Kürzlich entdeckte Anwendungsfälle:Erläuterung unseres Predictive Machining-Angebots
Ursprünglich veröffentlicht auf Towards Data Science
In den letzten Monaten haben wir im Stillen neue Anwendungsfälle für unser Predictive-Machining-Produkt beobachtet und entdeckt. Dank einer optimierten Bedienerschnittstelle, die auch bequem als „hinter den Kulissen“ gekennzeichnete Datenerfassungsplattform fungiert, haben wir bisher Hunderte von Werkzeugausfällen, Lagerausfällen und anderen Maschinenausfallszenarien gesehen.
In Zusammenarbeit mit unseren Kunden haben wir einen großen Katalog entwickelt, wie typische Maschinenausfälle aus Sicht der Motordaten aussehen, was uns sehr freut heute mit Ihnen zu teilen. Wir werden sechs Szenarien überprüfen, die wir an mehreren Kundenstandorten wiederholt gesehen haben, und wie sie sowohl aus der Perspektive „Punkte in einem Diagramm“ als auch aus ihrer physischen Manifestation in der Fertigung aussehen. Diese lauten wie folgt:
- Schaftfräserausfälle führen zu schlechter Oberflächengüte und Ausschussteilen
- Kugellagerausfälle führen zu beschädigtem Spindelgehäuse
- Ausfälle von Schruppwerkzeugen, die zu kaskadierenden Werkzeugausfällen bei Schlichtwerkzeugen führen
- Falscher Versatz, der zu einer Fehlausrichtung der Führungsbuchse führt
- Werkzeugfehler, der zu unvollständigem Abschneiden führt
- Falsche Schätzung der Werkzeuglebensdauer, was zu einer Über- oder Unterbeanspruchung von Werkzeugen führt
Bevor wir zu den guten Sachen kommen, lassen Sie uns unsere These für unser Angebot zur vorausschauenden Bearbeitung durchgehen:
Wir extrahieren umfangreiche Daten von eingebetteten Sensoren auf der Maschine, um verschiedene Szenarien vorherzusagen und zu verhindern, die sich als kostspielig erweisen könnten.
- Rich Data:1 Millisekunde Abtastrate -> 170 Millionen Beobachtungen pro Tag und Motor, Genauigkeit bis 0,001 U/min für Spindeldrehzahl, 0,01 % Dauerleistung für Leistung/ laden
- Eingebettete Sensoren:Keine zusätzlichen Sensoren erforderlich, da Daten notwendigerweise auf allen modernen CNC-Maschinen verfügbar sind. Wir ziehen nur Daten, die die Maschine verwendet, um ihre interne Steuerrückkopplungsschleife auszuführen. Alle gezeigten Szenarien wurden während der COVID-19-Pandemie eingesetzt, ohne dass das Personal von MachineMetrics jemals einen Fuß in die Fabrikhalle gesetzt hat
- Kostenträchtige Szenarien vorhersagen und verhindern:Die beschriebenen Situationen kosten unsere Kunden Geld, und sie zu vermeiden, spart ihnen Geld. Wir monetarisieren dies, indem wir einen Bruchteil der Einsparungen nehmen
Schaftfräserfehler
Nur zur Übersicht:Wir haben an jeder einzelnen Maschine von MachineMetrics ein Operator-Tablet , bei dem es sich im Grunde nur um ein Samsung Galaxy-Tablet oder iPad handelt, das auf die Webseite des jeweiligen Geräts in unserem SaaS-Produkt verweist.
Ein Kunde, der unser Operator-Tablet verwendet.
Das Bediener-Tablet ist direkt mit unserer Plattform verbunden, sodass jedes Mal, wenn die Maschine stoppt, ein Signal von der Maschine an unser Edge-Gerät gesendet wird, das dann an die Cloud gesendet wird, wo es aggregiert und mit anderen Metriken als Dashboard dargestellt wird. Das Tablet spiegelt dann diese neuen Informationen wider und gibt ein Popup-Fenster auf der Maschinen-Webseite aus, in dem der Bediener aufgefordert wird, zu erklären, warum die Maschine ausgefallen ist.
Wenn eine Maschine stoppt, erscheint ein Popup-Fenster, in dem der Bediener aufgefordert wird, einen Grundcode hinzuzufügen.
Im Laufe der Zeit häufen sich diese Anmerkungen an, was uns einen reichhaltigen, detaillierten Überblick darüber gibt, wann und aus welchem Grund eine Maschine ist kaputt gegangen.
Es liegt an MachineMetrics Data Science, das Warum und Wie zu finden des Maschinenausfalls anhand der extrem feinkörnigen Daten, die wir von den Motoren der Maschine sammeln. In einer Ausführungsform davon können wir Zehntausende von hergestellten Teilen und Dutzende von Anmerkungen betrachten, um Muster zu identifizieren, wie im folgenden Beispiel, wo schwarze Linien kommentierte Fehler sind und Punkte die von jedem hergestellten Teil verbrauchte Energie darstellen>
Schwarze Linien sind annotierte Fehler, während rote Punkte abnormale Belastung sind. Einige rote Punkte stimmen nicht mit schwarzen Linien überein, da Anmerkungen manchmal von Bedienern übersehen werden.
Im Laufe der Zeit entstehen Muster für jede Art von Fehler. Die schwarzen Linien im Diagramm repräsentieren vor allem Zeiten von Schaftfräserausfällen , wenn ein bestimmter Schaftfräser bricht und die zur Fertigstellung des Teils erforderliche Arbeit nicht ausführen kann. Das Tool, das nach kommt Der Schaftfräser muss dann zusätzliche Energie aufwenden, um seinen Schnitt auszuführen, was zu der erhöhten Lastsignatur in Rot führt, die Sie im Diagramm oben sehen. Dies wird immer wieder wiederholt, was es uns ermöglicht, einen einfachen Schwellenwertalgorithmus zu erstellen, um die Maschine anzuhalten, wenn wir die erste erhöhte Lastsignatur sehen.
In seiner physischen Manifestation können Sie sehen, dass ein gutes Teil, das von einem guten Schaftfräser geschnitten wurde, eine schöne und glänzende Oberfläche im Schlitz hat. Ein schlechtes Teil, das von einem gebrochenen Schaftfräser geschnitten wurde, hat einen rauen Schlitz, weil der Schaftfräser nicht in der Lage war, eine glatte Oberfläche zu erzeugen, und das nachfolgende Werkzeug konnte seine Arbeit auch nicht richtig erledigen.
Und in unserem Produkt überwachen wir jetzt die Lasten auf dieser Maschine, um einen Feed-Hold auszulösen, bevor eines dieser Bad-Slot-Teile hergestellt wird. In den letzten 4 Monaten haben wir 60 Feed Holds auf mehreren Maschinen ausgegeben, mit 3 Fehlalarmen und 2 verpassten Fehlern (95 % Präzision, 96 % Rückruf), wodurch die Herstellung von über 2.000 Ausschussteilen verhindert und unzählige Arbeitsstunden an Maschinen eingespart wurden Neukonfiguration. Oh, und nur um sicherzugehen, dies sind kleine Teile, die mit kleinen Werkzeugen hergestellt werden – die Größe ist für uns keine große Einschränkung, wenn wir sehr sensible Motordaten abrufen. Alle Teile, die aus diesen Maschinen kommen, sind jetzt glänzend und neu, ohne die Mängel, die sie früher trugen.
Ziemlich ordentlich, oder? Das ist nur einer von vielen Anwendungsfällen. Du dachtest nicht, wir wären nur ein One-Trick-Pony, oder?
Kugellagerfehler
Ähnlich wie Schaftfräserausfälle können sich Lagerausfälle sowohl in Bezug auf Material als auch auf Arbeitskraft als kostspielig erweisen.
Im Gegensatz zu Schaftfräserausfällen sehen Lagerausfälle in Bezug auf die Muster, nach denen wir suchen müssen, völlig anders aus.
Ähnlich wie Schaftfräserausfälle verwenden Lagerausfälle die gleiche Art von umfangreichen Motordaten und Erfassungsmethoden.
Anders als Schaftfräserausfälle manifestieren sich Lagerausfälle über lange Zeiträume (Tage bis Wochen) und können lange im Voraus verhindert werden.
Lassen Sie uns zuerst untersuchen, welche Belastung auf die Maschine kurz vor einem Lagerausfall wirkt, in einer Momentaufnahme der Daten 2 Stunden vor dem Ausfall.
[Bild in voller Größe anzeigen]
Jede dieser Zeilen wird auf ein bestimmtes Werkzeug geladen. Es braucht keinen Raketenwissenschaftler, um herauszufinden, was hier vor sich geht. Die Belastung explodiert ~15 Minuten vor dem eigentlichen Lagerausfall bei jedem einzelnen Werkzeug, wahrscheinlich aufgrund der Tatsache, dass die Maschine einer zusätzlichen Belastung durch eine zunehmend gefährdete Schlüsselkomponente ausgesetzt ist.
Wenn wir uns den Verlauf von Teil zu Teil in den 15 Minuten vor dem Ausfall ansehen, ergibt sich ein weiteres interessantes Muster, nämlich dass die Last erscheint degenerieren im Laufe der Zeit. Sie können sehen, dass die Belastung mit jedem Schnitt exponentiell mehr und mehr außerhalb der Spezifikation liegt.
Vergleichen Sie dies mit einem anderen Lagerausfall auf einer anderen Maschine, die das gleiche Teil herstellt, und die Muster sind bemerkenswert ähnlich. Das liegt daran, dass dies die eindeutige Signatur für einen Lagerschaden ist. Während Schaftfräserausfälle, die zu Ausschussteilen führen, einen Belastungssprung auf das nachfolgende Werkzeug zeigen, zeigen Lagerausfälle einen stark degenerierten Belastungsanstieg auf allen Werkzeugen.
Und wenn wir uns das im Laufe der Zeit ansehen, sehen wir tatsächlich, dass diese Degeneration Tage vor dem eigentlichen Ausfall beginnt. In zwei getrennten Fällen für zwei Maschinen können Sie sehen, dass es in den letzten 15 Minuten vor dem Bruch lange vor dem letzten steilen Anstieg eine Lasterhöhung gibt. Das liegt daran, dass ein Lager nicht einfach aus dem Nichts kommt. Es gibt wahrscheinlich eine Lockerung oder einen Bruch, der tagelang vor dem endgültigen Hari-Kari unkontrolliert bleibt, verursacht durch Missbrauch oder mangelnde Wartung. In diesem Fall verursachte das ausgefallene Lager auch Schäden am Spindelgehäuse, die weitere coole paar Tausende von $$$ für die Reparatur kosteten.
November Lagerausfall, zeigt erhöhte Belastung ~2 Tage vorher. [Bild in voller Größe anzeigen]
Februar Lagerausfall, zeigt erhöhte Belastung ~1 Woche vorher. [Bild in voller Größe anzeigen]
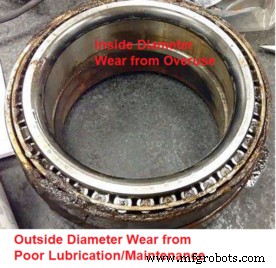
Die bemerkenswerte Konsistenz sehen wir für ähnlich Arten von Fehlern sind darauf zurückzuführen, dass wir physikalische Phänomene betrachten, die überraschenderweise von den Gesetzen der Physik beherrscht werden. Ausfälle folgen also deterministischen Mustern, die wir anhand von Daten mit ausreichend hoher Genauigkeit erkennen können. Der Trick besteht wirklich darin, diese Daten zu erhalten und zu bereinigen, damit sie nützlich sind, was einen großen Teil unseres IP ausmacht.
Wir schreiben diese Innovation der besonderen Mischung von Fähigkeiten zu, die wir im MachineMetrics-Team haben – wir glauben nicht, dass es typisch ist, dass erfahrene Maschinenbediener mit Cyber-Experten zusammenarbeiten - physikalische Protokolle, ergänzt von Physikern des CERN und Datenwissenschaftlern aus globalen Denkfabriken, die alle von Investoren unterstützt werden, die glauben, dass wir ein neues Industriezeitalter einläuten.
Cascading Tool Failures
Eine ganze Reihe von Werkzeugen kaputt zu haben, kann für jeden Maschinisten eine frustrierende Erfahrung sein. Leider kommt dies in unserer Branche allzu häufig vor. Was wäre, wenn wir sehen könnten, wann das erste Werkzeug kaputt geht, und dann die Maschine sofort anhalten könnten, bevor die anderen Werkzeuge herausgenommen werden?
Es stellt sich heraus, dass Sie das können. Nachdem das erste Werkzeug gegangen ist, wird Ihnen die Änderung der Ladesignatur bei nachfolgenden Werkzeugen so gut wie auf einem Tablett gereicht.
In einem Fall sehen wir, wie das erste Werkzeug viele Teilzyklen bricht, bevor die Maschine sich selbst stoppt, wenn sie etwas Katastrophales erkennt. Zu dem Zeitpunkt, an dem der Selbststopp auftritt, sind auch andere Werkzeuge herausgenommen worden, was die Werkstatt durch unnötigen Werkzeugwechsel im Wert von Hunderten von Dollar gekostet hat. Das erste Werkzeug ging wahrscheinlich kaputt, weil es abgenutzt war und das Ende seiner Lebensdauer überschritten hatte, sodass es wahrscheinlich sowieso nicht gerettet werden konnte. Aber es gibt keinen Grund, warum andere Tools danach, einige frisch ersetzt, ebenfalls gehen müssen.
Sie können eine Animation davon unten sehen, wo der angebliche Werkzeugfehler laut dem Bediener und als die Maschine sich selbst stoppte, bei Teil 40 war. Tatsächlich, Das Signal beginnt um Teil 37 herum zu degenerieren, volle 3 Zyklen, bevor die Maschine selbst erkannt hat, dass etwas nicht stimmt. Während dieser 3 Zyklen ging das Werkzeug, das auf das kaputte Werkzeug folgte, kaputt.
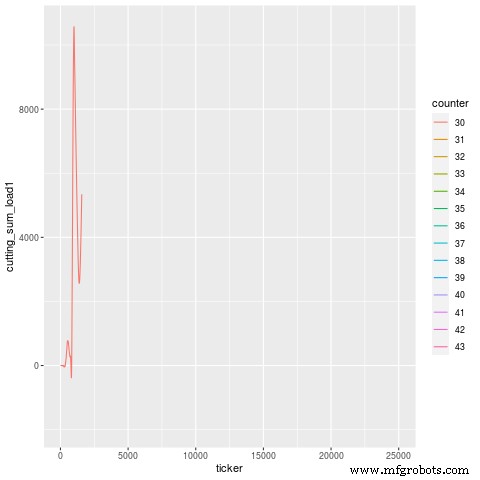
Lassen Sie uns diese Nutzungsdauer des Tools aufschlüsseln Neben der Teilenummer werden Werkzeuge durch verschiedene Linientypen gekennzeichnet.
Lassen Sie uns ein wenig in die beunruhigende Region hineinzoomen. Es ist ein wenig schwer zu erkennen, aber es sieht so aus, als ob T101 das störende Werkzeug ist, das kaputt gegangen ist, und T117 dasjenige ist, das in den Zyklen unmittelbar danach eine höhere Belastung erfährt, als Flatlines (stirbt). Sobald die Werkzeuge ersetzt sind, geht die Ladesignatur ungefähr wieder auf das zurück, was sie vorher war (unter Berücksichtigung eines kleinen Schlupfs aufgrund frischer Werkzeuge).
Die Anmerkung in diesem Fall lautete „H1t1 198/200 rauer brach, nahm Sitz heraus.“ – was bedeutet, „Kopf 1, Werkzeug 1, das Schruppwerkzeug, brach während der Arbeit, bei 198 von 200 Teilen, die hergestellt werden sollten, und nahm das Setzwerkzeug (nachfolgendes Werkzeug) heraus“.
[Bild in voller Größe anzeigen]
Tatsächlich ist das passiert.
Bleiben Sie dran für Teil 2, in dem wir die Schätzung der Werkzeuglebensdauer, die Folgen falscher Versätze auf Ihrer Maschine und unvollständige Schnitte durch Werkzeugversagen besprechen werden.
Vorgestelltes Bild mit freundlicher Genehmigung von Daniel Smyth.
Industrietechnik
- 30 erstaunliche NASA-Erfindungen, die wir in unserem täglichen Leben verwenden
- Maschinelles Lernen in der vorausschauenden Wartung
- CNC-Bearbeitung:Definition und Arten von CNC-Maschinen
- Was ist NC-Bearbeitung? - Definition und grundlegende Anleitung
- CNC-Bearbeitungsanwendungsfälle in der Militär- und Verteidigungsindustrie
- Verwendung von Oberflächen zur Bearbeitung komplexer Geometrien
- Wie sich KI und maschinelles Lernen auf die CNC-Bearbeitung auswirken
- Predictive Analytics in der Fertigung:Anwendungsfälle und Vorteile
- Die Bedeutung von Kühlmitteln bei der Bearbeitung
- Wie sich Schneidflüssigkeiten auf Bearbeitungsprozesse auswirken