Trends der Lebensmittelverpackungsautomatisierung im Jahr 2022
Geschrieben von den Spezialisten bei Emerson .
Die Convenience von verpackten Lebensmitteln und Getränken treibt das Wachstum in dieser Branche weiter voran. Tatsächlich wird für den US-amerikanischen Markt für verpackte Lebensmittel von 2021 bis 2028 ein durchschnittliches jährliches Wachstum von 4,1 % prognostiziert. Die Automatisierung von Lebensmittelverpackungsprozessen hat Unternehmen geholfen, mit der Nachfrage Schritt zu halten und sicherzustellen, dass verpackte Lebensmittel für die Kunden frisch sind.
Eine der wichtigsten Technologien in der Lebensmittelverpackungsautomatisierung ist die Pneumatik. Pneumatiktechnologie, einschließlich pneumatischer Ventile und pneumatischer Stellantriebe, ist sauber, zuverlässig und wartungsfreundlich. Die neuesten Fortschritte in den Bereichen Hygienedesign, Maschinensicherheit und Energieeffizienz pneumatischer Produkte gehören zu den größten Trends 2022 in der Verpackungsautomatisierung.
Hygienisches Design
Bei Lebensmittel- und Getränkeverpackungen müssen die in Verpackungsmaschinen verwendeten Komponenten strenge Vorschriften für den Kontakt mit Lebensmitteln erfüllen und robust sein, um wiederholten Reinigungsvorgängen standzuhalten. Die neuesten Ventilsysteme, wie sie in Vakuumverpackungsanwendungen verwendet werden, haben die höchste Schutzklasse und eine Reihe kostensparender Funktionen, die die Reinigung erleichtern.
Herkömmlicherweise erforderten Ventilsysteme Schränke oder andere Gehäuse, um empfindliche Komponenten vor nassen oder rauen Anwendungsumgebungen zu schützen. Edelstahlschränke bieten zwar den notwendigen Schutz, können aber teuer sein. Die heutigen Ventilsysteme sind schranklose Washdown-Produkte, die speziell entwickelt wurden, um das gleiche Maß an Schutz zu bieten und gleichzeitig die Zylinderleistung zu verbessern – ohne die zusätzlichen Kosten eines Gehäuses. Dies verbessert die Reaktionszeiten und erhöht die Energieeinsparungen bei Verpackungsanwendungen, da für jeden Zyklus des Ventils weniger Druckluft benötigt wird. Kürzere Druckluftleitungen vom Ventil zum Zylinder bedeuten weniger Volumen zum Füllen und Ablassen, wodurch die Leistung des Zylinders verbessert wird.
Diese Ventilsysteme sind für eine einfache Reinigung konzipiert und aus robusten, hygienischen Materialien gefertigt, die aggressiven Chemikalien und hohen Drücken, die in Washdown-Prozessen verwendet werden, standhalten können. Emersons AVENTICS TM Das Clean-Line-Ventilsystem der Serie CL03 hat zum Beispiel keine Fugen oder Lücken und verwendet Edelstahlkomponenten und Polymere, die für die Hochdruckreinigung mit aggressiven Chemikalien geeignet sind.
Der CL03 hat außerdem die Schutzart IP69K, die höchste Schutzklasse, erhalten. Produkte, die diese Einstufung erreichen, bieten Schutz vor Staub und Hochtemperatur- und Hochdruckwaschflüssigkeiten, wodurch sie ideal für Verpackungs- und Lebensmittelverarbeitungsanwendungen sind, bei denen Maschinen gründlich desinfiziert werden müssen. Es verwendet auch Schmiermittel NSFH1 (Lebensmittelqualität).
Zusätzlich zu ihrem hygienischen Design sind die neuesten Ventilsysteme in hohem Maße konfigurierbar, um den Anforderungen jeder Anwendung gerecht zu werden, und sind mit einer Vielzahl von Kommunikationsprotokollen kompatibel. Einige Anbieter von Ventilsystemen verfügen über Online-Konfigurationstools, die es Konstrukteuren erleichtern, schnell auf CAD-Zeichnungen, Schaltpläne, Teilenummern und zugehörige Komponenten zuzugreifen. Viele können mit pneumatischen Antrieben kombiniert werden; Der CL03 kann mit Emersons AVENTICS-Zylindern der Serien ICS und M in Washdown-Anwendungen gekoppelt werden.
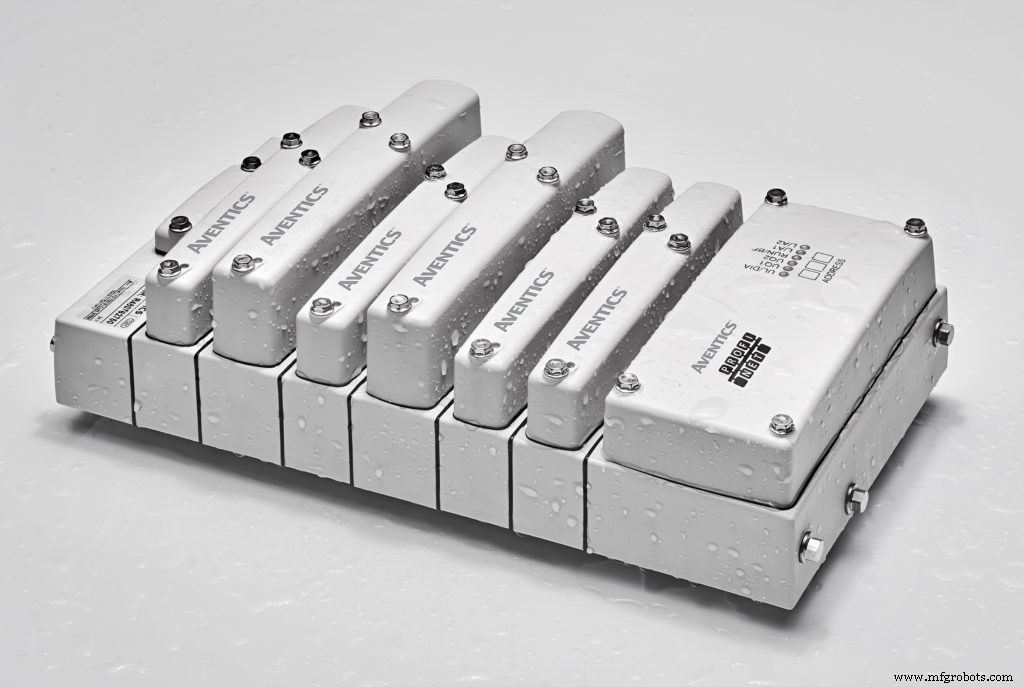
Maschinensicherheit
Bei Geräten, die gewartet werden müssen, gibt es einen wachsenden Trend bei CPG-Unternehmen (Consumer Packaged Goods), verschiedene Formen der funktionalen Sicherheit zu implementieren, am häufigsten gemäß ISO 13849. Ob es sich um ein vollständiges LOTO (Lockout/Tagout) oder die Implementierung des „ geringfügige Wartungsausnahme“ ist die gebräuchlichste Methode, um pneumatische Komponenten „sicher“ zu machen, die pneumatische Energie freizusetzen. Die bevorzugte Komponente zur Implementierung dieser „Sicherheitsfunktion“ ist ein redundantes Sicherheitsentlüftungsventil (siehe Abbildung unten), das Teil einer Luftaufbereitungsbaugruppe sein kann, die die Druckluft einer Maschine oder einem Maschinenabschnitt zuführt.
Wie aus Risikobewertungen hervorgeht, erfordert ein großer Prozentsatz solcher regelmäßiger Eingriffe in die Ausrüstung eine Sicherheitslösung der Kategorie 3 PLd, um die Ausrüstung sicher zu machen. Lösungen der Kategorie 3 PLd benötigen redundante Schaltkreise, um die Sicherheitsfunktion zu vervollständigen. Diese Sicherheitseinstufung erreicht das RSEV durch redundante Ventile und Diagnosedeckung (z. B. Schaltstellungsüberwachung), um sicherzustellen, dass gespeicherte Energie in Form von Druckluft abgebaut wird. Wenn ein Gerät wie z. B. ein Sicherheitstor ausgelöst wird, werden zwei Sicherheitsausgänge an das RSEV gesendet. Sollte ein Ventil ausfallen, erfüllt das redundante Ventil weiterhin die Sicherheitsfunktion. Die Diagnoseabdeckung löst einen Alarm aus, sodass Maßnahmen ergriffen werden können, um den Fehler zu beheben, bevor der Betrieb wieder aufgenommen wird.
Einige redundante Sicherheitsventile, wie das RSEV von Emerson, das mit Luftaufbereitungslösungen der Serien 652 und 653 von AVENTICS erhältlich ist, verfügen über eine integrierte Sanftanlauffunktion. Beim Start füllt sich diese Funktion mit einer reduzierten Rate von 60 – 70 % des endgültigen Systemdrucks, bevor sie sich vollständig öffnet. Der langsame Druck-/Kraftaufbau, wenn sich die Aktuatoren in ihre Ausgangs-/Startposition bewegen, verhindert Schäden an Komponenten und Ausrüstung.
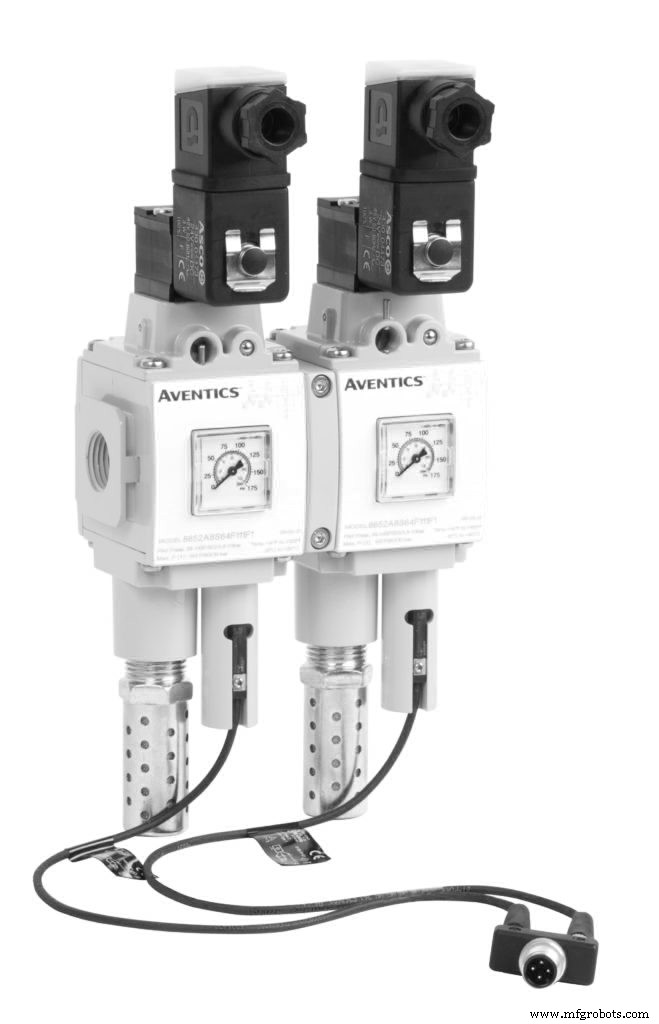
Energieeffizienz
Die Dekarbonisierung ist nach wie vor ein Trend in fast allen Branchen, einschließlich der Lebensmittel- und Getränkeindustrie. Die Reduzierung des Energieverbrauchs hat für Verpackungsunternehmen eine sehr hohe Priorität, und CPG-Hersteller suchen nach Möglichkeiten, den Energieverbrauch in ihren Anlagen besser zu kontrollieren. Daher statten viele neue Maschinen aus und rüsten bestehende Maschinen mit Luftstromsensoren nach.
Der Druckluftverbrauch ist eine bedeutende Quelle des Energieverbrauchs in Verpackungsanwendungen. Unentdeckt und unbehandelt können Druckluftlecks erhebliche Mengen an Energie und Geld verschwenden. Luftstromsensoren, die den Druckluftstrom kontinuierlich in Echtzeit überwachen, können Betreibern helfen, Lecks früher zu erkennen und zu beheben, Energieverluste zu minimieren und die Nachhaltigkeit zu verbessern.
Durch die kontinuierliche Messung von Prozessparametern wie Druck, Temperatur, Massendurchfluss, Volumendurchfluss, Strömungsgeschwindigkeit, Gesamtmasse, Gesamtvolumen und Energie können Sensoren den Bedienern helfen, den Luftverbrauch und den Energieverbrauch zu verfolgen. Betreiber können dann die gesammelten Daten verwenden, um potenzielle Probleme wie Lecks zu lokalisieren und zu beheben, bevor sie auftreten. Durch die Vermeidung von Lecks können Einrichtungen die Energieeffizienz verbessern und gleichzeitig Ausfallzeiten und Kosten reduzieren.
Luftströmungssensoren eignen sich für Einrichtungen jeder Größe und an jedem Punkt ihrer digitalen Transformation. Einige Luftstromsensoren, wie z. B. der AF2-Sensor der AVENTICS-Serie von Emerson, ermöglichen es Bedienern, Daten auf Maschinenebene anzuzeigen, und ermöglichen Einrichtungen, gesammelte Daten in ihrem eigenen IT-Netzwerk zu speichern, ohne eine Verbindung zur Cloud herzustellen. Einrichtungen können auch Sensoren mit einem Gateway verbinden, um auf zusätzliche Erkenntnisse zuzugreifen. Hersteller von Luftstromregelventilen mit Erfahrung in der digitalen Transformation können Einrichtungen bei der Entscheidung helfen, was für ihre individuellen Bedürfnisse und Ziele am besten geeignet ist.
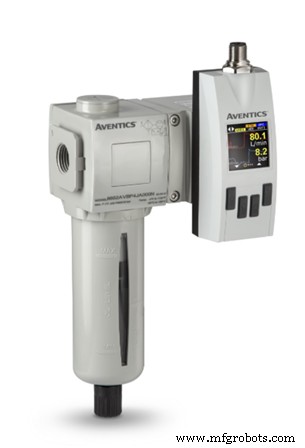
Ein höheres Leistungsniveau
Die neuesten Trends in der Lebensmittelverpackungsautomatisierung geben Verpackungsunternehmen die Möglichkeit sicherzustellen, dass die Maschinen in ihren Linien die höchsten Maschinensicherheits-, Energieeffizienz- und Hygienestandards erfüllen.
Weitere Informationen zu den pneumatischen Technologien, die das Erreichen dieses Leistungsniveaus ermöglichen, finden Sie unter https://www.emerson.com/en-us/industries/automation/food-beverage oder wenden Sie sich an einen Experten von JH Foster.
Industrielle Ausrüstung
- Zwei Akquisitionen im Bereich IML und Verpackungsautomatisierung
- Zukünftige Trends in der Luft- und Raumfahrtautomatisierung
- Fünf Lieferkettentrends, die im Jahr 2022 zu erwarten sind
- ABB prognostiziert Schlüsseltrends, die die Roboterautomatisierung im Jahr 2022 verändern werden
- Vorteile und Trends der ERP-Automatisierung
- Aktuelle Trends bei automatisierten Fertigungslinien
- Top-Trends zur Geschäftsautomatisierung
- Trends in der Industrieautomation
- Automatisierungstechnologie unterstreicht Sicherheit, flexible Fertigung
- Erwarten Sie diese Trends in der Lebensmittelherstellung im Jahr 2022