2-Komponenten-Epoxid für eine gesteigerte Produktion von Verbund-Flugzeugstrukturen mittels RTM
Dies ist der dritte Blog aus meiner Reihe von Blogs über Technologien, die Sie auf der CAMX 2019 (23.-26. September, Anaheim, CA, USA) besuchen sollten. Hexion (Columbus, Ohio, USA) hat auf Basis seines Epoxidharzes Epikote System 600 ein Zweikomponenten-(2K)-System für RTM von Flugzeugstrukturen entwickelt. Die folgende Einführung wird erklären, warum diese Entwicklung wichtig ist. Danach gebe ich weitere Details zu diesem neuen 2K-System und dazu, wie Hexion die Anforderungen der Luftfahrt-OEMs an die in-situ-Qualitätssicherung des gemischten Harzes erfüllt. Im Folgenden bespreche ich auch das 2K-Infusions-/RTM-Epoxid von Hexion für feuerbeständige (FR) Anwendungen.
Warum 2K-Harze für RTM?
Anfang dieses Jahres habe ich über Programme beim Werkzeugspezialisten Alpex Technologies (Mils, Österreich) und der Airbus-Tochter Composites Technology Center (CTC, Stade, Deutschland) zur Herstellung von Flugzeugbauteilen aus Verbundwerkstoff mit Resin Transfer Moulding (RTM) geschrieben . Der Einsatz von RTM in der Luft- und Raumfahrt ist nicht neu. Es gibt und gab eine Vielzahl von Flugzeugteilen, die mit RTM hergestellt wurden, darunter:
- Ruder für den Gulfstream G250 Business Jet (Israel Aerospace Industries und North Coast Composites)
- Schaufeln und Lüftergehäuse für das LEAP Turbofan-Flugzeugtriebwerk (Albany Engineered Composites)
- A350 Türrahmen (Airbus Helicopters Donauworth)
- Demonstration A350-Beifahrertür (Elbit Cyclone)
- Demonstration A320 Multisparklappe (Airbus Bremen)
- Matrix Composites hat mit RTM mehr als 6.000 Komponenten für die F-22 hergestellt.
RTM in Luft- und Raumfahrtanwendungen ist jedoch traditionell ein Niederdruckverfahren mit Zykluszeiten, die in Stunden gemessen werden. Die Programme bei Alpex und CTC konzentrieren sich auf die Nutzung der Automatisierung, des schnellen Einspritzens und derZykluszeiten von 15 bis 20 Minuten angeboten von Hochdruck-RTM (HP-RTM). In meinem Artikel „HP-RTM für die Serienfertigung kostengünstiger CFK-Flugzeugstrukturen“ habe ich die Frage des Einsatzes von 2-Komponenten (2K) Epoxidharzen gegenüber der aktuellen Norm der Verwendung vorgemischter 1-Komponenten (1K) Systeme diskutiert:
„Schiller [Jan Schiller, CTC-Projektleiter für Produktionssysteme und Hauptansprechpartner für RTM-Technologien] stellt fest, dass alle bisherigen RTM Flugzeugstrukturen haben nur 1K-Systeme verwendet Mischung durch den Lieferanten, der dann die Mischung zertifiziert und die Verantwortung dafür trägt, dass das Harz die Qualifikationsanforderungen erfüllt. „Jetzt ziehen wir 2K-Systeme in Betracht, aber die Herausforderung besteht darin, die Mischqualität sicherzustellen ," er erklärt. Vorgemischte 1K-Systeme erfordern einen kalten Versand und eine kalte Lagerung, um eine Reaktion bis zur Teileverarbeitung zu verhindern. Vorteile von 2K-Systemen sind daher der Wegfall dieser Kosten sowie eine höhere Reaktivität für eine schnellere Verarbeitung.“
„Ein Problem besteht jedoch darin, dass die Qualitätssicherung (QS) vom Harzlieferanten auf den Teilehersteller übergeht. „Diese QA erfordert die Erkennung des Mischungsverhältnisses und die gemischte Harzqualität . Beides wird für die Airbus-Qualifizierung eines neuen Materials benötigt. Das bedeutet also Messungen der beiden Komponenten kurz vor dem Mischen und des Harzes nach dem Mischen . Heute haben wir nur noch Sensoren vor dem Mischkopf, die anzeigen, wie viel Harz und wie viel Härter in die Mischung dosiert wird. Das reicht nicht für eine Qualifikation.“
Hexion (Columus, Ohio, USA), ein führendes Unternehmen in der Entwicklung von schnellhärtenden Epoxiden für HP-RTM in Automobil-Verbundwerkstoffen (siehe „HP-RTM auf dem Vormarsch“), gab im März 2019 bekannt, dass es ein 2K-System für RTM von . entwickelt hat Flugzeugstrukturen auf Basis des Epoxidharzes Epikote System 600. Ich habe Jean Rivière, den Leiter des Epoxy Global Aerospace Segments von Hexion, interviewt, um mehr über ihr 2K-System für die Luft- und Raumfahrt zu erfahren und wie sie diese Nachfrage nach in-situ-QA des gemischten Harzes erfüllen.
Überwindung der Einschränkungen von 1K-Systemen
„Genau wie beim Prepreg müssen die 1K-Systeme für RTM und Infusion in der Luft- und Raumfahrt kühl gehalten werden und eine begrenzte Haltbarkeit haben“, sagt Rivière. „Durch die Verwendung eines 2-Komponenten (2K) Epoxidsystems beseitigen Sie diese Einschränkungen. Wir haben 2K und hochreaktive Epoxidharze gesehen, die bei der Herstellung von Windflügeln und Automobilstrukturen verwendet wurden. Warum also nicht in der Luft- und Raumfahrt?“
Rivière erklärt, dass Hexion nach Gesprächen mit vielen Kunden das Hauptanliegen verstanden hat – Sie benötigen zu jedem Zeitpunkt eine Bestätigung, dass das Mischungsverhältnis korrekt ist, bevor Sie in das Werkzeug spritzen. Ohne dies besteht für den Teilehersteller ein inakzeptables Risiko“, stellt er fest. Er fügt hinzu, dass es zuvor keine Nachfrage nach Produktionsvolumen für Windflügel und Automobile gegeben habe. Jetzt wollen Airbus und Boeing jedoch die aktuellen Produktionsraten übertreffen und gleichzeitig mehr Verbundteile pro Flugzeug anstreben. „Jetzt besteht die Notwendigkeit, weg vom Prepreg-Layup und hin zu einem 2K-Epoxid für RTM oder Infusion in der Luft- und Raumfahrt“, sagt Rivière.
In den folgenden Lieferkettendiagrammen beseitigt die 2K-Technologie nicht nur die Schritte der Kühllagerung und des Wiedererwärmens, sondern hebt auch die Beschränkungen der Harzbehältergröße für den Versand auf. „Man muss die vorgemischte Harzmasse auf 20 Liter beschränken und diese Fässer auf sehr niedriger Temperatur halten“, sagt Rivière, „sonst kann das Harz anfangen zu reagieren. Für ein 2K-System können standardmäßige 200-Liter-Fässer ohne Einschränkungen bei niedrigen Temperaturen versandt werden. Es besteht also weniger Risiko, keine starke Kühlung und weniger Vorsichtsmaßnahmen.“
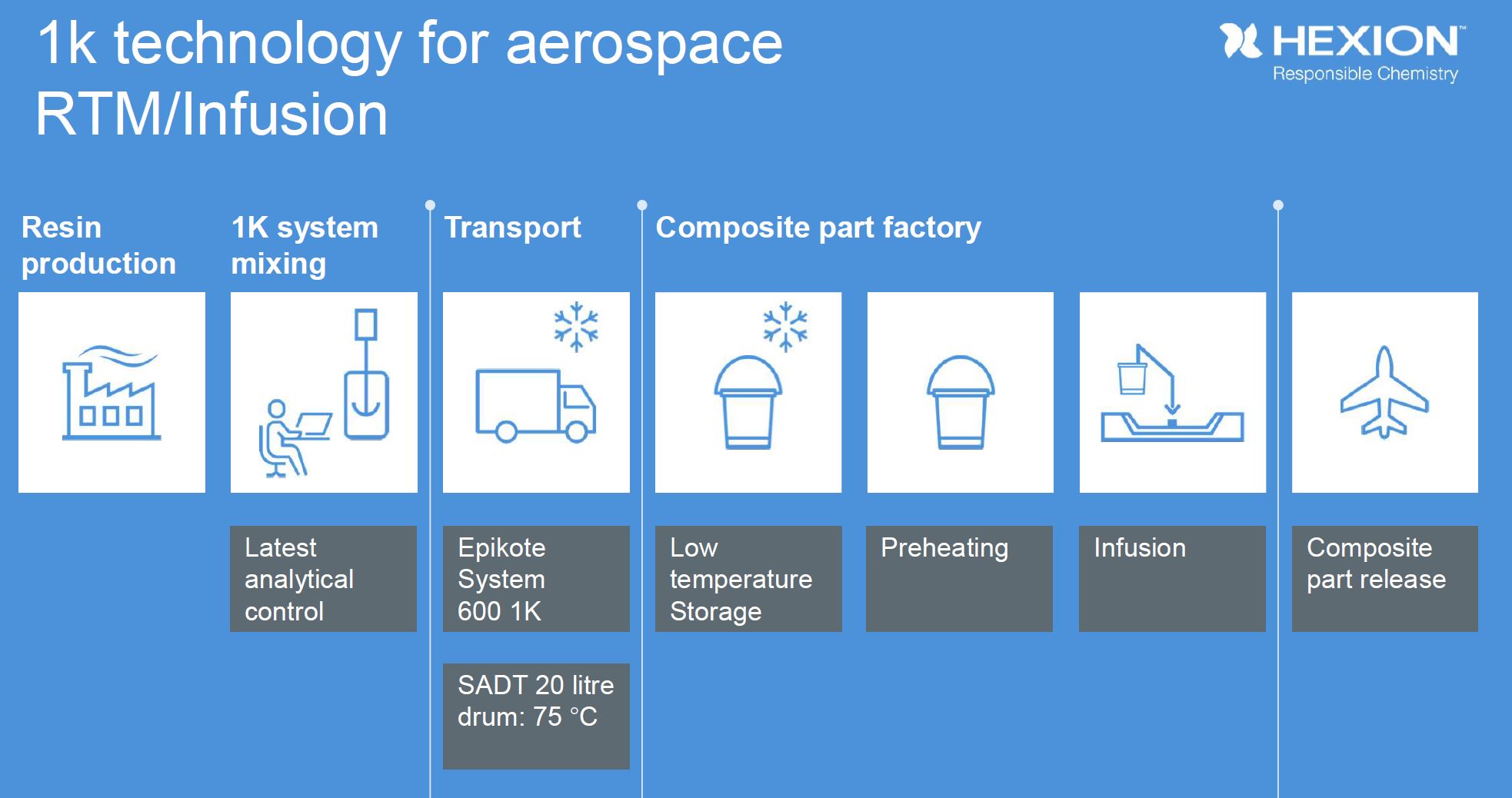
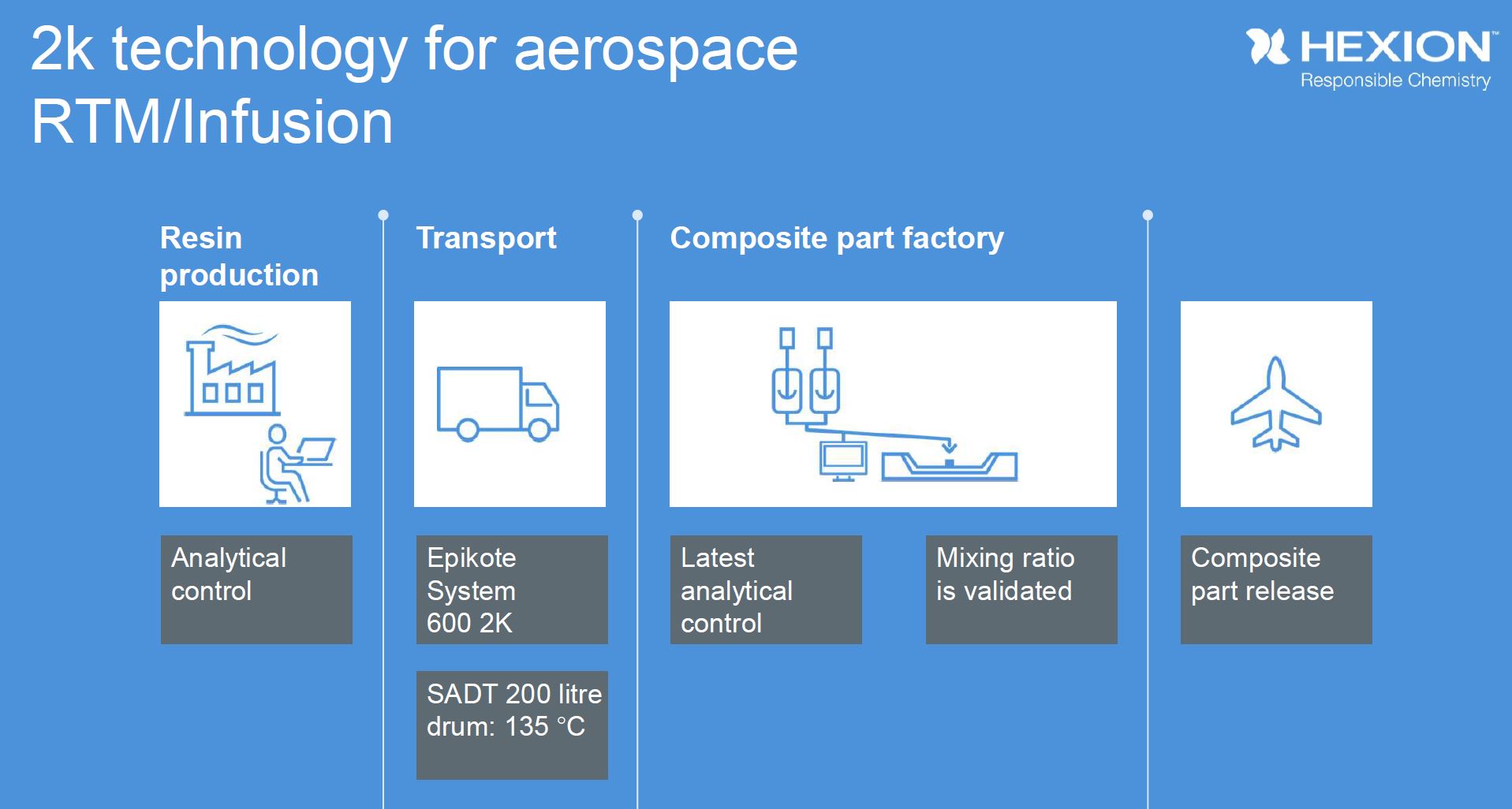
Die obigen Lieferketten zeigen, wie sich die analytische Kontrolle verändert. Während für 1K-Harzsysteme nur eine anfängliche Kontrolle am Herstellungsort durchgeführt wird, wird die Kontrolle für das 2K-System an mehreren Kontrollpunkten implementiert. Neben der Kontrolle der A- und B-Komponenten während der werkseigenen Produktion wird das A:B-Mischverhältnis auch digital in der Misch-, Dosier- und Dosieranlage (MMD) und noch einmal kurz vor der Harzinjektion in die Form gesteuert. QUELLE | Hexion.
Analytische Kontrolle
Bei der Entwicklung dieser 2K-Technologie arbeitete Hexion mit Hübers (Bocholt, Deutschland), einem Hersteller von Misch-, Dosier- und Dosiergeräten (MMD), und Composyst (Hurlach, Deutschland) zusammen, das eine exklusive Lizenz für das von Airbus patentierte Vacuum Assisted Process ( VAP) zur Infusion. Hübers hat einen guten Ruf für leistungsstarke MMD-Systeme, die bei der Herstellung von elektrischen und elektronischen Komponenten verwendet werden (z. B. Gießharz und imprägnierte Komponenten für Transformatoren usw.), während Composyst Experte für Harzinjektion und -infusion für Airbus-Anwendungen ist und somit , versteht, was der Flugzeug-OEM in Bezug auf die Verarbeitung und Qualitätssicherung (QS) von Mischharzen sucht.
„Die analytische Kontrolle kommt ins Spiel, nachdem die A- und B-Komponenten des Epoxids von den Hübers-Geräten präzise gemischt wurden und sich auf das Einbringen in die Form vorbereiten“, erklärt Rivière. Die schwarzen Schläuche zwischen dem Hübers MMD-System und dem vakuumverpackten VAP-Infusionssetup im Bild unten sind eine Schlüsselkomponente dieses analytischen Kontrollsystems. „Hier haben wir ein Analysegerät, das das Mischungsverhältnis in Echtzeit kontrolliert“, sagt Rivière. „Wir haben alle 12 Sekunden eine Mischungsverhältnismessung demonstriert, aber auch eine häufigere Messung ist möglich. Tatsächlich ermöglicht die Technologie eine kontinuierliche Kontrolle des Mischungsverhältnisses, die gemeldet und protokolliert wird.“
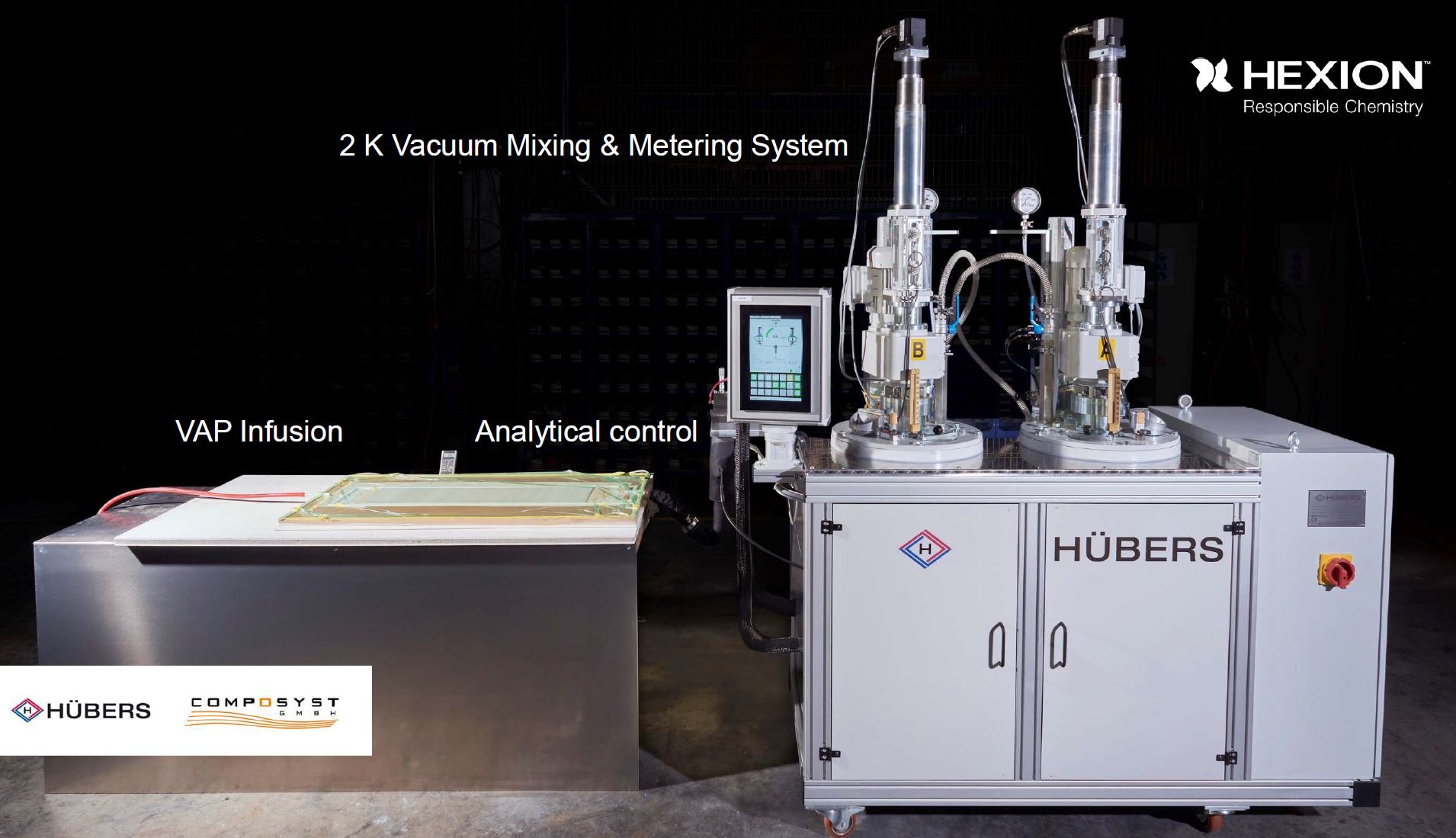
Beachten Sie die schwarzen Schläuche zwischen dem Hübers MMD-Gerät und dem VAP-Infusionssetup, bei dem Hexion eine Inline-Messung des Harzmischungsverhältnisses vor der Injektion entwickelt hat.Quelle | Hexion
„Bei diesem System“, fährt er fort, „gibt es eine doppelte Kontrolle:die normale Kontrolle in der MMD-Einheit und unsere analytische Kontrolle vor der Injektion obendrauf. Zunächst weist Rivière darauf hin, dass die MMD-Maschinen von Hübers für ihre Präzision und Genauigkeit bekannt sind. „Sie haben ein doppeltes Pumpsystem für die beiden Komponenten und müssen die Genauigkeit von Volumen und Temperatur sowie das Mischungsverhältnis für die Anwendungen, in die sie liefern, aufrechterhalten. Unser System fügt dann nach dem Mischen und kurz vor der Injektion eine zweite Messung hinzu, bei der Sie Ziele für Alarme festlegen können.“ Sollte das gemessene Mischungsverhältnis die Zielvorgaben nicht erfüllen und den Alarm auslösen, evakuiert das System das gemischte Harz in einen separaten Behälter und umgeht die Form, sodass es nicht ist in den infundierten Teil eingeführt. „Dann ist es möglich, den Prozess wiederherzustellen und die Injektion fortzusetzen“, bemerkt Rivière.
Er sagt, dass das analytische Kontrollsystem nach dem Mischen und Voreinspritzen von Hexion eine unabhängige Aufzeichnung für die Rückverfolgbarkeit bietet und je nach Kundenwunsch auch in die MMD-Einheit integriert werden kann. Rivière weist darauf hin, dass die Hübers MMD-Einheit auch eine gründliche Entgasung des Harzes durchführt, die von der Elektronikindustrie benötigt wird, wo keine Hohlräume oder Porositäten in den Anwendungskomponenten auftreten dürfen. „Dieses System bietet auch eine tragbare Kontrolle des Drucks auf die Form, indem es den Harzfluss auf hohe oder niedrige Niveaus regelt“, betont er. „Mit dieser Art der Steuerung erreichen Sie eine sehr gute Imprägnierung und können zudem die Infusionszeit verkürzen und gleichzeitig die Qualitätsanforderungen der Luft- und Raumfahrt hinsichtlich Porosität und Faservolumen erfüllen.“
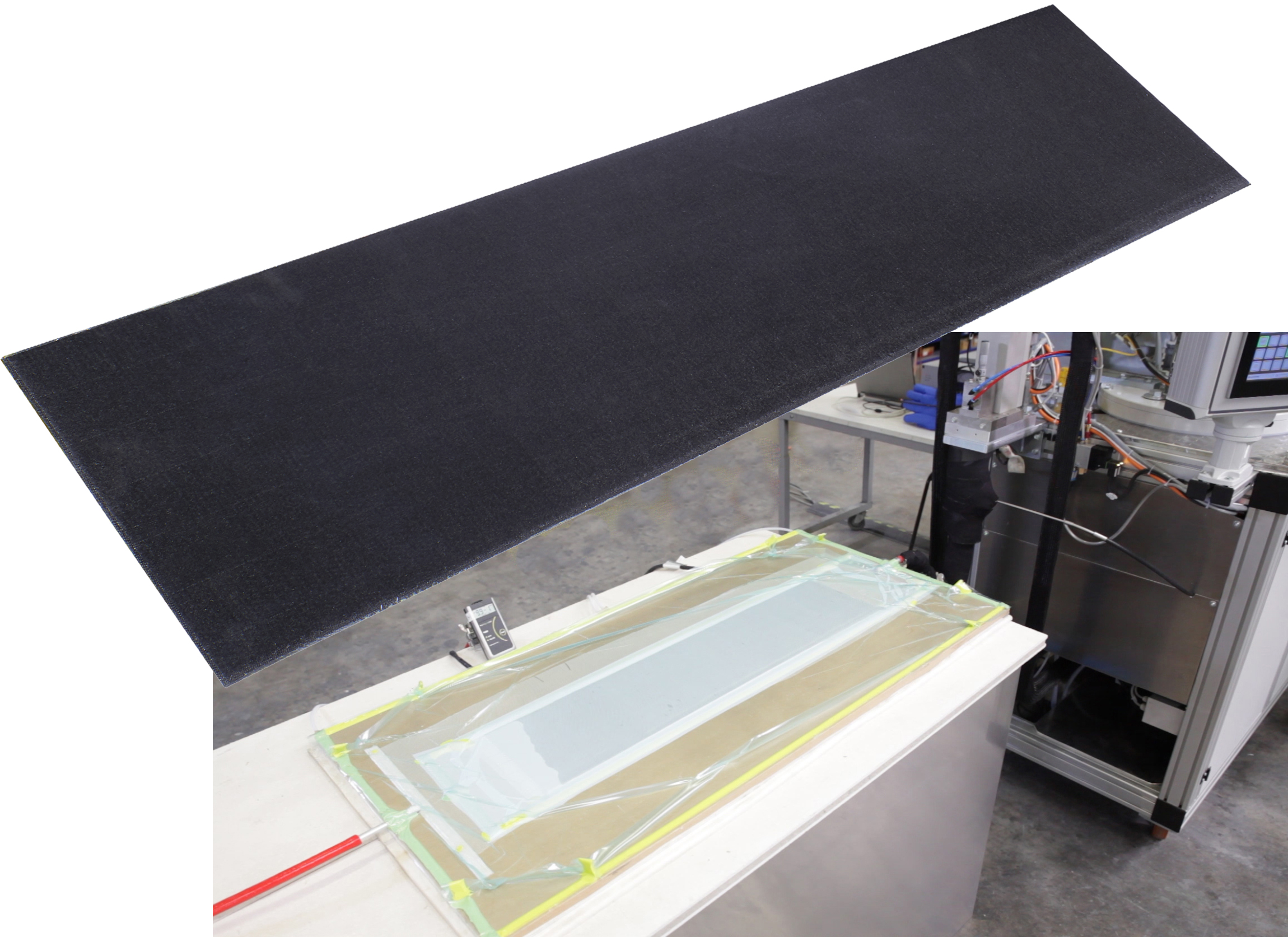
Fotos, die den Infusionsaufbau mit Hübers MMD-Geräten und Hexion 2K-Analysekontrolle und einem 2 Zentimeter dicken Kohlefaser-UD-Laminat zeigen, das mit diesem Aufbau hergestellt wurde und mehr als 60 % Faservolumen erreicht. QUELLE | Hexion
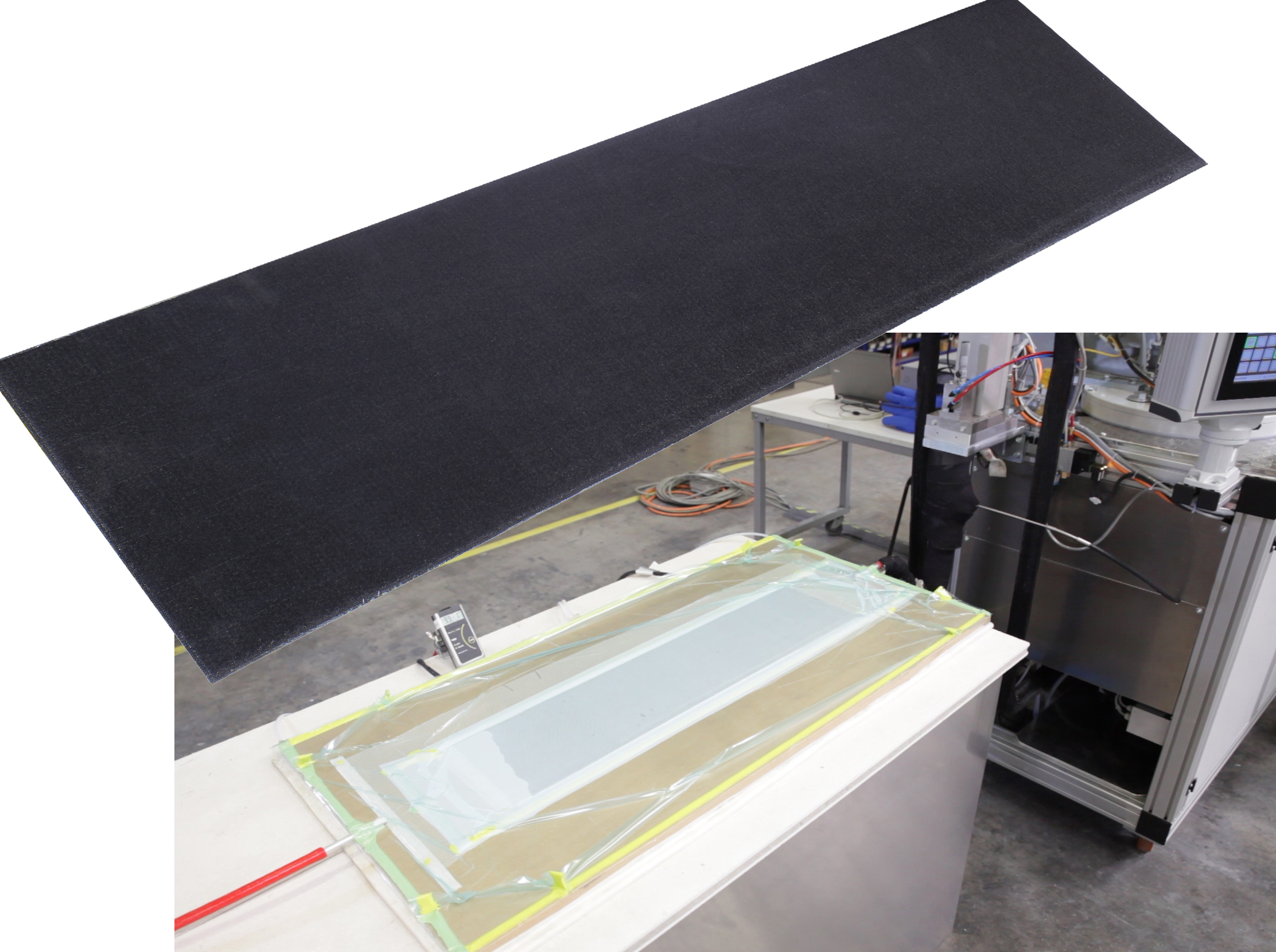
Besseres Verarbeitungsfenster
„Da das Mischen mit einem statischen Mischer und in kurzer Zeit direkt vor der Injektion erfolgt, bietet die Harzmischung eine längere Topfzeit (bis zu 40% im Vergleich zu 1K)“, bemerkt Rivière . Dies bietet ein besseres Verarbeitungsfenster und wir haben dicke Kohlefaserlaminate mit 60 % Faservolumen hergestellt. Die mechanische Leistung der 2K- und 1K-Systeme ist gleich, da die Chemie gleich ist. Wir glauben, dass dies ein zuverlässigerer Prozess ist und der vollständige Wert entsteht, wenn Sie die Mischsteuerung mit dem Harzinjektions-Setup verbinden.“
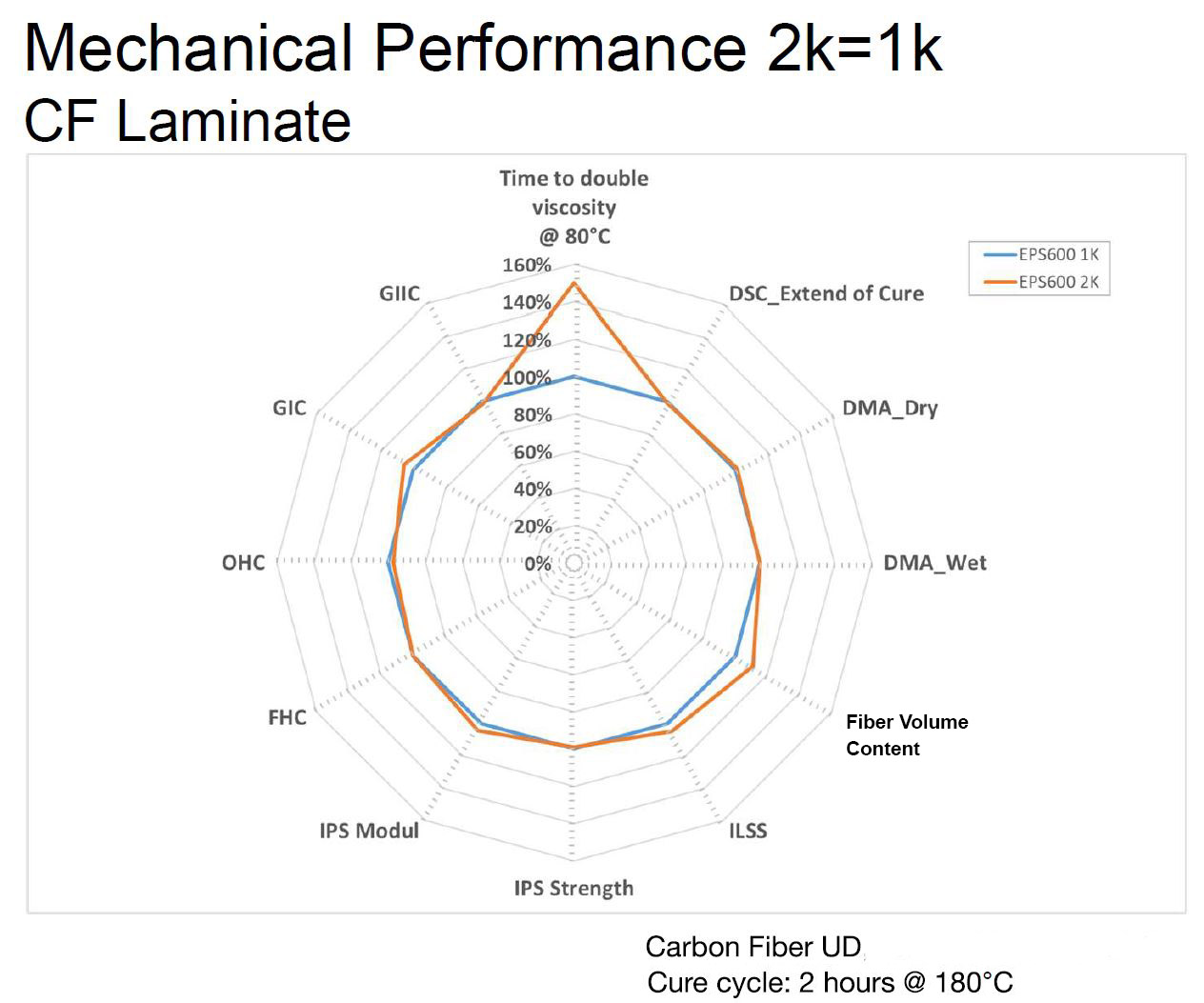
QUELLE | Hexion
Hexion wird im CAMX-Theater auf der Ausstellungsfläche detaillierte Informationen sowohl zu seinem 2K Epikote 600-System für RTM als auch zu seinem EPON FlameX-Epoxid zur Erfüllung der Anforderungen bezüglich Feuer, Rauch und Toxizität (FST) von Flugzeugen (siehe unten) präsentieren:
- Neuartige 2K-Technologie für die Epoxid-Luft- und Raumfahrtherstellung
Dienstag, 24. September — 11:00 - 11:25 Uhr - FlameX Epoxidsysteme für Brandschutzanwendungen
Dienstag, 24. September — 11:30 – 11:55 Uhr
Weitere Informationen erhalten Sie auch am Hexion-Stand Y24.
EPON FlameX Epoxy zur Infusion/RTM von feuerbeständigen Verbundwerkstoffen
Hexion hat auch ein 2-Komponenten-Epoxid für die Infusion/RTM von Teilen entwickelt, die die Anforderungen an Feuerbeständigkeit (FR) und Flamme, Rauch, Toxizität (FST) erfüllen müssen. Mit dem Ziel, phenolische Prepregs durch flüssiges Epoxidharz zu ersetzen, sind die Treiber dieser Entwicklung:
- Erhöhte Produktionsraten
- REACH-Vorschriften für halogenfreie, nicht-phenolische Systeme
- Stärkere, zähere Harze im Vergleich zu spröden Phenolen
- Konkurrenzfähig mit Phenolen, aber viel billiger als Thermoplaste.
Das EPON FlameX-System von Hexion verwendet keine Halogen- oder Partikelzusätze, um Feuerbeständigkeit zu erreichen, sondern baut diese Leistung stattdessen in das molekulare Rückgrat des Harzes ein. Während der Infusion findet keine Partikelfilterung statt. Das Harz lässt sich mit einer Viskosität von 250 cps bei 60-70 °C (140-158 °F) gut infundieren und härtet in 1,5 Stunden bei 150 °C (302 °F) aus. Für maximale strukturelle Eigenschaften wird eine freistehende oder werkzeuggestützte Nachhärtung bei 180 °C empfohlen.
Teile, die mit diesem System hergestellt wurden, bestehen ohne zusätzliche Beschichtungen oder FR-Maßnahmen:
- 60s vertikaler Brennen FAR25.853(a)
- Rauchtoxizität BSS7239
- Rauchdichte BSS7238
In bestimmten Konfigurationen mit einem zertifizierten intumeszierenden Gelcoat oder einer zertifizierten Beschichtung besteht es auch die Wärmefreisetzung gemäß OSU 65/65. Dies ist nur für Teile erforderlich, die während des Rollens, des Starts und der Landung des Flugzeugs berührt werden können.
„Wir haben Gepäckablagen gezeigt, deren Herstellung derzeit 10-12 Stunden mit herkömmlichen phenolischen Prepreg-Prozessen dauert, die jedoch in 90 bis 120 Minuten mit Infusion oder RTM mit dem FlameX-System hergestellt werden können“, sagt Nathan Bruno, Hexion Spezialist für Epoxidanwendungen und Produktentwicklung . „Da es keine Füllstoffe gibt, hat es außerdem eine geringere Dichte als gefüllte FR-Epoxidharze.“
Zu den Anwendungen gehören Flugzeuginnenräume, Frachtbereiche, Toiletten, Bordküchen und Sitzkomponenten sowie Schiffs-, Schienen- und Architekturinnenräume.
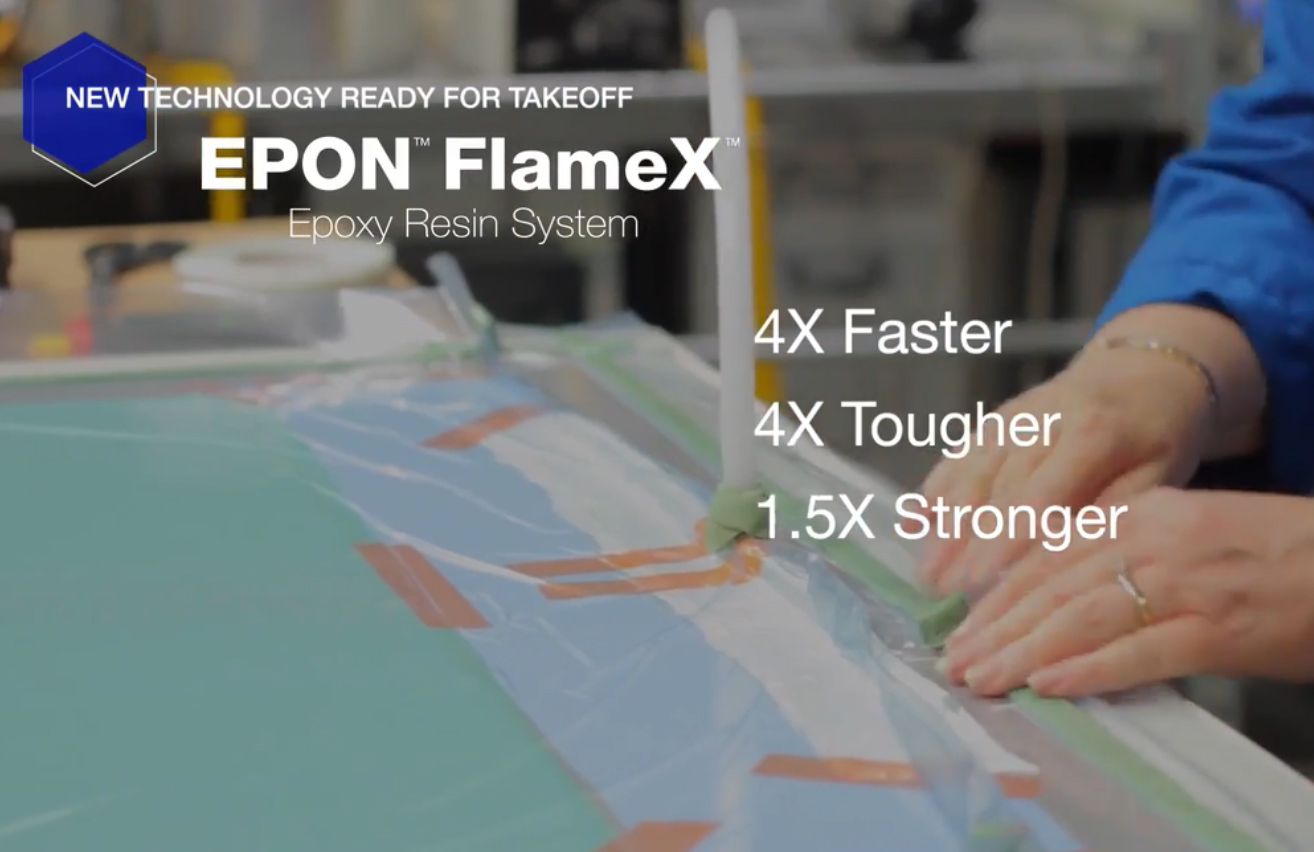
Harz
- Lanxess fügt zwei neue Produktionslinien für Verbundwerkstoff Tepex hinzu
- Reinigungsmassen für die Herstellung von dünnwandigen Polyolefinverpackungen
- Kunstharzanwendungen werden immer beliebter
- Fraunhofer nimmt automatisierte Engel-Produktionszellen für F&E thermoplastischer Verbundwerkstoffe in Betrieb
- Broetje-Automation erweitert AFP-Portfolio für die Serienfertigung von Verbundwerkstoffen
- INEOS Styrolution baut Produktionsstätte für thermoplastischen Verbundwerkstoff StyLight
- Total Composite Solutions (TCS) bringt Epoxid-Prepreg-Lösung für die Luft- und Raumfahrt auf den Markt
- Hexion führt Zweikomponenten-Epoxidlösung für die Herstellung von Verbundwerkstoffen in der Luft- und Raumfahrt ein
- Techsil bringt durchsichtigen Epoxidklebstoff für Verbundsubstrate auf den Markt
- Rhodes Interform fertigt Verbundpresse für AMRC