Hot-Drape-Formung
Diese Online-Seitenleiste für den Artikel vom März 2021, "Advancing the OOA Infused Wing Box", zielt darauf ab, das zusammenzuführen, was CW hat über die Bildung von Heißfolien im Laufe der Jahre an einem Ort geschrieben und bietet hoffentlich eine nützliche Ressource. Nachfolgend finden Sie Auszüge aus mehreren Artikeln – von 2010 bis 2020 – mit Fotos, um zu zeigen, wie das Heißfolienformen zur Automatisierung der Verbundstoffproduktion beiträgt.
2010, GKN Aerospace, A400M-Holm
Aus:„Verbundstoff-Flügelholme tragen die enormen Turboprop-Triebwerke“
Phil Grainger, technischer Direktor und Cheftechnologe von GKN Aerospace, erklärt, dass der manuelle Bau eines so großen Teils, wie es bei den frühen A400M-Holmen der Fall war, mit einer Ablegerate von typischerweise 0,75 kg/h (1,5 lb/h) langsam ist. Während der Serienproduktion wird das Teil jedoch mit einer automatisierten Tape-Schicht (ATL) flach gelegt und anschließend heiß drapiert in die C-Profilform. An diesem Punkt sind Auflegeraten von 25 kg/h (50 lb/h) erreichbar. Grainger betont, dass dies erreichbare Durchschnittsraten über eine Schicht an realen Teilen sind.
Um den Prozess zu automatisieren, hat GKN Aerospace in ein großes ATL mit einem 20 m/63-Fuß-Bett investiert, das von MTorres (Navarra, Spanien) hergestellt wird. Die ATL ist in der Lage, die komplexen Preforms in ihren entwickelten Formen aus unidirektionalem Prepreg zu verlegen, wobei ein 977-2 Carbonfaser/gehärtetes Epoxid-Uniband von Cytec Engineered Materials Ltd. (jetzt Solvay, Wrexham, UK) verwendet wird. Um den C-Abschnitt zu formen, wird der Vorformling von der Tapeschicht zu einem Heißdrapierformer bewegt bereitgestellt vom Gerätehersteller Aeroform Ltd. (Poole, Dorset, Großbritannien). Um das Ziehen eines Vakuums zu erleichtern, wird die Schichtung zwischen zwei Membranen aus Kapton-Polyimid-Folie gelegt, die von DuPont Electronic Technologies (Circleville, Ohio) geliefert werden. Der Raum zwischen den Filmen wird evakuiert und dann wird eine Infrarotheizung von oberhalb des Teils angewendet, um die Temperatur über einen Zeitraum von einer Stunde auf 60 °C/140 °F zu erhöhen. Dadurch wird sichergestellt, dass auch das Material in der Mitte des dicksten Abschnitts am Wurzelende gleichmäßig auf die gleiche Temperatur erwärmt wird. Dann wird sanft Druck ausgeübt, um das Laminat zu bilden, das von den beiden Membranen über einem leichten Werkzeug gehalten wird, das die Innenfläche des Holms genau darstellt. Dieser C-Formungsprozess wird sehr langsam über einen Zeitraum von 20 Minuten erreicht. (Nach dem Formen werden die Kaptonfilme verworfen.)
2014, FACC, A321-Klappen
Von:„FACC AG:Kraftpaket Aerocomposites“
Im Werk 3 werden verschiedenste Klappen, Verkleidungen und Flugleitflächen gefertigt. Auch hier Effizienzsteigerungen durch automatisiertes Tapelegen (ATL) und Heißdrapieren ausgenutzt werden. Letzterer wendet Hitze und Druck auf flache ATL-Preforms unter Verwendung eines Kerns und eines flexiblen Formkissens an, um dreidimensionale Formen zu erzeugen (siehe Abb. 7). Ein Beispiel ist die fortlaufende A321 Klappenproduktion, die eine hochmoderne automatisierte Arbeitszelle verwendet, die von Fill (Gurten, Österreich) kundenspezifisch entwickelt wurde.
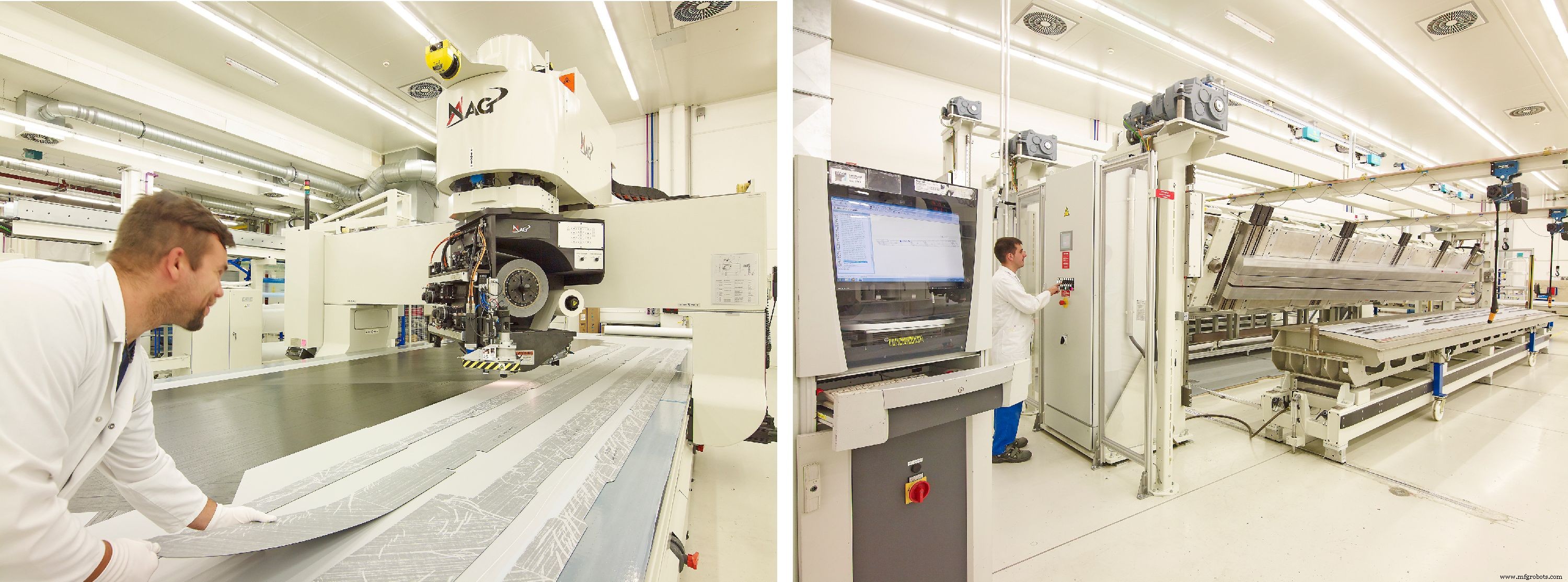
2018, Füllen, automatisiertes Vorformen
Aus:„Automatisiertes Preforming, Teil 7:Fill Gesellschaft“
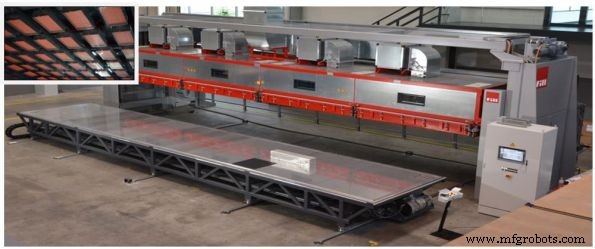
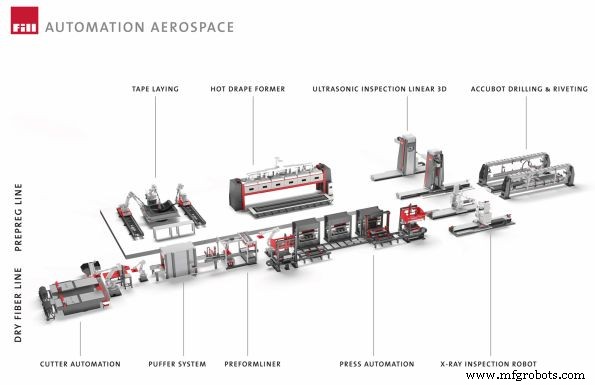
In den letzten Tour-Artikeln, die Sara Black und ich über Hochleistungs-Verbundwerkstoffe in Israel geschrieben haben, haben wir festgestellt, dass die meisten Unternehmen Heißdrapierung verwenden . Tatsächlich sagte unser Reiseleiter Jonathan Hulaty bei Elbit Cyclone:„Ich weiß nicht, wie Sie diese Art der Hochgeschwindigkeits-Prepreg-Teileproduktion ohne Heißdrapierung durchführen“ und bezog sich dabei auf Träger und Stützen für Boeing 787-Baugruppen. Hot-Drape-Former (HDF) werden auch von FBM und Israel Aerospace Industries als unverzichtbar angesehen.
Fill liefert seit Jahren HDF-Systeme, darunter mehrere Einheiten in der Produktion bei FACC. Sie sind im Wesentlichen Vakuumformsysteme, die mit Infrarot- oder anderen Arten von Heizelementen und einer wiederverwendbaren Silikonkautschukmembran ausgestattet sind, um Prepreg-Layups vor dem Aushärten auf ihren Werkzeugen zu erhitzen und zu komprimieren – debulk. HDF wird zu einem Schlüsselelement in der unten gezeigten kompletten Aerocomposites-Produktionslinie.
2018, FBM, 787 Teile
Aus:„Zusammenschluss unternehmerischer, metallzentrierter Firmen beansprucht Composites‘ First“
CW wird zunächst in einen Reinraum geführt, in dem Arbeiter verschiedenste Teile verlegen. An mehreren Stationen, die jeweils mit einem computergesteuerten Layup-Assist-Computerbildschirm ausgestattet sind, stehen an diesem Tag Teile für die Boeing 787 im Mittelpunkt. Leicht verständliche Touchscreens zeigen deutlich die Layup-Winkel für jede Lage und wie sie sind an jedem Werkzeug zu positionieren. Eine „Guillotine“-Maschine von Century Design (San Diego, CA, USA) mit einem 2m-Durchmesser-Drehtisch und einer Messerklinge in der Mitte ermöglicht das schnelle Schneiden von schrägen Lagen aus dem Carbon/Epoxy-Prepreg. Werkzeuge für die 787-Türrahmen sind geformte Stahldorne, die normalerweise länger als breit sind, von wenigen Zentimetern bis zu ~2 m Länge, die zur Herstellung von Hunderten von Rahmen, Halterungen und Clips verwendet werden. Ein automatisierter Flachbett-Schneidetisch von Assyst-Bullmer Inc. (Wakefield, UK) wird von den Layup-Technikern verwendet, um bis zu 50 gestapelte Lagen in einem Arbeitsgang zu schneiden.
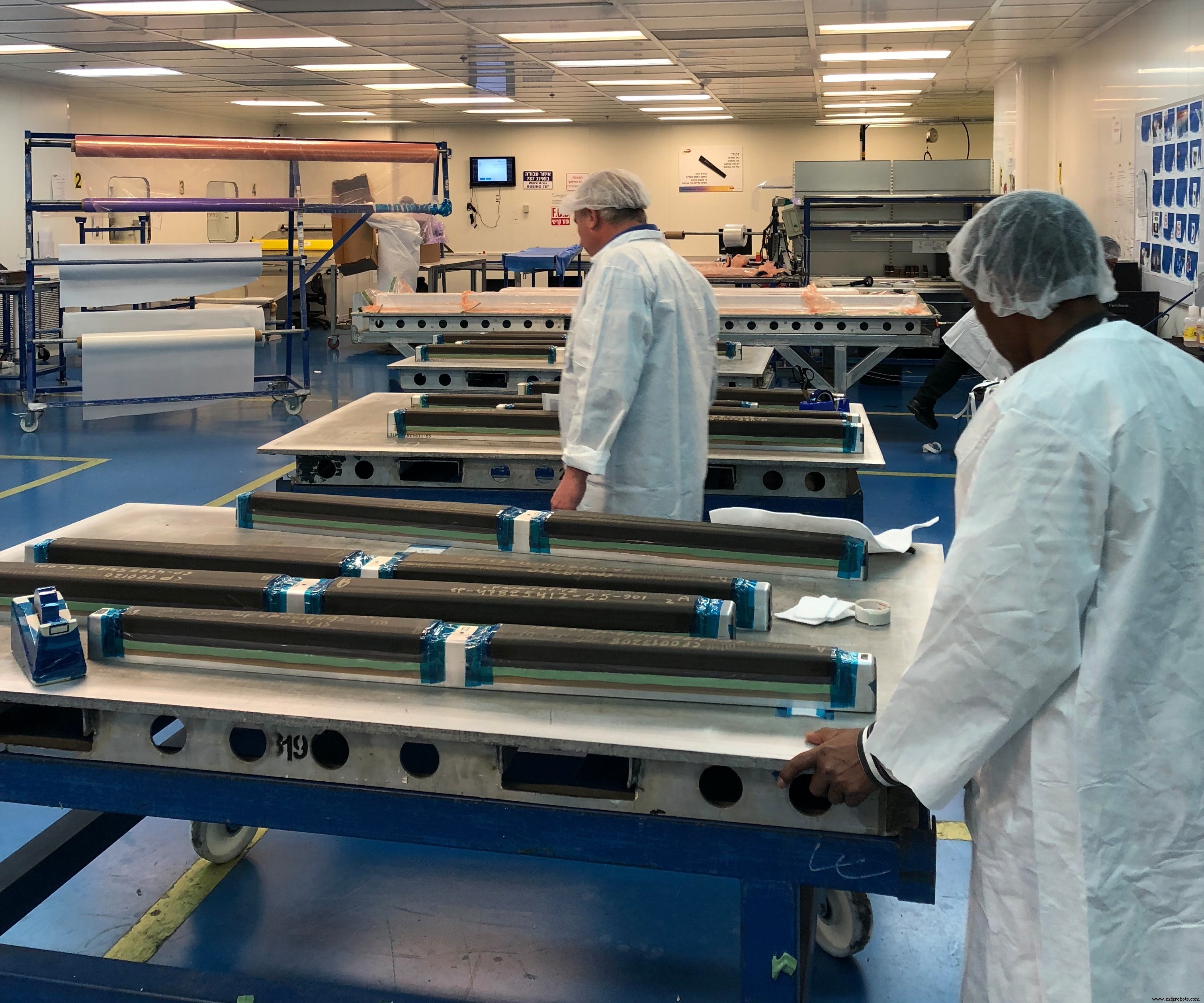
Kleinteilezuschnitt, Kitting und Layup im Reinraum von FBM für eine Vielzahl kleinerer autoklavierter Teile. Bildnachweis:CW , Sara Schwarz.
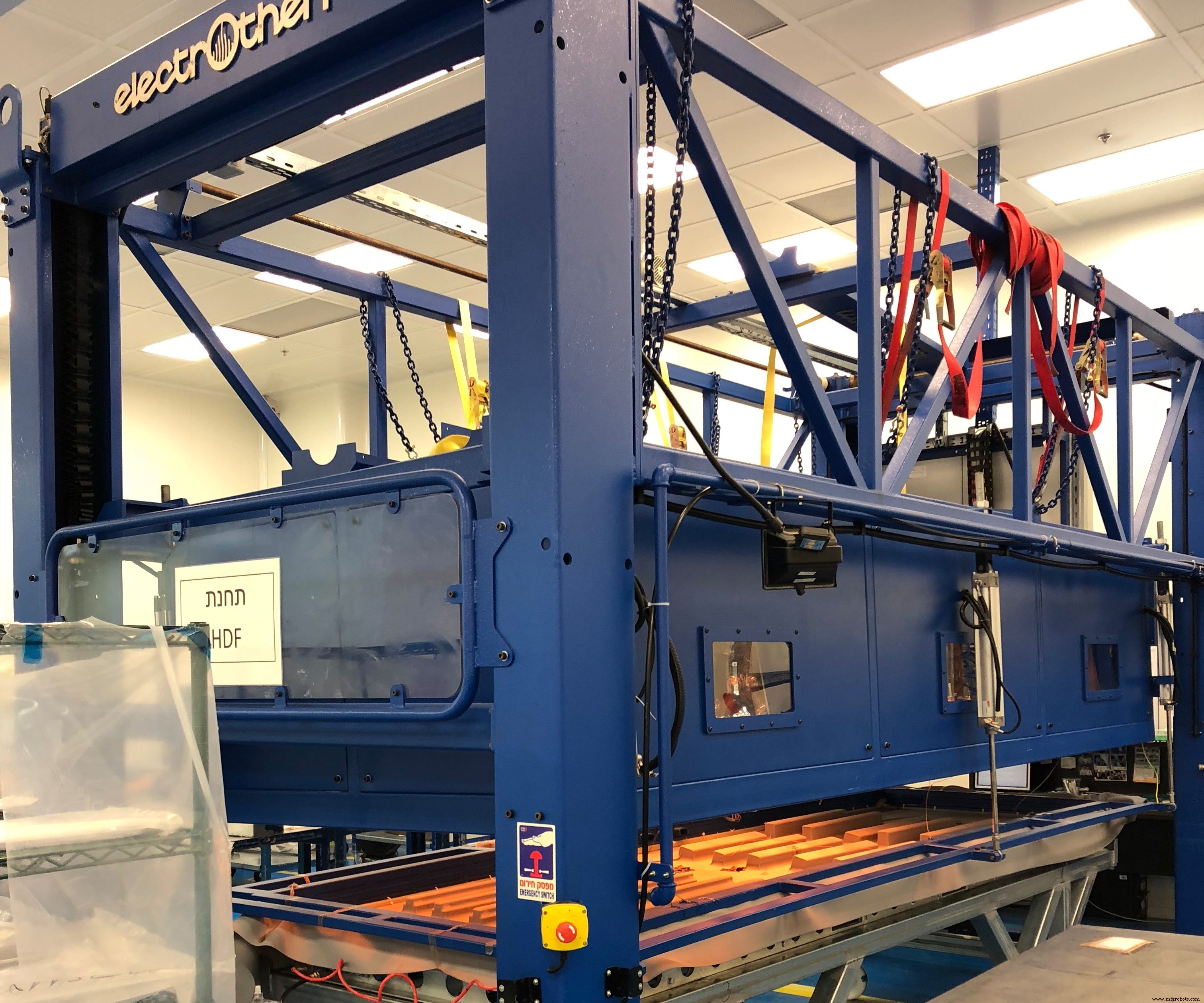
Die von der israelischen Firma Electrotherm Industry gelieferte Hot-Drape-Formmaschine von FBM macht Zwischenschritte zur Entbauchung überflüssig, formt bis zu 50 unidirektionale Lagen in einem Schuss und beschleunigt den Layup-Prozess von FBM vor dem Aushärten. Bildnachweis:CW , Sara Schwarz.
Im Reinraum dominiert ein Hot-Drape-Former (HDF) . Die von ElectroTherm Industry (Migdal HaEmek, Israel) hergestellte statische Maschine (das Unternehmen stellt auch bewegliche Versionen auf Wagen her) ist ein maßgeschneidertes Vakuumformsystem, das mit Infrarot-Heizelementen und einer Silikonkautschukmembran zum Erwärmen und Komprimieren des Verbundwerkstoffs ausgestattet ist Lagen auf den Werkzeugen vor dem Aushärten. Das HDF kann bis zu 50 gestapelte Lagen formen, sagt Poliker, ohne Zwischenschritte beim Debulking:„Wir wollten die Prozesskomplexität eliminieren, also bilden wir die Layups in einem Schuss.“ Nachdem das Prepreg im HDF erhitzt und konsolidiert wurde , wird vor dem Absacken eine Dichtung über den gesamten Layup gelegt. Die aus einem Kohlefaser-Verbundstoff hergestellte Dichtung weist eine raue Oberflächenbeschaffenheit auf. Poliker gibt keine Details zu dem proprietären Material bekannt, sagt jedoch, dass es die Härtungstemperaturen im Autoklaven von 177°C aushalten kann:„Es simuliert ein Matched-Die-Werkzeug.“ Er fügt hinzu, dass die Dornwerkzeuge bei Bedarf im eigenen Haus aufgearbeitet werden. Gepäck und Verbrauchsmaterialien werden von Airtech International (Huntington Beach, CA, USA) bereitgestellt.
2018, Elbit Cyclone, 787 Teile
Aus:„Im Dienste der Composites-Welt in Israel und den USA“
Rechts verlegen Arbeiter im Reinraum für Boeing 787-Teile Prepreg für eine Reihe von Teilen, von kleinen Clips und Rungen bis hin zu komplexen J-, I- und C-Trägern sowie mehrteiligen Bugfahrwerkstüren. Prepreg wird mit einem automatischen Stoffschneider von Assyst Bullmer (Wakefield, UK) und einer Guillotine-Maschine zum Schneiden dicker Stapel in jedem Winkel geschnitten. Der Prepreg-Gefrierschrank befindet sich neben dem Reinraum. Hulaty weist darauf hin, dass manchmal Stapel von Prepreg geschnitten, zusammengebaut und wieder in den Gefrierschrank gelegt werden. Aligned Vision (Chelmsford, MA, US) Laserprojektionssysteme, die sich im gesamten Reinraum befinden, unterstützen die Handauflegung.
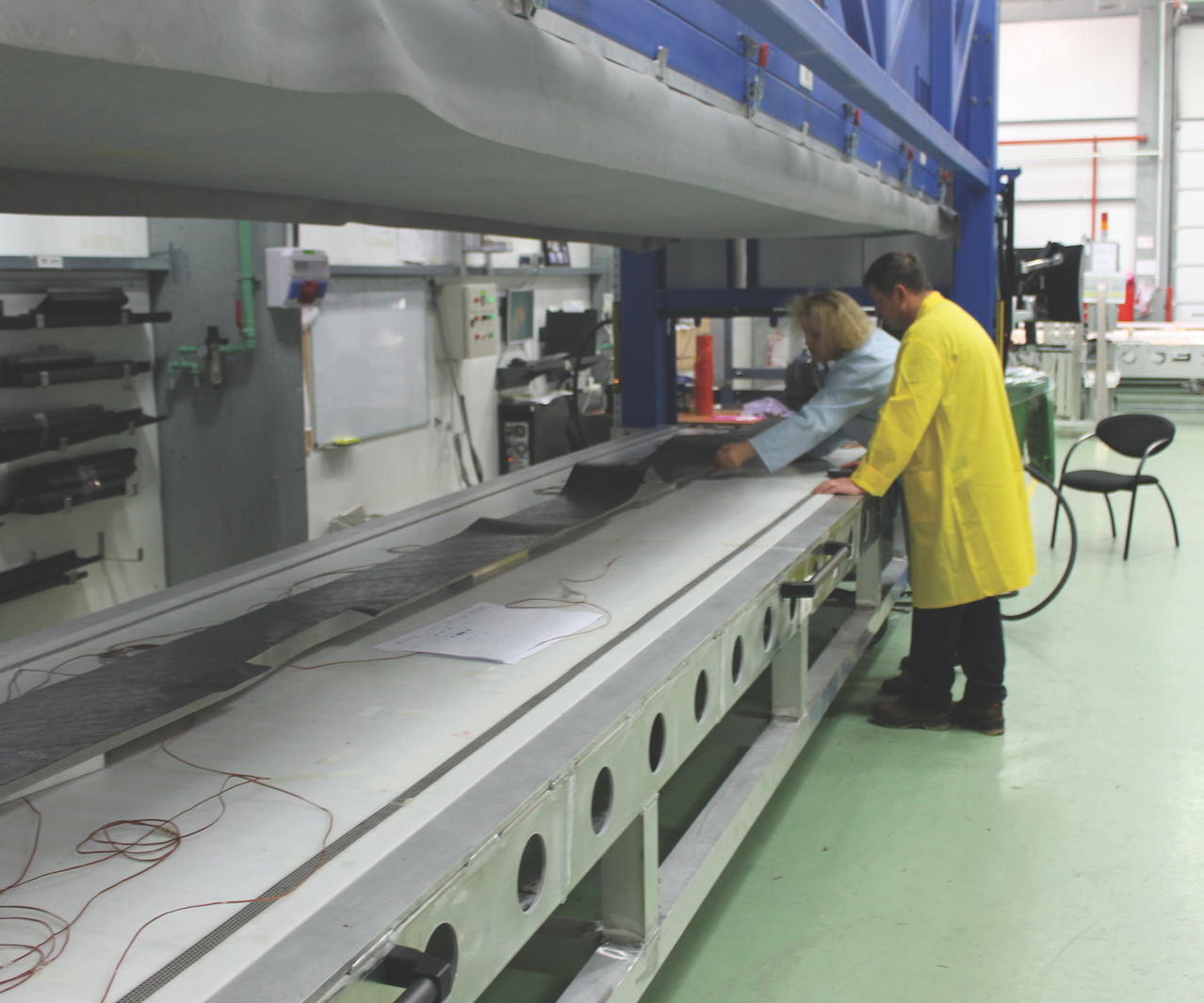
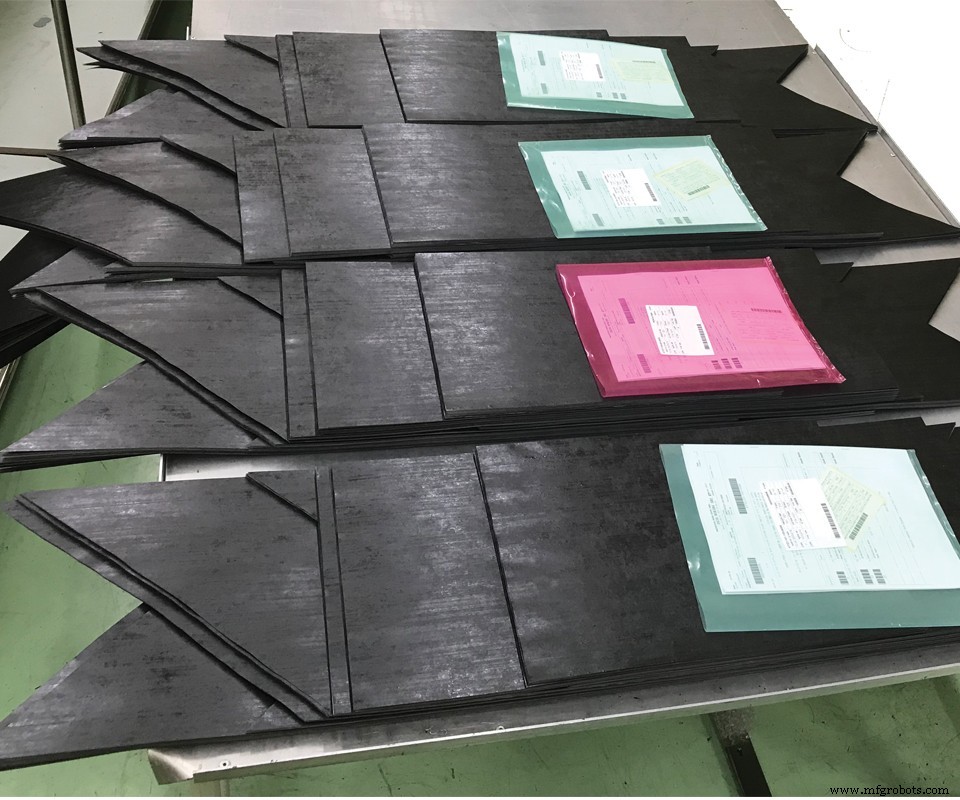
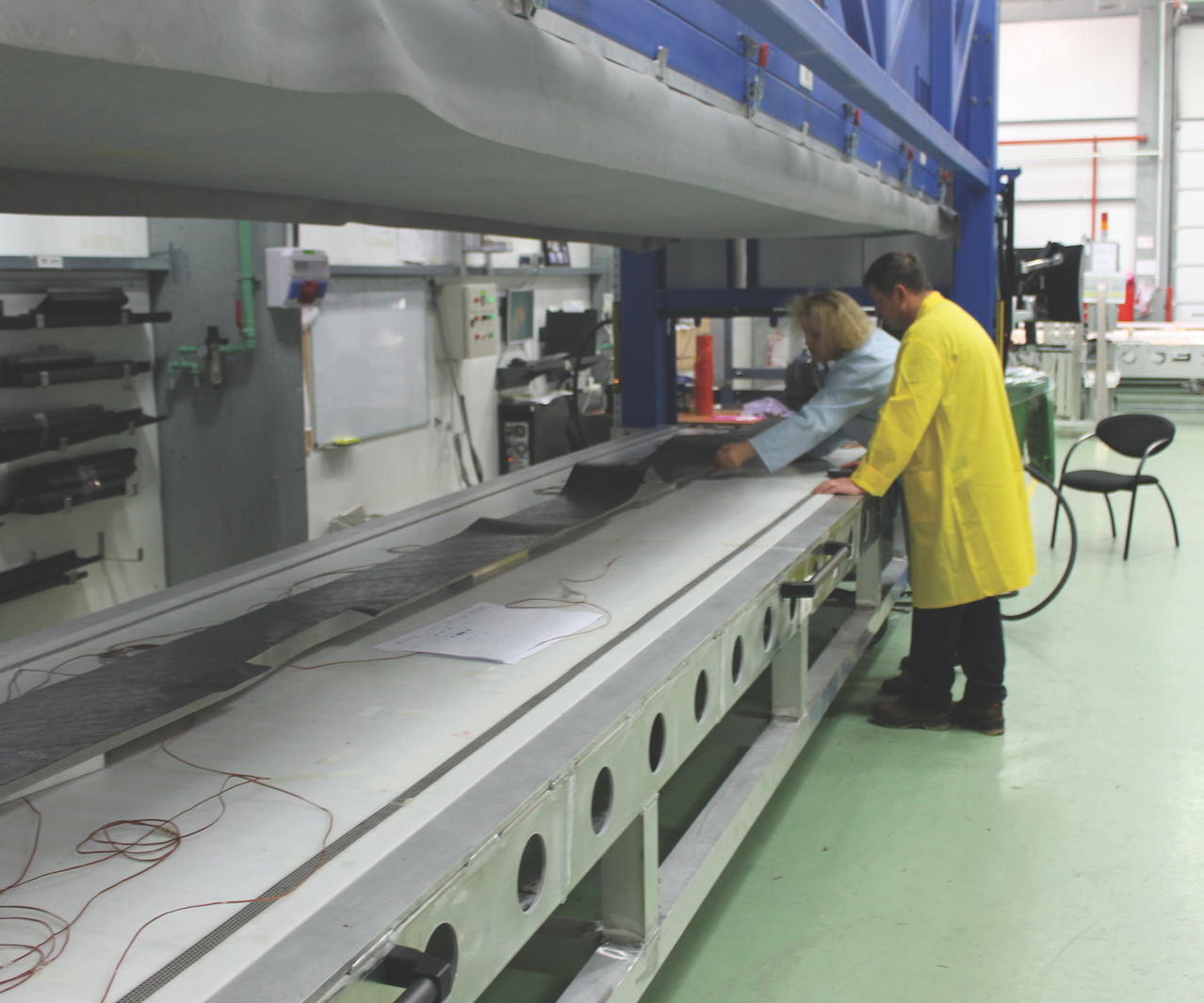
Auf männlichen Metalldornen werden Bodenträgerteile aus kohlenstofffaserverstärktem Kunststoff (CFK) aufgelegt. Hulaty beschreibt den optimierten Prozess so:„Wir legen zuerst die Prepreg-Stapel auf und bringen sie dann auf den Dorn auf. Dies spart eine Menge Zeit im Vergleich zum stückweisen Auftragen auf das Werkzeug. Die Layups werden dann mit einer von uns entwickelten CFK-Platte abgedeckt, die dazu beiträgt, eine 100-prozentige Wiederholbarkeit der Teile zu gewährleisten.“
Eine heiße Drapierung Die Maschine sitzt an der Rückwand des Reinraums und ermöglicht so das Debulking vieler Teile pro Zyklus. „Ich weiß nicht, wie man eine solche Hochgeschwindigkeitsproduktion von Prepreg-Teilen ohne Warmdrape-Umformung bewerkstelligt“, sagt Hulaty in Bezug auf Teile wie Träger und Rungen. Dabei räumt er ein, dass dieser Schritt weder der Flaschenhals noch der Autoklav ist. „Die Bearbeitung am Ende, nach dem Aushärten, ist der Engpass“, sagt er und erklärt, dass es bei langen Bodenträgerteilen schneller ist, einen einfachen Stapel aufzulegen und ihn nach dem Aushärten zu bearbeiten. „Der Autoklav ist nicht das Problem, da wir viele Teile gleichzeitig stapeln können“, fügt er hinzu. „Wir erzielen also tatsächlich eine gute Produktionsrate pro Aushärtungszyklus.“
2018, IAI, Flugzeugstruktur
Aus:„Israels Aerodefense-Eckpfeiler bereit für größere globale Reichweite“
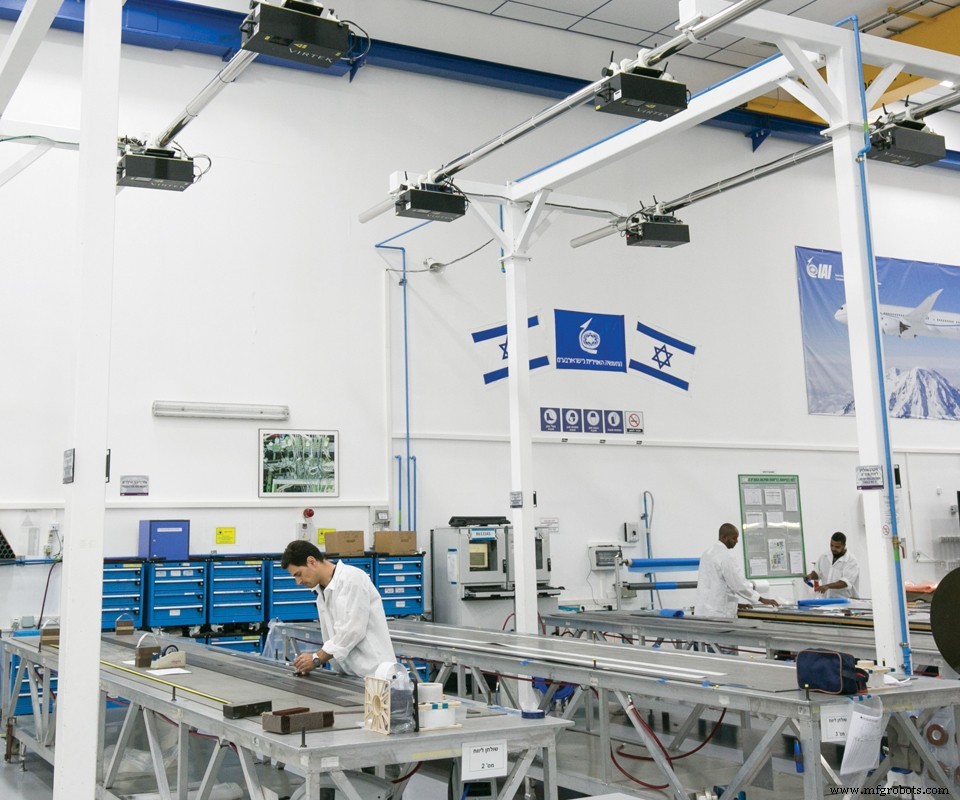
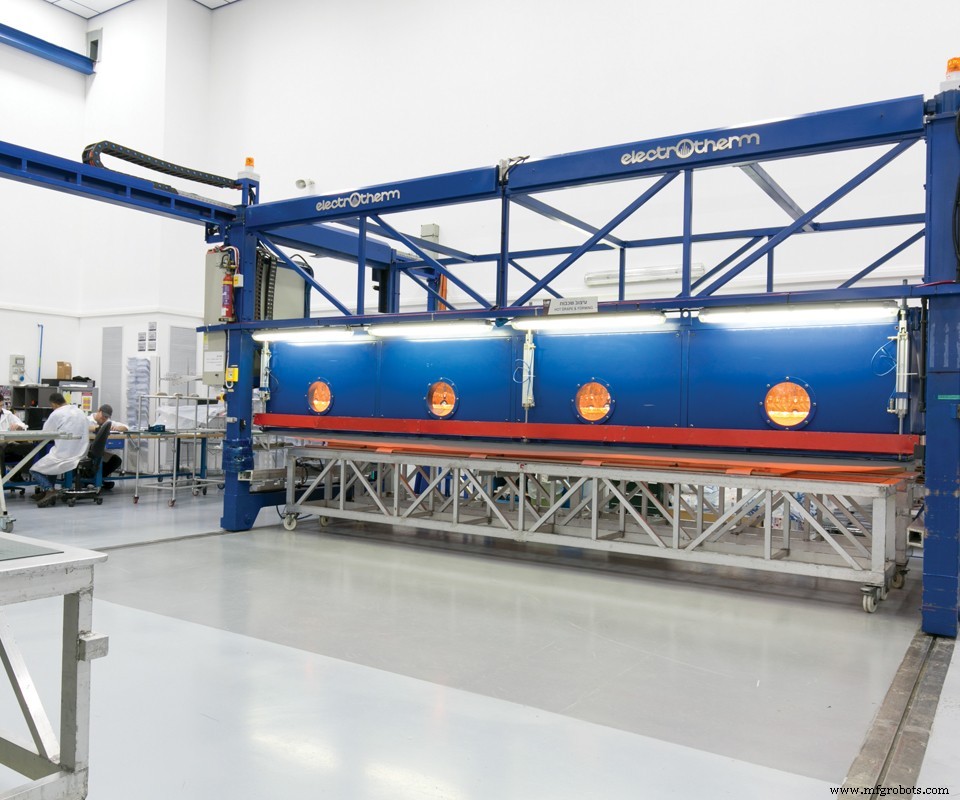
IAI verwendet eine Hot-Drape-Forming-Maschine, um dicke Prepreg-Layups en masse zu debulkieren, wodurch konventionelle Zwischenschritte zum Debulking überflüssig werden. Bildnachweis:Israel Aerospace Industries
Der Verbundwerkstoffbereich von IAI umfasst die Teilefertigung und Baugruppen für Geschäfts- und Verkehrsflugzeuge, unbemannte Luftfahrzeuge (UAVs) und Militärflugzeuge. Zu den produzierten Teilen gehören vertikale und horizontale Stabilisatoren, Seitenruder, Flügelstrukturen, Triebwerksgondeln, Bodenträger, Türeinfassungen, strukturelle Schotten, Rippen und Versteifungen, Steuerflächen, Verkleidungen und Radome. Zu den Fertigungskapazitäten zählen Prepreg-Handlaminierung und automatisiertes Tape-Layup (ATL), Heißdrapierung , Autoklaven- und Aushärtung außerhalb des Autoklaven (OOA), einschließlich Flüssigformverfahren, wie Harzinfusion und Harzspritzpressen (RTM), sowie komplexes Kleben und Zusammenbauen. Das Unternehmen entwickelt und baut auch seine eigenen Werkzeuge, verfügt über alle wichtigen Qualitätszertifizierungen für Luft- und Raumfahrt und Verbundwerkstoffe und bietet Qualitätssicherung durch umfassende zerstörungsfreie Prüfungen und Inspektionen.
- Die Produktionskapazität von IAI ist mit 10 Autoklaven, von denen sieben der Aero-Assemblys Div. und reichen in der Größe von 4,5 m Länge und 2 m Durchmesser bis zur größten mit 14 m Länge und 4,7 m Durchmesser.
- Prepreg-Layups werden vor dem Aushärten unter Verwendung einer Heißdrapierung vom Volumen befreit Maschine (6,9 x 2,7 x 3,1 m) von Electrotherm Industry (Migdal HaEmek, Israel).
2020, Strata, A350-900 Innenbordklappen
Von:„Strata liefert 100 Shipsets Innenbordklappen für A350-900“
Entworfen, um die Gesamtauftriebsfähigkeit des Flügels eines Flugzeugs zu erhöhen, ist an der Hinterkante des Flügels eine IBF [Inboard Flap] angebracht, um die Flügeloberfläche beim Start und bei der Landung zu vergrößern und die Stabilität während des Fluges zu verbessern. Strata plant, den IBF-Fertigungsprozess vollständig zu automatisieren, indem Hot-Drape-Forming (HDF) verwendet wird und computergesteuerte robotergesteuerte automatisierte Tape-Layup-(ATL)-Maschinen, die Anfang dieses Jahres die Erstteilqualifizierung (FPQ) und FAI-Design- und Qualitätsüberprüfungen erhielten.
Als Teil des Prozesses sagt das Unternehmen, dass die HDF-Maschine Kohlefaserkomponenten vorformt B. für Flugzeugteile, ermöglicht eine schnellere Produktion hochwertiger Verbundteile, und sein Infrarotstrahlungsheizsystem erweicht Kohlefasern schnell und gleichmäßig, um genaue Teile zu liefern, die frei von Spannungsfalten sind. Darüber hinaus legen die beiden ATL-Maschinen von Strata unidirektionale Prepreg-Materialien auf ein Flachbett, bevor sie zur Weiterverarbeitung in eine Form überführt werden. Laut Strata ermöglicht sein Arbeitsraum von 2,5 x 10 Metern die automatisierte Verarbeitung großer Verbundschichten, wodurch eine separate Ultraschallschneidmaschine überflüssig wird und die Bearbeitungszeiten verkürzt werden.
2020, Techni-Modul, Flügelrippe und Stringer
Aus:„Kompressions-RTM zur Herstellung zukünftiger Flugzeugstrukturen“
„Für uns ging es bei OPTICOMS auch um Automatisierung“, sagt Chevallet. Techni-Modul Engineering lieferte für das OPTICOMS-Projekt nicht nur ein C-RTM-Injektionssystem, sondern auch einen Pick-and-Place-Roboter und eine Hot-Drape-Forming (HDF) Maschine, alles integriert in eine vollautomatisierte Fertigungszelle. … „Wir haben das klassische manuelle Stapeln von Lagen mit Roboter-Pick-and-Place automatisiert“, sagt Chevallet. „Der Roboter nimmt Lagen von einem automatisierten Cutter auf und übergibt diese an das beheizte Preform-Werkzeug die auf einem Verdichtungstisch steht [Schritte 1 und 6].“ Eine Abziehschicht (blaue Folie in Schritt 6), ein Entlüfter (weißes Material in Schritt 6) und eine aufklappbare wiederverwendbare Vakuummembran (hellblau links in Schritt 2 und 6) werden aufgebracht, gefolgt von Vakuum und Erhitzen, um die Luft vorzuformen und die Luft zu entfernen Textilstapel (Heißdrapierung, HDF ) während die dünnen thermoplastischen Schleier geschmolzen werden, um eine verdichtete Vorform zu erhalten.
OPTICOMS Flügelrippe und Stringer
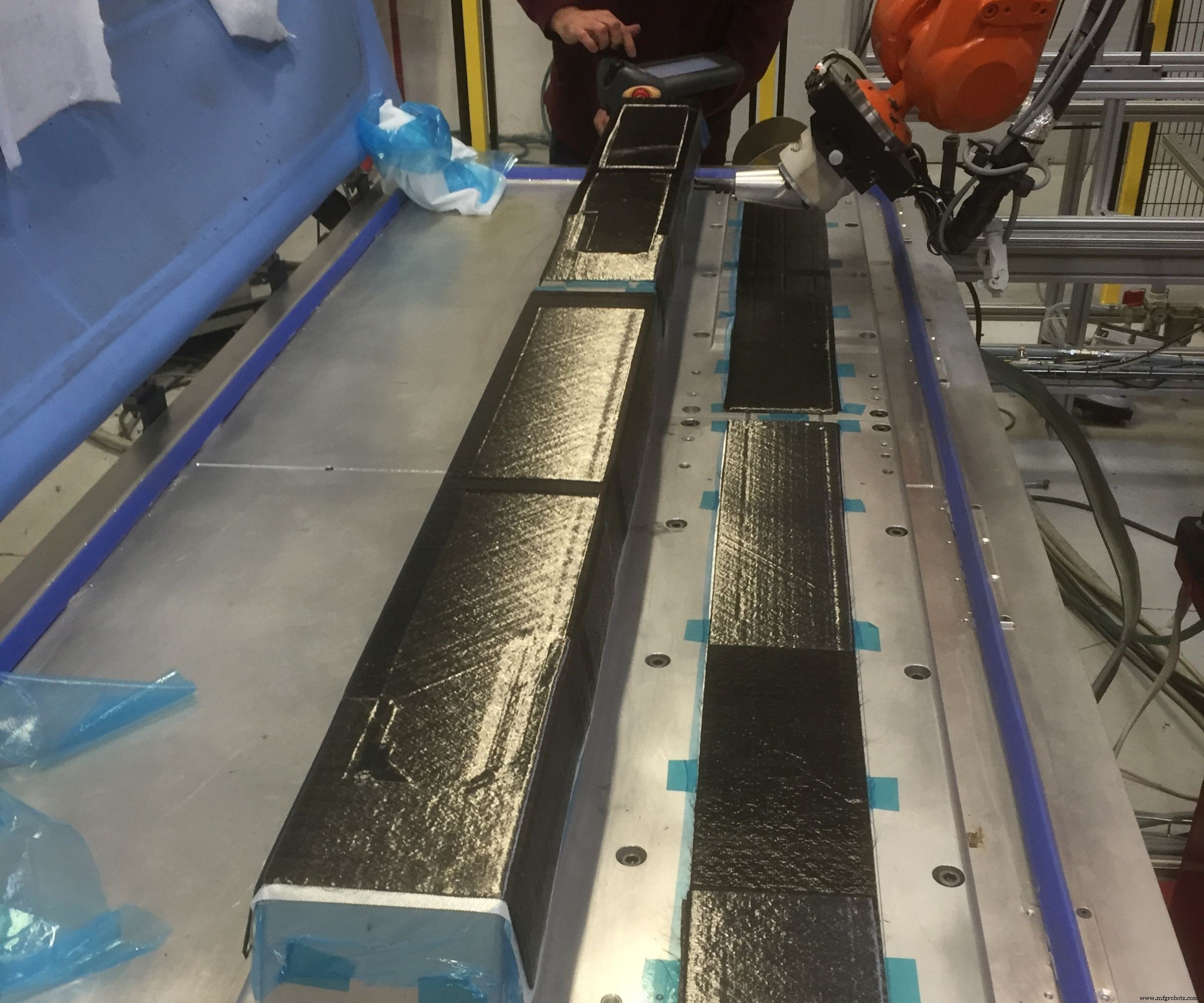
Schritt 2. Die Vorformwerkzeuge befinden sich auf einem Verdichtungstisch mit einer aufklappbaren wiederverwendbaren Vakuummembran (blau, links), die verwendet wird, um während des Auflegens alle 5-8 Lagen eine erhitzte Debulk zu vervollständigen. Bildnachweis alle Bilder:Tecni-Modul Engineering.
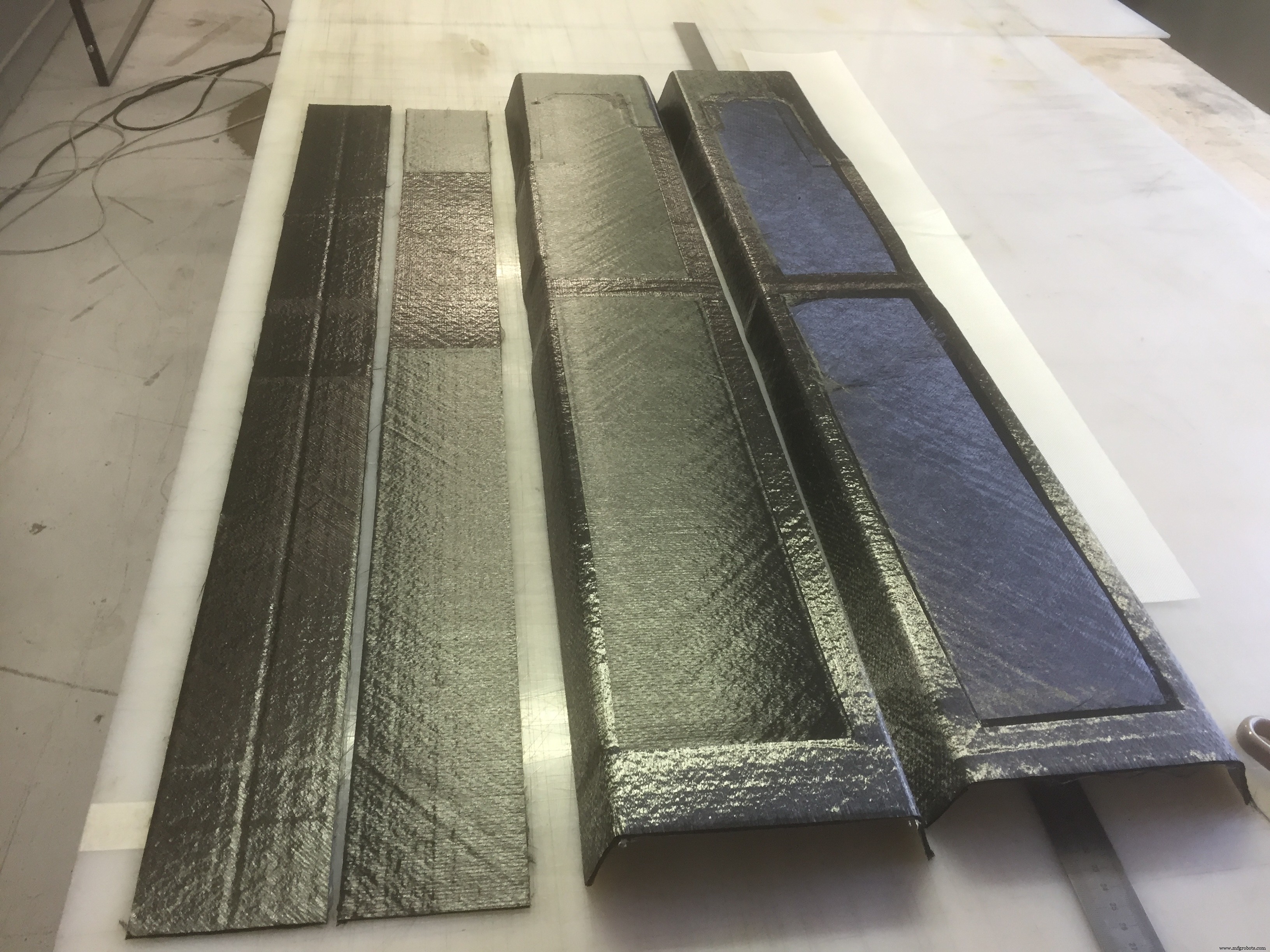
Schritt 3. Jeder Stringer-Vorformzyklus erzeugt einen C-Träger-Vorformling (zwei umfassen den I-Träger-Steg) und einen Flachflansch-Vorformling. Zwei Sätze, die für jeden I-Träger-Stringer erforderlich sind, werden hier gezeigt.
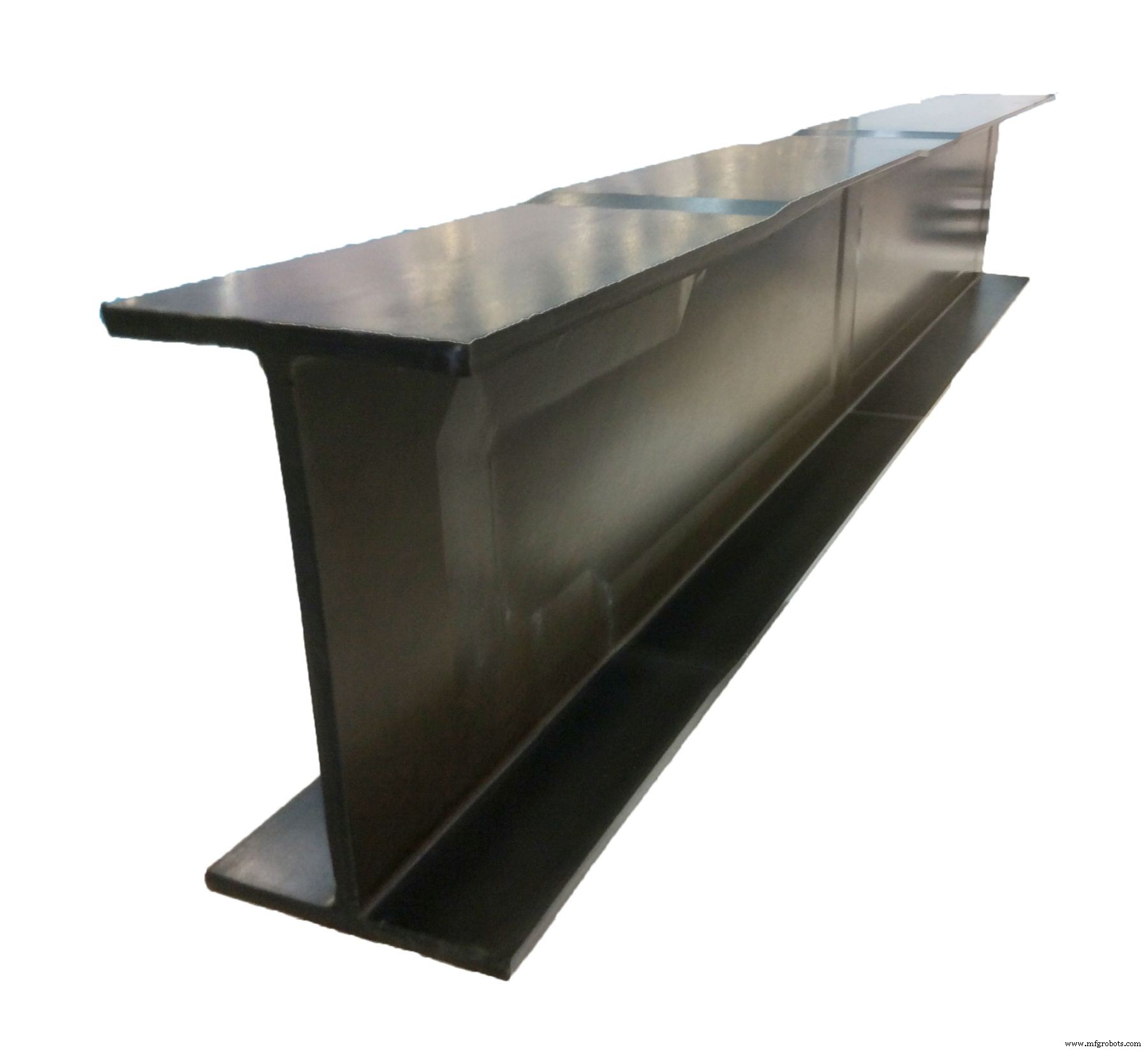
Schritt 5. I-Beam Stringer aus HDF-Preforms und RTM für das Clean Sky 2 OPTICOMS-Projekt.
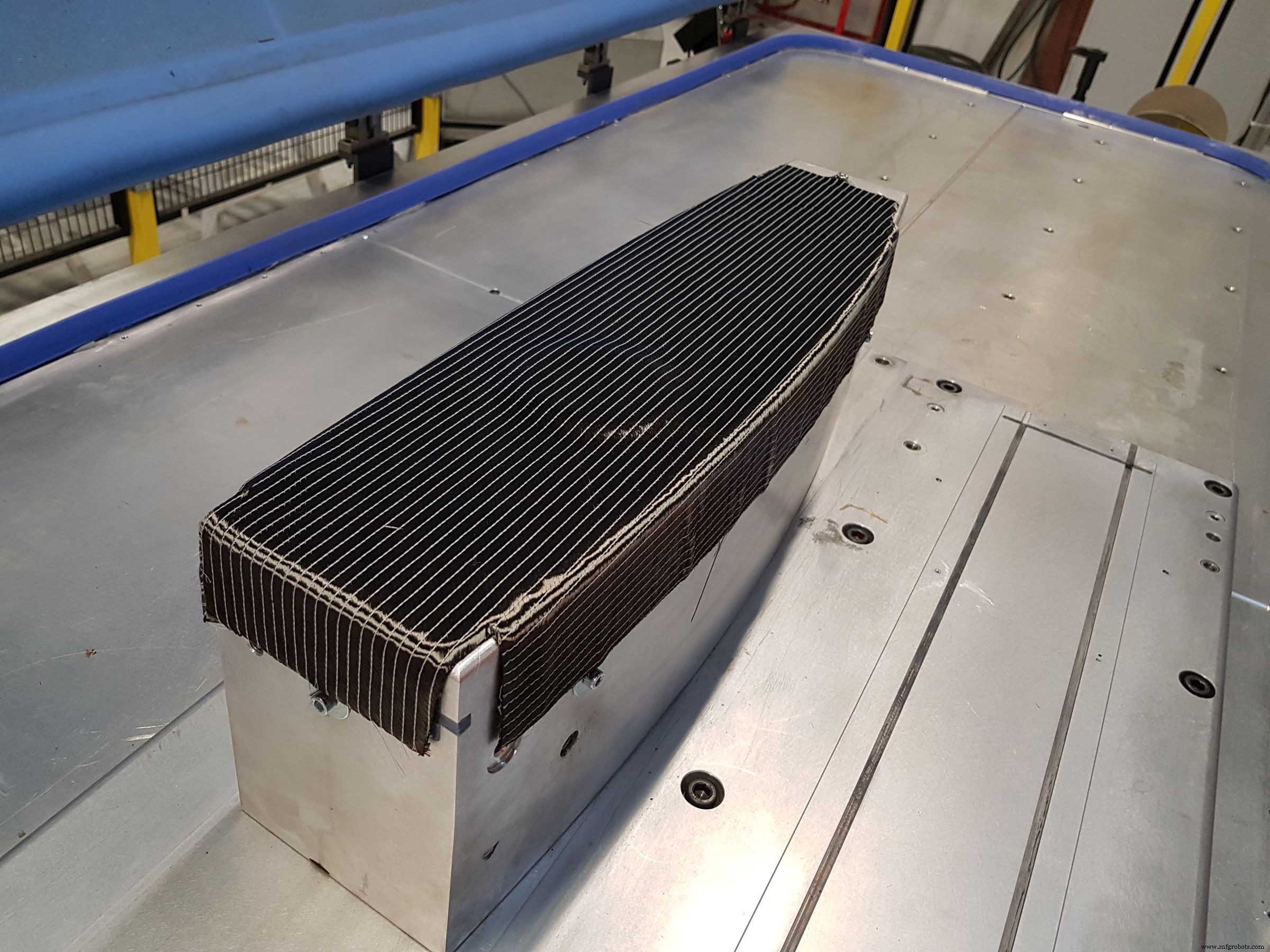
Schritt 6. Ein Roboter legt geschnittene Lagen auf das beheizte Vorformwerkzeug. Alle 5-8 Lagen wird eine erhitzte Schüttung vervollständigt, um den Vorformling zu verdichten.
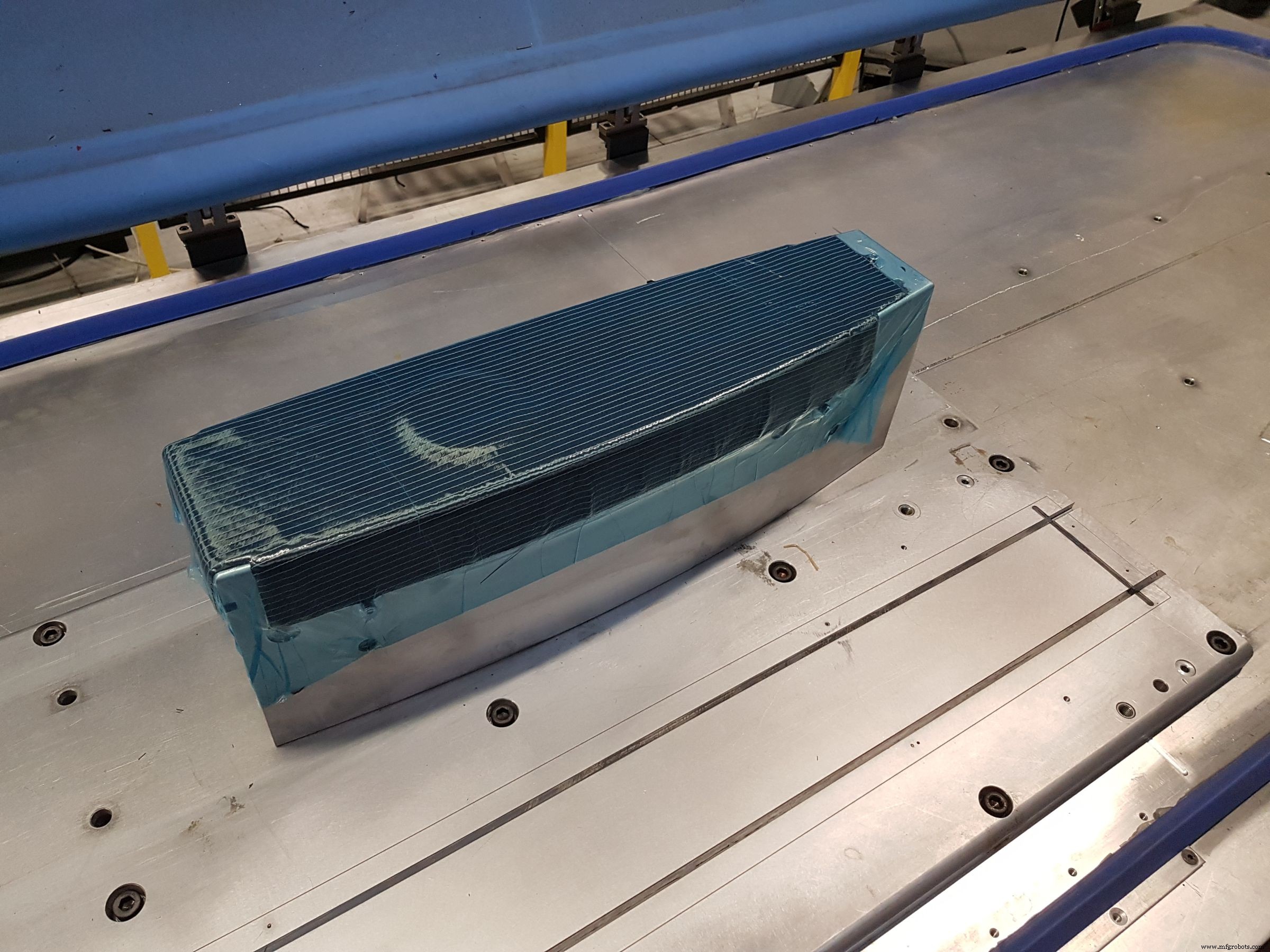
Vor dem Debulking wird eine blaue Trennfolie aufgetragen.
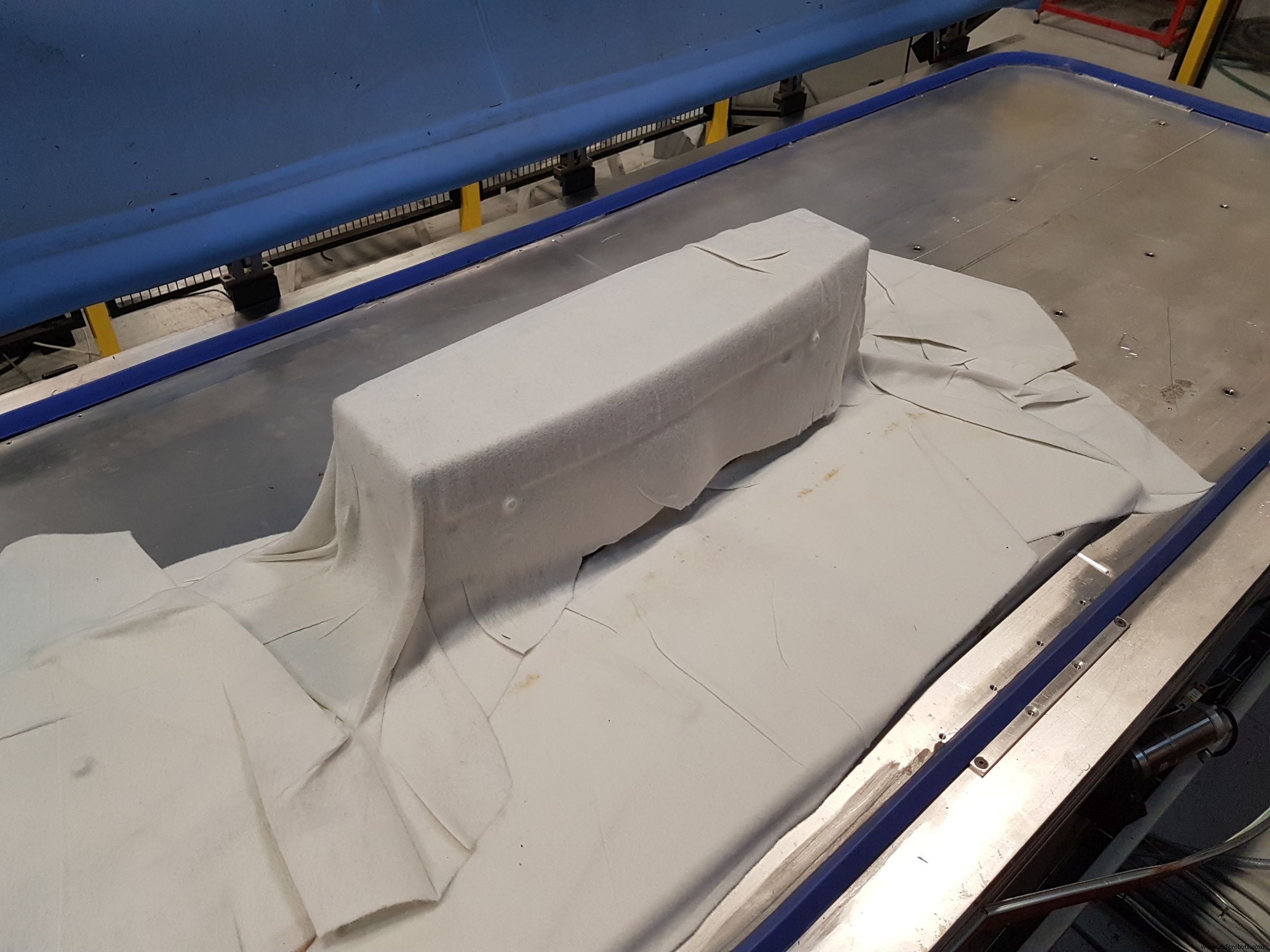
Die Entlüftung wird verwendet, um Luft über den Vorformling abzusaugen.
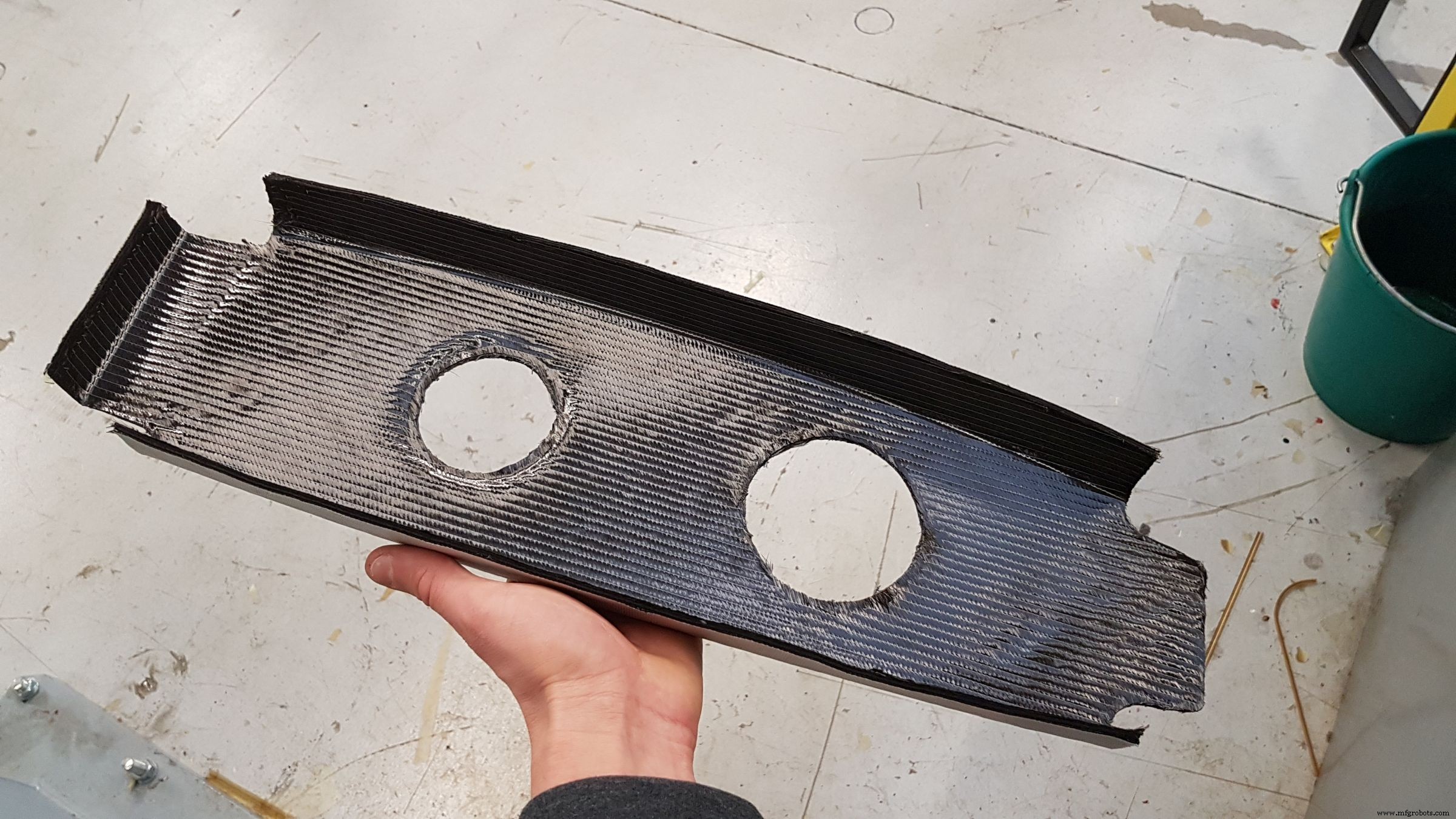
Nach dem endgültigen Debulk wird der Preform auf dem Werkzeug abgekühlt und die Ausschnitte werden besäumt.
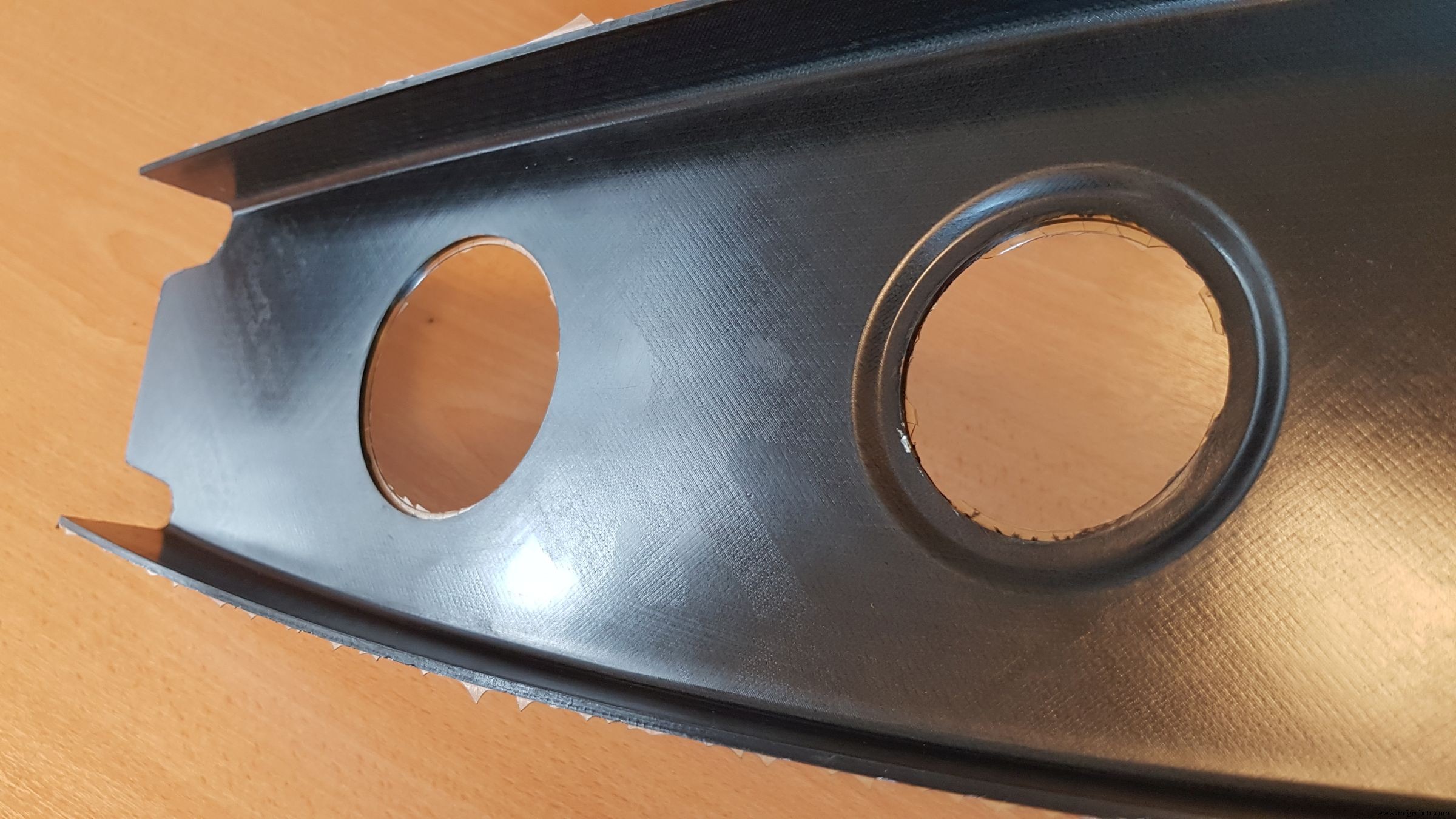
Schritt 10. Die Rippenvorform wird unter Verwendung von RTM und Epoxidharz geformt.
Vorherige Nächste„Wie viele Lagen Sie gleichzeitig verdichten können, hängt von den Materialien und der Form des Teils ab“, erklärt Chevallet. „Bei Teilen mit geringer Krümmung, wie einer Flügelhaut, könnte man möglicherweise alle 50 Lagen verdichten. Die OPTICOMS-Rippe hat jedoch 90-Grad-Winkel, und der Test-I-Träger-Stringer hat T-Form, daher müssen Sie beim Vorformen darauf achten, keine Falten in den Lagen zu bilden.“ Er fügt hinzu, dass solche komplexen Formen möglicherweise alle 5-8 Lagen verdichtet werden müssen, aber dennoch Teil eines großvolumigen, industrialisierten Prozesses sein können:Stapellagen, 2-Minuten-HDF-Verdichtung , wieder öffnen und wieder stapeln, gefolgt von wiederholten Verdichtungszyklen mit einer abschließenden Abkühlung der Preform auf dem Werkzeug vor der Übergabe an die RTM-Form.
Faser