flachsfasern Gewicht und Kosten bei gleichbleibender und teilweise sogar verbesserter Leistung. Es gibt eine Reihe möglicher Anwendungen, die über das Auto selbst hinausgehen, einschließlich Grubenausrüstung, LKW-Verkleidungen, Verpackungskisten, Steuerständern und Formwerkzeugen.“
Bei so vielen Anwendungsmöglichkeiten, so das McLaren-Team, sei der Rennsitz aus Naturfaserverbundstoff erst der Anfang. „Dieser Sitz ist der erste Schritt zum erfolgreichen Einsatz von Naturfaserverbundwerkstoffen in der Formel 1“, so Seidl abschließend. „Durch die Zusammenarbeit mit Bcomp können wir andere Komponenten identifizieren, die wir durch eine nachhaltige Alternative mit gleichem Gewicht und gleicher Leistung ersetzen können. Es gibt keinen Königsweg im Rennen um CO2-Neutralität. Stattdessen müssen wir kontinuierlich jedes Element unserer Autos und unseres Betriebs bewerten, um Wege zu finden, wie wir die Leistung verbessern, die Effizienz steigern und die Umweltbelastung reduzieren können.“
Faser
- Warum verwenden F1-Rennmotoren Kurbelwellen aus Wolframlegierung?
- Fahrradsitz
- 10 überraschende Beispiele für Verbundwerkstoffe
- Die Liste der Verbundwerkstoffe:Häufig verwendete natürliche Verbundwerkstoffe
- Verbundwerkstoffherstellung:Die Herstellung von Verbundwerkstoffen
- Was sind Verbundwerkstoffe?
- Warum Schweißdecken verwenden
- So verwenden Sie die Feuerlöschdecke richtig
- Wie verwenden Wasserparks FRP?
- Durchgehend faserverstärkter thermoplastischer Verbundwerkstoff vollständig aus natürlichen Ressourcen hergestellt