Kontinuierliche Isolationswiderstandsprüfung steigert die Motorproduktivität
Seit Jahrzehnten führt das Anlagenpersonal Isolationswiderstandsprüfungen mit tragbaren Megaohmmetern durch, um Motorausfälle zu verhindern, die zu kostspieligen ungeplanten Abschaltungen, Strafen für Produktionsausfälle und Rückwicklungsreparaturen führen. Diese Tests liefern jedoch nur eine „Momentaufnahme“ der motorischen Gesundheit. Innerhalb weniger Tage können Motorwicklungen und Kabel, die Feuchtigkeit, Chemikalien, Verunreinigungen oder Vibrationen ausgesetzt sind, beschädigt werden und beim Start ausfallen.
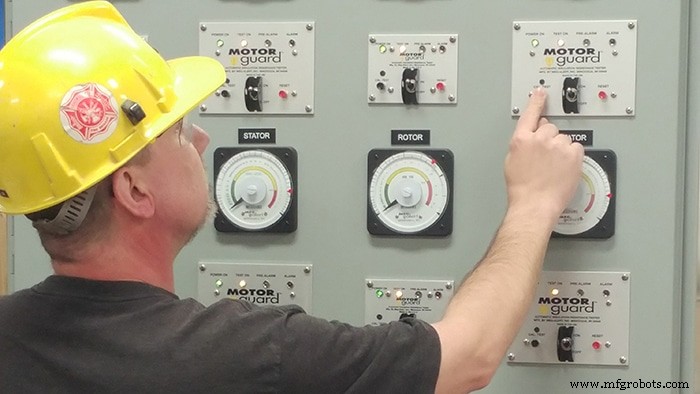
Tragbare Megaohmmeter erfordern auch, dass Elektrotechniker die Gerätekabel manuell trennen und die Messleitungen an möglicherweise unter Spannung stehenden oder beschädigten Geräten anschließen, um die manuelle Prüfung durchzuführen. Diese Tests setzen Techniker potenziellen Lichtbogenüberschlägen aus, wenn sie auf den Schrank zugreifen. In den Vereinigten Staaten kommt es ungefähr fünf- bis zehnmal pro Tag zu nicht tödlichen Störlichtbögen, wobei ungefähr einer pro Tag ums Leben kommt.
Bei so vielen Risiken erkennen Anlagenmanager den Wert einer kontinuierlichen Megaohm-Überwachung des Isolationswiderstands, die in dem Moment beginnt, in dem der Motor ausgeschaltet ist, bis er neu gestartet wird.
Ausgestattet mit diesen Echtzeitinformationen kann das Wartungspersonal frühzeitig Korrekturmaßnahmen ergreifen, um einen Ausfall zu vermeiden, der die Produktion unterbrechen würde. Auf diese Weise können Versorgungsunternehmen Hunderttausende von Dollar an Reparaturgebühren für teures Zurückspulen, Strafen für Produktionsausfälle und verlorene Produktionszeit einsparen.
Darüber hinaus ermöglichen fest installierte automatische Testgeräte eine „hands-off“-Überwachung, ohne auf Schränke zugreifen zu müssen, wodurch Techniker aus dem Weg geräumt werden.
Motorschutz bei Versorgungsunternehmen
Unabhängig von der Branche verlassen sich Produktions- und Verarbeitungsanlagen stark auf Motoren, obwohl Anzahl und Typ je nach Größe der Anlage und Art des verbrannten Brennstoffs variieren. Einige Anlagen können bis zu 20-30 kritische Motoren haben, im Durchschnitt fünf bis zehn.
Kritische Motoren sind diejenigen, die die Fähigkeit, die Geschäftsziele sicher zu erreichen, erheblich beeinträchtigen oder das Produktionsniveau beeinträchtigen könnten, wenn sie unerwartet offline gehen. Beispiele hierfür sind Motoren im Bereich von 480–13.800 V, die zum Betrieb von Kompressoren, Pumpen und Lüftern verwendet werden.
Die meisten Versorgungsunternehmen warten diese Motoren durch zeitbasierte vorbeugende Wartungsprogramme (PM). Isolationswiderstandstests werden in der Regel halbjährlich geplant. Angesichts des Personalabbaus in den meisten Werken kann dies jedoch auch seltener der Fall sein. Basierend auf diesen Tests können Motoren zur Überholung an Reparaturwerkstätten geschickt werden.
Üblicherweise werden Isolationswiderstandsprüfungen auch zu Beginn jährlicher Revisionen oder geplanter Stillstände durchgeführt, um eventuell ebenfalls reparaturbedürftige Motoren zu identifizieren. Trotz PM-Programmen können Motoren, die offline sind oder häufig getaktet werden, schnell beeinträchtigt werden. „Wir hatten unseren fairen Anteil an Motorausfällen, und es wurde ziemlich kostspielig“, sagte Richard Hohlman, der nach 37 Jahren Arbeit in Kraftwerken in den Ruhestand ging.
„Manchmal können die Ausfälle richtig teuer werden“, sagte er. „In diesem speziellen Werk hatten wir ein paar PAM-Wechselstrom-Induktionsmotoren mit zwei Geschwindigkeiten von Westinghouse, und die Neuwicklung eines davon wäre ein sechsstelliger Aufwand gewesen.“
Aus der Sicht von O&M (Betrieb und Wartung) „ist das eine große Einsparung, wenn wir einen schwachen Motor identifizieren und das Risiko vermeiden können, ihn zu starten und zu versagen“, fügte er hinzu.
Um Motorausfälle zu vermeiden, verlangt Hohlman, dass alle kritischen Motoren in einer 1.500-mW-Anlage in Long Island Sound, die für 24 Stunden oder länger abgeschaltet waren, vor dem Neustart manuell mit einem Megaohmmeter getestet werden müssen. „Das wurde zu einem eigenen Aufwand, weil die Tests oft zu unterschiedlichen Tageszeiten und zu Überstundensätzen durchgeführt wurden“, sagte Hohlmann. „Aber dadurch haben wir eine Reihe von Motorausfällen vermieden.“
Laut Hohlman entdeckte ein Mitglied seines Teams Meg-Alert, ein kontinuierliches Test- und Überwachungsgerät, hergestellt von Meg-Alert, Minocqua, Wisconsin. Das Werk installierte es zunächst auf vier Umwälzpumpen und mehreren Saugzuggebläsen. Später wurden die Geräte auch an mehreren Drucklüftern und anderen kritischen Motoren im gesamten Werk angebracht.
Die Meg-Alert-Einheit ist dauerhaft im Hochspannungsraum des MCC oder der Schaltanlage installiert und direkt mit den Motor- oder Generatorwicklungen verbunden. Das Gerät erkennt, wenn der Motor oder Generator offline ist, und führt dann einen kontinuierlichen dielektrischen Test an der Wicklungsisolierung durch, bis das Gerät neu gestartet wird.
Das Gerät funktioniert durch Anlegen einer zerstörungsfreien, strombegrenzten DC-Prüfspannung an die Phasenwicklungen und misst dann sicher jeden Leckstrom durch die Isolierung zurück zur Erde. Das System verwendet DC-Spannungspegel von 500, 1.000, 2.500 oder 5.000 V, die die internationalen Standards IEEE, ABS, ANSI/NETA und ASTM für eine angemessene Prüfspannung für den Isolationswiderstand basierend auf der Betriebsspannung des Geräts erfüllen.
Der Test verursacht keine Verschlechterung der Isolierung und umfasst eine Strombegrenzungstechnologie, die das Personal schützt.
„Durch die kontinuierliche Überwachung ist sich das O&M-Team jederzeit über die Einsatzfähigkeit des Motors im Klaren“, sagt Hohlmann. „Jedes Mal, wenn der Motor abschaltet – sei es für Sekunden, einen Tag oder für die 10 Tage eines Ausfalls – wird der Motor getestet. Und wenn es unter ein sicheres Niveau fällt, gibt es sofort einen Alarm aus und kann den Motor daran hindern, überhaupt zu starten.“
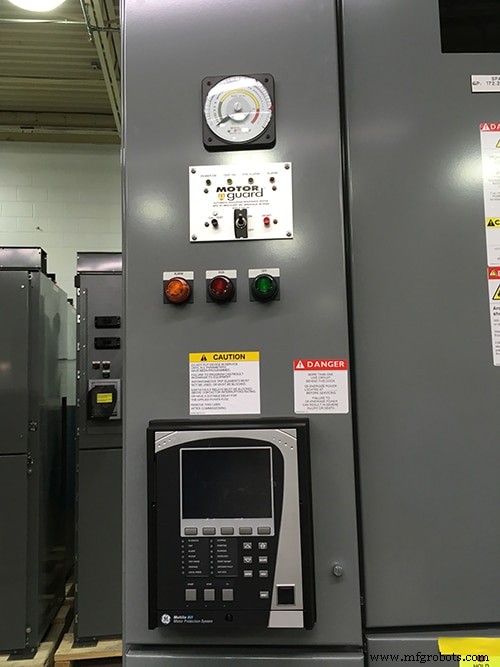
Dies steht im krassen Gegensatz zu der Momentaufnahme, die ein Megaohmmeter zu Beginn eines Shutdowns macht. Durch Feuchtigkeit und Verschmutzung kann der Motor schnell erhebliche Feuchtigkeit aufnehmen.
„Ein Elektromotor kann in der südlichen Region des Landes in nur wenigen Stunden genug Feuchtigkeit aufnehmen, um beim Start Schäden zu verursachen“, sagte Ricky Loupe, Elektro- und Instrumentenmanager in einer großen Anlage, die Polyvinylchlorid in Pulverform herstellt ( PVC) sowie der Hauptbestandteil Vinylchlorid. „Hier unten im Süden gibt es viele Regentage mit hoher Luftfeuchtigkeit, und Feuchtigkeit und Elektrizität vertragen sich nicht.
„Wenn ein Motor voller Feuchtigkeit ist und gestartet wird, gehen die Wicklungen auf Masse und beschädigen den Motor“, fuhr Loupe fort. „Jetzt haben Sie also einen kritischen Motor mit beschädigten Wicklungen, dessen Reparatur eine erhebliche Menge Geld kosten wird.“
Als damaliger Ingenieur führten er und sein Team eine Analyse durch, um die Grundursache des Problems zu ermitteln und zu verhindern, wie man es vermeidet. Nachdem er mehr über den Meg-Alert erfahren hatte, kaufte er einen als Testversion. Laut Loupe wurde es auf einem 4.160-V-, 1.200-PS-WP-Gehäusemotor installiert, der zum Antrieb eines Kompressors in einer Kühleinheit verwendet wurde.
Aufgrund der Produktionsanforderungen wurden einige der Kältemaschinen abgeschaltet und nur bei Bedarf verwendet. Dies bedeutete, dass die Motoren einiger Einheiten im Leerlauf bleiben konnten. Vor dem erneuten Betrieb einer Kältemaschine mussten die Motoren mit tragbaren Megaohmmetern getestet werden. „Oft fanden diese Arbeiten außerhalb der Geschäftszeiten statt, aufgrund der betrieblichen Anforderungen und der Notwendigkeit, sie so schnell wie möglich in Betrieb zu nehmen“, erklärte Loupe. „Wir ließen Techniker am Wochenende kommen – häufig zu Überstundensätzen – nur um die Motoren zu testen, damit sie sie starten konnten.“
Loupe sagte mit den Meg-Alert-Einheiten, dass Informationen jetzt in Echtzeit verfügbar sind. Er war außerdem davon überzeugt, dass das Gerät, das an den Anlasser angeschlossen ist, nach einem regnerischen Tag aufgrund niedriger Megaohm-Widerstandswerte das Einschalten des Motors nicht zulassen würde. „Der Meg-Alert ließ den Motor nicht starten, weil zu viel Feuchtigkeit im Motor war“, erklärte Loupe. „Damit hat sich die kontinuierliche Überwachungseinheit zehnmal bezahlt.“
Heute verfügt das Werk über Meg-Alerts für alle zehn Kühlermotoren sowie für vier 900-PS-Kühlturmpumpen in einem anderen Bereich des Werks.
„Hands-Off“-Überwachung
Das kontinuierliche Überwachungssystem ermöglicht auch einen „hands-off“-Ansatz, bei dem Servicetechniker nicht auf Schaltschränke zugreifen müssen, um eine manuelle Isolationswiderstandsprüfung durchzuführen. Stattdessen zeigt ein analoges Messgerät außen an der Schaltschranktür die in Megaohm gemessenen Isolationswiderstandswerte in Echtzeit an. Das Messgerät zeigt durch ein einfaches „grün, gelb, rot“-Farbschema auch gute, mittlere und schlechte Isolierungsgrade an.
Wenn vorgegebene Sollwerte für den Isolationswiderstand erreicht werden, schalten sich Anzeigeleuchten ein, um einen Alarmzustand anzuzeigen, und es können automatische Benachrichtigungen an das Überwachungsnetzwerk gesendet werden. Eine kontinuierliche Überwachung kann auch zeigen, ob die Heizungen, die zur Aufrechterhaltung der thermischen Temperaturen oder zur Vermeidung von Kondensation verwendet werden, ordnungsgemäß funktionieren.
Die meisten Motoren verwenden Heizungen, um die Temperatur im Inneren des Motors aufrechtzuerhalten, damit sie nicht drastisch von der Betriebstemperatur oder den Umgebungstemperaturen außerhalb des Geräts abweicht. Wenn der Taupunkt unterschritten wird, beginnt der Motor, während er offline ist, Kondenswasser aufzunehmen.
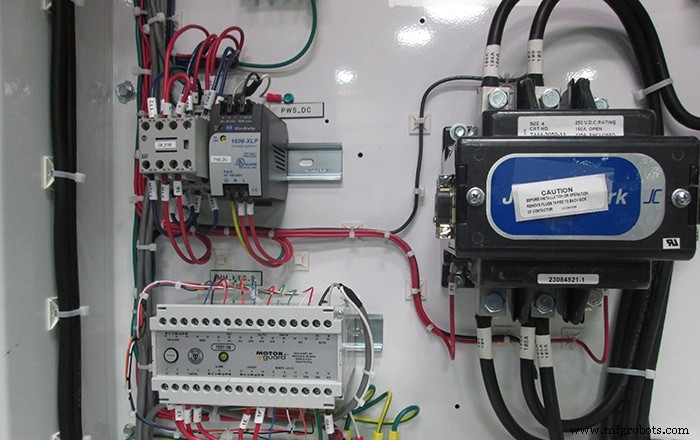
Wenn diese Heizungen jedoch nicht ordnungsgemäß funktionieren oder der Leistungsschalter ausgelöst wird, bemerkt das Wartungspersonal dies möglicherweise erst, wenn der Motor beim Starten ausfällt. Obwohl diese Motorheizungen regelmäßig überprüft werden, kann dies dazu führen, dass kritische Motoren und Generatoren wochen- oder sogar monatelang ungeschützt bleiben.
Vermeidung von Lichtbögen
Vielleicht noch wichtiger ist laut Loupe, dass der „hands-off“-Ansatz die Gefährdung der Mitarbeiter durch Lichtbogenblitze verringert. „Mit den Geräten zur kontinuierlichen Überwachung des Isolationswiderstands eliminieren Sie die potenzielle Gefahr von Lichtbogenüberschlägen, da der Techniker überhaupt keine Schränke für Megaohm-Tests öffnen muss“, sagte Loupe.
Lichtbögen sind eine unerwünschte elektrische Entladung, die sich durch die Luft zwischen Leitern oder von einem Leiter zu Erde ausbreitet. Der Blitz ist unmittelbar und kann Temperaturen erzeugen, die viermal so hoch sind wie die der Sonnenoberfläche. Die intensive Hitze verursacht auch eine plötzliche Ausdehnung der Luft, was zu einer Druckwelle führt, die Arbeiter durch Räume schleudern und sie von Leitern stoßen kann. Lichtbogenverletzungen umfassen Verbrennungen dritten Grades, Erblindung, Hörverlust, Nervenschäden, Herzstillstand und sogar den Tod.
Zu den möglichen Ursachen für einen Lichtbogenüberschlag, die von NFPA 70E aufgeführt werden, gehört „unsachgemäße Verwendung von Prüfgeräten“. Obwohl empfohlen wird, Geräte vor dem Testen stromlos zu machen und geeignete persönliche Schutzausrüstung (PSA) zu tragen, besteht die beste Lösung darin, den Zugang zu den Schaltschränken für die Durchführung von Isolationswiderstandstests überhaupt zu vermeiden.
Zusätzlich zum Risiko von Lichtbogenüberschlägen hat Loupe aus erster Hand ein weiteres potenzielles Risiko erlebt, das auftreten kann, wenn ein Motor in unmittelbarer Nähe eines Mitarbeiters kurzgeschlossen wird. In der Anlage ist das Personal beim Starten der Kältemaschine nur etwa 1,50 m vom Motor entfernt. Wenn der Motor kurzschließt, kann er einen gewaltigen Lärm machen und eine Menge Funken sprühen.
„Durch die kontinuierliche Überwachung des Isolationswiderstands ist kein Mitarbeiter in Gefahr, wenn der Motor beim Start ausfällt“, sagte Loupe. „Das Gerät verhindert auch diese Sicherheitsbedenken.“
Weitere Informationen erhalten Sie unter www.megalert.com oder telefonisch unter 800-778-5689.
Automatisierungssteuerung System
- Einphasen-Asynchronmotoren
- AC-Kommutatormotoren
- Testtipp:Ankerfehler bei Gleichstrommotoren
- Technischer Tipp:Motoren
- IQ Motion Control bringt eine neue Reihe von Servomotoren auf den Markt
- Die Grauzone zwischen Servo- und Schrittmotoren
- Über Industriemotoren und Anwendungen
- Eine Einführung in den BLDC-Motor
- Koppeln von Getrieben mit Servomotoren
- Richtige Wartung von Kompressormotoren