Muss sich eine Drehmühle drehen?
LeanWerks hat einen Prozess entwickelt, der Schneidwerkzeug und Werkstückhalterung kombiniert und Teilemesstechnologien, damit das Drehfräswerk fünf Seiten dieses Feingussteils in einer Aufspannung bearbeiten kann. Bildnachweis:LeanWerks
Vor einigen Jahren spornten die nachlassenden Geschäftsbedingungen auf Ölfeldern LeanWerks in Ogden, Utah, an, in anderen Branchen (einschließlich Luft- und Raumfahrt und Hochgeschwindigkeitsautomatisierung) tätig zu werden, um einen ausgewogeneren Kundenstamm und stabilere Arbeitsabläufe aufzubauen. Die Vertragswerkstatt, die jetzt nach dem Luft- und Raumfahrtstandard AS9100C registriert ist, begann auch damit, einige ihrer bestehenden Bearbeitungskapazitäten anzupassen, um sie besser an die Bearbeitungsaufgaben anzupassen, denen sie in diesen neuen Branchen begegnen würden.
Reid Leland, Präsident und Mitbegründer des Unternehmens, weist auf ein Beispiel hin:ein Aluminiumfeinguss für ein Kraftstofffiltergehäuse eines Strahltriebwerks. Als LeanWerks mit dieser Aufgabe vertraut gemacht wurde, war sein Gießereikunde für die Luft- und Raumfahrt fast ein Jahr hinter dem Lieferplan zurück, weil sein interner Bearbeitungsprozess und damit die Produktionsrate langsam waren. Infolgedessen verlor sein Kunde – der OEM des Strahltriebwerks, an dem dieses Gehäuse installiert ist – die Geduld, und der Rückstand, der durch die Verzögerungen bei diesem Auftrag verursacht wurde, enttäuschte andere Kunden. Um die internen Bearbeitungsressourcen etwas zu entlasten, wandte sich die Gießerei daher an LeanWerks, um die Übernahme der Bearbeitung dieser Gussteile in Erwägung zu ziehen.
Obwohl viele Ingenieure Feingussteile für ihre Teiledesigns spezifizieren, weil sie im Vergleich zu anderen Gussverfahren eine komplizierte Form mit guter Maßgenauigkeit bieten, müssen diese Komponenten dennoch maschinell bearbeitet werden, um eine genaue Passung und Funktion in Hochleistungsbaugruppen zu erreichen. Die Variabilität dieser Arten von Gussteilen und die damit verbundenen kniffligen Anforderungen an die Werkstückspannung führen jedoch dazu, dass einige Betriebe diese Art von Bearbeitungsarbeiten vermeiden.
Beispielsweise erfordert das Kraftstofffiltergehäuse mehrere Bearbeitungsvorgänge, einschließlich Tieflochfräsen, Bohren, Planen, Bohren, Gewindeschneiden, Innendurchmesser-Nuten und 3D-Konturierung. Ursprünglich dachte LeanWerks, dass es den Job mit mehreren Setups auf einer Drei-Achsen-Fräsmaschine und einem Setup auf einem Drehzentrum erledigen könnte. Letztendlich wurde entschieden, dass dies nicht die beste Strategie war, da die engen Positionstoleranzen des Teils mit dem komplizierten Bezugsschema aufgrund der mehreren Einstellungen nicht erreichbar wären.
Stattdessen überlegte LeanWerks, wie es die Fräsfunktion seines Dreh-Fräsers Mazak Integrex i200S nutzen könnte, um die Anzahl der Berührungen des Teils während der Bearbeitung zu minimieren. Die Werkstatt verwendete diese Maschine hauptsächlich zur Herstellung von Ventileinsätzen mit konischem Küken für Hochdruckpumpen in der Öl- und Gasindustrie, wie sie zum Beispiel für Hydraulikbruch- und Coiled-Tubing-Anwendungen benötigt werden. Der Integrex war für das Ventileinsatzteil gut geeignet, da er sowohl den konischen Außendurchmesser des Teils drehen als auch seine inneren Querachsen-Durchflussbohrungen fräsen konnte. Die Maschine konnte auch den zugehörigen O-Ring der Bohrung fräsen, was aufgrund der konischen Oberfläche der Bohrung eine fünfachsige Konturoperation erforderte.
Die Bearbeitung des Gehäuseteils des Kraftstofffilters auf dem Drehfräser, eine Arbeit, die kein Drehen erforderte, stellte jedoch eine Vielzahl von Herausforderungen dar. Zum Beispiel hat der A356.0-Aluminiumguss in Flugzeugqualität einen hohen Silikatgehalt und kann für Schneidwerkzeuge hart sein. Darüber hinaus weist die Geometrie des Teils mehrere Merkmale in mehreren Winkeln auf allen Flächen auf (einschließlich einer kritischen Passung im Boden des 13 Zoll tiefen Gussteils) und dünnwandige Bereiche verursachen Vibrationsprobleme während der Bearbeitung. Außerdem erfordert das Teil mit komplexer Bezugsstruktur enge Toleranzen, einschließlich einer Echtpositionstoleranz von 0,25 mm bei einigen weit voneinander entfernten Merkmalen und Größentoleranzen von ±0,01 mm und Echtpositionstoleranzen von 0,05 mm für andere, weniger getrennte Merkmale.
Infolgedessen unternahm LeanWerks im Wesentlichen drei Schritte, um es seinem Drehfräser zu ermöglichen, fünf Seiten des Feingusses in einer Aufspannung effektiv zu bearbeiten. Der erste Schritt bestand darin, eine Haltevorrichtung für das Gussteil zu konstruieren, um die Bearbeitung an fünf Seiten des Teils zu ermöglichen. Eine Schlüsselkomponente dieses Vorrichtungsdesigns ist eine Wiege, die in den Hauptkörper des Gussteils eingreift und gleichzeitig Zugang zu Merkmalen zwischen und neben den Wiegenbeinen bietet. Um das Gussteil an der Wiege zu befestigen, wurde ein Ketten- und Riemenscheibenmechanismus zwischen den Wiegenbeinen installiert, um eine gleichmäßig verteilte Klemmkraft bereitzustellen.
Da der Drehfräser keinen ausreichenden Y-Achsen-Verfahrweg bot, um alle Merkmale zu erreichen, wurde eine Setco-Schwalbenschwanzführung in die Vorrichtung eingebaut, damit die Wiege und das Teil verschoben und in einer zugänglichen Position wieder festgespannt werden können, ohne das Teil vollständig neu zu befestigen. Um die Steifigkeit zu gewährleisten, wurde die Wiege mit Passstiften und Schweißnähten auf einer Stahlgrundplatte montiert und verspannt. Diese Grundplatte wird am Schwalbenschwanzschlitten montiert, und die Schlittenbasis wird an den Hauptbacken des vorhandenen Dreibackenfutters der Maschine montiert.
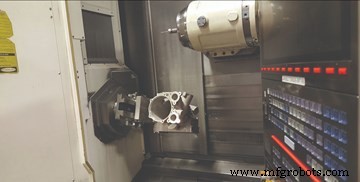
Aufgrund der Größe dieses Werkstücks ist die Der Y-Achsen-Verfahrweg des Drehfräsers ermöglicht es seiner Spindel nicht, alle Bereiche des zu bearbeitenden Teils zu erreichen. Um dies abzumildern, verwendet die von LeanWerks entwickelte Vorrichtung eine Schwalbenschwanzführung, damit das befestigte Teil verschoben und in einer zugänglichen Position wieder festgeklemmt werden kann. Nachfolgende Prüfroutinen bestimmen die wahre Position des neu positionierten Teils.
Als nächstes integrierte die Werkstatt ein taktiles Messsystem. Berührungsprüfung war notwendig, da die Form jedes Gussteils leicht variiert und die Gleitvorrichtung, die verwendet wird, um das Problem mit dem Y-Achsen-Verfahrweg zu mindern, die Position des Teils verändert. Durch das Abtasten konnte die neue Position des Teils nach der Verschiebung genau definiert und die nachfolgenden Werkzeugwege optimal an die tatsächliche Position des Teils angepasst werden.
Tatsächlich erkannte die Werkstatt, dass sie eine Sonde in Standardlänge sowie eine Sonde mit erweiterter Reichweite benötigte, um auf Merkmale zuzugreifen, die sich tief im Inneren des Teils befinden. Da die Dreh-Fräsmaschine nur über einen Messkanal verfügte, rüstete LeanWerks die Maschine mit einem RMI-Q-Funkempfänger von Renishaw nach und installierte eine speicherprogrammierbare Steuerungskarte (PLC) in der Hauptsteuertafel der Maschine, um ein zweites Messtastersignal zu verarbeiten. Die kurze Sonde verwendet einen 25 mm langen Taststift, während die lange Sonde einen 50 mm langen Taststift verwendet, der auf einer 200-mm-Verlängerung montiert ist. Beide verwenden einen Messtasterkörper RMP-60 von Renishaw.
Die Messroutinen wurden mit der Software Inspection Plus von Renishaw programmiert, und der resultierende Code wurde an den entsprechenden Stellen dem Maschinenprogramm hinzugefügt. Die anfängliche Prüfroutine misst Punkte an der unteren Öffnung innerhalb des Gehäuses und der Öffnung an der Vorderseite des Gehäuses, um die Mittelachse des Teils zu definieren. Andere Merkmale, die geprüft werden, umfassen eine der kleinen Öffnungen in der Nähe der Fläche, um die Rotationsausrichtung des Teils zu definieren, und eine Wand innerhalb des Hauptseitenflanschs, um die Position der Z-Achse des Teils zu definieren. Das Mazak-Softwaremodul Arbeitspositionsfehlerkompensation (WPEC) ermöglicht Abweichungen, die durch Berechnungen der wahren Position erkannt werden, die aus der anfänglichen Messroutine abgeleitet werden, um sich mit dem Teil durch Spindelindexbewegungen zu bewegen. Nach den anfänglichen Sondierungsroutinen wird eine zusätzliche Sondierung durchgeführt, um die Position verwandter Merkmale und nachbearbeiteter Oberflächen zu bestätigen.
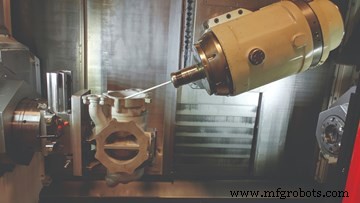
Um Merkmale tief im Inneren des Gehäuses zu untersuchen, hat LeanWerks verwendet einen 50 mm langen Stift, der auf einer 200 mm-Verlängerung montiert ist.
Schließlich führten die für dieses Teil erforderlichen tiefgreifenden Bearbeitungsvorgänge und das abrasive Aluminiummaterial dazu, dass die Werkstatt fortschrittliche Schneidwerkzeugtechnologie einsetzte. Für diesen Job setzt der Betrieb das Werkzeughaltersystem Rego-Fix powRgrip ein. Als Alternative zum Schrumpfsitz ist powRgrip ein mechanisches Einpresssystem, das aus einem Werkzeughalter, einer Präzisionsspannzange und einer kompakten hydraulischen Spanneinheit für den Tisch besteht, mit der die Spannzange und das Werkzeug in den Halter eingesetzt werden. Laut Rego-Fix ist das System in der Lage, hohe Klemmkräfte zu erzeugen und gleichzeitig einen Gesamtanzeigewert von weniger als 0,0001 Zoll aufrechtzuerhalten. Die Steifigkeit dieses Systems verbessert die Standzeit und Schnittgenauigkeit.
Schneidwerkzeuge, die für diese Arbeit verwendet werden, müssen positiv hohe Spanwinkel haben und mit sehr hohen Geschwindigkeiten mit geringen Schnitttiefen betrieben werden. Es werden Schaftfräser von Garr Alumistar sowie ein kleiner Planfräser mit unbeschichteten, hochglanzpolierten, hochpositiven Wendeschneidplatten verwendet.
LeanWerks stellt auch Werkzeuge für diesen Job mit einem Speroni STP Magis 400-Voreinstellgerät ein, das von Big Kaiser erhältlich ist. Das Einstellgerät ermöglicht nicht nur die externe Einstellung von Werkzeugen, sondern hilft vor allem bei der Qualifizierung und Fehlersuche, da es die Inspektion der Schneidkante, die Validierung der Form von Formwerkzeugen und die Messung des Rundlaufs erleichtert.
Wendepunkt
Das Verfahren, das LeanWerks entwickelt hat, um diesen Feingussauftrag auf seiner Drehmühle zu bearbeiten, verbesserte die Produktionsrate von 10 Stunden pro Teil auf weniger als zwei Stunden pro Teil. Infolgedessen erwägt das Geschäft weiterhin andere Möglichkeiten, wie es die Möglichkeiten seiner vorhandenen Kapazität auf ähnliche Weise maximieren kann, während es der Arbeit in verschiedenen neuen Branchen nachgeht.
Industrielle Ausrüstung
- Was ist Schleifstrahlbearbeitung und wie funktioniert sie?
- Faktoren, die die CNC-Bearbeitungskosten beeinflussen
- Zweispindelzentren drehen beide Teileenden in einer Einrichtung
- Größenbeschränkungen in der CNC-Bearbeitung
- Einblicke in Guss- und Bearbeitungsprodukte (Teil 3)
- Einblick in Guss- und Bearbeitungsprodukte (Teil 2)
- Wie können die Kosten für CNC-Bearbeitungsteile gesenkt werden?
- Was bedeutet 5-Achsen-CNC-Bearbeitung?
- Benötigen Sie eine VMC 5-Achsen-Maschine?
- Schritte umfassen den Bearbeitungsprozess